Preparação e Carregamento da Carga do Alto Forno
Preparação e carregamento da carga do alto-forno
O alto-forno (BF), exceto em sua fornalha, é basicamente uma passagem para gases e partículas de carga que se movem em contracorrente no BF. O requisito básico para a operação estável do BF é manter no forno uma camada de carga móvel que não flutue muito. Especificamente, é para formar um fluxo de gás estável e uma estrutura de camada de carga livre de camada de carga mista. Estes estão intimamente relacionados entre si. A estabilidade do fluxo de gás depende quase inteiramente da permeabilidade da carga, que é determinada pela estrutura de empacotamento da carga (tamanho da partícula, distribuição do tamanho da partícula e proporção de partículas finas etc.), e o comportamento de descida da carga, que é o fluxo sólido.
Em princípio, o processamento BF é um sistema complexo de fluxo em contracorrente, cocorrente e/ou corrente cruzada, de 4 fases, composto por sólidos, gases, líquidos e pós. As interações das fases são distintas e localizadas em diferentes regiões do BF. Existem normalmente cinco zonas distintas (Fig 1) em um BF a saber (i) zona irregular, (ii) zona coesiva, (iii) zona ativa de coque, (iv) zona de combustão (raceway) e (v) zona de homem morto ( região do centro da lareira). Devido às diferenças nas fases de carga e interações distintas em regiões particulares do BF, não há um único movimento de carga ou padrão de fluxo em todo o volume do BF.
Fig 1 Zonas de um alto-forno
Existem geralmente quatro tipos distintos de regiões de fluxo sólido no BF. Estas são (i) região de fluxo em pistão que está associada com a velocidade uniforme da carga descendo da linha de estoque e posição logo acima da zona coesiva ou de fusão, (ii) região de fluxo estagnado (dead-man) que é uma massa descontínua de partículas de coque reagidas na parte central da fornalha, (iii) região de fluxo parcialmente estagnada que é adjacente ao homem morto onde há um movimento lento de partículas de coque parcialmente reagidas e (iv) região de fluxo convergente que está ao redor da pista com variação significativa da velocidade das partículas dentro da distância da zona estagnada da parede do forno.
O mecanismo para a descida da carga envolve o desaparecimento de minério e coque através de sua reação, fusão e combustão, o movimento das partículas de carga no topo da camada de carga e próximo à parede do forno e a infiltração de matéria-prima de grão fino em um camada de granulação grossa etc. Os fatores que influenciam a carga descendo no BF incluem a condição das matérias-primas (tamanho da partícula, resistência, distribuição da carga - relação minério/coque), a condição da pista (injeção auxiliar de combustível) e o forno perfil de parede interna etc.
A operação do BF é bastante sensível ao perfil, distribuição do tamanho das partículas e todos os fatores que afetam o desempenho e a produtividade. Para garantir o bom funcionamento do BF, é essencial otimizar a distribuição dos materiais de carga sólida (minério de ferro, coque e fundentes) na linha de estoque. É importante controlar o estado interno do BF através do controle adequado da distribuição de carga no nível da linha de estoque.
O material de carga do BF deve atender a certos requisitos necessários para uma operação suave do BF. É para cumprir os requisitos mecânicos, químicos e térmicos. O material carregado deve formar uma estrutura forte e permeável para suportar a carga e permitir a passagem do gás redutor no eixo BF. A desintegração precoce da carga deve ser evitada, uma vez que a formação de finos perturba o fluxo de gás redutor no eixo, diminuindo assim a eficiência do processo. Assim, a carga de materiais de carga fina no BF deve ser eliminada.
O movimento descendente da carga, reações químicas, perfis térmicos e movimento do líquido nas zonas devem ser otimizados com o objetivo de maximizar a produtividade e garantir a operação estável do forno. A obtenção de uma operação de alta produtividade de BF estável e alta pode ser realizada por meio da otimização dos processos no forno e das operações periféricas, como controle completo das propriedades físicas e químicas das matérias-primas e distribuição de partículas. Tanto os processos no forno (alterações físicas do material carregado e reações químicas) quanto as operações auxiliares periféricas (armazenamento de carga, recuperação, transporte, armazenamento, descarga, transporte e carregamento) são funções sobrepostas para o bom funcionamento do processo BF que não podem ser tratadas isoladamente, pois são processos vinculados.
O material de carga BF, ou seja, minério de ferro, coque e fundentes são classificados como sólidos a granel, pois apresentam uma semelhança com partículas sólidas discretas que estão em contato umas com as outras. Esses materiais, como quaisquer materiais granulares, são feitos de partículas que interagem. Geralmente, a estrutura interna desses materiais é bastante evolutiva. De acordo com as classificações de material sólido a granel fornecidas na Tab 1, o material de carga para o BF é classificado volumosamente como um sólido quebrado/descontínuo.
Guia 1 Termos qualitativos para classificação de tamanho de sólidos a granel | |||
Sl. No. | Intervalo de tamanho em mm | Termo típico | |
Componente | Em massa | ||
1 | Menos de 0,1 | Partícula | Pó |
2 | 0,1 a -1 | Grânulo | Sólido granular |
3 | 1 a -3 | Grão | Sólido quebrado |
4 | 3 e superior | Protuberância | Sólido quebrado |
Em geral, o manuseio de sólidos a granel em qualquer forma apresenta um desafio em termos de manutenção da homogeneidade. Considerando partículas de mesmas propriedades físicas e químicas como componentes discretos dos sólidos a granel, foi demonstrado que a mistura (intencional ou não) de sólidos a granel inevitavelmente resulta em partição natural dos componentes. Este conceito é geralmente conhecido como segregação (de-mixing). Naturalmente e/ou industrialmente, a segregação entre componentes discretos dos sólidos a granel pode ser benéfica (por exemplo, em processos de separação física) ou prejudicial (por exemplo, em processos de mistura), dependendo da função pretendida do produto ou operação da subunidade.
Aspectos teóricos do manuseio de materiais de carga
Os materiais de carga BF consistem em coque, sinter, pellets, minério granulado calibrado (CLO), calcário, dolomita, minério de manganês e quartzito. Devido à natureza do processo, o processo BF é essencialmente sensível ao tamanho do material de carga, à distribuição e à resistência. A distribuição dos materiais de carga no BF afeta o movimento ascendente do fluxo de gás, bem como a química do processo, a transferência de calor e massa entre as diferentes fases do processo. A resistência do material é bastante importante porque à medida que o material desce, a carga aumenta. A integridade da carga é ainda mais comprometida por reações químicas subsequentes que ocorrem em alta temperatura e pressão, onde o atrito e a quebra são predominantes.
O coque BF serve como material de estrutura de suporte durante a operação do BF, pois é o único material de carga que desce para o forno do BF com reações parciais de solução. Constitui uma alta proporção dos custos de produção de metal quente (HM). Nos últimos anos, há um impulso para substituir o coque por fontes alternativas baratas de carbono. A alternativa normalmente utilizada é a injeção direta de carvão nas pistas em um processo geralmente conhecido como injeção de carvão pulverizado (PCI). No entanto, existe um limite teórico para a extensão da substituição, uma vez que o BF desprovido de coque adequado sofre de permeabilidade de carga reduzida, uma posição que leva à asfixia e suspensão do forno, um cenário que resulta ainda na ocorrência de escorregamento do forno.
A composição da carga de BF determina variáveis do processo no forno, como temperaturas de fusão, amolecimento, bem como alguns parâmetros de redução, o que afeta negativamente a produção se a distribuição da carga não for otimizada. Com tais limitações e desafios, existe a necessidade de um controle adequado da distribuição da carga. A faixa de tamanho típica dos materiais de carga BF é fornecida na Tab 2.
Guia 2 Faixa de tamanho típica de materiais de carga de BF | |||
Sl. No. | Componente do material | Tamanho em mm | |
Mínimo | Máximo | ||
1 | Coque BF | 25 | 50 |
2 | Minério granulado calibrado | 10 | 30 |
3 | Sinterização | 5 | 30 |
4 | Pelete de minério de ferro | 8 | 20 |
5 | Calcário | 10 | 40 |
6 | Dolomita | 10 | 40 |
7 | Minério de manganês | 10 | 40 |
8 | Quartzito | 10 | 40 |
9 | Coque de nozes | 10 | 25 |
Os fenômenos físicos e a estrutura do fluxo granular, incluindo o material de carga BF, parecem simples à primeira vista, mas na realidade mostram um comportamento complexo que é difícil de entender e prever. A situação é ainda mais complicada pela falta de informações diretas sobre os parâmetros de mistura e segregação para tais processos. No entanto, devido ao tamanho dos agregados do material de carga BF e à grande distribuição do tamanho do material, a tendência de segregação é um problema operacional sério que deve ser reduzido tanto quanto possível.
Manuseio de materiais a granel e comportamento do fluxo
A compreensão fundamental do comportamento e fluxo de materiais a granel permanece inadequada, apesar do fato de que os elementos da mecânica do pó são conhecidos desde meados do século XIX. Isso se deve principalmente às características únicas e complexas da física do fluxo. O manuseio de materiais a granel mostra um comportamento interessante. Um aspecto é a capacidade de uma mistura macroscópica de partículas desmisturar devido às propriedades individuais das partículas. Essas observações são principalmente resultado da tendência natural desses materiais ao desenvolvimento de padrões e à auto-organização. Este fenômeno é principalmente devido ao comportamento de materiais a granel para se assemelhar a características semelhantes a fluidos.
Na medida em que os materiais a granel se assemelham a características de fluido e em si mais parecidos com um sólido, o comportamento e as características gerais são completamente paralelos às observações nessas formas comuns de matéria. Normalmente, ao contrário de outras formas de matéria em que a dinâmica é afetada pela temperatura normal, esse efeito é insignificante na dinâmica de materiais a granel. É útil saber que competir por advecção caótica ou efeitos de mistura típicos de fluidos é responsável pela tendência de auto-organização observada em materiais a granel, enquanto a segregação induzida por fluxo não tem fenômenos de fluido.
O macrocomportamento dos processos fundamentais é governado principalmente pelo contato entre as micropartículas e pelas forças de atrito. Considerando os tamanhos dos materiais de carga BF que são superiores a 5 mm, os efeitos das forças de superfície, nomeadamente os efeitos eletrostáticos, van der Waals e capilares, são insignificantes. Além disso, o comportamento de fluxo dos materiais de carga corresponde a sólidos não coesivos, uma vez que as tendências coesivas são típicas para material em pó superfino ou ultrafino com tamanho de partícula inferior a 10 micrômetros.
Classificação do fluxo de materiais a granel
O fluxo de materiais a granel pode ser classificado de acordo com seus componentes, que podem ser definidos como um grupo de partículas com as mesmas características físicas, como tamanho, densidade e forma das partículas. A estrutura do fluxo é muitas vezes difícil de analisar e é significativamente influenciada pelas interações partícula a partícula, bem como excitações externas e condições de contorno. Como resultado, não há um método abrangente e genérico para descrever completamente toda a estrutura de fluxo de materiais a granel. Dependendo do segmento de tempo em que as partículas estão em contato, vários tipos diferentes de estruturas de fluxo distintas podem ser estabelecidas.
No caso de fluxo de material a granel, o fluxo granular mostra um número variável de estados instáveis metaestáveis. Esses estados instáveis metaestáveis duram indefinidamente se não houver distúrbios externos, como vibrações. A sustentação de tais estados depende em grande parte do segmento de tempo em que as partículas e os limites estão em contato. Isso depende da fração de volume de sólidos em relação ao volume total de fluido (gás ou líquido). Como resultado, o fluxo de materiais granulares é geralmente classificado como diluído ou denso (dominado por contato), dependendo da fração volumétrica de sólidos. Dependendo de um segmento de tempo em contato, o fluxo denso pode ser subcategorizado como dominado por colisão ou dominado por contato. Nessas três classificações, o comportamento e o fluxo característico são distintos para uma classificação particular. As interações fluido-partícula (ou seja, forças de sustentação e arrasto) dominam o movimento da partícula em fluxos diluídos, enquanto as colisões partícula a partícula ou partícula a parede ou o contato contínuo de partícula a partícula dominam fluxos densos.
A representação esquemática da classificação de material a granel entre fluxos diluídos, fluxos densos dominados por colisão e fluxos densos dominados por contato é mostrada na Fig 2. As classificações de material a granel diluído na Fig 2 podem ser observadas em separadores de ciclone, leito fluidizado e tremonha de material BF fluxo respectivamente. Os fluxos densos (dominados por colisão e contato) são típicos dos materiais a granel BF durante os processos de descarga, armazenamento e transporte.
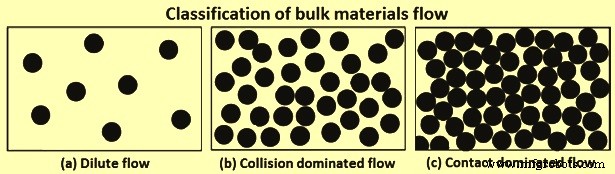
Fig 2 Classificação do fluxo de materiais a granel
Duas classificações de fluxo de materiais densos
A característica comum dos dois regimes de fluxo denso é uma progressão estrutural em função do comprimento e das escalas de tempo. Normalmente, isso leva à formação de padrões devido à reorientação das partículas. Tal orientação de materiais é impulsionada por estruturas de escala intermediária. A escala de partículas individuais, mais conhecida como microescala, é separada da escala macro ou contínua pela escala intermediária. Compreender as interações de partículas complexas de conjuntos de fluxo granular é fundamental na quantificação do fenômeno de segregação ou desmistura. Nesse sentido, deve-se estabelecer a relação entre o comportamento macroestrutural (em massa) e a dinâmica microestrutural (discreta) subjacente.
Fluxos dominados por colisões – Em escoamentos dominados por colisões, o escoamento é disperso, disperso e energético, com partículas interagindo predominantemente por colisões quase instantâneas e binárias. Os efeitos inerciais podem ser ignorados. As colisões são inelásticas e a energia é dissipada durante as interações partícula-partícula ou partícula-limite. Uma vez que as colisões são dissipativas, é necessária uma fonte de trabalho para sustentar a “fluidez” do material granular. Devido à natureza dissipativa das colisões, são observados comportamentos e padrões distintos de fluxo, como agrupamento e ondas de densidade. A onda de densidade é um fenômeno ligado à temperatura granular, onde as partículas não fluem uniformemente, mas sim em regiões com velocidade diferente da velocidade média.
Fluxos dominados por contato – Em escoamentos dominados por contato, as colisões de partícula a partícula são fortemente correlacionadas, nem binárias nem instantâneas, mas sim duradouras e múltiplas. Este fluxo mostra dois cenários característicos interessantes onde há tensão de cisalhamento crítica abaixo da qual o fluxo é possível e uma intrincada dependência da taxa de cisalhamento quando o fluxo começa. Como resultado dessa dependência, uma estrutura de fluxo completa requer a inclusão de características visco-plásticas associadas ao fluxo dominado em contato.
Existem várias leis constitutivas propostas com base em diferentes tratamentos e várias considerações, como adicionar um grau de liberdade através da rotação local, introdução da regra do fluxo estocástico e modificação dos coeficientes de transporte da teoria cinética, como termos viscosos, frequência de colisão e termos de dissipação. Uma formulação recente na qual um parâmetro denominado número de inércia parece ser uma formulação robusta, capaz de reproduzir uma ampla gama de características visco-plásticas dos escoamentos dominados por contato. O número de inércia é a taxa de cisalhamento multiplicada pela raiz quadrada da massa da partícula dividida pela pressão.
Mistura e segregação de materiais granulados
O manuseio de materiais granulares é bastante complicado, especialmente quando a distribuição de homogeneidade e uniformidade é necessária devido à tendência natural à segregação (desmistura), especialmente se os tamanhos dos materiais variarem muito. Ao contrário dos processos de fluidos em que a mistura promove a homogeneidade, o fluxo granular se assemelha a uma imagem espelhada de mistura e segregação, na qual a tendência de mistura prolongada promove a separação (segregação). Assim, no caso de materiais de carga BF que passam por processos repetitivos de manuseio, é útil tratar a mistura como um recurso silencioso.
A ordem natural do material granular é a segregação ou desvio do comportamento uniforme. Dependendo do estado do sistema (carga, armazenamento, descarga e transporte) ao qual o material granulado é exposto, existem diferentes formas de mecanismos pelos quais ocorre a segregação. Os principais fatores de segregação são uma diferença de tamanho de partícula, diferença de densidade, bem como diferenças de micropropriedades, como efeitos de atrito, coeficiente de restituição e ângulo de repouso. Dentre esses fatores, o tamanho das partículas parece ser o fator mais importante na determinação do comportamento segregante das partículas granulares.
Mecanismos de segregação de material granular
Em um estudo para minimizar a segregação, treze mecanismos de segregação de material granular foram propostos. No entanto, a maioria desses mecanismos são casos especiais ou sobrepostos de outros mecanismos. Considerando isso e para ter flexibilidade, a classificação de segregação de materiais granulares foi simplificada em cinco mecanismos principais. Nestes cinco mecanismos simplificados, os mecanismos de fluidização e segregação de aglomeração referem-se a partículas finas e coesivas respectivamente e não são aplicáveis para os materiais de carga BF. Assim, os três principais mecanismos de segregação restantes que são aplicáveis à carga, armazenamento, descarga e transporte de material de carga BF são descritos abaixo.
Mecanismo de peneiramento ou peneiramento dinâmico – Quando partículas com uma faixa de distribuição de tamanho são feitas para interagir (por exemplo, em uma caixa de armazenamento de material), a consolidação espontânea pode ocorrer com as partículas menores percolando e peneirando para baixo através de interstícios de grandes frações. Naturalmente, quando os materiais granulares fluem, a lacuna granular se alarga e quando isso acontece, os interstícios são criados. Pequenas partículas podem se espremer em pequenos interstícios abaixo de uma grande partícula, mas o inverso é muito menos provável de ocorrer, resultando em um fluxo segregante líquido das partículas menores para baixo, longe da superfície livre. Esta ação é normalmente conhecida como percolação. No estado estacionário, as partículas segregam com uma camada inferior com muitas partículas finas. O mecanismo de percolação é mostrado na Figura 3. Em um sistema binário com diâmetros de partículas, d1 e d2, onde d2 é maior que d1, ocorre peneiramento espontâneo quando d1/d2 é menor ou igual a 0,1547. O primeiro uso desta razão crítica foi feito para derivar um modelo detalhado para segregação devido a diferenças de tamanho de partículas em um fluxo de chute baseado no mecanismo de percolação.
Fig 3 Esquema do mecanismo de segregação por percolação
O mecanismo de segregação por percolação é intensificado pela indução de cisalhamento através do movimento de vibração, como telas vibro com partículas de tamanho grande e alta densidade migrando para o topo. Isso sugere que apenas considerações geométricas são necessárias para a segregação em sistemas vibrados. Em suma, para que o mecanismo de segregação por percolação ocorra, três condições precisam ser satisfeitas principalmente, que são (i) razões de tamanho crítico para peneiramento, (ii) partículas pequenas precisam ser não coesivas para passar pelos interstícios e (iii) existência de tensão suficiente ou movimento entre partículas para aumentar a probabilidade de orientação de partículas finas para os múltiplos interstícios.
Mecanismo de trajetória - O mecanismo de segregação acionado pela trajetória é normalmente visto nos pontos de transferência de material de carga, principalmente enchendo as caixas de armazenamento, descarregando das tremonhas de armazenamento e descarregando no final das correias transportadoras, conforme mostrado na Fig 4. Em um estudo investigando as condições de fluxo para garantir um fluxo suave de materiais granulares, foi apontado que materiais de tamanhos diferentes se movem em velocidades diferentes devido ao arrasto de atrito diferente que causa a segregação do material. O mecanismo de segregação da trajetória foi explicado matematicamente considerando partículas projetadas horizontalmente em um fluido. Considerando uma pequena partícula de diâmetro d, densidade Dp e arrasto governado pela lei de Stokes, foi mostrado que a distância máxima X, percorrida pela partícula com velocidade de projeção inicial Vi, em um fluido de viscosidade Vf e densidade Df, é dado na Equação X =Dp.Vi.(Dp)2/18 Vf. No entanto, ao considerar os tamanhos dos materiais de carga BF e assumindo que a força de arrasto é desprezível, a trajetória das partículas é dada por uma equação de trajetória adimensional. A equação da trajetória adimensional é y/x =tan A – [g/2 (cos A)2]. x/Vi, onde xey são coordenadas espaciais horizontais e verticais respectivamente, A é o ângulo de inclinação, g é a aceleração da gravidade e Vi é a velocidade inicial em voo livre. A partir da equação, pode-se ver que a trajetória da partícula é independente do tamanho (massa), mas sim da velocidade aleatória no início da queda livre associada a cada partícula individual.
Fig 4 Esquema do mecanismo de segregação de trajetória
Mecanismo de diferença de micropropriedades – Sob este mecanismo, existem três efeitos:(i) efeito de atrito (ii) efeito do coeficiente de restituição e (iii) efeito do ângulo de repouso.
O estudo do efeito de atrito sobre o material granular mostrou que o material granular com dois componentes com coeficiente de atrito estático diferente F, normalmente segrega. Durante o estudo, foi considerado um caso para uma partícula esférica com massa m a uma altura h, o coeficiente de atrito de deslizamento Fs, o coeficiente de atrito de rolamento Fr e raio r, descarregando sobre um declive com um ângulo de inclinação A, como mostrado na Fig. 5. Considerando os princípios de conservação de energia, se uma partícula em equilíbrio instável satisfaz a equação de momento dada na equação m.g.sin A.r =m.g.cos A. Fr. Nesta equação, a distância de deslocamento da partícula, X, pode ser obtida pelas equações X =(h/Fs).(Cos A)2.(1-Fs/tan A) e X =(r.h/Fr).(cos A) 2. (1- Fr/r.tan A). Essas duas equações fornecem as distâncias de deslocamento das partículas derivadas considerando o coeficiente de atrito de deslizamento e rolamento, respectivamente. A partir dessas equações, pode-se ver que a distância de deslocamento da partícula é dependente do diâmetro da partícula quando o coeficiente de atrito de rolamento é considerado e isso resulta em segregação. Pelo contrário, os efeitos de atrito de deslizamento mostram independência tanto do tamanho quanto da massa das partículas.
Fig 5 Esquema do movimento de partículas em um limite inclinado
O mecanismo do efeito do coeficiente de restituição é, em princípio, um efeito dinâmico. Quando as partículas colidem ou impactam os limites do sistema, elas saltam em diferentes velocidades e a posição final é determinada pela resiliência interfacial. Um exemplo do mecanismo é o carregamento de partículas em uma pilha ou em uma caixa de armazenamento. No impacto no ponto mais alto da pilha, as partículas pouco resilientes não saltam, mas ficam presas em sua posição. Pelo contrário, aquelas partículas com alta resiliência saltam e encontram uma posição final em algum lugar longe do local de deposição e possivelmente se concentram na periferia da pilha.
No caso do efeito ângulo de repouso, o mecanismo de segregação é observado durante o empilhamento do material granular. Ao construir uma pilha, verifica-se que o ângulo de inclinação (ângulo de repouso) depende do tipo de material e é independente do número de partículas. Em um estudo sobre efeitos de contorno sobre o ângulo de repouso em tambores rotativos, foi apontado que a segregação axial é influenciada pelo ângulo de repouso estático ou dinâmico. Em princípio, o efeito do ângulo de repouso depende dos parâmetros do material como tamanho da partícula, distribuição, forma e forças de atrito e, como tal, torna-se um mecanismo misto devido à inclusão de outras variáveis para o efeito.
Classificação da segregação de material granular
A segregação de materiais granulares é classificada com base nas variáveis consideradas para o processo considerado. Principalmente, é classificado com base em (i) propriedades físicas das partículas (ou seja, tamanho, densidade ou segregação de forma), (ii) entrada de energia (ou seja, vibração, gravidade ou segregação de cisalhamento), (iii) orientação do movimento das partículas (ou seja, horizontal , ou segregação vertical) e (iv) equipamento usado (ou seja, tremonha, calha ou transportador).
No entanto, o processo natural ou estabelecido mais conhecido como o mecanismo pelo qual a segregação é criada parece ser a abordagem de classificação mais comum. A segregação é amplamente considerada como um fenômeno de superfície. Como tal, os diferentes mecanismos observados são independentes das partículas abaixo das camadas superficiais. Em princípio, os mecanismos podem ser explicados considerando apenas o comportamento das partículas da camada superficial em movimento. Em vários tipos de segregação, em princípio e na maioria dos casos, o mecanismo geral de segregação é uma combinação de vários mecanismos de interação. Por exemplo, a segregação por peneiramento pode ser considerada um caso especial de segregação por percolação e deslocamento/migração, uma vez que ambas compartilham o princípio de filtragem de partículas pequenas em relação a partículas grandes.
Quantificação de segregação
Embora haja algum entendimento dos mecanismos e efeitos da segregação no fluxo de material granular, para que os problemas decorrentes desse fenômeno sejam adequadamente encapados, há a necessidade de passar da prevenção da ocorrência para o controle da segregação. Nesse sentido, métodos precisos de medição de segregação qualitativa e quantitativa são necessários para entender e controlar completamente os efeitos, principalmente no caso de materiais de carga de BF, que passam por um processo de manuseio repetitivo. Uma descrição completa da distribuição de partículas é um exercício não trivial em tais circunstâncias. No entanto, para sobrecarregar com precisão a linha de estoque do forno, é imperativo ter o conhecimento da distribuição do material particulado juntamente com a quantificação da mistura e segregação em fluxos granulares.
Índices de medição de segregação – Em princípio, a segregação é uma fração de um fluxo de material granular complexo. Além disso, a opacidade do fluxo granular torna praticamente difícil, se não impossível, extrair fisicamente dados úteis durante os estudos de segregação. A incorporação adequada de formulações teóricas em simulações de modelagem matemática pode tornar mais fácil caracterizar melhor a mistura de fluxo granular e a segregação de tais sistemas. A quantificação da segregação é uma tarefa importante, pois envolve a inclusão completa das inter-relações entre os fatores que causam a segregação e as equações de movimento das partículas. No entanto, vários índices para medir a qualidade da mistura granular, que podem ser usados como uma medida quantitativa de segregação, foram propostos e são geralmente expressos em termos estatísticos ou em termos numéricos adimensionais. As métricas comuns de mistura e segregação usadas são o desvio padrão relativo (RSD) que considera apenas o sistema de componente único. Esta métrica de segregação RSD é uma métrica de aplicação industrial reflexiva, pois fornece o estado macro misto de mistura para todo o sistema.
As métricas de medição de mistura e segregação são a espinha dorsal de muitos índices que estão sendo usados. É importante entender que a amostra concentrada e a medida de variância particular são usadas para definir o índice de mistura e/ou segregação. Embora a quantificação seja bastante informativa, a principal desvantagem de tal caracterização é a média sobre um domínio de medição enquanto negligencia a variação de distribuição de partícula para partícula que permanece desconhecida. Além disso, nos conceitos clássicos e fundamentais que foram desenvolvidos sobre mistura e segregação de materiais granulares, o processo de segregação granular foi definido e concluído como um fenômeno de superfície.
Vários estudos mostraram e provaram que diferentes formas de equipamentos de manuseio, modo de operação e propriedades do material podem ser correlacionadas com o comportamento de mistura e segregação do material. O grande desafio que ainda permanece é ter uma metodologia de caracterização unificadora, que não apenas descreva a dinâmica de mistura, mas também aborde essencialmente os fenômenos de segregação mais complicados. Uma nova abordagem é caracterizar a evolução das relações partícula a partícula em matérias-primas dentro do sistema de carregamento, de modo a informar a extensão da mistura e segregação no tempo e no espaço. O pivô do método é baseado na ideia de que alguns aspectos da relação entre a partícula e seus vizinhos mais próximos podem ser usados para deduzir insights úteis sobre o processo dinâmico de partículas em evolução.
Modelos de segregação mecânica de fluxo granular
Foi visto que a cinética de segregação é amplamente e em geral enquadrada em uma estatística matemática e estrutura de probabilidade. The apparent limitation to this approach is that the absolute reflection of the physical nature of the process is precluded coupled with the failure to prescribe the direction in which segregation is taking place. This limits the possibility of a generalization since the knowledge is quite empirical. In the first pioneering study to develop mechanistic models which incorporate all the physics surrounding the prevalent de-mixing tendencies that occur in real granular flow system, the application of kinetic theories for mixtures of granular materials has been applied to study segregation tendencies based on percolation mechanism. Using a combination of statistical and dimensional analysis, the developed formulations hold for negligible enduring frictional contacts with shear rates sufficiently high so that the dominant contributions to the total stresses are due to particle to -particle and particle to boundary collisions. In this study, it has been observed that in a chute flow with high solids volume fractions, there is a high probability of small voids formation relative to big ones. The resulting effect of such a postulation is that small particles sieves through and collects at the base of the bed. This results in a net segregation flux in a direction normal to the chute surface of the small particles.
In as much as the mechanistic models described above give some intended physical appreciation in segregation description, evaluation of key fundamentals such as dispersion coefficients of such granular flows are not small and cannot be established by the above models. In this direction, one study suggested mixed statistical and mechanical interactions based on the kinetic theory of dense gas systems since they give a general understanding of causes of granular flow segregation.
Clustering occurs as granular flow experiences damping as energy is lost after collisions. The change in velocity and movement is non-uniform hence the clusters are formed. Hence, constitutive equations have been proposed based on a kinetic theory for collisional rapid flows. The utilization of the kinetic theory expressions for the analysis of granular segregation shows that it can be used only for inelastic and different sized particles at low volume fractions. This is a limitation as typical granular flow systems are contact-dominated flows with high solids volume fractions. The application of the theory is more useful in case there are established constitutive equations for inelastic, different sized particles and high solids volume fractions.
It is seen that the granular flow resembles mixing and segregation mirror image in which the prolonged mixing tendency promotes segregation. The concentration gradients results in mixing whereas the individual contributions of pressure and temperature gradients produce segregation in granular flow systems characterized by particles with particle size range distributions and material density differences.
The theoretical aspects of the bulk handling of the materials have given a general but compact back ground on granular flow, free surface segregation, mechanisms and theoretical approaches in granular material processes. BF burden material storage, handling and transportation processes are susceptible to the fate associated with segregation. For example, the BF sinter material is known to have more in-bin size segregation and more out of bin size variation than the BF coke.
BF charging system
The charging system of the BF iron-making process can generally be described as a network of equipment and mechanisms designed to charge materials into the BF in a certain sequence, quantity and at a rate which ensure that the specified furnace productivity and prescribed stock-line level is maintained. The charging system consists of three sub-systems which are essentially responsible for (i) batching (ii) transportation, and (iii) charging into the furnace respectively. Batching is done in the stock-house which receives the bulk solid feed materials from their various sources (stockpiles, sinter plant, and coke ovens), storing each material in individual bins to provide several hours of feed material for usual BF operations. The batching process includes screens, weigh-hoppers, conveyor belts, feeders and control systems to prepare batches of charge materials. Transportation provides the means for the delivery of the materials to the top of the furnace. Normally, this is done with either by the belt conveyor system or the skip hoist arrangement. The third sub-system consists of a network of equipment and mechanisms for the charging and control equipment. The overall charging system is interconnected and controlled by an automated charge programme.
Under some conditions, furnace productivity can be limited due to the capacity of the batching (stock-house) process to deliver charge materials. This occurrence is mainly due to transient charge materials flow, equipment settings and charge requirement (burden ratios). A typical source of transient change in charge composition is caused by changes in materials delivered to the stock-house bins and is usually referred to as ‘stock transitions’. This normally occurs when the reclaimed material is used such as the substitution of fresh coke and sinter with stored coke and stored sinter respectively. Such reclaimed materials are known to alter furnace performance compared with the fresh materials. Hence, there is need and usefulness of knowing the different materials and to have their accurate tracking through the charging system so that burdening and blast parameters can be controlled optimally to maintain furnace operational stability.
One other important feature of the charging system is the mixing and segregation of charge material. For example, accurate weighing of several materials in the same hopper requires sequential delivery of the material. However, when the weigh hopper discharges, the materials inherently intermingle to some extent, yielding a time-varying composition of the delivered stream. It is imperative to have an accuracy of time-varying composition in order to estimate the radial variation in burden chemistry and physical properties of the material delivered to the furnace.
Since the burden materials undergo multi-stage handling, hence the processing of different types of charge materials need greater control for high productivity and stable operation of the BF. Also, charge material batching and transportation phenomena are required to be the key focus area for BF operator. For smooth BF operation, the operator is to be position to accurately track the burden materials upto their delivery to the furnace charging system.
The overall charging system is interconnected and controlled by an automated charge program which is coordinated by discrete event processes. Previously, BFs were generally small compared to the modern-day large capacity BFs. In small furnaces, the theoretical amount of coke was normally determined as the controlling charging factor as such, with skip charged furnaces, the optimum charging capacity is reached with full skips of coke.
In the modern BF operations, over and above the need to cope with burden material requirements of larger BF capacity, there are two additional operational factors which are (i) sustenance, and (ii) environmentally friendly operations. Sustenance is mainly through the realization of high furnace productivity which currently has been achieved by an array of technology uses. With this added dimension, the total skip weight is now normally the controlling charging factor and thus modern furnace can work with full skips of iron-bearing burden component. Considering the large size of the present day BFs, the required skip capacities become extremely large and as a result, the design and installation of such skip charging facility to cater for such a huge continuously charging system pose a challenge. Such commensuration of modern large furnaces can only be achieved with sufficient burden delivery capacity. As a result, the modern furnaces are equipped with the conveyor belts charging system. The modern BFs charging facilities consist of a stock-house with a conveyor belt transportation of burden materials to the BF bell-less top (BLT) charging system.
BLT charging system
The charge material is conveyed to the BLT charging system where it is eventually charged into BF top material hoppers (bins) which are alternately used. While one hopper is being filled, the other one is being discharged. The operation of weigh-hoppers and material hoppers is essentially the same and thus, the further description gives an account of particle behaviour during conveyance (conveyor belt), intermediate storage (material bins and weigh hoppers) and eventual discharge (chute or free fall).
Conveyor belt particles behaviour – It is seen that the granular material of varying size fractions and density cause segregation. The detailed phenomenon of the transport mechanism of granular material on a conveyor belt remains limited. However, segregation phenomena on a conveying system are difficult to explain without elaborate simplification of the problem. The system under study has to be defined in terms of mass flow rate and the conveyor speed which promote particle bed development. Operative mechanism of segregation can be established only if the system is well defined. In Fig 6, a schematic representation of the particle size segregation at the transfer point of a moving conveyor belt is shown.
Fig 6 Schematic representation of the particle segregation at the transfer point of a moving conveyor belt
It has been established that there are four main mechanisms to be considered in conveyor belt material movement segregation namely (i) percolation, (ii) particle migration, (iii) trajectory, and (iv) free surface segregation.
Material bins and weigh-hoppers particles behaviour
Granular material bins and weigh hoppers are often used for storage and eventual discharge of material to the subsequent process step. They both in principle have (i) a form of defined material feeding or filling mechanism, (ii) some retention time of material, and (iii) a defined discharge region below. All the three steps have a contribution to the overall material flow behaviour at discharge. Physical and numerical simulations have been done to clarify the relevant information about particle segregation in different kind of hoppers namely cylindrical, bins, conical, and wedge-shaped. The desirable operation is a proportionate outflow from these devices. However, since the flow is gravity induced, the outflow is not easily controlled and there are an inherent induced shear and dynamic effects which cause segregation.
The main prevalent mechanisms of segregation in material storage bins and hoppers are free surface (during feeding), percolation (during retention) and trajectory (during discharging). There is also the importance of particle size and boundary geometry dimensions during the emptying and discharge phases.
In a study to investigate how the internal angle of hoppers affect the granular flow, it has been identified some significant hindrance to free-flow for cohesion-less solids using digital particle image velocimetry (PIV) measurements. As a rule of thumb, to avoid mechanical arching (particle interlocking), the ratio Do/dp (max) is to be satisfied in the range of 5 to 10. Here Do is the boundary outlet diameter and dp (max) is a suitable maximum particle diameter. The ratio is the dimensionless characteristic scale number and it is mostly influenced by the angle of repose as well as the particle size distribution of the material.
In another study, it has been suggested that at least eight elements are to fit across the total width of any granular material handling devices in order to capture accurately the material flow rheology. This means that the diameter of the largest particle fractions in physical or theoretical experimentation is to be at most an eighth the width of a hopper, conveyor belt or any other granular material handling device outlet.
Chute flow particles behaviour
Granular material chute flow is a common feature of stock-house and BLT charging system. With the BLT charging system which comprises of the charge receiving system, material hoppers and rotating chute (distributor), chute flow has assumed additional importance. However, the core principles of the chute flow in the BF top charging system are the same as the one in the stock-house.
Chute flow can be characterized by defining three steps which are (i) burden movement before the chute, (ii) on the chute, and (iii) after the chute, as shown schematically in Fig 7. These three steps constitute three different flow classifications and as such, different considerations need to be employed to study the flow behaviour in this system. When considering burden movement before the chute, any particle collisions in this region can be ignored due to the dilute nature of the flow. When burden material is on the chute, a mathematical description can be used with velocity component along the chute being used as the initial velocity of the material flow. At the chute tip, the trajectory of the materials determines the impact point which in turn the final scatter and distribution of the material in the subsequent handling boundary/ equipment. It is possible that the mechanisms of segregation postulated for conveyor belts systems also apply to chute flow as such and segregation shown schematically in Fig 7 is possible. Three flow streams can be identified with the core flow sandwiched between lower and surface flow. At this stage, the main force considered is gravity.
Fig 7 Schematic of granular material flow in a chute
The knowledge of segregation associated with charge material is useful for understanding the charge proportioning in addressing one of the aspects of BF process intensification. However, process intensification in BF processing requires an optimized charging system capacity as BF productivity can be limited by the capacity of stock-house to supply the charge. There is a need to address and optimize multiple-handling operation stages in the product chain.
Charging system capacity analysis
The operation of the BF charging system is as critical as the design of the BF. As can be seen in the schematic representation of a typical modern BF charging system equipped with a conveyor belt delivery system in Fig 8, the material flow sequence is quite complex.
Fig 8 Typical charging system of a modern blast furnace with charging conveyor
In the interest of high productivity, the design of a BF charging system require attention to operating flexibility, availability of extra charging capability, high screening efficiency as well as a limited number of filling, discharge and transfer operations as these cause segregation problems. One important route to increase the efficiency of the BF is full utilization of the charging system capability. Further to this, if the stock-house is not adequately designed and optimal burden delivery is not achieved, the starvation of the BF take place due to the non-availability of the burden materials which consequently results into the loss of BF productivity.
As seen in Fig 8, there are numerous unit operations in a stock-house assembly and all of them have a cascading effect on the overall performance and output delivery to the BLT charging system. In order to understand the macro-behaviour of the burden movement and overall system performance, effective and comprehensive representation of salient system elements and their relationships are to be established. Technically, this involves a description of the various handling steps, materials requirements, duration and sequencing of operations. However, for complex systems such as the stock-house, it is a huge task to clarify all the unit process information. A blend of engineering judgement, experience from similar processes, and reasonable assumptions are used for model development input data and the stock house design.
Modelling of BF charging system optimization
BF charging system involves multiple-handling material movement. The major challenge associated with multiple-handling during materials movement is the timely fulfilling of the requirement and sudden change in the process. Simulations are often used to optimize materials handling systems. Such systems generally use computer-aided process design simulators. These simulators are generally designed to model transient and continuous processes and as such they cannot be used for BF charging system operations which is a batch and semi-continuous process at best. Two available options for modelling batch and semi-continuous processes like BF charging system are spreadsheets (Microsoft Excel) and discrete event simulation (DES).
Spreadsheet models are a common platform that focuses on material balances, equipment sizing and cost analysis. Typically, the development of such a model involves writing an extensive code (in the form of macros and subroutines) in visual basic for applications (VBA) which are incorporated in Microsoft Excel. They are easy to build, much applicable to simple systems but they lack robustness and become unwieldy for large and complex systems. DES is a mathematical/ logical model of a physical system which portrays state changes at precise points in simulated time. Both, the nature of the state change and the time at which the change occurs, mandate precise description. The main feature for a successful DES is an upfront requirement of precise details regarding system and interruptions. Typically, a DES can statistically account for downtime and events. Also, modules can be created and reused while multiple grades or change in process input can be easily handled. Hence, generally the DES-based model is normally used for the BF charging system.
Cyclograms analysis is a modest DES modelling technique which has been often used in BF charging systems for its optimization. The concept evolves on the minimization function of overall start – end sequence (delivery time) of a charging cycle. The delivery time is determined by the order of activation of the mechanisms, the duration of their sequence and the length of the intervals between individual operations. It is easy to follow that the minimum cycle duration occurs when the system is devoid of pauses between the operating cycles of individual mechanisms, as well as when the mechanisms are activated in an efficient sequence.
With cyclograms analysis, it is difficult to incorporate real-time changes in system input conditions. Furthermore, the structure of the analysis precludes detailed in-cooperation of micro-system variables such as discharge behaviour and segregation tendency of materials. Due to these weaknesses of the cyclograms analysis, a DES charge material delivery model based on a mathematical/ logical representation is the better choice for the BF stock house optimization
Processo de manufatura
- Escória de alto forno e seu papel na operação do forno
- Aspectos importantes do projeto de alto-forno e equipamentos auxiliares associados
- Sistema de automação, medição e controle de processos de alto forno
- Forno de indução e siderurgia
- Geração e uso de gás de alto-forno
- Produtividade do Alto Forno e os Parâmetros Influenciadores
- Operação de alto-forno e escória de alta alumina
- Sistema de resfriamento do alto-forno
- Sistemas de carregamento de alto-forno
- Fabricação de ferro por alto-forno e emissões de óxido de carbono