O processo de sinterização de finos de minério de ferro
O processo de sinterização de finos de minério de ferro
As plantas de sinterização são normalmente associadas à produção de gusa em altos-fornos em câmaras de aço integradas. O processo de sinterização é basicamente uma etapa do processo de pré-tratamento durante a fabricação do ferro para a produção do material de carga chamado sinterização para o alto-forno a partir de finos de minério de ferro e também de resíduos metalúrgicos (pós coletados, lodo e carepa de laminação etc.).
A tecnologia de sinterização foi originalmente desenvolvida com a finalidade de utilizar no alto-forno os finos de minério de ferro e o ferro presente nos rejeitos metalúrgicos de uma siderúrgica. Mas atualmente o foco mudou. Agora o processo de sinterização visa produzir uma carga de alta qualidade para o alto-forno. Hoje o sinter é a principal carga metálica para um alto-forno de grande porte.
O processo de sinterização é utilizado para aglomerar uma mistura de minérios de ferro (blend), finos de retorno, fluxos e coque, com granulometria inferior a 10 mm, de modo que a sinterização resultante, com granulometria de 10 mm a 30 mm, pode suportar condições de pressão e temperatura no alto-forno.
Princípio de sinterização
A sinterização é um processo térmico (realizado de 1300 graus C a 1400 graus C) pelo qual uma mistura de minério de ferro, finos de retorno, produtos reciclados da indústria siderúrgica (como carepa de laminação, pós de alto forno, etc.), escória elementos formadores, fundentes e finos de coque são aglomerados em uma planta de sinterização com o objetivo de fabricar um produto sinterizado de composição química, qualidade (física) e granulometria adequadas para ser alimentado no alto-forno, garantindo assim um funcionamento homogêneo e estável do forno alto . Antes da sinterização, existe um processo importante chamado granulação. A granulação é a homogeneização da mistura de minério de ferro em tambor rotativo com 7 % a 8 % de água com o objetivo de obter um produto pré-aglomerado, que é então entregue como uma camada sobre uma grelha ou fio em movimento contínuo para obter o produto sinterizado. Este processo tem um papel fundamental, pois garante uma adequada permeabilidade do leito de sinterização e, consequentemente, uma boa produtividade da máquina de sinterização.
A flexibilidade do processo de sinterização permite a conversão de uma variedade de materiais, incluindo finos de minério de ferro, pós capturados, concentrados de minério e outros materiais contendo ferro de pequeno tamanho de partícula (por exemplo, carepa de laminação) em um aglomerado semelhante ao clínquer.
O processo de sinterização envolve o aquecimento do produto pré-aglomerado para produzir uma massa semifundida que se solidifica em pedaços porosos de sinter com as características de tamanho e resistência necessárias para alimentação no alto-forno.
O produto sinter
O produto do processo de sinterização é chamado de sinter e as características de qualidade de um bom sinter incluem (i) análise química, (ii) distribuição do tamanho de grão, (iii) redutibilidade e (iv) resistência do sinter. Propriedades típicas de sinter são dadas na Tab 1
Tab 1 Propriedades típicas do sinter | |||
Sl. No. | Item | Unidade | Valor |
1 | Composição química | ||
Fe | % | 56,5 a 57,5 | |
FeO | % | 6,0 a 8,0 | |
SiO2 | % | 4,0 a 5,0 | |
Al2O3 | % | 1,0 a 2,5 | |
CaO | % | 7,5 a 8,5 | |
MgO | % | 1,6 a 2,0 | |
2 | Basicidade (CaO/SiO2) | 1,7 a 2,9 | |
3 | Força ISO (+ 6,3 mm) | % | Maior que 75 |
4 | Índice de degradação de redução (RDI) | (-3 mm) % | 27 a 31 |
5 | Índice de redutibilidade (RI) | (R60) % | 55-75 |
6 | Índice do copo | (-6,3 mm) % | 65-75 |
O produto de sinterização do minério de ferro é mostrado na Fig 1.
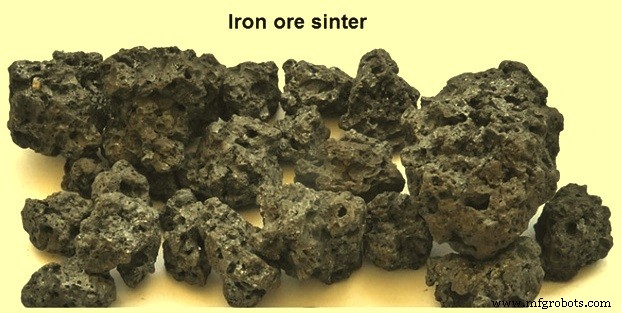
Fig 1 Sinterização de minério de ferro
Tipos de sinter
Os sinters são classificados em sinter ácido, sinter autofluxante e sinter superfluxado. O sinter autofluxante tem conteúdo suficiente de CaO (cal) que é necessário para fundir seus componentes ácidos (SiO2 e Al2O3). O sínter superfluxado possui conteúdo adicional de CaO para fluxo dos componentes ácidos introduzidos no alto-forno através de outros materiais de carga. No caso de sinterização autofluxante e superfluxada, a cal reduz a temperatura de fusão da mistura de sinterização e em temperaturas relativamente baixas (1100°C a 1300°C) fortes ligações são formadas na presença de FeO. A seguir estão as vantagens de adicionar fluxo ao sinter.
- Gera escória com as impurezas presentes nos minérios de ferro e combustíveis sólidos produzindo uma matriz adequada para coesão das partículas.
- Melhora as propriedades físicas e metalúrgicas do sinter
- Reduz a temperatura de fusão da mistura de sinterização.
- Reduz/elimina a adição de calcário no alto-forno economizando assim o combustível necessário para a reação de calcinação do calcário (CaCO3 =CaO + CO2) no alto-forno, reduzindo assim a taxa de coque no alto-forno. l>
O processo de sinterização
O processo de sinterização começa com a preparação das matérias-primas compostas por finos de minério de ferro, fundentes, resíduos metalúrgicos in-plant, combustível e finos de retorno da planta de sinterização. Esses materiais são misturados em um tambor de pelotização rotativo e é adicionada água para atingir a aglomeração adequada da mistura de matérias-primas. Esta aglomeração está na forma de micro-pellets. Esses micropellets auxiliam na obtenção de uma ótima permeabilidade durante o processo de sinterização. Esses micropellets são então transportados para a máquina de sinterização e formam a camada superior da mistura de carga.
O processo de sinterização é um processo contínuo que se baseia no tratamento de uma camada de mistura de carga (finos de minério, finos de retorno, fundentes etc.) na presença de brisa de coque à ação de um queimador colocado na superfície da camada. Desta forma, o aquecimento ocorre da parte superior para a parte inferior. A camada de mistura de carga repousa sobre um sistema de fios e um sistema de exaustão permite que toda a espessura atinja a temperatura adequada para a fusão parcial da mistura e a subsequente aglomeração.
Na sinterizadora Dwight-Lloyd, a grelha de sinterização é uma corrente contínua de grande comprimento e largura, formada pela união de uma série de carros-paletes que formam o cordão de sinterização (Fig. 2). Cada vagão-palete passa por baixo de uma tremonha de carregamento onde é carregado primeiramente por material de granulometria grossa (10 mm a 20 mm) em uma camada de espessura de 30 mm a 60 mm que forma a camada da fornalha composta principalmente de sinter de retorno. A camada da fornalha protege as grelhas de aço do superaquecimento durante o processo de sinterização.
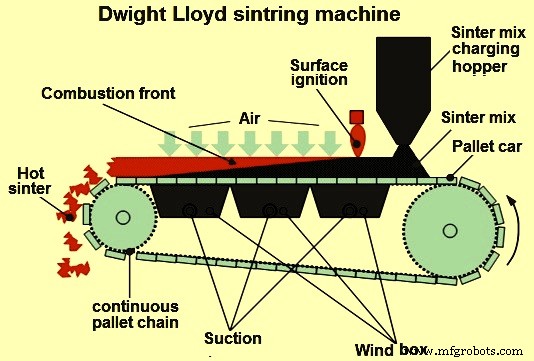
Fig 2 Máquina de Dwight Lloyd
Uma segunda camada de micropellets é carregada sobre a camada da lareira e nivelada. Em seguida, o carro-palete passa abaixo de um forno de inicialização, onde ocorre a ignição do combustível na superfície da mistura de carga. Ao mesmo tempo, a mistura é submetida a sucção descendente através da carga de sinterização. Devido à sucção descendente, o ar é puxado através do leito móvel fazendo com que o combustível queime.
O carro-palete continua o processo e a combustão progride na direção do fluxo de gás. Desta forma, o processo de sinterização ocorre. O processo de combustão não ocorre simultaneamente em toda a espessura do leito. Pelo contrário, a combustão acontece como uma camada horizontal que se move verticalmente através do leito. A espessura desta camada é uma pequena fração do leito. A permeabilidade do leito é um requisito de qualidade para a mistura de carga e, portanto, o processo de granulação da mistura de carga é uma etapa importante para o processo de sinterização (a permeabilidade do leito é melhorada devido à granulação).
Na região acima da zona de combustão, o produto sinterizado muito quente aquece o ar que passa por esta camada. Desta forma, o ar pré-aquecido chega à área de combustão. O calor do ar/gases previamente aquecidos é absorvido nestas seções frias, causando pré-aquecimento da carga e evaporação da umidade da mistura de carga. Nesse contexto, altas temperaturas que causam fusão parcial são atingidas e ocorre o processo de sinterização.
A alta eficiência térmica é causada pelo acúmulo de calor em uma camada parcial da mistura de carga chamada zona de sinterização ou frente de chama. A frente de chama avança a uma velocidade que varia de 10 mm a 30 mm/min em direção à grelha de sinterização. Em uma altura de leito de cerca de 500 mm, o processo normalmente leva cerca de 25 minutos. Uma vez alcançada a extremidade do cordão, o material sinterizado é descarregado e submetido a resfriamento, britagem e peneiramento.
O processo de sinterização é controlado pelo "ponto de queima" (BTP), que é definido como o ponto em que a temperatura do gás residual atinge seu valor mais alto. É o ponto em que a frente da chama atinge a base do fundo do leito de sinterização. A velocidade da máquina de sinterização e o fluxo de gás são controlados para garantir que o ponto de queima ocorra imediatamente antes da descarga do sinter. A determinação do ponto de queima é muito importante para estabilizar o processo e melhorar a qualidade e a produtividade.
No final da máquina, o material sinterizado na forma de torta é descarregado no britador de sinterização a quente. Aqui, a torta de sinterização quente é triturada até um tamanho de partícula máximo pré-determinado. A partir daqui, o sinter é descarregado no resfriador de sinter que pode ser em linha reta ou circular. Depois de resfriado o sinter é transferido para a seção de peneiramento onde é dividido normalmente em três frações granulométricas. A primeira fração consiste em 0 mm a 5 mm que é chamada de finos de retorno e é enviada para as tremonhas de alimentação. A fração de sinterização com uma faixa de granulometria dentro de 5 mm a 15 mm é usada como camada de sinterização na fita de sinterização. A quantidade de saldo de fração de 5 mm a 15 mm que não é usada para camada de lareira é misturada com a terceira fração granulométrica com uma faixa de tamanho de 15 mm a 50 mm é enviada para o alto-forno.
Os finos de retorno são inevitavelmente gerados durante o processo de sinterização e são reciclados de volta ao processo de sinterização. Os finos de retorno geralmente consistem em cerca de 30% a 40% dos materiais de rolamento de ferro. Os finos de retorno da peneira de sinterização são um pouco mais facilmente assimilados do que os da peneira de alto-forno devido ao menor teor de ferrita de alto teor de cálcio.
Existem quatro zonas que são identificadas na altura do leito de sinterização. Estes são dados abaixo.
- Zona fria e úmida – Inclui a zona do leito de sinterização com temperatura inferior a 100 graus C. Esta área é formada pela mistura de carga a ser sinterizada, com limite superior saturado em água/vapor de água. l>
- Zona de secagem – Inclui a área do leito de sinterização com temperaturas que variam entre 100°C e 500°C. Nesta zona ocorre a evaporação da umidade da mistura de sinterização e a subsequente desidratação dos hidróxidos.
- Zona de reação – Inclui a zona do leito de sinterização com temperatura variando entre 500°C (início da ignição do coque) e 900°C (início do período de resfriamento). A temperatura máxima que atinge esta zona está na faixa de 1300 graus C a 1400 graus C. Os principais processos que ocorrem nesta zona são (i) combustão de coque (exotérmica), (ii) decomposição de carbonatos (endotérmica), (iii ) reações em fase sólida, (iv) redução e reoxidação de óxidos de ferro, e (v) reações de formação da massa sinterizada.
- Zona de resfriamento – Esta zona é encontrada imediatamente após a zona de reação. Nesta zona ocorre o resfriamento e a recristalização do produto sinterizado. Existe uma zona superficial onde a camada de sinterização é frágil do que no resto do leito de sinterização.
A causa das flutuações do processo de sinterização foi estudada para reduzir o consumo de carbono, reduzindo assim as emissões de dióxido de carbono. A análise de frequência dos dados da planta (temperatura do gás de exaustão em uma caixa de vento, nível de carga da mistura e teor de umidade da mistura) indicou que as variações de umidade da mistura de alimentação estão ligadas a flutuações da temperatura de exaustão do gás na caixa de vento específica. A melhoria do controle do processo, controlando o teor de umidade da mistura de alimentação em uma faixa estreita de valores, permite a redução do consumo de carbono e leva a menores emissões de dióxido de carbono.
O circuito de gás residual deve ser totalmente à prova de vazamentos, não permitindo que o ar da atmosfera seja sugado pelo sistema. Isso resulta em economia de energia no circuito de gás residual. Os gases residuais são tratados para remoção de poeira em um ciclone, precipitador eletrostático, lavador úmido ou filtro de tecido. O fluxograma da planta de sinterização é mostrado na Fig 3.
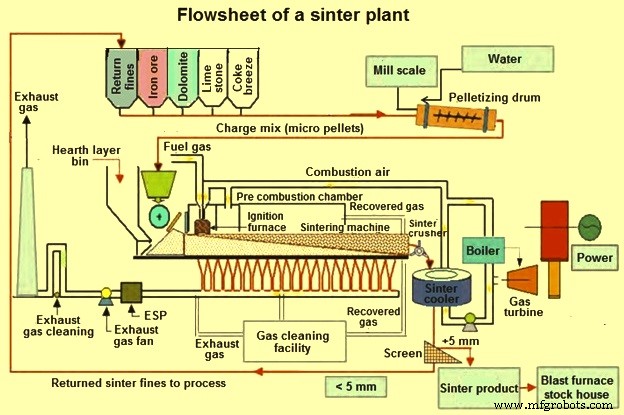
Fig 3 Fluxograma da planta de sinterização
Máquinas de sinterização
As máquinas de sinterização são de dois tipos:(i) máquinas circulares e ii) máquinas de linha reta. As máquinas de linha reta também estão sendo conhecidas como máquinas Dwight Lloyd. Dwight e Lloyd construíram a primeira planta de sinterização contínua em 1906.
As máquinas de sinterização circular são normalmente adequadas para altos-fornos com volumes úteis de 650 Cum ou menos. Os parâmetros man de algumas das máquinas circulares são fornecidos na Tab 2.
Tab 2 Principais parâmetros de máquinas de sinterização circulares | |||||
Assunto | Unidade | máquina de 12 m² | máquina de 17 m² | máquina de 25 m² | máquina de 33 m² |
Produção anual | 1000 tpa | 172 | 253 | 404,5 | 556 |
Requisito de energia total | kW | 700 | 1500 | 1750 | 2400 |
Terreno necessário para a planta | m² | 8000 | 9000 | 10.000 | 12.000 |
Terreno necessário para a construção | m² | 800 | 3400 | 35.000 | 3600 |
Várias características das máquinas circulares são como abaixo.
- Em comparação com as máquinas de linha reta, os custos de investimento de capital são baixos e os prazos de construção são curtos.
- A vedação é melhor e o vazamento de ar é menor nessas máquinas, pois as caixas de vento se movem em sincronia com as grelhas e a vedação da água é adotada.
- O sistema de descarga faz o tamanho do sinter a frio de tal forma que não há necessidade de um britador adicional.
- As máquinas circulares estão tendo alta flexibilidade operacional.
Uma máquina de sinterização circular é mostrada na Figura 4.
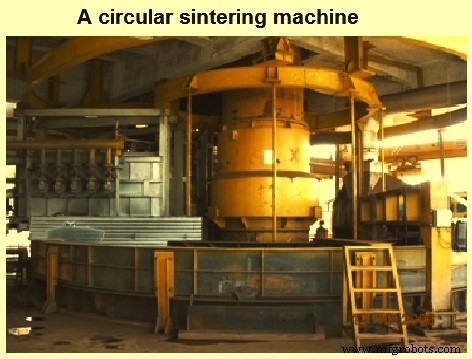
Fig 4 Máquina de sinterização circular
Máquinas de linha reta são normalmente usadas para plantas de sinterização de alta capacidade. As áreas de sinterização dessas máquinas são geralmente de 50 m² e acima. As atuais máquinas de linha reta são instaladas com larguras que variam de 2 m a 5 m e com áreas efetivas de sinterização que variam de 200 m² a 600 m². As produtividades dessas máquinas estão tipicamente na faixa de 30 t/m²/dia a 46 t/m²/dia. As capacidades dessas máquinas variam de 190.000 toneladas por ano a 6,5 Mtpa. Uma máquina reta é mostrada na Fig 5.
Fig 5 Máquina de sinterização de linha reta
Questões importantes relacionadas a sinterização e plantas de sinterização
A seguir estão as questões importantes relacionadas às plantas de sinterização e sinterização.
- O uso de sinter reduz a taxa de coque e aumenta a produtividade no alto-forno.
- O processo de sinterização ajuda na utilização de finos de minério de ferro (0-10 mm) gerados durante as operações de mineração de minério de ferro.
- O processo de sinterização ajuda na reciclagem de todos os resíduos de ferro, combustível e fluxo na usina siderúrgica.
- O processo de sinterização utiliza gases derivados da siderurgia.
- Sinter não pode ser armazenado por muito tempo, pois gera multas excessivas durante armazenamentos longos.
- A sinterização gera finos/pó excessivos durante o manuseio múltiplo na planta de sinterização.
Processo de manufatura
- Pó de metal refratário e seu processo de sinterização
- Sistema de automação e controle da planta de sinterização
- O diagrama de fases ferro-carbono
- ITmk 3 Processo de fabricação de pepitas de ferro
- Fatores que influenciam a Sinterização e o Processo de Sinterização
- Processo HIsmelt de fabricação de ferro
- Tecnologias para Melhoria no Processo de Sinterização
- Qual é o processo de torneamento CNC?
- Vários métodos de processo de fabricação de aço
- Entendendo o processo de fundição de minério de ferro