Sistema de resfriamento do alto-forno
Sistema de Resfriamento de Alto Forno
Considerando o enorme investimento de capital necessário para o reembasamento do alto-forno (BF), enormes esforços foram feitos no passado para estender a vida útil dos BFs. O desenvolvimento do processo de fabricação de ferro BF e os avanços nas ciências dos materiais melhoraram a produtividade, o consumo de combustível, a qualidade do produto e a vida útil da campanha do BF. A duração de uma campanha de BF até a década de 1990 foi influenciada principalmente pela vida útil do eixo inferior, ou seja, a área de maior carga térmica. Se a transferência de calor, estresse térmico e vida útil da campanha do forno, todos esses parâmetros não forem analisados, isso pode levar à falha do BF.
O resfriamento eficiente é necessário para equilibrar a carga térmica e o desgaste associado do revestimento interno do forno e para proteger o invólucro e seus elementos de resfriamento. Os sistemas de refrigeração de um BF desempenham um papel fundamental na vida útil de um BF e, portanto, nos custos operacionais. Elementos de resfriamento com água circulando neles são instalados entre a carcaça do BF e o revestimento refratário na parte superior do forno para proteger esses componentes da radiação de calor.
Fritz W Lurman, um conhecido homem do BF da época, opinou em 1892 que “independentemente do uso dos chamados materiais refratários, o melhor meio de manter as paredes do BF é com água de resfriamento”. A função do sistema de resfriamento BF é resfriar a carcaça do forno e evitar o superaquecimento e a queima subsequente. O sistema de resfriamento remove o excesso de calor gerado no BF que de outra forma é carregado no casco. O sistema de resfriamento, portanto, evita o aumento da temperatura do casco e do revestimento. Existem vários métodos que existem para o resfriamento do invólucro do BF.
Os sistemas de resfriamento BF estão sendo desenvolvidos desde 1884. Anteriormente (até 1920) o resfriamento era aplicado apenas às áreas de lareira e bosh. Nas décadas de 1930 e 1940, o resfriamento também foi aplicado ao eixo. Simultaneamente, foram tentados métodos de resfriamento externo, como resfriamento por chuveiro e jaqueta da carcaça do forno. Este método consistia em extrair o calor através da carcaça do forno para o meio de resfriamento, gerando altas tensões térmicas durante a transferência de calor e, portanto, comprometendo a integridade da carcaça.
No passado, além de ter seus próprios resfriadores, a parte do casco adjacente à fornalha e ao fundo do forno também era resfriada em alguns fornos na parte externa por jatos de água. Além disso, em épocas anteriores, caixas de resfriamento de diferentes tamanhos, número e design foram usadas para transferir o calor do forno para um meio de resfriamento em conjunto com o resfriamento externo (resfriamento por pulverização, revestimento duplo).
BFs com aduelas de resfriamento de ferro fundido estão operando desde meados de 1900. Uma aduela é um dispositivo de resfriamento com um ou mais canais internos de água e é instalado em números na superfície interna de um BF para proteger seu invólucro de aço do gás de alta temperatura e do material de carga fundido no forno e manter o perfil no interior a fornalha. As três propriedades que são principalmente necessárias de uma aduela são (i) longa vida útil e confiabilidade, (ii) capacidade de refrigeração adequada e (iii) capacidade de isolamento térmico.
O primeiro é a longa vida e confiabilidade. Uma vez que é impossível reparar uma aduela fora do BF devido à sua estrutura, é necessário um extenso trabalho de substituição quando as aduelas estão danificadas. Aduelas danificadas têm sérios efeitos adversos nas operações de BF, causando uma longa parada de sopro e a queda de temperatura no interior do forno devido ao vazamento de água, ou alterando o perfil que pode resultar em falha operacional. Por esta razão, é necessária uma longa vida estável para as aduelas.
A segunda é a capacidade de resfriamento apropriada. Para proteger o casco do gás de alta temperatura em torno de 1.200 graus C e do material líquido, é necessária uma capacidade de resfriamento adequada das aduelas. Uma vez que uma alta capacidade de resfriamento é necessária para resfriar a parte do forno entre o bosh e a parte inferior do poço que é exposta a alta temperatura, uma aduela de cobre é usada para esta parte em vários casos.
A terceira é a capacidade de isolamento térmico. Um BF no qual o óxido de ferro é reduzido e fundido em alta temperatura é desejado ter uma estrutura de isolamento térmico para não desperdiçar energia térmica. Por outro lado, conforme descrito acima, as aduelas são resfriadas para manter o perfil dentro do BF e proteger o casco. Assim, remove a energia térmica do gás e do material de alta temperatura. A remoção de calor por uma aduela envolve o consumo de combustível equivalente (coque), causando diretamente um aumento na taxa de agente redutor (RAR). Um aumento no RAR pode levar a um aumento nas emissões de dióxido de carbono e elevar a unidade preço do ferro líquido. Por esta razão, as aduelas são necessárias para ter um isolamento térmico adequado (restrição de remoção de calor), ou seja, capacidade de minimizar a energia térmica retirada do interior do forno, bem como capacidade de refrigeração adequada. Convencionalmente, tijolos com baixa condutividade térmica são embutidos na frente de uma aduela de ferro fundido para obter capacidade de resfriamento e capacidade de isolamento térmico. Enquanto isso, uma aduela de cobre é usada para formar uma camada de isolamento térmico a partir de material semilíquido localizado na frente das aduelas, resfriando esse material com alta capacidade de resfriamento para fazê-lo aderir à superfície interna das aduelas.
Os refrigeradores de aduelas começaram a ser desenvolvidos em meados de 1900. O resfriamento de aduelas de ferro fundido foi originalmente uma descoberta da antiga União Soviética, de onde viajou inicialmente para a Índia e o Japão. Na década de 1970, as aduelas de resfriamento de ferro fundido alcançaram aceitação mundial. Desde a introdução dos resfriadores de aço fundido, o trabalho de desenvolvimento do resfriamento BF foi acelerado e hoje uma grande variedade de resfriadores, como resfriador de placas, resfriador de charutos, etc., estão disponíveis para o resfriamento interno do invólucro do forno para atender a condições extremas de estresse em um grande BF moderno de alto desempenho. A vantagem do resfriamento de aduelas sobre o resfriamento de placas planas é o efeito de resfriamento das aduelas em comparação com o efeito de resfriamento ponto a ponto de placas planas e resfriadores de charutos. Isso garante um desempenho de resfriamento mais uniforme.
Para a maioria dos BFs de grande capacidade que operam hoje, os engenheiros de projeto optaram pelo uso de aduelas para o sistema de resfriamento, pois permitem um resfriamento intensivo e, acima de tudo, uniforme do forno. Classicamente, as aduelas são feitas de ferro fundido nodular, que é fundido ao redor dos tubos de água de resfriamento. Eles são instalados em todo o revestimento do forno, desde a placa inferior até a garganta. Frequentemente, no entanto, as aduelas são submetidas a fortes tensões causadas por altas cargas de calor, particularmente nas áreas de bosh e ventre, o que pode limitar a duração da campanha do forno. Isso pode levar à perda de todo o corpo da aduela, restando apenas os tubos condutores de água. Acredita-se que tanto a condutividade térmica do material de ferro fundido quanto a transferência de calor entre a tubulação e o corpo fundido podem ser o problema. Mesmo com os sistemas de refrigeração mais conhecidos, a área inferior do casco permaneceu o ponto fraco do BF.
As aduelas eram fabricadas convencionalmente em ferro fundido, mas a viabilidade de sua fabricação em cobre, que possui excelente condutividade térmica, foi confirmada na Alemanha por volta de meados da década de 1990 e, portanto, as aduelas de cobre passaram a ser utilizadas em vários BFs desde então. Em 1993, as aduelas de cobre foram introduzidas pela primeira vez na Alemanha no BF número 2 da Thyssen Krupp em Schwelgern e no BF 'B' em Salzgitter. A produção de aduelas de cobre, usando passagens de água perfuradas no lugar de tubos, ou fornecendo canais adequados ao fundir as placas de cobre, provou ser um passo significativo no projeto dos BFs modernos.
A teoria de que a alta condutividade térmica do cobre leva a uma maior dissipação do calor do processo foi refutada. A alta condutividade do cobre resulta em baixas temperaturas de superfície e uma rápida formação de uma camada fina que reduz a remoção de calor do forno. O efeito de resfriamento é tão intenso que uma camada protetora se forma em poucos minutos, mesmo na frente de uma aduela desprotegida. Resultados recentes mostraram que o nível de calor removido do forno é ainda menor do que o experimentado com aduelas de ferro fundido.
O efeito isolante de tais camadas mantém as perdas de calor no mínimo. Por esta razão, quando o BF número 2 Stahlwerke Bremen foi reembasado, nenhum material refratário permanente foi instalado na frente das aduelas acima das ventaneiras. Em vez disso, apenas uma fina camada de proteção soprada foi colocada. Essas aduelas provaram ser tão bem sucedidas que hoje o uso de aduelas de cobre na área de alta carga térmica é a tecnologia de ponta dos altos-fornos. A pilha inferior não é mais considerada um fator limitante para a vida da campanha do BF. Em vez disso, o status da lareira dita a vida da campanha do BF. Os resfriadores de aduela de cobre atuais isolam o invólucro externo do calor do processo gerado em fornos altamente estressados. No entanto, dependendo de onde eles estão posicionados dentro do BF, eles estão sujeitos a diferentes níveis de carga térmica.
A chave para a operação bem-sucedida de um sistema de resfriamento em BFs de alta carga térmica é a formação de um crânio na face quente do elemento de resfriamento. Este crânio é composto de vapores condensados, escória solidificada e metal que prende a superfície do elemento de resfriamento por respingos, gotejamento e congelamento. A espessura pode variar em até 20 mm. A estabilidade do crânio depende principalmente da capacidade de resfriamento e capacidade de aderência mecânica do elemento de resfriamento ao qual ele adere. A gravidade do fluxo de gás na parede também afeta a retenção do crânio. O crânio é um isolante natural se o conteúdo metálico for baixo. Durante períodos de extrema carga de calor (ou seja, jatos de gás de alta temperatura ou problemas no processo), o crânio pode se desprender e depois se acumular novamente. A queda e a formação de crânios causam flutuações significativas nas cargas de calor na parede do forno com picos de carga na faixa de 300.000 watts por metro quadrado (W/m²) a 500.000 W/m².
Portanto, o projeto de revestimento e resfriamento normalmente deve ser capaz de lidar com tais cargas de calor para evitar falhas prematuras. Investigações detalhadas revelaram que quanto maior a eficiência de resfriamento do elemento de resfriamento, mais estável o crânio e mais tempo ele adere ao elemento de resfriamento e mantém suas propriedades isolantes e protetoras. O resultado é que sistemas de resfriamento altamente eficientes normalmente resultam em menores perdas globais de calor do forno.
Enquanto a maioria dos BFs são do tipo independente sem suportes na carcaça do forno, alguns projetos de fornos incorporam uma manta onde o forno é suportado do nível do solo pelas colunas de aço ou concreto. O uso de um manto normalmente elimina a área da barriga. O manto é parte integrante do projeto do forno desses fornos e deve ser protegido contra superaquecimento nas mesmas condições experimentadas na área da barriga dos BFs independentes. O resfriamento do revestimento do forno na área da manta usando placas de cobre é difícil devido ao acesso limitado para troca e ao comprimento dos resfriadores de placas que devem ser usados. O uso de aduelas na área tem a vantagem de dar uma cobertura completa de resfriamento do manto. A Fig 1 mostra o arranjo de resfriamento da aduela na manta, bem como os diferentes tipos de arranjos de resfriamento nos BFs.
Fig 1 Diferentes tipos de arranjos de resfriamento no alto-forno
BFs modernos podem ter taxas de produção superiores a 3 toneladas de metal quente por metro cúbico de volume de trabalho por dia. Este nível de produtividade no BF é alcançado usando materiais de carga aprimorados, técnicas de distribuição de carga, controle de processo, altas temperaturas de jateamento quente, enriquecimento de oxigênio e injeção auxiliar de combustível. No entanto, essas práticas de alta produtividade resultam em altas cargas de calor e flutuações de carga de calor para atuar nas paredes do BF. Embora a zona específica e a magnitude das cargas de pico de calor possam variar consideravelmente entre os fornos, a barriga e a região inferior da chaminé normalmente encontram as maiores flutuações de calor, como mostrado na Figura 2.
Fig 2 Flutuações de carga de calor em várias regiões do alto-forno
A área na qual a carga de calor mais alta é experimentada está intimamente relacionada à posição e forma da zona coesiva e ao padrão de carga específico do forno. A principal causa de altas flutuações de calor são jatos de gás de alta velocidade irregulares que são ventilados em direção às paredes do forno através de fendas de coque na carga. Temperaturas altas e flutuantes são as principais cargas com as quais os elementos de resfriamento nos BFs precisam lidar. Observou-se que a composição e a qualidade da carga afetam consideravelmente as cargas de calor e as flutuações de calor. A carga de BF com mais de 70% de sinter pode resultar em cargas de pico de 100.000 W/m² a 200.000 W/m², enquanto cargas com uma alta porcentagem de pellets ou aglomerados podem gerar cargas de calor de pico de mais de 400.000 W/m². Dependendo da carga de calor esperada, diferentes elementos de resfriamento devem ser aplicados. A guia 1 fornece uma visão geral de diferentes projetos de resfriamento e refratários com seus recursos máximos de carga de calor de pico.
Guia 1 Visão geral de diferentes projetos de resfriamento e refratários com seus recursos máximos de carga de calor de pico | |
Design | Pico de carga de calor em W/m² |
Resfriadores de placas com refratários de alumina | 50.000 |
Aduelas de ferro fundido, primeira geração | 100.000 |
Aduelas de ferro fundido mais espessas com vários circuitos de água de resfriamento | 200.000 |
Resfriador de placas, espaçamento menor (300 mm) com refratários especiais | 400.000 |
Aduelas de cobre de alto desempenho | 500.000 |
É necessário enfatizar aqui que essa carga térmica de pico é o principal fator determinante para a sobrevivência a longo prazo do revestimento do forno ou dos elementos de resfriamento.
Os vários elementos de resfriamento desenvolvidos para o sistema de resfriamento BF são (i) aduelas de ferro fundido de diferentes gerações, (ii) resfriador de placas de cobre densamente espaçado, (iii) resfriador de charutos e (iv) aduelas de resfriamento de cobre. Esses elementos de resfriamento são descritos abaixo .
Refrigeradores de ferro fundido
Para os resfriadores de aduelas de ferro fundido, inicialmente foi usado ferro cinzento lamelar perlítico ligado, mas atualmente foi substituído por ferro dúctil ou ferro nodular, pois é menos sujeito a rachaduras em temperaturas superiores a 760 graus C. Aduelas de aço fundidas recentemente no local de aduelas de ferro fundido também foram testadas com sucesso. O efeito de resfriamento das aduelas de ferro fundido é determinado pelo tamanho e forma dos tubos de água de resfriamento dentro do resfriador de aduelas. As dimensões típicas das aduelas de ferro fundido consistem em 1,8 m a 2,4 m de comprimento, 0,8 m a 1,1 m de largura e 0,25 m a 0,6 m de espessura. Diferentes tipos de aduelas de resfriamento de ferro fundido são mostrados na Fig 3. Os resfriadores do tipo C são muito mais finos e são projetados para economizar espaço dentro do forno para aumentar seu volume de trabalho.
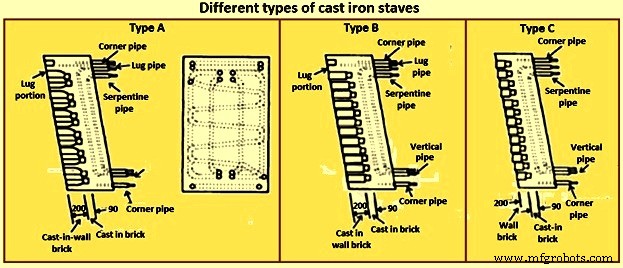
Fig 3 Diferentes tipos de aduelas de ferro fundido
Desde a aquisição da tecnologia de aduelas de ferro fundido da antiga União Soviética em 1969, os japoneses fizeram várias melhorias para aumentar a durabilidade das aduelas. Isso inclui o estreitamento do espaçamento dos tubos e a instalação de tubos de resfriamento de canto e tubos serpentina traseiros. As aduelas de quarta geração são caracterizadas pelo fato de possuírem dois planos de resfriamento, quatro tubos verticais no plano lateral quente e um tubo serpentino no plano lateral frio. As aduelas são equipadas com pontas refrigeradas e/ou suporte para suporte de materiais refratários. Além disso, os cantos das aduelas são intensamente resfriados. Os materiais refratários são vazados em furos de suporte especiais nas aduelas. As melhorias realizadas da primeira geração para a quarta geração de resfriadores de aduela de ferro fundido são mostradas na Fig 4.
Fig 4 Melhorias nos resfriadores de aço fundido
As aduelas de ferro fundido nas áreas de bosh e stack do BF têm uma expectativa de vida média de cerca de 8 anos a 10 anos. As aduelas de ferro fundido geralmente falham devido à perda de material de ferro fundido e exposição da bobina interna do tubo. O ferro fundido racha em serviço devido às altas cargas de calor a que está exposto. Espaços aleatórios entre os tubos de resfriamento e o ferro fundido reduzem a quantidade de calor que é removida. Também a diferença entre os coeficientes de expansão térmica dos materiais do tubo e do próprio resfriador pode fazer com que o ferro se separe do tubo e destrua o resfriador. O uso de resfriadores de ferro fundido, nos quais os tubos estão mais próximos do ferro fundido, complica o projeto do casco, mas não necessariamente aumenta a vida útil do sistema de resfriamento.
O mecanismo de falha das aduelas de ferro fundido sob altas cargas de calor flutuantes é devido à baixa condutividade térmica (cerca de 45 W/m.K) do ferro fundido. As aduelas de ferro fundido têm uma eficiência de resfriamento menor em comparação com as aduelas de cobre devido à condutividade relativamente baixa do ferro fundido e à presença de uma camada isolante. Esta camada resulta em uma barreira térmica entre o tubo resfriado a água e o corpo da aduela de ferro fundido reduzindo a transferência de calor. A transferência de calor ineficiente resulta em uma temperatura da face quente consideravelmente mais alta da aduela de ferro fundido (acima de 700 graus C) e subsequente deformação térmica da aduela de ferro fundido. O corpo de ferro fundido também sofre transformação de volume de fase em temperaturas elevadas, resultando em trincas por fadiga, perda de material do corpo de aduela e exposição dos tubos de resfriamento de aço diretamente ao calor do forno.
Resfriadores de placa plana de cobre
Os resfriadores de placas planas de cobre, como o nome descreve, são placas planas dispostas horizontalmente na carcaça do forno. Esses resfriadores de placa plana foram usados em quase todos os BFs europeus. Esses resfriadores são soldados ou fundidos em cobre eletrolítico. Com este último, não há problemas nas costuras de solda e há uma maior uniformidade das propriedades do material sobre o elemento de resfriamento completo. Este tipo de refrigerador é normalmente usado na área do bosh até e incluindo a pilha inferior. Ele é normalmente projetado para manter altas velocidades da água em todo o resfriador, proporcionando assim um coeficiente de transferência de calor uniforme e alto. Os resfriadores de placa plana de cobre típicos são mostrados na Fig 5.
Fig. 5 Refrigerador de placa plana de cobre
Os tamanhos normais de placas dos resfriadores de placas planas de cobre consistem em 0,5 m a 1,0 m de comprimento, 0,4 m a 0,8 m de largura e uma altura de cerca de 75 mm. O espaçamento vertical dos resfriadores é de 0,3 m a 0,6 m. Nas zonas com altas cargas de calor, especialmente nas áreas bosh e low stack, o espaçamento é frequentemente reduzido para 0,25 m. Os resfriadores planos de cobre têm uma maior uniformidade das propriedades do material em relação ao elemento de resfriamento completo. Nas regiões do BF que estão sujeitas a danos mecânicos, a parte frontal dos elementos de refrigeração é normalmente reforçada com materiais especiais. Esses resfriadores são soldados principalmente ao invólucro BF para garantir vedação à prova de gás. Os resfriadores de placas planas de cobre normalmente possuem múltiplos canais com uma ou duas câmaras independentes. As perdas mínimas de pressão da água são garantidas tanto na tubulação quanto no próprio elemento.
Um dos designs do resfriador de placa plana com tampadora tem seis passagens com câmara única. Esses resfriadores são projetados para manter altas velocidades da água em todo o resfriador, portanto, têm um coeficiente de transferência de calor uniforme e alto.
A falha dos resfriadores planos de cobre é atribuída a quatro mecanismos de falha. Eles são (i) deflexão, (ii) falhas na solda do tubo, (iii) falhas na solda do plugue e (iv) abrasão da face. Uma comparação do resfriador de placas de cobre com o resfriador de aduelas de ferro fundido é fornecida na Tab 2.
Guia 2 Comparação entre sistemas de refrigeração | |||||
Descrição | Unidade | Resfriador de placas de cobre | Refrigerador de aço fundido | ||
Média | Máximo | Média | Máximo | ||
Área de superfície específica do elemento de resfriamento por concha de metro quadrado | m² / m² | 1-2 | 2,5 | 0,8-1 | 1-2 |
Fluxo específico de água de resfriamento por metro quadrado (m²) de concha | cum / h | 5-10 | 3-5 | ||
Velocidade típica da água de resfriamento | m / seg | 0,5-1 | 2-2,5 | 1-1,2 | 2,5-3 |
Refrigeradores de charutos
Os resfriadores de charutos são usados para resfriamento mais intenso ou com espaçamento insuficiente existente do resfriador de placa plana. Estes também são conhecidos como jaquetas de cobre. Os resfriadores de charutos são usados nas áreas abertas entre os resfriadores de placas quando é necessário um resfriamento mais intenso ou há espaçamento insuficiente entre os resfriadores de placas planas. Eles também são usados às vezes para melhorias no sistema de resfriamento existente durante uma campanha. O resfriador de charutos é normalmente usinado a partir de uma barra de cobre sólida para formar um núcleo cilíndrico e um único canal é adicionado por perfuração e conexão.
Os resfriadores de charutos são normalmente inseridos nas linhas centrais entre os resfriadores de placa plana adjacentes em um plano horizontal e vertical. Para fins de instalação de um resfriador de charutos, normalmente um orifício cilíndrico é perfurado através do revestimento do forno e do revestimento refratário existente com uma broca de núcleo. O uso de resfriadores de charutos nas áreas bosh, ventre e pilha inferior aumenta a área do sistema de resfriamento. Como essa área do BF apresenta as maiores oscilações de temperatura e temperatura, o uso de resfriador de charutos pode aumentar a resistência do revestimento refratário a mecanismos de ataque químico e mecânico. No entanto, como o uso de resfriadores de charutos resulta em aumento de aberturas no forno, é necessário que a resistência do casco seja verificada antes de seu uso. Um resfriador de charutos típico e seu posicionamento entre os resfriadores de placas, visto do lado de fora da carcaça do BF, são mostrados na Fig 4.
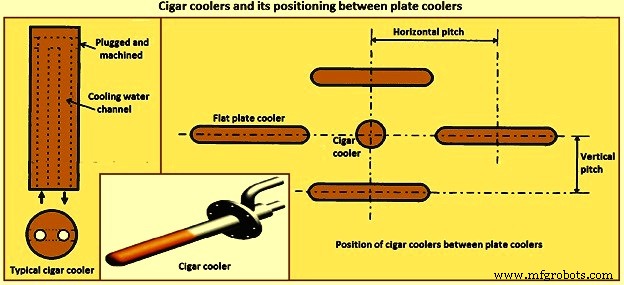
Fig 6 Refrigerador de charutos e seu posicionamento entre os refrigeradores de placas
Aduela de cobre
Considerando o grande investimento de capital necessário para o reembasamento dos BFs, grandes esforços foram feitos para estender a vida útil dos BFs. A tecnologia de aduelas de cobre é um dos produtos de tais esforços.
A aduela de ferro fundido, devido às suas características materiais, provoca a deterioração do material na parte inferior do alto-forno, que fica exposta a alta carga térmica. Isso dificultou a obtenção de uma vida útil estável do forno de 20 anos usando a aduela de ferro fundido. Como meio de resfriamento alternativo à aduela de ferro fundido considerando a alta carga térmica, foi desenvolvida a aduela de cobre laminada. Este tipo de aduela é feito de uma chapa de cobre laminada na qual são feitos furos e tubos de abastecimento de água e drenagem são soldados para formar canais de água. A utilização de aduelas de cobre laminadas teve início na Alemanha em meados da década de 1990, e se espalhou para os BFs em diversos países.
Outras aduelas de cobre desenvolvidas até o momento incluem aduelas de cobre fundido com canais de água formados usando um núcleo no processo de fundição e aduelas de cobre de tubo de monel fundido com canais de água formados usando tubos de monel dobrados em forma de canal e fundidos.
As aduelas de cobre foram utilizadas pela primeira vez em BFs no final da década de 1970 como o melhor elemento de resfriamento de parede de alta carga térmica. À medida que a produtividade do BF se intensificou e as metas de vida de campanha desejadas aumentaram para 20 anos, tornou-se evidente que as aduelas de cobre tinham o melhor potencial para atender ou superar essas demandas. Embora o uso de aduelas de cobre tenha se tornado predominante em meados da década de 1990, a maioria das instalações ocorre a partir do ano 2000. O desenvolvimento de aduelas de cobre foi realizado tanto no Japão quanto na Alemanha para uso na região de bosh, ventre e baixo pilha para lidar com altas cargas de calor e grandes flutuações de temperatura. Enquanto o Japão optou por aduelas de cobre fundido, as aduelas de cobre alemãs são placas de cobre laminadas com tolerâncias externas próximas e com perfuração feita para passagens de resfriamento. As aduelas de cobre perfuradas e conectadas são normalmente projetadas para quatro tubos de água em linha reta na parte superior e quatro tubos de água em linha reta na parte inferior. Os materiais para bobinas de tubos internos incluem monel, cobre ou aço. Ao contrário das aduelas de ferro fundido, as aduelas de cobre destinam-se a ser coladas ao tubo de resfriamento.
O canal de água de uma aduela de cobre era formado principalmente pela perfuração de um furo em uma placa de cobre laminada e soldagem de tubos de água nas extremidades do furo, e às vezes era formado por fundição usando um núcleo de areia descartável, no entanto, o trabalho de soldagem de cobre era indispensável em nenhum dos casos. Enquanto as aduelas de cobre convencionais se mostraram excelentes na capacidade de resfriamento, sua fabricação exigia várias etapas de trabalho e, portanto, eram caras.
Atualmente, o tipo mais popular de aduela de cobre é a aduela de cobre laminada, cujo processo de fabricação envolve a perfuração de uma placa de cobre. As extremidades do canal de água desta aduela são soldadas. A aduela de cobre de tubo de aço fundido, que foi desenvolvida, é feita pela fundição de tubos de aço dobrados no cobre, um processo de fabricação completamente diferente daquele da aduela de cobre laminada convencional. Este método de fabricação exclusivo permitiu alcançar alta eficiência energética e longa vida útil dos BFs, o que não pode ser alcançado com a aduela de cobre laminada.
As aduelas de cobre laminadas às vezes apresentam três problemas:(i) deformação, (ii) rachaduras na solda devido à fadiga térmica e (iii) desgaste. O primeiro problema é a deformação. As aduelas de cobre laminadas são deformadas devido à diferença na expansão térmica entre a superfície interna da aduela, que é exposta ao gás de alta temperatura, e a superfície externa da aduela que é resfriada. Eles são seriamente deformados quando uma aduela é muito longa ou quando as posições dos parafusos de fixação não são adequadas. Tal deformação pode causar desgaste de uma porção saliente e quebra de uma solda devido ao fluxo de gás de alta temperatura para as juntas de aduela e superfícies traseiras. O segundo problema é a fissuração da solda. Devido à fadiga térmica, isso ocorre porque as soldas das aduelas de cobre laminadas são submetidas a tensões térmicas repetidas. Devido à flutuação de temperatura, as aduelas de cobre laminadas resultam em rachaduras e quebras. O terceiro problema é o desgaste. O minério de ferro, o sinter e o coque têm dureza superior à do cobre. Esses materiais desgastam as aduelas de cobre quando entram em contato com a superfície da aduela e descem. Em geral, a taxa de desgaste de uma aduela de cobre depende da força de contato e da velocidade de descida do material em contato com a superfície da aduela, da dureza do cobre e do material e da forma do material.
O desenvolvimento da aduela de cobre fundido considerou os seguintes aspectos. De acordo com o primeiro aspecto, para a prevenção de deformações, é importante o dimensionamento adequado do comprimento da aduela e dos pontos de restrição do parafuso. O primeiro aspecto é que o uso da aduela de cobre de tubo de aço fundido com design próprio é benéfico para reduzir efetivamente o risco de deformação. A Fig. 7 mostra os pontos restritos de uma aduela de cobre laminada e a aduela de cobre de tubo de aço fundido. Uma aduela de cobre laminada é presa ao casco por parafusos e pinos de montagem. Para evitar que a solda na base de um tubo ascendente seja danificada por tensões, a tubulação ascendente é conectada ao casco por uma junta de expansão. Devido a esta estrutura, as extremidades superior e inferior da aduela são deslocadas livremente, fazendo com que a aduela seja facilmente deformada. A grande carga térmica que é aplicada repetidamente à aduela de cobre no curso da flutuação nas operações de BF, etc., faz com que a tensão plástica seja gradualmente acumulada e resulta em grande deformação. Há casos em que a deformação na extremidade superior atingiu 50 mm ou mais e uma solda foi quebrada, sob a condição de uma aduela excessivamente longa, uma posição inadequada do parafuso ou alta carga térmica excedendo a condição de projeto.
Fig 7 Pontos restritos de aduela de cobre de tubo laminado e fundido
Alta confiabilidade e baixos custos de fabricação são obtidos no caso da aduela de cobre de tubo de aço fundido por uma tecnologia de fundição para incorporar um tubo de aço em uma fundição de cobre aplicada à produção do novo tipo de aduela de cobre. Esta tecnologia de fundição foi desenvolvida com base na fabricação de aduelas de ferro fundido. O novo tipo de aduela de cobre com tubo de aço embutido tem as vantagens de (i) alta capacidade de refrigeração, pois a fundição de cobre de alta pureza garante uma capacidade de refrigeração tão alta quanto a de uma aduela de cobre convencional, (ii) alta confiabilidade desde o embutimento um tubo de aço em uma fundição de cobre elimina a soldagem de cobre na formação de um canal de água e a possibilidade de vazamento de água, (iii) ampla flexibilidade no projeto, pois a fabricação por fundição e embutimento de um tubo de aço permite uma flexibilidade muito maior na aduela design do que as aduelas de cobre convencionais em termos de formato da aduela e disposição do canal de água, e (iv) baixo custo.
A aduela de cobre de tubo de aço fundido tem as seguintes características de resistência à deformação. Conforme mostrado na Fig. 7, para o tubo de aço fundido a aduela de cobre possui caixas de vedação de gás além de parafusos que são utilizados para fixar os tubos de proteção nas extremidades da aduela. Isso aplica a restrição de deslocamento às extremidades superior e inferior da pauta. Além disso, como o tubo de proteção é fundido no corpo da aduela de cobre, não são utilizadas soldas com risco de ruptura.
Além disso, a aduela de cobre de tubo de aço fundido usa tubos de aço, que são mais rígidos que o cobre e servem como estrutura. A utilização de tubos de aço proporciona uma estrutura mais resistente à deformação do que as aduelas de cobre convencionais. A superfície interna da aduela de cobre do tubo de aço fundido é irregular. Uma vez que as aduelas de cobre laminadas têm uma forma de seção transversal retangular, a temperatura aumenta em locais na superfície interna da aduela longe dos canais de água. Em contraste, a aduela de cobre de tubo de aço fundido usa uma superfície irregular para tornar a distância entre a superfície interna da aduela e cada canal de água virtualmente constante ao redor do canal de água. This allows the stave inner surface to be uniformly cooled. Such uniform cooling in turn reduces the temperature difference between the stave inner and outer surfaces, and suppresses thermal stresses and deformation.
In addition, under large thermal load, compression plastic strain is caused on the stave inner surface of a rolled copper stave by the temperature difference between the stave inner and outer surfaces, which can lead to stave deformation. In contrast, the inner surface of the cast-in steel pipe copper stave is isolated at each bump, thereby making compression stresses less likely to act on the stave and suppressing plastic strain. Hence, the bumpy surface of the cast-in steel pipe copper stave reduces stresses and strains which act on the stave, and suppresses deformation. Also, since the cast-in steel pipe copper stave forms water channels using steel pipes, plug welding or pipe connection welding, which are indispensable for making rolled copper staves, are not necessary. By avoiding the use of welding, which is structurally weak parts, the risk for breakage of welds can be eliminated.
Copper staves prevent wear by the scabs formed by using its high cooling ability, thereby avoiding direct contact with the descending material in front of the stave. However, such accretion frequently falls off due to the fluctuations during furnace operations. Without accretion, the wear of a copper stave depends on the contact force and descending speed of the material in front of the stave, hardness of copper and the material, and shape of the material. Given this, counter-measures against wear feasible for a stave include reducing the contact force and descending speed of the material when there is no accretion, in addition to stably retaining accretion, as well as not allowing the hardness of copper to be reduced. While grooves for rolled copper staves is formed by machining, the cast-in steel pipe copper stave forms ribs by integrally casting, allowing for forming as-desired rib shapes. Based on this feature, cast-in copper stave normally has an upward rib structure with wear resistance. The hardness of copper depends on the cooling ability.
If there is no accretion inside-furnace surface of a rolled copper stave, material once entered between ribs hardly moves because the ribs are small. Hence, material in front of the stave descends without being influenced by the ribs. In contrast, since the ribs of the cast-in steel pipe copper stave face upward and are large, material which has entered between the ribs is discharged back into the furnace, creating a flow (load transfer). At this time, the material is discharged upward. This upward flow pushes the material in front of the stave back to the furnace, causing the contact force and descending speed of the material to be reduced at the rib tips.
In addition to the technical advantages in extending life and saving energy, the cast-in steel pipe copper stave has also the characteristic of the high design flexibility. When a cast iron stave or cooling plate which a BF uses is broken and something needs to be done in order to extend the life, the replacement with a copper stave using the existing shell opening may be needed. In the case of rolled copper staves, since water channels are formed by drilling, the water channel layout is restricted, making it difficult to freely form water channels in a manner tailored to the existing shell opening. In contrast, water channels of the cast-in steel pipe copper stave, which are formed using bent steel pipes, allow for flexible layout adopting steel pipes for the existing opening of the shell. Fig 8 shows high flexibility of cooling channel layout in cast-in steel pipe copper stave.
Fig 8 High flexibility of cooling channel layout
Layouts of cooling systems
Water cooling systems are normally designed to operate in a closed loop rather than the conventional open systems. This allows the pipe work to be chemically cleaned, and by controlling water chemistry throughout the campaign, this clean surface can be maintained, thus ensuring maximum heat transfer. The development of the sealing of the cooling tubes to the shell is towards the use of ever, thinner, ’softer’ metallic expansion joints. For both systems, i.e. flat plate coolers or staves, there is an increasing use of rubber bend and hoses.
Independent series are typical for water distribution in flat coolers. With stave coolers, it is normal to provide a number of independent flow and return headers in accordance with the number of tubes. This ensures that in the case of failure one feed system, the remaining stave tubes receive sufficient cooling. Nose and corner tubes are connected to the additional water circuits.
The rise in the BF productivity has been accompanied by a greater demand for efficient cooling systems. High-performance cooling systems are needed to ensure that the operational process runs smoothly even when under such stress. Reliable and effective cooling system solution is needed in the high loaded zones of the BF. There are three types of cooling circuits which are normally used for the BF cooling systems. These are (i) closed loop cooling circuits, (ii) combined closed loop cooling circuits, and (ii) semi-closed or open loop cooling circuits or evaporation cooling circuit
Closed loop cooling circuits – These cooling system circuits are normally designed with two or three nitrogen pressurized closed loop water circuits with forced recirculation. The advantages of such a system, as compared to an open loop cooling circuit are (i) circuit can be operated with treated, softened water, (ii) no corrosion, fouling, and clogging of pipes and cooling elements, (iii) low cost for chemical additives, (iv) low water consumption, (v) no contact with oxygen of ambient air, (vi) very sensitive leakage detection is possible, (vii) increase of the evaporation temperature of the cooling water due to operation under adjustable nitrogen pressure (e.g. pressure – 8 bar, evaporation temperature – 170 deg C), (ix) low electrical power consumption, since only the pressure drop is to be covered by the pumps and the differential height is not to be considered, (x) easy flow adjustment and control for the different cooling elements, (xi) low maintenance costs, and (xii) longer life time of circuit equipment and cooling elements resulting in high availability of and hence high productivity.
Combined closed loop cooling circuits – These circuits constitute an economic, but still efficient, reliable, and safe solution. The cooling water is used to cool serially different blocks of cooling elements, still respecting the operation requirements of the individual cooling elements. The total flow rate is considerably reduced while temperature difference of the cooling water is still in an acceptable range and the cooling tower operates efficiently.
Semi-closed or open loop cooling circuits or evaporation cooling circuit – These can also be used as an option in accordance with site conditions. This solution is mainly good for minimum cost upgrades at the existing BFs.
Processo de manufatura
- Sistema de automação, medição e controle de processos de alto forno
- Geração e uso de gás de alto-forno
- Uso de Nut Coke em um Alto Forno
- Injeção de carvão pulverizado em um alto-forno
- Irregularidades do alto-forno durante a operação
- Sistemas de carregamento de alto-forno
- Química da Ferragem por Processo de Alto Forno
- Revestimento refratário do alto-forno
- Fatores que afetam a taxa de coque em um alto-forno
- Alto-forno e seu projeto