Pelotas de minério de ferro e processo de pelotização
Pellets de minério de ferro e processo de pelotização
A pelotização de minério de ferro foi iniciada na década de 1950 para facilitar a utilização de concentrados de minério de ferro finamente moído na produção de aço. Para a pelotização de minério de ferro, existem dois tipos principais de processos, a saber, o processo de grade móvel reta (STG) e o processo de forno de grelha (GK). No processo STG, um leito estacionário de pellets é transportado em uma grelha móvel sem fim através das zonas de secagem, oxidação, sinterização e resfriamento. No processo GK, a secagem e a maior parte da oxidação são realizadas em um leito estacionário de pellets transportado em uma grelha móvel. Em seguida, os pellets são carregados em um forno rotativo para sinterização e depois em um resfriador circular para resfriamento.
Os processos de pelotização são discutidos no artigo no link http://www.ispatguru.com/iron-ore-pellets-and-pelletizing-processes/.
As pastilhas podem ser pastilhas ácidas ou fundidas.
- Pellets de ácido – A basicidade dos pellets de ácido é geralmente inferior a 0,1. A resistência do pellet queimado é, até certo ponto, devido a pontes de hematita de estrutura policristalina. Esses pellets normalmente possuem grande volume de poros abertos. O gás de redução penetra rapidamente através desses poros no núcleo do pellet e simultaneamente ataca a estrutura em muitos lugares. Isso resulta em uma mudança estrutural precoce que começa em baixas temperaturas em todo o volume do pellet.
- Pellets fluxados – Também são conhecidos como pellets básicos. A basicidade das pelotas fundidas é maior que 0,1 e pode variar. A basicidade dos pellets básicos normais varia de 0,1 a 0,6 e tem baixa porcentagem de CaO. Durante a queima desses pellets, uma fase de escória vítrea consistindo de SiO2, CaO e Fe2O3 em porcentagem variável é formada. Devido ao aumento da adição de fluxo, há formação de alguma escória e devido a isso, há uma certa ligação da escória com os cristais de minério de ferro. Os pellets de alta basicidade têm um nível de basicidade maior que 0,6. Esses pellets contêm maior nível de CaO. Esses pellets não só possuem fase vítrea composta principalmente por SiO2, CaO e Fe2O3, mas também ferritas de cálcio (CaO.Fe2O3). Durante a queima desses pellets, a disponibilidade de CaO favorece consideravelmente o crescimento de cristais de hematita. Esses pellets normalmente têm uma alta resistência mecânica após a queima do pellet.
As usinas de pelotização são normalmente integradas às usinas de beneficiamento de minério de ferro. Caso não estejam integrados, o minério de ferro concentrado na forma de polpa é geralmente bombeado para a planta de pelotização por dutos de polpa. Plantas de pelotização baseadas em finos ricos de minério de ferro são raras e pouco econômicas. Todo o processo de peletização pode ser dividido em dois segmentos principais de subprocessos a saber (i) o segmento dos subprocessos a frio e (ii) o segmento dos subprocessos a quente.
O segmento dos processos frios possui os seguintes subprocessos.
- Tanque de polpa para armazenamento de polpa de minério de ferro concentrado da planta de beneficiamento. O tamanho de partícula do minério de ferro na pasta de minério é inferior a 45 micrômetros para cerca de 80% das partículas.
- Materiais aditivos (como dolomita, calcário, cal ou olivina etc., dependendo da qualidade do pellet a ser produzido) são adicionados à pasta.
- A maior parte da água é removida da pasta por meio de filtros. O teor de água do minério de ferro após a filtragem é de cerca de 9%.
- Um misturador é usado para a adição do aglutinante (bentonita ou aglutinante orgânico) para obter resistência mecânica suficiente dos pellets verdes
- Discos de pelotização ou tambores de esferas são usados para a produção de pellets verdes. Os discos de pelotização são mais populares para a produção de pellets verdes.
- As telas vibratórias são normalmente usadas para separar diferentes frações de pellets verdes. Os pellets subdimensionados são reciclados de volta ao processo, enquanto os pellets superdimensionados são triturados antes de serem reciclados.
- O restante é em pellets de tamanho (8 mm a 16 mm) que são transportados em uma esteira para o processo de secagem no segmento de processos a quente.
O segmento dos processos quentes possui os seguintes subprocessos.
- Forno de secagem para remover a maior parte do conteúdo de água dos pellets verdes por fluxo de ar quente através do leito. As pelotas secas então entram no forno de pelotização.
- Os pellets secos são queimados (1250 graus C a 1300 graus C) no forno de peletização para converter os pellets verdes no produto final
- O resfriamento dos pellets endurecidos a quente até cerca de 200 graus C é realizado no refrigerador por sopro de ar frio.
A maioria dos subprocessos acima são operados atualmente com a ajuda de técnicas de controle usando controles automáticos. Alguns dos subprocessos dependem muito do bom funcionamento do subprocesso anterior. Por exemplo, se o tamanho das partículas for muito grande, ou os finos estiverem muito secos, ou a secagem não estiver funcionando, não será possível produzir pellets. Uma situação menos crítica é quando alguns segmentos estão funcionando abaixo do ideal. Por exemplo, se o processo no qual o ligante é adicionado a mistura do ligante não é uniforme, então o processo para a formação do pellet verde sofre. Portanto, o processo de pelotização de minério de ferro é uma cadeia de vários subprocessos que dependem muito do desempenho de cada um.
A adição de aglutinante ao minério atende a dois objetivos principais:(i) tornar o minério plástico para que ele possa nuclear sementes que crescem em pelotas bem formadas e (ii) manter a pelota unida durante o manuseio, secagem e pré-aquecimento ou até que tenha sido suficientemente reforçada por endurecimento durante a queima. O aglutinante ideal deve produzir pellets de alta qualidade a um custo mínimo e introduzir o mínimo de contaminantes possível. O aglutinante também não deve ser tóxico, fácil de manusear e não deve exigir um sistema de alimentação avançado. Pequenas adições de bentonita promovem a adesão pela formação de ligações cerâmicas e pela maior compactação das partículas durante o rolamento das bolas verdes.
A qualidade dos pellets verdes depende de parâmetros de entrada como mineralogia, química e granulometria de finos de minério, parâmetros de balling como tamanho de partícula de alimentação, quantidade de água adicionada durante a peletização, velocidade de rotação do disco, ângulo de inclinação do fundo do disco e tempo de residência dos materiais no disco etc.
Em pellets verdes, a água desempenha um papel importante. Aglomera o minério e desempenha a função de aglutinar o líquido. Aglomerados úmidos podem existir em vários estados diferentes, dependendo da quantidade de água presente. Estes são mostrados esquematicamente na Fig. 1. O grau de enchimento do líquido de ligação ou saturação do líquido descreve a porção do volume do poro que é preenchida com o líquido de ligação.
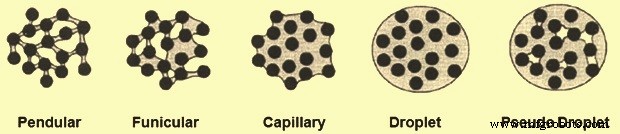
Fig 1 Apresentação esquemática de diferentes estados de aglomerado úmido
Em baixas saturações, as partículas são mantidas juntas por pontes líquidas (ligações pendulares, estado pendular). No estado de tensão (funicular), ambos os capilares cheios de líquido e as pontes líquidas coexistem. No estado capilar, todos os capilares são preenchidos com líquido e superfícies côncavas são formadas nas aberturas dos poros devido às forças capilares.
O estado de gota ocorre quando o aglomerado é mantido unido pela força coesiva do líquido. No estado de pseudo-gota, os vazios não preenchidos permanecem presos dentro da gota. Uma característica comum é que
nos estados capilares e gotículas, são esperadas aberturas capilares côncavas ou água superficial livre, sobre toda a superfície externa do aglomerado. A teoria capilar para a resistência do aglomerado úmido está bem estabelecida agora.
Aditivos têm sido empregados para melhorar tanto a operação quanto a economia do processo de pelotização. A cal (CaO) e a cal hidratada [Ca(OH)2] provaram ser aditivos benéficos durante a produção de pellets. As propriedades do pellet verde e seco, bem como do pellet queimado, foram significativamente melhoradas com a adição de cal ou cal hidratada
A qualidade física e metalúrgica dos pellets do produto depende amplamente da qualidade do pellet verde, tipo e quantidade de aglutinantes, fluxos e aditivos usados e parâmetros de endurecimento, como condições de queima (temperaturas e tempo, etc.). Os ingredientes dos pellets verdes reagem juntos, durante a queima, para formar nos pellets de produto diferentes fases e microestruturas.
O tipo e a quantidade dessas fases, sua química e distribuição desempenham um papel vital na decisão das propriedades metalúrgicas dos grânulos do produto durante a redução no processo subsequente de fabricação de ferro. Estudos de pelotas verdes e endurecimento de finos de minério de ferro magnetita e hematita de alto teor com baixa alumina têm sido realizados em diferentes partes do mundo. Mas os resultados desses estudos não podem ser interpretados diretamente para minérios de ferro com maior quantidade de alumina (Al2O3) devido à diferença de química e mineralogia. Os finos de minério de ferro com teor de Al2O3 comparativamente alto apresentam diferentes características de pelotização.
Quanto à queima de minérios de ferro hematita, é necessário fornecer mais calor de fontes externas devido à ausência da seguinte reação exotérmica de oxidação da magnetita.
4FeO + O2 =2Fe2O3
O consumo de energia necessário para a produção de pelotas a partir de finos de minério de hematita é maior do que o necessário para a pelotização de finos de minério de magnetita. Além disso, os pellets feitos de minérios de hematita têm propriedades de torrefação ruins e não atingem a resistência física adequada até que a temperatura de torrefação seja superior a 1300 graus C. Observa-se que as partículas de hematita e a estrutura do pellet mantêm suas formas originais se a temperatura estiver abaixo de 1200 graus C. O tamanho das partículas de hematita não aumenta, nem os defeitos da rede cristalina de Fe2O3 são eliminados até que a temperatura seja superior a 1300 graus C. Em altas temperaturas, as pontes de conexão iniciais são formadas entre os grãos de cristal e ocorre a recristalização de Fe2O3. No entanto, se a temperatura de torrefação for superior a 1350 graus C, será prejudicial, pois o Fe2O3 se decompõe em Fe3O4, conforme expresso pela reação a seguir, e isso resulta negativamente na perda da qualidade do pellet.
6Fe2O3=4Fe3O4+O2
A termodinâmica desta reação indica que a temperatura de decomposição do Fe2O3 aumenta com o aumento da pressão parcial de oxigênio. Portanto, a alta temperatura de queima excessiva e a baixa pressão parcial de oxigênio devem ser evitadas para evitar a decomposição do Fe2O3. Assim, é necessário manter uma temperatura de torra mais alta para os pellets de hematita, bem como uma faixa de temperatura de queima mais estreita. Isso dificulta a operação dos equipamentos de queima.
Para aumentar o endurecimento dos pellets de hematita, ambos os métodos de adição de magnetita e carregados de carbono são considerados as técnicas favoráveis na prática.
No caso da pelotização dos minérios de magnetita, quando uma pelota começa a oxidar, forma-se uma casca de hematita enquanto o núcleo da pelota ainda é magnetita. As mudanças de volume térmico nessas duas fases indicam que a sinterização na fase de magnetita começa mais cedo (950°C) em comparação com a fase de hematita (1100°C). A diferença nas taxas de sinterização entre as fases de magnetita e hematita é maior em torno de 1100 graus C. A taxa de sinterização aumenta em ambas as fases com o aumento da finura no concentrado de magnetita. Uma moagem mais fina na matéria-prima, portanto, promove a formação de estruturas duplex indesejadas com um núcleo mais fortemente sinterizado saindo da casca. Com porosidade original constante em pellets verdes, a taxa de oxidação diminui à medida que o concentrado de magnetita se torna mais fino, devido à sinterização aprimorada. No entanto, no balling prático, matérias-primas mais finas requerem o uso de mais água no balling, o que resulta em um aumento da porosidade do pellet verde. Esses dois efeitos opostos se nivelam e o tempo de oxidação se torna constante. Em condições de processo industrial, ainda são esperadas diferenças na estrutura duplex. Isso ocorre porque apenas a oxidação parcial ocorre antes do endurecimento.
A adição de cal (CaO) aos finos de minério de ferro diminui ligeiramente a produtividade das pelotas verdes, mas aumenta a resistência à queda e a resistência à compressão das pelotas verdes. Além disso, a resistência dos pellets é diretamente proporcional ao encolhimento que ocorre durante a queima dos pellets. No caso de pellets fluxados, a adição de cal aumenta a contração do pellet e, portanto, aumenta a resistência do pellet. Isso se deve à interação entre cal, sílica e óxido de ferro formando silicato de cálcio e ferritas de cálcio. A adição de cal resulta na sinterização de partículas finas de hematita suportadas por ligações minerais secundárias muito localizadas próximas aos locais originais das partículas de cal. Com o aumento da temperatura e da concentração de cal, forma-se mais escória que consolida a estrutura e diminui a porosidade acessível.
O uso de cal hidratada [Ca(OH)2] tem uma influência positiva na resistência à queda e na resistência à compressão de pellets verdes e secos. Também há uma boa influência do Ca(OH)2 na resistência final dos pellets queimados.
A adição de Ca(OH)2 resulta na diminuição da eficiência da bentonita como aglutinante pela substituição do íon sódio mais eficiente pelo íon cálcio, convertendo-o no mais cálcico e menos eficiente, levando à deterioração das propriedades do pellet. portanto, em alguns casos, não é desejável adicionar mais de um aglutinante ao mesmo tempo durante o processo de peletização, pois isso pode resultar na deterioração das propriedades do pelete em vez de seu aprimoramento. Depois que uma certa quantidade de Ca(OH)2 é adicionada, algumas melhorias nas propriedades do pellet são alcançadas, o que pode ser atribuído ao efeito do Ca(OH)2 como aglutinante durante o processo de peletização. A cinética de redução dos pellets contendo 0,4% de bentonita e 4% Ca(OH)2, possuindo as maiores propriedades físico-químicas, mostra que a redução desses pellets é controlada por reação química interfacial.
Processo de manufatura
- O processo de sinterização de finos de minério de ferro
- Introdução aos processos de pelotização e pelotização de minério de ferro
- ITmk 3 Processo de fabricação de pepitas de ferro
- Processo HIsmelt de fabricação de ferro
- Processos FASTMET e FASTMELT de fabricação de ferro
- Beneficiamento de Minérios de Ferro
- Mineração de minérios de ferro
- Uso de Pelotas de Minério de Ferro na Carga do Alto Forno
- Qualidade de Sinterização e Processo de Sinterização de Minérios de Ferro
- Entendendo o processo de fundição de minério de ferro