Mecanismo de remoção de camada atômica única baseado em corte de cobre monocristalino:efeito de raio de borda
Resumo
O objetivo final do corte mecânico é reduzir a espessura mínima do cavaco para uma única camada atômica. Neste estudo, o mecanismo de remoção de camada atômica única baseado em corte em cobre monocristalino é investigado por uma série de análises de dinâmica molecular. Os resultados da pesquisa relatam que, quando a profundidade de corte diminui para a escala atômica, a espessura mínima do cavaco pode ser reduzida a uma única camada atômica pelo corte mecânico usando uma ferramenta de borda arredondada. O comportamento de remoção de material durante a remoção de camada atômica única baseada em corte exibe quatro características, incluindo formação de cavacos por movimento de deslocamento acionado por cisalhamento, deformação elástica na superfície processada, efeito de dimensionamento atômico e efeito de raio de ponta. Com base neste entendimento, um novo modelo de corte é proposto para estudar o comportamento de remoção de material no processo de remoção de camada atômica única baseado em corte, significativamente diferente daqueles para nanocorte e corte convencional. Os resultados fornecem suporte teórico para a pesquisa e o desenvolvimento da tecnologia de fabricação em escala atômica e próxima à atômica.
Introdução
O corte mecânico, como um dos mais importantes métodos de usinagem subtrativa, tem sido aplicado para produzir peças com alta qualidade de acabamento superficial [1, 2]. Um grande número de estudos teóricos e experimentais foram realizados para esclarecer o mecanismo de remoção de material subjacente em nanoescala para estabelecer e enriquecer a teoria básica da nanocorte [3,4,5,6]. Os resultados da pesquisa contribuem significativamente para a aplicação do corte nanométrico na academia e na indústria, possibilitando a fabricação de peças de alto desempenho que requerem formas complexas e acabamento superficial nanométrico de qualidade [7, 8]. No entanto, ainda não há relatório sobre o mecanismo de remoção de material no corte em escala atômica e quase atômica (ACS), restringindo seriamente o progresso do desenvolvimento de tecnologia de fabricação de próxima geração - fabricação em escala atômica e quase atômica ( ACSM), ou seja, Fabricação III [9]. Além disso, o desenvolvimento progressivo de dispositivos em escala atômica também reforçou a demanda por diversos processos de usinagem para atingir o ACSM [10].
No corte em macroescala convencional, a profundidade de corte é significativamente maior do que o raio da aresta de corte, onde a remoção de material é realizada pela formação de cavacos por cisalhamento de material [11,12,13]. Em micro / nanocorte, como a profundidade de corte é comparável ou menor que o raio da borda da ferramenta, a formação de cavacos de extrusão torna-se gradualmente dominada com a profundidade de corte diminuindo para nanoescala, o que é muito influenciado pelos efeitos do raio de ponta [14,15,16 , 17,18,19]. No corte ACS, à medida que a profundidade de corte é ainda mais reduzida para uma escala próxima da atômica e até mesmo para a escala atômica, que é muito menor do que o raio da aresta de corte, o efeito do raio da aresta inevitavelmente afetaria o comportamento de remoção de material.
Além disso, ao contrário do corte convencional e micro / nano corte, no corte ACS, a profundidade de corte não é apenas significativamente menor do que o raio da aresta de corte, mas também comparável ou até menor do que o raio dos átomos da peça de trabalho. O comportamento prático de remoção de material seria alterado em diferentes proporções de profundidade de corte para o raio atômico da peça, o que é reconhecido como um novo efeito de dimensionamento, ou seja, efeito de dimensionamento atômico [20]. Portanto, no corte ACS, tanto o efeito do raio de ponta quanto o efeito do dimensionamento do átomo devem ser considerados. No entanto, não há nenhum relatório sobre essa questão extremamente importante no estudo da tecnologia de corte ACS.
Por essas razões, no presente estudo, o efeito de dimensionamento atômico e efeito de raio de borda no mecanismo de remoção de camada atômica única baseado em corte são investigados usando modelagem por dinâmica molecular (MD).
Este artigo está estruturado nas seguintes seções. A seção 2 apresenta a metodologia usada, incluindo modelagem e protocolo, função potencial adequada. A seção 3 apresenta os resultados da análise e as discussões relevantes. A seção 4 discute o mecanismo de remoção de camada atômica única baseado em corte detalhado, sob a influência acoplada de efeito de ponta e efeito de dimensionamento atômico. Os resultados do estudo são concluídos na Seção 5.
Metodologia
Modelo e protocolo de simulação
À medida que a profundidade de corte diminui para a escala atômica ou quase atômica, é realmente um desafio observar experimentalmente o processo de remoção de material na prática. Neste estudo, uma série de simulações de MD são conduzidas para analisar o mecanismo de remoção de camada atômica única com base em corte, focalizando enfaticamente o efeito de dimensionamento atômico da peça de trabalho e o efeito de raio de ponta.
A Figura 1 mostra os instantâneos para a configuração atômica do modelo de corte de cobre-diamante, que consiste em uma peça de cobre de cristal único e uma ferramenta de corte de diamante. As simulações são conduzidas no plano (111) de cobre de cristal único. As dimensões da peça de trabalho em x - [1 -1 0], y - [1 1 -2], e z - [1 1 1] direções são 27, 10 e 5 nm, respectivamente. Durante as simulações de MD, os átomos da peça de trabalho são divididos em átomos da camada limite, átomos da camada termostática e átomos da camada newtoniana, respectivamente, como mostrado na Fig. 1. As duas camadas na parte inferior da peça, ou seja, camada limite, são mantidas fixas sobre as simulações MD, para eliminar a possível translação da posição induzida pelo corte da peça. As três camadas atômicas adjacentes à camada limite são átomos da camada do termostato. A temperatura da camada termostática é mantida em 298 K por métodos de reescalonamento de velocidade. Os átomos restantes da peça pertencem à camada newtoniana. Nas presentes simulações, o ângulo de saída e o ângulo de afastamento da ferramenta de corte são 0 ° e 12 °. Os parâmetros detalhados do modelo estão resumidos na Tabela 1. Uma vez que o corte ACS é preferencialmente conduzido a uma velocidade de corte mais baixa, uma velocidade de corte de 25 m / s ao longo da direção [-1 1 0] é usada após considerar o efeito da velocidade de corte e tempo computacional custo.
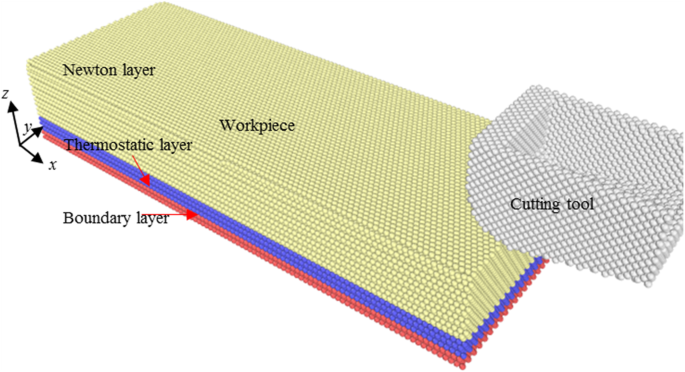
Modelo de simulação para modelo de corte de diamante
Função potencial
O sistema de corte cobre-diamante envolve principalmente dois tipos de átomos, a saber, cobre e átomos de diamante. Nas simulações MD, as interações interatômicas devem ser descritas com precisão para garantir a precisão computacional dos resultados da simulação. Assim, a seleção razoável da função potencial é criticamente significativa. Neste estudo, a função potencial frequentemente utilizada do método do átomo incorporado (EAM) é adotada para descrever as interações interatômicas entre os átomos de cobre [21]. A função de Morse é aplicada para calcular as interações entre átomos de cobre e átomos de diamante (Cu-C), principalmente dependendo do r.
$$ E ={D} _0 \ left [{e} ^ {- 2 \ alpha \ left (r- {r} _0 \ right)} - 2 {e} ^ {\ alpha \ left (r- {r} _0 \ right)} \ right] $$ (1)
onde E e D 0 referem-se ao par de energia potencial e energia de coesão, α representa uma constante, r 0 é a distância de equilíbrio, e r é a distância entre dois átomos. Para interações Cu-C, D 0 é 0,087ev, r 0 é 0,205 nm [22], e α é 51,40 nm −1 . Para as interações entre átomos de carbono na ferramenta de corte (C-C), a força de ligação significativamente mais forte entre átomos de diamante do que átomos de cobre é insignificante. A ferramenta de corte é considerada rígida durante a análise.
Definição de profundidade de corte
Profundidade de corte ( a ) é definida como a distância entre o ponto mais alto da superfície da peça de trabalho e o ponto mais baixo da ferramenta de corte. O tamanho de um átomo da peça é geralmente representado pelo raio atômico ( r w ). Conforme apresentado na Fig. 2, quando a primeira camada atômica superior é direcionada para ser removida da superfície da peça de trabalho, teoricamente, a profundidade de corte máxima usada pode ser obtida da seguinte forma:
$$ {a} _ {\ mathrm {max}} ={r} _w + 0,5 \ ast {d} _ {layer} $$ (2)
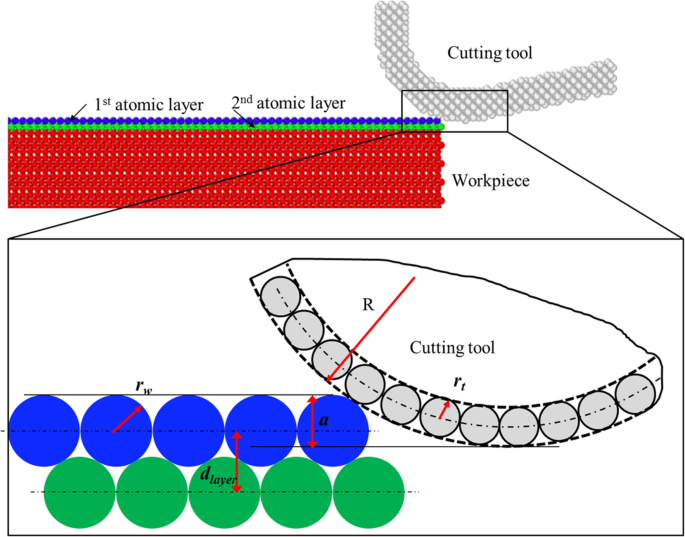
Diagrama esquemático para a definição da profundidade de corte na remoção da camada atômica única
Aqui, d camada representa a distância de espaçamento entre as camadas atômicas vizinhas superiores na superfície da peça de trabalho. Neste estudo, todas as análises são baseadas na (111) superfície da peça de cobre monocristalino; portanto, o r w na Eq. (2) refere-se ao raio dos átomos de cobre, a saber, 1,28 Å. O d camada é 2.087 Å. Quando a é maior que a máximo , o ponto mais baixo da ferramenta de corte entrará em contato direto com a segunda camada atômica e pode induzir a deformação do material e até mesmo a remoção. Portanto, no presente estudo, as profundidades de corte utilizadas são menores do que a máximo (2,32 Å).
Com base nas descobertas, o mecanismo fundamental de remoção da camada atômica única com base no corte será muito alterado em várias combinações das proporções de a para R e a para r w .
Resultados e discussão
De acordo com os resultados do MD, tanto o efeito de dimensionamento atômico quanto o efeito de raio de ponta influenciaram muito o processo de remoção de camada atômica única baseado em corte. Nas seções a seguir, para descrever claramente o efeito do dimensionamento atômico e o efeito do raio da aresta da ferramenta, a proporção da profundidade de corte ( a ) para o raio atômico da peça ( r w ), a / r w , e a da profundidade de corte ( a ) até o raio da borda ( R ), a / R , estão empregados. Os resultados da análise são sistematicamente estudados sob os aspectos de formação do chip, geração de superfície, deformação subsuperficial e comportamento de deslocamento atômico. Os resultados fornecem insights detalhados sobre as características típicas no mecanismo de remoção de camada atômica única com base em corte.
Formação do chip
Os resultados da análise indicam que, devido ao efeito de dimensionamento atômico da peça [20], existem dois valores críticos da relação da profundidade de corte ( a ) para o raio atômico da peça ( r w ), a saber, valor crítico 1 (C 1 ) e valor crítico 2 (C 2 ), que dividiu o comportamento de formação do chip em diferentes casos.
- a.
A proporção de a / r w menor do que o valor crítico 1 (C 1 )
A Figura 3 mostra os resultados da simulação MD em vários raios de aresta da ferramenta na profundidade de corte de cerca de 1,1 Å. Aqui, a relação da profundidade de corte ( a ) para o raio atômico da peça ( r w ) é 0,781.
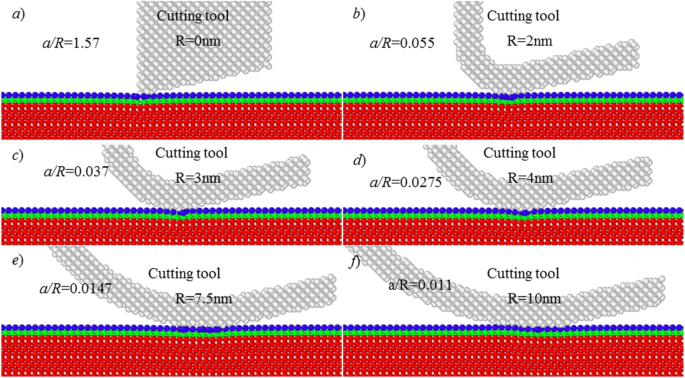
Resultados da simulação na profundidade de corte de 1,1 Å
Apesar do raio de corte aumentado, há deformação elástica ocorrendo na superfície processada de cada Cu (111). Não há formação de cavacos e remoção de material durante o processo de corte. O estudo mostra que a profundidade de corte deve ser maior do que cerca de 1,1 Å para permitir a remoção de material na superfície de Cu (111).
- b.
A proporção de a / r w é maior do que C1, mas menor do que o valor crítico 2 (C 2 )
Quando a profundidade de corte é maior do que cerca de 1,1 Å, ou seja, a proporção de a / r w for maior que 0,781, há remoção de material ocorrendo na superfície da peça. Como mostrado na Fig. 4, uma parte do material é removida da superfície da peça de trabalho, mas um grande número de átomos dentro da primeira camada superior é mantido na nova superfície processada, formando defeitos na superfície. Além disso, conforme o raio da borda aumenta para 7,5 nm, a proporção de a / R é 0,019. Nesse caso, uma parte dos átomos na primeira camada atômica foi pressionada na segunda camada e mesmo na terceira camada atômica, como mostrado na Fig. 4e, que deve ser atribuída à ação de extrusão da ferramenta de corte. Também indica que o efeito do raio da aresta da ferramenta passa a ter influência no processo de remoção de material, embora uma remoção contínua de material não tenha sido obtida.
- c.
A proporção de a / r w é maior que C 2 .
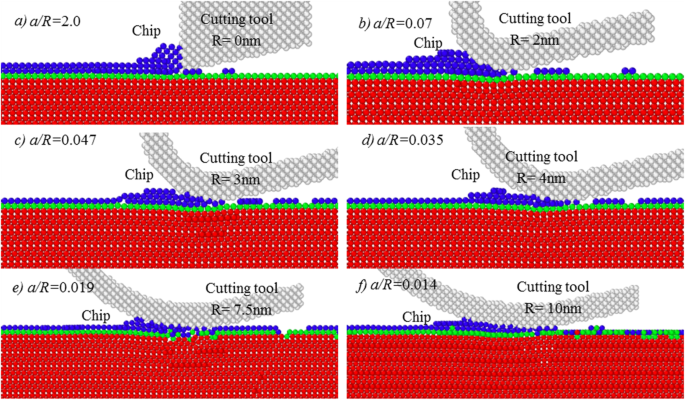
Resultados da simulação na profundidade de corte de 1,4 Å
A Figura 5 mostra a formação de cavacos na profundidade de corte de cerca de 2 Å. Aqui, a proporção de a / r w =2 Å / 1,28 Å =1,563. Em comparação com a Fig. 3, com um aumento da profundidade de corte para 2 Å, os átomos dentro da camada atômica direcionada poderiam ser continuamente e estavelmente removidos pela formação de cavacos. Isso indica que a profundidade de corte foi maior do que a espessura mínima do cavaco de cobre monocristalino e a espessura mínima do cavaco poderia ser reduzida a uma única camada atômica com uma profundidade de corte de cerca de 2 Å. Após o corte, os materiais dentro da primeira camada atômica foram totalmente removidos da superfície da peça.
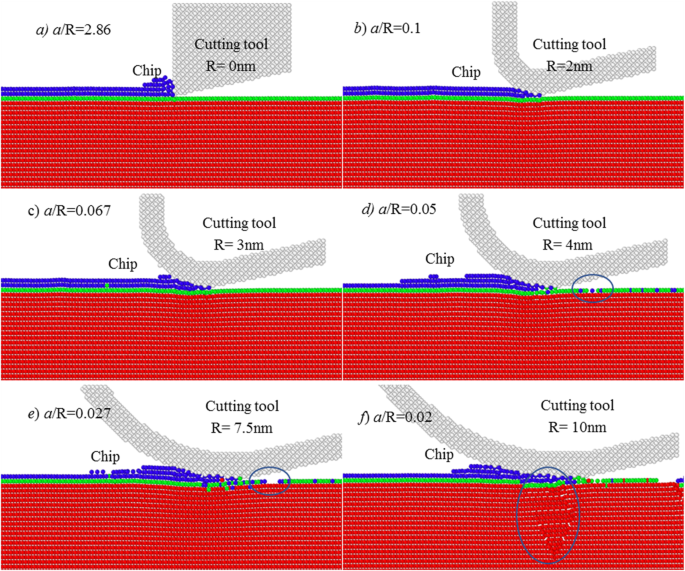
Resultados da simulação de corte ACS na profundidade de corte =2 Å
No entanto, também pode ser notado na Fig. 5 que, devido ao aumento da razão de a / R , os átomos da primeira camada atômica passam por processos de remoção evidentemente diferentes, principalmente a deformação induzida por corte na superfície processada. Na profundidade de corte de 2 Å, quando a ferramenta de corte afiada é usada, ou seja, a relação de a / R é 5,70, ocorre apenas uma ligeira deformação na superfície processada. Conforme o raio de ponta aumenta para 3 nm, a proporção de a / R for 0,134, a amplitude da deformação elástica foi evidentemente aumentada.
Quando o raio da borda da ferramenta é aumentado para 4 nm, como mostrado na Fig. 5d, muitos átomos dentro da primeira camada atômica alvo foram pressionados na segunda camada atômica, formando a nova superfície processada. No raio da borda da ferramenta de cerca de 7,5 nm, uma parte dos átomos na primeira camada é ainda difundida para a terceira camada atômica. Quando o raio da borda da ferramenta atinge cerca de 10 nm, ocorre uma deformação elástica e plástica evidente, que também pode ser determinada na Seção 3.3 a seguir.
Portanto, a remoção da camada atômica única baseada no corte não depende apenas da proporção de a / r w , mas também a proporção de a / R . Para alcançar a remoção da camada atômica única por corte mecânico, isto é, remoção de material em escala atômica, ambos os efeitos de dimensionamento de átomo e efeito de raio de ponta devem ser considerados, significativamente diferente de micro / nanocorte e corte em macroescala convencional.
Geração de superfície
Um dos objetivos da remoção da camada atômica com base no corte é obter a superfície processada livre de defeitos com estrutura cristalina ideal. O efeito do dimensionamento atômico da peça na geração de superfície no corte ACS foi estudado recentemente [20]. No presente estudo, para indicar claramente o efeito do raio de ponta na geração de superfície no corte ACS, a topografia da superfície e a composição da superfície da nova superfície processada são estudadas a seguir.
Topografia de superfície
A Figura 6 mostra as topografias da superfície do Cu (111) processado em diferentes raios de borda. Aqui, uma profundidade de corte de 2 Å é adotada. Como mostrado na Fig. 6a, b, quando o raio da borda da ferramenta é menor que 3 nm, as superfícies de Cu (111) com estrutura cristalina ideal podem ser obtidas. Já os defeitos do lado esquerdo da superfície da peça devem-se à deformação durante o corte-saída da ferramenta. Durante o corte em um estágio estável, não há nenhum defeito superficial formado na superfície processada.
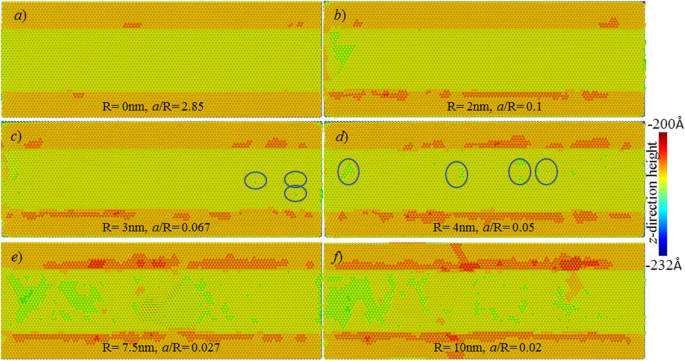
Efeitos do raio da aresta da ferramenta em topografias de superfície. Os átomos são coloridos com base em suas alturas na direção z
À medida que o raio da aresta da ferramenta aumenta, no entanto, muitos defeitos são formados gradualmente na superfície processada. No raio da borda de 4 nm, muitos defeitos semelhantes a furos são formados na superfície processada, ver Fig. 6d. Além disso, quando o raio da borda da ferramenta é igual ou maior do que 5 nm, há um grande número de defeitos de superfície formados, deteriorando seriamente a qualidade da superfície. Nesse caso, mais de uma camada de átomos foi removida da superfície da peça de trabalho. Portanto, pode ser determinado que na profundidade de corte de 2 Å, quando o raio da borda da ferramenta for menor que 3 nm, a remoção da camada atômica única poderia ser alcançada na superfície de Cu (111). Devido ao efeito do raio da aresta de corte, a relação da profundidade de corte ( a ) até o raio da borda ( R ) deve ser maior do que um limite, a fim de alcançar a superfície processada sem defeitos por meio da remoção de camada atômica única baseada em corte. Aqui, o valor crítico da proporção de a / R é [0,05, 0,067].
Composição da superfície
A Figura 7 mostra a composição das superfícies processadas em vários raios de borda da ferramenta e a profundidade de corte de 2 Å. Aqui, os átomos verdes e azuis são aqueles da primeira e segunda camadas, enquanto os átomos vermelhos são aqueles abaixo da segunda camada atômica. Conforme mostrado na Fig. 7a, quando uma ferramenta de corte afiada é usada, a proporção de a / R é 2,85, a superfície processada consiste apenas em átomos na primeira camada. Este resultado indica que a primeira camada atômica alvo foi completamente removida da peça de trabalho. Além disso, significa que a remoção do material é conduzida na forma de camada por camada, na qual o material removido provém apenas da primeira camada atômica visada na superfície da peça.
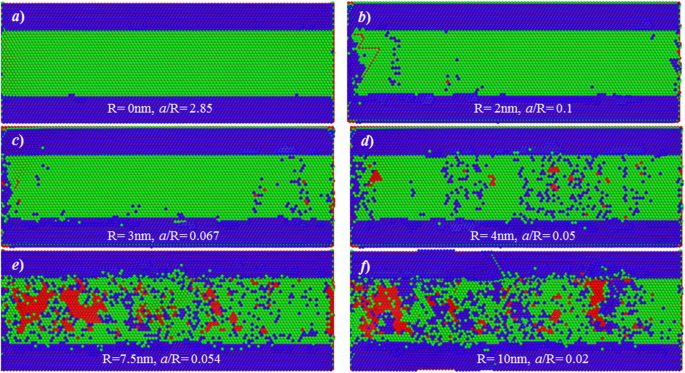
Composição da superfície das superfícies processadas. Os átomos são coloridos com base no número da camada atômica
No entanto, quando o raio da borda da ferramenta é 2 nm e 3 nm, como mostrado na Fig. 7b, c, as superfícies processadas são compostas por duas camadas atômicas (azul e verde). Isso indica que, embora a remoção da camada atômica única tenha sido alcançada, o processo de geração de superfície envolve no mínimo 2 camadas atômicas. Além disso, quando o raio da borda da ferramenta é maior do que 4 nm, há um grande número de átomos da primeira camada atômica na superfície processada, indicando que muitos átomos na primeira camada foram pressionados para gerar uma nova superfície.
Portanto, com o aumento do raio da aresta de corte, a geração da superfície mudou muito. Dois tipos de mecanismo de geração de superfície envolvidos são resumidos abaixo:
- 1.
Camada por camada :a primeira camada atômica visada é totalmente removida para gerar uma nova superfície processada. Apenas os átomos da primeira camada são removidos durante o processo de corte.
- 2.
Remoção de várias camadas :embora a remoção da camada atômica única possa ser realizada, os átomos dentro da camada atômica alvo sofrem dois comportamentos de deslocamento típicos. Uma parte dos átomos seria transformada em cavacos pelo movimento de deslocamento acionado por cisalhamento, enquanto outros seriam extrudados na superfície processada, sob a ação da ferramenta de corte. O processo de remoção de material envolve no mínimo duas camadas atômicas.
Mecanismo de deformação de subsuperfície
Na nanocorte, ocorre deformação elástica e plástica na superfície processada durante o processo de corte. Depois que a ferramenta de corte passa sobre a superfície da peça de trabalho, a parte elástica salta para trás, enquanto a parte plástica deformada levaria a uma deformação duradoura [1, 2]. À medida que a profundidade de corte diminui para a escala atômica, no corte para a remoção da camada atômica única, postula-se que há apenas deformação elástica ocorrendo na superfície processada. Para verificar isso, os estados de deformação do subsolo da peça de trabalho durante e após o corte são analisados. A Figura 8 ilustra as estruturas defeituosas na subsuperfície da peça em vários raios da borda da ferramenta. Aqui, os átomos são coloridos com base no parâmetro de simetria centralizada (CSP), e os átomos com CSP menor que 3 são omitidos, o que representa aqueles com estrutura FCC perfeita.
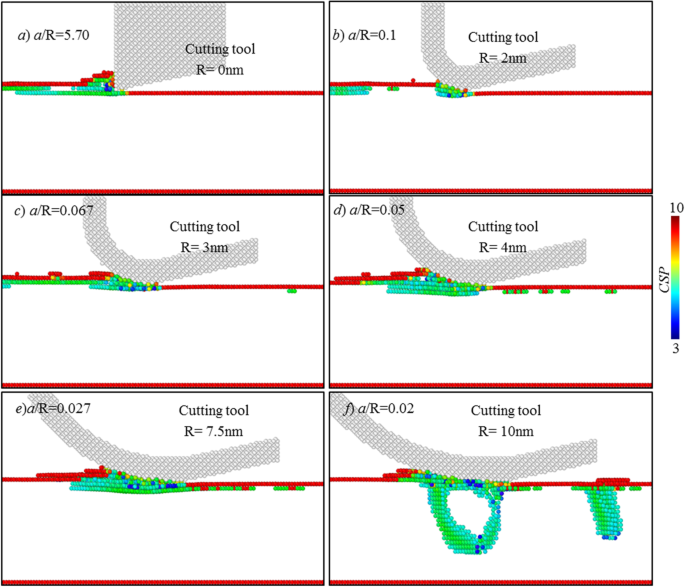
Composição da superfície das superfícies processadas. Os átomos são coloridos com base em seus CSPs
Quando o raio da aresta de corte é menor que 4 nm, nenhum defeito subsuperficial é formado na superfície processada. Há apenas deformação elástica na superfície processada no corte.
Conforme mostrado na Fig. 8, quando o raio da aresta de corte é igual ou maior que 4 nm, existem defeitos de subsuperfície inicializados. Além disso, conforme o raio de corte aumenta, o número de defeitos de subsuperfície aumenta significativamente. Quando o raio da borda atinge cerca de 10 nm, uma alça de deslocamento foi formada e não pode desaparecer após o corte, como mostrado na Fig. 9e. Indica claramente a deformação plástica que ocorre na superfície processada.
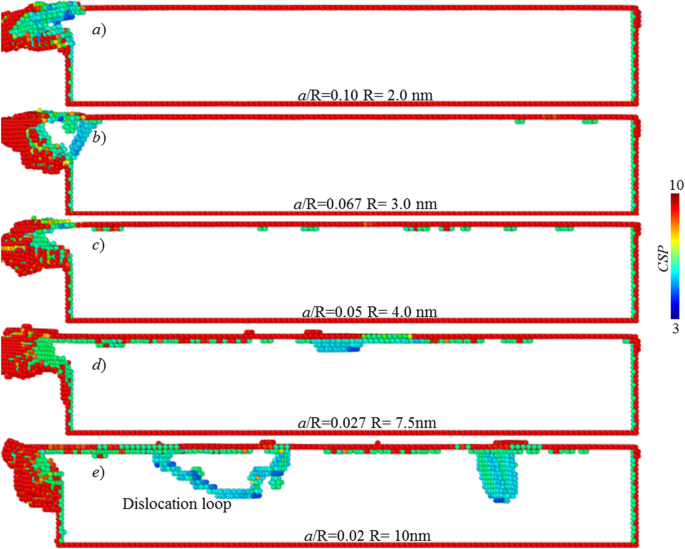
Defeitos de subsuperfície em vários raios de aresta da ferramenta. Os átomos são coloridos com base em seus CSPs
Após a ferramenta passar sobre a superfície da peça de trabalho, a parte elasticamente deformada voltaria a saltar; assim, partes de defeitos de subsuperfície são aniquiladas. Conforme exibido na Fig. 9a-c, finalmente, não existe defeito de subsuperfície quando o raio da borda da ferramenta é de 2 nm ou 3 nm.
Já a parte deformada plasticamente leva a uma deformação duradoura. Conforme mostrado na Fig. 9, quando o raio da borda da ferramenta é de 7,5 nm, há um pequeno número de defeitos de subsuperfície remanescentes. Quando o raio da borda da ferramenta é de 10 nm, o loop de deslocamento e a falha de empilhamento finalmente existem na subsuperfície da peça.
Com base na análise acima, pode-se inferir que para permitir a remoção da camada atômica única com base no corte, a deformação plástica deve ser evitada, e apenas a deformação elástica é permitida na superfície processada. É considerada uma característica do processo de remoção de camada atômica única com base em corte.
Comportamento de deslocamento atômico
De acordo com os arquivos de trajetória MD, o movimento de deslocamento tem dominado o processo de remoção de camada atômica única com base em corte. A Figura 10 mostra os resultados da simulação usando diferentes raios de aresta da ferramenta. No raio da aresta de 2 nm, sob a ação da ferramenta de corte, apenas a primeira camada atômica é deslizada ao longo da direção de corte para formar um cavaco, enquanto as outras permanecem imobilizadas. Pode ser considerado como uma seção transversal de um deslocamento de borda.
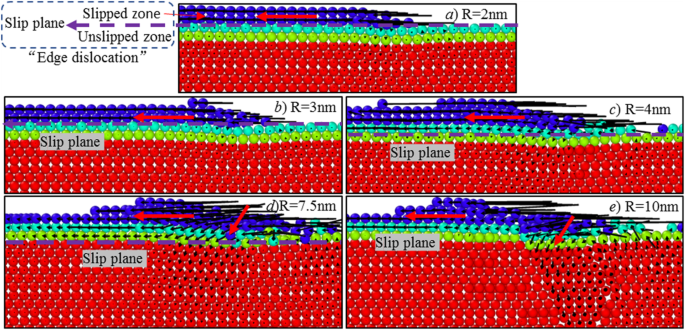
Comportamento de deslocamento atômico em vários raios de ponta
Conforme o raio da borda da ferramenta aumenta, parte do material dentro da primeira camada atômica foi pressionada na superfície processada, induzindo o deslizamento das camadas atômicas abaixo da primeira camada. Além disso, à medida que o raio da borda da ferramenta aumenta, o número de camadas atômicas submetidas ao processo de deslizamento do material tende a aumentar. Quando o raio da borda da ferramenta é de 4 nm, exceto para a primeira camada atômica, a segunda camada atômica também conduz deslizamento do material ao longo da direção de corte, conforme ilustrado na Fig. 10. Quando o raio da borda da ferramenta é de 7,5 nm, conforme a ferramenta de corte avança, os três primeiros camadas atômicas na superfície da peça de trabalho deslizaram ao longo da direção de corte. Além disso, quando o raio da borda da ferramenta é aumentado para 10 nm, um grande número de materiais foi pressionado para formar uma nova superfície processada; há deformação plástica (ver Fig. 10e) ocorrendo na superfície da peça de trabalho, o que também pode ser determinado na Fig. 9.
A Figura 11 mostra o processo de deslizamento da camada atômica alvo ao longo da direção de corte. A área da zona deslizante é continuamente ampliada com o avanço da ferramenta de corte. Na distância de corte de 17,5 nm, a zona escorregada atingiu um valor máximo. Subsequentemente, os materiais dentro da zona deslizante são continuamente formados em chip; o volume do chip também é aumentado.
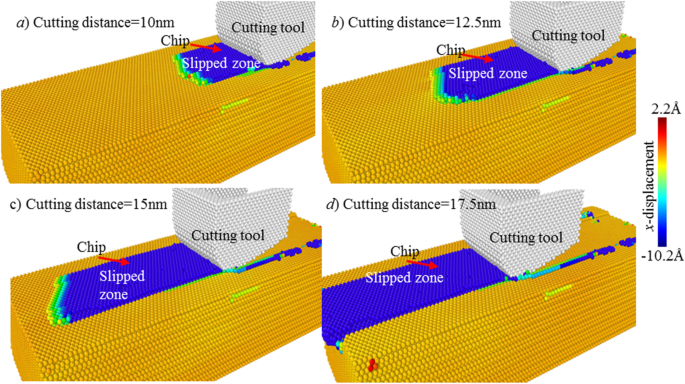
Processo de deslizamento da camada atômica alvo em raio de ponta de 2 nm. Os átomos são coloridos com base em seus valores de deslocamento atômico na direção x
No geral, de acordo com a análise nas Seções 3.3 e 3.4, conforme o raio da borda da ferramenta aumenta, tanto o mecanismo de deformação subsuperficial quanto o comportamento de deslocamento atômico mudaram muito. Em diferentes raios de borda da ferramenta, diferentes números de camadas atômicas tendem a deslizar ao longo da direção de corte, enquanto diferentes regimes de deformação ocorrem na superfície processada, conforme resumido na Tabela 2. Além disso, pode-se descobrir que na remoção de camada atômica única baseada em corte processo, a formação de cavacos é governada por movimento de deslocamento conduzido por cisalhamento, significativamente diferente da formação de cavacos em corte convencional e nano-corte. Também pode ser considerado como uma característica característica da remoção de camada atômica única baseada em corte.
Força de corte
Influência do Efeito Edge Radius
A Figura 12 mostra o efeito do raio da aresta de corte nas forças de corte médias na profundidade de corte de 2 Å. Aqui, os componentes tangencial e normal das forças de corte, a saber, F t e F n , são comparados. Conforme ilustrado, para uma ferramenta de corte afiada, a proporção de a / R é 2,85, e o F t de 16,4 nN é evidentemente menor que F n de 23,7 nN. Conforme o raio da aresta da ferramenta aumenta, ambos de F t e F n são aumentados. No entanto, o F n exibiu amplitudes de crescimento muito maiores do que F t . Isso indica claramente que conforme o raio da aresta da ferramenta aumenta, a força de corte normal teria um efeito maior no processo de remoção de material no processo de corte ACS. No entanto, quando o raio da borda da ferramenta é maior do que cerca de 3 nm, a remoção da camada atômica única não pode ser alcançada. Assim, uma força de corte normal maior não seria útil para permitir a remoção da camada atômica única com base no corte, e uma força de corte normal mais baixa deve ser preferencialmente adotada.
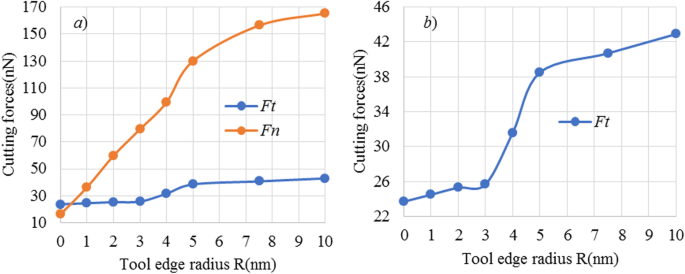
Gráfico das forças de corte versus raio da aresta de corte na profundidade de corte de 2 Å
Como as forças de corte normais fornecem a tensão de compressão para permitir a deformação elástica e / ou plástica na superfície processada, as forças de corte tangencial forneceriam a tensão de cisalhamento para a formação de cavacos. Portanto, pode-se inferir que a formação de cavacos na remoção de camada atômica única com base no corte deve ser impulsionada principalmente pela força de corte tangencial. Também pode ser visto na Fig. 12b que o F t exibiu três tipos de mudanças, o que ainda leva a diferentes topografias de superfície (ver Fig. 6), incluindo o seguinte:
Quando o raio da aresta da ferramenta é menor do que cerca de 3 nm, ou seja, a proporção de a / R é 0,067, o F t permanece aproximadamente inalterado, e é sempre menor que 25 nN, conforme o raio da borda aumenta. Nesse caso, apenas uma camada atômica é removida da superfície da peça.
Quando o raio da aresta da ferramenta é de 3 nm e 5 nm, as relações de a / R são 0,04 e 0,067, enquanto F t é evidentemente aumentado para cerca de 38,5 nN. Consequentemente, mais de uma camada atômica é removida da superfície da peça de trabalho, mas há um pequeno número de defeitos de superfície formados.
Quanto ao raio da borda maior que 5 nm, F t também converge gradualmente para um valor constante. Nesse caso, mais de uma camada atômica é removida. No entanto, um grande número de defeitos superficiais são formados na superfície e subsuperfície da peça de trabalho.
Pode-se concluir que uma força de corte tangencial muito baixa poderia permitir a remoção de camada atômica única baseada em corte em um raio de ponta razoável, como 2 nm. Por sua vez, a remoção da camada atômica única não pôde ser realizada, apesar da maior força de corte tangencial.
Influência do efeito de dimensionamento atômico
A Figura 13 fornece ainda o gráfico das forças de corte em relação à profundidade de corte no raio da aresta de corte de 2 nm. Pode-se descobrir que no raio da aresta de corte de 2 nm, conforme a profundidade de corte aumenta, a força de corte normal e as forças de corte tangencial exibem mudanças em três estágios. Existem mudanças evidentes na profundidade de corte de cerca de 1,1 Å e 1,6 Å. A proporção correspondente da profundidade de corte ( a ) para o raio atômico da peça ( r w ) são 0,055 e 0,080, que são os dois valores críticos mencionados acima de a / r w , C 1 e C 2, conforme descrito na Seção 3.1.
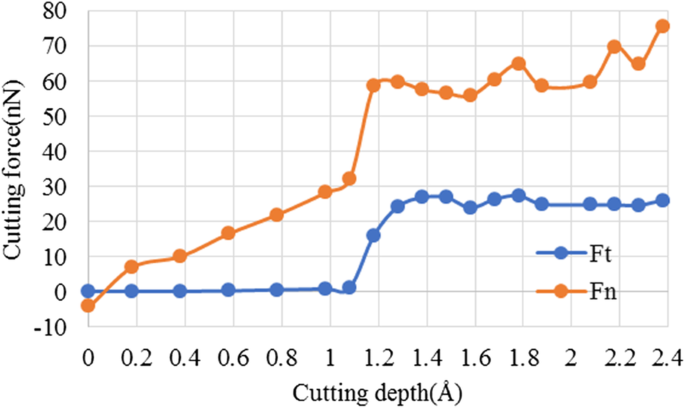
Plot of cutting forces versus cutting depth at edge radius of 2 nm
When cutting depth is smaller than 1.1 Å, namely, the ratio of a/r w is less than 0.055, F t is always 0 nN, while F n is linearly increased to about 32 nN. However, the cutting forces could not enable plastic material deformation and removal on the workpiece surface. Consequently, there is only elastic deformation on workpiece surface, as shown in Fig. 3.
When the cutting depth is larger than 1.1 Å, but smaller than 1.6 Å, the ratio of a/r w is more than 0.055 but less than 0.080. If this case, F t has greatly increased from 0 nN to about 25 Nn, while F n further increased to about 58 nN. The cutting forces are larger enough to enable material removal on workpiece surface. At the cutting depth of 1.4 Å, there is chip formation and material removal on workpiece surface. But the stable and continuous material removal could not be realized and many defects are formed on the processed surface, as shown in Fig. 4.
When the cutting depth is larger than 1.6 Å, both F t and F n are large enough to enable continuous material removal on workpiece surface. Consequently, chip is stably formed over the workpiece surface, and the targeted atomic layer is continuously removed via chip formation, forming a new processed surface, as shown in Fig. 5b and Fig. 6b.
Overall, both cutting-edge radius effect and atomic sizing effect have an influence on cutting force in cutting-based single atomic layer removal process, thereby changing the material removal and surface generation process.
Discussions About Cutting-Based Single Atomic Layer Removal Mechanism
As per above analysis, both atomic sizing effect and cutting-edge radius effect have a great influence on the cutting-based single atomic layer removal mechanism. As summarized in Table 3, depending on the ratio of cutting depth to workpiece atomic radius(a/r w ) and the ratio of cutting depth to edge radius(a/R ), there are minimum 5 typical cases of material deformation and removal behaviours in cutting-based single atomic layer removal process. In this section, the fundamental material deformation and removal mechanism of each case is summarized.
In conventional machining, as cutting depth is significantly larger than the cutting-edge radius, the cutting-edge radius effect can be ignored. As the cutting depth is decreased to nanoscale, which is comparable or lower than the edge radius, the edge radius effect can be no longer ignored. In nanocutting, the material removal process is dominated by the extrusion deformation, which is greatly influenced by cutting-edge radius. As the cutting depth is further decreased to atomic scale, except for cutting-edge radius effect, a new sizing effect, atomic sizing effect [20] has a great influence on material removal.
As shown in Fig. 14, in the cutting-based single atomic layer removal process, there are two portions involving in cutting, i.e., nanometric cutting edge and the lowest cutting tool atoms (B ) Such two portions could be coupled to enable single atomic layer removal. The size of cutting edge, regarded as ‘nano-tool,’ is described by edge radius (R ) The cutting edge is the envelope curve of the outermost atoms in cutting tool. Regarding the lowest atoms, as ‘atomic-tool,’ it is described by workpiece atomic radius (r w ) The cutting-based single atomic layer removal is the results of the coupled actions of nano-tool and atomic-tool on workpiece material.
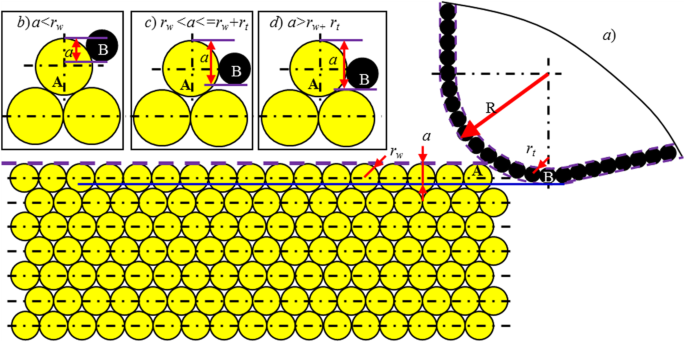
Schematic diagram for cutting-based single atomic layer removal
Firstly, depending on the ratio of cutting depth (a ) to the workpiece atomic radius (r w ), i.e., a/r , there are three kinds of material deformation behaviour in ACS cutting process.
- 1.
The ratio of a/r w is smaller than critical value 1(C1 )
As shown in Fig. 15, chip formation does not occur, but elastic deformation does occur on the workpiece surface. During cutting process, after workpiece passes the lowest point of cutting tool, the elastically deformed part would recover completely. Consequently, no material deformation and removal occurred on the topmost surface. In such case, the tool edge effect could be ignored. This ratio could be affected by material properties (case 1).
- 2.
The ratio of a/r w is larger than C 1 , but smaller than critical value 2 (C2 )
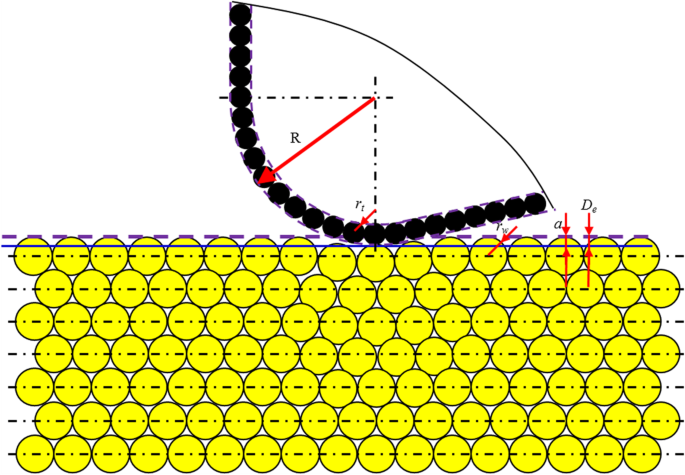
Schematic illustration of cutting-based single atomic layer removal at the ratio of a/rw smaller than C1
As the ratio of the cutting depth to atomic radius (a/r w ) increases to be larger than C1 but smaller than critical value 2(C2 ), there is material removal on the workpiece surface, but it is noncontinuous. In such case, only part of material within targeted atomic layer is formed into chip by shear stress-driven dislocation motion, while others are remained on the workpiece surface. When cutting tool passes over the workpiece surface, the surface quality of the processed surface is seriously deteriorated (case 2) (Fig. 16).
- 3.
The ratio of a/r w is larger than critical value 2 (C2 )
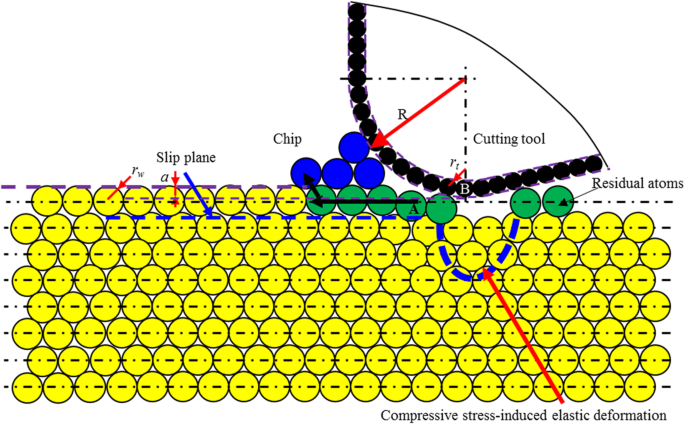
Schematic illustration of cutting-based single atomic layer removal at a/rw larger than C1 and smaller than C2
When the ratio of cutting depth to atomic radius (a/r w ) increases to be larger than critical value, there is a continuous material removal by chip formation during cutting process. In such case, the edge radius effects can no longer be ignored. For ACS cutting process, the maximum cutting depth is subnanometer order. At such extremely low cutting depth, regardless of the nominal rake angle, the effective rake angle is always largely negative. The negative rake face can produce the necessary shear stress to enable chip formation by dislocation motion and the compressive force to enable the elastic and/or plastic deformation on the processed surface.
Depending on the ratio of cutting depth (a ) to tool edge radius (R ), different kinds of elastic and/or plastic deformation process occur on the workpiece surface. There are two threshold values of a/R , namely, threshold value 1 (T 1 ) and threshold value 2 (T 2 ), leading to different material removal processes.
- a.
The ratio of a/R is larger than threshold (T 1 )
As shown in Fig. 17, there is one atomic slip plane. The workpiece material below this plane would have an elastic deformation. As for the materials above this slip plane, it undergoes a plastic deformation by dislocation motion. A part of materials is also formed into chip by shearing stress-driven dislocation motion, while the other undergoes dislocation slip. After the workpiece passes the lowest point of the cutting tool, the elastically deformed part recovers completely (case 3).
- b.
The ratio of a/R is lower than threshold 1 (T 1 ), but larger than threshold 2 (T 2 )
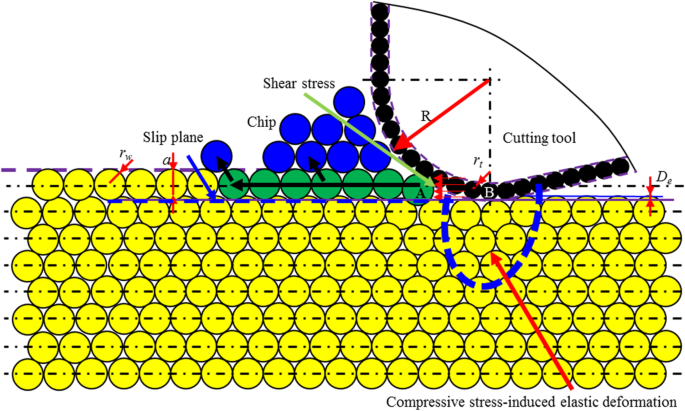
Schematic illustration of cutting-based single atomic layer removal at a/rw larger than C2 and a/R larger than T1
Under the action of cutting edge, minimum two atomic layers undergo dislocation slip, while elastic deformation occurs on the processed surface, as shown in Fig. 18. The cutting edge provides a force to generate the shear stress to enable chip formation by dislocation motion and compressive stress to induce elastic deformation on the processed surface. In such case, part of material within the targeted atomic layer is formed into chip by dislocation motion, while the other is extruded into other atomic layers to form new processed surface. It also drives the slip of other atomic layers on the workpiece surface, leading to the negative dislocation climb. After workpiece material passes the lowest point of the cutting tool, the elastic portion springs back (case 4).
- c.
The ratio of a/R is lower than threshold 2 (T 2 )
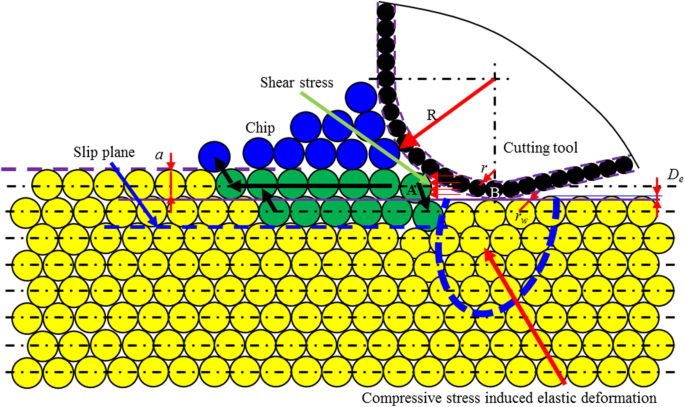
Schematic illustration of cutting-based single atomic layer removal at a/rw larger than C2 , a/R larger than T2 , smaller than T1
As the ratio of a/R decreases to lower than T 2 , there is either no chip formation or extremely small volume of chip formation, but elastic-plastic deformation occurs on the processed surface, as shown in Fig. 19. After workpiece material passes the lowest point of cutting edge, the elastic deformed part springs back. The plastic deformed part (Δ ) leads to lasting deformation. Such ratio is related with material properties, tool geometry and process conditions (case 5).
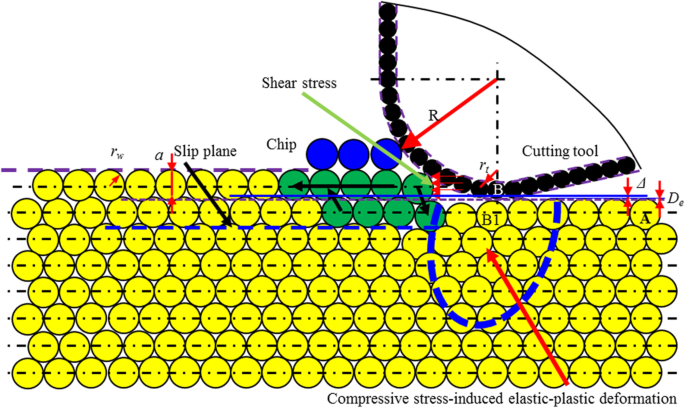
Schematic illustration of cutting-based single atomic layer removal at a/r larger than C2 and a/R lower than T2
Conclusions
In the present study, both of atom sizing effect and cutting-edge radius effect are analysed to investigate their influence on chip formation, surface generation, subsurface deformation, and atomic displacement behaviour during the cutting of monocrystalline copper towards single atomic layer removal. The following conclusions can be drawn.
- 1.
A new model is proposed to describe the underlying material deformation and removal mechanism in the cutting-based single atomic layer removal process, which exhibits four characteristics, including chip formation by dislocation motion, elastic deformation occurring on the processed surface, atomic sizing effect, and cutting-edge radius effect.
- 2.
Both of atomic sizing effect and cutting-edge radius effect have a great influence on the material deformation and removal during the cutting process of monocrystalline copper towards single atomic layer removal. With a specific ratio of cutting depth to workpiece atom radius (a/r w ) and that of cutting depth to edge radius (a/R ), cutting-based single atomic layer removal could be achieved on Cu (111) surface.
- 3.
Chip formation is affected by the ratios of a/r w and a/R . There is a chip formation only when the ratio of a/r w is larger than one critical value (C1) and the ratio of a/R is smaller than one threshold value (T1). Moreover, chip formation is mainly dependent on the shear stress-driven dislocation motion, significantly different from the extrusion-dominated chip formation in nanocutting and shearing-dominated chip formation in conventional machining.
- 4.
Single atomic layer removal can be achieved via layer-by-layer removal and multi-layer removal. The former one refers to that the targeted atomic layer could be either fully removed from workpiece surface. The latter one means that the first atomic layer is partly removed while the remaining materials are pressed into other atomic layers, forming a new processed surface.
- 5.
There is only elastic deformation occurring on the processed surface during ACS cutting process, different from the elastic-plastic deformation in nanocutting. It can be regarded as one characteristic feature in ACS cutting.
- 6.
Depending on the combined effect of atom sizing effect and cutting-edge radius effect, there exist five cases of material deformation and removal processes during the cutting-based single atomic layer removal, i.e., no workpiece material is removed (case 1), workpiece materials are non-continuously removed (case 2), a part of materials is formed into chip while others undergoes material slip via dislocation motion (case 3), a part of materials within the targeted atomic layer is formed into chip while others are extruded into other atomic layers to form new processed surface (case 4), and the elastic deformed part springs back, while the plastic deformed part leads to a lasting deformation (case 5).
Disponibilidade de dados e materiais
Os autores declaram que os materiais, dados e protocolos associados estão à disposição dos leitores, e todos os dados usados para a análise estão incluídos neste artigo.
Abreviações
- ACS:
-
Atomic and close-to-atomic scale
- ACSM:
-
Atomic and close-to-atomic scale manufacturing
- MD:
-
Dinâmica Molecular
Nanomateriais
- Tecnologias de Deposição de Camada Atômica Avançada para Micro-LEDs e VCSELs
- Remoção de adsorção fotocatalítica sinérgica do efeito magenta básico de nanocompósitos de AgZnO / polioxometalatos
- As Nanofibras Hierárquicas de Poliamida 6-ZnO Antibacteriana Fabricadas por Deposição de Camada Atômica e Crescimento Hidrotérmico
- Propriedades fotocatalíticas de pós de TiO2 revestidos com Co3O4 preparados por deposição de camada atômica aprimorada com plasma
- Ajuste de nível de Fermi de filmes ZnO por meio de deposição de camada atômica superciclada
- Estudo do Efeito da Direção de Impacto no Processo de Corte Nanométrico Abrasivo com Dinâmica Molecular
- Dependência da espessura nas propriedades interfaciais e elétricas na camada atômica AlN depositado no plano c GaN
- Deposição de camada atômica aprimorada com plasma de baixa temperatura de SiO2 usando dióxido de carbono
- Células solares de heterojunção de nanowire de silício com um filme de passivação de Al2O3 fabricado por deposição de camada atômica
- Corte de esquadria simples em comparação com serra de esquadria dupla