Estratégias de moagem vão de boa a ótima
Como o software, a automação e os avanços abrasivos estão levando as peças e a retificação de ferramentas ao overdrive.
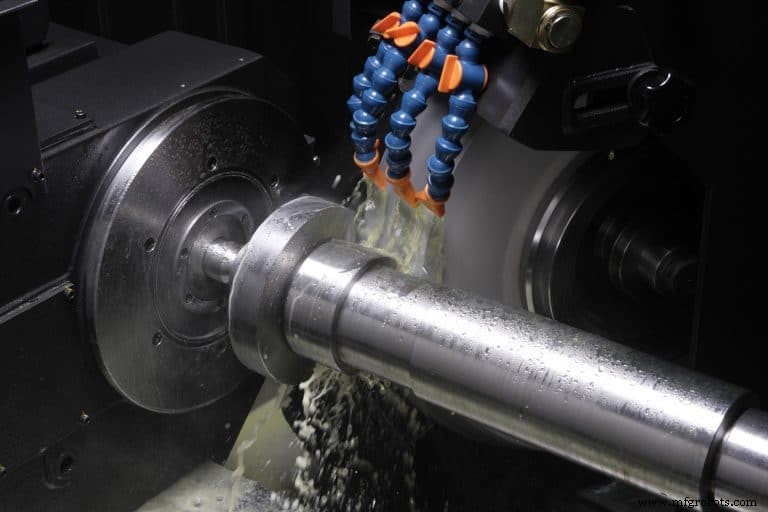
Talvez sua empresa seja especializada em componentes aeroespaciais ou médicos e você precise produzir geometrias complexas em metais muito difíceis de cortar por meio de métodos convencionais de usinagem. Ou talvez você trabalhe ou possua uma oficina de ferramentas e cortadores e esteja procurando maneiras mais rápidas e econômicas de produzir brocas, fresas de topo e ferramentas de forma. Seja qual for o motivo, e qualquer que seja o requisito, você está com sorte. Tal como acontece com a maioria das tecnologias de metalurgia, a retificação – mais apropriadamente chamada de usinagem abrasiva – melhorou muito nos últimos anos.
Como assim? Para começar, os fabricantes de rebolos desenvolveram novos ligantes e superabrasivos
que claramente merecem o título de “super”, capazes de remover mais material em menos tempo do que nunca. E os fabricantes de retificadoras estão fornecendo equipamentos cada vez mais capazes, rígidos e poderosos o suficiente para tirar o máximo proveito desses abrasivos avançados, ao mesmo tempo em que adicionam recursos inteligentes como automação, monitoramento remoto e sistemas de software inteligentes às suas máquinas-ferramentas.
Simplificando, a retificação entrou em uma nova era de produtividade e precisão das peças; se você não estiver aproveitando isso, poderá estar perdendo oportunidades significativas de melhoria de processos, aumento da qualidade do produto e um aumento nos resultados.
Melhor controle é fundamental
Um fator-chave para isso é a falta de maquinistas qualificados. Isso é de acordo com Shane Farrant, gerente nacional de produtos para trituradores da JTEKT Toyoda Americas Corp., Arlington Heights, Illinois, que acrescentou que tornar a interface homem-máquina (HMI) mais fácil de entender é um primeiro passo necessário para minimizar os efeitos de um mão de obra menos qualificada.
“Uma HMI mais simples e intuitiva é um dos muitos aprimoramentos de máquina que desenvolvemos para nossa linha de retificadoras universais, cilíndricas, de eixo de comando e virabrequim”, disse ele. “Isso significa um formato fácil de usar, com maior dependência de imagens e outros gráficos para auxiliar nos procedimentos de configuração e programação.”
Também houve um grande impulso em direção a um ambiente de trabalho baseado na Internet das Coisas (IoT). Por exemplo, a página de diagnóstico no controle de toque TOYOPUC da Toyoda exibe os níveis de refrigerante, vibração da máquina, temperatura do óleo - qualquer coisa que possa se traduzir em baixa qualidade da peça ou criar um problema de produção enviará um alerta imediato para quem for responsável por consertá-lo. Além disso, é possível coletar essas informações do controle da máquina e enviá-las para um banco de dados em rede para análise histórica.
Outro recurso de economia de tempo é a geração automática de programas alternativos, que um operador pode chamar se houver um problema relacionado ao processo. O gerente de engenharia de proposta da JTEKT Toyoda, Steve Earley, disse que esta opção de controle de conversação está disponível na retificadora de rolos GE6 da empresa, uma máquina que também se beneficiou de algumas modificações na fundição, motores e outros componentes, todos projetados para reduzir a vibração e aumentar a precisão da máquina em esta aplicação especial.
Os materiais usados para fabricar as baterias de lítio usadas em veículos elétricos são bastante finos, explicou, e os rolos que produzem esse material devem, portanto, ser extremamente precisos, com acabamentos superficiais muito finos. “Quando um operador está configurando a máquina, o controle apresentará um programa generalizado para começar, bem como duas alternativas – uma que é mais agressiva para tempos de ciclo mais rápidos e um programa mais conservador que produz melhores acabamentos de superfície”, disse Earley . “Com base nos resultados iniciais, o operador pode facilmente decidir mudar para qualquer conjunto de parâmetros de usinagem que forneça a melhor peça no menor tempo possível.”
Requer menos operações
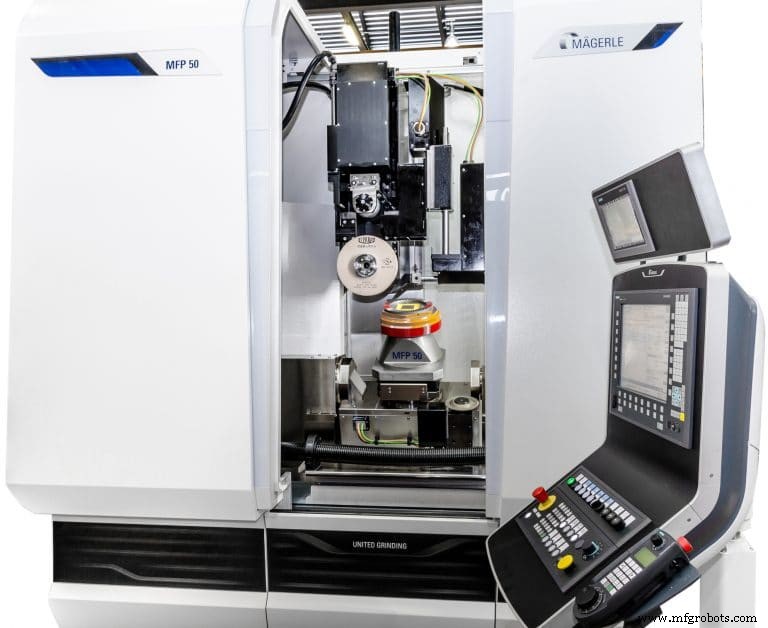
Larry Marchand, vice-presidente do grupo de perfis da United Grinding North America Inc., Miamisburg, Ohio, concordou com a necessidade de controles fáceis de usar, especialmente à medida que as retificadoras se tornam mais capazes. Mas ele disse que também há um tremendo apelo em toda a comunidade de manufatura para reduzir o trabalho em processo e menos operações de usinagem, levando a United Grinding e outras empresas a adotar a chamada abordagem "feito em um" para reduzir o tempo de toque do operador e aumentar o valor por operação.
Para dar suporte a isso, a United Grinding introduziu “processos, operações e recursos adicionais” para retificadoras de perfil que antes eram de propósito único. “Os clientes querem agregar mais valor no manuseio de uma única peça”, disse Marchand. “Temos visto uma grande demanda por máquinas com trocadores automáticos de ferramentas, possibilitando retificar a peça e depois trazer uma furadeira ou fresa para completar a peça. Isso elimina operações secundárias, reduz o tempo de entrega das peças e melhora a qualidade.”
Isso significa que as oficinas mecânicas devem trocar suas máquinas-ferramentas CNC por um super-retificador que faz tudo? De jeito nenhum. Assim como as máquinas multitarefas fazem um ótimo trabalho ao fresar uma ranhura ou moer um mancal, uma rebarbadora multitarefa agora pode executar tarefas antes reservadas para centros de usinagem e máquinas de furação – dito isso, nenhum estilo de máquina-ferramenta pode substituir o outro. Como Marchand apontou:“Se você tem uma peça que está moendo intensamente, é sempre melhor com um moedor dedicado”.
Há várias razões para isso, disse ele. A retificação requer substancialmente mais fluido de corte do que as operações de fresamento e torneamento, visando precisamente a interseção da peça e do rebolo. Dirigir uma roda que mede alguns metros de diâmetro requer muita potência, muito mais do que está disponível em uma máquina média de fabricação de chips. Finalmente, manter décimos e acabamentos de superfície de um dígito o dia todo é algo em que a maioria das retificadoras CNC se destaca porque são projetadas para otimizar essas operações. Centros de usinagem? Não muito.
Enfrentando as coisas difíceis
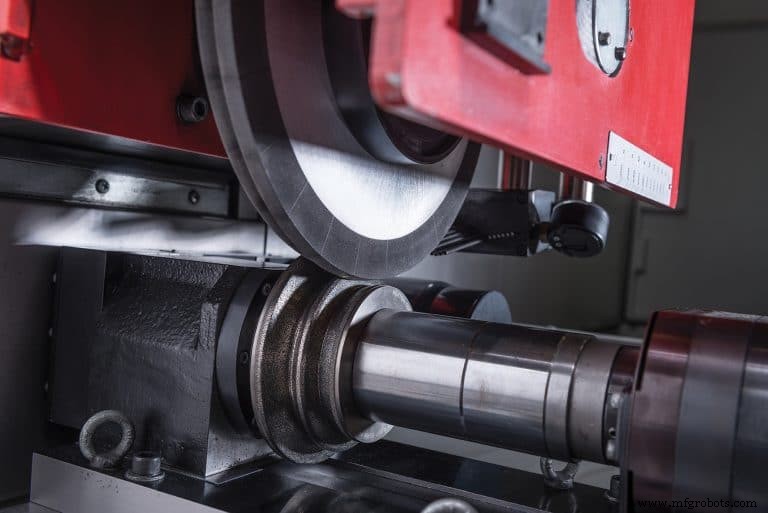
Essas capacidades são especialmente relevantes com metais ricos em níquel, cromo e cobalto, disse Marchand. “Muito do nosso negócio vem de clientes que produzem peças de Inconel e Rene, materiais que – pelo menos em seu estado endurecido – são quase não usináveis. Sua única opção é eletroerosão ou retificação e, graças à rigidez, potência e precisão das modernas retificadoras, além da disponibilidade de superabrasivos que não estavam disponíveis até recentemente, a maioria opta pelo último.”
Um dos principais fabricantes de superabrasivos é a Norton|Saint-Gobain Abrasives, Worcester, Massachusetts. Alfredo Barragan, engenheiro sênior de aplicação corporativa para superabrasivos na América do Norte, disse que a retificação já foi considerada um processo “apenas de acabamento”, mas, com o desenvolvimento de tecnologia de retificação cada vez mais capaz, evoluiu para um processo de usinagem convencional. Para obter o maior sucesso com este processo, no entanto, abrasivos igualmente modernos devem ser aplicados.
“Rebolos tradicionais de resina ou matriz diamantada com ligação metálica tendem a ser muito densos”, disse Barragan. “Ser denso é uma coisa boa porque lhe dá uma estrutura robusta e ajuda a fornecer uma forte ligação que mantém essa estrutura unida, mas levanta uma consideração:a roda tende a carregar mais rápido, o que a longo prazo reduz a produtividade. As rodas bond híbridas Norton Winter Paradigm resolvem esse problema.”
Diz-se que as rodas proporcionam uma combinação de retenção de grãos aprimorada com altos níveis de porosidade, reduzindo assim as forças de corte. A maior porosidade também reduz a carga – o rebolo retifica mais frio, mais livremente, com menos tempo de inatividade, produzindo mais peças por dia. Dependendo do abrasivo usado, os rebolos de liga híbrida retificam eficientemente metal duro, cerâmica avançada, aços ferramenta endurecidos e as ligas de alta temperatura que a United Grinding’s Marchand acabou de mencionar.
No entanto, há mais nisso do que a tecnologia de abrasivos. Assim como as máquinas-ferramenta às quais estão conectadas, as próprias rodas estão ficando mais inteligentes, com etiquetas RFID incorporadas para melhor gerenciamento de ativos, aquisição simplificada, rastreamento de informações de uso e preparação e proteção contra erros do operador.
A Norton|Saint-Gobain também não restringe seus esforços a produtos abrasivos. Seu sistema de monitoramento e diagnóstico de processo 4Sight fornece funcionalidade de IoT semelhante à discutida anteriormente, com monitoramento em tempo real, independente da marca, dos valores da retificadora, como carga do eixo e utilização da máquina, e a capacidade de armazenar dados para análise de tendências ou enviar alertas conforme necessário . “Esta é uma das maiores iniciativas do ano para nós e, juntamente com nossos sistemas de etiquetas inteligentes, serve como base de nossa solução Industry 4.0”, disse Barragan.
Chegando à sua tela:V@dison
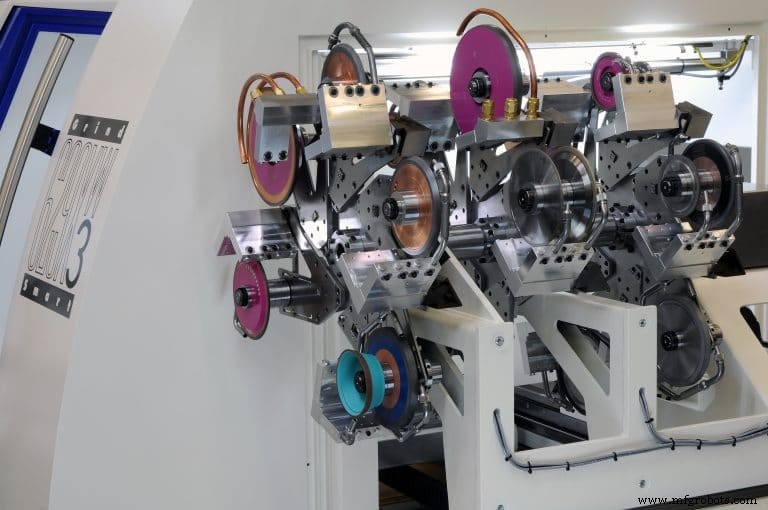
Eles não estão sozinhos. A Vollmer of America Corp., Carnegie, Pa., juntamente com sua empresa-mãe, o Vollmer Group, está trabalhando em uma série de ferramentas e serviços projetados para “transformar digitalmente” as operações de retificação. Com a marca V@dison, eles incluem a tela V@ para maior visibilidade dos parâmetros da máquina, verificação V@ para simulação de processo, V@ boost para otimizar o desempenho da máquina de acordo com a peça e guia V@ para manutenção preventiva mais consistente.
Vollmer ainda está nos estágios iniciais desta iniciativa, mas a gerente de vendas norte-americana Shannon Fox disse que ainda há muitas frutas de melhoria de baixo custo disponíveis para a comunidade de moagem. A principal delas é a automação - a Fox apontou para os recursos robóticos de carregamento de peças e troca de rodas de sua ferramenta e rebarbadora VGRIND 360 como um exemplo, opções que a Vollmer e, de fato, a maioria dos fabricantes de máquinas-ferramenta instalam rotineiramente à medida que seus clientes trabalham em direção às luzes. fora de fabricação.
A simulação é outra solicitação de rotina. Embora o sistema de verificação V@ da Vollmer ainda esteja em desenvolvimento, Fox observou que o software NUMROTOplus oferecido na Vollmer e em outras marcas de equipamentos de moagem é uma alternativa madura e bem aceita. “A simulação está se tornando mais importante à medida que os trituradores se tornam mais capazes”, disse ele. “Os quartos são mais apertados, as geometrias das ferramentas são cada vez mais complexas e muitas máquinas, inclusive as nossas, permitem o uso de vários conjuntos de rodas em um único trabalho, levantando preocupações de interferência. Sem simulação, você corre o risco de travar uma máquina-ferramenta muito cara.”
Ver para crer
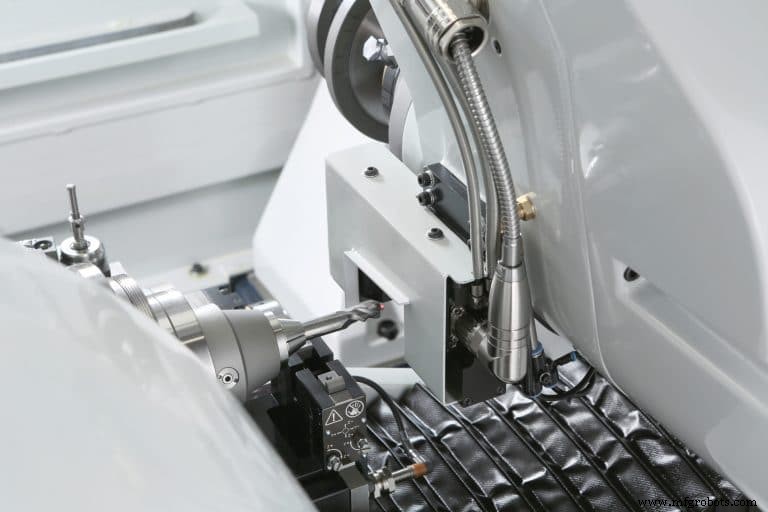
A simulação também é importante por outras razões. A ANCA CNC Machines, com sede em Melbourne, Austrália, por exemplo, a utiliza para prever o desequilíbrio da ferramenta em fresas de topo de passo variável. “Essa é uma das desvantagens das fresas de alto desempenho – como o espaçamento das ranhuras é irregular, elas são inerentemente desequilibradas”, disse Lucas Hale, gerente de marketing global. “Para combater isso, desenvolvemos um software de simulação que calcula o desequilíbrio e ajusta o programa NC para compensá-lo, removendo material adicional em locais estratégicos. A ferramenta sai da esmerilhadeira perfeitamente equilibrada, proporcionando maior vida útil da ferramenta e melhor acabamento superficial na peça usinada.”
Hale concordou com o pedido de automação, incluindo peças robóticas e manuseio de rodas, mas ofereceu várias maneiras adicionais de aumentar a produtividade. Onde a rotina de “colar” da roda para remover o carregamento era feita manualmente, a ANCA o automatizou, reduzindo os custos de mão de obra e prolongando a vida útil da roda. Diz-se que o software e as máquinas da ANCA fornecem “significativa facilidade de uso”, reduzindo o tempo de configuração. E os sistemas de medição baseados em laser fornecem verificação durante o processo da precisão e geometria da ferramenta de corte, seguida por offsets automatizados ou dressagem do rebolo para compensar o desgaste.
E a ANCA levou esse processo um passo adiante. Através da colaboração com empresas como a Zoller Inc., fornecedora líder de equipamentos de pré-ajuste de ferramentas, a ANCA desenvolveu uma interface que suporta inspeção automatizada e feedback para a retificadora CNC – um robô coloca a fresa no pré-ajuste, que a mede e envia os resultados para um sistema de software que ajusta a máquina conforme necessário. Isso “fecha o ciclo”, explicou Hale, e junto com os sistemas integrados de gerenciamento de blanks, permite que os clientes “carregem centenas de ferramentas, pressionem e voltem no dia seguinte para as ferramentas de corte concluídas”, disse ele.
“A construção básica da máquina também melhorou nos últimos cinco anos”, continuou Hale. “Por exemplo, os motores lineares se tornaram muito mais comuns em nossa indústria. Eles não apenas contribuem para a qualidade das ferramentas de corte e, portanto, a qualidade das peças que estão sendo feitas com elas, mas as máquinas lineares se movem muito mais rápido do que as com fusos de esferas, reduzindo os tempos de ciclo. E como há menos desgaste nos componentes da máquina, a vida útil do equipamento é estendida. É por isso que os motores lineares se tornaram um componente padrão de qualquer retificadora de alta precisão e alto desempenho.”
Primeira Parte, Parte Boa
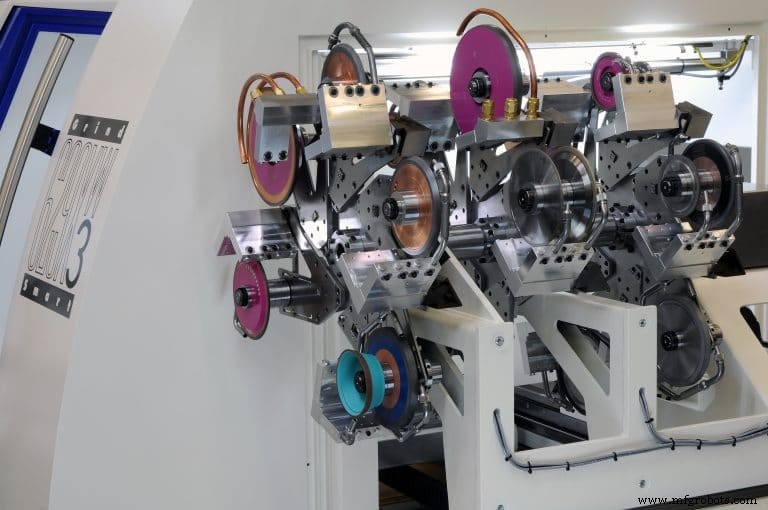
Assim como a JTEKT Toyoda está abordando a escassez de maquinistas qualificados com software de controle mais intuitivo, a Rollomatic Inc., Mundelein, Illinois, está trabalhando para tornar as configurações das máquinas mais fáceis e rápidas. Isso porque a maioria dos fabricantes de ferramentas e cortadores não são diferentes de qualquer oficina de corte de metal; eles se deparam com tamanhos de lote menores e prazos de entrega mais curtos, tornando o tempo de configuração uma porcentagem maior de qualquer execução de produção. Uma parte da solução? Melhor software.
“Durante décadas, as oficinas queimaram três, quatro, cinco peças em bruto por configuração, discando gradualmente na máquina até obter uma boa peça”, disse Eric Schwarzenbach, presidente da Rollomatic Inc. “Mas usando software inteligente, é muito possível para reduzir o número de peças de sucata, com zero sendo o objetivo final. Isso não apenas reduz os custos de material, mas também o tempo de configuração.”
O software auxilia o operador fazendo uma representação 3D da máquina-ferramenta, peça de trabalho e rebolo, disse Schwarzenbach, eliminando a necessidade de uma execução a seco. O operador pode acelerar a animação, desacelerá-la, retroceder ou ampliar áreas problemáticas, ajudando-o a evitar possíveis colisões entre o conjunto de rodas e a peça de trabalho. E quando a animação é feita e a máquina está realmente fazendo as peças, o software trabalha para eliminar “movimentos vazios” e reduz as distâncias de segurança ao mínimo.
O software inteligente é ótimo, mas Schwarzenbach foi rápido em apontar que a máquina-ferramenta e seus sistemas relacionados são igualmente importantes. Quanto mais precisa e estável for a máquina-ferramenta, mais fácil será atingir a dimensão alvo na primeira tentativa. Além disso, a tecnologia aprimorada de correção de rebolos, procedimentos de calibração automatizados, controles mais rápidos que processam cálculos mais rapidamente e ligações híbridas de rebolo que são resistentes ao desgaste, corte livre e retêm cantos afiados por mais tempo são essenciais. Esses fatores desempenham um papel importante em configurações mais rápidas e uma capacidade aprimorada de tornar a primeira peça uma boa peça, com tempos de ciclo mais curtos para inicializar.
Como outros já mencionaram, a troca automatizada de rebolos é outro divisor de águas - Schwarzenbach disse que os trocadores de alta velocidade da Rollomatic podem trocar um pacote de rebolos em cinco segundos, mandril para mandril, e atingir tempos de moagem para moagem de 11 segundos. O benefício vai além de tempos de ciclo mais curtos, no entanto. “Se você tem um pacote com quatro rodas, o potencial de colisão é maior do que um com uma ou duas rodas. Isso complica a configuração. Portanto, se você pode dividir um pacote de rodas grande e permitir o tempo de troca de roda de 11 a 12 segundos, essa é a maneira preferida de ir hoje em dia. ”
Sistema de controle de automação
- Quão bom é o GCP como uma escolha de carreira?
- Bom a ótimo:Olhe no espelho
- Estratégias para componentes de transmissão de energia mais confiáveis
- Por que as ordens de serviço merecem mais amor de todos nós
- Por que e quando atualizar de luzes indicadoras para uma tela HMI
- Como obter mais do seu investimento em caminhão articulado
- Benefícios de usar um rebolo ou disco de aba de 5 ou 6 polegadas
- Automação da UE:as melhores tendências tecnológicas de 2020
- 7 estratégias de grandes gerentes de segurança
- Lixamento de superfície:mais do que apenas fiação