Processo de fabricação de placas de circuito impresso

Índice:
- Etapa 1: Projetando o PCB
- Etapa 2: Revisão do projeto e perguntas de engenharia
- Etapa 3 :Imprimindo o design do PCB
- Etapa 4: Imprimindo o cobre para a camada interna
- Etapa 5: Grave as camadas internas ou o núcleo para remover o cobre
- Etapa 6: Alinhamento de camadas
- Etapa 7: Inspeção óptica automatizada
- Etapa 8: Laminação das camadas de PCB
- Etapa 9: Perfuração
- Etapa 10: Chapeamento de PCB
- Etapa 11: Imagem da camada externa
- Etapa 12: Gravação da camada externa
- Etapa 13: AOI da camada externa
- Etapa 14: Aplicação de máscara de solda
- Etapa 15: Aplicação de serigrafia
- Etapa 16: Finalizando o PCB
- Etapa 17: Teste de confiabilidade elétrica
- Etapa 18: Perfil e rota de saída
- Etapa 19: Verificação de qualidade e inspeção visual
- Etapa 20: Embalagem e entrega
O que é o processo de fabricação de PCB?
O processo de fabricação de placas de circuito impresso (PCB) requer um procedimento complexo para garantir o desempenho do produto acabado. Embora as placas de circuito possam ser simples, duplas ou multicamadas, os processos de fabricação utilizados só diferem após a produção da primeira camada. Devido a diferenças na estrutura dos PCBs, alguns podem exigir 20 ou mais etapas durante a fabricação.
O número de etapas necessárias para a produção de placas de circuito impresso está relacionado à sua complexidade. Pular qualquer etapa ou reduzir o procedimento pode afetar negativamente o desempenho da placa de circuito. No entanto, quando concluídos com êxito, os PCBs devem executar suas tarefas adequadamente como componentes eletrônicos essenciais.
Solicite um orçamento gratuito
Quais são as partes de um PCB?
Existem quatro partes principais em um PCB:
- Substrato: O primeiro, e mais importante, é o substrato, geralmente feito de fibra de vidro. A fibra de vidro é usada porque fornece uma resistência do núcleo ao PCB e ajuda a resistir à quebra. Pense no substrato como o “esqueleto” do PCB.
- Camada de cobre: Dependendo do tipo de placa, esta camada pode ser folha de cobre ou um revestimento de cobre completo. Independentemente de qual abordagem é usada, o ponto do cobre ainda é o mesmo - para transportar sinais elétricos de e para o PCB, assim como seu sistema nervoso transporta sinais entre seu cérebro e seus músculos.
- Máscara de solda: A terceira peça do PCB é a máscara de solda, que é uma camada de polímero que ajuda a proteger o cobre para que não entre em curto-circuito ao entrar em contato com o meio ambiente. Desta forma, a máscara de solda atua como a “pele” do PCB.
- Serigrafia: A parte final da placa de circuito é a serigrafia. A serigrafia geralmente está no lado do componente da placa usada para mostrar números de peças, logotipos, configurações de interruptores de símbolos, referência de componentes e pontos de teste. A serigrafia também pode ser conhecida como legenda ou nomenclatura.
Obtenha o preço e o prazo de entrega
Agora que analisamos os conceitos básicos de PCBs e anatomia de PCBs, percorreremos todo o processo de como construir um PCB.
Como uma PCB é fabricada?
As etapas do processo de projeto de PCB começam com o projeto e a verificação e continuam até a fabricação das placas de circuito. Muitas etapas exigem orientação por computador e ferramentas acionadas por máquina para garantir a precisão e evitar curtos-circuitos ou circuitos incompletos. As placas concluídas devem passar por testes rigorosos antes de serem embaladas e entregues aos clientes.
Primeiro passo:projetar o PCB
O passo inicial de qualquer fabricação de PCB é, obviamente, o design. A fabricação e o design da PCB sempre começam com um plano:o projetista estabelece um projeto para a PCB que atende a todos os requisitos descritos. O software de projeto mais usado pelos projetistas de PCB é um software chamado Extended Gerber — também conhecido como IX274X.

Quando se trata de design de PCB, o Extended Gerber é um excelente software porque também funciona como um formato de saída. O Gerber estendido codifica todas as informações que o projetista precisa, como o número de camadas de cobre, o número de máscaras de solda necessárias e as outras peças de notação de componentes. Uma vez que um projeto para o PCB é codificado pelo software Gerber Extended, todas as diferentes partes e aspectos do projeto são verificados para garantir que não haja erros.
Uma vez que o exame pelo projetista esteja completo, o projeto de PCB finalizado é enviado para uma casa de fabricação de PCB para que o PCB possa ser construído. Na chegada, o plano de projeto da placa de circuito impresso passa por uma segunda verificação pelo fabricante, conhecida como verificação Design for Manufacture (DFM). Uma verificação adequada do DFM garante que o projeto da PCB atenda, no mínimo, às tolerâncias exigidas para a fabricação.
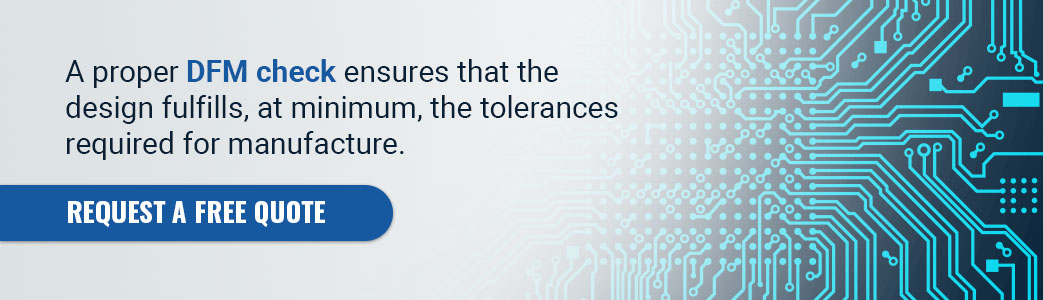
Etapa dois: Revisão de projeto e perguntas de engenharia
Outra etapa importante do processo de fabricação de placas de circuito impresso envolve a verificação de possíveis erros ou falhas no projeto. Um engenheiro analisa cada parte do projeto da PCB para garantir que não haja componentes ausentes ou estruturas incorretas. Depois de obter autorização de um engenheiro, o design passa para a fase de impressão.
Etapa Três:Imprimindo o Design da PCB
Depois que todas as verificações estiverem concluídas, o design da PCB pode ser impresso. Ao contrário de outros planos, como desenhos arquitetônicos, os planos de PCB não são impressos em uma folha de papel comum de 8,5 x 11. Em vez disso, é usado um tipo especial de impressora, conhecido como impressora plotadora. Uma impressora plotter faz um “filme” do PCB. O produto final desse “filme” se parece muito com as transparências que costumavam ser usadas nas escolas – é essencialmente um negativo fotográfico do próprio quadro.
As camadas internas do PCB são representadas em duas cores de tinta:
- Tinta preta: Usado para os traços e circuitos de cobre do PCB
- Tinta transparente: Indica as áreas não condutoras do PCB, como a base de fibra de vidro
Nas camadas externas do design da placa de circuito impresso, essa tendência é revertida – a tinta transparente refere-se à linha de caminhos de cobre, mas a tinta preta também se refere às áreas onde o cobre será removido.
Cada camada de PCB e a máscara de solda que a acompanha recebe seu próprio filme, portanto, uma PCB simples de duas camadas precisa de quatro folhas - uma para cada camada e uma para a máscara de solda que a acompanha.
Depois que o filme é impresso, eles são alinhados e um orifício, conhecido como orifício de registro, é perfurado através deles. O orifício de registro é usado como guia para alinhar os filmes posteriormente no processo.
Etapa Quatro:Imprimindo o Cobre para as Camadas Interiores
O passo quatro é o primeiro passo no processo em que o fabricante começa a fazer o PCB. Depois que o desenho do PCB é impresso em um pedaço de material laminado, o cobre é então pré-ligado ao mesmo pedaço de laminado, que serve como estrutura para o PCB. O cobre é então gravado para revelar o projeto anterior.
Em seguida, o painel laminado é coberto por um tipo de filme fotossensível chamado resist. A resistência é feita de uma camada de produtos químicos fotorreativos que endurecem após serem expostos à luz ultravioleta. O resist permite que os técnicos obtenham uma combinação perfeita entre as fotos do projeto e o que é impresso no fotorresistente.
Uma vez que a resistência e o laminado estão alinhados - usando os orifícios anteriores - eles recebem uma explosão de luz ultravioleta. A luz ultravioleta passa pelas partes translúcidas do filme, endurecendo o fotorresistente. Isso indica áreas de cobre que devem ser mantidas como caminhos. Em contraste, a tinta preta impede que a luz chegue às áreas que não devem endurecer para que possam ser removidas posteriormente.
Uma vez que a placa foi preparada, ela é lavada com uma solução alcalina para remover qualquer um dos restos fotorresistentes. A placa é então lavada à pressão para remover qualquer coisa deixada na superfície e deixada para secar.
Após a secagem, a única resistência que deve ser deixada no PCB é em cima do cobre que permanece como parte do PCB quando finalmente é solto. Um técnico examina os PCBs para garantir que não haja erros. Se nenhum erro estiver presente, então é para a próxima etapa.
Etapa Cinco: Grave as camadas internas ou o núcleo para remover o cobre
O núcleo ou as camadas internas da placa de circuito impresso precisam ter o cobre extra removido antes que o processo de fabricação do PCB possa continuar. A gravação envolve cobrir o cobre necessário na placa e expor o restante da placa a um produto químico. O processo de gravação química remove todo o cobre desprotegido da PCB, deixando apenas a quantidade necessária da placa.
Esta etapa pode variar em seu tempo ou na quantidade de solvente de gravação de cobre utilizado. PCBs grandes ou com estruturas mais pesadas podem usar mais cobre, resultando em mais cobre que deve ser submetido à corrosão para remoção. Portanto, essas placas exigirão tempo extra ou solvente.
Se um processo de fabricação de placas de circuito impresso for para projetos multicamadas
As placas de circuito impresso multicamadas têm etapas adicionais para considerar as camadas extras do projeto durante sua fabricação. Essas etapas espelham muitas daquelas usadas durante PCBs de camada única. No entanto, as fases se repetem para cada camada do tabuleiro. Além disso, em PCBs multicamadas, a folha de cobre normalmente substitui o revestimento de cobre entre as camadas.

Imagem da camada interna
A imagem da camada interna segue os mesmos procedimentos da impressão do design da PCB. O design é impresso em uma impressora plotter para criar um filme. A máscara de solda para a camada interna também é impressa. Depois de alinhar ambos, uma máquina cria um orifício de registro nos filmes para ajudar a manter os filmes alinhados adequadamente com as camadas posteriormente.
Depois de adicionar cobre ao material laminado para a camada interna, os técnicos colocam o filme impresso sobre o laminado e os alinham usando os orifícios de registro.
A luz ultravioleta expõe o filme, também conhecido como resist, para endurecer os produtos químicos das áreas de cores claras no padrão impresso. Essas áreas endurecidas não serão lavadas durante a fase de ataque, enquanto as áreas não endurecidas sob o filme de cor escura terão seu cobre removido.
Gravação da camada interna
Após a imagem, as áreas cobertas pela tinta branca endureceram. Este material endurecido protege o cobre por baixo que permanecerá na placa após a gravação.
Os técnicos primeiro lavam a placa com alcalino para remover qualquer resistência restante da placa que não endureceu. Essa limpeza expõe áreas que cobriam partes não condutoras da placa de circuito impresso. Em seguida, os trabalhadores irão remover o excesso de cobre dessas áreas não condutoras, submergindo a placa em um solvente de cobre para dissolver o cobre exposto.
Resistir à decapagem
A etapa de remoção de resistência remove qualquer resistência restante que cobre o cobre da camada interna do PCB. A limpeza de qualquer resiste restante garante que o cobre não terá nada que prejudique sua condutividade. Após a remoção do resist, a camada está pronta para passar pela inspeção de seu projeto básico.
Pós-Etch Punch
O punção pós-gravação alinha as camadas e faz um furo através delas usando os furos de registro como guia. Assim como na inspeção subsequente desse furo e alinhamento, a punção acontece a partir de um computador que orienta exatamente uma máquina conhecida como punção ótica. Após o punção óptico, as camadas se movem para a inspeção óptica automatizada (AOI) da camada interna.
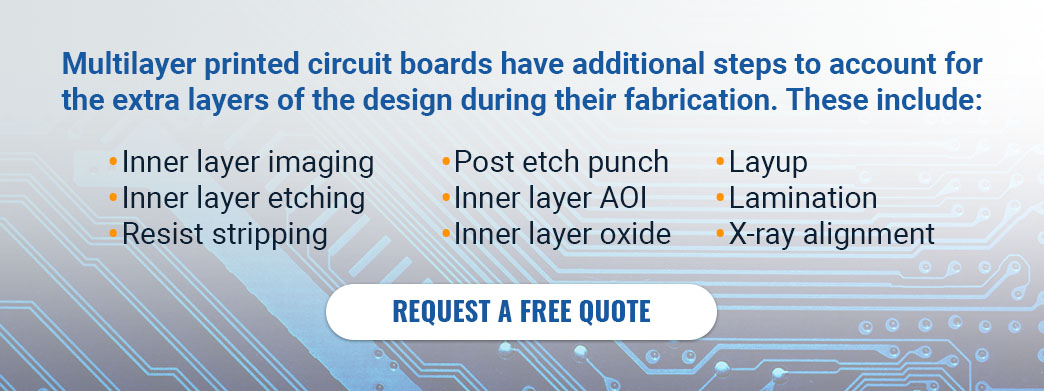
AOI da camada interna
A inspeção óptica automatizada da camada interna usa um computador para examinar cuidadosamente a camada interna para procurar padrões incompletos ou resistências que ainda possam estar na superfície. Se a camada PCB passar pela AOI, ela continuará no processo.
Óxido de camada interna
O óxido aplicado na camada interna garante uma melhor ligação da folha de cobre e das camadas de resina epóxi isolante entre as camadas interna e externa.
Fixação
A etapa de layup no processo de fabricação de PCB multicamadas acontece quando uma máquina ajuda a alinhar, aquecer e unir as camadas com uma camada de folha de cobre e material isolante entre as camadas interna e externa. Normalmente, os computadores guiam essas máquinas porque o alinhamento das camadas e a ligação devem ser exatos para a estrutura adequada da placa de circuito impresso.
Laminação
A laminação usa calor e pressão para derreter o epóxi de ligação entre as camadas. Os PCBs devidamente laminados manterão suas camadas firmemente unidas com isolamento eficaz entre as camadas.
Alinhamento de Raios-X
Ao perfurar placas multicamadas após a laminação, um raio X garante o alinhamento da broca. Esses orifícios permitem que as conexões ocorram entre as camadas do PCB multicamadas. Portanto, a precisão de seu posicionamento e tamanho em relação ao restante da camada e às demais camadas é crucial. Seguindo o alinhamento de raios-X das camadas, a placa de circuito impresso passa por perfuração, pegando com a etapa nove da fabricação da placa PCB simples ou dupla face.
Etapa seis:alinhamento de camadas
Após a limpeza de cada uma das camadas do PCB, elas estão prontas para alinhamento de camadas e inspeção óptica. Os furos anteriores são usados para alinhar as camadas interna e externa. Para alinhar as camadas, um técnico as coloca em um tipo de máquina de punção conhecida como punção óptica. O perfurador óptico empurra um pino pelos orifícios para alinhar as camadas do PCB.
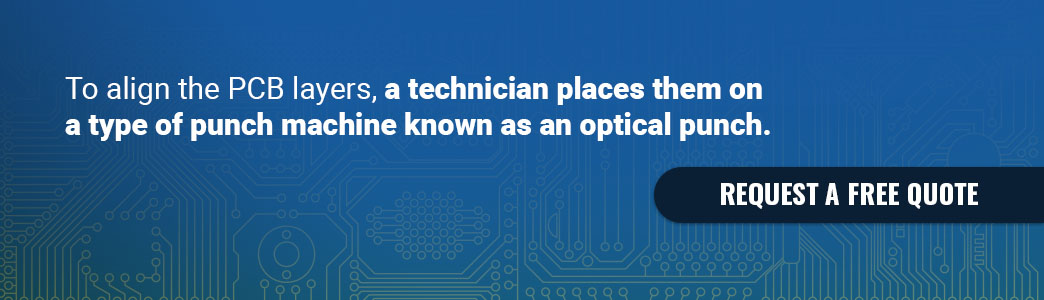
Etapa sete:inspeção óptica automatizada
Após o punção óptico, outra máquina realiza uma inspeção óptica para garantir que não haja defeitos. Essa inspeção óptica automatizada é incrivelmente importante porque, uma vez que as camadas são colocadas juntas, quaisquer erros existentes não podem ser corrigidos. Para confirmar que não há defeitos, a máquina AOI compara o PCB com o projeto Extended Gerber, que serve como modelo do fabricante.
Depois que o PCB passou pela inspeção - ou seja, nem o técnico nem a máquina AOI encontraram nenhum defeito - ele passa para as últimas etapas da fabricação e produção do PCB.
A etapa AOI é crucial para o funcionamento da placa de circuito impresso. Sem ele, placas que poderiam ter curto-circuitos, não atender às especificações de projeto ou ter cobre extra que não foi removido durante a gravação poderiam passar pelo resto do processo. O AOI evita que as placas defeituosas continuem servindo como um ponto de verificação de qualidade no meio do processo de produção. Mais tarde, esse processo se repete para as camadas externas depois que os engenheiros terminam a imagem e gravam-nas.
Etapa Oito:Laminação das Camadas de PCB
Na etapa seis do processo, as camadas de PCB estão todas juntas, esperando para serem laminadas. Assim que as camadas forem confirmadas como livres de defeitos, elas estarão prontas para serem fundidas. O processo de laminação de PCB é feito em duas etapas:a etapa de lay-up e a etapa de laminação.
A parte externa do PCB é feita de pedaços de fibra de vidro que foram pré-embebidos/pré-revestidos com resina epóxi. A peça original do substrato também é coberta por uma fina camada de folha de cobre que agora contém as gravuras para os traços de cobre. Quando as camadas externas e internas estiverem prontas, é hora de juntá-las.

O ensanduichamento dessas camadas é feito com grampos de metal em uma mesa de prensa especial. Cada camada se encaixa na mesa usando um pino especializado. O técnico que faz o processo de laminação começa colocando uma camada de resina epóxi pré-revestida conhecida como pré-impregnada ou pré-impregnada – na bacia de alinhamento da mesa. Uma camada do substrato é colocada sobre a resina pré-impregnada, seguida por uma camada de folha de cobre. A folha de cobre, por sua vez, é seguida por mais folhas de resina pré-impregnada, que são finalizadas com um pedaço e um último pedaço de cobre conhecido como placa de prensagem.
Uma vez que a placa de prensagem de cobre está no lugar, a pilha está pronta para ser prensada. O técnico o leva para uma prensa mecânica e pressiona as camadas para baixo e juntas. Como parte desse processo, os pinos são perfurados através da pilha de camadas para garantir que sejam fixados corretamente.
Se as camadas forem fixadas corretamente, a pilha de PCBs é levada para a próxima prensa, uma prensa de laminação. A prensa de laminação usa um par de placas aquecidas para aplicar calor e pressão à pilha de camadas. O calor das placas derrete o epóxi dentro do prepeg - ele e a pressão da prensa se combinam para fundir a pilha de camadas de PCB.
Uma vez que as camadas de PCB são pressionadas juntas, há um pouco de desempacotamento que precisa ser feito. O técnico precisa remover a placa de pressão superior e os pinos anteriores, o que permite que eles puxem a PCB real.
Solicite um orçamento gratuito
Passos nove:Perfuração
Antes da perfuração, uma máquina de raios X é usada para localizar os pontos de perfuração. Em seguida, os furos de registro/guia são perfurados para que a pilha de PCB possa ser protegida antes que os furos mais específicos sejam perfurados. Quando chega a hora de fazer esses furos, uma broca guiada por computador é usada para fazer os próprios furos, usando a lima do projeto Extended Gerber como guia.
Quando a perfuração estiver concluída, qualquer cobre adicional que sobrar nas bordas é lixado.
Dez etapas:Chapeamento de PCB
Depois que o painel for perfurado, ele estará pronto para ser chapeado. O processo de galvanização usa um produto químico para fundir todas as diferentes camadas do PCB. Depois de bem limpo, o PCB é banhado em uma série de produtos químicos. Parte desse processo de banho reveste o painel com uma camada de cobre de mícron de espessura, que é depositada sobre a camada superior e nos orifícios que acabaram de ser perfurados.
Antes de os furos serem preenchidos com cobre, eles servem apenas para expor o substrato de fibra de vidro que compõe o interior do painel. O banho desses furos em cobre cobre as paredes dos furos previamente perfurados.

Passo 11:imagem da camada externa
No início do processo (Passo Quatro), um fotorresistente foi aplicado ao painel PCB. No Passo Onze, é hora de aplicar outra camada de fotorresistente. No entanto, desta vez, o fotorresistente é aplicado apenas na camada externa, pois ainda precisa ser fotografado. Uma vez que as camadas externas foram revestidas com fotorresistência e imagens, elas são revestidas exatamente da mesma maneira que as camadas internas do PCB foram revestidas na etapa anterior. No entanto, embora o processo seja o mesmo, as camadas externas recebem um revestimento de estanho para ajudar a proteger o cobre da camada externa.
Etapa Doze:Gravação da Camada Externa
Quando chega a hora de gravar a camada externa pela última vez, o protetor de estanho é usado para ajudar a proteger o cobre durante o processo de gravação. Qualquer cobre indesejado é removido usando o mesmo solvente de cobre anterior, com o estanho protegendo o cobre valioso da área de gravação.
Uma das principais diferenças entre a gravação da camada interna e externa abrange as áreas que precisam ser removidas. Enquanto as camadas internas usam tinta escura para áreas condutoras e tinta transparente para superfícies não condutoras, essas tintas são invertidas para as camadas externas. Portanto, as camadas não condutoras têm tinta escura cobrindo-as, e o cobre tem tinta clara. Esta tinta leve permite que o estanhamento cubra o cobre e o proteja. Os engenheiros removem o cobre desnecessário e qualquer revestimento de resistência remanescente durante a gravação, preparando a camada externa para AOI e mascaramento de solda.
Etapas Treze:AOI da Camada Externa
Tal como acontece com a camada interna, a camada externa também deve passar por inspeção óptica automatizada. Essa inspeção óptica garante que a camada atenda aos requisitos exatos do projeto. Ele também verifica se a etapa anterior removeu todo o cobre extra da camada para criar uma placa de circuito impresso funcionando corretamente que não criará conexões elétricas inadequadas.

Etapas quatorze:aplicação de máscara de solda
Os painéis requerem uma limpeza completa antes da aplicação da máscara de solda. Depois de limpo, cada painel tem uma película de tinta epóxi e máscara de solda cobrindo a superfície. Em seguida, a luz ultravioleta atinge as placas para indicar onde a máscara de solda precisa ser removida.
Uma vez que os técnicos retiram a máscara de solda, a placa de circuito entra em um forno para curar a máscara. Esta máscara fornece ao cobre da placa uma proteção extra contra danos causados por corrosão e oxidação.
Etapa Quinze:Aplicação Silkscreen
Como os PCBs precisam ter informações diretamente na placa, os fabricantes devem imprimir dados vitais na superfície da placa em um processo conhecido como aplicação de serigrafia ou impressão de legenda. Essas informações incluem o seguinte:
- Números de identificação da empresa
- Etiquetas de aviso
- Marcas ou logotipos dos fabricantes
- Números de peça
- Localizadores de pinos e marcas semelhantes
Depois de imprimir as informações acima nas placas de circuito impresso, geralmente com uma impressora a jato de tinta, as PCBs têm seu acabamento superficial aplicado. Em seguida, seguem para as fases de teste, corte e inspeção.

Etapa Dezesseis:Finalizando o PCB
O acabamento do PCB requer revestimento com materiais condutores, como os seguintes:
- Prata de imersão: Baixa perda de sinal, sem chumbo, compatível com RoHS, o acabamento pode oxidar e manchar
- Ouro duro: Durável, longa vida útil, compatível com RoHS, sem chumbo, caro
- Ouro de imersão em níquel sem eletrodo (ENIG): Um dos acabamentos mais comuns, longa vida útil, compatível com RoHS, mais caro que outras opções
- Nivelamento de solda de ar quente (HASL): Econômico, duradouro, retrabalhável, contém chumbo, não compatível com RoHS
- HASL sem chumbo: Econômico, sem chumbo, compatível com RoHS, retrabalhável
- Lata de imersão (ISn): Popular para aplicações de encaixe por pressão, tolerâncias apertadas para furos, compatível com RoHS, o manuseio do PCB pode causar problemas de solda, bigodes de estanho
- Conservante orgânico de soldabilidade (OSP): Compatível com RoHS, econômico e com vida útil curta
- Ouro de imersão de paládio sem eletrodo de níquel sem eletrodo (ENEPIG ):Alta resistência da solda, reduz a corrosão, requer um processamento cuidadoso para um desempenho adequado, menos econômico do que as opções que não usam ouro ou paládio
O material correto depende das especificações do projeto e do orçamento do cliente. No entanto, a aplicação de tais acabamentos cria uma característica essencial para o PCB. Os acabamentos permitem ao montador montar componentes eletrônicos. Os metais também cobrem o cobre para protegê-lo da oxidação que pode ocorrer com a exposição ao ar.
Solicite um orçamento gratuito
Etapa Dezessete:Teste de Confiabilidade Elétrica
Após o revestimento e cura da PCB (se necessário), um técnico realiza uma bateria de testes elétricos nas diferentes áreas da PCB para garantir a funcionalidade. Os testes elétricos devem seguir os padrões da IPC-9252, Diretrizes e requisitos para testes elétricos de placas impressas não preenchidas. Os principais testes realizados são os testes de continuidade e isolamento do circuito. O teste de continuidade do circuito verifica se há desconexões na PCB, conhecidas como “aberturas”. Por outro lado, o teste de isolamento do circuito verifica os valores de isolamento das várias partes do PCB para verificar se há algum curto. Embora os testes elétricos existam principalmente para garantir a funcionalidade, eles também funcionam como um teste de quão bem o projeto inicial da PCB resistiu ao processo de fabricação.
Além dos testes básicos de confiabilidade elétrica, existem outros testes que podem ser usados para determinar se uma PCB está funcionando. Um dos principais testes usados para fazer isso é conhecido como teste do “cama de pregos”. Durante este texto, vários dispositivos de mola são fixados nos pontos de teste na placa de circuito. Os dispositivos de mola submetem os pontos de teste na placa de circuito com até 200g de pressão para ver como o PCB resiste ao contato de alta pressão em seus pontos de teste.
Se o PCB passou em seu teste de confiabilidade elétrica - e em qualquer outro teste que o fabricante optar por implementar - ele pode ser movido para a próxima etapa:roteamento e inspeção.
Etapa dezoito:criação de perfil e saída de rota
A criação de perfis exige que os engenheiros de fabricação identifiquem a forma e o tamanho das placas de circuito impresso individualmente cortadas da placa de construção. Essas informações normalmente estão nos arquivos Gerber do projeto. Esta etapa de criação de perfil orienta o processo de roteamento programando onde a máquina deve criar as pontuações na placa de construção.
O roteamento, ou pontuação, permite uma separação mais fácil das placas. Um roteador ou máquina CNC cria várias peças pequenas ao longo das bordas da placa. Essas bordas podem permitir que a placa se quebre rapidamente sem danos.
No entanto, alguns fabricantes podem optar por usar uma ranhura em V. Esta máquina criará cortes em forma de V ao longo das laterais da placa.
Ambas as opções para marcar os PCBs permitirão que as placas se separem de forma limpa sem que as placas rachem. Depois de marcar as placas, os fabricantes as quebram da placa de construção para movê-las para a próxima etapa.
Etapa Dezenove:Verificação de Qualidade e Inspeção Visual
Depois de marcar e quebrar as placas, o PCB deve passar por uma inspeção final antes de embalar e enviar. Esta verificação final verifica vários aspectos da construção das placas:
- Os tamanhos dos furos devem corresponder em todas as camadas e atender aos requisitos do projeto.
- As dimensões da placa devem estar alinhadas às especificações do projeto.
- Os fabricantes devem garantir a limpeza para que as placas não tenham poeira.
- As placas acabadas não podem ter rebarbas ou bordas afiadas.
- Todas as placas que falharam nos testes de confiabilidade elétrica devem ser reparadas e testadas novamente.
Etapa Vinte:Embalagem e Entrega
A última etapa da fabricação de PCB é a embalagem e a entrega. A embalagem normalmente envolve material que veda as placas de circuito impresso para impedir a entrada de poeira e outros materiais estranhos. As placas seladas vão então para recipientes que as protegem de danos durante o transporte. Por último, eles saem para entrega aos clientes.
Como implementar um processo de fabricação de PCB eficaz
Muitas vezes, os processos de projeto e fabricação de PCB têm diferentes entidades por trás deles. Em muitos casos, o fabricante contratado (CM) pode fabricar uma placa de circuito impresso com base no projeto criado pelo fabricante do equipamento original (OEM). A colaboração em componentes, considerações de design, formatos de arquivo e materiais de placa entre esses grupos garantirá um processo eficaz e uma transição perfeita entre as fases.
Componentes
O projetista deve consultar o fabricante sobre os componentes disponíveis. Idealmente, o fabricante terá todos os componentes exigidos pelo projeto em mãos. Se algo estiver faltando, o projetista e o fabricante precisarão encontrar um meio-termo para garantir uma fabricação mais rápida e, ao mesmo tempo, atender às especificações mínimas do projeto.
Considerações do Design for Manufacturing (DFM)
O projeto para fabricação considera quão bem o projeto pode progredir através dos vários estágios do processo de fabricação. Muitas vezes, o fabricante, geralmente o CM, terá um conjunto de diretrizes de DFM para suas instalações que o OEM pode consultar durante a fase de projeto. O projetista pode solicitar essas diretrizes do DFM para informar seu projeto de PCB para se adaptar ao processo de produção do fabricante.
Formatos de arquivo
A comunicação entre o OEM e o CM é crucial para garantir a fabricação completa do PCB de acordo com as especificações de projeto do OEM. Ambos os grupos devem usar os mesmos formatos de arquivo para o design. Isso evitará erros ou perda de informações que podem ocorrer nos casos em que os arquivos precisam mudar de formato.
Materiais do Conselho
Os OEMs podem projetar placas de circuito impresso com materiais mais caros do que o CM prevê. Ambas as partes devem concordar com os materiais disponíveis e com o que funcionará melhor para o projeto da placa de circuito impresso, mantendo o custo-benefício para o comprador final.
Entre em contato com a Millennium Circuits para tirar dúvidas
Engenharia de alta qualidade e fabricação de PCBs são componentes críticos das operações das placas de circuito em eletrônica. Compreender as complexidades do processo e por que cada etapa deve ocorrer dá a você uma melhor avaliação do custo e do esforço investido em cada placa de circuito impresso.
Quando sua empresa precisar de PCBs para qualquer trabalho, entre em contato conosco na Millennium Circuits Limited. Trabalhamos para fornecer pequenos e grandes lotes de placas de circuito impresso com preços competitivos para nossos clientes.

Tecnologia industrial
- Placa de circuito impresso
- Os Fundamentos da Fabricação de Placas de Circuito Impresso
- Desgaseificação em uma placa de circuito impresso
- Como testar e corrigir os defeitos da placa de circuito impresso (PCB)?
- Como a fabricação de PCB é tão precisa?
- Técnicas de fabricação de placas de circuito impresso de protótipo
- Por que o processo de fabricação de PCB é tão essencial?
- Por que os conjuntos de placas de circuito são impressos?
- O processo de montagem de uma placa de circuito impresso
- Montagem da placa de circuito – Como é fabricada?