Processos de preparação e triagem de sucata de aço e sucata
Processos de separação e preparação de sucata de aço e sucata
A reciclagem de sucata de aço está recebendo um impulso crescente nos dias de hoje devido ao foco de uma iniciativa ambiental emergente, uma vez que o aumento do consumo de sucata reduz a necessidade de extração adicional de recursos e, portanto, reduz o impacto ambiental. A reciclagem de sucata de aço também faz parte de uma gestão sensata dos recursos de ferro. A recuperação de 1 tonelada de aço da sucata conserva minério de ferro, carvão e calcário. De acordo com a associação mundial do aço, a rota siderúrgica integrada, baseada no alto-forno (BF) e forno básico a oxigênio (BOF), utiliza 1.400 kg de minério de ferro, 800 kg de carvão, 300 kg de calcário e 120 kg de reciclado aço para produzir 1.000 kg de aço bruto e a rota de forno elétrico a arco (EAF) utiliza em média 880 kg de aço reciclado combinado com quantidades variadas de outras fontes (DRI, metal quente e ferro granulado), 16 kg de carvão e 64 kg de calcário, para produzir 1.000 kg de aço bruto. Em média, a recuperação de 1 tonelada de aço da sucata conserva cerca de 1.030 kg de minério de ferro, 580 kg de carvão e 50 kg de calcário. A reciclagem de sucata de aço também economiza o consumo de energia. Na produção de aço, 99,9 % da sucata fundida é consumida na produção de aço novo, ao mesmo tempo em que produz resíduos ambientalmente indesejáveis desprezíveis.
A sucata de aço é classificada em três categorias principais:(i) sucata doméstica, (ii) sucata nova e (iii) sucata velha, dependendo de quando se torna sucata em seu ciclo de vida.
A sucata doméstica é a sucata gerada internamente durante a fabricação dos novos produtos siderúrgicos nas siderúrgicas. Também é conhecido como sucata runaround e é o material na forma de aparas ou rejeitos gerados dentro de uma siderúrgica durante o processo de produção de ferro e aço. Essa forma de sucata raramente sai da área de produção da siderúrgica. Em vez disso, é devolvido ao forno de fabricação de aço no local e derretido novamente. Esta sucata possui propriedades físicas e composição química conhecidas. Os avanços tecnológicos reduziram significativamente a geração de sucata doméstica.
A nova sucata (também chamada de sucata pronta ou industrial) é gerada a partir de unidades fabris envolvidas na fabricação e fabricação de produtos siderúrgicos. A sucata se acumula quando o aço é cortado, estirado, extrudado ou usinado. O processo de fundição também produz sucata como excesso de metal. A sucata nova inclui itens como aparas, recortes e sobras de estampados quando as peças são feitas de ferro e aço durante os processos de fabricação. Geralmente, é transportado rapidamente de volta para as siderúrgicas por meio de processadores e revendedores de sucata ou diretamente de volta para a siderúrgica para refusão, evitando espaço de armazenamento e custos de controle de estoque. A oferta de sucata nova é função da atividade industrial. Quando a atividade é alta, mais quantidade de novo refugo é gerada. A composição química e as características físicas da nova sucata são bem conhecidas. Esta sucata é normalmente limpa, o que significa que não é misturada com outros materiais. Em princípio, a nova sucata não precisa de nenhum grande processo de pré-tratamento antes de ser derretida, embora o corte no tamanho adequado possa ser necessário.
A sucata velha também é conhecida como sucata pós-consumo ou sucata obsoleta. É o aço que foi descartado quando produtos siderúrgicos industriais e de consumo (como automóveis, eletrodomésticos, máquinas, edifícios, pontes, navios, latas e vagões e vagões ferroviários etc.) cumpriram sua vida útil. A sucata velha é coletada após um ciclo de consumo, separadamente ou misturada, e muitas vezes é contaminada até certo ponto, dependendo muito de sua origem e dos sistemas de coleta. Como o tempo de vida de muitos produtos pode ser superior a dez anos e às vezes até mais de 50 anos (por exemplo, produtos de construção civil), há um acúmulo de produtos de ferro e aço em uso desde que a produção do aço começou em uma grande escala. Uma vez que a sucata velha é muitas vezes material que está em uso há anos ou décadas, a composição química e as características físicas geralmente não são bem conhecidas. Também é frequentemente misturado com outro lixo. Devido a essas razões, a sucata velha é a forma de aço mais difícil e cara de reutilizar. A incorporação em produtos reciclados pode exigir limpeza, classificação, remoção de revestimentos e outras preparações antes do uso.
O grande número de fontes e formas de sucata de aço requer o uso de vários processos de triagem e preparação de sucata para remover os contaminantes e/ou recuperar outros materiais valiosos (ou seja, metais não ferrosos) antes de entrar no processo de fabricação de aço.
Processos para triagem e preparação de sucata de aço
A sucata doméstica dificilmente precisa de qualquer preparação, exceto que os pedaços maiores da sucata podem ter que ser lancetados ou cortados a gás para tornar o tamanho adequado para seu carregamento no forno de fabricação de aço. O mesmo vale também para uma quantidade substancial da nova sucata. No entanto, alguns dos novos refugos podem precisar de processamento.
Grandes itens como navios, automóveis, eletrodomésticos, vagões e vagões ferroviários e aço estrutural precisam ser cortados para permitir que sejam carregados no forno de fabricação de aço. Isso pode ser feito usando tesouras, maçaricos de corte manuais, trituradores ou trituradores. A triagem manual obviamente envolve a remoção manual de componentes da sucata. É mais adequado quando acessórios diversos devem ser removidos da sucata (ou seja, radiadores de automóveis sucateados, tanques de plástico de radiadores etc.). A separação de metálicos de não metálicos também é muitas vezes realizada manualmente.
Ampla gama de equipamentos e processos estão disponíveis para a redução do tamanho de grandes sucatas em pedaços pequenos o suficiente para permitir a consolidação, transporte e posterior alimentação no forno siderúrgico. Os equipamentos e processos utilizados para isso são descritos abaixo.
Processos mecânicos
Os processos mecânicos que são normalmente utilizados para preparar a sucata de aço incluem nomeadamente (i) enfardamento, (ii) briquetagem, (iii) corte e (iv) trituração (Fig. 1). Processos químicos também são usados em certos casos.
- Enfardamento – No processo de enfardamento, o material de sucata é comprimido em uma poderosa prensa mecânica ou hidráulica, para produzir blocos cúbicos densos chamados fardos. Na prensa de enfardamento, a sucata solta que tem uma alta área de superfície e baixa densidade (ou seja, torneamento de torno) é compactada. A prensa enfardadeira é um equipamento pesado de processamento que utiliza até três carneiros hidráulicos para comprimir a sucata que requer maior densidade para carregamento no forno siderúrgico. Com 600 cavalos de potência, a maior prensa enfardadeira pode levar três automóveis achatados sem motores e em menos de dois minutos produzir um fardo de 2,5 toneladas e um tamanho de 1 m x 0,5 m x 2 m. As vantagens do processo de enfardamento são (i) mais peso pode ser carregado em um caminhão, reduzindo assim o custo de transporte, (ii) mais material pode ser armazenado em um determinado espaço, (iii) manuseio e armazenamento da sucata torna-se mais fácil, mais rápido, e sistemática que, por sua vez, reduz o custo de manuseio e armazenamento da sucata, e (iv) obtém-se uma carga mais densa do forno.
- Briquetagem – Em uma máquina de briquetagem, pequenos fragmentos são compactados em bolsões à medida que passam entre dois tambores giratórios. A compactação pode ser auxiliada pelo calor, dependendo do material.
- Cisalhamento – No processo de cisalhamento, o material de sucata é cortado no comprimento por uma poderosa lâmina de uma máquina de cisalhamento. A guilhotina hidráulica corta peças pesadas de aço, incluindo vigas I, placas de navios, tubos e laterais de vagões ferroviários. As tesouras variam em tamanho de 300 toneladas a mais de 2.000 toneladas de força de cabeça. A máquina de corte mais barata é uma tesoura de crocodilo que pode cortar sucata de fusão pesada de 200 mm de espessura. As tesouras maiores são ainda mais poderosas.
- Trituração – É utilizada para sucata de aço que pode conter outros materiais (vidro, plástico, borracha, quaisquer metais não ferrosos, etc.) como automóveis e eletrodomésticos. Martelos ou facas de aço temperado, acionados por motores elétricos de enorme potência, reduzem o objeto a pequenos pedaços que podem então ser separados, principalmente pelos ímãs que retiram a sucata de aço e deixam todos os outros materiais. Os trituradores geralmente têm alto custo de capital e operacional e só são justificados quando grande quantidade de sucata de aço está disponível regularmente para alimentar a trituradora para processamento. Máquinas de trituração também são conhecidas como fragmentadoras. Eles podem reduzir sucata volumosa em pedaços do tamanho de um punho usando enormes moinhos de martelo. Um triturador de tamanho médio usa 36 martelos pesando cerca de 120 kg cada para triturar a sucata em pedaços. Embora a matéria-prima predominante para o triturador sejam carrocerias de automóveis, 'produtos da linha branca' (eletrodomésticos como fogões, lavadoras, secadoras e geladeiras) e outros itens grandes também podem ser triturados. Dependendo do seu tamanho, um triturador pode processar de 1.500 toneladas a mais de 20.000 toneladas de sucata por mês. O processo de trituração produz três tipos de materiais a saber:(i) metal ferroso (ferro e aço), (ii) resíduo triturador de fração leve e (iii) resíduo triturador de fração pesada. As duas frações de resíduos, individualmente ou coletivamente, são muitas vezes referidas como resíduos do triturador (SR). 'Fluff Shredder' é o termo dado aos materiais de baixa densidade ou leves, que são coletados durante o processo de trituração para separação do ar do ciclone. Cada tonelada de aço recuperada produz cerca de 300 kg de SR, composto por plásticos, borracha, vidro, espuma e têxteis, contaminados por óleo e outros fluidos. Os metais ferrosos são recuperados pelo operador do triturador usando separação magnética. A fração pesada SR contém principalmente alumínio, aço inoxidável, cobre, zinco e chumbo. Os metais não ferrosos e ferrosos são recuperados da fração pesada do SR. A separação de meios pesados e a separação por correntes parasitas são as tecnologias usadas principalmente para recuperar o material metálico da fração pesada SR.
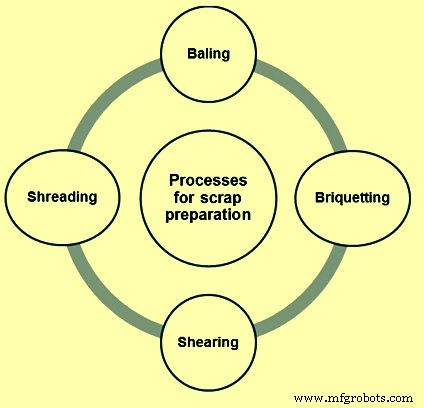
Fig 1 Processos para preparação de sucata de aço
Processo de separação magnética
A separação magnética é usada quando uma grande quantidade de sucata ferrosa deve ser separada de outros materiais. Ímãs permanentes e eletroímãs são usados neste processo. Este último pode ser ligado e desligado para pegar e largar itens. O processo de separação magnética pode ser do tipo correia ou do tipo tambor. No processo do tipo tambor, um ímã permanente está localizado dentro de um invólucro rotativo. O material passa sob o tambor em uma correia. Um separador de correia é semelhante, exceto que o ímã está localizado entre as polias em torno das quais uma correia contínua viaja. O processo de separação magnética tem algumas limitações. Não pode separar ferro e aço de níquel e aços inoxidáveis magnéticos. Além disso, são coletadas peças compostas contendo ferro que podem contaminar o aço fundido. A classificação manual costuma ser usada em conjunto com a separação magnética para evitar essas incidências.
Processo de separação de correntes parasitas
O processo de separação por correntes parasitas é usado para separar metais não ferrosos de resíduos e SR. O processo geralmente segue o processo de separação magnética primária e explora a condutividade elétrica de metais não magnéticos. Isso é conseguido passando uma corrente magnética através do fluxo de alimentação e usando forças repulsivas que interagem entre o campo magnético e as correntes parasitas nos metais. O separador de rampa inclinado representa a aplicação mais simples do processo. Ele usa uma série de ímãs em uma placa inclinada coberta com uma superfície deslizante não magnética, como aço inoxidável. Quando uma alimentação de materiais misturados é alimentada pela rampa, os itens não metálicos deslizam para baixo, enquanto os metais são desviados lateralmente pela interação do campo magnético com a corrente parasita induzida. Os dois fluxos são então coletados separadamente. Variações do processo de separação de correntes parasitas incluem a separação do disco rotativo, na qual os ímãs são dispostos em torno de um eixo rotativo. Há também outro processo que utiliza um transportador com uma polia de cabeçote equipada com ímãs. Ambos os processos dependem das trajetórias variadas de materiais afetados ou não afetados por campos magnéticos, para fazer a separação.
Processo de separação de mídia pesada
A recuperação de materiais recicláveis geralmente é alcançada usando uma separação de meio pesado (HMS) para a recuperação de metais não ferrosos de resíduos de trituradores. Este processo utiliza um meio que normalmente consiste em magnetita finamente moída ou ferrossilício e água. Variando as proporções relativas dos sólidos, a gravidade específica do meio pode ser ajustada. A gravidade específica do meio é tipicamente a meio caminho entre as densidades dos dois materiais que estão sendo separados. Uma vez separados, os produtos/materiais são drenados e o meio recuperado é então devolvido ao processo. Qualquer meio ainda aderente ao produto/material é removido por um spray de água. A solução resultante é passada através de separadores magnéticos para recuperar o meio. O efluente é então reutilizado como água de pulverização. O processo HMS é geralmente conduzido em um banho aberto para atingir uma força de separação igual à força da gravidade. Para partículas menores, as forças de viscosidade média tendem a trabalhar contra a força de separação. Nestes casos, são utilizados separadores ciclônicos que resultam em uma separação em várias vezes a força da gravidade.
Separação por características físicas e químicas
A separação por características físicas e químicas utiliza testes de cor, densidade, magnético, faísca, química e espectroscópica. Os materiais de sucata são normalmente identificados por operadores qualificados (classificadores) usando um número limitado de testes físicos e químicos. Esses testes baseiam-se no reconhecimento de objetos por cor, densidade aparente, reação com reagentes químicos, análise química, propriedades magnéticas, natureza do padrão de faísca quando moído por uma roda abrasiva e análise espectrográfica.
Propriedades físicas como cor, densidade e dureza relativa podem ser usadas para separar rapidamente certas classes de materiais. Por exemplo, cobre e latão podem ser identificados pela cor, enquanto o chumbo pode ser reconhecido por sua densidade e suavidade relativa. A diferenciação entre ligas de graus e composições semelhantes pode ser difícil. Nesses casos, o teste magnético, o método de teste de faísca e a análise química e espectroscópica são frequentemente usados. O teste magnético também pode ser usado, pois o ferro, o níquel e o cobalto são ferromagnéticos, assim como os aços inoxidáveis de baixa liga. Assim, embora o teste magnético não possa ser usado para diferenciar ligas, ele pode classificar ligas em suas séries.
O teste de faísca envolve a retificação de uma liga em uma roda abrasiva. A cor e o comprimento da faísca podem ser usados para identificar a liga. Existe um espectrômetro que analisa os espectros emitidos pela faísca e os compara com os padrões para identificar a liga, mas esta unidade não é verdadeiramente portátil e, portanto, não é amplamente utilizada. No entanto, operadores experientes em testes de faíscas podem diferenciar o material observando a cor e o comprimento das faíscas.
Vários espectrômetros ópticos e de raios X estão sendo usados para identificar a composição das ligas. O teste termoelétrico envolve o uso do efeito Seebeck para identificar materiais. Esses dispositivos termoelétricos contêm duas sondas feitas do mesmo metal, uma aquecida e outra à temperatura ambiente. Ao entrarem em contato com a sucata, é gerada uma diferença de potencial que é característica do metal que está sendo testado. Testes químicos também são usados em que reagentes, como ácidos, são colocados no metal e a reação é observada. A análise química quantitativa normalmente é feita para confirmar a composição exata da liga.
Processos de decapagem
Esses processos também são conhecidos como processos de purificação de sucata e são eficazes para a remoção de elementos residuais da sucata. Muitos elementos residuais dissolvidos no aço fundido, e. cobre, estanho, antimônio e chumbo, não são oxidados na presença de ferro durante o processo de fabricação do aço devido à sua baixa afinidade pelo oxigênio. Isso significa que esses elementos não podem ser removidos de uma sucata de aço fundido por um processo pirometalúrgico comum, como é o caso do silício, manganês e alumínio que são oxidados e dissolvidos na escória. Para remover elementos residuais, a sucata deve ser pré-tratada a temperaturas mais baixas enquanto permanece no estado sólido. O pré-tratamento da sucata em estado sólido tem muitas vezes a vantagem de os elementos residuais estarem presentes em estado puro, quer misturados com a porção ferrosa da sucata, quer existentes nas superfícies da sucata, facto que deverá facilitar a sua remoção.
Vários produtos de aço estão sendo usados com revestimento de outros metais sobre eles. Exemplos são chapas galvanizadas, folha-de-flandres etc. É essencial que a sucata de aço gerada a partir de tais produtos revestidos seja despojada do material de revestimento antes de ser processada nos fornos siderúrgicos. Atualmente, existem diversos processos utilizados na indústria para decapagem da sucata de aço.
Processo de dezimagem para sucata de aço
A principal fonte de zinco é a sucata de chapas de aço galvanizado. A sucata revestida de zinco incluída na carga resulta na descarga de óxido de zinco na poeira da chaminé. Devido à sua alta pressão de vapor (71 kg/sq cm a 1600°C), a maior parte do zinco evapora durante o processo de fabricação do aço. Um balanço de zinco para um EAF mostra que 97,9% da entrada de zinco escapa com os fumos, restando apenas 2% dissolvido no aço e 0,1% na escória. Embora a remoção de zinco na etapa de fundição de sucata não seja problemática, é útil se a dezimação da sucata revestida de zinco for feita em uma etapa de pré-tratamento de sucata, de modo a evitar os problemas associados à reciclagem de grandes quantidades de sucata galvanizada.
A remoção de zinco usando métodos térmicos geralmente é realizada usando qualquer um dos seguintes métodos.
- As peças galvanizadas são aquecidas a uma temperatura alta (superior a 900 graus C) na qual o zinco evapora.
- As peças galvanizadas são aquecidas a uma temperatura suficiente para fragilizar o revestimento que é então removido por abrasão.
- As peças galvanizadas são aquecidas e a remoção do revestimento é feita posteriormente por jateamento.
A remoção do zinco também pode ser realizada usando técnicas químicas nas quais a lixiviação de amônia ou soda cáustica é usada para dissolver o revestimento de zinco da sucata galvanizada.
Um processo contínuo de dezimagem eletrolítica de sucata de processo da indústria automotiva foi desenvolvido pela Hoogovens (Holanda) e uma planta piloto foi operada na França. A sucata galvanizada é imersa em uma solução cáustica quente onde o zinco se dissolve enquanto o aço permanece inalterado. Depois de sair do reator de dissolução, a sucata dezinzada é lavada e compactada. A solução enriquecida com zinco é circulada para células de eletrólise onde o zinco é recuperado eletroliticamente por deposição em placas de cátodo. Os altos custos de processamento e os custos adicionais de transporte são desvantagens do processo. No entanto, particularmente para nichos de mercado determinados por uma combinação regional de uma grande oferta de sucata de processo revestida de zinco e uma demanda por matéria-prima de fabricação de aço confiável, esse processo de dezimagem oferece uma solução real de reciclagem direta. Vários outros métodos de dezincagem da sucata também foram investigados recentemente. Estes incluem tratamento térmico, tratamento com misturas de gases Cl2-O2 e pós-tratamento mecânico após tratamento térmico
Processo de destintagem para sucata de aço
O estanho, que tem um ponto de fusão mais baixo, causa zonas de fraqueza no aço quente, levando a 'falta a quente' e outros problemas A sucata de rolamentos de estanho (ou seja, recipientes de alimentos e rolamentos de automóveis) na reciclagem de aço afeta a qualidade da superfície dos produtos de aço porque o estanho segrega para os contornos de grão e causa crostas na superfície durante o trabalho. Alguns dos processos usados para destinar a sucata de folha-de-flandres incluem a destinação eletrolítica e alcalina.
A destinação eletrolítica de sucata de folha-de-flandres é um processo comercializado há muito tempo. A sucata de folha de flandres é prensada em feixes com uma densidade superior a 1,2 t/m³. Os feixes que servem como ânodos no processo eletrolítico são imersos em um banho de soda cáustica a uma temperatura de 85 graus C. O estanho é depositado em um cátodo de aço como um material esponjoso que é então raspado, prensado em grandes pílulas para sua eliminação a indústria do estanho. Após a destinação, o teor residual de estanho que pode ser obtido na sucata é tão baixo quanto 0,02%. A destinação eletrolítica só é economicamente eficiente se a unidade de destinação tiver uma capacidade anual de processamento de sucata superior a 30.000 t de sucata. Além disso, a destinação eletrolítica é adequada para sucata nova, mas é problemática para sucata velha.
O revestimento de estanho na folha de flandres não pode ser removido por tratamento mecânico (por exemplo, triturando). Na faixa de temperatura de 400°C a 550°C, a sulfetação do revestimento com gases reativos com potencial de enxofre e sua posterior remoção como fase quebradiça de sulfeto tem sido aplicada com sucesso em escala laboratorial. Atualmente, é impossível remover o estanho de sucata de aço fundido em condições industriais. No laboratório, o estanho foi removido com sucesso por tratamento com escórias contendo Ca em condições redutoras, bem como por tratamento a vácuo de aço fundido a uma pressão de 1 kg/m².
Processo de descoperização para sucata de aço
O cobre não pode ser removido do aço fundido à base de sucata por um método de refino convencional. Várias abordagens para reduzir o teor de Cu do aço têm sido propostas, a saber, melhoria da triagem de sucata, diluição de cargas contaminadas por ferro diretamente reduzido, bem como pré-tratamento mecânico ou químico de sucata visando a remoção de impurezas. Esforços significativos de pesquisa têm sido feitos para desenvolver técnicas de descoperização pirometalúrgica. Foi confirmado em escala de laboratório que o cobre pode ser removido por tratamento com fluxos de sulfeto, mas um método mais promissor é o tratamento de fundidos de aço a pressão reduzida da fase gasosa. Este método que consiste na vaporização seletiva do cobre foi testado com sucesso em escala laboratorial. Atualmente, estão sendo realizadas investigações para otimizar a operação do triturador em relação ao teor de cobre da sucata do triturador. Resultados preliminares mostram que o teor de cobre pode ser controlado variando o grau de abertura da grade do triturador. No que diz respeito à triagem de sucata, verificou-se que o cobre é removido de forma mais eficaz na colheita manual.
Incineração
O processo de incineração é frequentemente usado para a remoção de materiais combustíveis, incluindo óleo, graxa, tintas, lubrificantes e adesivos.
Tecnologias recentes de classificação de sucata de aço
Algumas das tecnologias de classificação de sucata recentemente desenvolvidas são descritas abaixo.
Espectrômetros portáteis de emissão óptica
Os espectrômetros portáteis de emissão óptica estão evoluindo como ferramentas importantes para a triagem e identificação no local de metais na sucata de aço. Sua precisão e exatidão analíticas, embora não tão boas quanto os espectrômetros instalados em laboratório, são mais do que adequadas para a classificação de misturas e a maioria dos requisitos de verificação de grau. Um espectrômetro portátil é capaz de separar diferentes tipos de aço, além de separar pelo menos 90% a 95% dos tipos individuais que compõem cada tipo de aço.
Processo de classificação de cores
A classificação por cores é um dos primeiros processos de classificação automatizados a ser usado industrialmente e foi desenvolvida pela Huron Valley Steel Corporation (HVSC), que é a maior classificadora de sucata não ferrosa do mundo. Na última década, a HVSC usou essa tecnologia para classificar zinco, cobre, latão e aço inoxidável. A classificação de cores é baseada na análise de imagens por computador, onde a cor de cada peça metálica é detectada. As peças cuja cor está dentro de uma faixa especificada são automaticamente direcionadas para fora do material de alimentação. Para que isso funcione corretamente, um mecanismo de separação é usado para produzir um perfil em cadeia de partículas de sucata antes do detector de imagem.
O processo de classificação de cores do HVSC provou ser muito preciso, produzindo purezas de metal acima de 98%. Essa pureza é possível porque esse método de classificação é independente do tamanho e da forma das partículas. O avanço tecnológico dos computadores na última década aumentou muito a velocidade da análise de imagens em tempo real. Devido ao avanço das máquinas industriais de classificação de cores nos últimos anos, a capacidade de classificar efetivamente diferentes metais com pequenas variações de cor melhorou drasticamente.
Processo utilizando espectroscopia de quebra induzida por laser
A espectroscopia de ruptura induzida por laser (LIBS) é um processo de classificação de sucata que determina a composição química real de cada pedaço de sucata de maneira rápida e econômica para obter a mais alta qualidade possível da sucata. A tecnologia LIBS foi desenvolvida pela primeira vez pelo Laboratório Nacional de Los Alamos no início dos anos 80 para uma ampla variedade de aplicações. No entanto, só no início da década de 1990 esse processo foi implementado para a análise de peças metálicas sólidas em um projeto conjunto com a Metallgesellschaft. Os resultados deste projeto mostraram os aspectos práticos deste processo para determinar com precisão a composição elementar da sucata metálica. No entanto, o foco de seu projeto estava na identificação do elemento da matriz e não na análise espectral completa de todos os elementos da sucata. Embora o processo tenha muitas vantagens, o LIBS tem suas limitações. A maior desvantagem é que a superfície da sucata deve estar livre de tintas, lubrificantes ou adesivos, pois o laser de pulso só pode penetrar uma profundidade de trinta angstroms ou menos na superfície do metal.
Raios-X também podem ser usados em vez de um laser para iluminar a superfície da sucata. A fluorescência de raios X (XRF) tem sido usada para identificação de ligas, e vários dispositivos comerciais, tanto portáteis quanto portáteis, já estão disponíveis.
Processo de manufatura
- Inclusões em aço fundido contínuo e sua detecção
- Inclusões em siderurgia e siderurgia secundária
- Inclusões, Engenharia de Inclusão e Aços Limpos
- Avaliação do ciclo de vida e sustentabilidade do aço
- Introdução aos processos de pelotização e pelotização de minério de ferro
- Fornos de reaquecimento e seus tipos
- Tipos de aço inoxidável e classes de aço inoxidável
- Processos e técnicas de usinagem
- Diferentes propriedades e classes de aço ferramenta
- Entendendo o aço ferramenta e como ele é feito