Fabricação médica fica mais inteligente
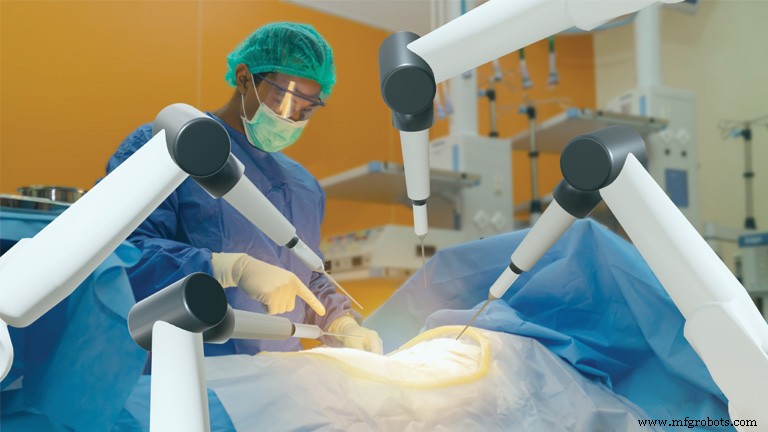
A fabricação digitalizada e automatizada está avançando no mundo da fabricação médica, evidenciada por sistemas recentes colocados em linhas de produção durante a pandemia do COVID-19.
Dados os rigorosos padrões que regulam a fabricação de dispositivos médicos, o ambiente da Indústria 4.0 centrado em dados é feito sob medida para fabricantes contratados que tentam permanecer dentro das especificações, ao mesmo tempo em que lidam com a dramática falta de operadores qualificados.
Como sempre, os materiais estão ficando mais sofisticados e as peças estão ficando menores, com geometrias mais complexas e requisitos de tolerância mais rígidos.
Em um sentido amplo, as tendências de cuidados de saúde – populações envelhecidas, a busca por diagnósticos e terapias mais remotos fora do ambiente hospitalar caro, terapias mais personalizadas – estão impulsionando o desenvolvimento de dispositivos médicos. E com incertezas pandêmicas contínuas e cadeias de suprimentos prejudicadas resultantes, estabelecer mais visibilidade sobre o funcionamento de fornecedores e vendedores é a prioridade nº 1.
Junto com a digitalização dos cuidados de saúde vem a necessidade de proteger todos os dados coletados. Para esse fim, há iniciativas como o novo Centro de Segurança Cibernética de Dispositivos Médicos da Universidade de Minnesota, anunciado em 9 de setembro. Cinco pesos pesados do setor de saúde se uniram para trabalhar juntos no novo centro:Boston Scientific, Smiths Medical, Optum, Medtronic e Abbot Laboratórios. Seu objetivo é eliminar vulnerabilidades de software em dispositivos médicos que podem ser usados para prejudicar pacientes ou interromper instalações de saúde.
O futuro de alta tecnologia dos cuidados de saúde também significa mais diagnósticos e procedimentos robóticos, daí a necessidade de mais ferramentas e peças médicas dedicadas ao uso com esses sistemas. Por exemplo, a XACT Robotics em Hingham, Massachusetts, desenvolvedora do XACT ACE Robotic System, anunciou em 30 de agosto que concluiu com sucesso a inscrição de pacientes no primeiro estudo dos EUA avaliando o XACT ACE para uso em procedimentos pulmonares percutâneos. Isso inclui biópsias para confirmar a presença de câncer. O sistema robótico de mãos livres pode detectar câncer mais cedo e de forma menos invasiva.
Enquanto isso, a iData Research projeta que 3 milhões de procedimentos cirúrgicos robóticos serão realizados anualmente até 2025. Braços robóticos em equipamentos como o Sistema Cirúrgico da Vinci exigirão muitos instrumentos miniaturizados que os médicos controlam para realizar essas operações minimamente invasivas. As cirurgias robóticas usam incisões menores, resultando em menos perda de sangue e cicatrizes, internações hospitalares mais curtas e recuperações mais rápidas.
A IA alimentada por dados também virá à tona para melhorar os resultados dos pacientes. Um claro indicador desse caminho é a aquisição pela Stryker da Gauss Surgical de Menlo Park, Califórnia. Gauss desenvolveu o Triton, uma plataforma habilitada para inteligência artificial para monitorar a perda de sangue durante a cirurgia.
A manufatura aditiva também continuará a expandir seu papel crítico na produção de implantes, ferramentas e modelos de treinamento cirúrgico específicos para pacientes. Por exemplo, a Tsunami Medical da Itália está impressionando a indústria com o uso de sistemas de impressão 3D de feixe de elétrons e laser GE Additive para produzir uma variedade de implantes espinhais altamente complexos.
Pequenas peças, desafios de classificação
À medida que os materiais de dispositivos médicos evoluem e as peças ficam menores, as máquinas de estilo suíço da série L da Marubeni Citizen-Cincom (MCC), Allendale, N.J., estão atendendo ao chamado.
“Medical tem materiais que você nunca ouviu falar antes”, brincou o presidente e COO Brian Such. Materiais resistentes podem ser usados para peças simples ou componentes mais complexos, exigindo o uso de muitas ferramentas para criar os diferentes recursos.
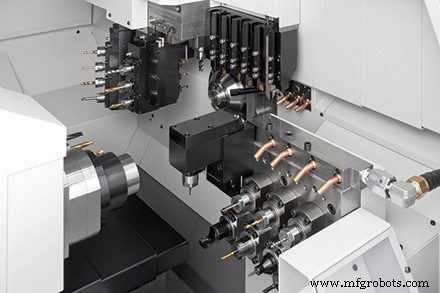
“Nossas máquinas da série L são uma máquina de grupo com subfuso”, e sua vantagem significativa para a produção médica é que são modulares, explicou Such. “Com várias ferramentas disponíveis a qualquer momento, podemos simplesmente retirar uma e colocar três no mesmo lugar.”
Para lidar com os diâmetros menores típicos das brocas e fresadoras médicas atuais, a MCC oferece aceleradores de até 4x aceleração. “Nossas ferramentas motorizadas atingem velocidades de até 6.000 ou 9.000 rpm, dependendo dos modelos, mas podemos inserir um porta-ferramentas diferente e agora estamos com 36.000 rpm. Quando isso não for suficiente, podemos adaptar nossos fusos elétricos, que podem chegar a 80.000 rpm.”
Como exemplo, observou Such, um cliente pode estar perfurando um furo de oito milésimos, “então você precisa de alguma velocidade para isso – ou utilizar uma fresa de topo de 16 milésimos ou talvez até uma fresa de topo de oito milésimos para inclinar um canto em algum lugar . Com nossos fusos elétricos de 80.000 rpm, podemos deslizar para esses bolsos. E essa mesma ferramenta pode ser usada como uma ferramenta de face, uma ferramenta cruzada ou uma ferramenta voltada para trás, por isso é muito modular.” A MCC fez parceria com o vendedor de fusos de alta velocidade NSK para criar esses fusos proprietários.
Há cerca de dois anos, a MCC ampliou a funcionalidade do eixo B de suas máquinas ao introduzir a versão ATC (troca automática de ferramentas) de sua máquina L20. “Agora temos a capacidade de 13 ferramentas no eixo B”, disse Tal, enquanto normalmente um eixo B tem apenas quatro ferramentas – e isso “é muito importante para o mercado médico” devido aos ângulos apertados das peças de hoje.
Outra inovação do MCC, introduzida por volta de 2016, é o corte por vibração de baixa frequência (LFV). Nesse processo, a máquina-ferramenta “oscila o caminho de corte do eixo Z ou X, movendo-se para dentro e para fora em uma velocidade muito alta para fazer pequenos cortes de ar e quebrar os cavacos enquanto você está usinando”, disse Such. “A área médica adora a tecnologia LFV, e a maioria dos clientes que a usam pela primeira vez dizem:'Nunca mais compro uma máquina sem ela'.” Com LFV “você 100% vai quebrar as fichas; não há meio-termo. Uma vez que você tenha o processo em execução, é garantido. Você ainda precisa conhecer suas ferramentas de corte, e as ferramentas de corte ainda podem falhar, mas o problema do encapsulamento de cavacos desaparece.”
Os clientes da MCC variam de OEMs com 300 ou 400 máquinas a fabricantes menores com 10 máquinas. E esses clientes “estão fazendo todas as peças diferentes”, desde parafusos ósseos comuns e gaiolas de cirurgia da coluna até várias ferramentas cirúrgicas, como alargadores de ossos necessários para cirurgias de quadril e joelho. Existem pequenos parafusos ósseos de aproximadamente 4 mm de diâmetro com orifícios para suturas. “Nove ferramentas diferentes entram para cortar as diferentes formas”, disse Such. “Há muitos recursos neste pequeno parafuso ósseo – não é apenas um parafuso com cabeça.”
Depois que essas pequenas peças são feitas, a classificação se torna a questão principal, continuou. A MCC fabrica equipamentos de automação sob medida para a tarefa.
“Essas peças são tão pequenas que, quando caem no balde, podem ter 300 lá. Se você vai tentar escolher o último para tentar medi-lo, qual foi esse? Podemos ter um dispositivo que tenha bandejas diferentes para contar”, disse Such.
O cliente pode colocar 100 peças em uma bandeja, então quando a bandeja se mover, coloque uma na próxima bandeja, 100 na próxima bandeja, uma na próxima bandeja e assim por diante. Se houver 10 bandejas, ele pode funcionar por oito horas ou durante a noite sem supervisão. Ao medir as peças em intervalos, os clientes podem isolar se as peças anteriores são boas ou ruins graças às bandejas de coleta.
A Vantagem dos Seis Eixos
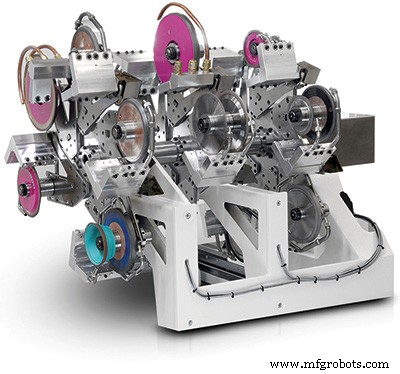
A demanda constante por retificadoras de ferramentas de corte da Rollomatic USA Inc., Mundelein, Illinois, é um indicador claro da resiliência da fabricação de dispositivos médicos, afirmou o presidente Eric Schwarzenbach.
Entre os muitos instrumentos, as máquinas Rollomatic são solicitadas por OEMs e fabricantes contratados para fabricar várias ferramentas de corte ortopédico, como limas, brocas de osso, perfuradores de crânio e brocas artroscópicas. Durante a pandemia, “nossos clientes investiram como antes – nem mais, nem menos”, apesar do adiamento de cirurgias ortopédicas ou eletivas. “Havia negócios suficientes para manter essas empresas funcionando e manter sua necessidade de reinvestimento.”
Nos últimos dois anos, observou ele, vários instrumentos para cirurgias robóticas estão crescendo em demanda. Mas esses dispositivos representam um desafio particular.
“Uma broca que um cirurgião usa com uma peça de mão para perfurar o osso é diferente do que um robô emite”, explicou ele. “Os robôs usam brocas mais longas do que os cirurgiões. A natureza de fazer uma broca longa é mais difícil do que uma broca mais curta. Em primeiro lugar, os blocos de ferramentas cirúrgicas estão sendo usinados em um estado macio em um torno tipo suíço e posteriormente endurecidos. Esses processos inerentemente causam deformação nesses espaços em branco, e quanto mais longos eles são, mais dobrados eles são. E quando eles são dobrados, temos problemas para carregar, triturar e descarregar de forma confiável. Quando ensinamos aos clientes nossa máquina e configuração, temos que ter muito cuidado para ensiná-los com alguma profundidade e garantir que eles entendam os recursos para contornar um blank dobrado. Os blanks dobrados geralmente são endireitados pelo fabricante, mas mesmo assim nunca são perfeitos - embora não precisem ser perfeitos. A máquina é capaz de lidar com uma pequena distorção.”
Quanto mais robótica a indústria se torna, “mais foco deve haver no ponto de perfuração. Enquanto um cirurgião sempre pode perfurar o osso porque ele pode olhar, ver, ajustar sua mão e pressão para que o ponto não se afaste, o robô não. Então, esses pontos devem ser projetados para serem mais autocentrados. Ajudamos os fabricantes de dispositivos médicos a ensiná-los como é um ponto de autocentragem.”
Schwarzenbach também observou mais variantes em aço inoxidável 17-4 para cortadores ortopédicos. “O material tornou-se mais macio e menos endurecido, o que é um desafio para nós em termos de encontrar os rebolos certos para retificá-los. Como você sabe, quanto mais macio o material, mais difícil é moer.” Para atender a essa necessidade, a Rollomatic fez parceria com fabricantes de rodas na Suíça e nos EUA para adquirir rodas adequadas para materiais mais macios.
“Quanto mais macio o material, mais rebarbas ele emite”, explicou Schwarzenbach, “portanto, a remoção de rebarbas é um problema. Nossos clientes geralmente usam escovas de nylon para remover rebarbas após a retificação, especialmente com materiais mais macios. Mas nenhuma roda ou processo é perfeito; sempre haverá um pouco de rebarba solta que precisa ser removida por algum método. Usamos escovas de nylon ou às vezes impregnadas com cerâmica ou abrasivos para remover essas rebarbas.”
As garras de desconexão rápida para ferramentas médicas são outra área de crescimento, continuou ele. Essas ferramentas podem ser encaixadas em uma peça de mão por um cirurgião ou presas a um braço robótico. Esses apertos “se tornaram muito mais complexos do que já vimos. Usamos um moedor de casca para a maioria deles.”
A capacidade de seis eixos da Rollomatic é o divisor de águas para fabricantes médicos que precisam de mais flexibilidade para programação e configuração mais fácil do volante, disse Schwarzenbach.
“Você não precisa usar rodas complexas; você pode usar rodas de formato mais simples, principalmente nos pontos de perfuração”, disse ele. “Você pode produzir uma ponta de perfuração com mais facilidade do que em uma máquina de cinco eixos. E não se esqueça:os pontos de perfuração agora estão se tornando tão baixos quanto 50 a 60 graus, inclusive. Eles são muito íngremes, ao contrário de uma broca de metal duro em metal a 120 ou 130 graus. Nossas máquinas de seis eixos realmente ajudam a retificar esses pontos de perfuração com muito mais facilidade do que lutar com a configuração de uma máquina de cinco eixos.”
E o trocador rápido de rodas da Rollomatic oferece ainda mais vantagens, acrescentou. “Temos vendido muito mais máquinas de troca de rodas. O trocador de rodas básico tem seis estações, então você pode colocar seis conjuntos de rodas para aumentar a flexibilidade, o que serve para lotes mais curtos. Lotes mais curtos precisam de mais flexibilidade com a troca frequente. As máquinas de troca de rodas são muito boas para isso.” Enquanto cerca de 80% das máquinas que a Rollomatic vende para a indústria médica mantêm os fusos padrão que abrigam um par de rodas na frente e atrás, alguns fabricantes “estão começando a adotar nossa nova tecnologia”.
O papel do teste de força
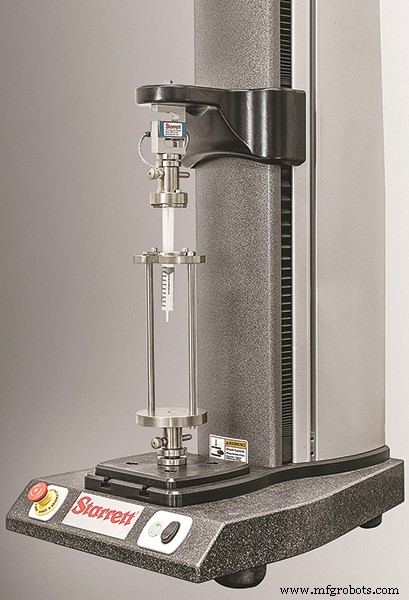
Desde a preparação para a fabricação até depois que a peça é feita, o equipamento de teste de força e seu software integrado executam funções importantes para produtos médicos – muitas vezes com o objetivo de conforto do paciente.
Por exemplo, os contornos e o revestimento de uma agulha podem ser testados quanto à facilidade com que entram na pele, enquanto os adesivos podem ser avaliados quanto à aderência à pele ou à facilidade de remoção.
Antes da fabricação, “você pode criar testes para garantir que seu equipamento funcione da maneira que deveria antes de usá-lo na fabricação”, explicou Jacob Morales, engenheiro de suporte técnico da The L.S. Starrett Co., Athol, Massachusetts. E para bandagens, “você pode testar o adesivo antes de usá-lo em sua linha de fabricação”, em lotes que variam, por exemplo, de uma em 100 a uma em 10.000 amostras. “Pós-processo, você pode executar esses testes novamente para garantir a consistência.”
Esses testes são particularmente importantes na fabricação de acordo com as normas ASTM e ISO, bem como na produção de documentação crítica para rastreabilidade, acrescentou Eric Perkins, gerente de tecnologia da Starrett para testes de força e material. O software Starrett permite testes de força e propriedades do material, e simplesmente clicando no ícone direito, o software pode realizar o teste apropriado. A medição de força abrange cenários de ir/não ir, incluindo testes de carga de pico, carga média, testes de compressão e muito mais. Seringas, um excelente exemplo que requer aplicação de força uniaxial, podem ser testadas com substâncias de amostra para determinar a força de injeção para taxas de injeção controladas.
Embora esses testes forneçam informações de amostra, eles nem sempre retornam dados específicos do material que compõe a amostra. O teste de material vai além, usando propriedades do material para testar alongamento e tensão-deformação, por exemplo.
O software Starrett pode ser integrado ao processo de fabricação, explicou Morales.
“Se você tem um sistema de força testando uma amostra, pode programá-lo com um sistema de entrada-saída para que o teste seja executado constantemente. O equipamento de fabricação move uma amostra para a máquina e envia um sinal; a máquina responde executando o teste e fornece uma saída de sinal com base nos resultados do teste. O restante do seu equipamento de fabricação pode responder adequadamente. Se você obtiver um resultado fora da tolerância, o sinal pode alertar um operador.”
Essa flexibilidade significa que “você pode conectar o sistema de força a um PLC e colocá-lo em linha com o ambiente de produção, para que você tenha eliminado possíveis erros de entrada de dados humanos”, disse Perkins. “Os usuários podem testar automaticamente um produto toda vez que ele estiver na fila.”
Do software básico de força L1 da Starrett às opções mais avançadas L2, L2Plus e L3, “damos aos clientes a capacidade de testar exatamente como qualquer padrão de fabricação afirma”, disse Perkins. E como o software Starrett é compatível entre plataformas, a adição de sistemas ópticos e de visão cria uma solução de metrologia extremamente ampla.
Esse nível de personalização não para no software, no entanto. A Starrett vem trabalhando com fabricantes para criar sistemas completamente automatizados.
“Estamos usando robôs para inserir peças em nosso sistema de teste de força”, disse Perkins. “Estamos usando garras pneumáticas para pegar as peças.” Com uma plataforma de teste em execução constante aliada a esse nível de automação, “nosso sistema dirá se você tem uma peça boa ou ruim, então o robô executa qualquer programa necessário e coloca essas peças no compartimento designado.”
Visão geral da GE
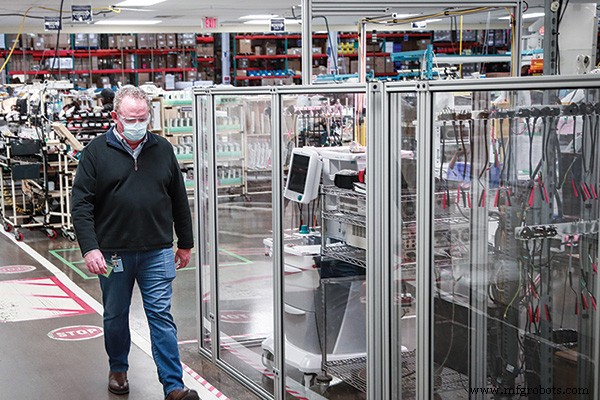
Melhorar os fluxos de trabalho hospitalares e manter a resiliência da cadeia de suprimentos foi uma prioridade para a GE Healthcare durante a pandemia.
“Estamos vendo um aumento nas solicitações de mais automação – não apenas do ponto de vista típico de produtividade, mas em termos de alavancar a automação para que possamos manter a produção em diferentes locais”, disse Jimmie Beacham, engenheiro-chefe executivo de manufatura avançada da GE Healthcare em Milwaukee. “Isso é mais fácil do que ter que treinar uma força de trabalho nova ou rotativa. Não se trata necessariamente da mão de obra, mas da segurança da cadeia de suprimentos, onde a automação faz sentido. Se eu tiver que mudar a produção de uma região para outra, é muito mais fácil se o processo já estiver automatizado.”
Uma parte importante dessa filosofia é à prova de erros, acrescentou. “Treinaríamos operadores e teríamos procedimentos escritos”, explicou Beacham. “Agora estamos procurando empregar outras tecnologias que digitalizem o que as operadoras precisam fazer e que interajam com elas. Digamos que você tenha uma estação de torque, onde você está apertando os parafusos, seguido por uma montagem complexa e depois um cobot. Estamos analisando tecnologias que conectam digitalmente tudo isso – que funcionam em sintonia com o operador para que ele interaja com essa pessoa e não exija que o operador se lembre de tudo. Isso nos dá muita flexibilidade quando estamos fazendo o mesmo produto em três regiões ao redor do mundo. Agora temos um processo de controle. Não dependemos de operadores memorizando procedimentos em papel quando precisam percorrer várias partes complexas da operação.”
Isso é vital para a GE Healthcare, que produz uma variedade de equipamentos de diagnóstico inteligentes. A manufatura aditiva é uma grande parte da equação, e a GE Healthcare também refinou seus processos nesse sentido.
“Quando começamos, provavelmente 80% a 90% do nosso tempo era investido em P&D, tentando descobrir como o aditivo funciona, como você desenvolve materiais e parâmetros para atender aos nossos requisitos de engenharia”, disse ele. “Agora estamos com cerca de 80 por cento de execução, onde estamos movendo as coisas para a produção, e os outros 20 por cento do nosso tempo são dedicados ao desenvolvimento de novos materiais para os novos funis que estão chegando. Temos uma unidade de produção em Monterrey, México, e temos um funil bastante ativo de coisas acontecendo lá. Depois, temos algumas outras aplicações aditivas que executamos no ponto de uso.”
Em última análise, embora a pandemia tenha se mostrado desafiadora, a GE Healthcare resistiu à tempestade.
“Nosso grande desafio foi o abastecimento, levando as pessoas com segurança para a fábrica”, disse Beacham. “Em alguns casos, como nos ventiladores, confiamos muito na automação para atender a uma demanda sem precedentes. Trouxemos muitas pessoas para fazer o trabalho, mas ainda precisávamos encontrar maneiras criativas de fabricar o volume de produtos que nossos clientes precisavam desesperadamente. E aprendemos que podemos fabricar as coisas de maneira diferente; que inspirou ainda mais ideias.”
Sistema de controle de automação
- Avaliação do Impacto da Indústria 4.0 na Manufatura
- 8 mitos proeminentes da fabricação de metal desmascarados
- Tecnologias para fabricação de componentes médicos mais eficazes vistas na MD&M West 2018
- 6 maneiras de a IIoT tornar a fabricação mais eficiente
- Stratasys:sendo mais sustentável com impressão 3D
- RELATÓRIO:2016 será um 'ponto de inflexão' para a tecnologia de fabricação
- Tornando a manufatura britânica mais inteligente:expectativas para 2018
- Preenchendo a lacuna de habilidades na fabricação de automóveis
- Stora Enso:o futuro da fabricação ficou mais inteligente
- Construindo uma cadeia de suprimentos de manufatura resiliente