Monitoramento baseado em condição não funciona se você estiver brincando
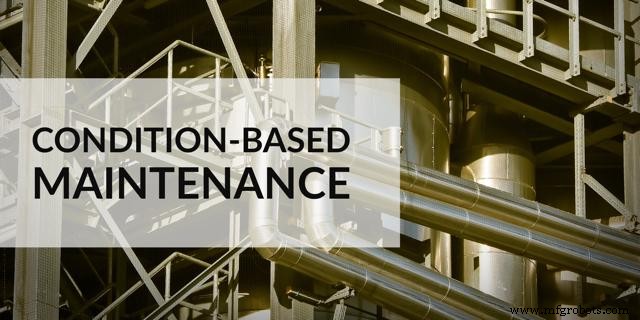
A primeira vez que isso aconteceu foi em 1995. Eu estava no meio de uma apresentação em uma conferência da Associação de Fabricantes de Produtos Químicos quando um cara gritou no fundo da sala:"Que monte de besteira!"
Não surpreendentemente, a sala ficou em silêncio.
O cavalheiro estava reagindo a um slide que mostrava que as melhores empresas da indústria química geram 55% de seu fluxo de trabalho com atividades de monitoramento baseado em condições (CBM).
Então, parei e disse:“Agradeço seu feedback. Você gostaria de compartilhar sua experiência? ”
Ele explicou que estava fazendo análise de vibração, termografia infravermelha, ultrassom, análise de óleo, teste de motor e teste não destrutivo em sua fábrica, mas afirmou que CBM estava gerando apenas 5 por cento do fluxo de trabalho, não 55 por cento. Em sua opinião, eu estava contando algumas histórias fantásticas para essas pessoas.
Depois de pensar por um momento, perguntei quantos trens de máquinas rotativas ele tinha em sua fábrica. Ele disse cerca de 1.000.
“Quantos estão no monitoramento de vibração de rotina?” Eu perguntei. Ele disse 60.
Foi quando me dei conta. “Então, o que estou ouvindo é que você está aplicando as tecnologias a 6% de sua base de ativos e elas estão gerando 5% de seu fluxo de trabalho. Faz sentido que, se você aplicasse as tecnologias a 60 por cento de sua base de ativos, elas pudessem gerar 50 por cento de seu fluxo de trabalho? ”
Ele apenas ficou sentado lá, sem palavras. Era como se ele nunca tivesse pensado nisso dessa forma e tivesse perdido as discussões do modelo de cobertura de referência sobre o que as fábricas de melhores práticas fazem. Mesmo que isso tenha sido há mais de 10 anos, ainda vejo o mesmo erro hoje:as pessoas esperam grandes resultados da CBM apenas brincando com ela.
Outro exemplo comum de dabbling é quando as empresas aplicam apenas uma ou duas tecnologias em suas fábricas.
Vamos voltar ao conceito central por trás do monitoramento de condição.
Praticamente todas as peças do equipamento emitem sinais de alerta precoce (calor, vibração ou som) antes de finalmente falhar. Esses sinais de aviso, também conhecidos como modos de falha, podem ser detectados com certas tecnologias CBM. Mas, aqui está o problema. Equipamentos industriais possuem mais de um modo de falha. Isso significa que muitas vezes você precisa de várias tecnologias CBM para detectá-los.
Considere o exemplo de um chiller, onde você pode aplicar vibração, análise de óleo, análise de refrigerante, teste de motor on-line e off-line e detecção de vazamento ultrassônico e ainda perder os primeiros sinais de uma falha pendente do feixe de tubos. Para isso, você também precisa de testes de correntes parasitas. Na verdade, dependendo do material de construção e do que ele está bombeando, você pode literalmente aplicar uma dúzia de tecnologias a um resfriador.
Portanto, a base de um programa CBM de sucesso é simples:determine todos os modos de falha prováveis para seu equipamento e aplique cada uma das tecnologias que irão detectá-los.
Por que as empresas esperam resultados mágicos de se intrometer no CBM? Porque fazer mais do que isso significa que eles teriam que se comprometer. Isso significa risco. Eles preferem experimentar primeiro e depois expandir o programa se virem o retorno do investimento.
O problema de brincar é que simplesmente não funciona. Você não será capaz de detectar a maioria dos problemas que ocorrem, então o equipamento funcionará até a falha de qualquer maneira. Como resultado, todos ficam frustrados com o programa. Eventualmente, a conclusão é "CBM não funciona aqui."
O resultado final é que há pouco ou nenhum retorno em usar uma ou duas tecnologias - ou aplicar CBM a uma pequena quantidade de seus ativos - e esperar que evolua para um programa de sucesso. Claro, ao aplicar qualquer tecnologia a um conjunto específico de equipamentos, você pode fazer cálculos de redução de custos do tipo "sentir-se bem", mas não afetará sua lucratividade final com essa abordagem.
O retorno ocorre quando você integra toda a gama de tecnologias em uma alta porcentagem de sua base de ativos. Essa é a única abordagem que permite que você planeje e agende a maior parte do seu trabalho, coloque os artesãos lá fora com as habilidades certas, obtenha as peças certas no momento certo, faça reparos de precisão e minimize o impacto na eficácia geral do seu equipamento (OEE).
Se você for na direção oposta, sempre terá um programa evolutivo. E esses tipos de programas nunca fornecem resultados de melhores práticas. Os resultados das melhores práticas devem ser projetados.
John Schultz recebeu a designação de Certified Maintenance and Reliability Professional da Society for Maintenance &Reliability Professionals e é um parceiro da Allied Reliability. Schultz e Allied Reliability são líderes reconhecidos na aplicação de manutenção baseada em condições para alcançar o modelo de manutenção proativa. Leia mais de seus artigos online em www.alliedreliability.com. Para obter mais informações sobre este tópico, envie um e-mail para [email protected] ou ligue para 918-382-9400.
Manutenção e reparo de equipamentos
- As tecnologias de sensores avançados permitem o monitoramento personalizado da qualidade do ar
- Priorizando ordens de serviço de manutenção
- Manutenção envolvida do operador - funciona?
- Práticas padrão x práticas corretas
- Posso interromper o cronograma de manutenção?
- Confiabilidade orientada para a família
- Certifique-se de que o trabalho de manutenção não crie gargalos no processo
- O Supervisor de Manutenção Enigma
- Planejamento de manutenção
- Saúde da máquina e monitoramento de ativos em aplicações industriais:uma visão das tecnologias de sensores