Fio-máquina e Moinhos de fio-máquina
Arames-máquina e Fresas de fio-máquina
O fio-máquina de aço é um talento versátil, pois é o principal produto da indústria siderúrgica com múltiplos usos. Eles são usados como material para fixadores, molas, rolamentos, cabos de aço, correntes, cabos, telas de arame, cercas de arame, cordão de pneu, reforço em dormentes ferroviários e muitos outros usos. Eles são usados para os componentes necessários para a indústria automotiva, indústria química, centrais elétricas e engenharia de máquinas. Ao contrário de chapas laminadas a frio, chapas grossas, tubos, perfis e outros produtos siderúrgicos, os fios-máquina raramente são utilizados como laminados a quente para produtos finais, mas são fabricados em peças de máquinas após passarem por uma ou mais etapas do chamado pós-processamento, como tratamento térmico, forjamento e trefilação em fábricas especializadas. Os fios-máquina são geralmente estirados até um diâmetro específico antes de serem submetidos a forjamento ou outras operações de conformação no processamento secundário. Em muitos casos, o tamanho dos fios-máquina antes de serem submetidos a essas operações de conformação deve ser inferior ao tamanho mínimo de 5,5 mm que pode ser fornecido laminado.
Geralmente cada produto fio-máquina é desenvolvido com a devida atenção ao seu comportamento nas etapas de pós-processamento. O que se exige de uma siderúrgica em relação ao fio-máquina é uma boa processabilidade e atendimento das propriedades exigidas após o beneficiamento. Além disso, como os custos do pós-processamento são muitas vezes superiores ao preço do fio-máquina, é cada vez mais importante reduzir o custo total de fabricação integrada desde o material de aço até o produto final.
Também tratado termomecanicamente ( TMT) barras de reforço de 6 mm, 8 mm e 10 mm basicamente necessárias para a construção civil são produzidas nos moinhos de fio-máquina.
O seguinte geralmente caracteriza os produtos de fio-máquina.
- Os graus dos produtos variam amplamente, desde graus comuns padronizados para aplicações gerais até graus de alta qualidade para aplicações de ponta com as especificações definidas individualmente para cada cliente, principalmente para a indústria automobilística e outras indústrias de manufatura.
- Os produtos de ponta para aplicações relacionadas à segurança, como motores de automóveis, sistemas de transmissão e chassis, são usados como materiais funcionais e, como tal, devem ter propriedades altamente exigentes, como alta resistência e longa vida útil à fadiga.
- Os produtos de aço fio-máquina são produtos semi-acabados, raramente usados como laminados a quente, e são fabricados em produtos finais após processamento secundário e até ternário, como forjamento, tratamento térmico e usinagem.
- Os produtos industriais finais para os quais são utilizados estão sujeitos a uma forte concorrência no mercado internacional.
- Os produtos industriais para os quais são usados são necessários para minimizar a carga no ambiente global durante todo o ciclo de vida.
Ao desenvolver um novo produto de aço de fio-máquina considerando o exposto acima, deve-se prestar atenção às questões importantes, como as seguintes.
- Se é possível eliminar ou simplificar um ou mais processos secundários e ternários para melhorar a produtividade e reduzir os custos de fabricação
- Se o novo produto melhora a funcionalidade, prolonga a vida útil, reduz o peso ou traz outras vantagens ao produto final para o qual é usado
- Se é possível eliminar substâncias prejudiciais ao meio ambiente
Esses requisitos nem sempre são compatíveis entre si, sendo importante prosseguir com as etapas de desenvolvimento com base no bom entendimento das condições de operação nas etapas de processamento, da condição de uso e das características do produto final para o qual os fio-máquina serão utilizados e similares. .
Os fios-máquina são usados em uma ampla gama de campos industriais. Portanto, eles precisam atender a determinadas combinações de propriedades, como resistência, ductilidade, conformabilidade a frio, trefilação e temperabilidade. Além disso, o mercado atual exige algumas propriedades adicionais no fio-máquina que são (i) tolerâncias dimensionais e ovalização de ultraprecisão, (ii) menor perda de escala, (iii) tolerâncias negativas (em peso seccional), (iv) nenhuma variação de dimensões ao longo do comprimento do fio-máquina, (v) propriedades físicas uniformes, e (vi) peso uniforme com variação nominal entre a parte frontal, média e traseira.
A qualidade do fio-máquina tornou-se cada vez mais importante nos dias de hoje. Para muitas aplicações de fio-máquina, é importante que os fios-máquina tenham superfícies sem marcas, arranhões, conchas, rachaduras, transbordamentos e partículas de óxido.
A garantia de qualidade em todo o comprimento do fio-máquina após a laminação demanda tempo e mão de obra e, por isso, o controle de qualidade dos tarugos, os materiais antes da laminação, é de grande importância. Os tarugos são normalmente inspecionados por equipamentos automáticos de inspeção magnaflux e condicionados para a remoção dos defeitos superficiais.
Devido à grande variedade de requisitos dos fios-máquina, os moinhos de fio-máquina são geralmente projetados com a versatilidade em mente. Equipamento confiável, consistência de processo, flexibilidade de produção e minimização de resíduos, tudo isso é necessário em um moinho de fio-máquina. Além disso, todas as faixas de tamanho, materiais e ligas precisam ser laminados de forma eficiente e com alta produtividade nos moinhos de fio-máquina. A fábrica deve maximizar a produtividade por meio da otimização do processo e do tempo de inatividade minimizado e da interligação perfeita dos estágios de produção. O layout complexo do moinho precisa ser otimizado para garantir o tempo necessário para cada etapa do processo, os perfis de temperatura necessários e áreas de transferência eficientes. Uma troca mais rápida é a chave para a flexibilidade do moinho. A fábrica deve ser capaz de converter para o próximo pedido enquanto ainda processa o atual e mudar a linha de um produto para outro praticamente sem tempo de inatividade. Um layout típico de um moinho de fio-máquina com capacidade de 400.000 toneladas por ano é mostrado na Figura 1.
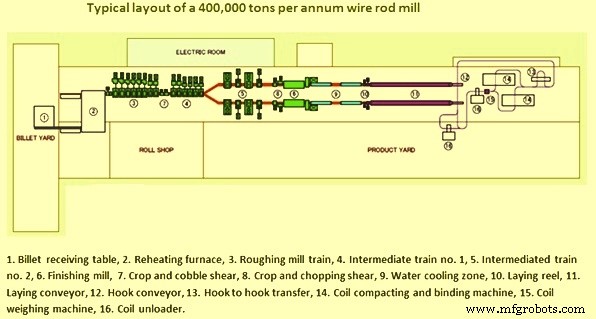
Fig 1 Layout típico de um moinho de fio-máquina
Além disso, é necessário que os moinhos de fio-máquina sejam capazes de atingir uma precisão muito alta com carrinhos de laminação projetados para suportar altas cargas e mudanças de temperatura. A combinação de tecnologia de processo, equipamentos mecânicos, componentes elétricos e funções de automação é um aspecto crucial para o projeto do moinho. Estes juntos permitem uma ampla gama de condições de processo para as qualidades desejadas dos produtos de fio-máquina. Além disso, o moinho deve ser otimizado para o custo. A otimização de custos tem muitas facetas, incluindo a maximização do rendimento controlado pelo processo, redução do tempo de inatividade e controles de custos de manutenção.
Além disso, para atender aos requisitos necessários, o aço usado para laminação de fio-máquina pode precisar de elementos de liga suficientes que possam dar reforço à austenita durante a laminação a quente e deterioração da conformabilidade a frio e do limite de trefilação, devido ao aumento da dureza do fio laminado . Portanto, tratamentos térmicos caros (por exemplo, recozimento) são realizados para amolecer o fio-máquina laminado a quente. Para reduzir os custos de produção, através de uma simplificação de todo o processo, são aplicados sistemas de refrigeração controlados on-line, mas são necessárias melhorias adicionais para satisfazer os clientes. Os produtores de fio-máquina mudaram para produtos de fio-máquina mais sofisticados com tratamento térmico em linha, bem como tecnologias de laminação de precisão baseadas em controle de tensão mais AGC (controle automático de bitola). O aquecimento uniforme dos tarugos e o controle de tensão durante a laminação a quente são geralmente utilizados para atingir a precisão dimensional necessária, pois na prática é difícil garantir tolerâncias mais estreitas pelos laminadores de fio-máquina convencionais durante longos períodos de produção.
Nos moinhos de fio-máquina, é normal o uso de rolos com ranhuras. As sequências de ranhuras comuns nos moinhos intermediários são “oval quadrado” e “oval falso redondo (redondo)”. Também é difundido o uso de sequências 'diamante-quadrado', diamante-diamante e 'ranhura de caixa' a montante no desbaste. Existem outros tipos de designs de passe também. A sequência patenteada de passagem de rolo oval-round-round-round da Morgan foi projetada para laminação de alta redução e para processamento normalizado e termomecânico, melhorando a qualidade da superfície e prolongando a vida útil do rolo. O projeto do roll pass visa garantir um alto rendimento e qualidade adequada dos fios-máquina, o que é de extrema importância para manter o custo de produção sob controle.
Para melhorar a produtividade, os moinhos de fio-máquina normalmente se concentram em minimizar o tempo de inatividade do moinho. A eficácia desse foco geralmente é aprimorada pela redução do tempo e da necessidade de troca de rolos quando novas dimensões finais e novos tipos e formatos de aço devem ser fabricados. Isso é conseguido melhorando a faixa de trabalho, também chamada de flexibilidade da série. Maior flexibilidade é alcançada quando grandes quantidades de diferentes tipos de aço, com diferentes formas e dimensões são laminadas com uma alteração mínima do cronograma de laminação. Cada classe de aço é caracterizada por sua forma específica de fluxo de material, como espalhamento diferente, ao passar pela fenda do rolo. Além disso, o tempo de partida e o tempo de espera pela temperatura de laminação correta, dependendo do grau real do aço, precisam ser reduzidos. No entanto, ciclos de aquecimento diferentes ainda causam tempos de inatividade muito altos quando uma ampla gama de classes deve ser laminada. Para atender às demandas do mercado atual, que incluem lotes menores e diversos tipos de aços, tornou-se uma necessidade que os modernos laminadores de barras apresentem um alto grau de flexibilidade.
Avanços nas tecnologias de produção de fio-máquina (por exemplo, resfriamento interstand, adição de equipamentos de dimensionamento após bloco de acabamento convencional, instalações de resfriamento controlado aprimoradas) permitem a introdução de laminação de precisão, bem como processo de controle termomecânico (TMCP), expandindo a faixa de baixa e fio-máquina de aço de médio carbono e fabricação de fio-máquina adequados para rotas de produção simplificadas ou processamento direto.
Por meio de tecnologias de laminação de alta precisão, é possível obter baixas temperaturas de laminação de acabamento, além de melhores dimensões do produto (tolerâncias). A localização da calibragem compacta após o bloco de acabamento é vantajosa não só para obter maior produtividade, mas também para melhorar as propriedades metalúrgicas. A capacidade de laminação de produtos a baixas temperaturas permite aproveitar os benefícios da laminação termomecânica no refinamento de grãos para aumentar a ductilidade e encurtar os processos de tratamento térmico subsequentes.
No entanto, existem vários parâmetros que precisam ser considerados no processo termo-mecânico. Estas são (i) localização do equipamento de laminação, (ii) localização do resfriamento a água, (iii) taxas de laminação e (iv) temperaturas de laminação de acabamento.
Por exemplo, a introdução de um mini-bloco ajuda a reduzir as temperaturas de laminação de acabamento abaixo de 950°C em um moinho de fio-máquina existente que está tendo limitações na separação de força e potência e, portanto, com temperaturas de laminação de acabamento superiores a 1000°C. No entanto, é necessária uma distância adequada entre o moinho sem torção e o moinho de calibragem para o uso de resfriamento a água, a fim de reduzir a temperatura do material rodante. A localização do moinho de dimensionamento é importante para dar tempo para que a haste seja controlada, resfriada e equalizada antes da redução final, reduzindo assim o risco de superaquecimento do núcleo da haste. Isso é crucial para aços especiais que são sensíveis ao engrossamento de grãos em altas temperaturas de acabamento.
Também é necessária uma combinação crítica de tensão e temperatura de acabamento para promover uma microestrutura uniforme. Os processos de recristalização estática e metadinâmica são fortemente dependentes da temperatura e da tensão acumulada. Durante o dimensionamento da haste, sem uma quantidade suficiente de tensão, ou o processo de recristalização não é adequadamente promovido ou um baixo número de sítios recristalizados é nucleado. Consequentemente, grãos grosseiros localizados podem ocorrer.
A introdução do processamento termomecânico de fio-máquina leva a uma maior velocidade de acabamento e granulometria de austenita mais fina. A consequência é que um padrão de resfriamento diferente deve ser usado ao longo do transportador devido a um comportamento de transformação diferente e sobreposição de envoltório (acúmulo de bobina na camada de loop). A este respeito, modelos matemáticos capazes de prever a evolução da austenita durante a laminação a quente e resfriamento controlado de fio-máquina, podem ser efetivamente aplicados, juntamente com a planta atual e dados tecnológicos, para prever o efeito da configuração da planta, práticas de laminação e resfriamento na evolução e uniformidade da microestrutura do fio-máquina.
Propriedades metalúrgicas superiores
Com o moinho de redução e dimensionamento de fio-máquina localizado entre o bloco de acabamento e o cabeçote de assentamento, as zonas de resfriamento a água e equalização fornecem temperaturas de entrada controladas, que podem ser tão baixas quanto 750 graus C, para obter uma estrutura de grão fino. As propriedades aprimoradas resultantes podem reduzir ou eliminar os custosos processos de recozimento a jusante. Vários tipos de aço podem se beneficiar da laminação a baixa temperatura, conforme indicado abaixo.
- No caso de varetas a frio, os benefícios incluem a necessidade de menos descamação, reduzindo assim as perdas. Descascando, as perdas de material podem ser reduzidas em até 30% para certos aços inoxidáveis e produtos de titânio. Também a melhor conformabilidade e a excelente tolerância podem resultar em economia de refugo de até 50% para processos posteriores, como a fabricação do parafuso.
- No caso do fio-máquina de aço mola os benefícios incluem a redução da formação de martensita, principalmente em fio-máquina de pequeno diâmetro. Também nesses fios-máquina há menor necessidade de tratamento térmico frequente de pré-estiramento.
- No caso de fio-máquina com qualidade de eletrodo, os benefícios incluem microestrutura refinada que permite melhor trefilação e tamanho de grão mais fino que suprime a formação de martensita.
- No caso de fio-máquina de qualidade de aço de rolamento, os benefícios incluem a formação de microestrutura pseudo-esferoidizada com carbonetos finos e bem dispersos. Também evita o recozimento de esferoidização a jusante, eliminando ou reduzindo totalmente as temperaturas e os tempos de imersão. Também reduz a temperabilidade, o que elimina a formação de martensita.
- No caso de fio-máquina de qualidade de trefilação, o processamento a baixas temperaturas através do moinho de redução e dimensionamento pode fornecer várias vantagens para a planta de trefilação a jusante. São eles (i) melhor desincrustação mecânica, com quebra uniforme de incrustações, redução da martensita na superfície da haste e diminuição das quebras de arame, (ii) melhor uniformidade de tração como resultado da excelente tolerância de tamanho e ovalização, (iii) aumento da vida útil da matriz, com melhor lubrificação e desenho uniforme e (iv) configuração otimizada da matriz com tamanhos de haste não padronizados por meio de laminação de tamanho livre.
Muitos moinhos de fio-máquina de hoje têm sistemas de medição de bitolas em linha e procedimentos de ajuste de folgas em linha. Esses sistemas possibilitam o dimensionamento no primeiro fio-máquina laminado e o controle total da laminação sem a necessidade de barras de teste de laminação.
Em moinhos de fio-máquina, os métodos tradicionalmente disponíveis para detectar defeitos de superfície são brutos, que incluem gravação e limar, testes de recalque, testes visuais, etc. o ambiente hostil em que o pessoal de controle de qualidade tem que trabalhar. Os consumidores de produtos de arame laminado a quente estão sempre exigindo melhor qualidade de superfície. Esforços para melhorar a qualidade do produto embarcado necessariamente se afastaram da mera inspeção para a melhoria do processo.
Escondidos dentro dos processos de fusão e laminação são fontes potenciais de defeitos de superfície. Encontrá-los requer engenhosidade. Qualquer pessoa familiarizada com a melhoria do processo entende a importância de uma boa variável de resposta pela qual os efeitos das mudanças no processo podem ser medidos com segurança.
Faz pouco bem e frequentemente muito mal ajustar as variáveis do processo quando não há uma maneira clara de medir os resultados da mudança. Dadas as condições do moinho descritas acima, a variável de resposta para a qualidade da superfície tem sido elusiva, mas um sistema de inspeção de superfície por correntes parasitas em linha mostrou-se promissor. É o único método disponível nos dias de hoje para detectar potenciais problemas de produção antes que eles levem a graves perdas de qualidade e material e ao mesmo tempo. Este método também realiza a detecção confiável de falhas no produto laminado. Ele provou ser um dispositivo muito útil para encontrar muitos tipos de defeitos superficiais em bobinas de fio-máquina laminadas a quente. Ainda não está claro se ele pode detectar costuras bem enroladas. Ainda mais impressionante, no entanto, foi sua capacidade de indicar os efeitos de mudanças deliberadas ou não planejadas nos processos que produziram a bobina.
Processo de manufatura
- Tipos e usos do fio de molibdênio
- O que são laminadores e seus tipos?
- 5 Benefícios e aplicações dos EDMs com fio
- Epóxi RM511A - Haste
- Liga 3 (C17510) TB00 Haste e Barra
- Liga 3 (C17510) TD04 Haste e Barra
- UGI 4362, barras laminadas a quente, barras torneadas e fio-máquina
- AMPCO® 8 Varas extrudadas e trefiladas
- solução UGI® 4062 recozida, barras laminadas a quente e fio-máquina
- Diferenças e aplicações do Sinker EDM e Wire EDM