Inspeção de solda para conjuntos críticos de segurança
As apostas são altas para os fabricantes de peças automotivas. Motoristas e passageiros de automóveis confiam na qualidade da solda para resistir às condições para as quais foi projetada. Um erro não descoberto durante o processo de fabricação pode deixar um negócio vulnerável ou pior, especialmente quando a peça em questão é “segurança crítica” para uma montagem.
Assentos automotivos, por exemplo, ficam em contato direto com os passageiros; portanto, as soldas do assento são consideradas críticas para a segurança. Esta classificação determina um protocolo específico antes da produção. Embora os requisitos do OEM variem, eles tendem a ser consistentes com as práticas da indústria e são implementados com pequenas diferenças, dependendo da peça, planta e equipamento industrial que está sendo usado. Aqui estão os elementos básicos de um protocolo:
Protocolo de pré-produção
- Definição de parâmetros - Estabelecer parâmetros de soldadura e verificar a sua aceitabilidade. Isso pode ser feito cortando e gravando seções de solda para verificar a penetração da solda (15-20%).
- Processo de Liberação - Um processo definido para liberar ou aprovar a produção assim que o acima for verificado.
- Gerenciamento de mudanças - Mudanças de variáveis essenciais além de certos limites requerem revalidação por meio de testes de corte e corrosão.
- Garantia de qualidade - Peças aleatórias podem ser selecionadas da produção para corte e corrosão em uma frequência ditada pelo OEM.
A soldagem robótica ajudou a melhorar imensamente a qualidade da peça sempre colocando soldas no mesmo local com parâmetros de solda programados. A adesão aos procedimentos acima ajuda a produzir um produto soldado de qualidade. Os OEMs automotivos têm se concentrado em soldas críticas de segurança e isso resultou na revisão de alguns elementos-chave:
Protocolo de produção
- Segurança - Verifique se pessoal qualificado tem acesso ao equipamento e se não estão sendo feitas alterações que afetem negativamente a qualidade.
- Monitoramento de arco - A implementação de um sistema de monitoramento de arco pode ajudar a verificar se o processo está sob controle e pode permitir que a frequência de testes destrutivos seja reduzida. O monitoramento do arco verifica se os parâmetros de soldagem atendem aos limites estabelecidos. Soldas fora dos limites são marcadas para inspeção adicional.
- Rastreabilidade - Rastreie alterações e resultados de soldagem e mantenha a capacidade de registrar a data, hora e número de série em que ocorreram alterações de peças.
Na Yaskawa Motoman, dedicamos tempo para aprender sobre os requisitos de fabricação e rastreabilidade de nossos clientes. Ao longo dos anos, desenvolvemos vários aprimoramentos de software e E/S para nossos controladores que permitem aos fabricantes realizar inspeções de solda confiáveis e rastreáveis.
Funções de segurança
Função de senha
O sistema de segurança padrão de uma senha global de vários níveis é conveniente para vários técnicos manterem várias células robóticas em uma planta. No entanto, as senhas globais correm o risco de serem compartilhadas entre os funcionários da fábrica, sem controle sobre o que está sendo alterado e por quem.
A função de senha do controlador DX da Yaskawa cria um banco de dados de usuários com senhas e autorizações de nível de segurança. Os usuários devem fazer login para operar o robô; a função de registro registrará o nome do usuário e as alterações feitas.
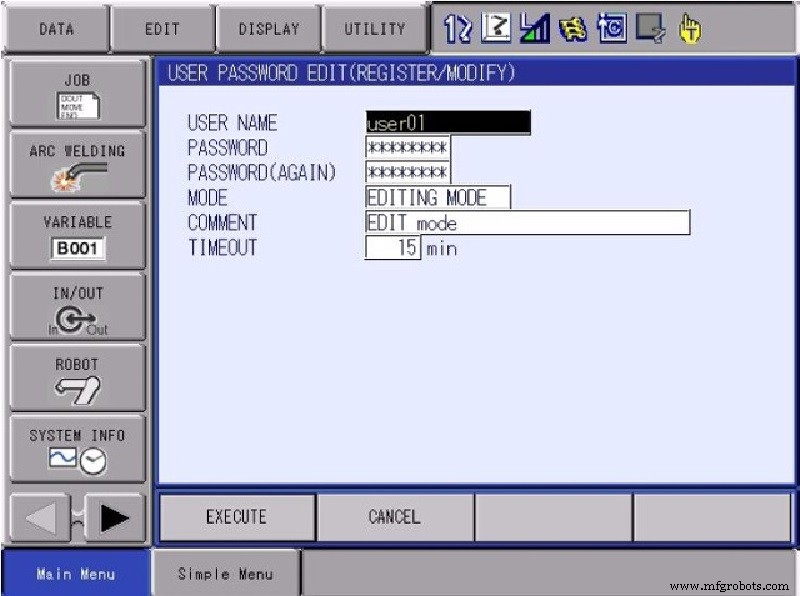
O software foi adicionado ao controlador DX200 para permitir o controle remoto de senha por PLC. Os engenheiros de controle podem implementar lógica para usar controles baseados em fábrica/célula para administrar remotamente usuários e logins com base em seus crachás internos de funcionários ou sistema de segurança.
Níveis de segurança
- Nível de operação - Por padrão, este nível básico permite que qualquer pessoa mova ou percorra um programa, mas não altere pontos ou configurações de solda.
- Editar nível - Permite ao usuário fazer programas e alterar configurações de solda, mas não permite acesso a parâmetros ou dados de nível superior.
- Modo de gerenciamento - Fornece acesso total aos parâmetros e funções de manutenção.
- Nível de segurança - Permite o acesso para configurar e administrar os limites de software confiáveis de controle e a lógica de segurança implementada nos controladores DX (Functional Safety Unit – FSU).
O que esses níveis permitem que os usuários façam e acessem é definido pelo sistema. O nível ao qual o gerenciamento controla o acesso varia de acordo com a localização da planta.
Função de registro
Muitos controladores de robôs mais novos vêm com uma função de registro padrão que acompanha as alterações feitas no sistema por data e hora. Por exemplo, um operador do turno diurno pode ver se alguém do turno da noite fez uma alteração. O robô mantém um arquivo local da última série de alterações, portanto, uma rotina de salvamento de dados pode manter um registro histórico da atividade do usuário. O robô também pode usar o Password Security, exigindo que os usuários façam login para fazer alterações. Os nomes de usuário também são anotados quando as alterações são feitas.
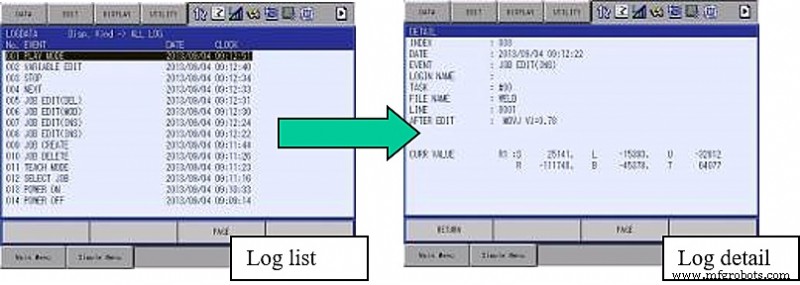
Função de edição de reensinamento de segurança
O nível de operação não permite que os usuários alterem os pontos do programa, mas algumas empresas permitem que os operadores ou técnicos de primeiro nível façam pequenas alterações para variação da peça. O Safety Re-Teach permite que os usuários do nível de operação modifiquem os pontos programados dentro de uma faixa 3D definida pelo modo de gerenciamento. Isso normalmente é definido em alguns milímetros, e um gerente pode limitar a quantidade de mudança de ângulo para a tocha ou eixo externo. Os usuários do nível de operação não podem alterar os parâmetros de soldagem, portanto, as variáveis de soldagem essenciais não são alteradas. Isso evita testes destrutivos repetitivos. Safety Re-Teach pode ser ativado por parâmetro no modo de gerenciamento em qualquer controlador DX.
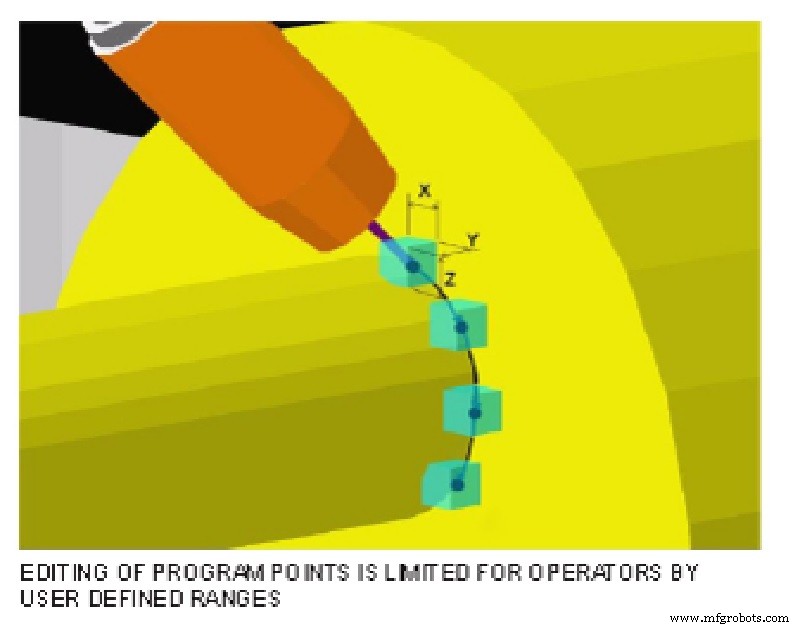
Monitoramento de arco
Como um fornecedor de robôs que integra sistemas de soldagem e constrói uma história de joint venture com uma empresa de soldagem, Yaskawa Motoman tem uma experiência abrangente com monitoramento de arco. Projetamos nossas interfaces de soldagem para suportar a capacidade de monitoramento de arco que os fabricantes de fontes de energia podem ter integrado.
Os recursos integrados do Miller Insight Centerpoint™ e do Lincoln Electric Production Monitoring™ podem ser acessados no pingente de instrução do robô. O WeldCube, da Fronius, se comunica diretamente com a(s) fonte(s) de energia. Yaskawa e Fronius estão trabalhando para que o resultado do monitor seja informado nos bits de status do soldador.

O desafio de cumprir os mandatos de "segurança crítica" também envolve a apresentação clara dos resultados de solda do monitoramento do arco da fonte de energia em um formato útil. O melhor formato é destacar os resultados do monitor em um diagrama de peça em uma IHM de célula de robô. Dessa forma, os operadores da estação de solda podem detectar facilmente as irregularidades e reagir rapidamente. Os operadores precisam inspecionar visualmente as soldas sinalizadas pelo sistema, com resultados do monitor fora da faixa, para julgar se as soldas estão em conformidade ou não.
Embora o controlador do robô possa relatar o status do monitor de arco localmente em uma HMI, os fabricantes de fontes de alimentação também oferecem software projetado para relatar os resultados do monitor de arco remotamente, por meio de um computador pessoal ou software baseado em nuvem.
Miller Insight Centerpoint
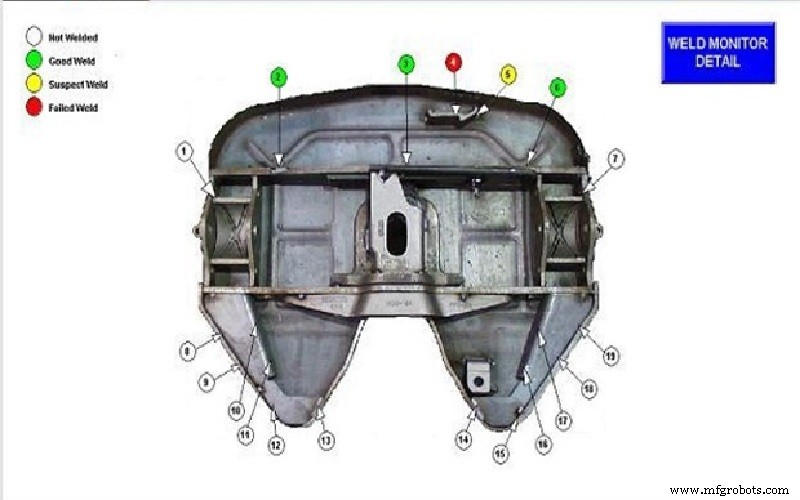
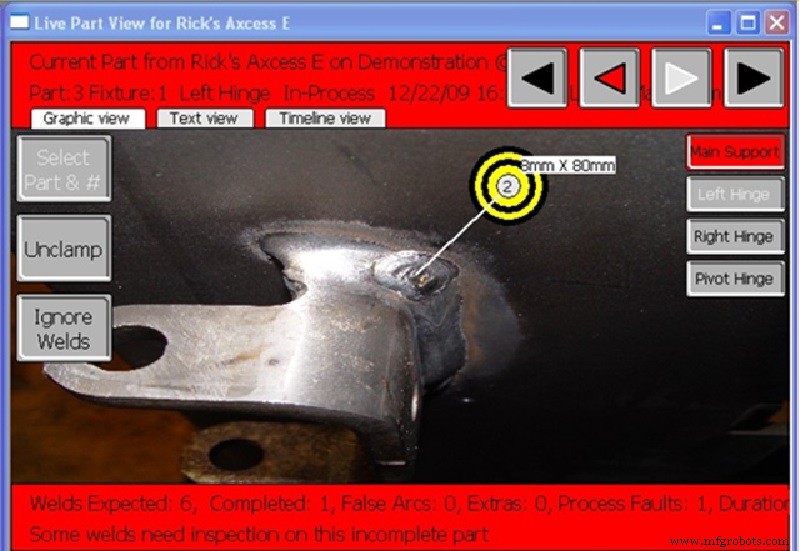
Rastreabilidade
Os OEMs automotivos não estão apenas pedindo a seus fornecedores que façam boas peças, mas também que implementem sistemas de qualidade para fornecer “rastreabilidade” que associará os resultados de soldagem de uma peça ao seu número de série. O objetivo é poder rastrear até um ponto na produção em que as peças eram conhecidas por estarem em conformidade se uma peça não conforme for detectada.
Para ajudar os fabricantes a atender à rastreabilidade, os dados de monitoramento de arco da fonte de energia de soldagem e do controlador do robô, além de quaisquer dados específicos da peça que precisam ser acessados remotamente e registrados no PLC, devem ser capturados e associados ao número de série da peça. Como harmonizar esse mashup de dados – e a dificuldade de fazê-lo – depende do que o fabricante é capaz de integrar imediatamente, sem comprometer os protocolos de segurança internos.
Variáveis de string
Um truque é usar uma função de criação de variável de string do controlador do robô para criar identificadores exclusivos como um mecanismo de rastreamento. Há uma mistura de variáveis usadas para armazenar números ou mesmo posições, e essas variáveis diferem com base no formato e no número de dígitos. Variáveis de string podem ser uma combinação de caracteres ou números de até 32 caracteres. Estes podem ser chamados para exibir uma mensagem no pingente ou para outros usos.
No caso da produção automotiva, nós os usamos para conter as informações do número de série da peça específica que está sendo produzida. Os engenheiros de controle podem usar a comunicação ethernet para "ler" os valores de um PLC ou leitor de código de barras e podemos passá-los para outros dispositivos.
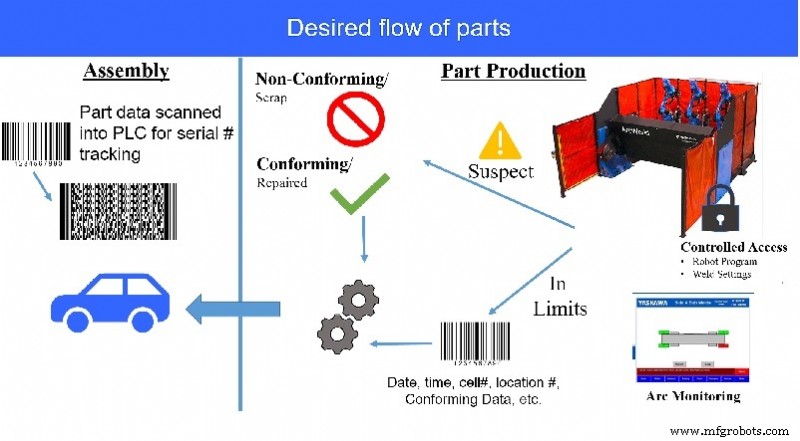
E/S simultânea
Yaskawa Motoman usa Concurrent I/O (CIO) para executar o controle lógico programável e comunicar dados entre o robô e a fonte de alimentação. Embora usado para configurações de solda, também pode ser usado para passar resultados de monitoramento de arco entre a fonte de alimentação e o robô. Para rastreabilidade, usamos para concatenar os resultados de solda para cada local de solda e enviá-lo, com o número de série da peça, para o PLC da planta para registro da peça. Também pegamos o número de série da peça e o enviamos para um carimbador de pinos que grava o número de série nas peças que passam pelo monitor de solda.
Recentemente, entregamos um sistema que coleta dados de inspeção de solda do Lincoln Electric Production Monitor e os apresenta ao operador em uma representação gráfica da peça. Ele destacará, em verde ou vermelho, os resultados do monitor em cada local de solda - com base em estar dentro ou fora dos limites. O monitoramento CheckPoint™ (um software externo) é projetado para armazenar dados na nuvem. O CIO permitiu acesso imediato aos resultados do Monitor de Produção para que fosse apresentado ao operador enquanto a peça estava sendo produzida.
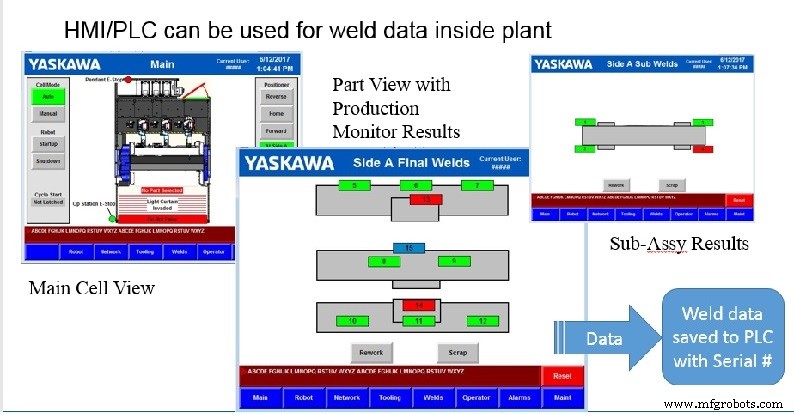
Implementação
O manuseio dos dados de monitoramento de solda deve considerar o controle de produção, juntamente com os requisitos de registro histórico e rastreabilidade. Os dados capturados ao longo do caminho são usados de maneira diferente em toda a organização, e essas necessidades devem ser consideradas para cada função em cada etapa.
Embora o uso de dados de monitoramento de solda deva simplificar a verificação da qualidade da peça pelos operadores no local, os dados históricos podem ser usados pelo pessoal de supervisão para administrar planos de qualidade e solucionar problemas. Os recursos de segurança tornam quase impossível desviar-se dos protocolos e parâmetros estabelecidos, e o monitoramento de arco fornece indicações gráficas em tempo real de soldas que precisam de inspeção adicional.
Com o PLC como destino final, os dados de solda específicos da peça são registrados, armazenados e rastreáveis. Pode ser necessário um trabalho inicial considerável para chegar à harmonização total dos dados; no entanto, os resultados são clientes confiantes e qualidade aprimorada que também podem ajudar a garantir o futuro de sua operação.
Robô industrial
- Temperaturas críticas para supercondutores
- Por que a excelência em confiabilidade é fundamental para a segurança
- As 10 regras de codificação para escrever o programa crítico de segurança da NASA
- Dicas de segurança no local de trabalho para operadores CNC
- Desenvolvendo uma Nova Era para uma Segurança Alimentar Mais Inteligente
- Um Caso para Atualizar Caminhões Envelhecidos
- Estratégias para a preparação adequada da solda
- 5 dicas de segurança para preparar equipamentos pesados
- Dicas de segurança para soldagem de tanques de combustível
- Entendendo a inspeção de soldagem