Processo Tempcore para a Produção de Barras de Reforço TMT
Processo Tempcore para a Produção de Barras de Reforço TMT
O processo Tempcore para a produção de barras de reforço (vergalhões) é um processo patenteado no qual a barra laminada a quente é intensamente temperada com água, imediatamente após a saída da barra da última bancada de laminação a quente do laminador e durante o resfriamento a ar subsequente, a A camada externa temperada é temperada pela dissipação do calor retido do núcleo.
O processo Tempcore é um dos processos termomecânicos que foi desenvolvido no início da década de 1970 pelo Centre de Rechaerche Metallurgiques (CRM), em Liège Bélgica, para produzir vergalhões soldáveis de alta resistência ao escoamento a partir de tarugos de aço macio sem prejudicar sua ductilidade e sem a adição de micro- elementos de liga.
Requisitos de propriedade de vergalhões
A resistência juntamente com a ductilidade, soldabilidade e conformabilidade são os requisitos de qualidade mais essenciais dos vergalhões. Assim, o limite de escoamento, juntamente com a resistência à tração, é o primeiro requisito para o aço de reforço nas normas e o grau de aço é classificado de acordo com o limite de escoamento mínimo especificado. O uso de vergalhões de aço de grau superior é econômico, pois é necessário menos aço para a mesma condição de carregamento e o custo total é reduzido. Quando a resistência ao escoamento garantida dos vergalhões é aumentada, o peso dos vergalhões a serem utilizados para uma determinada construção civil é reduzido e, consequentemente, os custos das armaduras são reduzidos. Essa redução na quantidade também reduz o custo de transporte, manuseio e fixação das barras durante a construção civil.
Em muitas técnicas de montagem de vergalhões no canteiro de obras, a soldagem dos vergalhões é uma necessidade para garantir a precisão dimensional necessária. Em muitos casos, as conexões amarradas não são fortes o suficiente, enquanto as emendas mecânicas nem sempre são aplicáveis. Por essas razões, a soldagem torna-se um requisito e uma quantidade considerável de soldagem em campo ocorre. Assim, a soldabilidade dos vergalhões também é uma grande preocupação. É bem conhecido que a soldabilidade dos vergalhões requer baixo teor de carbono (em torno de 0,25% ou mesmo em torno de 0,22% para o processo de resistência à aderência) e um baixo carbono equivalente (em torno de 0,45%) nos aços. Vários tipos de métodos de soldagem podem ser usados, como soldagem manual por arco de metal (MMAW), soldagem por arco de metal a gás (GMAW), soldagem por flash (FW) e soldagem por resistência (RW). Entre as várias técnicas de soldagem, a soldagem por sobreposição e a soldagem cruzada são as mais sensíveis à fissuração da zona afetada pelo calor devido ao baixo aporte de calor e à rápida dissipação de calor.
Outra propriedade importante é a dobrabilidade. Vergalhões com boa dobrabilidade possibilitam o uso de um projeto ideal e, portanto, trazem uma redução ainda maior dos custos. No caso da presença de reforços de conexão requer uma boa capacidade de reflexão. De fato, algumas normas prescrevem que os vergalhões devem ter sucesso nas operações de dobra e redobramento e isso em mandris de pequeno diâmetro (até 3 ou 4 vezes o diâmetro do vergalhão) ou em clima frio (- 20 graus C).
Anteriormente, o projeto de uma construção de concreto era baseado em um conceito de tensão, ou seja, na suposição de que as cargas que normalmente aparecem em serviço induzem apenas tensões elásticas no aço de reforço. Nesse caso, a segurança de uma construção pode ser definida em termos de uma relação de tensão, por exemplo. a razão entre a tensão de serviço e a tensão de escoamento do vergalhão (Fig. 1a). No entanto, estudos recentes levaram à conclusão de que um cálculo baseado em tensões do concreto armado não é suficiente porque, em alguns casos, deformações plásticas locais de uma determinada extensão têm que ser absorvidas sem ruptura das armaduras (por exemplo, quando ocorre compactação ). Nesses casos, a segurança de uma construção de concreto é expressa em termos de uma relação de deformação, por exemplo. a relação entre a deformação plástica local que pode ocorrer e o alongamento uniforme do vergalhão (Fig. 1b). Tal forma de projeto é agora adotada em muitos países e requer vergalhões dúcteis e um alongamento uniforme garantido de até 4% é prescrito para vergalhões como recebidos e para vergalhões soldados.
Fig 1 Conceitos de segurança para o uso de vergalhões durante a construção
Outro aspecto importante para a segurança das construções de concreto é evitar a perda de ductilidade após a reflexão. Isso novamente enfatiza a necessidade de uma boa capacidade de reflexão. Além disso, o uso de vergalhões de aço de alta resistência ao escoamento também pode permitir uma redução na largura das grandes vigas ou no tamanho dos pilares em edifícios altos, reduzindo assim o custo do concreto e do manuseio. A ductilidade adequada é necessária durante a fabricação por questões de segurança. Isso é particularmente importante para estruturas onde a possibilidade de terremotos faz parte da consideração do projeto. Do ponto de vista da fabricação, onde estão ocorrendo dobras e dobras de vergalhões, uma boa ductilidade é muito importante. A preocupação com a ductilidade é refletida em todas as normas, sendo normalmente especificados o diâmetro mínimo do mandril para curvatura de 180 graus e o alongamento total.
Outros requisitos incluem resistência à fadiga, propriedades de alta e baixa temperatura, propriedades de impacto, resistência à corrosão, mas estes geralmente não são especificados por vários padrões nacionais, embora a preocupação esteja aumentando.
Assim, pode-se ver que, dos requisitos dos vergalhões e do ponto de vista dos usuários, as propriedades importantes que os vergalhões devem ter são (i) alta resistência ao escoamento, (ii) boa soldabilidade, (iii) boa dobrabilidade e dobrabilidade, e (iv) ductilidade.
Processos de produção para vergalhões
Existem vários processos convencionais que podem ser utilizados para a produção de vergalhões soldáveis de alta resistência. Esses métodos podem ser classificados em duas categorias distintas (Fig. 2), conforme indicado abaixo.
Os vergalhões podem ser usados na condição de laminados após resfriamento lento ao ar. Para a produção desses vergalhões, o limite de escoamento é aumentado modificando a composição química, mas os teores de carbono e manganês devem ser mantidos baixos para evitar uma diminuição significativa na soldabilidade. Isso é feito por microligação, ou seja, adicionando quantidades apropriadas de elementos de microligação, como nióbio ou vanádio.
Os vergalhões podem ser produzidos colocando os vergalhões em um endurecimento por deformação após a laminação a quente, por exemplo, por deformação a frio. Para tais barras, a resistência ao escoamento pode ser aumentada aumentando a extensão do encruamento. Este método permite a produção de vergalhões soldáveis de alta resistência a partir de aços de baixo carbono e manganês. Exemplo de tais vergalhões são os vergalhões deformados torcidos a frio, popularmente conhecidos como vergalhões CTD.
Fig 2 Processos usados para produção de vergalhões soldáveis de alta resistência
Processo temporário
No laminador que produz vergalhões, os tarugos de aço são aquecidos a cerca de 1150°C no forno de reaquecimento e rolados através de uma sequência de tiras de laminação que reduzem progressivamente os tarugos ao tamanho e formato final das barras de reforço. Ao sair do último fio, um resfriamento controlado é aplicado de tal forma que a barra sofre transformações metalúrgicas de três estágios, conforme mostrado por um diagrama típico de transformação de resfriamento contínuo (CCT) na Fig 3. Conforme mostrado no diagrama CCT, o processo Tempcore depende da temperatura e do tempo.
Fig 3 Processo Tempcore em um diagrama CCT
Uma característica importante do processo Tempcore é sua grande versatilidade. As propriedades do vergalhão para um determinado diâmetro e composição de aço podem variar em grande parte escolhendo corretamente a duração do primeiro estágio (tempo de resfriamento) e o fluxo de água na instalação de têmpera (intensidade de resfriamento). Aplicado corretamente, o processo permite um aumento do limite de escoamento de 150 MPa para 230 MPa sem uma diminuição proibitiva e significativa da ductilidade. Graus de alta resistência (soldáveis) e ganho na resistência do aço são alcançados nos vergalhões de aço Tempcore sem qualquer adição de elementos de liga.
O processo Tempcore é capaz de produzir vergalhões de aço soldáveis de alta resistência com baixo teor de carbono e baixo teor de manganês sem a adição de elementos de microliga caros, como vanádio ou nióbio. Como a mesma composição do tarugo pode ser utilizada para diferentes graus e diâmetros de aço, uma racionalização significativa pode ser feita na planta. O tratamento de têmpera a água e auto-revenimento é aplicado diretamente na linha após a bancada de acabamento sem redução da velocidade de laminação ou perda de produtividade. Por uma combinação criteriosa de tratamento Tempcore e química de microligação, novos graus mais altos (resistência ao escoamento superior a 700 MPa e resistência à tração superior a 800 MPa) podem ser produzidos, especialmente para vergalhões de grande diâmetro (até 75 mm).
O processo Tempcore para a produção de vergalhões possui três etapas. Essas etapas do processo Tempcore são (i) têmpera da camada superficial, (ii) auto-revenimento da martensita e (iii) transformação do núcleo. O processo, devidamente aplicado, leva a um aumento da resistência ao escoamento dos vergalhões e esse aumento depende da intensidade de resfriamento. Esquemas do processo são mostrados na Fig 3.
Na primeira etapa, o vergalhão que sai da última bancada do laminador a quente passa por uma seção especial de resfriamento a água. A eficiência de resfriamento desta instalação é tal que a camada superficial do vergalhão é temperada em martensita enquanto o núcleo permanece austenítico. O tratamento de têmpera é interrompido quando uma determinada espessura de martensita foi formada sob a pele (parte externa da seção de vergalhões caindo abaixo da temperatura inicial de transformação de martensita Ms).
Na segunda etapa, o vergalhão sai da seção de resfriamento intenso e um gradiente de temperatura é estabelecido em sua seção transversal que faz com que o calor seja liberado do centro para a superfície. Este aumento da temperatura da camada superficial resulta no auto-revenimento da martensita. O nome Tempcore foi escolhido para ilustrar o fato de que a camada martensítica é temperada pelo calor deixado no CORE no final do estágio de têmpera.
Finalmente, na terceira etapa, durante o resfriamento lento do vergalhão no leito de resfriamento, o núcleo austenítico se transforma em ferrita e perlita ou em bainita, ferrita e perlita. Assim, um vergalhão de aço Tempcore é essencialmente um material compósito que consiste em uma camada externa dura disposta concentricamente e um núcleo macio com uma camada intermediária que é endurecida intermediária. Com teor de carbono relativamente baixo, os vergalhões de aço Tempcore proporcionam alta resistência, excelente ductilidade e soldabilidade, entre outras vantagens.
Fig 4 Esquema do processo Tempcore para produção de vergalhões
Existem dois modelos de processo que foram desenvolvidos para o processo Tempcore pelo CRM (Fig 5). Ambos estão continuamente sendo usados e aprimorados com os resultados de comissionamento das novas instalações. O primeiro modelo é usado para o projeto de instalações. Ele calcula o tempo de têmpera necessário para obter a classe para produzir o limite de escoamento mínimo (ou seja, limite de escoamento + margem de segurança) a partir (i) dos dados do vergalhão (diâmetro, temperatura de acabamento), (ii) pela seleção do diâmetro interno dos bicos de resfriamento, e (iii) a vazão específica de água. O segundo modelo relaciona as propriedades mecânicas com a composição química do aço e com o diâmetro do vergalhão.
A otimização de cada nova instalação do Tempcore leva em consideração as restrições do moinho, a linearidade do vergalhão e a controlabilidade do processo, e um melhor compromisso é alcançado entre (i) comprimento total do equipamento, (ii) vazão total de água de resfriamento (na pressão nominal de 1,2 MPa), e (iii) número de faixas de bicos de resfriamento necessários para cobrir toda a faixa de diâmetros de vergalhões.
Fig 5 Modelos para o projeto da instalação Tempcore
Outro ponto importante é reduzir o tempo e mão de obra necessários durante as mudanças de diâmetro ou para produzir produtos não Tempcore. Quando o espaço disponível é suficiente, é escolhida uma caixa coletora de água móvel lateralmente. Para linha de resfriamento longa, também é possível uma segmentação em duas ou três caixas d'água (cada uma individualmente móvel lateralmente) como foi feito em uma instalação recente para vergalhões de grande diâmetro (até 75 mm). É a instalação Tempcore mais longa de 54 m de comprimento (3 seções de 18 m cada). Está equipado com válvula remota de ligar/desligar em cada bocal de refrigeração. Quando o espaço disponível (largura, nível da linha de passagem) é a principal restrição, a caixa de coleta de água pode ser fixada com uma variedade de bicos de resfriamento.
A instalação Tempcore também pode ser projetada com 4 linhas de resfriamento paralelas para laminação de vergalhões de 8 mm a 12 mm de diâmetro. Esta linha possui uma caixa coletora de água compacta, equipada em cada vertente com controle individual de comprimento de resfriamento e vazão de água. Algumas outras características específicas também são utilizadas, como a proteção dos bicos de resfriamento não utilizados contra superaquecimento (principalmente na entrada da linha de resfriamento) por bicos externos de cone cheio, ou por meio de camisas de água ao longo dos tubos de resfriamento a jusante com água passando por dois bicos de cone cheio para resfriar o injetor. Um dispositivo anti-sucção é usado na frente do bocal de resfriamento (para diâmetros de vergalhões a partir de 25 mm) para evitar a sucção de ar pelos bocais e evitar a diminuição correspondente na eficiência de resfriamento na extremidade frontal dos tarugos.
Controle do processo Tempcore
O procedimento de controle é baseado nas relações limite de elasticidade/temperatura de revenimento, que são obtidas a partir dos resultados dos testes de comissionamento. Se houver variação da espessura da camada de martensita versus o limite de escoamento, então o poder de resfriamento das linhas de têmpera deve ser ajustado para obter o valor necessário para o limite de escoamento (YS do grau + margem de segurança).
Os pirômetros são o coração do controle do processo. A localização do pirômetro de têmpera é de primordial importância para obter medições o mais próximo possível da temperatura máxima de recuperação (máxima atingida pela superfície). O pirômetro localizado na entrada da caixa Tempcore também é importante para medir a variação da temperatura de acabamento ao longo do tarugo ou entre tarugos sucessivos. Uma variação de 50°C da temperatura de acabamento corresponde a uma variação de cerca de 8% do comprimento de resfriamento em igual vazão específica de água e, portanto, à variação das propriedades de tração após o tratamento.
As duas variáveis de controle fáceis de ajustar e poderosas no processo Tempcore são a taxa de fluxo de água e o tempo de têmpera (Fig 6). O controle da potência de refrigeração de uma linha Tempcore é realizado em duas etapas. Na primeira etapa (controle principal), o comprimento da linha de têmpera (ou seja, o número de bicos em uso) é ajustado. Para realizar um controle eficiente e manter uma boa homogeneidade do resfriamento, os bicos a serem desligados são os de montante. Na segunda etapa (ajuste fino), a vazão de água é ajustada atuando na válvula moduladora principal.
Fig 6 Controle on-line do processo Tempcore
O tempo de resfriamento e o tempo de têmpera estão ligados pela velocidade de laminação na bancada de acabamento. Esta velocidade deve ser mantida constante ao longo do tarugo durante o seu cruzamento com o equipamento de têmpera, e mais particularmente quando a cauda do tarugo está saindo da bancada de acabamento. Isso é assumido pelo pinch-roll localizado entre a saída da caixa Tempcore e o cisalhamento divisor. Sem usar este pinch-roll, quando a cauda sai do suporte de acabamento, pequenos diâmetros de vergalhões são desacelerados pela água enquanto os maiores diâmetros são acelerados.
Para um determinado diâmetro, os parâmetros de entrada (comprimento de resfriamento, vazão de água, temperatura de acabamento e composição química do aço) influenciam o parâmetro de saída do processo (temperatura de revenimento, limite de escoamento, resistência à tração e relação TS/YS ). Essa influência é mostrada na Figura 7.
Fig 7 Influência dos parâmetros de entrada nos parâmetros de saída
Uso adequado da instalação do Tempcore
Para obter um tratamento homogêneo, a intensidade do resfriamento (dada pela vazão de água por metro de linha) deve ser alta o suficiente para obter um anel externo de martensita completo e regular, constante ao longo do tarugo. A boa retilinidade dos vergalhões é obtida com o tratamento homogêneo Tempcore. Se o anel de martensita estiver aberto, barras onduladas são observadas no leito de resfriamento. Alguns dos pontos importantes que não devem ser feitos para o uso adequado da instalação do Tempcore são apresentados abaixo.
- Quando vergalhões de diâmetro muito pequeno são tratados através de um bocal de resfriamento muito grande, então o coeficiente de enchimento F é muito baixo. Isso leva a um anel de martensita aberto. Este fenômeno também é observado quando os bicos de resfriamento apresentam um desgaste excessivo, muitas vezes devido ao desalinhamento desses bicos de resfriamento.
- Ao usar todo o comprimento de resfriamento disponível com baixa vazão de água por metro, a intensidade de resfriamento é muito baixa.
- O método anterior é mais impressionante quando o comprimento de resfriamento projetado é mais que o dobro do necessário.
- Usar um bocal de resfriamento ativo sempre na entrada da linha de resfriamento, seguido por alguns bocais de resfriamento próximos e, finalmente, um determinado comprimento de resfriamento ativo até o stripper é útil. Em seguida, a taxa de resfriamento é interrompida e se torna muito baixa para obter uma camada uniforme de martensita.
- O método errado anterior, se usado frequentemente para proteger os bicos de resfriamento fechados do superaquecimento no caso da barra quente (cerca de 1000 ° C) na entrada, leva a vazamentos de água. Portanto, um projeto correto deve existir para apresentar uma proteção séria desses bicos de resfriamento para evitar a queima das gaxetas.
- O entupimento parcial ou total de alguns bicos de resfriamento pode causar resfriamento irregular ao redor do produto.
- O entupimento parcial ou total dos decapantes pode causar resfriamento excessivo do vergalhão porque o resfriamento não é interrompido na saída da instalação. A água nas guias a jusante também pode afetar a detecção da fotocélula que aciona o pinch-roll ou o cisalhamento.
- A localização incorreta do pirômetro de têmpera pode resultar em falta de visibilidade para controlar o processo.
- Caso não haja manutenção do pirômetro (proteção eletrônica por resfriamento, limpeza periódica da lente, verificação periódica na frente de um forno de corpo negro), isso causa um desvio de temperatura e, em seguida, os vergalhões produzidos são rejeitados.
- Se não houver rolagem de pinça na saída da linha de têmpera ou se houver configuração incorreta de pinçamento/velocidade, isso levará a grandes variações de propriedades mecânicas ao longo do comprimento do tarugo.
Propriedades características do vergalhão de aço Tempcore
Várias propriedades características do vergalhão de aço Tempcore são descritas abaixo.
Tipo de aço – Os aços para os vergalhões Tempcore são basicamente aços lisos de baixo carbono especificados para limite de escoamento, ductilidade, carbono ou carbono equivalente e relação rendimento/tração. O teor máximo e mínimo de carbono especificado visa garantir a soldabilidade e temperabilidade. Com teor de carbono muito baixo, a temperabilidade do aço geralmente não é suficiente e, portanto, uma têmpera mais severa é necessária, o que afeta o projeto do laminador, por exemplo, a velocidade do laminador, bem como o comprimento e a eficiência da câmara de resfriamento. O aço carbono com teor de carbono na faixa de 0,13% a 0,24% e o carbono equivalente (CE) inferior a 0,45% provou ser o melhor equilíbrio para satisfazer as considerações acima.
Fases metalúrgicas e microestrutura – A martensita temperada na forma de pacotes de placas finas com morfologia martensítica caracteriza a camada endurecida. Uma mistura de bainita e ferrita poligonal está na camada intermediária endurecida e ferrita poligonal e perlita se desenvolve no núcleo.
A microestrutura geralmente é boa devido a um resfriamento relativamente rápido no núcleo e devido ao tratamento termo-mecânico envolvido no processo Tempcore, por exemplo, grãos de ferrita poligonal na região do núcleo podem ser tão pequenos quanto 8 micrômetros de diâmetro e até 3 micrômetros de diâmetro. diâmetro quando a temperatura de têmpera mais baixa é usada. No entanto, conglomerado grosseiro de pseudo-eutetóide e ferrita de Widmanstatten no núcleo também são possíveis resultados do processo. A microestrutura do vergalhão de aço Tempcore é mostrada na Fig 8.
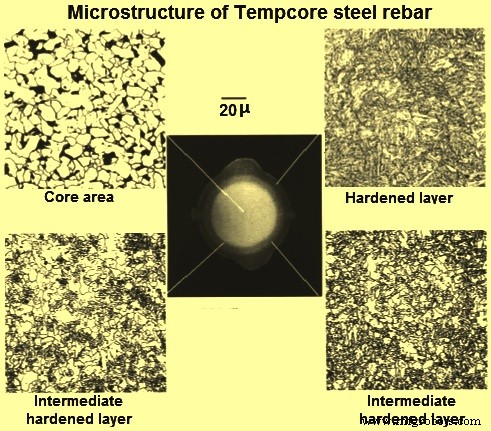
Fig 8 Microestrutura do vergalhão de aço Tempcore
Às vezes, a ferrita de Widmanstatten é formada devido à temperatura de equalização mais alta. É possível que a alta temperatura de acabamento e talvez também a deformação de laminação insuficiente sejam as principais razões para a formação desse tipo de microestrutura. Alta temperatura de acabamento e deformação de laminação insuficiente resulta em grandes grãos austeníticos no final da laminação e, assim, martensita e bainita grosseiras se desenvolvem na camada endurecida e na camada endurecida intermediária durante a têmpera subsequente. Grande tamanho de grão de austenita no núcleo evita o impacto da ferrita de contorno de grão, permitindo assim que a ferrita de Widmanstatten cresça.
A seção transversal gravada típica mostrando as três regiões metalúrgicas e microestruturas típicas e a homogeneidade da microestrutura do vergalhão de aço Tempcore são mostradas na Fig 9.
Fig 9 Microestrutura e a homogeneidade da microestrutura do vergalhão de aço Tempcore
Efeitos dos parâmetros do processo e composição do aço -Os parâmetros do processo e as composições do aço influenciam nas propriedades finais. Normalmente, se a camada de martensita for mais espessa, o calor retido é menor e, portanto, o revenimento é mais modesto, de modo que o vergalhão apresenta maior resistência ao escoamento e menor alongamento. Maior tempo de têmpera, menor temperatura de acabamento e maior intensidade de têmpera resultam em uma camada martensítica mais espessa e menor temperatura de revenimento. Maior teor de carbono e manganês aumenta a temperabilidade do aço e, portanto, mais martensita é formada. Além disso, a resistência da martensita temperada aumenta à medida que o teor de carbono aumenta.
Os modelos da Fig. 5 descrevem a relação entre o limite de escoamento e todos os parâmetros que influenciam. O modelo foi originalmente usado para o projeto de instalações. Embora a temperatura de revenimento não apareça diretamente neste modelo, a temperatura de acabamento, o tempo de têmpera, o diâmetro da barra e a vazão de água estão fortemente relacionados a ela. O alongamento de vergalhões de aço Tempcore tem uma correspondência virtualmente linear com o limite de escoamento.
Propriedades de tração – O processo Tempcore pode aumentar a tensão de escoamento para uma determinada composição de 150 MPa a 200 MPa sem perder muito alongamento. As propriedades de tração das barras dependem dos parâmetros do processo e da composição do aço. A faixa de resistência ao escoamento típica do vergalhão de aço Tempcore está entre 415 MPa a 550 MPa e o alongamento em um comprimento de referência 5d é de 30% a 25% na mesma ordem. As características da curva de tensão deformação típica mostram (i) o módulo de elasticidade é de 200.000 MPa, (ii) a barra tem um limite de escoamento marcado e um tipo de escoamento Luders e, portanto, a tensão de prova de 0,01% coincide com a tensão de prova de 0,2%, (iii) a a relação entre tensão de escoamento e resistência à tração é de cerca de 0,85, e (iv) a barra tem grande alongamento (25% a 30%), grande deformação de Luders e grande deformação uniforme.
O vergalhão de aço Tempcore tem duas características principais quando as propriedades de tração são comparadas com as das barras de aço convencionais. Essas características são (i) maior razão entre limite de escoamento e resistência à tração, 0,85 versus 0,65 no caso de barra convencional, e (ii) maior alongamento, 25% versus 4,5% a 22% no caso de barra de aço convencional.
Formabilidade – Outras propriedades notáveis do vergalhão de aço Tempcore é que ele possui excelentes propriedades de flexão e reflexão. Apesar da camada externa endurecida, o diâmetro mínimo da dobra para uma dobra simples de 180 graus é especificado como 1d para barras de 12 mm a 28 mm de diâmetro e 2d para barras de 32 mm e 36 mm de diâmetro.
Alguns dos vergalhões Tempcore (20 mm e 28 mm de diâmetro) podem até ser dobrados sem mandril. As barras também podem suportar todos os testes de flexão e reflexão após o envelhecimento, atendendo aos requisitos da norma. Além disso, a operação de dobra requer menos energia quando comparada com outros tipos de vergalhões devido à baixa relação resistência à tração para resistência ao escoamento. Estima-se que 10% a 20% de energia seja economizada na flexão. A comparação das propriedades de flexão de vergalhões Tempcore com barras de aço convencionais é fornecida na Tab 1.
Guia 1 Comparação das propriedades de flexão de vergalhões de aço Tempcore com barras de aço convencionais | |||
Teste de dobra | Valores D típicos | ||
Aços convencionais (CE =0,61%) | Vergalhão de aço Tempcore (CE =0,30%) | ||
1 | 180 graus de flexão | 3 | 0,5 |
2 | 90 graus de flexão e dobra após o envelhecimento | 6 | 3.2 |
3 | 90 graus de flexão após soldagem elétrica de topo | 15 | 4 |
4 | 90 graus de flexão após soldagem cruzada elétrica | Maior que 20 | 7 |
Observação:a dobrabilidade é expressa em termos de diâmetro de dobra mínimo D. (D é a razão entre o diâmetro de dobra mínimo possível e o diâmetro do vergalhão |
Soldabilidade – A soldabilidade do aço é muito sensível à composição química, principalmente ao teor de carbono e carbono equivalente (CE). Duas fórmulas populares são usadas, uma é seguida pelo International Institute for Welding (IIW) e a outra é dada por Ito e Besseyo, cobrindo as faixas alta e baixa de carbono, respectivamente.
A fórmula IIW é CE =C + (Mn + Si)/6 + (Cr + Mo + V)/5 + (Cu + Ni)/15 para carbono superior a 0,18%, enquanto a fórmula de Ito e Besseyo é CE =C + Si/30 + (Mn + Cu + Cr)/20 + Ni/60 + Mo/15 + V/10 + 5B para carbono inferior a 0,18%. A fórmula equivalente de carbono IIW mostra menos tolerância a elementos de liga de substituição do que a equação de Ito-Besseyo. Para a soldabilidade de vergalhões de aço, normalmente é utilizada a fórmula IIW ou fórmula IIW simplificada (CE =C + Mn/6) devido ao teor de carbono.
Com a fórmula IIW, quando CE é inferior a 0,45% o aço é considerado soldável com técnicas modernas. O CE dos vergalhões de aço Tempcore está bem abaixo do valor crítico de 0,45% e, portanto, novamente é superior a outros tipos de vergalhões.
A excelente soldabilidade dos vergalhões de aço Tempcore é bem demonstrada pelo teste de dobra em uma solda cruzada (Fig. 10). Não há sinal de trincas na ZTA na solda de uma barra de 20 mm de diâmetro quando ela é dobrada em um ângulo de 180 graus em um mandril 3d. Os vergalhões de aço Tempcore em baixa temperatura e/ou em estado úmido apresentam notável soldabilidade. Não é necessário pré-aquecimento e pós-aquecimento.
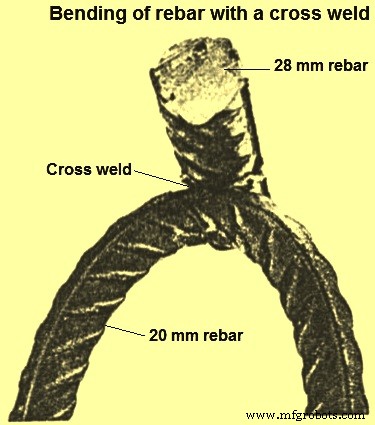
Fig 10 Dobragem do vergalhão Tempcore com uma solda cruzada
A excelente soldabilidade também é demonstrada pelas propriedades de tração obtidas após a soldagem. Na solda de topo nivelada, geralmente não é observada diminuição na resistência ao escoamento com a fratura localizada fora da solda. Além disso, é visto que sob diferentes processos de soldagem e soldagem, não ocorrem trincas na solda.
Outras propriedades – Além da alta resistência à tração, excelente ductilidade e notável soldabilidade, os vergalhões de aço Tempcore apresentam boa tenacidade a baixas temperaturas, menor sensibilidade a danos na superfície, e a resistência à fadiga e sensibilidade ao calor também são muito competitivas. Foi demonstrado que a -60°C um vergalhão de 20 mm de diâmetro com um corte de 1 mm de profundidade absorveu 190 calorias no teste de queda de peso sem quebrar. Testes de peso de queda em vergalhões de aço Tempcore danificados por arco de 12 mm, 16 mm e 20 mm de diâmetro mostram que não há fratura a -75 graus C. Da mesma forma, barras danificadas por entalhe e envelhecidas por deformação sobrevivem no teste de peso de queda a -60 graus C.
Um número limitado de testes de fadiga foi realizado nos vergalhões de aço Tempcore. Esses testes indicam que as propriedades de fadiga dos vergalhões de aço Tempcore atendem aos requisitos das normas. Um teste de fadiga realizado em vergalhões de aço Tempcore de 12 mm de diâmetro mostrou propriedades de fadiga superiores em relação às barras trabalhadas a frio. Também foram realizadas investigações sobre as propriedades de fadiga dos vergalhões de aço Tempcore com interesse nos efeitos da galvanização. Todos os resultados dos testes sugeriram que a resistência à fadiga dos vergalhões de aço Tempcore é tão boa quanto a de outros tipos de vergalhões de aço com limite de escoamento equivalente.
As propriedades de resistência ao calor dos vergalhões de aço Tempcore são importantes devido à possibilidade de danos causados pelo fogo. Esta resistência foi avaliada de duas maneiras, nomeadamente (i) perda de resistência à tração à temperatura ambiente após aplicação de calor anterior e (ii) perda de resistência à tração a temperatura elevada. Foi demonstrado que após o aquecimento em condições de laboratório a temperaturas entre 250°C e 900°C por meia hora, a resistência à tração à temperatura ambiente aumenta ligeiramente com o pré-aquecimento até 500°C e ocorre uma queda significativa acima dessa temperatura. Esta propriedade é tão boa quanto os vergalhões torcidos a frio e melhor do que as mostradas por algumas barras laminadas a quente. Vergalhões trabalhados a frio começam a perder resistência em 300 graus C a 400 graus C. As barras de aço laminadas a quente perdem resistência considerável a partir de 350 graus C e os vergalhões de aço microligado de baixo carbono laminados a quente começam a mostrar perda de resistência a partir de 600 graus C . Tensile strength of Tempcore steel rebars at elevated temperature is similar to cold worked and micro-alloyed rebars with a 20 % and 40 % reduction in yield strength at 300 deg C and 500 deg C respectively.
Processo de manufatura
- Barras de reforço temperadas e temperadas
- Processo Finex para Produção de Ferro Líquido
- Processo CONARC para Siderurgia
- Processo de Laminação para Aço
- Entendendo o processo de produção de matrizes, punções e lâminas para máquinas de punção e cisalhamento
- Entendendo o processo de soldagem por fricção
- 11 tipos diferentes de processo de soldagem com auxílio de diagrama
- Entendendo o processo de soldagem a gás
- Preparação para os protótipos para o processo de fabricação de produção
- Protótipos para Manufatura de Produção:O Processo