Leonardo e CETMA:interrompendo compósitos para reduzir custos e impacto ambiental
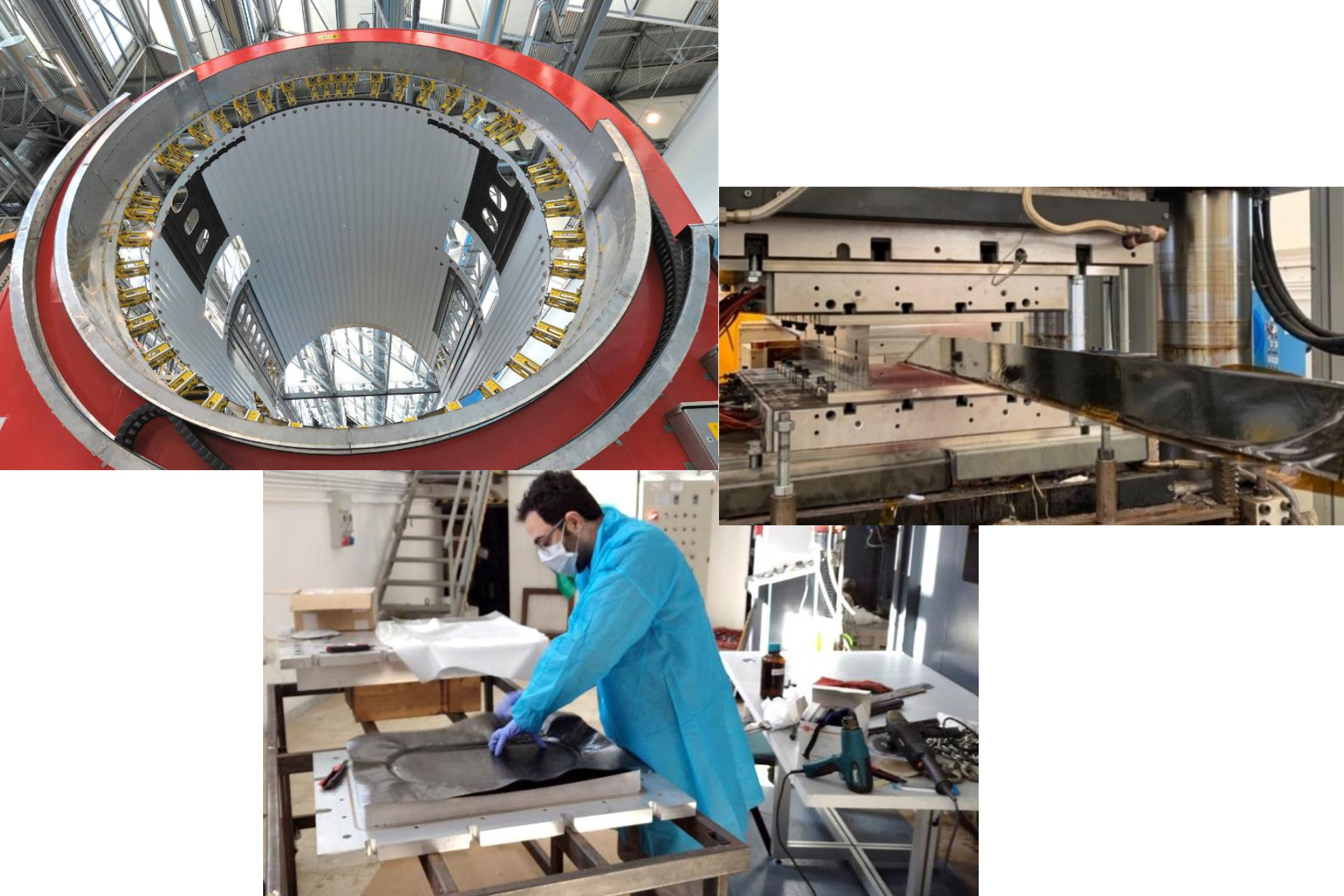
Este blog é baseado na minha entrevista com Stefano Corvaglia, engenheiro de materiais, chefe de pesquisa e desenvolvimento e gerente de IP da Divisão de Aeroestruturas da Leonardo (Grottaglie, Pomigliano, Foggia, instalações de produção de Nola, sul da Itália) e Dr. Silvio Pappadà, engenheiro de pesquisa e chefe de programas com Leonardo no CETMA (Brindisi, Itália).
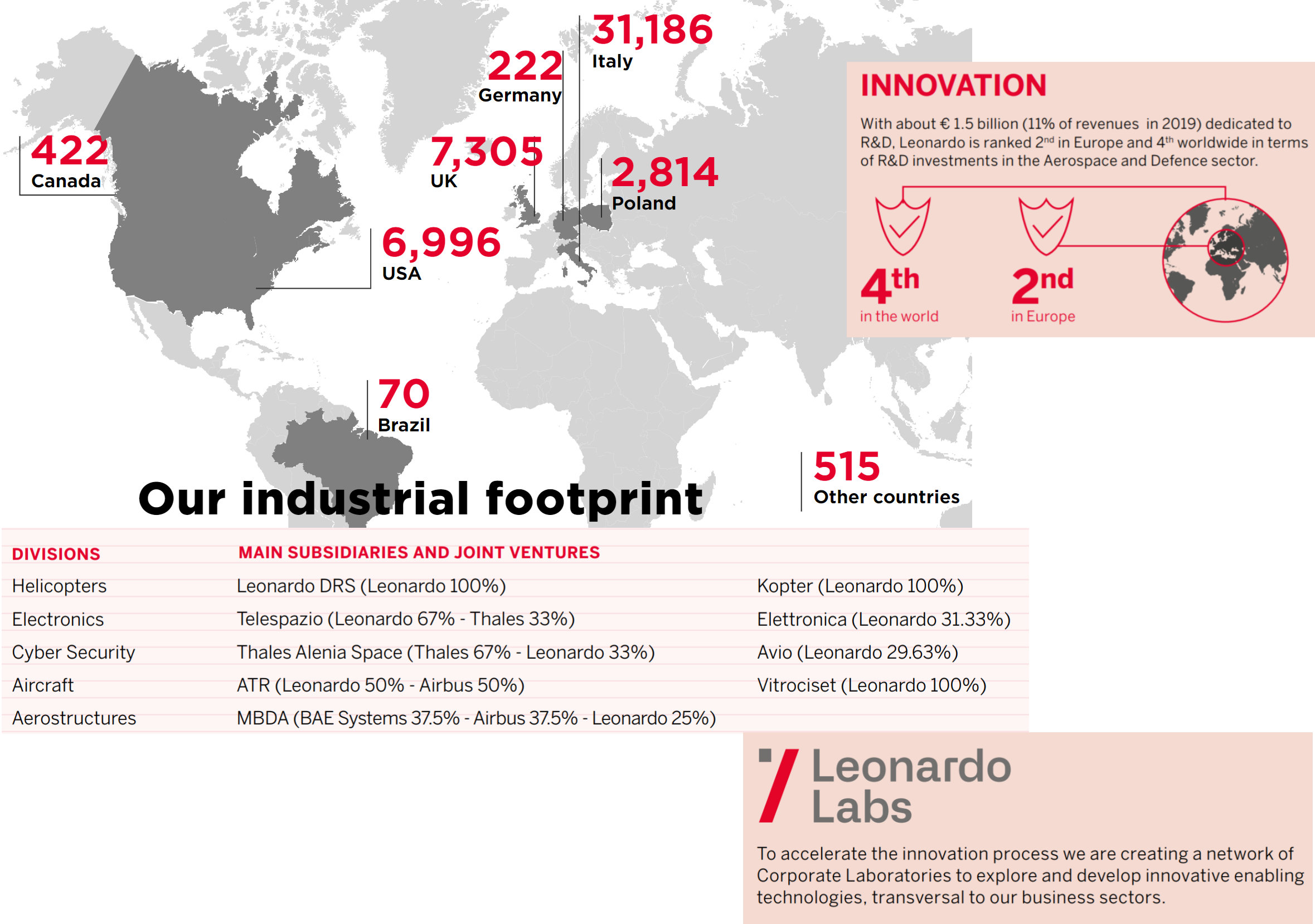
Leonardo (Roma, Itália) é um dos maiores players mundiais em Aeroespacial, Defesa e Segurança, com 13,8 bilhões de euros em receitas e mais de 40.000 funcionários em todo o mundo. A empresa oferece soluções abrangentes em escala global para sistemas aéreos, terrestres, marítimos, espaciais, cibernéticos e de segurança e sistemas não tripulados. Com cerca de € 1,5 bilhão (11% das receitas em 2019) dedicados à P&D, Leonardo está classificado em 2 ° lugar na Europa e 4 ° em todo o mundo em termos de investimentos em pesquisa no setor Aeroespacial e Defesa.
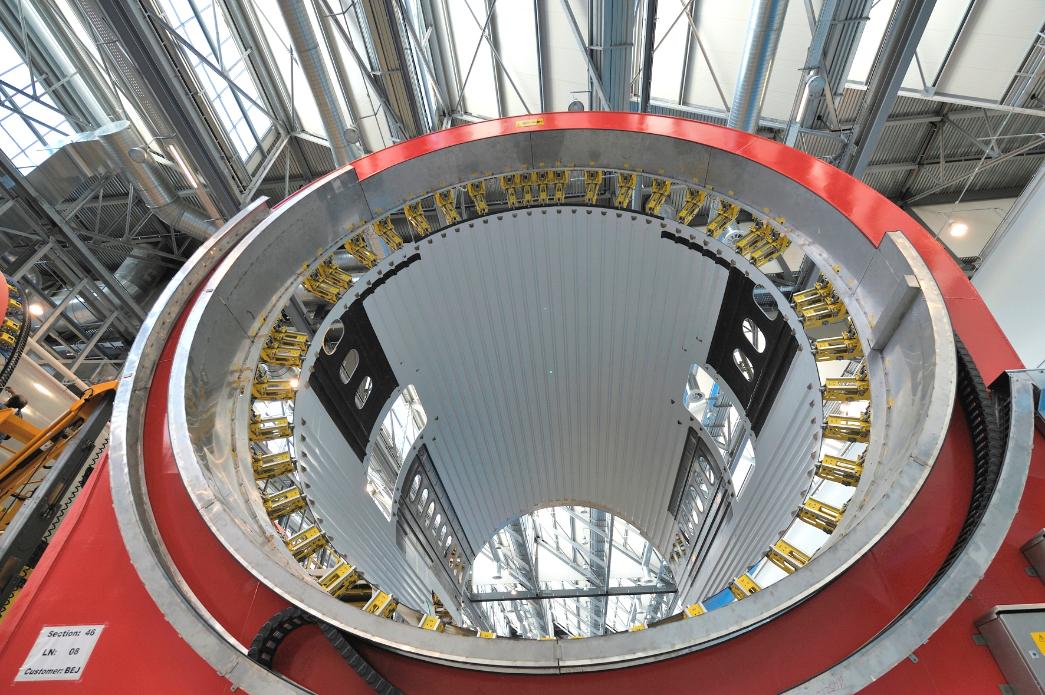
Por meio de sua Divisão de Aeroestruturas, a Leonardo fornece fabricação e montagem de grandes componentes estruturais, incluindo fuselagens e empenagens, em compósitos e materiais tradicionais para os principais programas de aeronaves civis do mundo.
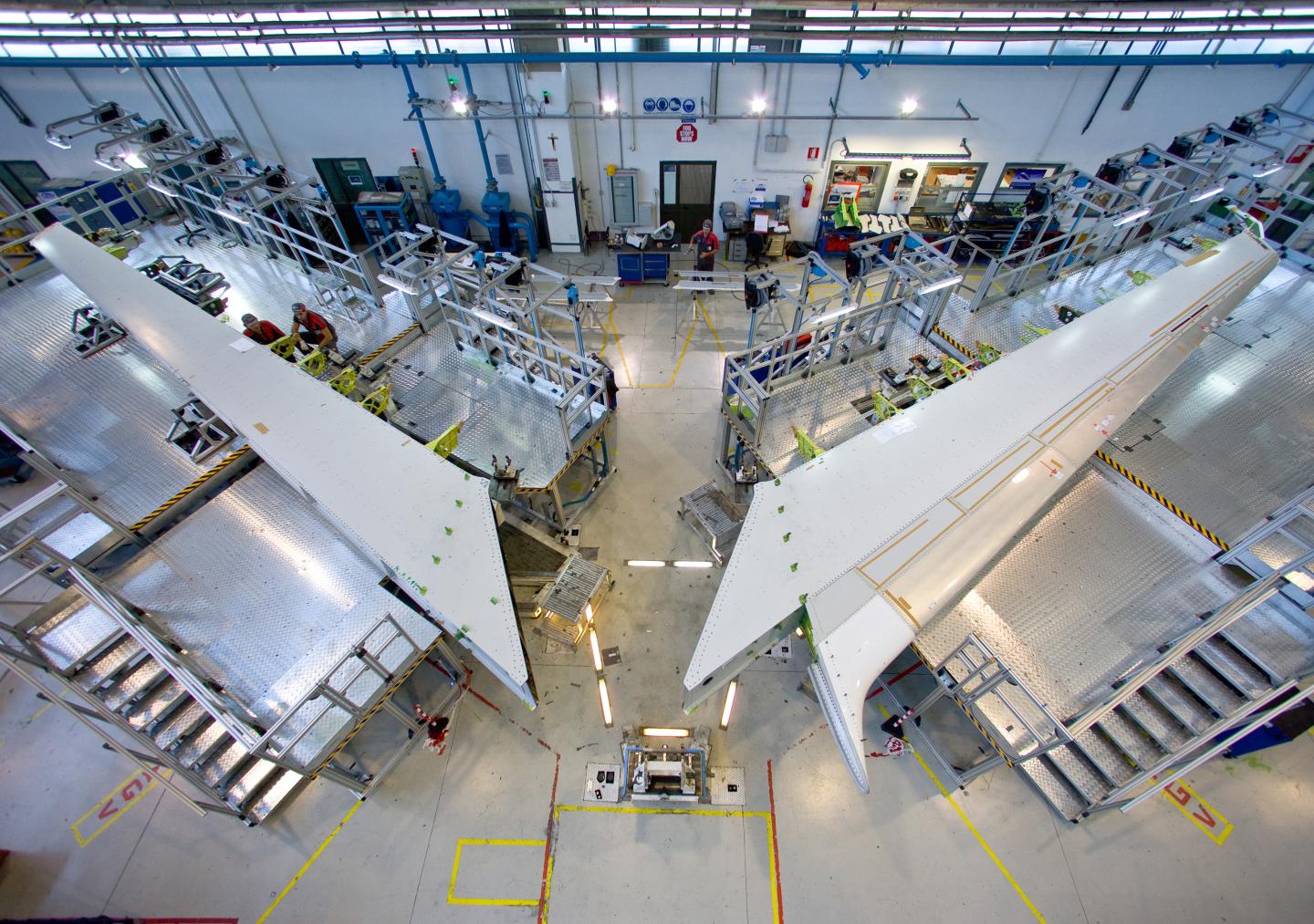
Em materiais compostos, a Divisão Aeroestruturas da Leonardo produz “barris inteiros” para as seções 44 e 46 da fuselagem central do Boeing 787 em sua fábrica de Grottaglie, bem como os estabilizadores horizontais em sua fábrica de Foggia - totalizando cerca de 14% da fuselagem do 787. A produção de outras estruturas compostas inclui, em sua planta de Foggia, a fabricação e montagem de empenagens para aeronaves comerciais ATR e Airbus A220. Foggia também produz peças compostas para o Boeing 767 e para programas militares, incluindo o Joint Strike Fighter F-35, o jato de combate Eurofighter Typhoon, o transporte militar C-27J e o Falco Xplorer, o último membro da família Falco de aeronaves não tripuladas produzidas por Leonardo.
Trabalhando com CETMA
“Temos muitas atividades em andamento com o CETMA, por exemplo, em compósitos termoplásticos e moldagem por transferência de resina (RTM)”, diz Corvaglia. “Nosso objetivo é ter as atividades de P&D prontas para produção no menor tempo possível. Em nosso departamento (P&D e gerenciamento de IP), também buscamos tecnologias disruptivas com um TRL mais baixo [nível de prontidão de tecnologia - ou seja, TRL mais baixo é mais nascente e mais distante da produção], mas procuramos ser mais competitivos e ajudar nossos clientes em todo o mundo . ”
“Desde o início do nosso trabalho em conjunto”, acrescenta Pappadà, “sempre procuramos manter baixos os custos e o impacto ambiental. Descobrimos que os compósitos termoplásticos (TPC) oferecem uma redução em ambos os termofixos. ”
Corvaglia observa que, “junto com a equipe de Silvio, desenvolvemos essas tecnologias e construímos alguns protótipos de células automatizadas para avaliá-los em produção”.
Moldagem por compressão contínua (CCM)
“O CCM é um bom exemplo do nosso trabalho conjunto”, afirma Pappadà. “Leonardo identificou alguns componentes feitos em compostos termofixos e juntos exploramos a tecnologia para fornecê-los no TPC, observando onde há um grande número de peças na aeronave, como estruturas de emenda e escoras com geometria simples.”
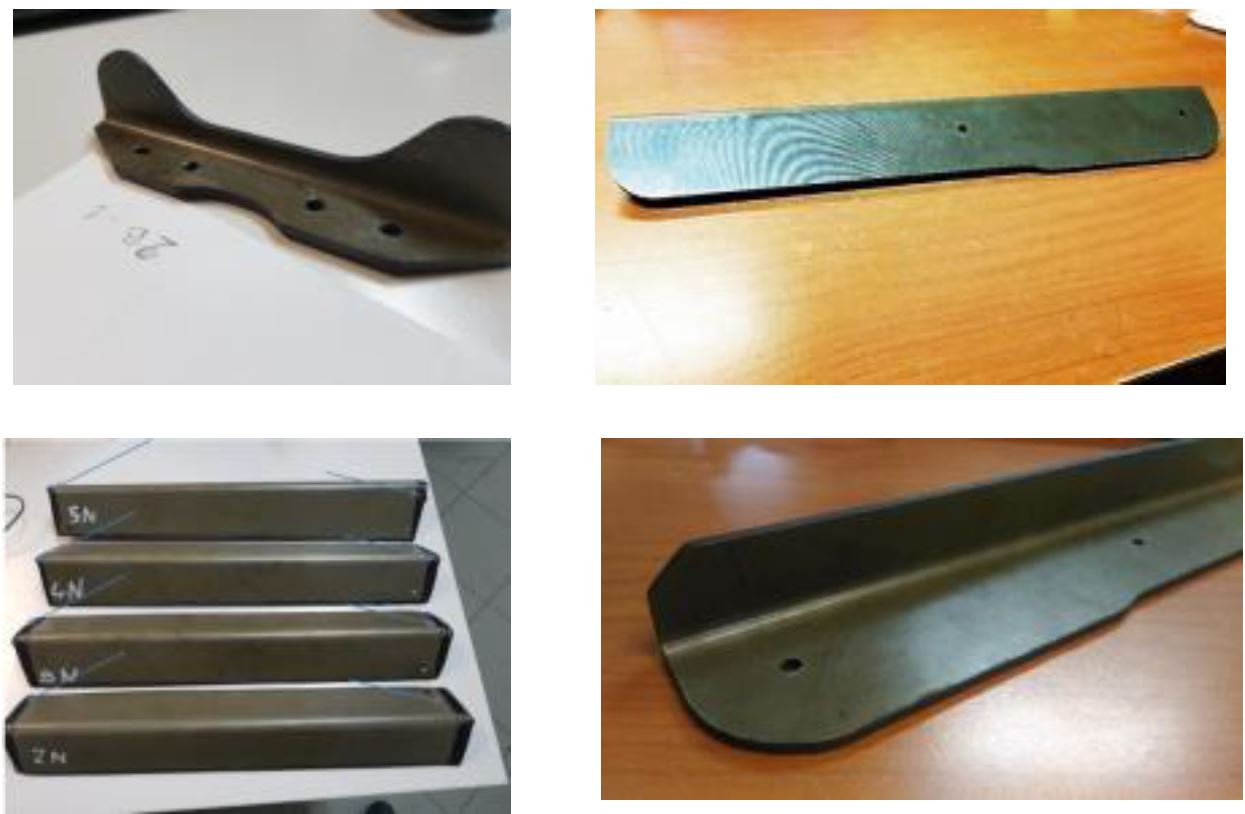
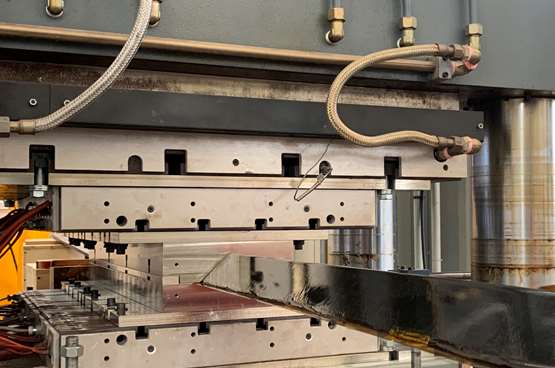
“Precisávamos de uma nova tecnologia de produção caracterizada por baixo custo e alta taxa”, continua ele. Ele ressalta que, no passado, os componentes simples do TPC eram fabricados com uma grande quantidade de resíduos. “Portanto, produzimos perfis líquidos com base na moldagem por compressão não isotérmica, mas com algumas inovações (patentes em andamento) para reduzir o refugo. Projetamos uma célula totalmente automatizada para isso, que uma empresa italiana então construiu para nós. ”
Esta célula é capaz de produzir os componentes que Leonardo projetou, diz Pappadà, “a uma taxa de um componente a cada 5 minutos, trabalhando 24 horas / dia”. No entanto, sua equipe teve que descobrir a produção da pré-forma. “No início, precisávamos de um processo de laminação plana, pois esse era o gargalo naquele ponto”, explica. “Então nosso processo começa com um blank (laminado plano), aquece em um forno infravermelho (IR) e depois em uma prensa para moldagem. Laminados planos são geralmente produzidos em grandes prensas e requerem ciclo de 4-5 horas. Decidimos investigar um novo método capaz de produzir laminados planos de forma mais rápida. Assim, desenvolvemos uma linha CCM de alta produtividade no CETMA com o apoio dos engenheiros da Leonardo. Reduzimos o tempo de ciclo de uma peça de 1 metro por 1 metro para 15 minutos. É importante ressaltar que é um processo contínuo, então podemos produzir comprimentos ilimitados. ”
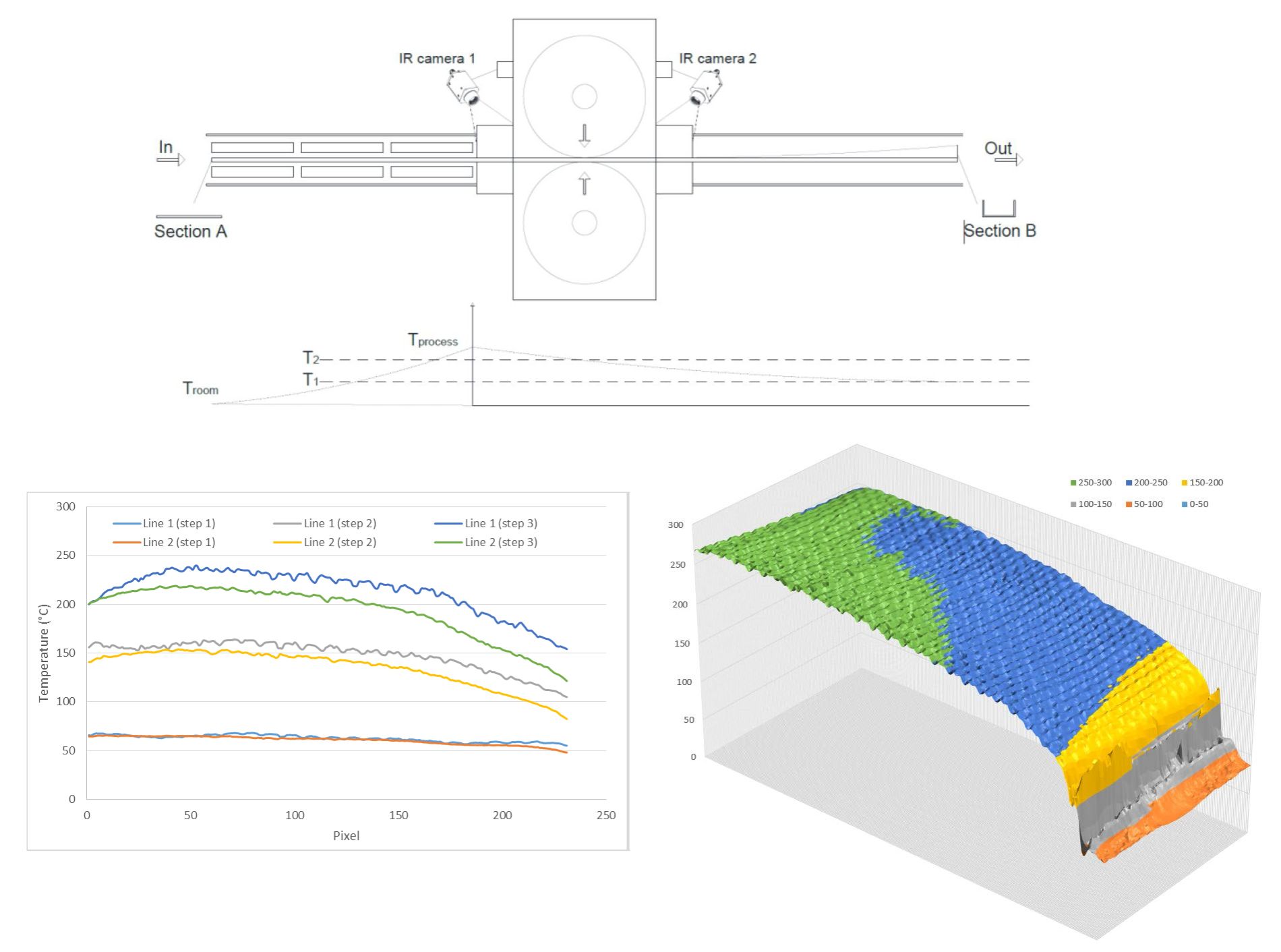
Mas como isso é novo em comparação com o CCM usado por mais de uma década pelo Xperion, agora XELIS (Markdorf, Alemanha)? “Desenvolvemos modelos analíticos e numéricos capazes de prever defeitos como vazios”, diz Pappadà. “Fizemos isso em cooperação com Leonardo e a Universidade de Salento (Lecce, Itália) para entender os parâmetros e sua influência na qualidade. Usamos esses modelos para desenvolver este novo CCM, onde podemos ter uma espessura muito alta, mas também alta qualidade. Graças a esses modelos, podemos otimizar a temperatura e a pressão, mas também como aplicá-las. Existem muitos aspectos tecnológicos que você pode desenvolver para ter uma distribuição uniforme de temperatura e pressão; no entanto, precisávamos entender o impacto disso no desempenho mecânico e no crescimento de defeitos em estruturas compostas. ”
Pappadà continua, “Nossa tecnologia é mais flexível. Além disso, o CCM foi desenvolvido há 20 anos, mas não há informações sobre ele porque as poucas empresas que o utilizaram não compartilhavam conhecimento e know-how. Então, tivemos que começar do nada, apenas com nosso conhecimento de compósitos e processamento. ”
“Agora estamos trabalhando por meio de programas internos e com nossos clientes para encontrar peças para essas novas tecnologias”, diz Corvaglia. “Essas peças podem ser reprojetadas e requalificadas para iniciar a produção.” Por quê? “O objetivo é ter um avião o mais leve possível, mas também com preço competitivo. Portanto, devemos otimizar também com espessura. Mas podemos descobrir que uma peça pode ficar ainda mais leve ou identificar várias peças com um formato semelhante, o que pode permitir economias de custo significativas. ”
Até agora, ele reitera, essa tecnologia esteve nas mãos de poucos. “Mas desenvolvemos tecnologias alternativas para tornar esses processos ainda mais automatizados, adicionando conformação por prensagem mais avançada. Colocamos um laminado plano e sai uma peça pronta para usar. Estamos na fase de redesenho de peças e de desenvolvimento de CCM plano versus em formato. ”
“Agora temos na CETMA uma linha de CCM muito flexível”, diz Pappadà, “onde podemos aplicar diferentes pressões conforme necessário para obter formas complexas. A linha que desenvolveremos junto com a Leonardo será mais focada em componentes que se adaptem às suas necessidades específicas. Achamos que poderíamos ter linhas CCM diferentes para telas planas e longarinas em comparação com formas mais complexas. Desta forma, podemos manter o custo do equipamento mais baixo em comparação com as grandes prensas usadas atualmente para produzir peças TPC de geometria complexa. ”
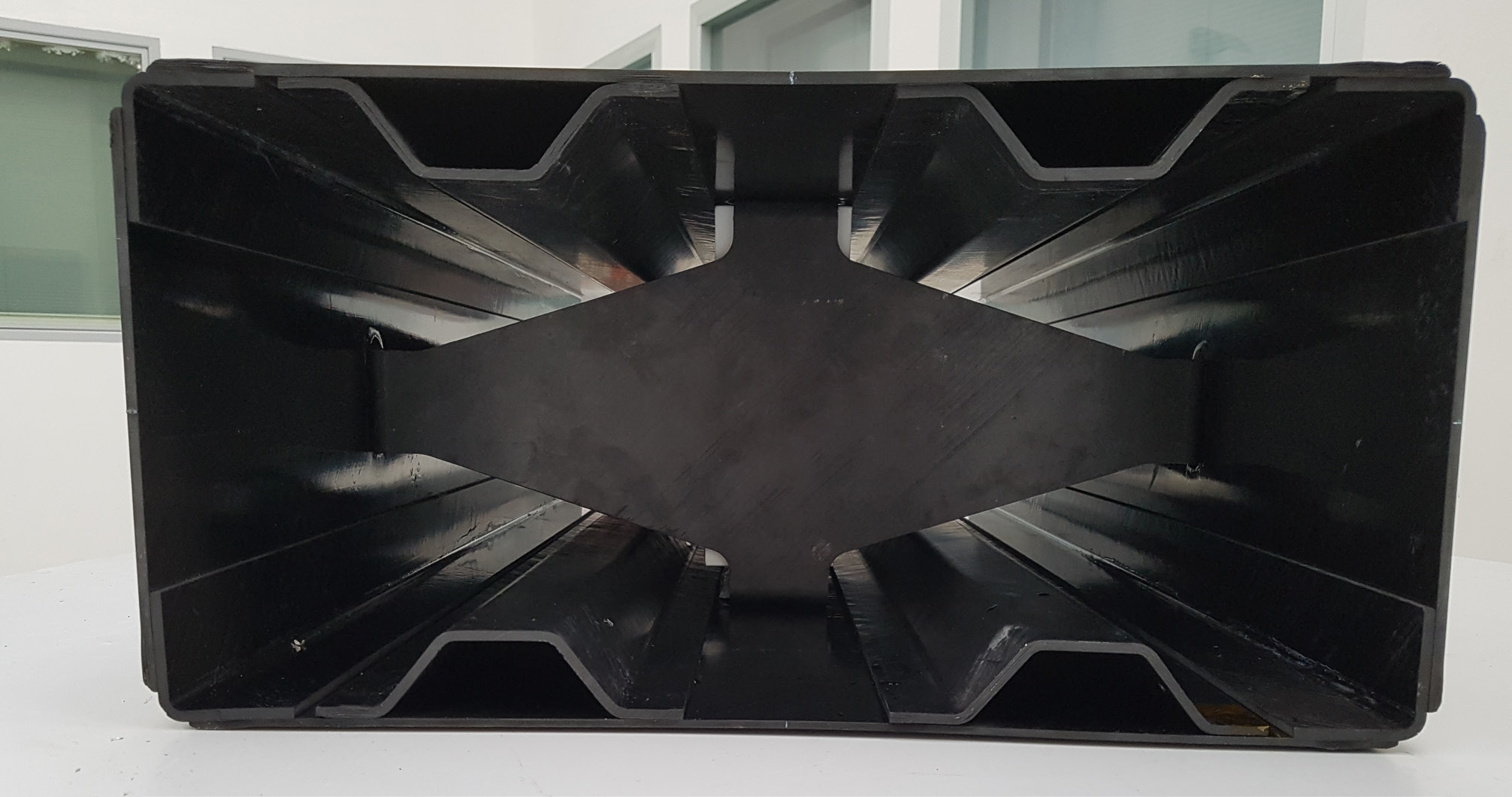
Soldagem por indução para consolidação in-situ
“A soldagem por indução é muito interessante para compósitos porque é possível ajustar e controlar a temperatura muito bem, aquecer muito rapidamente e controlar com muita precisão”, observa Pappadà. “Com Leonardo, desenvolvemos soldagem por indução para unir componentes TPC. Mas agora estamos pensando em usar soldagem por indução para consolidação in-situ (ISC) de fitas TPC. Para isso, desenvolvemos uma nova fita de fibra de carbono que pode ser aquecida muito rapidamente por soldagem por indução usando uma máquina dedicada. A fita usa os mesmos materiais de matriz das fitas comerciais, mas com uma arquitetura diferente que melhora o aquecimento eletromagnético. Estamos otimizando o desempenho mecânico, mas também pensando no processo, tentando atender às diferentes necessidades, por exemplo, como processar de forma econômica com automação. ”
Ele ressalta que o ISC é muito difícil de conseguir com fita TPC em boas taxas de produção. “Para ter isso na produção industrial, é preciso aquecer e resfriar mais rápido e aplicar a pressão de forma muito controlada. Portanto, decidimos usar solda por indução para aquecer uma pequena região apenas onde estamos consolidando o material, mas deixar o resto do laminado frio. ” A soldagem por indução usada para montagem tem um TRL mais alto, diz Pappadà. “
Usar o aquecimento por indução para consolidação in-situ parece muito perturbador - algo que nenhum outro OEMs ou fornecedores de nível está fazendo abertamente neste momento. “Sim, esta é possivelmente uma tecnologia disruptiva”, diz Corvaglia. “Patenteamos a máquina e os materiais. Nosso objetivo é algo que possa ser comparável aos compostos termofixos. Muitos tentaram AFP (colocação automatizada de fibra) com TPC, mas precisam fazer uma etapa secundária para a consolidação. Esta é uma grande limitação em termos de geometria, custo, tempo de ciclo e tamanho das peças. Podemos, de fato, mudar a forma de produzir peças aeronáuticas ”.
SQRTM
Além dos termoplásticos, Leonardo continua a olhar para as tecnologias RTM. “Esta é outra área em que trabalhamos com a CETMA e patenteamos novos desenvolvimentos baseados em uma tecnologia mais antiga, neste caso, SQRTM. A moldagem por transferência de resina com a mesma qualificação (SQRTM) foi inicialmente desenvolvida pela Radius Engineering (Salt Lake City, Utah, EUA). “Ter um método fora da autoclave (OOA) que nos permita utilizar um material já qualificado é importante”, diz Corvaglia. “Também nos permite usar pré-impregnados com propriedades e qualidade bem conhecidas. Projetamos, demonstramos e patenteamos uma moldura de janela de aeronave usando esta tecnologia. ”
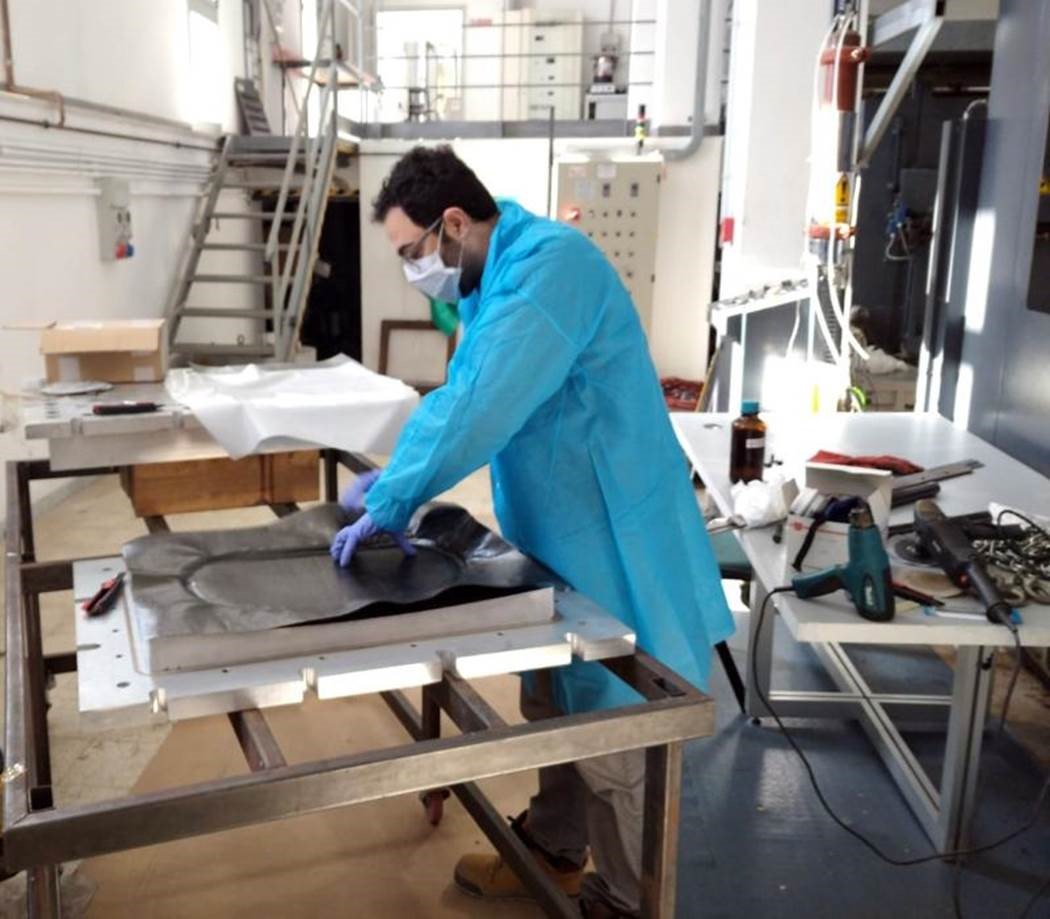
“Essa também é uma tecnologia mais antiga, mas se você entrar na web, não encontrará informações sobre essa técnica”, observa Pappadà. “O importante é que, novamente, estamos usando modelos analíticos para prever e otimizar os parâmetros do processo. Com essa tecnologia, podemos ter uma boa distribuição de resina - sem regiões secas ou acúmulo de resina - e conteúdo vazio próximo a zero. Podemos produzir alto desempenho estrutural porque podemos controlar o conteúdo de fibra e essa tecnologia pode ser usada para produzir formas complexas. Estamos usando os mesmos materiais qualificados para a cura em autoclave, mas em vez de um método OOA, mas você também pode decidir usar resinas de cura rápida para reduzir o tempo de ciclo para minutos. ”
“Mesmo com o prepreg atual, reduzimos o tempo de cura”, observa Corvaglia. “Por exemplo, em comparação com um ciclo normal de autoclave de 8-10 horas, podemos atingir 3-4 horas com SQRTM para uma peça como uma moldura de janela. Calor e pressão são aplicados diretamente na peça, e a massa para aquecer é menor. Além disso, o aquecimento da resina líquida em relação ao ar em uma autoclave é mais rápido e a qualidade da peça é excelente, o que é uma vantagem especialmente para formatos complexos. Não há retrabalho, vazios quase nulos e excelente qualidade de superfície porque a ferramenta está controlando, não um saco de vácuo. ”
Futuro visionário e baseado em tecnologia
Leonardo está produzindo inovação em um amplo e diversificado conjunto de tecnologias. Devido à rápida evolução da tecnologia, vê o investimento em P&D de alto risco (baixo TRL) como fundamental para desenvolver as novas tecnologias necessárias para os produtos futuros, que vão além do desenvolvimento incremental (curto prazo) que já sustenta nos produtos atuais. Essa combinação de estratégias de curto e longo prazo são combinadas no plano mestre de P&D de Leonardo para 2030, uma visão unificada para uma empresa sustentável e competitiva.
Como parte desse plano, está lançando o Leonardo Labs, uma rede internacional de laboratórios de P&D corporativos dedicados à pesquisa avançada e inovação tecnológica. Para 2020, a empresa buscará abrir os seis primeiros Laboratórios Leonardo nas áreas de Milão, Torino, Gênova, Roma, Nápoles e Taranto e está recrutando 68 pesquisadores (Leonardo Research Fellows) com habilidades nas seguintes áreas:36 vagas em Inteligência Artificial e sistemas inteligentes autônomos, 15 em big data analytics, 6 em computação de alto desempenho, 4 em eletrificação de plataformas aeronáuticas, 5 em materiais e estruturas e 2 em tecnologias quânticas. Leonardo Labs desempenhará o papel de postos avançados de inovação e geradores das tecnologias futuras de Leonardo.
Notavelmente, as tecnologias que Leonardo comercializa em aeronaves também podem ter aplicações em suas divisões terrestres e marítimas. Fique ligado para mais atualizações sobre o Leonardo e seu impacto potencial em composições.
Resina
- Compósitos TPE ultraleves para calçados
- Foam PP para melhorar a sustentabilidade e o custo
- Compostos de grafeno e polímero para aplicações de supercapacitor:uma revisão
- Personalização de sensores ultrassônicos para otimização e controle de processos compostos
- OTOMcomposite desenvolve software para produção de Composites 4.0 usando colocação e enrolamento assistido por laser
- Resinas epóxi reprocessáveis, reparáveis e recicláveis para compósitos
- Compostos Solvay selecionados para catamarã de corrida
- Consórcio de compósitos termoplásticos visa produção de alto volume para automotivo e aeroespacial
- Impacto Ambiental da Fabricação de Semicondutores e Eletrônicos
- Sensor de gás vestível para monitoramento de saúde e meio ambiente