Processo de forno rotativo de redução direta à base de carvão
Processo de forno rotativo de redução direta baseado em carvão
O processo de forno rotativo de redução direta à base de carvão foi desenvolvido para converter minério de ferro diretamente em ferro metálico sem a fusão dos materiais. O processo tem a vantagem de baixo investimento de capital e não requer carvão de coque. O ferro metálico neste processo é produzido pela redução do óxido de ferro abaixo da temperatura de fusão do minério de ferro (1535°C) utilizando material carbonáceo presente no carvão não coqueificável. Como o minério de ferro está em contato direto com o agente redutor durante todo o processo de redução, é muitas vezes denominado como ferro reduzido direto (DRI). O produto reduzido com alto grau de metalização apresenta uma “estrutura em favo de mel”, devido à qual é frequentemente chamado de ferro-esponja.
As plantas DRI à base de carvão são flexíveis em relação à localização da planta, uma vez que o carvão não coqueificável é amplamente distribuído em grandes depósitos e é fácil de transportar. A maioria das plantas emprega o processo de redução que é realizado em fornos rotativos. Essas plantas utilizam grande variedade de matérias-primas e carvão não coqueificável. A qualidade desses materiais tem influência direta no processo e no produto. Algumas usinas não usam minério de ferro diretamente. Essas usinas utilizam pelotas de minério de ferro no forno rotativo. A mistura de matéria-prima composta por minério de ferro, dolomita e carvão não coqueificável é alimentada em uma extremidade do forno rotativo e é aquecida por queimadores de carvão para produzir DRI. O produto DRI junto com o char (às vezes chamado de dolo char) é retirado da outra extremidade do forno. Além disso, o ar primário e o ar secundário são fornecidos ao forno para iniciar a combustão e sustentar o processo de reação no forno.
Matérias-primas
As principais matérias-primas para a produção de DRI pelo processo de forno rotativo são (i) minério de ferro calibrado ou pelotas de minério de ferro, (ii) carvão não coqueificável e (iii) dolomita em pequenas quantidades para eliminação do enxofre.
O minério de ferro de qualidade adequada é o insumo básico para o processo de redução direta a base de carvão. A maioria das plantas de redução direta baseadas em carvão usa minério de ferro granulado. Os principais requisitos de qualidade são (i) alto teor de Fe com menos ganga e elementos deletérios como fósforo e enxofre, (ii) boas propriedades de manuseio (índice de tumbler e índice de abrasão), (iii) calibrado para tamanho com menos finos, (iv) alto redutibilidade, (v) baixa decrepitação durante a redução e (vi) boa compatibilidade com o carvão redutor utilizado.
O requisito de qualidade do minério de ferro dimensionado é atender aos requisitos físicos, metalúrgicos e químicos. Os requisitos físicos são força e granulometria. O minério deve ser duro e possuir alta resistência. A resistência ideal do tumbler do minério deve ser de 90% no mínimo. Dependendo da redutibilidade, geralmente é usado minério calibrado na faixa de tamanho de 5 mm a 20 mm. Os requisitos metalúrgicos do minério incluem alta redutibilidade, estabilidade térmica e baixa tendência à aderência e desintegração durante o aquecimento e redução. As exigências químicas do minério são uma característica importante, pois além da remoção do oxigênio, nenhuma outra alteração química ocorre durante o processo de redução direta. O material de ganga em DRI, originário do minério de ferro, ou seja, sílica e alumina, juntamente com teores de enxofre e fósforo, afetam negativamente a economia na operação de aciaria subsequente. Assim, o minério deve ter alto teor de ferro e baixo teor de ganga. As especificações físicas e químicas desejadas do minério são as seguintes.
Tamanho - 5 mm -20 mm
Oversize e undersize – menos de 5% no máximo cada
Índice de copo - mais de 90%
Contaminação (laterite etc.) - menos de 5%
Fe total - 65% mínimo
Sílica – menos de 3%
Sílica + alumina - 5% no máximo
Enxofre - 0,01% máximo
Fósforo - 0,05% máximo
Umidade - 1% no máximo
O carvão não coqueificável utilizado em fornos rotativos tem dupla função. Fornece calor para o processo e também atua como agente redutor. Os principais requisitos de qualidade do carvão não coqueificável são (i) características não coqueificáveis, (ii) baixo teor de cinzas, (iii) baixo teor de enxofre, (iv) boa reatividade, (v) alta temperatura de fusão de cinzas e (vi ) matéria volátil média. O caráter não coqueificável do carvão é necessário, pois a reação de coqueificação leva à formação de anéis dentro do forno. O limite de índice de aglomeração praticamente permitido para o processo de forno rotativo é 3 no máximo. O baixo teor de cinzas do carvão é necessário, pois o alto teor de cinzas leva à subutilização do volume do forno disponível para redução. Também aumenta o consumo de carbono fixo, uma vez que energia adicional é consumida no aquecimento da massa de cinzas inertes até a temperatura de reação. Um teor máximo de cinzas de 20% é o limite prático para uma operação eficiente. Baixo teor de enxofre é necessário para controlar o enxofre no DRI. O enxofre no carvão deve ser de 0,01% no máximo. É necessária uma boa reatividade do carvão, pois uma etapa importante no processo de redução do estado sólido é a reação direta, pela qual o dióxido de carbono gerado pela queima do carvão reage com o carvão para regenerar o monóxido de carbono (reação de Boudouard). Portanto, o carvão deve possuir reatividade suficiente para que a reação de Boudouard ocorra na taxa desejada. Carvões betuminosos e sub-betuminosos apresentam geralmente boa reatividade adequada para a produção de DRI. A temperatura de fusão das cinzas é outra característica importante. Carvões com baixa temperatura de fusão de cinzas levam a massa pegajosa resultando em operação instável do forno devido à formação de acreções dentro do forno o que reduz a taxa de redução pela formação de camada de escória na superfície do minério. Portanto, carvões com temperatura de fusão de cinzas superior a 1400°C são desejáveis para operação de forno rotativo. A matéria volátil do carvão deve ser ideal para o processo de forno rotativo à base de carvão. O carvão com matéria volátil muito baixa resulta em reatividade muito baixa do carvão e, portanto, dá origem a um produto metalizado pobre. Carvões muito voláteis, embora produzam carvão altamente reativo, também não são preferidos, pois aumentam o volume de gás no forno. Normalmente, para o processo de forno rotativo, a matéria volátil deve estar na faixa de 25% a 30%. Os carvões para redução direta no forno rotativo precisam ter baixo índice de inchamento. Normalmente, o índice de dilatação deve ser inferior a 1. As especificações físicas e químicas do carvão não coqueificável são as seguintes.
Tamanho dos pedaços – 5 mm a 20 mm
Tamanho dos finos - menos de 5 mm
Contaminação (xisto, pedras etc.) – menos de 3%
Carbono fixo – mínimo de 45%
Matéria volátil – 25% a 30%
Cinza - 20% no máximo
Umidade - 8% no máximo
A dolomita é usada para dessulfurização no processo de produção DRI. A especificação típica da dolomita é dada abaixo.
MgO - 22% mínimo
CaO - 28% máximo
LOI - saldo
Reações químicas
As reações químicas ocorrem dentro do forno rotativo. A seção transversal do forno rotativo está na Fig 1.
Fig 1 Seção transversal do forno rotativo
O processo de redução direta à base de carvão é baseado no agente redutor sólido que é o carvão não coqueificável. A reação ocorre em alta temperatura (1000°C a 1100°C). O carvão desempenha um papel duplo no forno. Parte do carvão é utilizada como combustível para fornecer o calor desejado para levar as matérias-primas à temperatura desejada. Mas o principal papel do carvão é fornecer carbono para o processo de redução. A dolomita é usada como removedor de enxofre que finalmente sai com o carvão. Char contém cinzas de carvão e outras impurezas de minério de ferro. As reações dentro do forno ocorrem em várias etapas durante a redução do minério de ferro a DRI. O minério de ferro sofre a seguinte reação de redução final.
Fe2O3 + 3CO =2 Fe + 3CO2
A reação mostra que o monóxido de carbono (CO) é um gás redutor que é obtido pela combustão controlada do carvão, de acordo com a reação de Boudouard apresentada abaixo.
C + O2 =CO2
C + CO2 =2CO
O monóxido de carbono produzido como acima reduz o óxido de ferro do minério de ferro a ferro metálico conforme a reação dada acima. No entanto, a redução de óxido a metal não ocorre em uma única etapa, mas pela remoção gradual do oxigênio dando origem a vários óxidos intermediários. A sequência de redução pode ser expressa como Fe2O3 a Fe3O4 a FeO a Fe.
As reações que ocorrem dentro do leito de minério de ferro e carvão são de natureza heterogênea. Dois conjuntos de reações ocorrem. O primeiro conjunto de reações ocorre entre carvão, dióxido de carbono e oxigênio, enquanto no segundo conjunto as reações são entre partículas de minério de ferro e CO. Como o oxigênio do minério de ferro é removido como CO2, o escape do gás CO2 torna o produto DRI poroso. A reação entre a partícula de minério e o redutor gasoso pode ser visualizada nos cinco estágios seguintes.
- Estágio 1 – Neste estágio, a difusão do reagente gasoso ocorre através do filme que envolve a partícula de minério até a superfície do sólido.
- Estágio 2 – Neste estágio, ocorre a penetração e difusão do reagente através da manta da camada externa reagida até a superfície do núcleo não reagido.
- Fase 3 – Nesta fase, ocorre a reação do reagente gasoso com o sólido na superfície da reação.
- Estágio 4 – Neste estágio, a difusão de produtos gasosos ocorre através da camada reagida até a superfície externa do sólido.
- Estágio 5 – Neste estágio, difusão de produtos gasosos através do filme de gás de volta ao corpo principal do gás.
Como a reação ocorre em vários estágios e cada estágio em sucessão, o estágio com a menor velocidade controla a velocidade da reação. Tanto a taxa de difusão quanto a taxa de reação são principalmente uma função dos três parâmetros, a saber (i) concentração de reagentes, (ii) temperatura de interface ativa e (iii) área ativa de reação.
O processo de redução direta
O processo de redução direta é realizado em um forno rotativo onde as temperaturas de operação são mantidas na faixa de 1.000 graus C a 1.100 graus C. O produto do forno (DRI e char mix) é então resfriado em um refrigerador rotativo com sistema de refrigeração a água. Os produtos do forno são peneirados e separados magneticamente. O DRI sendo magnético é atraído e se separa do char não magnético.
O minério de ferro e o carvão britados e peneirados nos respectivos tamanhos são alimentados ao forno rotativo através do tubo de alimentação em proporção pré-determinada. O forno rotativo é ligeiramente inclinado em um ângulo de 2,5 graus e girado pelo motor de velocidade variável AC a uma velocidade variável que varia de 0,2 rpm (rotações por minuto) a 1,0 rpm. Devido à inclinação e movimento rotativo do forno, o material se desloca da extremidade de alimentação até a extremidade de descarga do forno em cerca de 7 horas a 8 horas.
O fino de carvão é soprado da extremidade de descarga para manter a temperatura necessária e a concentração de carbono no leito. O forno tem vários ventiladores de ar de concha montados na parte superior que sopram ar nas respectivas zonas para manter o perfil de temperatura necessário. O material e os gases quentes movem-se em contracorrente, como resultado, o minério de ferro é pré-aquecido e é gradualmente reduzido ao longo do tempo em que atinge a extremidade descarregada.
O forno rotativo é amplamente dividido em duas zonas, nomeadamente a zona de pré-aquecimento e a zona de redução (Fig. 2). A zona de pré-aquecimento se estende por 40 a 50 por cento do comprimento do forno. Nesta zona, a umidade da carga é eliminada e a matéria volátil do carvão, liberada em uma faixa de temperatura de 600°C a 800°C, é queimada com o ar de combustão fornecido pelos tubos de ar no espaço livre. acima da carga. O calor da combustão aumenta a temperatura do revestimento e da superfície do leito. À medida que o forno gira, o revestimento transfere o calor para a carga. O material de carga, pré-aquecido a cerca de 950 graus C, entra na zona de redução. A temperatura da ordem de 1000°C a 1100°C é mantida na zona de redução, que é a temperatura apropriada para a redução no estado sólido do óxido de ferro a ferro metálico. O termopar instalado ao longo do comprimento da carcaça do forno determina o perfil térmico do forno. A temperatura no interior do forno é controlada regulando a quantidade de ar de combustão admitido no forno através de portas com a ajuda de ventiladores montados na carcaça do forno e por injeção controlada de carvão. O óxido de ferro do minério é reduzido a ferro metálico pelo monóxido de carbono gerado no forno a partir do carvão.
O material reduzido a quente do forno passa então para o resfriador rotativo através do chute de transferência para resfriamento. O resfriador também é inclinado em 2,5 graus e é girado a uma velocidade variável de 0,3 rpm a 1,2 rpm acionado por um motor CA de velocidade variável. A água é pulverizada no topo da casca para resfriar indiretamente o material quente dentro da casca. O material é resfriado a cerca de 100°C e é descarregado na esteira transportadora por meio de uma válvula de pêndulo duplo, que atua como uma vedação e impede que o ar atmosférico entre no resfriador rotativo.
O produto resfriado do forno após sua descarga do forno rotativo é enviado para a área de separação do produto onde o DRI é separado magneticamente do carvão e é peneirado em várias frações de tamanho.
Os gases que fluem em direção contrária à corrente para o material no forno viajam para a câmara de decantação de poeira (DSC), onde as partículas mais pesadas se acomodam. Essas partículas são removidas continuamente pelo sistema raspador úmido. Os gases passam então para a câmara de pós-queimador (ABC) onde o carbono residual ou CO é queimado pelo excesso de ar disponível. Após o ABC, os gases estão em alta temperatura e possuem muita energia térmica que normalmente é utilizada para geração de vapor através da caldeira de recuperação de calor residual (WHRB). Este vapor é geralmente usado para geração de energia. Os gases resfriados a cerca de 200 graus C na descarga do WHRB viajam para equipamentos de controle de poluição, como filtros de manga, depurador ou precipitador eletrostático (ESP) para remoção das partículas de poeira mais finas. Os gases limpos são liberados para a atmosfera a cerca de 80 graus C através da chaminé.
Para evitar a formação significativa dos anéis do forno, as temperaturas de operação no forno devem ser mantidas dentro de uma temperatura de 1.100 graus C.
Como o processo de forno rotativo requer em torno de 7 horas a 8 horas de tempo de redução, a produtividade do processo é limitada e geralmente está na faixa entre 30.000 toneladas/ano a 150.000 toneladas/ano dependendo do tamanho do forno. Etapas importantes do processo e o conceito do processo são mostrados na Fig 2.
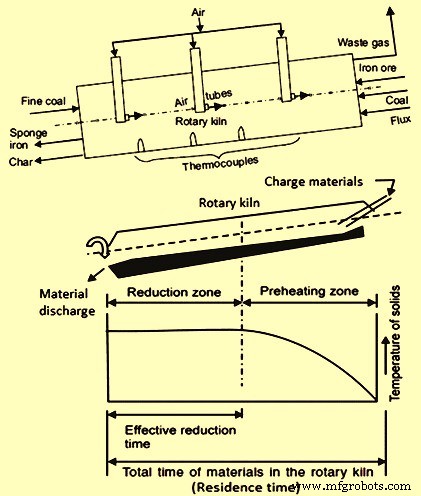
Fig 2 Etapas importantes e o conceito de processo do processo de forno rotativo
Além disso, no processo de redução do forno rotativo à base de carvão, são necessários cerca de 6 GCal de energia de combustível. Mais de 2 GCal de energia são liberados do forno como gás residual. Parte dessa energia é recuperada no WHRB.
Um fluxograma esquemático típico do processo de redução direta baseado em carvão está na Fig 3.
Fig 3 Fluxograma esquemático do processo de redução direta baseado em carvão
Existem vários processos e conceitos de processo que foram desenvolvidos nesta área durante a segunda metade do século XX. Alguns deles sobreviveram, enquanto outros não. Os processos e conceitos de processo que sobreviveram têm várias características comuns ou ligeiramente diferentes, conforme indicado abaixo.
- Um método de vedação para evitar a entrada de ar no forno rotativo.
- Um método de lançar ou lançar carvão não coqueificável da extremidade de descarga do forno rotativo.
- Um método de pesagem de alimentação, dosagem e carregamento de matérias-primas.
- Um método de introdução de quantidade controlada de ar em intervalos regulares ao longo do comprimento do forno de tal forma que não oxide o produto reduzido no leito.
- Um método para medir e registrar a temperatura em intervalos regulares ao longo do comprimento do forno.
- Um método de resfriamento indireto de DRI - mistura de carvão em uma casca cilíndrica de aço rotativo por pulverização de água na superfície externa da casca.
- Um método para a separação de DRI da mistura DRI-char.
- Um método de tratamento de gases residuais e manutenção do perfil de fluxo desejado por meio do controle de pressão.
- Um método para a recuperação de energia a partir de gases residuais
Equipamentos e instalações
Os seguintes equipamentos e instalações são necessários para o processo de forno rotativo de redução direta à base de carvão.
- Seção de preparação de matéria-prima – Esta seção contém equipamentos como vibro-alimentadores, britadores e peneiras. A britagem de minério de ferro normalmente não é necessária, uma vez que o material dimensionado (5 mm a 20 mm) é geralmente obtido. O minério de ferro geralmente é levado para a moega moída, de onde é encaminhado para a peneira com auxílio de vibro-feeder, onde o oversize (+ 20 mm) e o undersize (- 5 mm) são separados por peneiramento. O material superdimensionado é transportado para o britador superdimensionado para obter o material dimensionado. No caso de carvão não coqueificável, o tamanho recebido é normalmente -200 mm que é britado com os britadores primários e secundários em circuito fechado com peneiras primárias e secundárias. As peneiras separam as duas frações, ou seja, pedaços de carvão para carvão de alimentação (5 mm a 20 mm) e finos de carvão (-5 mm) para carvão de injeção que são necessários para o processo. A britagem e peneiramento de dolomita geralmente não são necessários, uma vez que o material dimensionado (3 mm a 8 mm) é geralmente adquirido e alimentado diretamente ao silo diário através do transportador. Todas as matérias-primas de seus pontos de descarga são alimentadas ao silo diário por meio de transportadores.
- Seção de armazenamento de matéria-prima – Consiste em posições de armazenamento (caixas diárias). Para diferentes matérias-primas, são fornecidas caixas de armazenamento separadas. Os silos são normalmente projetados para o armazenamento de matérias-primas para consumo mínimo de um dia.
- Sistema de alimentação de matéria-prima – Consiste em alimentadores de pesagem que são fornecidos abaixo de cada caixa para extrair várias matérias-primas na proporção necessária das caixas e entregar aos transportadores para alimentação no forno.
- Forno rotativo – É o coração do processo de redução à base de carvão, uma vez que a reação de redução ocorre neste reator. O diâmetro e o comprimento do forno dependem da sua capacidade. O forno é geralmente revestido com refratários calcináveis de alta alumina em toda a sua extensão com barragens na extremidade de alimentação e na extremidade de descarga. O forno é geralmente inclinado em 2,5 graus para baixo e repousa sobre duas a quatro estações de apoio, dependendo do tamanho do forno. A taxa de transporte de materiais através do forno pode ser controlada variando sua inclinação e velocidade de rotação. Existem cones de entrada e saída em extremidades opostas do forno que são resfriados por seus ventiladores individuais. O invólucro do forno é fornecido com pequenas portas de amostragem. O posicionamento longitudinal do forno em seus anéis de condução é controlado por sistemas hidráulicos. O carvão e o minério de ferro são medidos na extremidade superior do forno inclinado. Uma parte do carvão também é injetada pneumaticamente a partir da extremidade de descarga do forno. A carga passa primeiro por uma zona de pré-aquecimento onde ocorre a desvolatilização do carvão e o minério de ferro é aquecido à temperatura de pré-aquecimento para redução. O controle da temperatura e do processo no forno é realizado pela instalação de um número adequado de tubos de injeção de ar feitos de aço resistente ao calor espaçados uniformemente ao longo do comprimento do forno e em contracorrente ao fluxo de minério de ferro. As pontas dos tubos de ar são equipadas com redemoinhos internos especiais para melhorar a uniformidade da combustão. Um queimador central localizado na extremidade de descarga do forno é usado com LDO (óleo diesel leve) para aquecer o forno frio. Após o aquecimento inicial, o fornecimento de combustível é desligado e o queimador é usado para injetar ar para a combustão do carvão. As temperaturas do forno são medidas com termopares fixos e portas de 'termopares de resposta rápida' (QRT). Termopares fixos estão localizados ao longo do comprimento do forno para que as temperaturas em várias seções do forno possam ser monitoradas. Termopares fixos, às vezes podem dar leituras erráticas caso sejam revestidos com cinzas, minério ou acreção. Nesses casos, o QRT é usado para monitorar as temperaturas do forno.
- Resfriador rotativo – O produto (DRI) juntamente com cinzas de carvão, dolomita calcinada e carvão residual é descarregado do forno a cerca de 1000 graus C. Uma calha fechada na extremidade de descarga do forno equipada com um separador de grumos e uma porta de acesso para a remoção de grumos transfere o DRI quente para um resfriador rotativo. O resfriador é um cilindro giratório de tamanho apropriado que é inclinado em 2,5 graus. O DRI é resfriado indiretamente por spray de água na superfície superior do resfriador. A água de resfriamento é coletada em calhas abaixo do resfriador e bombeada para a torre de resfriamento para reciclagem junto com a água de reposição. Os sólidos descarregados para o resfriador através de uma calha fechada são resfriados a cerca de 100°C sem contato com o ar. Um grizzly no chute remove acúmulos grandes (maiores que 50 mm) para entupir ou danificar os mecanismos de descarga do resfriador. Esses aglomerados de acreção são descarregados separadamente através do portão de aglomerado. O restante do material é descarregado em um transportador através de uma válvula de duplo flap. O produto é então transportado para o sistema de separação de produtos através do transportador.
- Seção de separação de produtos – É composta por peneira vibratória e separadores magnéticos. O produto resfriado é transportado para a seção de separação de produtos por esteiras transportadoras. Os produtos da descarga do resfriador contêm DRI, carvão e cinzas de carvão. No edifício de separação de produtos, o produto é primeiramente peneirado em peneira de dois andares com peneiras de 3 mm e 20 mm. O produto peneirado está sendo alimentado em separadores magnéticos para separação de porções magnéticas e não magnéticas. O produto é peneirado primeiro para remover o DRI mais 20 mm. O subdimensionamento (uma mistura de DRI, carvão e cinzas de carvão) é peneirado em frações de +/- 3 mm. Cada fração passa por um separador magnético. A porção não magnética da fração mais 3 mm é principalmente carvão que pode ser reciclado para o forno, se desejado, ou pode ser usado na caldeira da usina como combustível. A porção não magnética da fração de -3 mm, principalmente dolomita calcinada gasta, cinzas e carvão fino é descartada. A porção magnética de cada fração é DRI. A fração mais 3 mm pode ser usada diretamente para a fabricação de aço e a fração mais fina pode ser briquetada e coletada em sacos.
- Seção de armazenamento de produtos – Consiste em compartimentos de armazenamento. Os pedaços DRI (3 mm a 20 mm) e os finos DRI (-3 mm) são armazenados em diferentes compartimentos de armazenamento. As caixas são normalmente projetadas para ter armazenamento de produção mínima de 1 dia. O carvão gerado na usina é armazenado separadamente para uso como combustível na usina.
- Sistema de gases residuais – Os gases residuais do forno a uma temperatura de cerca de 850°C a 900°C passam por uma câmara de deposição de poeira onde as partículas de poeira mais pesadas se depositam devido à diminuição repentina da velocidade dos gases. Os gases de combustão passam então por uma câmara de pós-combustão onde os combustíveis não queimados são queimados soprando o excesso de ar. A temperatura da câmara do pós-queimador, às vezes, é controlada por jatos de água. Os gases queimados passam então por um duto descendente para o resfriador de evaporação, onde a temperatura é reduzida e através de equipamentos de controle de poluição, como ESP / filtro de mangas / purificador, onde as partículas de poeira são separadas. Em seguida, o gás pode escapar para a atmosfera através da chaminé através do ventilador de tiragem induzida (ID). No entanto, é desejável equipar o sistema de gases residuais com uma caldeira de recuperação de calor residual (WHRB) para a recuperação da energia sensível transportada pelos gases residuais. Neste caso, os gases de combustão após a câmara de pós-combustão passam por um duto de cotovelo para WHRB, onde o calor sensível dos gases é extraído. O gás é então liberado na atmosfera depois de passar por equipamentos de controle de poluição, como ESP/filtro de bolsa/depurador, ventilador de identificação e chaminé.
- Fornecimento de utilidades – Ar comprimido e água de resfriamento são as duas utilidades necessárias para o processo. Os compressores de ar são normalmente instalados para fornecimento de ar comprimido, enquanto o sistema de água de resfriamento consiste em casa de bombas e torre de resfriamento.
Formação de acreção em forno rotativo
O material dentro do forno cai e desliza, e uma fina camada de poeira invariavelmente se forma na superfície do revestimento refratário. Algumas zonas do forno podem ser especificamente propensas ao acúmulo de partículas e o efeito combinado das condições térmicas e de fluxo resulta na formação de depósitos cilíndricos ou anéis devido ao seu movimento rotativo. À medida que o anel se torna mais espesso, a abertura disponível do forno diminui, ou seja, o volume de trabalho do forno diminui, resultando na obstrução do fluxo de produto e gases de combustão através do forno. Os anéis estão geralmente situados perto da zona de redução ou do queimador e são causados pela temperatura muito alta nesta área, particularmente quando o revestimento refratário é superaquecido devido ao impacto direto da chama do queimador. Estes são os tipos de anéis mais comuns e também os mais problemáticos.
A principal razão para a formação de acreção em fornos rotativos é devido à formação de compostos complexos de baixo ponto de fusão no sistema FeO-SiO2-Al2O3, como wustita, faialita, cordierita de ferro, hercinita e no sistema CaO-MgO-FeO-SiO2- Sistema Al2O3, como melilita ou anortita, akermanita, cordierita de ferro-magnésio, espinélio e silicato de ferro-magnésio. A coexistência desses compostos complexos diminui a temperatura de fusão da carga do forno, que por sua vez adere às paredes refratárias. Algumas acreções também são formadas devido à aglomeração de finos mais próximo da extremidade de carga ou devido à sinterização do DRI devido à temperatura excessiva e/ou menor relação carbono/ferro na extremidade de descarga de um forno rotativo.
Como esses anéis não podem ser alcançados de fora do forno, eles são, portanto, impossíveis de serem removidos durante o funcionamento do forno. Em vários casos, os anéis crescem rapidamente e causam desligamentos não programados do forno. Observou-se que a maioria das paradas do forno se deve apenas à formação dos acréscimos.
Termos associados à produção de DRI
Alguns dos termos associados à medição da eficácia das reações de redução para DRI são definidos como segue.
Porcentagem total de ferro 'Fe T' é o ferro total em uma amostra, incluindo ferro metálico e ferro quimicamente combinado com outros elementos, como oxigênio.
Fe T =(peso do ferro/peso da amostra)*100
Porcentagem de ferro metálico 'Fe M' é ferro quimicamente não combinado e como cementita (Fe3C).
Fe M =(peso do ferro metálico/peso da amostra)*100
Óxidos de ferro residuais são óxidos de ferro remanescentes presentes no DRI na forma de FeO, Fe3O4 ou Fe2O3, embora normalmente o FeO seja o único óxido residual presente.
Total de carbono é o carbono total presente no DRI e é igual à soma do carbono livre e combinado (como cementita).
Impurezas são elementos/compostos indesejáveis no DRI, sendo o enxofre e o fósforo os mais comuns entre eles.
Metalização é uma medida da conversão de óxidos de ferro em ferro metálico (seja livre ou em combinação com carbono como cementita) pela remoção de oxigênio devido à ação do redutor utilizado.
Grau de metalização refere-se àquela porção do ferro total presente como ferro metálico.
Grau de metalização =(peso do ferro metálico/peso do ferro total)* 100 =(Fe M/Fe T)*100
Metalização equivalente – O teor de carbono no ferro-esponja em um determinado grau de metalização é importante. Tem a capacidade de remover o oxigênio dos óxidos de ferro restantes durante a fabricação do aço. Isso leva ao conceito de metalização equivalente, que é definido a seguir.
Metalização equivalente em % =Grau de metalização (%) + 5 vezes a % de carbono total em DRI
Redução percentual refere-se ao oxigénio que foi removido na produção do DRI com referência ao Fe inicial como Fe2O3.
% de redução ={[(%O/% Fe T) em Fe2O3 – (%O/% Fe M) em DRI]/(%O/%Fe T) em Fe2O3}*100
% de redução =[1- 2,327* (%O/%Fe T) em DRI]*100
Esta definição dá o estado do ferro contido no DRI. A confusão pode surgir quando algumas pessoas definem a redução percentual em referência ao estado inicial de óxido do minério, que pode incluir Fe3O4 e FeO. Nesse caso, a redução percentual define a quantidade de redução realizada no processo DRI.
Porcentagem de ganga refere-se aos compostos não ferrosos (SiO2, Al2O3, CaO, MgO, etc.) no DRI.
Ganga =100 – %O com Fe – %Fe M – %C
Basicidade quaternária é a razão de CaO, MgO e Al2O3, SiO2, e é expressa como a razão de (% CaO + % MgO)/(% Al2O3 + % SiO2).
Processo de manufatura
- Uma introdução à sinterização a laser de metal direto
- Quais são as tinturas e o processo de tingimento?
- Hovercraft RC baseado em Arduino DIY
- O processo de sinterização de finos de minério de ferro
- Gaseificação de carvão
- Processo HIsmelt de fabricação de ferro
- Tecnologias para Melhoria do Processo de Coqueamento em Fornos de Coque de Subprodutos
- Uma introdução à bomba direta
- Entendendo o processo de fundição de minério de ferro
- Entendendo o processo de extrusão