Processos FASTMET e FASTMELT de fabricação de ferro
Processos FASTMET e FASTMELT de fabricação de ferro
O processo FASTMET é um processo de fabricação de ferro à base de carvão. Permite a conversão de óxidos metálicos de finos de minério de ferro ou resíduos metalúrgicos de siderurgia, em ferro metalizado. O processo FASTMELT é o processo FASTMET com a adição de um "forno elétrico de fusão de ferro" (EIF) para produzir ferro líquido ou metal quente. A Kobe Steel em colaboração com a Midrex Technologies, Inc., uma subsidiária da Kobe Steel nos EUA, desenvolveu este processo. FASTMET é um processo único que utiliza um forno rotativo (RHF) para reduzir aglomerados contendo carvão com uma alta taxa de redução e alta produtividade. A Fig. 1 mostra uma seção transversal simplificada e uma vista plana de um RHF.
Fig 1 Seção transversal simplificada e vista plana de um RHF
O processo FASTMET converte pellet feed de minério de ferro, finos de minério de ferro e/ou resíduos metalúrgicos de siderurgia em ferro reduzido direto (DRI) usando carvão pulverizado não coqueificável como redutor. O produto final DRI pode ser briquetado a quente para produzir ferro briquetado a quente (HBI), ou descarregado como DRI quente em recipientes de transferência, ou resfriado se for necessário DRI frio. O DRI quente é descarregado diretamente do RHF no EIF e é fundido para produzir metal quente. O metal quente pode ser fundido em ferro gusa. O ferro reduzido / metal quente pode ser alimentado em um forno primário de fabricação de aço.
Além de facilitar a reciclagem dos resíduos metalúrgicos para alimentação do forno básico de oxigênio/forno elétrico a arco, existem dois grandes alvos do processo. Uma delas é a maior metalização dos óxidos de ferro, o que reduz a carga no processo de fusão. Outra é a alta taxa de remoção de zinco, que reduz a concentração de zinco dentro do ciclo de reciclagem. Para alimentação de alto-forno, é necessária alta resistência à compressão, que também é alcançada ajustando o ligante e a proporção de mistura de matérias-primas com o processo FASTMET.
Desenvolvimento histórico
A redução do minério de ferro em um RHF foi tentada pela primeira vez pela Midland Ross Co., precursora da Midrex Technologies, Inc. O processo, chamado 'Heat Fast', foi o único que envolveu pelotas compostas, consistindo de minério de ferro e material carbonáceo, que são pré-aquecidos em uma grelha, pré-reduzidos em um RHF e resfriados em um resfriador de eixo. O processo 'Heat Fast' foi testado com sucesso na planta piloto de 2 toneladas por hora (tph) em Cooley, Minnesota, de 1965 a 1966.
Simultaneamente ao desenvolvimento do 'Heat Fast', também estava sendo desenvolvido o processo Midrex DRI baseado em gás natural, que oferecia um produto de qualidade superior ao 'Heat Fast' e custos operacionais mais baixos (o gás natural tinha um preço muito baixo na época). Devido aos então baixos custos operacionais do processo de gás natural, o trabalho do processo 'Heat Fast' foi interrompido e o desenvolvimento comercial nunca foi realizado.
Midrex reviveu seu interesse em usar o RHF para redução direta no início de 1980. Vários estudos foram conduzidos que indicaram que um processo baseado em RHF poderia ser desenvolvido para produzir ferro reduzido direto a um preço atraente. Na década de 1990, o preço do gás natural subiu e, em seguida, uma planta piloto FASTMET foi construída e comissionada no centro técnico Midrex com um RHF de 2,75 m de diâmetro e capacidade de produção de 160 quilos por hora. Mais de 100 campanhas foram realizadas de 1992 a 1994.
Kobe Steel e Midrex Technologies, Inc. colaboraram para reiniciar o desenvolvimento de um processo baseado em carvão RHF com a intenção de comercializar a tecnologia. Com base no trabalho da planta piloto “Heat Fast” que remonta à década de 1960, foram feitas melhorias na tecnologia que resultaram em maior produtividade, melhor qualidade do produto, maior flexibilidade do processo e maior eficiência do processo. O resultado final foi o desenvolvimento do processo FASTMET. A Kobe Steel e a Midrex levaram o processo FASTMET um passo adiante no desenvolvimento do processo FASTMELT, que precisa da descarga quente de DRI do RHF e carregamento por gravidade em um EIF, um forno de fusão projetado especificamente para fundir FASTMET hot DRI para produzir metal quente.
Uma planta piloto de demonstração foi construída em 1995 na fábrica de Kakogawa da Kobe Steel limited (KSL). A planta tinha 8,5 m de diâmetro RHF e uma capacidade de produção de 2,5 tph. A planta esteve em operação contínua de 1995 a 1998. Por meio de várias operações de demonstração realizadas lá, a Kobe Steel e a Midrex Technologies, Inc. estabeleceram o processo FASTMET para comercialização. Em 2000, uma primeira planta comercial FASTMET foi fornecida às fábricas de Hirohata da Nippon Steel Company (NSC) para reduzir 190.000 toneladas por ano (tpa) de resíduos siderúrgicos. O processo FASTMET foi reconhecido por sua capacidade de reciclar com eficiência o pó de ferragens. Os detalhes das primeiras cinco plantas que foram comissionadas são fornecidos na Tab 1.
Aba 1 FASTMET plantas comerciais | ||||||
Unidade | NSC Hirohata nº 1 | NSC Hirohata nº 2 | NSC Hirohata nº 3 | JFE Steel, Fukuyama | KSL Kakogawa | |
Taxa de alimentação RHF | tpa | 190.000 | 190.000 | 190.000 | 190.000 | 16.000 |
Matérias-primas | Poeira BOF | poeira BOF | poeira BOF | pó BF, pó BOF | poeira BF, poeira BOF, poeira EAF | |
Aplicação do produto | alimentação BOF, DRI | alimentação BOF, DRI | alimentação BOF, HBI | alimentação BOF, DRI | feed BF e BOF, DRI | |
Diâmetro externo RHF | m | 21,5 | 21,5 | 21,5 | 27 | 8,5 |
Data de comissionamento | abril de 2000 | janeiro de 2005 | Dezembro de 2008 | abril de 2009 | abril de 2001 |
Pode-se observar que este processo está sendo utilizado atualmente para o aproveitamento dos resíduos metalúrgicos da siderurgia. Além do resíduo metalúrgico, o processo também pode utilizar finos de minério de ferro com tamanho igual ao tamanho do pellet feed (inferior a 45 micrômetros). Isso ocorre porque o processo possui etapas de aglomeração embutidas. O processo FASTMET/FASTMELT apresenta uma rota alternativa para a fabricação de ferro em capacidades que variam de 100.000 tpa a 500.000 tpa. O processo FASTMELT oferece uma alternativa para a tecnologia de mini alto-forno (BF). Os refratários usados em RHF e EIF são de especificação padrão normalmente usados na fabricação de ferro. O projeto do EIF é baseado em projetos comprovados das tecnologias EAF (forno elétrico a arco) e LF (forno panela).
Recursos do processo FASTMET
O processo FASTMET é claramente diferente do processo de redução baseado em gás usando gás reformado produzido a partir de gás natural, pois aquece e reduz aglomerados compostos, cada um consistindo de minério de ferro ou resíduos metalúrgicos de usinas siderúrgicas e carvão. Este processo simples e único envolvendo aquecimento rápido realiza uma reação de redução rápida. Os aglomerados são colocados em uma ou duas camadas uniformes sobre a lareira e são aquecidos usando calor de radiação. Isso evita a oxidação dos aglomerados, apesar da condição no forno dos gases de escape da combustão, que tem um potencial de oxidação considerável.
O processo pode atingir o aquecimento e a redução dos aglomerados simultaneamente e efetivamente em uma relação ar-gás ideal no RHF. Além disso, o gás combustível gerado a partir do carbono nos aglomerados queima em combustão secundária acima deles. Isso suprime consideravelmente a emissão de NOx, apesar do RHF ser um forno que possui um ambiente de alta temperatura. Esta é outra característica do processo FASTMET.
À medida que a fornalha do RHF gira, os pellets ou briquetes passam por três zonas e são aquecidos rapidamente. Cada zona possui três queimadores a gás, cuja relação ar/combustível pode ser ajustada para obter a combustão pobre ou rica desejada em cada zona. No final da zona 3, o material passa por baixo de uma parede divisória que separa a zona de queima final da zona de descarga. Um parafuso helicoidal transporta o produto DRI quente da fornalha para uma calha desviadora e, em seguida, por gravidade, para um recipiente de produto DRI purgado com nitrogênio ou para um EIF.
Um trocador de calor instalado no equipamento de tratamento dos gases de escape converte a energia contida nos gases de escape de alta temperatura em energia para aquecer o ar que é usado para queima ou secagem das matérias-primas. Isso reduz o consumo geral de energia.
Matérias-primas, como poeira de usinas siderúrgicas, podem ocasionalmente gerar dioxinas à medida que queimam. No processo FASTMET, no entanto, a temperatura RHF é de 1.300 graus C ou superior, que é alta o suficiente para suprimir a geração de dioxinas. O gás de exaustão do RHF é resfriado rapidamente através da região de temperatura na qual a dioxina pode se recombinar, evitando assim sua recomposição. A Fig. 2 mostra um fluxograma típico do processo FASTMET / FASTMELT.
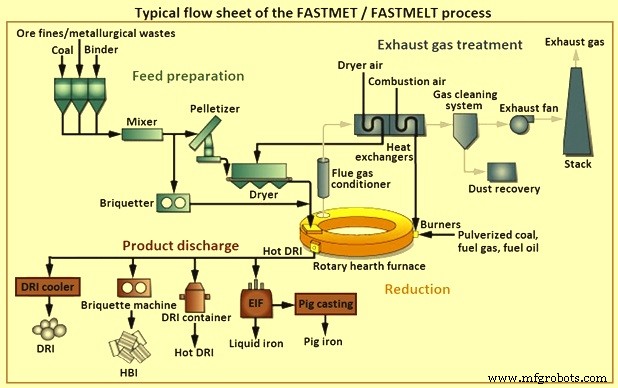
Fig 2 Fluxograma típico do processo FASTMET / FASTMELT
O gás quente que sai do RHF é resfriado por meio de um resfriador evaporativo antes de entrar em um trocador de calor. O calor sensível no gás de exaustão é usado para pré-aquecer o ar de combustão RHF e o ar do secador de bolas verdes para cerca de 350 graus C. O gás de exaustão que sai do pré-aquecedor é ainda resfriado por um segundo resfriador evaporativo antes de entrar em um compartimento de mangas, onde o o óxido de zinco é recuperado e enviado para o silo de pó para armazenamento. Um ventilador de tiragem induzida é posicionado na saída do compartimento de mangas para atingir a queda de pressão necessária para o sistema de gases de escape e controlar o RHF sob uma pressão ligeiramente negativa.
Os utilitários necessários são o ar da planta, nitrogênio, vapor, ar de instrumentos, água de reposição e gás natural liquefeito. A planta também precisa de um circuito aberto de recirculação de água de processo, bem como um circuito fechado de água de resfriamento de máquinas.
O DRI quente, descarregado do RHF, tem três opções de descarga, a saber (i) resfriado para produzir DRI frio, (ii) briquetado em uma máquina de briquete para produzir HBI, (iii) fundido em um EIF para produzir ferro líquido. Este ferro líquido pode ser fundido em um fundidor de gusa para produzir ferro gusa.
O DRI tem muitos poros deixados após o processo de redução. Se exposto ao ar por muito tempo, o ferro metálico reoxida em óxido de ferro, deteriorando sua qualidade. Se o DRI não for usado imediatamente como matéria-prima para um forno de fusão ou alto-forno, compactar e densificar o DRI em ferro briquete quente (HBI) evita a reoxidação. Isso permite o armazenamento de ferro reduzido por um longo período de tempo sem degradação da qualidade. O HBI armazenado pode ser alimentado em um forno primário de fabricação de aço ou em um alto-forno. Se o ferro reduzido produzido pelo processo FASTMET é utilizado como DRI na forma de pellets/briquetes ou se é conformado em HBI utilizando equipamentos HBI depende da aplicação do produto (fonte de ferro) e seu período de armazenamento.
O resíduo metalúrgico (pó) gerado na siderurgia tem sido convencionalmente peletizado ou sinterizado internamente para reciclar o pó como matéria-prima para os altos-fornos. A matéria-prima do alto-forno, no entanto, contém componentes voláteis, principalmente zinco, que vaporiza na zona de alta temperatura do alto-forno. No entanto, nem todo o vapor escapa do alto-forno. Uma parte do vapor é resfriada e retida por materiais recém-carregados, permanecendo no forno. Os componentes voláteis acumulados diminuem a permeabilidade do alto-forno e prejudicam consideravelmente sua produtividade.
O processo FASTMET vaporiza metais pesados como zinco e chumbo, que inibiram a reciclagem de sucata de ferro, e os converte em óxido de zinco bruto e similares. Isso permite a descarga desses elementos em linhas de exaustão sem circulá-los no processo. As estações de tratamento de gases de exaustão são equipadas com um sistema de resfriamento e coleta de poeira que, combinado com resfriamento a ar e resfriamento a água, evita que os componentes voláteis adiram às paredes do equipamento. Isso permite uma operação estável e contínua por um longo período de tempo e a coleta de óxido de zinco bruto e similares, usando um filtro de mangas. O óxido de zinco bruto coletado é um recurso valioso e é reciclado junto com o ferro reduzido.
O processo e as principais reações
O processo FASTMET inicia-se com a mistura de finos de minério de ferro ou rejeitos metalúrgicos de siderurgia (contendo alto percentual de óxido de ferro) com carvão pulverizado, aglomerando a mistura em pelotas ou briquetes usando uma peletizadora ou briquetadeira, secando os aglomerados em um secador, e colocando os aglomerados sobre a lareira de um RHF em uma ou duas camadas pares.
Os pellets ou briquetes devem ser isolados do ar quando entrarem no forno. Sua taxa de alimentação é controlada precisamente ao mesmo tempo. O processo FASTMET contém um sistema de tubos de alimentação que permite ajustar o número de tubos de acordo com o tamanho do forno, conseguindo simultaneamente o isolamento do ar e o controle de volume. Um sistema de nivelamento tipo parafuso é adotado para colocar os aglomerados em uma ou duas camadas uniformes.
À medida que a fornalha gira, os briquetes são aquecidos pela radiação das temperaturas da zona RHF de mais de 1.300 graus C e os óxidos de ferro são reduzidos a ferro metálico. A redução do óxido de ferro é realizada principalmente por carbono elementar fixo reagindo com magnetita (Fe3O4) ou hematita (Fe2O3) para formar ferro metálico (Fe) e wustita na forma sólida enquanto libera monóxido de carbono (CO) e dióxido de carbono (CO2) gasoso . Parte do carbono entra em solução sólida com o ferro metálico para formar carboneto de ferro (Fe3C).
Óxido de zinco, óxido de chumbo e outros óxidos metálicos voláteis contidos na alimentação de resíduos metalúrgicos também são reduzidos à forma metálica e vaporizados. Esses vapores metálicos são reoxidados no gás de exaustão antes de deixar o forno pela saída.
Um método de aquecimento rápido, uma tecnologia proprietária da Kobe Steel é adotada para aquecer os pellets ou briquetes que são colocados sobre a lareira, atingindo rapidamente uma alta temperatura de 1.350 graus C. Este aquecimento gera a reação de óxidos e carbono. Residindo de 8 minutos a 16 minutos, os aglomerados são convertidos em DRI, que é descarregado do forno ou fornecido ao processo a jusante, a uma temperatura de 1.000 graus C a 1.200 graus C. Diferentes reações que estão ocorrendo entre óxidos e carbono são (i) Fe2O3 + 3C =2Fe + 3CO, (ii) Fe3O4 + 4C =3Fe + 4CO, (iii) Fe2O3 + 3CO =2Fe + 3CO2, (iv) Fe3O4 + 4CO =3Fe + 4CO2, (v) FeO + CO2 =Fe + CO2 e (vi) ZnO + CO2 .
O gás de combustão (gás CO) emitido pelos pellets/briquetes como resultado da reação de redução pode ser utilizado como combustível para o RHF, o que diminui consideravelmente a quantidade de combustível fornecida ao queimador.
A atmosfera no EIF do processo FASTMELT consiste essencialmente em gás CO e, portanto, altamente redutor. Esta atmosfera redutora promove a redução de silício e remoção de enxofre.
A descarga estável e contínua de DRI do RHF em alta temperatura é alcançada por uma tecnologia proprietária da KSL como a elevação da lareira de um forno de redução. Ao contrário de um alto-forno, o FASTMET pode iniciar e interromper a operação com relativa facilidade, dependendo da quantidade de produção, o que permite a produção em resposta à demanda.
Mecanismo de redução
A cinemática da reação de redução em um forno de redução direta é normalmente controlada pela difusão do gás de redução do lado de fora. No processo FASTMET, a reação de redução ocorre dentro dos pellets/briquetes compostos de carbono formados por finos de minério de ferro e carvão pulverizado. Uma vez que os pellets/briquetes compósitos são aquecidos, o gás CO dentro deles, promove a redução do óxido de ferro. Portanto, a reação de redução ocorre mais rapidamente nos pellets / briquetes de compósito de carbono do que a reação de redução que ocorre no processo convencional de redução direta. As reações básicas de redução que ocorrem durante o processo FASTMET são (i) FexOy + yC =xFe + y CO (reação endotérmica), (ii) CO2 + C =2CO (reação endotérmica) e (iii) FexOy + yCO =xFe + yCO2 (reação exotérmica).
Em temperaturas abaixo do ponto de fusão do ferro, dificilmente há qualquer reação direta com o carbono sólido do carvão pulverizado e, portanto, a reação dada na equação (i) domina a cinemática da reação. Em temperaturas mais altas de 1.000 graus C e mais, a reação da geração de gás CO por perda de solução de carbono conforme a equação (ii) e a reação do óxido de ferro pelo gás CO conforme a equação (iii) ocorrem em série dentro do carbono pellets / briquetes compósitos. Nestas reações, a geração de gás CO controla a cinemática da reação com sua natureza altamente endotérmica. Portanto, para promover a reação, é necessário fornecer o calor necessário para a reação ao interior do pellet / briquete composto de carbono na temperatura mais alta de 1.000 graus ou mais. Isso significa que o calor deve ser transferido eficientemente por radiação da atmosfera para a superfície do pellet/briquete e por condução da superfície do pellet/briquete para seu interior. A Fig 3 mostra o mecanismo de redução de pellets / briquetes de compósito de carbono
Fig 3 Mecanismo de redução de pellets / briquetes de compósito de carbono
Em RHF, os pellets/briquetes são normalmente aquecidos com temperaturas de zona superiores a 1.300 graus C e são reduzidos a ferro metálico. O tempo de residência na lareira é normalmente de 8 minutos a 16 minutos. Isso varia de acordo com o material que está sendo processado, tamanho dos pellets/briquetes e outros fatores. A rápida taxa de redução alcançada no processo FASTMET se deve à alta temperatura de redução, à alta taxa de transferência de calor e ao íntimo contato do carbono contido no interior dos briquetes com o óxido de ferro. A transferência de calor e as diferentes reações de redução que estão ocorrendo em RHF são mostradas esquematicamente na Fig 4.
Fig 4 Esquema de transferência de calor e reações de redução em RHF
Produto
O produto final do processo FASTMET / FASTMELT pode ser HBI, DRI quente descarregado diretamente em recipientes de transferência, DRI frio ou ferro líquido (hot metal). A metalização alcançada durante o processo é superior a 85%. A temperatura do gusa produzido pelo processo FASTMELT varia de 1.450°C a 1.550°C e tem a composição típica de carbono – 3% a 5%, silício – 0,3% a 0,6%, manganês – 0,6% a 1,2% , enxofre – menos de 0,05% e fósforo – menos de 0,03%.
Tratamento de gases de escape e controle ambiental
O gás de exaustão que sai do RHF está totalmente queimado, contendo cerca de 2% de oxigênio. Os trocadores de calor usam a energia térmica do gás de exaustão para pré-aquecer o ar de combustão para os queimadores RHF e secadores de preparação de matéria-prima. O gás de exaustão sai do forno rotativo através do teto e flui através de uma tomada de saída revestida de refratário para o duto de gás de exaustão. A localização adequada da saída dos gases de escape em relação às zonas de combustão RHF é determinada pela análise dos materiais de alimentação, cinética de redução e verificada por 'Dinâmica de Fluidos Computacional'. O ar de diluição é injetado no duto de gás de exaustão para fornecer resfriamento e queimar quaisquer combustíveis restantes (hidrogênio e CO) no fluxo de gás de exaustão.
Água de pulverização é adicionada ao resfriador primário para resfriar o gás de mais de 1.400 graus C a 1.000 graus C para minimizar a formação de NOx e fornecer uma temperatura de entrada aceitável para o recuperador. Do resfriador primário, o gás de exaustão flui através do ar de combustão e do pré-aquecedor de ar do secador, onde o calor do gás de exaustão é usado para aquecer o ar de combustão para os queimadores rotativos e o secador rotativo. O gás de exaustão sai do pré-aquecedor de combustão para o resfriador secundário. Água de pulverização é adicionada ao resfriador secundário para resfriar o gás de cerca de 800°C a 120°C para fornecer uma temperatura de entrada aceitável para o sistema de filtro de mangas. O gás de exaustão então flui para uma caixa de filtro de tecido a jato onde o óxido de zinco bruto é coletado e depois para um ventilador de ID onde é descarregado através de uma chaminé para a atmosfera.
O controle de SO2 normalmente não é necessário no processo FASTMET, pois a maior parte do SO2 reage e é absorvida pelos óxidos metálicos na corrente de combustão do gás. A injeção de cal pode ser usada para controlar ainda mais o SO2. O NOx é controlado pelo uso de queimadores de baixo NOx e controle operacional próximo da relação ar/combustível e temperaturas de combustão. As dioxinas e os furanos são destruídos pelas altas temperaturas e pelo longo tempo de residência no RHF. A taxa de resfriamento do gás de combustão é controlada para minimizar a formação de dioxinas e furanos. As partículas são removidas do gás de combustão por um sistema de filtro de mangas. O óxido de zinco bruto é coletado pelo sistema de filtro de mangas e armazenado em um silo.
O processo FASTMET é um processo amigo do ambiente. A emissão de CO2 do processo FASTMELT é de cerca de 1,6 toneladas por tonelada de gusa (t/tHM) contra cerca de 2,1 t/tHM de emissão de CO2 no caso de mini alto-forno. A emissão de NOx está na faixa de 0,3 kg por tonelada de gusa (kg/tHM) a 1,5 kg/tHM e a emissão de SOx é em torno de 2,4 kg/tHM.
Benefícios do processo FASTMET
O processo FASTMET oferece mais uma opção para o tratamento dos resíduos metalúrgicos da siderurgia. Uma planta FASTMET localizada em uma siderúrgica pode processar o pó e produzir dois produtos primários, DRI para realimentação ao forno primário de fabricação de aço e óxido de zinco bruto para venda aos processadores de zinco. Ele transforma um passivo em um ativo. O alto custo de descarte é eliminado e um suprimento barato de unidades de ferro se torna disponível.
Os benefícios do processo incluem (i) geração de finos muito baixa no processo resulta em alto teor de zinco e teor de ferro muito baixo do pó secundário, (ii) alta metalização e alta remoção de zinco tornam o produto de ferro reduzido reciclável para o forno primário de fabricação de aço, ( iii) nenhum resíduo é gerado para descarte, (iv) o tratamento em alta temperatura decompõe as dioxinas e (v) o pó de zinco pode ser tratado economicamente e se torna um produto, não um resíduo.
Processo de manufatura
- Desenvolvendo Padrões Operacionais e Processos
- Ferro Reduzido Direto e seus Processos de Produção
- Introdução aos processos de pelotização e pelotização de minério de ferro
- ITmk 3 Processo de fabricação de pepitas de ferro
- Processo HIsmelt de fabricação de ferro
- Processo HIsarna para fabricação de ferro
- Processos FASTMET e FASTMELT de fabricação de ferro
- Pelotas de minério de ferro e processo de pelotização
- Qualidade de Sinterização e Processo de Sinterização de Minérios de Ferro
- Fabricação de ferro por alto-forno e emissões de óxido de carbono