FRACAS:O segredo para melhorar a confiabilidade dos ativos
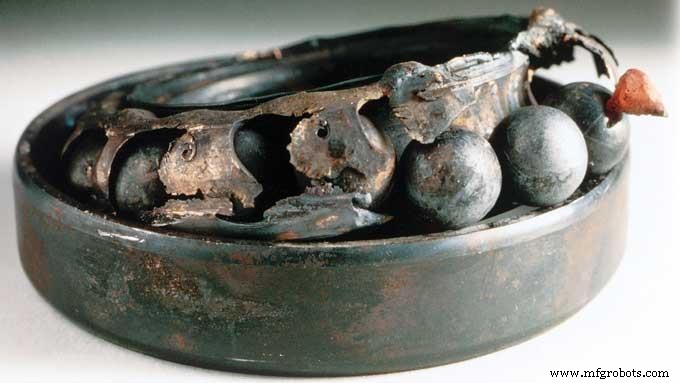
Em sua essência, a engenharia de confiabilidade trata de prever e prevenir falhas. Ao listar todas as maneiras pelas quais um sistema pode falhar, é possível resolver todas as maneiras pelas quais a falha pode ser detectada, atrasada ou interrompida antes mesmo de começar de verdade.
Sistema de relatório de falhas, análise e ação corretiva (FRACAS) é um método organizado de classificação através dos possíveis meios de falha do ativo e trabalhando de volta para todas as possíveis causas raiz. O produto final atua como um mapa de todas as maneiras pelas quais as coisas podem falhar, permitindo que um plano seja traçado para corrigir os problemas à medida que surgem e para eliminar os problemas crônicos no ponto de início.
O processo FRACAS deve abranger uma compreensão da criticidade do componente em todo o sistema e deve fazer uso de planejadores, mantenedores e operadores experientes para listar todas as inúmeras maneiras em que uma máquina falha.
Falha
A falha é melhor definida como qualquer estado operacional diferente do ideal. A maioria pensaria em falha como um estado de total inoperabilidade, mas operar em um estado degradado deve ser considerado uma falha da mesma forma. Estive recentemente em uma fábrica onde uma máquina havia sido refeita para operar a uma velocidade maior do que a projetada originalmente. Os operadores e mantenedores naquela área específica da planta consideraram um grande sucesso fazer com que seu sistema funcionasse tão bem, mas logo abaixo a alimentação excessiva não foi contabilizada e o produto estava derramando no próximo bombeamento ponto, criando uma grande pilha de resíduos. Então, o fracasso pode ser algo que funciona melhor do que deveria, bem como funciona pior.
A melhor maneira de proceder é listar todas as maneiras pelas quais uma máquina pode falhar, dividindo-a em subcomponentes menores que seriam trabalhados ou substituídos como parte do reparo. O nível de subcomponente pode ir até porcas e parafusos ou para equipamentos “prontos para uso” que podem ser facilmente substituídos, como um pequeno motor ou sensor. É muito útil ter acesso ao programa de estoque de materiais que seu site usa.
Isso já pode estar vinculado ao CMMS em uso ou pode ser um sistema distinto. Usar o programa de estoque de material será útil novamente mais tarde, durante a seção de ação corretiva, ao determinar quantas peças sobressalentes e consumíveis devem ser mantidas à mão.
Relatórios
Outra palavra que caberia bem aqui seria registrar. A frase de efeito do meu primeiro gerente de manutenção foi "você tem que anotar". É importante registrar tudo em um método estruturado e organizado. Existem muitas opções de software que podem ser adquiridas para ajudar nesta área, mas para uma planta ou sistema menor, considere o uso de Projetos ou uma planilha. Ter uma cascata estruturada de subcomponentes e tipos de falha é importante porque ocorrerão padrões e métodos de repetição de falha. Teoricamente, há infinitas maneiras de algo falhar, mas na prática você encontrará muitos deles aparecendo continuamente.
Outro método de relatório é usar um mapa de causa para cada sistema. Esta é uma abordagem mais gráfica e pode ser mais difícil de capturar eletronicamente sem alguma experiência nesse processo, mas em muitos casos permite uma compreensão mais fácil do que está acontecendo por outras pessoas fora do processo FRACAS. Uma versão simples seria um desenho básico ou imagem do sistema ou máquina em questão, com caixas de texto em árvore a partir dos pontos de falha. Essas caixas podem posteriormente ramificar-se para outras causas ou efeitos, criando uma espécie de nuvem de modos de falha em torno do equipamento intermediário.
Análise
Ter todos os métodos de falha listados de forma organizada agora permite que uma equipe de especialistas no assunto analise e observe as tendências. Ter um grupo experiente revisando os dados permite que uma boa quantidade de história entre em jogo também. Cada planta tem pelo menos uma máquina com um histórico estabelecido de quebras e ter uma equipe de pessoas mais familiarizadas com esses tipos de incidentes é vital para uma fase de análise bem-sucedida.
Com isso, também é importante distinguir entre falhas crônicas e eventos únicos. Pode haver uma tendência de se concentrar em eventos notáveis ou particularmente catastróficos e tentar evitar que o mesmo conjunto específico de circunstâncias aconteça novamente. Embora seja importante considerar todas as possibilidades, às vezes o fracasso material é uma ocorrência tão bizarra que não há lição prática a ser aprendida.
Paralelamente à análise de falhas, está a realização de uma avaliação de criticidade. Quando combinada com a cascata estruturada de equipamentos, subcomponentes e modos de falha, uma avaliação de criticidade ajudará a determinar o quão detalhada a equipe de análise deve ser na atribuição de ações corretivas. A criticidade deve ser definida por uma combinação de preço para reparar ou substituir, custo de mão de obra para reparar ou substituir e o efeito do tempo de inatividade no sistema ou planta como um todo.
No mundo lean / Six Sigma, tem havido um forte foco na redução do estoque e nas entregas just-in-time de produtos ou materiais para economizar nos custos de armazenamento. Aplicar uma análise de criticidade ao seu sistema permitirá que você veja quais máquinas ou componentes precisam de reposições sobressalentes na prateleira e quais podem ser solicitados no momento em que acontecem. Isso também ajuda a decidir por quanto tempo uma máquina com falha pode operar nesse estado.
Considere uma máquina que exigiria o desligamento de todo o sistema, mas poderia ser consertada em dois dias com uma peça já disponível em vez de operar esse mesmo sistema a 90 por cento até o final do mês, enquanto espera por uma máquina de substituição para chegar que pode ser trocado instantaneamente. Eficiência de noventa por cento parece ser o caminho a percorrer, mas ter o uso total do sistema por 28/30 dias é mais de 93 por cento, um aumento não insignificante na produção da planta naquele período de tempo. Uma avaliação de criticidade completa ajudará a listar esses tipos de ações a serem ponderadas em relação à lista de eventuais ações corretivas.
Ação corretiva
A ação corretiva mais simples a ser listada para cada instância de falha é substituir o componente com falha. Um pouco mais complexo é consertá-lo. Liste livremente todas as ações corretivas possíveis para cada falha, mas também adicione uma quantia em dólares que considere a peça e a mão de obra necessária para reparar ou substituir. As ordens de serviço pré-escritas podem ser escritas para qualquer caso e armazenadas no CMMS para uso no caso de ocorrer uma falha.
Uma possível ação corretiva que pode ser listada pode ser "executado até a falha". Não existe uma solução única para todos os casos para prevenir ou corrigir todos os modos de falha, mas a aplicação do princípio de Pareto produzirá uma lista de atividades e ações facilmente gerenciada que pode ser aplicada rapidamente. Em outras palavras, provavelmente descobriremos que a maioria dos problemas crônicos que afetam um sistema provém de uma lista de falhas menor e gerenciável e pode ser corrigida por uma lista gerenciável de ações de acompanhamento.
Sistema
A parte mais importante do FRACAS é que ele é mantido como um sistema. A repetibilidade desse processo é vital para adicionar sistemas adicionais, novos equipamentos, tecnologias emergentes e até mesmo novo pessoal na planta. Tenha um plano para revisar a eficácia das ações corretivas e trazer novos membros para o grupo de análise para ajudar a iluminar qualquer área da planta que não pareça mostrar uma melhora acentuada no tempo de atividade.
Outra parte sistemática desse processo consiste em educar outros membros da planta. Isso aumenta a propriedade do processo para o pessoal não envolvido na análise inicial e pode ser um evento de construção de cultura. Treinar outras pessoas no início do processo os ajuda a ver que o processo é imparcial e aberto para incorporar suas ideias também.
A falha é aleatória, mas na maioria dos casos pode ser detectada, adiada ou totalmente evitada com uma abordagem sistemática. A coleta de dados e a revisão por pessoal experiente da fábrica são essenciais, assim como calcular uma quantia em dinheiro para cada ação ou resultado possível para ajudar a orientar o eventual processo corretivo. Aplicar esses métodos metodicamente ao longo do tempo, bem como ensinar os princípios básicos do processo a outros membros da equipe, ajudará a melhorar a cultura e a aumentar a confiabilidade geral dos ativos. Lembre-se, você quer ter um FRACAS, não uma briga.
Manutenção e reparo de equipamentos
- O caso para manutenção móvel:Fiix para pelo podcast Asset Reliability @ Work
- Qual é a função do engenheiro de confiabilidade?
- A chave nº 1 para o sucesso da confiabilidade
- RH:O elo que faltava para a confiabilidade
- O lado não técnico da confiabilidade
- A importância das tendências na confiabilidade do motor elétrico
- O valor da confiabilidade como um serviço
- O sistema secreto que dará suporte a toda a indústria de IoT
- Como a IIoT aumenta a viabilidade de um sistema de monitoramento de ativos?
- Os benefícios dos sistemas hidráulicos