Design em destaque:adaptação do aditivo à moldagem por injeção
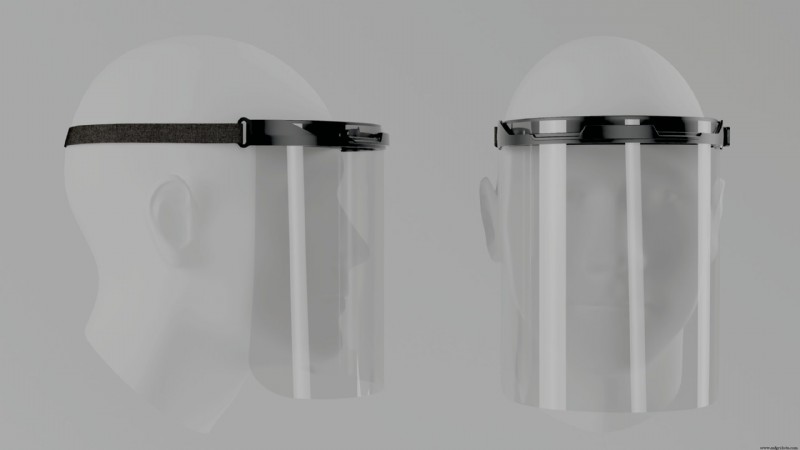
À medida que a pandemia do COVID-19 atingiu os Estados Unidos, nossa equipe da Fast Radius rapidamente direcionou uma parte significativa de nossos recursos de manufatura aditiva para a produção de protetores faciais. Até o momento, fabricamos e enviamos milhares de protetores faciais fabricados com aditivos para proteger os trabalhadores da linha de frente do coronavírus. A blindagem é reutilizável, extremamente durável, fácil de montar e confortável, mas a demanda excedeu em muito nossa capacidade de produção aditiva.

Para tornar nosso produto disponível para mais pessoas, decidimos mudar a produção para moldagem por injeção. A moldagem por injeção torna o escudo mais acessível em dois aspectos; ela nos permite produzir um volume muito maior, e a moldagem por injeção reduz significativamente o custo do produto devido aos custos de material mais baixos e à fabricação mais rápida.
Em nosso trabalho com os clientes, muitas vezes usamos a tecnologia aditiva para fabricar peças enquanto avançamos para a produção de moldagem por injeção. Nossa própria história é um forte exemplo de como usar a tecnologia de manufatura digital para redesenhar um produto aditivo para moldagem por injeção.
Iteração de design rápida com ferramentas de simulação
Precisávamos fazer modificações significativas no design aditivo do escudo “halo” (ou headband) para torná-lo adequado para moldagem por injeção, mantendo seu desempenho. Sabíamos que a rigidez precisava ser otimizada para reduzir as condições do aço fino que poderiam causar danos à ferramenta durante as operações de moldagem. Como sabíamos que a rigidez do halo atual funcionava bem, simulamos o deslocamento flutuante do halo aditivo e usamos esse deslocamento como objetivo para a rigidez do projeto moldado por injeção.
Para entender os elementos que contribuem para a rigidez, usamos a Análise de Elementos Finitos (FEA) para identificar as variáveis de projeto que produziram melhores resultados. Contamos com o pacote de simulação do Autodesk 360, uma ferramenta que usamos para diversas finalidades, incluindo projeto, análise e simulação. Testamos os padrões de coroa e nervuras na frente do anel externo. Embora as nervuras adicionassem alguma rigidez, descobrimos que adicionar altura à coroa era uma maneira mais eficaz de minimizar o deslocamento.
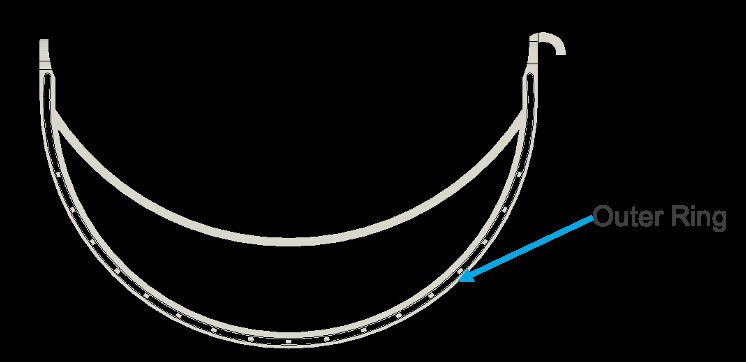
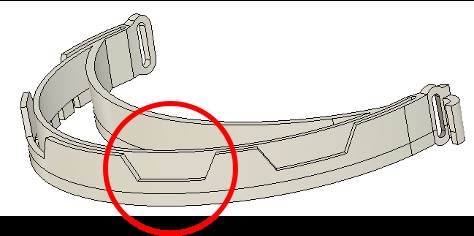
Adicionar altura à coroa, no entanto, pode criar más condições da ferramenta (aço ferramenta fino) entre os anéis externo e intermediário. A ranhura onde a própria blindagem é inserida é muito fina — tão fina quanto um a dois milímetros; quanto mais altas as seções na coroa, mais aço fino seria necessário para a ferramenta, tornando mais provável que o aço da ferramenta fosse danificado durante a operação de moldagem.
Precisávamos encontrar a altura ideal da coroa que reduzisse o aço fino, preservando a rigidez no anel externo do halo. Para determinar isso, executamos 16 simulações, ajustando ligeiramente o design para melhorar o desempenho a cada vez. Nesta fase do processo de projeto, já tínhamos atingido nosso objetivo e tínhamos muitos projetos com deslocamento semelhante ou melhor que o halo aditivo.
Prototipagem rápida com HP Multi Jet Fusion (MJF)
Dos conceitos que simulamos, escolhemos três para imprimir com HP MJF, pois essa é a tecnologia que usamos para produzir nosso halo aditivo original. Normalmente, levaria três dias para uma peça MJF esfriar o suficiente para poder ser usada, mas nossa equipe de engenheiros de fabricação embalou a construção de uma maneira que nos permitiu ter nossas peças em mãos no dia seguinte.
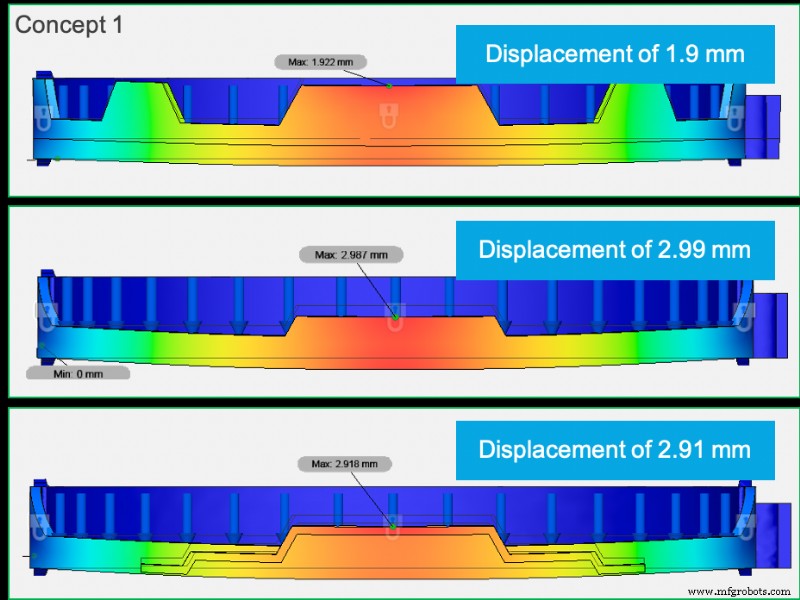
A equipe de operações da fábrica Fast Radius Chicago usou os três halos conceituais e os comparou com a versão original fabricada com aditivos para comparar conforto e facilidade de montagem. O conceito 10 (veja acima, terceiro projeto) aceitou o escudo mais facilmente, mas eles sugeriram várias modificações para melhorar o conforto e facilitar a montagem. O design resultante (veja abaixo) foi usado para produzir as ferramentas de moldagem por injeção que farão a próxima versão do nosso halo de proteção facial.

Em última análise, mudar da manufatura aditiva para a moldagem por injeção tornará o halo muito mais acessível para quem precisa. Conseguimos reduzir o preço em 55%.
Quando começamos a fazer halos aditivos, estávamos atendendo a uma demanda que não tínhamos como prever. Quando ficou claro que poderíamos tornar nosso produto mais acessível, modificamos nosso design aditivo para moldagem por injeção e colocamos uma ferramenta em produção em apenas três dias.
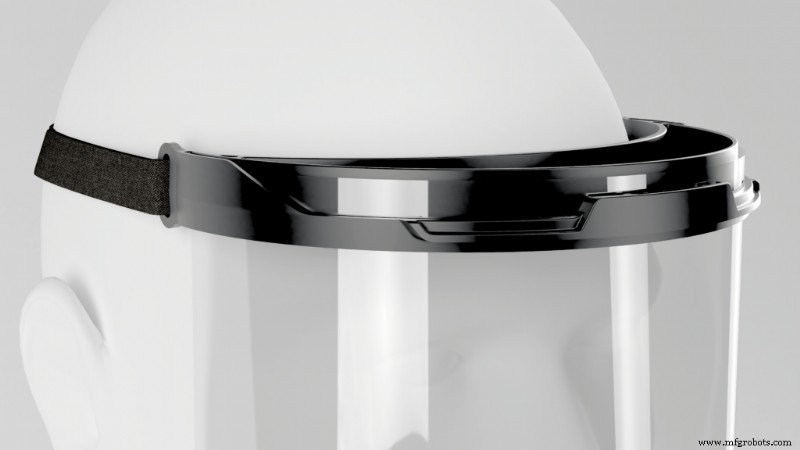
Nossa equipe trabalhou 24 horas por dia para colocar esse importante produto no mercado. Conseguimos esse cronograma notável graças em grande parte ao software de simulação, fabricação digital e nosso modelo de trabalho ágil. Essa pandemia nos forçou a nos tornar mais flexíveis com os ciclos de desenvolvimento de produtos, uma tendência que achamos que continuará por muito tempo após a pandemia.
Pronto para fazer suas peças com Fast Radius?
Comece sua cotaçãoTecnologia industrial
- O que é moldagem por injeção de reação
- Fundição x moldagem por injeção
- Termoformagem versus moldagem por injeção de reação (RIM)
- Moldagem por injeção versus moldagem por injeção de reação (RIM)
- Moldagem por fundição versus moldagem por injeção de reação
- Dicas de design para moldagem por fundição
- Serviços de design da Protocase:6 dicas
- Projeto de portão de moldagem por injeção:um guia definitivo para fabricação de plástico
- Moldagem por injeção de alumínio na fabricação de produtos
- Draft Angle for Injection Molding:Design Guide and Best Practices