Diferença entre o cortador de ponto único e o cortador de vários pontos
A usinagem ou corte de metal é um processo de fabricação secundário em que o excesso de material é gradualmente removido da peça de trabalho para conferir acabamento, dimensão e tolerância desejados. Para atender a necessidade de usinagem eficiente e econômica de uma grande variedade de materiais de diferentes maneiras, vários processos relevantes surgiram ao longo dos anos. Em linhas gerais esses processos podem ser agrupados em usinagem convencional (macro e micro), acabamento abrasivo e usinagem não tradicional (NTM). Os processos convencionais de usinagem estão bem estabelecidos e consistem em um grande número de operações para geração de diversos recursos. Por exemplo, torneamento, fresamento, rosqueamento, recartilhamento, faceamento, furação, mandrilamento, alargamento, etc. Todas essas operações são realizadas com o auxílio de uma ferramenta de corte que efetivamente retira material da peça na forma de cavacos.
Ferramenta de corte , também chamado de cortador, é um dispositivo em forma de cunha e arestas afiadas que comprime uma fina camada de material da peça de trabalho para cisalhá-lo na forma de cavacos durante a usinagem. Durante a usinagem, a máquina-ferramenta realmente segura a fresa e o trabalho e, ao mesmo tempo, transmite os movimentos relativos desejados (velocidade, avanço, profundidade de corte). Portanto, o cortador é parte integrante de todas as operações de usinagem convencionais; entretanto, sua forma e tamanho podem variar dependendo do recurso a ser produzido e da operação empregada. Qualquer que seja a geometria do cortador, ele deve consistir em uma aresta de corte afiada para remover facilmente o material que requer o mínimo de esforço. Uma vanguarda é basicamente uma aresta reta ou curva produzida pela interseção de quaisquer duas superfícies de ponta de ferramenta (superfície de saída, superfície de flanco principal e superfície de flanco auxiliar). Com base no número de arestas de corte presentes, os cortadores podem ser classificados como cortador de ponto único e cortador multiponto.
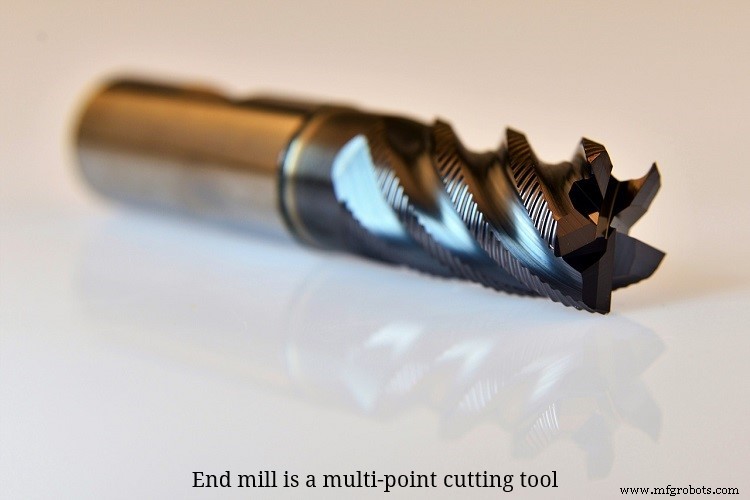
Um cortador de ponto único contém apenas uma aresta de corte principal que pode participar ativamente da ação de remoção de material durante a usinagem. Assim, uma aresta de corte remove todo o volume de material em uma única passagem. Ao contrário disso, um cortador multiponto consiste em pelo menos duas arestas de corte e todas elas podem participar igualmente na ação de remoção de material em uma única passagem. Assim, a carga de cavacos por aresta de corte reduz significativamente. As operações de torneamento, modelagem, planejamento, mandrilamento, corte com mosca, etc. são realizadas usando cortador de ponto único; enquanto, fresamento, furação, recartilhamento, alargamento, etc. utilizam cortador multi-ponto. Uma fresa multiponto pode conter desde duas (broca ou fresa de topo) até centenas de arestas de corte (abrasivos de rebolo). Várias diferenças entre o cortador de ponto único e o cortador multiponto são dadas abaixo no formato de tabela.
Tabela:Diferenças entre cortadores de ponto único e multiponto
Cortador de ponto único | Cortador multiponto |
---|---|
As fresas de ponta única contêm apenas uma aresta de corte principal que pode participar ativamente do cisalhamento em uma única passagem durante a usinagem. | Os cortadores de várias pontas podem conter mais de uma (duas a centenas) arestas de corte que podem participar do cisalhamento em uma única passagem. |
Uma única aresta de corte permanece em contato contínuo com a peça de trabalho. | Aqui todas as arestas de corte podem ou não permanecer em contato contínuo com a peça de trabalho. |
Devido ao contato contínuo, a taxa de aumento da temperatura da ferramenta é alta e, portanto, as precauções adequadas devem ser adotadas para evitar danos térmicos. | Geralmente, as arestas de corte engatam e desligam simultaneamente durante o corte e, portanto, protegem-se inerentemente contra superaquecimento e danos consequentes. |
A carga total de cavacos em uma única passagem é suportada por apenas uma aresta de corte. | A carga total de cavacos em uma única passagem é distribuída entre todas as arestas de corte. |
Velocidade, avanço e profundidade de corte mais baixos são empregados para proteger a ferramenta de corte contra quebras não planejadas. Portanto, o MRR e a produtividade são baixos. | Velocidade, avanço e profundidade de corte mais altos podem ser empregados com segurança. Assim, o MRR e a produtividade são maiores. |
A quebra não planejada de uma aresta de corte requer o término imediato de todo o processo e a substituição do cortador. | A quebra de uma aresta de corte não possui problema significativo e, portanto, a operação pode ser realizada, pelo menos para esse passe. |
As fresas de ponta única são fáceis de projetar e fabricar. | As fresas multiponto são comparativamente difíceis de projetar e fabricar. |
As seguintes operações de usinagem são executadas com fresa de ponta simples:
| As seguintes operações de usinagem são executadas usando a fresa de ponto único:
|
Número de arestas de corte: Como o nome sugere, as ferramentas de corte de ponto único consistem em apenas uma aresta de corte principal. Esta aresta participa da ação de remoção de material ao longo do passe durante a usinagem. Na próxima passagem, a mesma aresta de corte pode ser utilizada ou pode ser substituída por uma nova mais afiada. Vale ressaltar que tais fresas podem conter mais de uma aresta de corte por vez na ferramenta; no entanto, apenas uma irá engatar durante a usinagem (por exemplo, considere a ferramenta de torneamento baseada em pastilhas que normalmente contém 3 ou 4 arestas de corte presentes no corpo da ferramenta por vez, mas apenas uma participa do corte). Ao contrário disso, as fresas multiponto contêm mais de uma aresta de corte e todas (ou a maioria delas) participam ativamente da ação de cisalhamento em uma única passagem.
Contato entre fresa e peça e suas consequências: Quando a usinagem é realizada com fresa de ponta única, apenas uma aresta de corte permanece em contato contínuo com a peça de trabalho. Isso causa um aumento acentuado da temperatura da ferramenta e o resultado são danos térmicos da fresa, como maior taxa de desgaste, deformação plástica, vida útil da ferramenta degradada, etc. no cortador, etc.) devem ser tomadas para se livrar de tais danos. Por outro lado, na fresa multiponto, todas (exemplo:furação, alargamento, etc.) Normalmente fresas com maior número de arestas, removem material por engate e desengate simultâneos de arestas de corte. Isso protege o cortador de superaquecimento, permitindo tempo suficiente para dissipar o calor durante o período de desconexão. No entanto, o corte intermitente pode aumentar a vibração e as forças desequilibradas.
Carga de chip: É axiomático que durante a usinagem a fresa comprime uma fina camada de material de trabalho e gradualmente corta-a. Assim, a cada instante, o movimento do cortador é restringido por uma área de material de trabalho, que deve ser removido. Essa área do material da peça logo à frente da fresa em um determinado instante é chamada de carga de cavacos. Matematicamente, pode ser expresso pela multiplicação do avanço e profundidade de corte (s×t) e pode ser expresso em termos de unidade de tempo ou por revolução. No caso de fresa de ponta única, toda a carga de cavacos é suportada por apenas uma aresta de corte; enquanto que, na fresa multiponto, toda a carga de cavacos é distribuída entre todas as arestas de corte e, portanto, cada aresta é submetida a uma carga de cavacos significativamente menor.
Provisão para maior velocidade, avanço e profundidade de corte: Com a fresa de ponta única, se a velocidade, o avanço e a profundidade de corte mais altos forem empregados, a aresta de corte estará sujeita a uma carga de cavacos mais alta e, portanto, a ferramenta pode falhar prematuramente por quebra catastrófica. Com a fresa multiponto, velocidades, avanço e profundidade de corte mais altos podem ser empregados sem nenhum problema palpável. Como a taxa de remoção de material (MRR) é proporcional à velocidade de corte, taxa de avanço e profundidade de corte (MRR =1000V.s.t), essas fresas podem fornecer maior MRR, o que consequentemente ajuda a melhorar a produtividade.
Quebra de ponta: Durante a usinagem com fresa de ponta única, em caso de quebra não planejada de uma aresta de corte por algum motivo inexorável (como falta de homogeneidade no material de trabalho, vibração, entupimento de cavacos, mau funcionamento da máquina, etc.), a operação é obrigatoriamente necessária para parar para substituir o cortador com um novo. No entanto, em casos semelhantes com fresas multiponto (ou seja, quebra de uma aresta), a operação pode ser realizada sem muitos problemas com a ajuda de outras arestas de corte intactas. No entanto, pode não ser possível em todos os cenários, especialmente quando a ferramenta consiste em menos arestas de corte.
Design e fabricação: Devido à geometria simples, as fresas de ponta única são fáceis de projetar e também podem ser fabricadas facilmente em comparação com as fresas multiponto.
A comparação científica entre cortadores de ponto único e cortadores multiponto é apresentada neste artigo. O autor também sugere que você consulte as seguintes referências para melhor compreensão do tema.
- Usinagem e máquinas-ferramentas por A. B. Chattopadhyay (1 st edição, Wiley).
- Engenharia e Tecnologia de Manufatura:Edição SI por S. Kalpakjian e S. R. Schmid (7 th edição, Pearson Ed Asia).
Tecnologia industrial
- Diferença entre acionamento por corrente e acionamento por engrenagem
- Diferença entre acionamento por correia e acionamento por corrente
- Diferença entre o cortador de ponto único e o cortador de vários pontos
- Diferença entre a superfície de inclinação e a superfície de flanco da ferramenta de corte
- Diferença entre o ângulo de saída e o ângulo de folga da ferramenta de corte
- Diferença entre o processo de torneamento e o processo de fresamento
- Diferença entre ferramenta de corte e rebolo
- Diferença entre usinagem e retificação
- Qual é a diferença entre a Indústria 4.0 e a Indústria 5.0?
- Diferença entre o compensado de madeira macia e o compensado de madeira dura