Você pode levar com você:métodos de trabalho híbridos mudam algumas tarefas para qualquer lugar
O aumento no uso de ferramentas digitais de produção e comunicação durante a pandemia do COVID-19 acelerou o futuro do local de trabalho híbrido, no qual alguns funcionários e tarefas podem ser redirecionados para fora da fábrica.
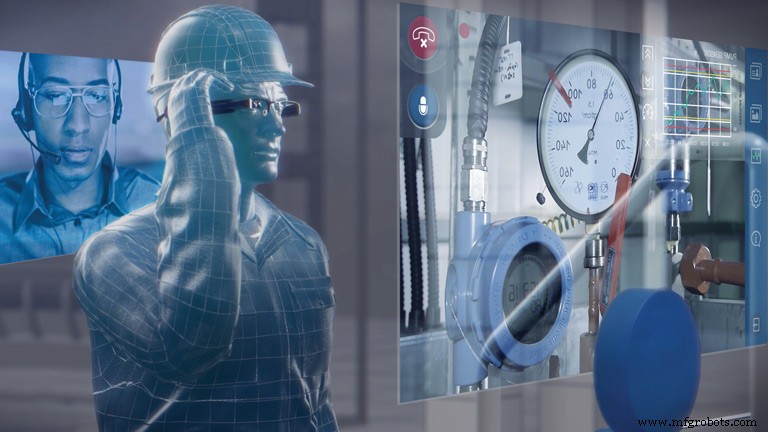
No entanto, embora pessoal como projetistas e engenheiros possam trabalhar facilmente remotamente – e, dependendo da empresa, o fizessem antes da pandemia – as máquinas ainda precisam de operadores no local. Dito isso, soluções como realidade virtual ou mista e conectividade baseada em nuvem estão levando as organizações a repensar como programam e executam determinadas tarefas de fabricação.
Os benefícios do híbrido
Confrontados não apenas com a escassez de trabalhadores qualificados, mas também com a necessidade de reformar seus locais de trabalho para acomodar os protocolos de pandemia, os fabricantes intensificaram sua busca para encontrar e otimizar ferramentas digitais para seus ambientes exclusivos.
“Embora os benefícios de uma perspectiva de saúde e segurança sejam claros durante uma pandemia global, os fabricantes, em particular, viram os benefícios de produtividade e retenção de funcionários” para buscar acordos de trabalho híbridos, disse Reid Paquin, diretor de pesquisa da IDC Manufacturing Insights de Needham, Massachusetts. um terço também experimentou maior experiência/satisfação dos funcionários, o que achamos que desempenhará um papel nos esforços do setor para lidar com questões de talento/trabalho.”
Além da fabricação, “a maioria dos grandes OEMs tem elementos de serviço de campo, e um problema que é quase universal no momento é a perda de funcionários e problemas com a transferência de conhecimento”, disse Charlie Neagoy, vice-presidente sênior de sucesso do cliente da Librestream. “Atualmente, estamos cerca de três milhões de pessoas adiantadas em termos de aposentadoria, e isso acelerou essa lacuna de conhecimento. A força de trabalho híbrida — a capacidade de fazer coisas de lugares diferentes — ajuda a compensar a perda de conhecimento que vem da aposentadoria precoce. As forças de trabalho híbridas podem oferecer empregos em todo o mundo e diferentes tipos de flexibilidade para seus funcionários.”
A Librestream, com sede em Winnipeg, Manitoba, Canadá, fornece uma plataforma de solução remota de realidade aumentada (AR). “Um benefício relacionado aos locais de trabalho híbridos é que eles permitem plataformas de colaboração compartilhadas entre várias partes”, acrescentou Neagoy. “A segurança também é um dos principais motivos para usar forças de trabalho híbridas. Muitos dos locais e equipamentos de fabricação são perigosos, portanto, acessar um local remotamente diminui o risco de acidente.”
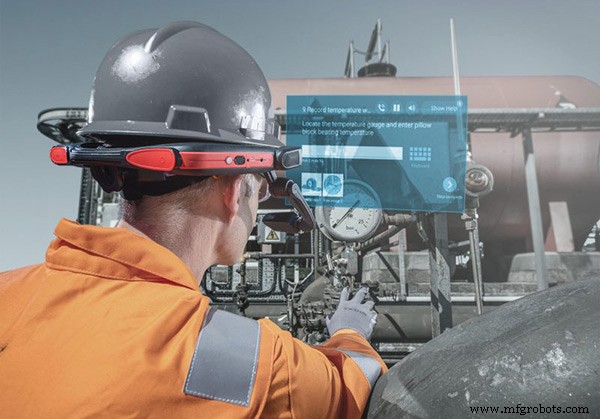
Além disso, as inspeções e certificações necessárias podem ser feitas remotamente, continuou Neagoy. “Nossa plataforma Onsight nos permite rastrear quantas inspeções nossos clientes fazem toda semana. Nossos clientes fazem entre 7.000 e 8.000 inspeções remotamente todas as semanas. Antes do COVID, gravávamos cerca de 2.000 inspeções por semana.”
A pandemia demonstrou que uma força de trabalho híbrida traz maior resiliência organizacional e eficiência do trabalhador, de acordo com Federico Sciammarella, presidente e CTO da MxD, Chicago, que se concentra na fabricação digital e faz parte da Manufacturing USA, uma rede de 14 institutos avançados de fabricação.
“Se uma organização possui a infraestrutura de rede certa e segura, é possível executar operações remotamente”, disse Sciammarella. “A infraestrutura de rede adequada torna uma empresa mais resiliente porque os indivíduos ainda podem acessar os dados necessários para manter as operações em execução mesmo trabalhando remotamente.”
Como e por onde começar
Como em qualquer transformação organizacional ou industrial, a tecnologia sozinha não resolverá os problemas emergentes. As ferramentas de monitoramento e colaboração remotas se tornaram comuns, mas, como sempre, o planejamento adequado é fundamental para adotar um modelo híbrido.
“Colaboração, videoconferência e plataformas/aplicativos de compartilhamento de conteúdo são algumas das áreas nas quais os fabricantes investiram ou estão procurando fazer investimentos para habilitar melhor os modelos de trabalho híbridos”, observou Paquin da IDC Manufacturing Insights. “A maioria dos fabricantes quase sempre precisará ter alguns funcionários no local. A manutenção/gestão de ativos é uma daquelas áreas onde este será o caso; precisa haver alguém girando uma chave inglesa. No futuro, os fabricantes poderão transferir mais disso para robôs, mas no momento a maturidade da tecnologia e os custos de investimento não tornam isso uma realidade para a maioria dos fabricantes.”
Os fabricantes que já haviam feito grandes investimentos em automação, coleta de dados e conectividade remota tinham a infraestrutura para apoiar essa mudança antes da pandemia, reconheceu Paquin. “Vimos que os fabricantes que tinham sistemas em nuvem, como ERP, eram mais adequados para o trabalho híbrido. A melhor abordagem é construir uma estratégia/roteiro em toda a organização, mas implementá-la em etapas menores. Comece com funções do tipo back office, pois seria necessário menos investimento para permitir o trabalho remoto para esses grupos. Preste atenção às políticas de trabalho remoto em vigor e como gerenciar funcionários remotos e incorpore as melhores práticas e lições aprendidas à medida que você continua a expandir para mais funções.”
Observando que o trabalhador médio gasta 240 horas por ano – 10 dias – esperando por informações, Neagoy, da Librestream, aconselhou que “se você é um operador no chão, uma boa estratégia é pegar o conhecimento de um especialista no assunto e incorporá-lo em instrução de trabalho, então você não está mais esperando por aquele especialista.”
Colocar a nova tecnologia nas mãos dos trabalhadores certos é essencial, continuou Neagoy. “Se você vai introduzir uma nova tecnologia, comece com o adepto da tecnologia. Nossos clientes normalmente veem uma distribuição bimodal da aceitação dos usuários:é radicalmente diferente entre pessoas com 10 anos de aposentadoria e pessoas com menos de 10 anos de carreira.”
Tenha certeza, disse ele, que “isso é algo que pode ser implementado em três meses. Não será realizado completamente em três meses, mas em três meses você poderá mover a agulha.”
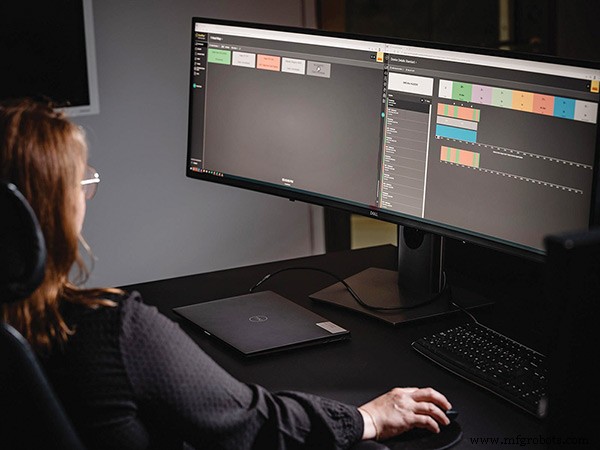
Assim como na abordagem de outras operações de fabricação, disse Sciammarella, da MxD, “as ações devem ser planejadas de forma cuidadosa e holística, tendo em mente as ferramentas básicas de melhoria contínua. É importante revisar primeiro o que você tem atualmente e por quê. O 'porquê' é crítico e pode parecer óbvio, mas nem sempre é esse o caso, especialmente se você tiver um longo histórico de fluxos de trabalho. Uma empresa desejará chegar a um ponto em que a equipe saiba quais dados e informações podem ser digitalizados - se ainda não o são - e como isso pode ser usado para oferecer suporte não apenas a horários de trabalho flexíveis, mas também a um processo de melhoria contínua que pode ser aproveitado remotamente para que a produção possa continuar a fazer produtos e otimizar o trabalho conforme necessário.”
Se uma organização iniciou a implementação de tecnologias de nuvem para dados de negócios, acrescentou, “poderia alavancar essas tecnologias de nuvem para coleta de dados operacionais e disponibilizar arquivos e informações prontamente para essa força de trabalho”.
Sucessos recentes
Para Fives Lund de Seattle, um produtor de maquinário altamente personalizado, flexibilidade no local de trabalho e ter as ferramentas certas para realizar tarefas críticas remotamente faz parte da cultura há anos.
Abraçar oportunidades para garantir que seus funcionários possam ser tão eficazes quanto possível onde quer que estejam “tem sido um processo contínuo desde que nos juntamos ao grupo Fives em 2015”, disse o CEO Casey McGarity. “Mesmo antes do COVID, esse era um processo contínuo e uma jornada – não um destino.”
Antes da pandemia, “nossa força de trabalho estava bastante concentrada em nossas instalações em Seattle – mas sempre tivemos engenheiros e técnicos que estavam em campo dando suporte a equipamentos”, acrescentou Jonathan Schwedhelm, engenheiro mecânico líder e diretor de engenharia. “Também projetamos alguns de nossos complexos equipamentos de automação com nossas empresas irmãs em todo o mundo.”
Depois veio a pandemia. E enquanto a Fives Lund estava no mesmo ritmo de outros grandes empregadores em sua região no que diz respeito às pessoas que trabalham em casa, “temos um ambiente bastante prático”, explicou Schwedhelm. “Nossos engenheiros e técnicos trabalham muito juntos para construir, testar e dar suporte aos nossos equipamentos.” Isso significava ser criativo para continuar projetando e entregando equipamentos e dando suporte aos clientes.
“No início, isso significava que alguns engenheiros levavam projetos e montagens menores para casa para trabalhar. Alguns de nossos engenheiros de controle instalaram hardware em suas casas para que pudessem programar as máquinas, mas isso realmente não é escalável.”
Foi aí que surgiu o Run MyVirtual Machine da Siemens. O software de simulação de operação da máquina “abre oportunidades para que os engenheiros de controle possam começar a construir os controles da máquina e testar a cinemática e a operação, bem como simular as máquinas em escala para certifique-se de que eles façam as coisas tão rápido quanto você acha que farão”, disse Schwedhelm.
Run MyVirtual Machine fez maravilhas em um projeto que começou no ano anterior à pandemia, continuou ele.
“Em 2019, começamos a trabalhar em um grande equipamento de automação e nosso cliente exigiu que usássemos controles CNC da Siemens. Estamos familiarizados com vários sistemas de controle NC diferentes, mas a máquina que estávamos construindo tinha uma cinemática realmente única e sabíamos que havia alguns grandes obstáculos técnicos que precisávamos eliminar antes do hardware estar disponível - e garantir poderíamos fazer isso sem precisar sentar na frente dos painéis de controle aqui em nossas instalações.”
Embora experiente com outros softwares de modelagem, ele continuou, “como este era um projeto da Siemens, ele nos permitiu pela primeira vez tirar proveito dessa ferramenta - usá-la no planejamento, usá-la para eliminar riscos e garantir que estamos tomar boas decisões ao longo do processo de design. E agora que a cadeia de suprimentos está se tornando um problema maior e os prazos de entrega para nossos componentes de controle podem ser desafiadores, isso nos permite continuar em movimento sem ficar completamente paralisado.”
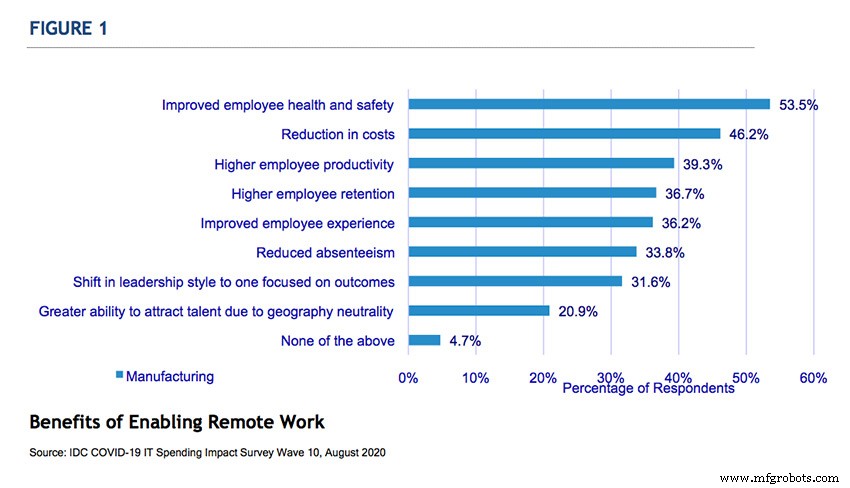
A cultura da Fives Lund é o fato de que “nossos engenheiros – mecânicos, elétricos e de software – muitas vezes trabalham lado a lado no chão e realmente construindo máquinas e solucionando problemas”, observou McGarity. “No mínimo, os engenheiros estão disponíveis para visitar o chão de fábrica à medida que se deparam com problemas” ou para auxiliar no planejamento, montagem ou teste. Na medida em que os engenheiros não estão “lá fora participando ativamente” das tarefas do chão de fábrica, “eles estão profundamente envolvidos no planejamento dessas coisas”.
Abordando a questão central da implementação de fluxos de trabalho híbridos na fabricação, McGarity observou que, embora a equipe da fábrica tivesse que permanecer no local, “era muito difícil e muito diferente para a Fives Lund não ter os engenheiros ali para ajudar nesse processo. Como muitas empresas, estávamos avaliando os riscos do COVID versus o risco da cultura e da eficiência decorrentes de uma equipe forte e coesa. As ferramentas que temos ajudam a manter essa cultura. Começamos com um grupo particularmente saudável e forte, mas esses músculos coletivos atrofiam um pouco, mesmo com boas ferramentas. Quanto mais eficazes forem as ferramentas, mais capazes seremos de manter nossa força por mais tempo. Mas também precisamos voltar e nos lembrar:'Somos mais fortes quando estamos fisicamente próximos'”.
Adaptação com fluxos de trabalho ajustados
As soluções híbridas também vêm naturalmente para a Sandvik Coromant, que não apenas fornece ferramentas que promovem oportunidades de trabalho remoto para seus clientes, mas também ajustou os fluxos de trabalho em suas próprias fábricas de ferramentas de corte.
“Ter a tecnologia instalada, no que diz respeito ao CAD/CAM, nos ajudou, mas obviamente ainda precisamos de pessoas aqui para operar o equipamento”, disse Richard Boyle, gerente da unidade de produção. “Não chegamos ao ponto de nossos equipamentos ficarem sem luz - ainda precisamos de nossos operadores aqui - mas isso nos deu uma boa oportunidade de avançar com os aspectos de engenharia de nosso chão de fábrica, com engenheiros de fabricação no escritório, em o chão de produção e também poder trabalhar em casa uma porcentagem do tempo.”
Quando a pandemia chegou, os designers da Sandvik também trabalhavam remotamente na maior parte do tempo, disse Boyle, indo de bicicleta para o chão de fábrica todas as semanas em um cronograma rotativo para fornecer suporte à produção e, ao mesmo tempo, limitar a exposição de qualquer pessoa. Enquanto isso, a empresa emprega o que chama de produção não tripulada, alternando operadores de máquinas “quando temos um equipamento que possui automação e funciona sem a presença de um operador”.
Boyle explicou que entre dois turnos de oito horas de operador de máquina, um intervalo de quatro horas está programado. Com duas células opostas uma à outra, esses horários podem ser escalonados para que apenas um operador esteja no local para atender a uma interrupção em cada célula. “Temos pessoas começando a trabalhar praticamente 24 horas por dia para garantir que tenhamos cobertura total.”
Ele também credita a parceria da Sandvik com a Microsoft e sua tecnologia de realidade mista HoloLens por facilitar o trabalho híbrido. “A maior parte da tecnologia que estamos utilizando na produção de nosso MES e nossos painéis – todos os dados disponíveis – vem de suas soluções. Tivemos uma interrupção aqui e ali, talvez por algumas horas, onde não conseguimos fazer logon em um serviço, mas são poucos e distantes entre si.”
Durante a pandemia, a Sandvik encomendou um novo equipamento que veio da Suécia quando todas as viagens de passageiros foram canceladas, lembrou Boyle. “Em vez de esperar até que a viagem fosse permitida novamente e o técnico da Suécia pudesse vir e terminar de instalá-lo, por meio do uso de tecnologia como HoloLens, conseguimos que nossa equipe de manutenção local trabalhasse diretamente com esse indivíduo, que podia ver diretamente através de seus observar o que eles estavam fazendo e certificar-se de que estávamos nos concentrando nas coisas certas para colocar esta máquina em operação e comissionada.”
Em última análise, disse Boyle, equilibrar fluxos de trabalho híbridos e tradicionais é “sempre uma luta. É algo que você tem que trabalhar. Com o híbrido, não dizemos que ninguém é 100% remoto. Se você pode tentar abrir um processo remoto que não está totalmente pronto para isso, às vezes é difícil recuperá-lo. Temos sido muito lentos e meticulosos na abertura de um processo para híbrido, garantindo que estamos capaz de sustentá-lo e modificá-lo rapidamente para que não falhe.”
Para os clientes, a Sandvik fornece produtos prontos para uso remoto, incluindo CoroPlus Machining Insights e CoroPlus Process Control, disse Jeff Rizzie, diretor de vendas de usinagem digital para as Américas.
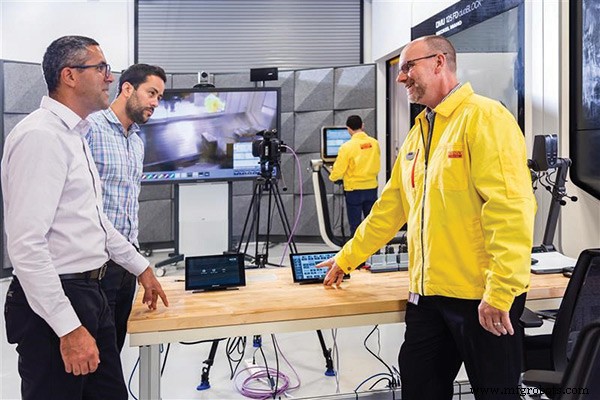
O Machining Insights é uma plataforma de software como serviço que monitora as condições da máquina, explicou Rizzie. “Podemos saber o que está acontecendo com uma determinada máquina-ferramenta apenas fazendo login em um site. Consigo entender os dados de utilização, quantas peças estou fabricando e observar a programação e vários pontos de dados vindos diretamente da máquina. Esses tipos de soluções são de grande valor, mesmo do ponto de vista operacional. Agora não preciso mais estar no chão de fábrica para entender o que está acontecendo na minha loja usando os dados da maneira certa.”
O CoroPlus Process Control vai um passo além na medição da saúde de todo um processo de fabricação, continuou Rizzie. “Ele pode realizar o controle adaptativo e substituir a máquina. Se detectar uma colisão ou uma ferramenta quebrada, pode desligar automaticamente a máquina. Ele pode emitir um comando para adquirir uma ferramenta irmã ou ferramenta redundante e reiniciar a fabricação. E pode ajudar na usinagem não tripulada – adiciona uma medida extra de segurança ao processo.”
Além disso, a Sandvik se esforça para “qualificar” seus funcionários para melhor equipá-los para oferecer suporte aos clientes remotamente, observou Annika Langeen, vice-presidente de marketing das Américas. “Equipamos nossos Sandvik Coromant Centers com a mais recente tecnologia para permitir suporte remoto em projetos de clientes e aulas de treinamento virtual ao vivo”, disse ela. “Com a mais recente tecnologia de áudio e vídeo, os clientes podem ver o que está acontecendo dentro e fora das máquinas em nossos Sandvik Coromant Centers e interagir com nossos especialistas em Yellow Coat em tempo real de qualquer local que desejarem. Por muitos anos, também oferecemos um extenso programa de e-learning para fornecer aos clientes, alunos e funcionários conhecimentos de corte de metal. Os participantes podem participar do programa de treinamento e obter a certificação de onde quiserem, a qualquer momento.”
Trabalho híbrido no futuro
A fabricação digital é frequentemente apontada como uma ferramenta de recrutamento e retenção de trabalhadores. Paquin da IDC concorda.
“O trabalho híbrido/remoto pode ampliar um grupo de candidatos para determinadas funções, e ouvimos consistentemente dos fabricantes que é a parcela mais jovem de sua força de trabalho que deseja mais flexibilidade e opções em torno dos modelos de trabalho”, observou ele. “Para uma indústria que luta para atrair novos talentos, não adotar modelos de trabalho híbridos pode tornar isso ainda mais desafiador.”
O grande desafio, observou Neagoy da Librestream, “é simplesmente entender onde um local de trabalho híbrido pode ser aplicado. Oitenta por cento da força de trabalho está em campo, portanto, criar forças de trabalho híbridas pode ser uma perspectiva esmagadora. A receita para o sucesso na implementação de uma força de trabalho híbrida é identificar objetivos de negócios muito claros. Tenha algo que seja quantificável e mensurável e comece pequeno. Se você tem diferentes áreas funcionais que são essencialmente duplicatas umas das outras, escolha uma e tenha sucesso com isso e aplique o que aprendeu em toda a organização.”
Observe também que “há uma estranha dualidade na forma como as pessoas se adaptam às forças de trabalho híbridas”, aconselhou Neagoy. “As pessoas com mais conhecimento sobre o negócio podem ser as menos adeptas tecnologicamente. Deixe os funcionários experientes saberem que as novas tecnologias híbridas não estão lá para ajudá-los – elas estão lá para ajudar os outros.”
Embora as plataformas e tecnologias que existem para tornar o híbrido uma realidade tenham feito a transição durante o COVID, o problema agora é “como integrá-las de uma maneira que seja eficaz para as necessidades de cada empresa”, observou Sciammarella. “As redes e conectividade certas – ou seja, 5G – estão presentes e como sua segurança pode ser garantida? Isso pode ser caro e exigirá uma reflexão cuidadosa sobre como incorporar essas ferramentas e plataformas da maneira mais econômica possível.
“A MxD sempre viu empresas habilitadas digitalmente se saírem melhor quando surgem crises. Com a pandemia não foi diferente”, continuou. “As organizações estão em caminhos diferentes para realizar a transformação digital – e aquelas que eram mais avançadas naturalmente poderiam fazer a transição facilmente para práticas híbridas em geral.”
Em última análise, apenas porque as ferramentas estão disponíveis para criar uma força de trabalho híbrida, isso depende realmente da cultura de uma determinada empresa e de sua disposição de “investir em mudanças significativas para que sua empresa não apenas sobreviva, mas também prospere. Honestamente, o maior desafio é a mudança de cultura. Na manufatura, as pessoas são criaturas de hábitos, e é difícil romper com isso. O outro grande desafio são os custos financeiros de se tornar digital para capacitar uma força de trabalho híbrida”, observou Sciammarella. “É extremamente difícil para as pequenas empresas avaliar o que poderia trazer mais retorno sobre o investimento quando há tanto por aí.”
Sistema de controle de automação
- Como as empresas aeroespaciais podem levar a fabricação de aditivos ao próximo nível com o MES?
- O que você pode fazer com uma máquina Roteador CNC?
- Com IA, lojas Big-Box podem enfrentar rivais E-Tail
- Router CNC à venda:o que você pode fazer com ele?
- 5 maneiras de automatizar o processo de fabricação para economizar dinheiro
- Como os robôs de software podem ajudar você a assumir o controle do 'novo normal'
- O que você pode fazer com uma máquina CNC?
- Conectividade na fabricação:como ela pode ser melhorada?
- A IA pode criar empregos na indústria?
- ABB diz que flexibilidade é necessária com a mudança para eletrificação de veículos