Utilização de Metal Quente para Siderurgia em Forno a Arco Elétrico
Uso de metal quente para fabricação de aço em forno elétrico a arco
A fabricação de aço pelo forno elétrico a arco (EAF) tem uma flexibilidade muito boa com relação à seleção de materiais de carga. O material de carga tradicional para o processo EAF tem sido 100% sucata fria, mas as questões relacionadas à sucata, como sua disponibilidade e qualidade, flutuações de preços de mercado e restrições impostas pela sucata na fabricação de alguns tipos de aço devido a elementos residuais e nível de nitrogênio, etc. materiais de carga alternativos têm sido usados em porcentagem variável com sucesso pelos operadores de EAF. Os materiais de carga alternativos são ferro reduzido direto (DRI), ferro briquetado a quente (HBI), ferro gusa ou metal quente.
O uso de metal quente é mais popular naquelas áreas onde há escassez de sucata e/ou energia elétrica ou a energia elétrica tem alto custo. A fonte popular de metal quente é o alto-forno, portanto, o metal quente pode ser usado nos EAFs que estão próximos ao alto-forno, caso contrário, o operador do EAF deve usar ferro-gusa. O ferro-gusa precisa de energia extra para seu derretimento. Uma grande variação nas proporções de metal quente e sucata é possível na fabricação de aço EAF. Com operação 100% sucata em uma extremidade da balança; o FAF também pode ser operado com uma carga de apenas 20% de sucata e 80% de metal quente. Existem atualmente muitos EAFs que foram projetados para usar até 80% de metal quente na carga.
A combinação de uma carga de metal quente e sucata ao EAF ajuda a melhorar o desempenho operacional do processo. O metal quente dissolve carbono e silício, que são importantes fontes de calor disponíveis com sua oxidação. O calor de oxidação desses elementos juntamente com o calor sensível disponível no gusa auxilia na redução substancial do consumo de energia durante a fabricação do aço no EAF. Além disso, o metal quente está livre de materiais não metálicos estranhos que foram removidos como escória durante o processo de fabricação de ferro. No entanto, os operadores de EAF são obrigados a cuidar da forte reação que ocorre no forno devido ao carbono no metal quente. O metal quente pode ser carregado de maneira controlada para cuidar do teor de carbono no banho de metal líquido no forno.
Os principais benefícios associados ao carregamento de metal quente no EAF incluem maior produtividade, melhor formação de espuma de escória e maior teor de carbono na carga. A alta pureza e baixo teor de ganga do metal quente permite a produção daqueles produtos de aço que precisam de baixo teor residual. Além disso, o metal quente tem uma química conhecida e consistente certificada por análise e isso compensa as amplas flutuações químicas comuns com o uso de sucata obsoleta.
A energia química contida no metal quente é fornecida de forma eficiente pelo carbono contido, o que promove uma fusão mais rápida e maior produtividade. O metal quente é extremamente benéfico para aumentar a produtividade do EAF e alcançar tempos curtos entre as torneiras, desde que o projeto do forno não restrinja a taxa de descarbonetação. O metal quente também permite uma flexibilidade considerável na seleção de sucata. Devido ao baixo teor residual do gusa, é possível utilizar sucata de baixa qualidade quando maior proporção de gusa é utilizada no EAF.
O metal quente oferece benefícios semelhantes ao ferro-gusa, com o benefício adicional de que o material já está a uma temperatura de cerca de 1.300 graus C ou superior. Assim, a maior parte da necessidade de energia no EAF (necessária para fundir o Fe) já está fornecida. Uma tonelada de metal quente a 1.430 graus C fornece cerca de 250 kWh na forma de calor sensível, com base apenas no teor de Fe. Para o uso de ferro-gusa no EAF, a economia típica de energia está normalmente na faixa de 3,1 kWh/% de ferro-gusa a 3,6 kWh/% de ferro-gusa. O uso de metal quente aumenta a economia para 4,8 kWh/por cento de metal quente. O uso de grandes quantidades de metal quente pode diminuir o consumo de energia para o nível de 200 kWh por tonelada de metal quente e, portanto, pode ser muito benéfico para locais com uma rede elétrica fraca.
Influência do HM nos principais parâmetros do processo EAF
Nos últimos tempos, a principal ênfase na fabricação de aço EAF tem sido relacionada à obtenção da máxima eficiência energética. Além disso, os materiais de carga de alimentação estão influenciando o projeto do EAF e sua prática de operação. A influência do HM como material de carga em vários parâmetros-chave de um processo EAF de fabricação de aço é detalhada abaixo.
Elementos residuais – Elementos residuais, também conhecidos como elementos residuais, não podem ser removidos do aço durante o processamento. Assim, a quantidade desses elementos no produto é uma função direta da quantidade desses elementos carregados no processo siderúrgico por meio de materiais de carga. Altos níveis de elementos residuais podem afetar as operações de fundição e laminação, além de afetar a qualidade do produto. Ao adicionar HM, que é uma unidade de ferro limpo, na mistura de carga o nível de elementos residuais no aço líquido pode ser reduzido a níveis aceitáveis através do processo de diluição.
Nível de nitrogênio no aço – O nitrogênio é geralmente considerado como uma impureza indesejável que causa fragilização nos aços e afeta o envelhecimento por deformação. O nitrogênio no aço líquido está presente na forma de solução. Durante a solidificação do aço em lingotamento contínuo, o nitrogênio é a principal razão para a formação de furos. O metal quente por causa de seus níveis mais baixos de nitrogênio fornece um efeito de diluição e também resulta na geração de gás de monóxido de carbono (CO) dentro do banho de aço através da fervura C, o que leva ainda à redução do teor de nitrogênio no aço.
Remoção de hidrogênio – O gás CO liberado durante o processo de descarbonetação auxilia na remoção do hidrogênio. Foi demonstrado que a descarbonetação a uma taxa de 1% por hora pode reduzir os níveis de hidrogênio no aço de 8 ppm para 2 ppm em 10 minutos.
Influência na produtividade e outros parâmetros operacionais – Com o uso de HM na mistura de carga há maior consumo de oxigênio o que auxilia na melhoria da produtividade do EAF, em menor tempo de tap to tap, melhor rendimento de Fe e redução no consumo específico de energia. Com o uso de HM na mistura de carga, a economia está na faixa de 4 kWh por % de metal quente a 8 kWh por % de metal quente na carga. A Fig. 1 mostra a relação da produtividade e consumo específico de energia com a porcentagem de gusa na carga do EAF.
Fig 1 Relação entre o metal quente responsável com o consumo de energia e a produtividade
Papel do carbono – Durante a fabricação de aço em EAF, o carbono é necessário para reagir com o oxigênio e o óxido de ferro para ajudar na formação de espuma de escória. Algum carbono também é necessário para atender aos requisitos do produto. O carbono também é carregado no EAF para reagir no banho com o oxigênio injetado para produzir gás CO, bem como fornecer energia química suficiente para economizar o consumo de energia elétrica. A geração de gás CO dentro do banho ajuda a obter baixa concentração de gases dissolvidos no aço. As bolhas de gás CO também ajudam na formação de espuma de escória (criam uma emulsão) que ajuda a conter o arco elétrico e melhorar a transferência de energia para o banho de aço em vez de para o casco do forno e transferência para o banho por energia de radiação. As eficiências de transferência sob várias condições de escória são fornecidas na Tab 1.
Tab1 Tipo de arco e eficiência de transferência de energia elétrica | ||
Sl. n.º | Tipo de arco | % de eficiência de energia elétrica |
1 | Gravação livre | 26 |
2 | Parcialmente cercado por escória espumante | 65 |
3 | Totalmente cercado por escória espumante | 93 |
4 | Aquecimento por resistência parcial | 97 |
5 | Aquecimento por resistência total | 100 |
Pode-se observar que a imersão total do arco elétrico na escória espumante tem enorme efeito positivo na transferência de energia. Assim, as perdas de calor através de radiações podem ser reduzidas. A quantidade total de adição de carbono necessária na operação do EAF depende de vários fatores, a saber (i) teor de carbono dos materiais de alimentação (ii) nível planejado de consumo de oxigênio (iii) nível de carbono desejado (iv) economia do rendimento de Fe em comparação com o custo do carbono e (v) capacidade do sistema de gases de escape. O carbono é normalmente adicionado no EAF na forma de carvão ou coque que possui um teor de cinzas que é um material indesejado na fabricação de aço. O metal quente tem carbono na faixa de 3,8% a 4,5%. Portanto, o uso de metal quente economiza muito custo quando comparado com a adição de carbono ao banho de fontes externas.
Devido à recuperação errática de carga de carbono no EAF, muitos operadores de EAF recorreram a materiais de alimentação com alto teor de carbono, como ferro-gusa ou metal quente, etc., como forma de reduzir as variações nas operações de fabricação de aço. Quando grandes quantidades de ferro-gusa ou metal quente são usadas, não é necessário adicionar carga de carbono. Cada 1% de metal quente na carga fornece 0,435 kg por tonelada de carbono de carga (assume-se 4% C em metal quente e 92% de rendimento de sucata). Assim, 20% de metal quente na carga fornece o equivalente a quase 9 kg por tonelada de carga de carbono. A recuperação do carbono contido nas matérias-primas metálicas é muito alta (tipicamente 90% a 100%). Quando a recuperação aprimorada de carbono é levada em consideração, essa quantidade de metal quente pode substituir 10 kg por tonelada de carvão de carga para 60 kg por tonelada de carvão de carga.
Recursos de design – A questão-chave da EAF é sua capacidade de descarbonetação. O alto teor de carbono na carga requer tempo adicional para descarbonetação. A EAF não pode utilizar taxas de injeção de oxigênio que são típicas da prática de fabricação de aço BOF. A participação de metal quente superior a 40% foi considerada como um limite máximo acima do qual a produtividade do EAF é reduzida devido à capacidade insuficiente de injeção de oxigênio. No entanto, atualmente estão disponíveis EAFs projetados para usar até 80% de metal quente.
Os limites de injeção de oxigênio nos EAFs de projeto normal geralmente estão relacionados a problemas com extensos fenômenos de respingos, retorno de chama, aumento do consumo de eletrodos e erosão do revestimento refratário, bem como redução da vida útil dos painéis do telhado e da peça central delta refratária. As taxas típicas de descarbonetação em EAFs de projeto normal variam de 0,06% a 0,1%. Um nível de carbono muito alto nos materiais de carga de alimentação em tais EAFs pode aumentar o tempo de toque a toque devido a essa limitação. A relação típica entre a taxa de descarbonetação e a carga de metal quente nos materiais de carga EAF é mostrada na Fig 2.
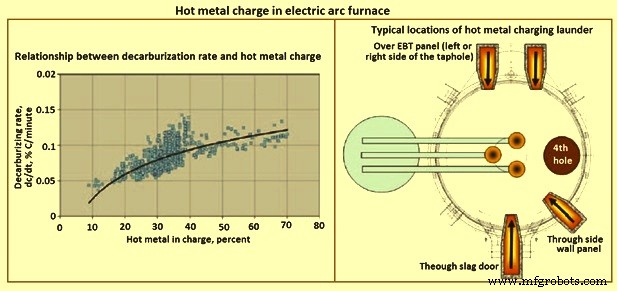
Fig 2 Carga de metal quente em forno elétrico a arco
Comparação com teor de carbono de DRI e/ou HBI – Além disso, no caso de DRI/HBI (material de alimentação EAF), o carbono também é necessário para reduzir o óxido de ferro presente no DRI e/ou HBI. Isso aumenta a necessidade de carbono de carga. No caso do gusa tal exigência não existe, pois o gusa está tendo 100% de metalização.
Conteúdo de silício e manganês de metal quente – O metal quente contém uma quantidade substancial de silício e manganês. Esses elementos quando oxidados fornecem energia química que reduz ainda mais o consumo de energia elétrica. Além disso, esses óxidos sendo de natureza ácida aumentam o consumo de fluxo (CaO e MgO) para manter o nível necessário de basicidade da escória no banho do forno.
Carregamento de metal quente
O carregamento de metal quente para o EAF parece uma proposta simples, embora na verdade seja bastante complexa. O carregamento de metal quente em um EAF requer cuidados extras, pois o contato com escória de forno altamente oxidada ou sucata fria pode resultar em reações violentas. A perda de controle durante o carregamento de metal quente pode resultar em transbordamento de escória e metal do EAF. Reações violentas semelhantes normalmente acontecem quando grandes gradientes de concentração de carbono se desenvolvem no banho líquido durante a fase de superaquecimento. A perda de controle durante o carregamento de metal quente acaba com o transbordamento de escória e aço do forno. Em casos extremos, também são observados danos nos braços dos eletrodos durante erupções violentas no forno.
O carregamento de metal quente pode ser feito em dois locais, através do telhado ou da porta de escória. Algumas fábricas carregam metal quente no EAF balançando o telhado e despejando-o na fornalha. Isso causa uma mistura muito rápida do metal quente com a escória altamente oxidada no EAF e, às vezes, devido a isso, ocorrem explosões. Portanto, para este modo de operação, é recomendado que um desoxidante de escória seja adicionado antes da adição de metal quente. Desoxidantes típicos são finos de silício, finos de alumínio e carboneto de cálcio.
Os pontos importantes durante o carregamento de metal quente no EAF são (i) o carregamento de metal quente deve ser realizado com a energia ligada para evitar perdas de produtividade, (ii) o controle de inclinação da panela de metal quente deve ser preciso o suficiente para garantir taxas de vazamento estáveis , (iii) o canal de metal quente deve ser o mais curto possível para evitar o congelamento do metal quente, e (iv) o canal deve ser pré-aquecido entre as operações de vazamento.
Para aproveitar a vantagem da temperatura do metal quente, seu carregamento no forno deve ser feito com um teto fechado. O método alternativo de carregar o metal quente no EAF é despejá-lo em uma lavadora que é inserida na lateral do EAF. Este método requer mais tempo para carregar o metal quente, mas resulta em uma operação muito mais segura.
Normalmente, os problemas de limitações logísticas e de layout não deixam muita liberdade para selecionar o local onde as panelas de metal quente podem ser entregues à oficina do EAF, ou seja, no lado de carregamento ou rosqueamento do forno. O próprio projeto EAF impõe limitações adicionais. A posição do transformador, exaustão de gases, etc. limitam seriamente o espaço disponível, onde o canal de metal quente pode ser inserido no forno e o posicionamento real do canal é um compromisso entre várias considerações. As soluções típicas são dadas na Fig2. O corredor inserido através da porta de escória deve ser móvel (por meio de um carro de carregamento de metal quente dedicado). Em outras posições, o corredor pode ser fixado na carcaça do forno ou no carro de carregamento.
A desvantagem mais séria do carregamento da porta de escória é o vazamento de metal quente contra o fluxo de escória. Em alguns casos, isso pode resultar em má remoção de fósforo do banho. Além disso, o vazamento só pode ser iniciado depois que a área atrás da porta de escória estiver livre de escória. A posição da parede lateral do corredor é problemática em caso de transbordamento de metal quente. Nesse local, é difícil recolher o metal derramado. Além disso, qualquer transbordamento cria um risco para todas as tubulações instaladas na área vizinha. O corredor localizado na varanda do EBT parece ser o mais vantajoso. Devido à presença limitada de sucata nessa área, o carregamento de metal quente pode ser iniciado muito cedo. Em caso de transbordamento, o metal quente pode ser coletado no poço de drenagem abaixo do forno.
A maioria das operações modernas injeta oxigênio em vários locais em vez de usar a única lança de porta de escória. Sob esta condição, foi estabelecido que a carga de metal quente de 30% a 40% é mais adequada para EAFs. O carregamento de metal quente de até 50% foi usado com sucesso em alguns dos EAFs. No entanto, uma carga de metal quente superior a 50% resulta em problemas operacionais, pois o calor excessivo é gerado pela oxidação de elementos, como carbono, manganês e silício, o que pode levar ao superaquecimento dos fornos.
Com os novos avanços no EAF e na tecnologia de processo, a remoção de carbono em alta velocidade do metal quente pode ser alcançada no EAF sem perder rendimento ou sobrecarregar o sistema de gás de saída. À medida que a tecnologia EAF evoluiu, a utilização econômica do metal quente na EAF aumentou de um máximo de 50% para até 80%. A plena utilização do conteúdo de energia do metal quente pode agora ser alcançada.
Processo de manufatura
- 5 casos de uso inovadores para impressão 3D de metal
- Forno de indução e siderurgia
- Uso de Nut Coke em um Alto Forno
- Forno de arco elétrico DC
- Uso de Ferro Reduzido Direto em Forno a Arco Elétrico
- Química da Siderurgia por Forno Básico de Oxigênio
- Processo CONARC para Siderurgia
- Areia de fundição para uso industrial
- Por que usar um cortador a laser de metal?
- Como usar um torno de metal – para iniciantes