Introdução aos processos de pelotização e pelotização de minério de ferro
Introdução aos processos de pelotização e pelotização de minério de ferro
A pelotização é um processo que envolve a mistura de partículas finamente moídas de finos de minério de ferro com um tamanho inferior a 200 mesh (0,074 mm) com aditivos como bentonita e, em seguida, moldando-os em bolas quase ovais/esféricas com tamanho na faixa de 8 mm a 16 mm de diâmetro por um peletizador e endurecendo as bolas por queima com um combustível. É um processo de aglomeração de conversão de finos de minério de ferro em 'pelotas de minério de ferro de tamanho uniforme' que podem ser carregadas diretamente em um alto-forno (BF) ou em um forno vertical ou forno rotativo normalmente usado para a produção de ferro reduzido direto (DRI) . As pelotas de minério de ferro são mostradas na Fig 1.
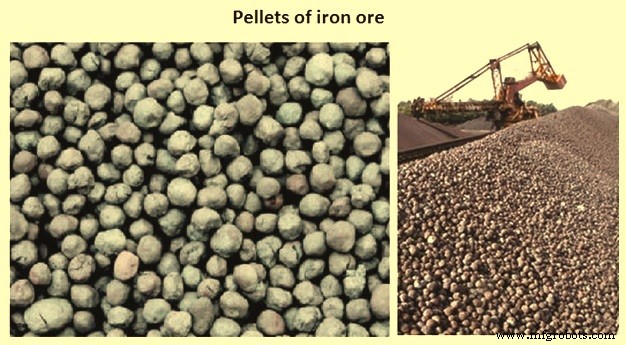
Fig 1 Pelotas de minério de ferro
As propriedades típicas das pelotas de minério de ferro são dadas na Tab 1
Guia 1 Propriedades típicas de pelotas de minério de ferro | |||
Análise química (em base seca) | Unidade | Valor | Tolerância |
Fe | % | 65 | Mínimo |
FeO | % | 0,3 | Máximo |
SiO2 + Al2O3 | % | 5 | Máximo |
CaO | % | 0,03 | ± 0,01 |
MgO | % | 0,06 | ± 0,01 |
Basicidade | % | 65 | Máximo |
Fósforo | % | 0,05 | Máximo |
Propriedades físicas | |||
Densidade de massa | t/cum | 2.2 | ± 0,2 |
Índice do copo | % | 93 | Mínimo |
Índice de abrasão | % | 3 | Mínimo ± 0,5% |
Força de esmagamento a frio (média) | kg/p | 250 | Mínimo |
Análise de tamanho | |||
8 mm – 16 mm | % | 94 | Mínimo |
-5 mm | % | 2 | Máximo |
+16 mm | % | 4 | Máximo |
Propriedades metalúrgicas | |||
Porosidade | % | 18 | Mínimo |
Redutibilidade | % | 62 | Mínimo |
Tecnologia de processo
Existem quatro etapas envolvidas na produção de pelotas de minério de ferro. Essas etapas consistem em (i) preparação da matéria-prima, (ii) formação de bolas verdes ou pellets, (iii) endurecimento dos pellets e (iv) resfriamento, armazenamento e transporte dos pellets.
Preparação da matéria-prima – Durante o processo de pelotização, o concentrado de minério de ferro da planta de beneficiamento de minério de ferro é seco e aquecido a cerca de 120°C. O material seco é alimentado ao moinho de bolas para moagem. Minério de ferro concentrado/moído de tamanho típico 80% menor que 45 mícrons (0,045 mm) com um teor de umidade de cerca de 9% é necessário para a produção de pellets. Aglutinante adequado (normalmente bentonita) é adicionado ao concentrado que é completamente misturado em misturador de alta intensidade.
Formação de bolas verdes ou pellets – Os pellets verdes com uma faixa de tamanho de 8 mm a 16 mm são preparados em um tambor de esferas ou em um peletizador de disco. A peletizadora de disco é preferida para a produção de pellets verdes de qualidade, pois na peletizadora de disco é fácil controlar a operação com o mínimo de espaço para os pés. A peletizadora de disco é uma panela inclinada com cerca de 5 metros (m) a 7,5 m de diâmetro. Ele gira em torno de 6 rpm (rotações por minuto) a 8 rpm. A inclinação do disco é em torno de 45 graus e pode ser ajustado na posição off-line entre 45 graus a 49 graus.
A mistura pré-molhada é alimentada no disco a uma taxa controlada. No disco, o material é coagulado e devido ao movimento rotativo contínuo se forma em nódulos/pellets. Os finos de minério são levantados para cima até que o atrito seja superado pela gravidade e o material rola para baixo até o fundo do disco. Essa ação de rolamento primeiro forma pequenos grânulos chamados sementes. O crescimento ocorre nas revoluções subsequentes do disco pela adição de mais alimentos frescos e pela colisão entre pequenos pellets. À medida que os pellets crescem em tamanho, eles migram para a periferia e para o topo do leito nos discos, até transbordarem a borda. O crescimento do pellet é controlado pela pequena quantidade de água pulverizada no disco e pelo ajuste na velocidade de rotação do disco. Esses pellets são chamados de pellets verdes, pois não têm a força necessária. Os pellets verdes são então peneirados em uma peneira de rolos e o material de tamanho necessário é alimentado na grelha móvel de uma máquina de peletização.
A tensão superficial da água, a ação capilar da água e a força gravitacional no disco de esferas são as forças que atuam sobre as partículas de minério. Assim, eles se unem e formam núcleos que crescem em tamanho e em forma de bola. Essas forças responsáveis pela aglomeração de finos de minério de ferro são geradas no disco de esferogamento devido ao movimento rotacional do disco de esférico. Quando as partículas sólidas entram em contato com a água, a superfície do minério é umedecida e revestida com filme de água. Devido à tensão superficial do filme de água, são formadas pontes líquidas. Como resultado do movimento das partículas dentro do disco de esférico e devido à combinação das gotículas de água individuais contendo grãos de minério, as partículas primeiro se aglomeram. A aglomeração inicial das partículas provoca a formação de sementes. As pontes líquidas no interior dessas sementes mantêm as partículas juntas como se as partículas estivessem em uma rede. Com o fornecimento adicional de água, os aglomerados condensam-se e tornam-se mais densos. As forças capilares das pontes líquidas são mais ativas neste estágio de formação da bola verde. O ótimo desta fase de formação de bolas é atendido quando todas as portas dentro das bolas são preenchidas com líquido. Quando as partículas sólidas são totalmente revestidas com água, a tensão superficial das gotículas de água torna-se totalmente ativa dominando as forças capilares. Além deste efeito, o movimento de rolamento dos grãos e o movimento ou deslocamento das partículas umas em relação às outras também desempenham um papel importante.
Induração – Durante o endurecimento, o endurecimento térmico dos pellets verdes é realizado. A induração de pellets verdes consiste em três etapas principais:(i) secagem de pellets verdes, (ii) queima de pellets em torno de 1300 graus C para sinterizar as partículas de óxido de ferro e (iii) resfriamento de pellets quentes antes da descarga.
Durante a secagem (faixa de temperatura de 180°C a 350°C), o teor de umidade do pellet verde é evaporado. A umidade superficial e intersticial evapora em temperaturas mais baixas, onde a água quimicamente combinada (como goethita ou limonita) ou qualquer combinação de hidrato ou hidróxido perde sua água em temperatura ligeiramente mais alta. Durante a fase de pré-aquecimento (faixa de temperatura de 500 graus C a 1.100 graus C), ocorre a decomposição de carbonatos e hidratos. A gaseificação de combustíveis sólidos como carvão ou coque e a conversão de óxidos de ferro como goethita, siderita e magnetita em hematita em estado de óxido mais alto também ocorre durante este estágio. O início da ligação do óxido sólido e o crescimento do grão são as etapas importantes desta etapa. Durante a fase de queima (faixa de temperatura de 1250°C a 1340°C), a temperatura está abaixo da temperatura de fusão da fase de óxido principal, mas dentro da faixa de reatividade de componentes de ganga e aditivos. A formação de óxidos e ligações de escória é decisiva nesta etapa.
A ligação dos grãos minerais desenvolvidos durante o endurecimento das pelotas é afetada pelos três fatores que consistem em (i) ligação de óxido sólido, (ii) recristalização de óxido de ferro e (iii) ligação de escória. A ligação de óxido sólido é devido à oxidação de óxidos de ferro ferroso em óxidos de ferro férrico, o que resulta em ligação e ponte, mas apenas em uma quantidade limitada. A recristalização de óxidos de ferro é essencialmente um processo físico no qual partículas menores se consolidam em maiores com a perda de energia superficial. Durante a recristalização de óxidos de ferro, o crescimento contínuo de cristais de óxido de ferro confere resistência suficiente. Durante o processo, o crescimento de grãos de hematita começa em torno de 1100 graus C. No caso de ligação de escória, ganga, formando meio de transporte de fusão para óxidos ferrosos ou férricos, facilita o crescimento de grãos e a cristalização de grãos de óxido. Também permite que o mecanismo prossiga a temperaturas mais baixas do que o necessário na sua ausência.
O tratamento de endurecimento provoca a ocorrência de certas reações químicas que alteram as propriedades metalúrgicas específicas dos pellets. Essas reações podem incluir a oxidação da magnetita e a desidratação da hematita terrosa. Para o grau BF, os pellets fluxados são produzidos com adições de calcário, dolomita, sílica, etc. à alimentação do balling. Essas adições reagem com a ganga no minério de ferro para melhorar o desempenho das pelotas em certas etapas de processamento a jusante.
Resfriamento e manuseio de pellets – Os pellets são resfriados e peneirados após o endurecimento. Os pellets superdimensionados são triturados e enviados junto com os subdimensionados para os silos do almoxarifado onde são reprocessados. Os pellets resfriados são enviados para o armazenamento para seu transporte para as plantas a jusante para processamento posterior.
Processos de pelotização
Existem vários processos/tecnologias de pelotização de minério de ferro que estão disponíveis para a produção das pelotas. Alguns deles são (i) processo de forno de cuba, (ii) processo de grelha móvel reta, (iii) processo de forno de grelha, (iv) processos de ligação de cimento (processo Grangcold, processo MIS Grangcold e processo de carvão etc.), e (v) ) processos hidrotérmicos (processo COBO, processo MTU e processo INDESCO etc.). No entanto, atualmente, apenas o processo de grelha móvel reta (STG) e o processo de forno de grelha (GK) são processos mais populares.
Processo de grelha móvel reta
O processo foi desenvolvido pela antiga Lurgi Metallurgie e responde por grandes capacidades instaladas globais. Neste processo, uma peneira de rolos de dois andares garante que o tamanho certo dos pellets verdes (8 mm a 16 mm de tamanho) seja distribuído uniformemente pela largura da grelha móvel. A grelha transporta os pellets verdes em um leito com uma altura na faixa de 300 mm a 550 mm através de um forno com várias zonas. Estas zonas são com updrafting, downdraft secagem, pré-aquecimento, queima, pós-queima e zonas de aquecimento. Um fluxograma do processo é dado na Figura 2.
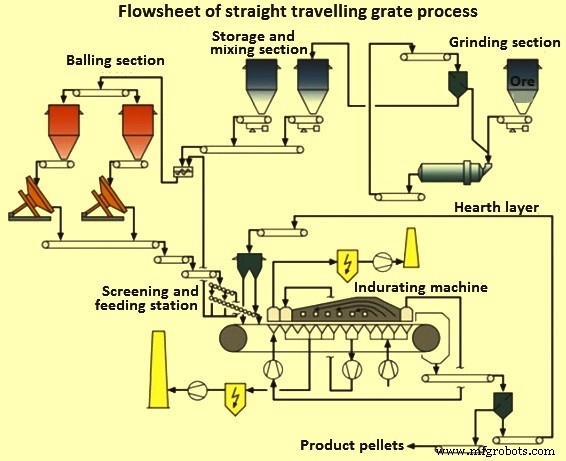
Fig 2 Fluxograma do processo de grelha móvel reta
Processo de forno de grelha
O processo de forno de grelha foi desenvolvido pela ex-Allis Chalmer e a primeira planta com esta tecnologia foi construída em 1960. No processo de forno de grelha (Fig. 3) a grelha móvel é usada para secar e pré-aquecer os pellets. O material se move na grelha reta até atingir a temperatura na faixa de 800 graus C a 1000 graus C. Depois disso, o material é transferido para um forno rotativo revestido de refratário para endurecimento, onde a temperatura é aumentada ainda mais na faixa de 1250 graus C a 1300 graus C. A 800 graus C, o FeO do minério de ferro magnetita é convertido em Fe2O3 em uma reação exotérmica. O calor liberado endurece as bolas verdes, o que ajuda a suportar o impacto da queda devido à rotação do forno rotativo. Um resfriador circular é usado para resfriamento dos pellets queimados. O fluxograma do processo de forno de grelha é dado na Fig 3.
Fig 3 Fluxograma do processo de forno de grelha
Uma comparação dos dois processos é dada na Tab 2.
Tab 2 Comparação entre o processo de grelha móvel reta e o processo de forno de grelha | ||
Sl. No. | Processo de grelha móvel reta | Processo de forno de grelha |
1 | Secagem, pré-aquecimento, endurecimento e ciclo de resfriamento são realizados em uma única unidade | Secagem, pré-aquecimento, induração e ciclo de resfriamento são realizados em diferentes unidades |
2 | Os pellets verdes permanecem intactos durante o processo | Todo o processo ocorre em três equipamentos:grelha móvel, forno rotativo e resfriador circular, portanto, a transferência de pellets ocorre. |
3 | Os carros de grade se movem na mesma velocidade nas zonas de secagem, induração e resfriamento. Qualquer distúrbio em uma zona afeta as outras zonas | Controle independente das três zonas, portanto, o processo tem melhor flexibilidade operacional |
4 | A geração de multas é insignificante, pois não há transferência de materiais | Como a transferência de material ocorre em vários locais, há maior geração de multas |
5 | Não há exigência de força do produto intermediário | Antes de transferir para o forno, os pellets verdes devem estar suficientemente endurecidos |
6 | A disponibilidade do processo é maior | A disponibilidade do processo é menor |
7 | Consumo específico de energia mais alto | Consumo específico de energia mais baixo |
8 | Menor manutenção | Maior manutenção |
9 | Menor geração de poeira | Maior geração de poeira |
10 | Maior custo de investimento | Menor custo de investimento |
11 | Adequado para minérios de hematita e magnetita | O processo é mais adequado para minérios de magnetita. |
Uma comparação da distribuição de temperatura durante os dois processos é mostrada na Fig. 4
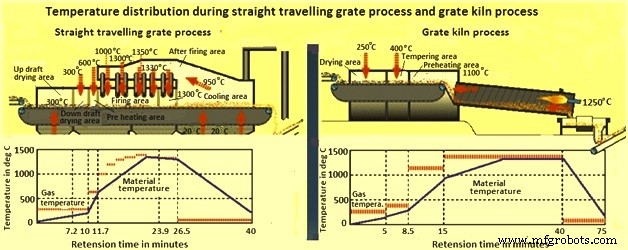
Fig 4 Comparação da distribuição de temperatura durante os dois processos
Vantagens dos pellets
As várias vantagens das pelotas de minério de ferro são apresentadas abaixo.
- Pelota de minério de ferro é um tipo de aglomerado de finos que apresenta melhor índice de tombamento quando comparado ao minério de ferro e pode ser utilizado como substituto dos caroços de minério de ferro tanto no BF quanto na produção de DRI.
- Os pellets têm boa redutibilidade, pois possuem alta porosidade (25% a 30%). Normalmente, os pellets são reduzidos consideravelmente mais rápido do que a sinterização, bem como os pedaços de minério de ferro. A alta porosidade também ajuda na melhor metalização na produção de DRI.
- Os pellets têm um tamanho uniforme geralmente na faixa de 8 mm a 16 mm.
- Os pellets têm formato esférico e poros abertos que lhes conferem boa permeabilidade ao leito.
- Os pellets têm baixo ângulo de repouso, o que é uma desvantagem, pois cria uma distribuição desigual do aglutinante.
- A análise química é uniforme, pois é controlada durante o processo de beneficiamento. O teor de Fe varia na faixa de 63% a 68%, dependendo do teor de Fe dos finos de minério. Ausência de LOI (perda na ignição) é outra vantagem dos pellets.
- Os pellets possuem resistência mecânica elevada e uniforme e podem ser transportados a longas distâncias sem geração de finos. Além disso, tem resistência à desintegração. Alta resistência mecânica e uniforme dos pellets é mesmo sob estresse térmico em atmosfera redutora.
Processo de manufatura
- Uma introdução à fabricação de metal
- Ferro Reduzido Direto e seus Processos de Produção
- Processos FASTMET e FASTMELT de fabricação de ferro
- Beneficiamento de Minérios de Ferro
- Mineração de minérios de ferro
- Uso de Pelotas de Minério de Ferro na Carga do Alto Forno
- Eficiência Energética e Produção de Ferro e Aço
- Introdução às peças fundidas de ferro fundido
- Propriedades e Composição do Ferro Gusa
- Entendendo o processo de fundição de minério de ferro