Helicóptero
Antecedentes
Os helicópteros são classificados como aeronaves de asa rotativa, e sua asa rotativa é comumente referida como o rotor principal ou simplesmente o rotor. Ao contrário das aeronaves de asa fixa mais comuns, como um biplano esportivo ou um avião comercial, o helicóptero é capaz de decolagem e aterrissagem verticais diretas; ele também pode pairar em uma posição fixa. Esses recursos o tornam ideal para uso onde o espaço é limitado ou onde a capacidade de pairar sobre uma área precisa é necessária. Atualmente, os helicópteros são usados para espanar as plantações, aplicar pesticidas acessar áreas remotas para trabalho ambiental, entregar suprimentos aos trabalhadores em plataformas marítimas de petróleo remotas, tirar fotos, filmar filmes, resgatar pessoas presas em locais inacessíveis, transportar vítimas de acidentes e apagar incêndios. Além disso, eles têm inúmeras aplicações militares e de inteligência.
Numerosas pessoas contribuíram para a concepção e desenvolvimento do helicóptero. A ideia parece ter sido de origem biônica, o que significa que derivou de uma tentativa de adaptar um fenômeno natural - neste caso, o fruto giratório e bifurcado da árvore de bordo - a um projeto mecânico. Os primeiros esforços para imitar os frutos de bordo produziram o whirligig, um brinquedo infantil popular na China e também na Europa medieval. Durante o século XV, Leonardo da Vinci, o renomado pintor, escultor, arquiteto e engenheiro italiano, desenhou uma máquina voadora que pode ter sido baseada no redemoinho. O próximo esboço sobrevivente de um helicóptero data do início do século XIX, quando o cientista britânico Sir George Cayley desenhou uma aeronave de dois rotores em seu caderno. Durante o início do século XX, o francês Paul Cornu conseguiu se erguer do solo por alguns segundos em um helicóptero. No entanto, Cornu foi restringido pelos mesmos problemas que continuariam a atormentar todos os primeiros projetistas por várias décadas:ninguém ainda havia desenvolvido um motor que pudesse gerar impulso vertical suficiente para levantar o helicóptero e qualquer carga significativa (incluindo passageiros) do solo .
Igor Sikorsky, um engenheiro russo, construiu seu primeiro helicóptero em 1909. Quando nem este protótipo nem seu sucessor de 1910 tiveram sucesso, Sikorsky decidiu que não poderia construir um helicóptero sem materiais mais sofisticados e dinheiro, então ele transferiu sua atenção para aeronaves. Durante a Primeira Guerra Mundial, o engenheiro húngaro Theodore von Karman construiu um helicóptero que, quando amarrado, era capaz de pairar por longos períodos. Vários anos depois, o espanhol Juan de la Cierva desenvolveu uma máquina que chamou de autogiro em resposta à tendência dos aviões convencionais de perder potência do motor e cair durante a aterrissagem. Se ele pudesse projetar uma aeronave em que a sustentação e o empuxo (velocidade para frente) fossem funções separadas, especulou Cierva, ele poderia contornar esse problema. O autogiro que ele inventou posteriormente incorporava características tanto do helicóptero quanto do avião, embora se parecesse mais com este último. O autogiro tinha um rotor que funcionava como um moinho de vento. Uma vez posto em movimento por taxiamento no solo, o rotor pode gerar sustentação suplementar; entretanto, o autogiro era movido principalmente por um motor de avião convencional. Para evitar problemas de pouso, o motor poderia ser desconectado e o autogiro parado suavemente pelo rotor, que aos poucos deixaria de girar conforme a máquina atingisse o solo. Populares nas décadas de 1920 e 1930, os autogiros deixaram de ser produzidos após o aprimoramento do helicóptero convencional.
O helicóptero foi finalmente aperfeiçoado por Igor Sikorsky. Avanços na teoria aerodinâmica e nos materiais de construção foram feitos desde o esforço inicial de Sikorsky e, em 1939, ele decolou do solo em seu primeiro helicóptero operacional. Dois anos depois, um design aprimorado permitiu que ele permanecesse no ar por uma hora e meia, estabelecendo um recorde mundial de vôo sustentado de helicóptero.
O helicóptero foi colocado para uso militar quase imediatamente após sua introdução. Embora não tenha sido utilizado extensivamente durante a Segunda Guerra Mundial, o terreno da selva da Coréia e do Vietnã levou ao uso generalizado do helicóptero durante ambas as guerras, e os refinamentos tecnológicos o tornaram uma ferramenta valiosa durante a Guerra do Golfo Pérsico também. Nos últimos anos, no entanto, a indústria privada provavelmente foi responsável pelo maior aumento no uso de helicópteros, já que muitas empresas começaram a transportar seus executivos por meio de helicópteros. Além disso, os serviços de transporte por helicóptero proliferaram, principalmente ao longo do corredor urbano do Nordeste americano. Ainda assim, entre os civis, o helicóptero continua mais conhecido por seus usos médicos, de resgate e socorro.
Design
A força de um helicóptero vem de um motor a pistão ou de uma turbina a gás (recentemente, a última predominou), que move o eixo do rotor, fazendo com que o rotor gire. Enquanto um avião padrão gera empuxo empurrando o ar para trás de sua asa à medida que avança, o rotor do helicóptero alcança a elevação empurrando o ar abaixo dele para baixo enquanto gira. A sustentação é proporcional à mudança no momento do ar (sua massa vezes sua velocidade):quanto maior o momento, maior a sustentação.
Os sistemas de rotor de helicóptero consistem de duas a seis pás conectadas a um cubo central. Normalmente longas e estreitas, as lâminas giram relativamente devagar, porque isso minimiza a quantidade de energia necessária para atingir e manter a elevação e também porque torna o controle do veículo mais fácil. Embora os helicópteros leves e de uso geral geralmente tenham um rotor principal de duas pás, as embarcações mais pesadas podem usar um design de quatro pás ou dois rotores principais separados para acomodar cargas pesadas.
Para pilotar um helicóptero, o piloto deve ajustar a inclinação das pás, que pode ser ajustada de três maneiras. No coletivo sistema, o passo de todas as pás acopladas ao rotor é idêntico; no cíclico sistema, o passo de cada pá é projetado para flutuar conforme o rotor gira, e o terceiro sistema usa uma combinação dos dois primeiros. Para mover o helicóptero em qualquer direção, o piloto movimenta a alavanca que ajusta o passo coletivo e / ou o manche que ajusta o passo cíclico; também pode ser necessário aumentar ou reduzir a velocidade.
Ao contrário dos aviões, que são projetados para minimizar o volume e as protuberâncias que sobrecarregariam a aeronave e impediriam o fluxo de ar ao seu redor, os helicópteros têm um arrasto inevitavelmente alto. Assim, os projetistas não utilizaram o tipo de trem de pouso retrátil familiar às pessoas que viram aviões decolando ou pousando - os ganhos aerodinâmicos de tal sistema seriam proporcionalmente insignificantes para um helicóptero. Em geral, o trem de pouso de helicópteros é muito mais simples do que o de aviões. Enquanto os últimos requerem pistas longas para reduzir a velocidade de avanço, os helicópteros precisam reduzir apenas a sustentação vertical, o que eles podem fazer pairando antes do pouso. Assim, eles nem precisam de amortecedores:seu trem de pouso geralmente é composto apenas de rodas ou patins, ou ambos.
Um problema associado às pás do rotor do helicóptero ocorre porque o fluxo de ar ao longo do comprimento de cada pá difere amplamente. Isso significa que a sustentação e o arrasto flutuam para cada pá ao longo do ciclo de rotação, exercendo assim uma influência instável sobre o helicóptero. Um problema relacionado ocorre porque, conforme o helicóptero se move para frente, a sustentação sob as pás que entram primeiro na corrente de ar é alta, mas abaixo das pás no lado oposto do rotor é baixa. O efeito líquido desses problemas é desestabilizar o helicóptero. Normalmente, o meio de compensar essas variações imprevisíveis de elevação e arrasto é fabricar pás flexíveis conectadas ao rotor por uma dobradiça. Este design permite que cada lâmina se desloque para cima ou para baixo, ajustando-se às mudanças na elevação e arrasto.
O torque, outro problema associado à física de uma asa em rotação, faz com que a fuselagem (cabine) do helicóptero gire na direção oposta do rotor, especialmente quando o helicóptero está se movendo em baixas velocidades ou pairando. Para compensar essa reação, muitos helicópteros usam um rotor de cauda, uma lâmina exposta ou um ventilador montado na extremidade da cauda normalmente vista nessas aeronaves. Outro meio de neutralizar o torque envolve a instalação de dois rotores, acoplados ao mesmo motor, mas girando em direções opostas, enquanto um terceiro, com design mais eficiente em termos de espaço, apresenta dois rotores que estão entrelaçados, algo como um batedor de ovos. Alternativas adicionais foram pesquisadas e pelo menos um projeto NOTAR (sem rotor de cauda) foi introduzido.
Matérias-primas
A fuselagem, ou estrutura fundamental, de um helicóptero pode ser feita de metal ou de materiais compostos orgânicos, ou alguma combinação dos dois. Os requisitos de desempenho mais elevados inclinarão o projetista a favorecer os compósitos com maior relação resistência-peso, geralmente epóxi (uma resina) reforçada com vidro, aramida (uma fibra de náilon forte e flexível) ou fibra de carbono. Normalmente, um componente composto consiste em muitas camadas de resinas impregnadas de fibra, unidas para formar um painel liso. Subestruturas tubulares e de chapa de metal são geralmente feitas de alumínio, embora aço inoxidável ou titânio às vezes são usados em áreas sujeitas a maior estresse ou calor. Para facilitar a dobra durante o processo de fabricação, o tubo estrutural é frequentemente preenchido com silicato de sódio fundido. As lâminas de asa rotativa de um helicóptero são geralmente feitas de resina reforçada com fibra, que pode ser colada com uma camada externa de folha de metal para proteger as bordas. O pára-brisa e as janelas do helicóptero são revestidos de policarbonato.
O processo de fabricação
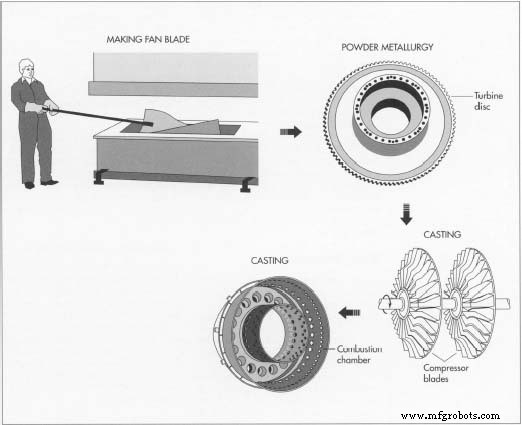
Em 1939, um emigrado russo para os Estados Unidos testou o que se tornaria um protótipo proeminente para helicópteros posteriores. Já um próspero fabricante de aeronaves em sua terra natal, Igor Sikorsky fugiu da revolução de 1917, atraído para os Estados Unidos pelas histórias de Thomas Edison e Henry Ford.
Sikorsky logo se tornou um fabricante de aeronaves de sucesso em sua terra natal. Mas seu sonho era decolagem vertical, voo de asa rotativa. Ele experimentou por mais de vinte anos e finalmente, em 1939, fez seu primeiro vôo em uma nave batizada de VS 300. Amarrado ao solo com cordas longas, sua nave voou a não mais que 15 metros do solo em seus primeiros voos. Mesmo assim, havia problemas:a nave voava para cima, para baixo e para os lados, mas não para a frente. No entanto, a tecnologia de helicópteros se desenvolveu tão rapidamente que alguns foram realmente colocados em uso pelas tropas dos EUA durante a Segunda Guerra Mundial.
O helicóptero contribuiu diretamente para pelo menos uma tecnologia de produção revolucionária. À medida que os helicópteros ficavam maiores e mais poderosos, os cálculos de precisão necessários para a engenharia das hélices, que tinham requisitos exigentes, aumentavam exponencialmente. Em 1947, John C. Parsons de Traverse City, Michigan, começou a procurar maneiras de acelerar a engenharia das lâminas produzidas por sua empresa. Parsons contatou a International Business Machine Corp. e pediu para experimentar um de seus novos computadores de escritório de estrutura principal. Em 1951, Parsons estava experimentando fazer com que os cálculos do computador realmente guiassem a máquina-ferramenta. Suas ideias foram desenvolvidas na indústria de máquinas-ferramenta de controle numérico computadorizado (CNC), que revolucionou os métodos de produção modernos.
William S. Pretzer
Estrutura da aeronave:preparando a tubulação
- 1 Cada parte tubular individual é cortada por uma máquina de corte de tubos que pode ser rapidamente configurada para produzir comprimentos diferentes e precisos e quantidades de lote específicas. Tubos que requerem dobras angulares são moldados no ângulo apropriado em uma máquina de dobra que utiliza ferramentas intercambiáveis para diâmetros e tamanhos diferentes. Para outras curvas que não sejam menores, os tubos são preenchidos com silicato de sódio fundido que endurece e elimina dobras, fazendo com que o tubo se curve como uma barra sólida. O chamado copo d'água é então removido colocando o tubo dobrado em água fervente, que derrete o material interno. A tubulação que deve ser curvada para combinar com os contornos da fuselagem é instalada em uma máquina formadora de estiramento, que estica o metal para uma forma contornada com precisão. Em seguida, os detalhes tubulares são entregues à oficina de máquinas, onde são mantidos em grampos para que suas extremidades possam ser usinadas no ângulo e forma exigidos. Os tubos são então rebarbados (um processo no qual quaisquer cristas ou aletas que permaneçam após a usinagem preliminar são desbastadas) e inspecionados quanto a rachaduras.
- 2 Reforços (placas de reforço ou suportes) e outros detalhes de reforço de metal são usinados a partir de chapa, ângulo ou perfil extrudado por fresamento, cisalhamento, cunhagem ou serragem. Alguns detalhes críticos ou complexos podem ser forjados ou fundidos. O último processo envolve a injeção de cera ou liga com baixo ponto de fusão em um molde ou matriz. Quando o molde é formado, ele é mergulhado no metal fundido tantas vezes quantas forem necessárias para atingir a espessura desejada. Quando a peça seca, ela é aquecida para que a cera ou liga derreta e possa ser derramada. Aquecido a uma temperatura mais alta para purificá-lo e colocado em uma caixa de molde onde é suportado por areia, o molde está pronto para transformar o metal fundido em peças de reforço. Após a remoção e resfriamento, essas peças são então usinadas por métodos padrão antes de serem rebarbadas novamente.
- 3 Os tubos são limpos quimicamente, encaixados em um acessório do subconjunto e soldados por MIG (gás inerte com arco de metal). Neste processo, um pequeno arame eletrodo é alimentado através de uma tocha de soldagem, e um gás inerte de proteção (geralmente argônio ou hélio) é passado através de um bico ao redor dele; os tubos são unidos pelo derretimento do fio. Após a soldagem, o subconjunto é aliviado de tensões - aquecido a uma temperatura baixa para que o metal possa recuperar qualquer elasticidade que tenha perdido durante o processo de modelagem. Finalmente, as soldas são inspecionadas quanto a falhas.
Formando detalhes de chapa metálica
- 4 A folha de metal, que constitui outras partes da fuselagem, é primeiro cortada em blocos (peças cortadas em um tamanho predeterminado na preparação para o trabalho subsequente) por jato de água abrasivo, matrizes de estampagem ou roteamento. Os blanks de alumínio são tratados termicamente para recozê-los (proporcionando-lhes uma estrutura uniforme e livre de deformações que aumentará sua maleabilidade). Os blanks são então refrigerados até serem colocados em matrizes onde serão prensados no formato adequado. Após a formação, os detalhes da folha de metal são envelhecidos até sua resistência total e cortados por roteamento para a forma e tamanho final.
- 5 As peças de chapa metálica são limpas antes de serem montadas por meio de rebitagem ou colagem com adesivo. As peças de alumínio e subconjuntos soldados podem ser anodizados (tratados para engrossar a película protetora de óxido na superfície do alumínio), o que aumenta a resistência à corrosão. Todas as peças de metal são quimicamente limpas e pintadas com primer, e a maioria recebe tinta de acabamento por pulverização com epóxi ou outro revestimento durável.
Fazendo os núcleos dos componentes compostos
- 6 Os núcleos, as partes centrais dos componentes do compósito, são feitos de Nomex (uma marca de aramida produzida pela Du Pont) ou alumínio "favo de mel", que é cortado no tamanho por serra de fita ou faca alternativa. Se necessário, os núcleos têm suas bordas aparadas e chanfradas por uma máquina-ferramenta semelhante a um cortador de pizza ou lâmina de fatiar carne. O material com o qual cada componente é construído a partir de seus núcleos (cada componente pode usar vários núcleos) é chamado de camada pré-impregnada. As camadas são camadas de fibras orientadas, geralmente epóxi ou poliimida, que foram impregnadas com resina. Seguindo as instruções escritas dos designers, os trabalhadores criam painéis de pele altamente contornados, colocando camadas individuais em ferramentas de molde de ligação e ensanduichando os núcleos entre as camadas adicionais conforme as instruções.
- 7 layups concluídos, como são chamadas as camadas de prepreg afixadas ao molde, são então transportadas para uma autoclave para cura. Uma autoclave é uma máquina que lamina plásticos expondo-os a vapor pressurizado, e "cura" é o endurecimento que ocorre quando as camadas de resina "cozinham" na autoclave.
- 8 Linhas de acabamento visíveis são moldadas nos painéis por linhas de marcação presentes nas ferramentas de molde de colagem. O excesso de material em torno das bordas é então removido com serrote de fita. Grandes painéis podem ser cortados por um jato de água abrasivo manipulado por um robô. Após a inspeção, os painéis aparados e outros detalhes compostos são limpos e pintados por métodos normais de pulverização. As superfícies devem ser bem vedadas com tinta para evitar a corrosão do metal ou absorção de água.
Confecção da fuselagem
- 9 Os dosséis ou pára-brisas e as janelas do habitáculo são geralmente feitos de folha de policarbonato. Painéis frontais
A maioria dos componentes cruciais em um helicóptero são feitos de metal e são formados usando os processos usuais de conformação de metal:cisalhamento, estampagem, forjamento, corte, fresamento e fundição de revestimento. O pára-brisa e as janelas de policarbonato são feitos colocando-se a folha sobre um molde, aquecendo-a e moldando-a com pressão de ar em um processo denominado "sopro livre", em que nenhuma ferramenta jamais toca a peça. Sujeito a colisão de pássaros ou outro impacto pode ser laminado de duas folhas para maior espessura. Todas essas peças são feitas colocando uma peça em bruto superdimensionada em um acessório, aquecendo-o e, em seguida, moldando-o para a curvatura necessária pelo uso de pressão de ar em um processo de sopro livre. Neste método, nenhuma superfície de ferramenta toca as superfícies ópticas para causar defeitos.
Instalação do motor, transmissão,
e rotores
- 10 Os motores de helicópteros modernos são do tipo turbina, e não do tipo pistão, e são adquiridos de um fornecedor de motores. O fabricante do helicóptero pode comprar ou produzir o conjunto de transmissão, que transfere energia para o conjunto do rotor. As caixas de transmissão são feitas de alumínio ou liga de magnésio.
- 11 Como acima, os conjuntos do rotor principal e de cauda são usinados a partir de metais de alta resistência especialmente selecionados, mas são produzidos por métodos típicos de oficina mecânica. As próprias lâminas do rotor são usinadas a partir de formas compostas de layup. As pás do rotor principal podem ter uma camada de folha de metal colada para proteger as bordas de ataque.
Sistemas e controles
- 12 Os chicotes elétricos são produzidos colocando os fios necessários em placas especiais que servem como gabaritos para definir o comprimento e o caminho para os conectores. Teares, ou capas de proteção tricotadas, são colocados nos feixes de fios e os conectores adquiridos são soldados no lugar manualmente. Os tubos hidráulicos podem ser cortados à mão no comprimento e moldados à mão por artesãos ou medidos, moldados e cortados por máquinas de dobrar tubos. As extremidades são alargadas e os tubos são inspecionados quanto à precisão dimensional e para garantir que não haja rachaduras. Bombas hidráulicas e atuadores, instrumentação e dispositivos elétricos são normalmente adquiridos de acordo com as especificações, em vez de produzidos pelo fabricante do helicóptero.
Montagem final
- 13 Peças acabadas e inspecionadas da fuselagem, incluindo chapas, tubulares e itens usinados e soldados, são entregues aos gabaritos de submontagem (acessórios que prendem as peças que estão sendo montadas). As peças centrais estão localizadas em cada gabarito e os detalhes associados são aparafusados no lugar ou, onde os rebites devem ser usados, perfurados com brocas pneumáticas para perfurar e escarear cada furo do rebite. For aerodynamic smoothness on sheet metal or composite skin panels, holes are countersunk so that the heads of flat-headed screws won't protrude. All holes are deburred and rivets applied. A sealant is often applied in each rivet hole as the rivet is inserted. For some situations, semi-automated machines may be used for moving from one hole location to the next, drilling, reaming, sealing, and installing the rivets under operator control.
- 14 After each subassembly is accepted by an inspector, it typically moves to another jig to be further combined with other small subassemblies and details such as brackets. Inspected "top level" subassemblies are then delivered to final assembly jigs, where the overall helicopter structure is integrated.
Upon completion of the structure, the propulsion components are added, and wiring and hydraulics are installed and tested. Canopy, windows, doors, instruments, and interior elements are then added to complete the vehicle. Finish-painting and trimming are completed at appropriate points during this process.
- 15 After all systems are inspected in final form, along with physical assemblies and appearance aspects, the complete documentation of materials, processes, inspection, and rework effort for each vehicle is checked and filed for reference. The helicopter propulsion system is tested, and the aircraft is flight-tested.
Controle de qualidade
Once tubular components have been formed, they are inspected for cracks. To find defects, workers treat the tubes with a fluorescent liquid penetrant that seeps into cracks and other surface flaws. After wiping off the excess fluid, they dust the coated tube with a fine powder that interacts with the penetrant to render defects visible. After the tubular components have been welded, they are inspected using X-ray and/or fluorescent penetrant methods to discover flaws. Upon completion, the contours of sheet metal details are checked against form templates and hand-worked as required to fit. After they have been autoclaved and trimmed, composite panels are ultrasonically inspected to identify any possible breaks in laminations or gas-filled voids that could lead to structural failure. Prior to installation, both the engine and the transmission subassemblies are carefully inspected, and special test equipment, custom-designed for each application, is used to examine the wiring systems. All of the other components are also tested before assembly, and the completed aircraft is flight-tested in addition to receiving an overall inspection.
O Futuro
Manufacturing processes and techniques will continue to change in response to the need to reduce costs and the introduction of new materials. Automation may further improve quality (and lower labor costs). Computers will become more important in improving designs, implementing design changes, and reducing the amount of paperwork created, used, and stored for each helicopter built. Furthermore, the use of robots to wind filament, wrap tape, and place fiber will permit fuselage structures to be made of fewer, more integrated pieces. In terms of materials, advanced, high-strength thermoplastic resins promise greater impact resistance and repairability than current thennosets such as epoxy and polyimide. Metallic composites such as aluminum reinforced with boron fiber, or magnesium reinforced with silicon carbide particles, also promise higher strength-to-weight ratios for critical components such as transmission cases while retaining the heat resistance advantage of metal over organic materials.
Processo de manufatura
- Meetup de tecnologia de veículos autônomos
- Como A3 está ajudando membros durante esta crise
- Programa de confiabilidade pode ser a diferença durante tempos apertados
- Equipe de manutenção de defesa homenageada durante o simpósio DoD
- A função da IoT na saúde durante a Covid-19
- Como promover a aceleração do crescimento dos negócios durante o COVID-19
- Dicas para mitigar interrupções durante o ano novo chinês
- Aumentando a eficiência de fabricação durante COVID-19
- Mitigação dos riscos de segurança cibernética durante uma crise
- Melhor máquina CNC para comprar durante a promoção de Natal