7 processos de depósito e como otimizá-los
Qualquer armazém, centro de distribuição ou centro de distribuição precisa gerenciar um fluxo constante de estoque dentro e fora da instalação. A tecnologia facilitou muito esse processo com plataformas centralizadas como um Warehouse Management System (WMS). Esses programas de software podem ser conectados a sensores, scanners e códigos de barras para criar um ambiente de trabalho digital e automatizado.
Para otimizar o fluxo de estoque, os gerentes de armazém devem dividir a distribuição do trabalho em etapas específicas. Neste post, vamos rever os sete principais processos dentro de um armazém e discutir como cada um deles pode ser otimizado. Observando todo o sistema como um todo, é possível identificar etapas importantes que podem ser simplificadas para tornar o armazém mais eficiente. O objetivo final de qualquer plano de melhoria deve ser melhorar a precisão do estoque, a precisão da previsão de demanda e outras métricas importantes do local.
1. Recebendo
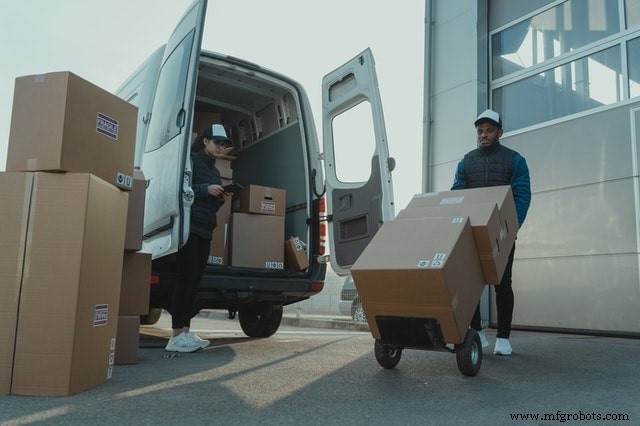
O processo de recebimento é crítico em um ambiente de armazém porque define o ritmo de todas as outras atividades dentro da instalação. Uma operação eficiente deve ter um layout de área de recebimento bem organizado para evitar um acúmulo desnecessário de entregas. Para otimizar as atividades de recebimento, pode ser benéfico instalar transportadores e outras formas de equipamentos automatizados de manuseio.
O equipamento de manuseio pode ser especialmente útil se houver uma grande quantidade de espaço entre a área de recebimento e outros locais para armazenamento temporário e de estoque. Também é recomendável automatizar os procedimentos de recebimento usando códigos de barras que podem ser digitalizados rapidamente a qualquer momento. Outra prática recomendada é buscar Avisos de Remessa Avançado (ASNs) com seus fornecedores, que podem ser digitalizados após o recebimento para adicionar itens rapidamente ao estoque.
2. Armazenamento
O próximo processo em um fluxo de trabalho de armazém típico é o armazenamento, quando as mercadorias são movidas das áreas de recebimento para as áreas de armazenamento. Uma das considerações mais importantes ao gerenciar o estoque é escolher os locais certos para armazenamento. Para tornar o processo de armazenamento rápido e eficiente, é importante definir os locais de armazenamento com antecedência e criar caminhos de viagem claros para pessoas e empilhadeiras dentro do armazém.
Esses locais podem ser rotulados com etiquetas de piso de armazém, placas e etiquetas retrorrefletivas de armazém, placas de armazém suspensas e placas de corredor de armazém que sejam claramente visíveis e/ou escaneáveis a distâncias maiores, como de uma empilhadeira, para permitir que os trabalhadores localizem rapidamente os locais de armazenamento corretos para tarefas de armazenamento. Etiquetas e etiquetas de código de barras de paletes e etiquetas de código de barras para sacolas, bandejas e contêineres retornáveis também podem ajudar os funcionários do armazém a organizar o estoque nas áreas de armazenamento apropriadas. Uma plataforma WMS pode ajudar tremendamente ao atribuir locais de estoque e digitalizar itens dentro e fora do armazenamento.
3. Armazenamento
Para planejar adequadamente os locais de armazenamento em uma fábrica, o layout deve ser cuidadosamente considerado para maximizar a quantidade de espaço útil. O plano de organização específico para cada depósito será exclusivo com base nas necessidades de negócios, estrutura das instalações e sistemas locais usados.
Uma das melhores maneiras de otimizar o armazenamento é definir métricas claras que possam rastrear a utilização e a eficiência de diferentes tipos de mercadorias. Isso ajudará a identificar melhorias, como realocar o estoque de baixa movimentação para um local de armazenamento posicionado longe de vias movimentadas.
4. Seleção
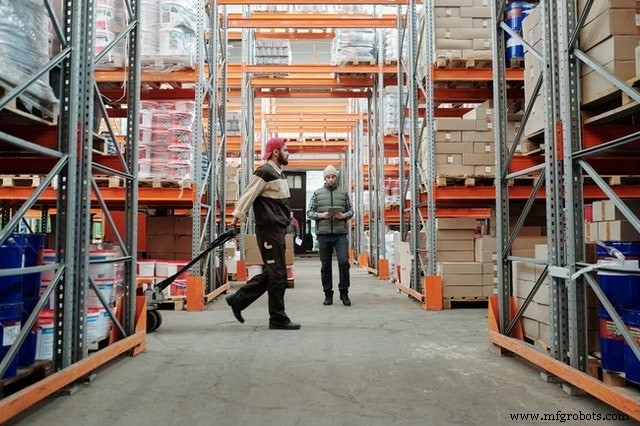
Picking é um processo necessário em qualquer armazém para selecionar mercadorias que precisam ser enviadas para atender pedidos. Uma quantidade significativa de custo e tempo é dedicada às tarefas de separação e é uma das etapas mais importantes para otimizar. Um processo de separação eficiente hoje deve ser viabilizado pela tecnologia.
Embora existam muitas metodologias de separação que podem ser empregadas, as etiquetas de rack de armazém integradas a um sistema de software permitirão que você acompanhe a eficiência em várias etapas individuais e encontre maneiras de gerar melhorias adicionais. As etiquetas de rack de armazenamento a frio e os cartazes de rack de armazenamento a frio possibilitam a etiquetagem de racks de armazém mesmo em áreas de armazém com controle climático. Compreender a precisão do picking em seu armazém também pode ajudar na tomada de decisões sobre ajustes na estratégia de picking e necessidades de pedidos individuais.
5. Embalagem
Quando um pedido de venda é recebido pelo depósito e os itens são separados, eles devem ser embalados e preparados para expedição. A otimização desse processo geralmente envolve a racionalização dos materiais de embalagem e o aumento da velocidade das inspeções. Também é importante que cada item tenha uma cadeia de custódia completa dentro do armazém para que o movimento possa ser rastreado caso seja identificado um problema.
6. Envio
O processo de envio, ou expedição, é a última etapa antes que os itens saiam do armazém. Para minimizar os atrasos nas docas de carregamento, os pedidos devem ser cuidadosamente coordenados com o gerenciamento do centro de distribuição para garantir que as mercadorias sejam coletadas assim que estiverem prontas. Uma das melhores maneiras de otimizar o envio é organizar as atividades de coleta em “ondas” para que vários pacotes relevantes possam ser preparados para uma única coleta.
7. Devoluções
Uma etapa adicional que merece atenção cuidadosa é o processo de devolução. Embora não seja uma parte desejável do gerenciamento de depósitos, as devoluções são uma realidade empresarial. Todas as empresas devem utilizar um procedimento de Autorização de Gerenciamento de Devolução (RMA) para atribuir um número único para cada devolução e fornecer instruções ao cliente. Também é importante ter um espaço dedicado dentro do armazém para lidar com devoluções e estoque para reabastecimento.
Como você pode ver, esses sete processos principais se conectam entre si dentro do armazém e não podem ser gerenciados no vácuo. Observando todo o sistema como um todo e identificando métricas úteis para cada etapa principal, é possível fazer melhorias até mesmo no design de armazém mais avançado. Esperamos que as dicas apresentadas neste post o ajudem a identificar algumas áreas de melhoria em sua própria operação de armazém.
Tecnologia industrial
- Sete erros comuns de pick-and-pack - e como corrigi-los
- Seis erros comuns de logística e como evitá-los
- Sete desafios de entrega da última milha e como resolvê-los
- Como abordar a segurança cibernética por meio de tecnologia, pessoas e processos
- Quatro tipos de ataques cibernéticos e como evitá-los
- Três armadilhas da entrega na última milha - e como evitá-las
- Sete erros comuns de remessa e como evitá-los
- 4 principais causas de falha de aparelhagem e como evitá-las
- Principais causas de falha de máquina e como evitá-las
- 3 principais processos de depósito (e como melhorá-los)