Sistema de Combustão de um Forno de Reaquecimento
Sistema de Combustão de um Forno de Reaquecimento
A principal função de um forno de reaquecimento é elevar a temperatura dos aços semi-acabados (tarugos, blocos, placas ou redondos) tipicamente para temperaturas entre 1000°C e 1250°C, até que seja plástico o suficiente para ser laminado na temperatura desejada. seção, tamanho ou forma no laminador a quente. O forno de reaquecimento também deve atender a requisitos e objetivos específicos em termos de taxas de aquecimento por motivos metalúrgicos e de produtividade. No forno de reaquecimento há um fluxo contínuo de material que é aquecido até a temperatura desejada à medida que percorre o forno.
As operações de laminação a quente exigem aços semi-acabados reaquecidos de alta qualidade com o menor custo possível e com a taxa de produção ideal do laminador. Os fornos de reaquecimento utilizados para aquecer os aços semi-acabados em um laminador a quente consomem grande quantidade de energia e simultaneamente geram grande quantidade de poluentes. Devido a isso, há a necessidade de buscar formas de reduzir o consumo de energia, bem como os poluentes e, consequentemente, os custos. Isso pode ser feito melhorando a eficiência de combustível dos fornos de reaquecimento.
O sistema de combustão do forno de reaquecimento tem uma grande influência tanto na qualidade do produto de aço semi-acabado reaquecido quanto na quantidade de combustível necessária para o reaquecimento. As expectativas importantes de um forno de reaquecimento hoje não são apenas reduzir a emissão de poluentes e o consumo de energia, mas também melhorar a alta qualidade do produto de aço aquecido, confiabilidade, temperatura uniforme, fluxo de calor e segurança do equipamento e pessoal. Todos estes são os principais fatores que têm um efeito considerável no sistema de combustão do forno de reaquecimento.
As três coisas básicas que são necessárias para iniciar e sustentar a combustão são (i) combustível, (ii) oxigênio e (iii) energia suficiente para a ignição. O processo de combustão é mais eficiente se o combustível e o oxigênio puderem se encontrar e reagir sem quaisquer restrições. No entanto, em aplicações práticas de aquecimento não é suficiente considerar apenas a combustão eficiente, mas os aspectos de transferência de calor também devem ser levados em consideração. A seguir estão os parâmetros importantes para um sistema de combustão no forno de reaquecimento.
- Quantidade de calor necessária para ser transmitida ao material de carga.
- A geração de calor dentro do forno é necessária não apenas para aquecer o material de carga, mas também para superar todas as perdas de calor.
- Transferência de parte do calor disponível dos gases do forno para a superfície do material de carga de aquecimento.
- Equalização da temperatura dentro do material de carga.
- Perdas de calor do forno através das portas e paredes, etc.
- Calor transportado pelos gases de escape.
- Emissões de poluentes (por exemplo, NOx etc.) causadas pelos gases de escape.
O ar composto de oxigênio diluído com 78% de nitrogênio e 1% de argônio não oferece condições ideais para combustão e transferência de calor. O nitrogênio do ar é aquecido durante o processo de combustão e para evitar a perda de energia transferida para o nitrogênio torna-se necessário recuperar essa energia para economizar combustível.
O calor é transferido para uma superfície de produto sólido por convecção, condução e radiação. A transferência de calor dentro do produto é apenas por condução. Isso implica que a superfície do produto, que muda ao longo do tempo quando aquecida, as dimensões e o material dos aços semi-acabados são importantes, assim como as dimensões internas do forno.
Para um aquecimento eficiente e uniforme, a composição do gás e o padrão de fluxo dentro do forno são importantes. Uma estratégia de aquecimento tradicional, não otimizada, pode parecer suficiente sob condições de estado estacionário, mas não fornece qualidade e desempenho de custo ideais quando há interrupções na produção, variação nos graus ou dimensões do produto ou variação nas temperaturas de saída desejadas. Na situação atual, é necessária uma solução para fornecer aquecimento da mais alta qualidade e menor custo sob todas as condições com o mínimo impacto no meio ambiente.
Atualmente, devido ao aquecimento global, regulamentações ambientais rígidas exigem a minimização do consumo específico de combustível e, ao mesmo tempo, reduzem os poluentes, incluindo os óxidos de nitrogênio (NOx). Objetivos conflitantes de consumo mínimo de energia e descarga de poluentes e, ao mesmo tempo, atender aos requisitos de produção, desafiam os operadores e os fornecedores de equipamentos a usar todas as tecnologias disponíveis para projetar sistemas de combustão eficientes em termos de energia e ambientalmente compatíveis nos fornos de reaquecimento.
Com projetos de queimadores convencionais, esses dois objetivos são frequentemente conflitantes. No entanto, usando a mais recente tecnologia e projetos de queimadores com técnicas de combustão de chama difusa, agora estão sendo alcançados altos níveis de eficiência através do ar de combustão pré-aquecido com emissões de NOx correspondentemente baixas.
Existem muitos tipos de fornos de reaquecimento que estão em operação nas siderúrgicas. A estrutura de um forno de reaquecimento consiste em várias zonas. Os fornos de reaquecimento são normalmente projetados com múltiplas zonas de aquecimento, nomeadamente (i) zona de pré-aquecimento, (ii) zonas de aquecimento e (iii) zonas de imersão. As peças de aço semiacabadas são alimentadas na zona de pré-aquecimento e movidas lentamente pelas zonas de aquecimento e imersão, sequencialmente. As peças de aço são aquecidas aproximadamente à temperatura alvo nas zonas de pré-aquecimento e aquecimento e são embebidas na zona de imersão para manter a temperatura uniforme através das peças de aço, que são aquecidas principalmente pela transferência de calor radiativa do gás circundante. Cada zona tem uma finalidade diferente e as zonas normalmente têm controles de queimadores independentes, mesmo que os produtos da combustão se movam pelas zonas anteriores para sair da chaminé. A relação ar-combustível é normalmente definida com a intenção de produzir um nível desejado de excesso de oxigênio no gás de combustão. O objetivo é garantir que todo o combustível seja queimado dentro do forno de reaquecimento, mas ao mesmo tempo evitar excesso de ar de combustão que reduz a eficiência de aquecimento do forno.
A construção multizona dos fornos de reaquecimento torna a otimização da combustão muito difícil devido à interação da zona, mudanças constantes nos requisitos do produto, mudança na velocidade de extração e o próprio ato de extrair barras. Existem muitos problemas que podem causar um desvio no resultado final. Algumas dessas questões são as seguintes.
- Medição imprecisa de gás ou ar
- Mudanças na umidade do ar
- Quantidades significativas de combustível ou oxigênio migrando de outra zona do forno
- No caso de ar pré-aquecido via recuperadores, pode haver (i) vazamentos em tubulações ou recuperadores, (ii) fatores de correção de temperatura fora de calibração e (iii) variações sazonais
- Desgaste ou danos na válvula e atuadores
- Vazamentos no forno
Além disso, com base nas capacidades do queimador e nos níveis desejados de excesso de oxigênio, são necessárias proporções estequiométricas fixas para cada zona. As proporções podem diferir de zona para zona pelos dois motivos a seguir.
- O excesso de oxigênio desejado pode ser diferente para cada zona devido à relação entre o nível de oxigênio, a temperatura e a formação de incrustações.
- Pode ser necessário ajustar a estequiometria para diferentes taxas de desligamento do queimador devido à capacidade de mistura dos queimadores.
Normalmente, o operador do forno de reaquecimento não sabe se o oxigênio está próximo ou próximo do ponto de ajuste desejado devido à falta de feedback do processo em tempo real. As consequências de operar um forno com esse nível de incerteza podem ser significativas. Considerando as reações do queimador e os produtos teóricos da combustão, pode haver possibilidades quando a estequiometria varia fora do set point. Se o nível real de oxigênio no gás de combustão exceder o ponto de ajuste, a eficiência é reduzida, adicionando custos desnecessários de combustível. Se o nível real de oxigênio for inferior ao ponto de ajuste, os níveis de monóxido de carbono aumentam, o que cria uma condição de operação insegura e uma eficiência reduzida devido ao combustível não queimado que sai do forno. Além disso, os controladores da razão ar-combustível nos fornos de reaquecimento estão continuamente ajustando seus pontos de ajuste para atender às mudanças nas demandas do forno e, portanto, o estado de oxidação também está sempre mudando. Na prática, o forno de reaquecimento apresenta algum grau de combustão incompleta. Existem vários problemas que contribuem para uma mistura pobre. Essas questões são apresentadas a seguir.
- Eficiência do queimador
- Redução
- Velocidades do ar e do combustível incomparáveis
- Controle de proporção fora de ajuste
- Vazamentos no forno
A combustão incompleta devido à má mistura também pode resultar na coexistência de monóxido de carbono e oxigênio. Na prática, é comum ter tanto monóxido de carbono quanto oxigênio presentes. Portanto, a operação ideal de um forno de reaquecimento requer dados do produto de combustão em tempo real com os sensores adequados.
Um recuperador é normalmente usado nos fornos de reaquecimento como uma unidade de recuperação de calor residual para obter alta eficiência térmica e conservação de energia. O calor residual recuperado é usado para pré-aquecer o ar de combustão, que é então alimentado a um queimador. O ar pré-aquecido resulta em economia de energia e bom desempenho de combustão. No entanto, as desvantagens incluíam a incorporação de um sistema de recuperação de calor em larga escala para o calor residual. Além disso, a temperatura do ar pré-aquecido é normalmente apenas em torno de 600 graus C a 700 graus C na melhor das hipóteses.
Há dois grandes desenvolvimentos na área de reaquecimento de aço semi-acabado no passado recente. Estes desenvolvimentos são nomeadamente (i) combustão de ar a alta temperatura, e (ii) combustão de combustível de oxigénio.
Combustão de ar de alta temperatura
A tecnologia de combustão de ar de alta temperatura (HiTAC) utiliza ar pré-aquecido em excesso de 1000 graus C. A adoção desta tecnologia de combustão no forno de reaquecimento permite que a usina de aço contribua muito para a redução simultânea do consumo de energia, bem como a redução das emissões de dióxido de carbono e óxidos de nitrogênio. A utilização da tecnologia HiTAC também resulta na redução do tamanho físico do forno de reaquecimento em comparação com o tipo tradicional de forno.
O conceito básico da tecnologia HiTAC é que a combinação de recuperação máxima de calor residual por regenerador de alto ciclo e mistura controlada de ar de combustão altamente pré-aquecido com gases queimados produz chamas uniformes e de temperatura relativamente baixa.
O queimador regenerativo utilizado na tecnologia HiTAC possui características de combustão únicas. Essas características resultam em uma chama eficiente e limpa com um perfil uniforme de temperatura e fluxo de calor. Essas propriedades resultam em uma taxa de produção melhorada e melhor qualidade do produto e um ambiente muito mais suave para os componentes do forno. A tecnologia HiTAC pode resultar em custos operacionais reduzidos.
A tecnologia HiTAC fornece estabilidade de chama significativamente maior em todas as misturas ar-combustível (incluindo misturas de combustível muito pobres), maior transferência de calor e baixa perda de calor da chaminé (calor residual). O método fornece um meio de recircular o calor do lado de alta temperatura (gás queimado) de volta para o lado da mistura não queimada usando um método de troca de calor apropriado. O pré-aquecimento confere entalpia adicional à mistura não queimada sem diluição pelos produtos da combustão.
Com a tecnologia HiTAC, há recursos de chama significativamente diferentes, estabilidade de chama, emissões reduzidas e economia significativa de energia. A cor da chama é muito diferente do azul ou amarelo normalmente observado. Sob certas condições, foi observada chama de cor verde azulada e verde usando combustíveis típicos de hidrocarbonetos. Em contraste, a oxidação sem chama (ou incolor) do combustível também foi observada.
As principais características da tecnologia HiTAC são apresentadas abaixo.
- Combustão de hidrocarbonetos com temperaturas de pré-aquecimento do ar muito altas usando um regenerador no queimador.
- O calor sensível dos produtos de exaustão é usado para aquecer o ar de combustão (temperatura superior a 1000 graus C). A tecnologia tenta pré-aquecer o ar próximo à temperatura alvo do forno.
- As temperaturas dos gases de escape estão em torno de 150°C a 200°C.
- Extraia a maior parte da energia do combustível para o processo de aquecimento.
- Há uma economia de combustível entre 50% (substituição do ar frio) e 30% (substituição do ar dos recuperadores).
- Há uma distribuição de calor muito uniforme no forno.
- A geração de NOx é muito baixa.
No queimador regenerativo, há uma configuração de pares com cada ciclo de queimador entre a queima e a exaustão. O ar de combustão circula entre dois conjuntos de caminhos no queimador. Ele entra através de um conjunto e pega calor do material regenerador no queimador. Os gases do produto da combustão saem pelo outro conjunto e aquecem o material regenerador a alta temperatura. No ciclo seguinte, o ar de combustão e os produtos de combustão trocam de caminho.
O conceito do HiTAC é ilustrado na Fig. 1 e é comparado com o da combustão do forno de reaquecimento convencional. Chamas de temperatura extremamente alta geralmente são geradas em fornos, se ocorrer combustão direta entre combustível e ar fresco de alta temperatura. Como resultado da geometria modificada do forno, não apenas a extinção das chamas de base ocorre pelo movimento de cisalhamento do ar de entrada de alta velocidade, mas também a diluição do ar com gás queimado (BH) deve ocorrer antes da combustão, separando o combustível e as entradas de ar. Deve-se notar que essas são as condições nas quais a combustão comum não pode ser mantida com ar à temperatura ambiente. Além disso, o combustível injetado separadamente na fornalha também arrasta gás queimado na fornalha e algumas alterações no combustível, como pirólise, decomposição e vaporização do combustível líquido, se houver, durante esse período de preparação. Reações de combustão fracas podem ocorrer entre combustível e produto arrastado (B*F) e a combustão principal segue na zona de mistura de combustível e ar diluído com grande quantidade de gás queimado (B*F*BH). A mudança de chama devido a uma baixa concentração de oxigênio causada pela alta taxa de reciclagem do gás queimado provavelmente produz uma zona de reação ampliada, onde reações relativamente lentas podem estar ocorrendo. Na combustão estabelecida sem ar pré-aquecido, a combustão direta entre combustível e ar fresco (F*A) ocorre no campo próximo do queimador. Depois disso, alguma combustão em condição diluída com gases queimados pode seguir na porção a jusante da chama devido ao arrastamento de gás queimado recirculado pelo ar de combustão que entra. A combustão (F*A) nas proximidades do queimador mostra a temperatura máxima no forno, e a maioria dos óxidos nítricos emitidos do forno são formados ali. No entanto, a combustão nesta região é essencial para sustentar a combustão no forno, e a chama inteira não pode existir se ocorrer extinção nesta porção.
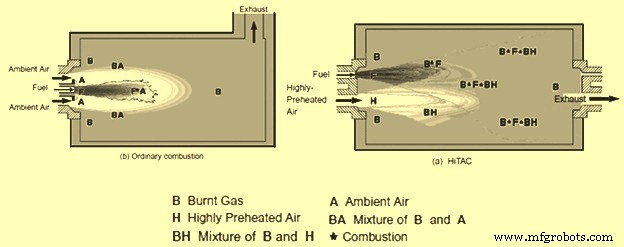
Fig 1 Conceito de mistura e combustão com tecnologia HiTAC
Apesar do uso de ar altamente pré-aquecido, a temperatura média, bem como a temperatura de pico instantânea, é consideravelmente menor no HiTAC do que na combustão comum.
Sistema de combustão oxi-combustível
Oxi-combustível refere-se à prática de substituir totalmente o ar como fonte de agente oxidante para combustão por oxigênio que pode ser produzido por tecnologia criogênica ou tecnologias de adsorção. A vantagem geral de substituir o ar por oxigênio é que a quantidade de nitrogênio trazida para o processo de combustão com ar é quase ou completamente eliminada. A redução do nitrogênio na combustão permite uma maior temperatura da chama e eficiência de combustão, uma vez que o menor volume do gás de combustão reduz a quantidade de calor retirado da chama e perdido para a exaustão. Assim, as vantagens do uso de oxi-combustível em comparação com a combustão de ar-combustível são as seguintes.
- Redução no consumo de energia
- Taxa de aquecimento aprimorada resultando em maior produção (sem aumento no ponto de ajuste de temperatura do forno)
- Redução nas emissões do forno
Além das vantagens acima, o uso da combustão de oxi-combustível às vezes pode resultar em menor investimento de capital em comparação com outros métodos de melhoria da eficiência, como recuperadores ou equipamentos de controle de emissões. A combustão de oxi-combustível também pode resultar em menor perda de escala devido ao melhor controle e menor tempo de aquecimento.
Em comparação com o ar-combustível, a combustão de oxi-combustível tem uma pressão parcial muito maior em relação aos dois produtos de combustão, CO2 e H2O. Isso melhora a taxa de transferência de calor. Como os gases de exaustão não são diluídos com nitrogênio, a fase gasosa tem um papel mais ativo no processo de transferência de calor, não apenas porque a condutividade de transferência de calor e a capacidade térmica de CO2 e H2O são maiores, mas também porque ambos são de alta irradiação de calor três gases atômicos.
O padrão de fluxo em um forno de oxi-combustível é vantajoso em comparação com o ar-combustível. O volume de gases de escape é reduzido em 70% a 80% porque não há nitrogênio presente e devido à economia de combustível. Assim, o tempo de residência do gás é maior, com mais tempo de transferência de calor para o produto. O produto é de fato imerso em um fluido de exaustão gasoso composto por CO2 e H2O, ou seja, um ambiente úmido com maior capacidade de transferência de calor.
Ao comparar um forno de oxi-combustível com um forno de ar-combustível, ambos ajustados na mesma temperatura do forno, o material atinge um valor de ponto de ajuste mais rápido no forno de oxi-combustível. Isto é devido às propriedades do gás.
Com a combustão de oxi-combustível há um aumento substancial no calor disponível em comparação com a combustão de ar-combustível. O aumento do calor disponível está diretamente relacionado a reduções no consumo de energia e aumentos no rendimento do forno.
Um aumento no calor disponível de combustão significa que menos calor é perdido para a exaustão e uma porcentagem maior da entrada total de energia é deixada para fazer o trabalho no forno de reaquecimento. Assim, quando o calor disponível é aumentado, a quantidade total de energia necessária para realizar uma quantidade constante de trabalho é reduzida.
As economias de energia variam dependendo do tipo de combustível, taxa de combustão existente e temperatura do ar de combustão. Outros fatores, como a redução no tamanho da porta de combustão e a perda de radiação, podem afetar as taxas reais de redução de energia com oxi-combustível. Outro impacto do aumento da eficiência de combustão com oxi-combustível é a capacidade de aumentar a taxa de aquecimento e obter mais rendimento do forno.
O limite prático para o aumento da produção depende da capacidade do material de aço semi-acabado de absorver calor e do tempo e temperatura em que o material de aço semi-acabado é exposto ao calor. A experiência de várias instalações de oxi-combustível indica que o rendimento do material pode ser aumentado na maioria das operações sem aumentar o ponto de ajuste da temperatura do forno, com exceção dos fornos que já estão atendendo a um limite de rampa de temperatura definido. Além do aumento do calor disponível, a maior temperatura da chama do oxi-combustível e o potencial de radiação dos gases de combustão têm um impacto positivo na capacidade de aquecimento e na taxa de produção.
A temperatura da chama do oxi-combustível é geralmente de 500°C a 800°C mais alta do que a temperatura da chama do ar-combustível. Como a transferência de calor por radiação depende da diferença de temperatura da fonte para o receptor até a quarta potência, a combustão de oxi-combustível resulta em um grande aumento do potencial de radiação da chama para o material. Os produtos de combustão do oxi-combustível também são melhores fontes de transferência de calor radiante. Isso ocorre porque a maioria dos produtos de combustão ar-combustível é nitrogênio, que não é um mecanismo eficiente de transferência de calor radiante como o dióxido de carbono e o vapor de água que compõem a maioria dos produtos de combustão oxi-combustível.
Em alguns casos, a produção do forno é limitada pela quantidade de emissões gasosas permitidas para sair do forno. A combustão de oxi-combustível também pode ser um meio de reduzir as emissões do forno e permitir o aumento da capacidade de produção dentro de um limite de emissão permitido.
O volume de gases de escape é substancialmente menor com oxi-combustível. O volume total de gases de escape com oxicombustível é geralmente 70% a 90% inferior ao volume total de gases de escape ar-combustível. Em muitos casos, a redução do volume de gases de escape por si só pode ser benéfica, especialmente quando o equipamento de controle de poluição existente é limitado e/ou onde as emissões de partículas são uma preocupação. Um resultado mais importante com a combustão oxi-combustível é a menor emissão de certos constituintes dos gases de escape. O resultado mais óbvio do uso da combustão oxi-combustível é a redução do consumo de combustível. Com a redução do consumo de combustível a emissão de CO2 é menor em um determinado tempo ou por unidade de material semi-acabado de aço aquecido. Embora a geração de CO2 não seja atualmente uma grande preocupação, o aquecimento global e as mudanças climáticas que estão ocorrendo indicam que condições mais rigorosas de emissão de CO2 podem ser um fator no futuro próximo. Uma preocupação mais imediata de muitos operadores de fornos é a emissão de NOx. Com a combustão de oxi-combustível, a pressão parcial de nitrogênio nos produtos de combustão é drasticamente reduzida, diminuindo o potencial de formação de NOx mesmo em temperaturas de chama elevadas. Muitos fatores afetam a taxa de emissão de NOx de fornos a oxi-combustível. A pureza do produto oxigênio é um desses fatores. No entanto, o principal fator para minimizar as emissões de NOx de oxi-combustível é o controle da pressão do forno. Vazamento de ar secundário combinado com alta temperatura de chama de oxi-combustível pode reduzir bastante o impacto da combustão de oxi-combustível como uma técnica de controle de NOx.
As chamas de oxi-combustível têm uma temperatura mais alta com menos volume e comprimento do que as chamas de ar-combustível. A característica de chama com oxi-combustível deve ser considerada ao projetar sistemas de queimadores de oxi-combustível para aplicação de reaquecimento de materiais de aço. Geralmente, o reaquecimento do aço requer uma distribuição uniforme da temperatura, de modo que o superaquecimento ou subaquecimento localizado no produto de aço reaquecido seja evitado. O tipo e a colocação dos queimadores de oxi-combustível dependem do tipo de forno de reaquecimento e da proximidade das chamas aos materiais de aço semi-acabados.
A recirculação dos produtos de combustão promove o movimento dos gases na câmara de aquecimento, minimizando assim as diferenças de temperatura. Além disso, a recirculação dos gases de combustão na chama de oxi-combustível reduz a temperatura de pico da chama e promove um perfil de radiação de chama mais uniforme para proteger o produto mais próximo do queimador de superaquecimento. Existem vários projetos de queimadores de oxi-combustível disponíveis para obter o efeito de recirculação, incluindo um bico patenteado junto com outros projetos que utilizam o momento da chama de oxi-combustível para produzir recirculação de gás.
Embora forneça benefícios substanciais para a eficiência, o baixo volume de produtos de combustão com combustão oxi-combustível precisa de atenção especial ao projetar sistemas de controle de combustão. O controle adequado da taxa de combustão é fundamental para o processo de reaquecimento, pois os produtos da combustão compõem a atmosfera de aquecimento e, em última análise, afetam a taxa e o tipo de formação de incrustações. Em sistemas de combustão ar-combustível, o alto volume de nitrogênio trazido para o processo de combustão com ar fornece um amortecedor ou fator de segurança contra mudanças na relação ar/combustível. Com o oxi-combustível este amortecedor é quase completamente eliminado. Isso significa que uma mudança percentual na proporção de oxigênio para combustível com combustão oxi-combustível terá um impacto maior na atmosfera do forno de aquecimento do que a mesma mudança com combustão ar-combustível.
Um bom controle da atmosfera do forno com combustão oxi-combustível precisa de um nível mais alto de precisão para o sistema de controle do que com combustão ar-combustível. A compensação de fluxo de massa é geralmente necessária para atender a precisão necessária para manter uma boa atmosfera do forno com combustão de oxi-combustível. Outra variável importante para o controle da combustão do oxi-combustível envolve os sistemas de exaustão do forno e controle de pressão.
O volume de gases de escape com combustão oxi-combustível reduz na faixa de 10% a 30% do volume de exaustão da combustão ar-combustível, dependendo da quantidade de ganhos de eficiência térmica. Isso significa que os projetos existentes usados para controlar a pressão do forno com combustão ar-combustível não são, na maioria dos casos, adequados para manter um bom controle de pressão do forno ao converter para combustão oxi-combustível. Especificamente, a faixa de controle da instrumentação de controle de pressão com a maior porta de combustão e tamanhos de amortecedor usados com combustão ar-combustível reduz a ponto de ser ineficaz com o volume de exaustão da combustão oxi-combustível. Portanto, é necessário reduzir o tamanho da porta de combustão ao converter para combustão oxi-combustível ou compensar o menor volume de exaustão ao projetar novas instalações de fornos de reaquecimento. A falta de um bom controle de pressão do forno pode resultar em vazamento de ar terciário que pode fornecer uma fonte de nitrogênio para formação adicional de NOx, minimizando ou eliminando o potencial de redução de emissões. O vazamento de ar no forno de reaquecimento também influencia a atmosfera do forno e apresenta complicações para o controle de qualidade da superfície do aço.
A taxa e o tipo de formação de incrustações são uma consideração importante para as operações do forno de reaquecimento de aço, independentemente do tipo de sistema de combustão. Além do tipo de liga de aço, a atmosfera do forno juntamente com a taxa de aquecimento são os principais fatores que governam a formação de incrustações. Um bom controle da taxa de combustão e da pressão do forno é necessário para manter o controle na formação de incrustações e na qualidade da superfície do aço. No entanto, a atmosfera produzida pela combustão oxi-combustível é diferente da atmosfera com combustão ar-combustível mesmo em condições ideais. .
Processo de manufatura
- Sistema de aquecimento solar
- C# usando
- Sistema de estacionamento inteligente
- Sistema de automação, medição e controle de processos de alto forno
- Forno de Otimização de Energia
- Fornos de reaquecimento e seus tipos
- Sistema Básico de Recuperação e Limpeza de Gás de Forno de Oxigênio
- Entendendo o sistema de transporte
- Entendendo o sistema de resfriamento em motores de combustão interna
- Entendendo o Sistema de Suspensão