Diferença entre o raio da aresta e o raio da ponta da ferramenta de corte
A usinagem ou corte de metal é um processo de fabricação subtrativo em que o excesso de material é gradualmente removido na forma de cavacos de peças pré-formadas usando uma ferramenta de corte para conferir forma, tamanho e acabamento superficial pretendidos. Para remover continuamente (cortar) camadas de material, um cortador de arestas afiadas é indispensável. Durante a usinagem, os movimentos relativos são fornecidos entre a peça de trabalho e a ferramenta de corte em direções específicas com base na geometria do recurso pretendido e na operação selecionada. Assim, o cortador comprime uma fina camada de material pela ponta e, posteriormente, a corta. Como a ação de cisalhamento de todo o material é realizada por esta fresa, sua geometria, orientação e material são três fatores cruciais que influenciam todo o desempenho da usinagem.
O que vem na geometria do cortador?
A geometria da ferramenta lida com várias características geométricas da ferramenta de corte que influenciam diretamente a capacidade e o desempenho da usinagem. Existe uma forma básica de fresa para cada operação de usinagem; no entanto, muitas características geométricas podem variar dentro de um certo limite para fornecer um resultado ideal sob condições especificadas, mantendo a forma básica inalterada. Esses recursos também são exibidos de maneira padronizada em vários sistemas de designação de ferramentas (por exemplo, ASA, ORS, NRS, MRS, etc.).
A superfície de saída e a superfície de flanco são duas superfícies importantes de cada fresa e suas inclinações são indicadas com a ajuda do ângulo de saída e ângulo de incidência, respectivamente. Certas fresas também podem ter mais de uma superfície de flanco e, portanto, são denominadas superfícies de flanco primária e auxiliar e os ângulos correspondentes como ângulos de folga primários e auxiliares. Uma fresa específica pode ter ângulos variados com base na direção (ou plano) em que é medida e o mesmo também se reflete nas assinaturas da ferramenta (por exemplo, inclinação lateral e inclinação traseira - ambos indicam inclinação da superfície de inclinação, mas em direções diferentes).
Além dos ângulos de saída e de afastamento, a assinatura da ferramenta também pode exibir outras informações, como o raio da ponta. No entanto, a geometria da ferramenta pode incluir outras informações relevantes além daquelas encontradas na assinatura da ferramenta. O raio da borda é um exemplo vital.
Conceito de aresta e ponta do cortador
Fisicamente, a borda ocorre quando duas superfícies sólidas se cruzam e um nariz ocorre quando três ou mais superfícies sólidas se cruzam. No cortador também, a aresta emerge onde a superfície de saída e a superfície do flanco se cruzam e o mesmo é denominado como aresta de corte. Se o cortador contiver duas superfícies de flanco, duas arestas de corte serão produzidas – aresta de corte primária (interseção entre a superfície de saída e a superfície de flanco principal) e a aresta de corte auxiliar (interseção entre a superfície de saída e a superfície de flanco auxiliar). Um cortador pode conter uma ou mais arestas de corte e, portanto, os cortadores podem ser classificados como ferramenta de corte de ponto único e multiponto.
Quando três superfícies de ponta de ferramenta (entrada, flanco principal e flanco auxiliar) se cruzam, surge uma ponta de corte. Durante a usinagem, este nariz permanece em contato físico com a peça de trabalho e é submetido a extrema pressão e atrito.
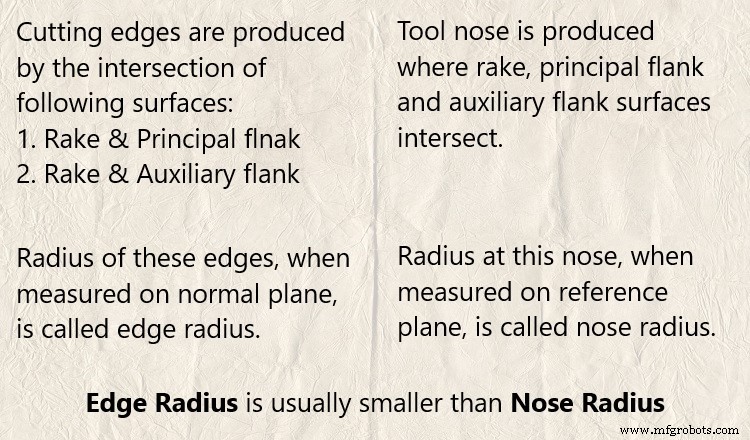
O que é o raio da borda?
Nenhuma borda é perfeitamente afiada. Mesmo que seja perfeitamente afiado, não pode ser medido com precisão, pois todos os instrumentos de medição têm capacidade limitada. Na verdade, a nitidez não pode ser medida diretamente. É o arredondamento da borda que é medido e a nitidez é inversamente proporcional ao arredondamento. Quanto maior a redondeza ou o raio da borda, menos afiada ela é. Assim, a circularidade é a medida quantitativa do raio da aresta; enquanto que a nitidez é uma medida qualitativa baseada no valor da circularidade.
Valor do raio da borda: Embora o limite mínimo teórico para a circularidade seja o raio do átomo do material em questão, praticamente tal aresta terá uma resistência muito baixa e, portanto, não tem aplicação. Isso indica que uma aresta de corte muito afiada (raio muito baixo) terá baixa resistência e, portanto, quebrará rapidamente durante a usinagem. Assim, uma redondeza adequada é fornecida em cada aresta do cortador para que não falhe ou fique sem corte rapidamente. O valor do raio da aresta geralmente varia entre 0,5 – 10µm para ferramentas micro e de precisão e 10 – 500µm para ferramentas convencionais.
Efeitos do raio da aresta na macrousinagem: Na usinagem convencional em macroescala, como torneamento, fresamento, furação, etc., este parâmetro tem uma influência insignificante no desempenho geral da usinagem, pois a espessura do cavaco não cortado é esmagadoramente maior que o raio da aresta. Normalmente, a espessura do cavaco não cortado é de 0,2 a 2 mm, enquanto o raio da aresta é de 0,5 a 10 µm; isso significa 500 – 1000 vezes maior. Por ser um parâmetro trivial na usinagem convencional, não é incorporado na assinatura da ferramenta da fresa correspondente.
Efeitos do raio da borda na microusinagem: No entanto, quando a usinagem é realizada em escala micro ou nano, o raio da aresta se torna um parâmetro predominante que influencia a capacidade de corte e a qualidade da superfície usinada. Nesses casos, o raio da aresta se torna comparável à espessura do cavaco não cortado. Por exemplo, em fresas de microfresamento (microfresa de topo), o raio da aresta é normalmente de 2 a 5µm, enquanto a taxa de avanço (equivalente à espessura de cavacos não cortados no fresamento de topo) é de apenas 0,5 a 10µm/canal. Da mesma forma, no torneamento com diamante (usinagem de precisão), o raio da aresta é um parâmetro significativo. Várias investigações revelaram que a profundidade mínima de corte deve estar dentro de 10 – 50% (com base em outros parâmetros) do raio da aresta para remover o material com eficiência em cada passagem.
O que é o raio do nariz?
Na ferramenta de corte, o nariz é o resultado da interseção da superfície de saída, superfície de flanco principal e superfície de flanco auxiliar. Como de costume, não pode ser perfeitamente afiado e uma circularidade adequada é fornecida na ponta da ferramenta. O raio desta ponta arredondada, quando medido no plano de referência, dá o valor do raio da ponta. É um parâmetro significativo para a usinagem convencional, pois seu valor está próximo da espessura do cavaco não cortado.
Valor do raio do nariz: Normalmente, o raio da ponta das fresas convencionais varia entre 0,8 – 2 mm; enquanto a espessura do cavaco não cortado pode ser de 0,2 a 2 mm. Para micro-cortadores, o raio da ponta é muito menor, normalmente algumas dezenas de mícrons.
A comparação científica entre o raio da aresta e o raio da ponta é apresentada neste artigo. Em conclusão pode-se dizer que o raio fornecido na aresta de corte é basicamente o raio da aresta e o raio fornecido na ponta da ferramenta é denominado como raio de ponta. Na usinagem convencional em macroescala, o raio da aresta tem uma influência insignificante, mas em microescala ou usinagem de precisão é um parâmetro de dominação. O raio da ponta, no entanto, sempre influencia o desempenho da usinagem.
Tecnologia industrial
- Diferença entre acionamento por corrente e acionamento por engrenagem
- Diferença entre acionamento por correia e acionamento por corrente
- Diferença entre o cortador de ponto único e o cortador de vários pontos
- Diferença entre a superfície de inclinação e a superfície de flanco da ferramenta de corte
- Diferença entre o ângulo de saída e o ângulo de folga da ferramenta de corte
- Diferença entre o processo de torneamento e o processo de fresamento
- Diferença entre ferramenta de corte e rebolo
- Diferença entre usinagem e retificação
- Qual é a diferença entre a Indústria 4.0 e a Indústria 5.0?
- Diferença entre o compensado de madeira macia e o compensado de madeira dura