8 dicas para moldagem por injeção econômica
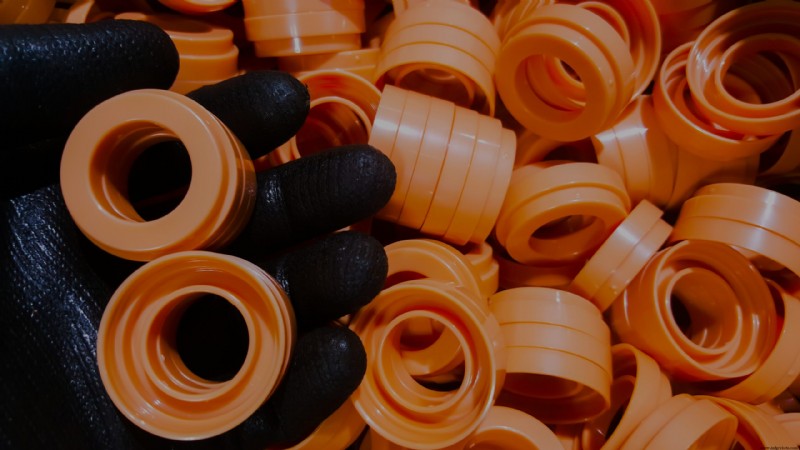
A moldagem por injeção é um processo de fabricação que usa um bico pressurizado para injetar material fundido em um molde de metal durável, ejetar a peça depois de definida e reabastecer o molde em rápida sucessão. Isso permite a produção econômica de peças idênticas com tolerâncias repetíveis em alto volume, incluindo produtos como componentes de garrafas plásticas, dispositivos médicos, caixas de eletrônicos e peças automotivas.
Um processo altamente adaptável, a moldagem por injeção é compatível com uma ampla gama de materiais e permite uma boa flexibilidade de projeto em termos de geometria da peça. Mas quanto custa a moldagem por injeção? Pode ser um método de produção bastante caro, devido ao investimento de tempo e fundos necessários para ferramentar e testar adequadamente os moldes de aço endurecido - como tal, as equipes de produto podem se beneficiar ao encontrar algumas maneiras eficazes de reduzir custos ao longo do processo de desenvolvimento do produto . Aqui estão alguns lugares para começar.
1. Evite rebaixos
Os rebaixos são recursos de design salientes (como guias de encaixe rápido) que impedem que uma peça seja ejetada do molde sem danos. Em muitos casos, os rebaixos podem ser evitados orientando os recursos da peça para que fiquem paralelos à linha de tração quando o molde estiver aberto. No entanto, se os rebaixos forem inevitáveis, a incorporação de ações secundárias será benéfica a longo prazo, mas aumentará os custos de moldagem por injeção.
2. Projete peças (e moldes) com eficiência
O objetivo de projetos de moldagem por injeção eficientes deve ser atingir requisitos predefinidos, minimizando o uso de material e sem sacrificar a qualidade. A remoção de recursos de moldagem por injeção personalizados desnecessários, como marcas, superfícies texturizadas e números de peças de projetos de moldes, é fundamental para manter os custos baixos.
A incorporação de material adicional no projeto da peça pode danificar a integridade estrutural de uma peça. Isso ocorre porque peças grandes e seções grossas não apenas são propensas a empenamento e afundamento, mas também aumentam os custos de material e os tempos de resfriamento. Além disso, otimizar a orientação da peça dentro de um molde pode melhorar as taxas de preenchimento, minimizar o material de refugo e reduzir os custos.
3. Use moldes com várias cavidades
Se o material e a geometria permitirem, incluir cavidades de peças adicionais em um projeto de molde é uma maneira bastante direta de aumentar a eficiência da produção. Embora as cavidades adicionais aumentem o custo de corte de moldes individuais, elas são muito mais econômicas de produzir do que moldes e ferramentas separados para cada peça. Os moldes de várias cavidades aumentam a velocidade de produção e ajudam a reduzir significativamente o custo de produção por unidade ao longo do tempo.
4. Consolide peças semelhantes no mesmo molde
Se famílias de peças ou vários projetos de moldagem por injeção de plástico envolvem componentes que utilizam o mesmo material e são aproximadamente do mesmo tamanho, é possível que eles possam ser consolidados em um único molde, outra forma de reduzir os gastos com ferramental. Isso é chamado de “molde familiar”.
A união de componentes de peças com uma dobradiça viva ou recursos de autoacoplamento é outra maneira de eliminar as etapas de pós-processamento (embora isso possa limitar as opções de materiais viáveis para aqueles como polipropileno, que oferece boa durabilidade e flexibilidade).
5. Otimize as tolerâncias das peças
Embora um grau de variação seja inevitável na fabricação, as tolerâncias – ou a faixa aceitável de variação entre componentes e execuções – permitem que as equipes de produto garantam que as peças viáveis tenham tamanho, formato e qualidade consistentes.
Tolerâncias mais apertadas requerem melhor definição de molde, e os custos de usinagem CNC associados a ferramentas de tolerância apertada aumentam rapidamente. Se houver espaço para flexibilidade na tolerância de uma peça, as equipes de produto podem reduzir potencialmente as despesas com ferramentas especificando apenas tolerâncias críticas.
6. Modifique os moldes em vez de criar novos
Se uma peça passar por várias iterações antes que um projeto viável seja finalizado, as equipes de produto poderão cortar custos modificando seus moldes existentes em vez de criar novos. Projetar insertos de ferramentas ou reusinar um molde em etapas para incluir recursos adicionais elimina a necessidade de várias rodadas de ferramentas. Fazer isso geralmente reduz drasticamente os custos de desenvolvimento.
7. Aproveite as ferramentas de análise de preenchimento de molde
Ferramentas de moldagem por injeção, como o software de simulação de preenchimento de molde, podem ser fundamentais para refinar o projeto do molde antes do início da ferramenta. Os protótipos de moldes digitais permitem que as equipes melhorem a eficiência de resfriamento, otimizem os tempos de ciclo e testem problemas como taxas de preenchimento irregulares, bolsas de ar e empenamento. Devidamente implementadas, essas ferramentas contribuem para moldes de alta qualidade e evitam revisões dispendiosas.
8. Monitore o tempo de ciclo
Tempos de ciclo mais rápidos reduzem o custo unitário de produção. Em geral, o tempo do ciclo de moldagem por injeção supera o de outros métodos de fabricação, permitindo a produção rápida e econômica de peças em grandes volumes.
O material da peça, a geometria da peça e a composição do molde afetam a rapidez com que a resina termoplástica resfria - que é um dos principais impulsionadores do tempo de ciclo. O alumínio oferece melhores taxas de transferência térmica do que os aços avançados de alta resistência - permitindo tempos de ciclo mais rápidos - mas também é muito menos durável e, portanto, não pode produzir tantas peças.
Moldes de aço endurecido levam mais tempo para serem usinados, mas são menos propensos a serem danificados por geometrias de componentes intrincadas ou materiais difíceis. Os moldes que requerem aquecimento e resfriamento devem ser equipados com circuitos de água para melhorar o tempo de ciclo.
Comece a melhorar a eficiência de custos hoje
A eficiência operacional é a chave para reduzir os custos de produção da moldagem por injeção e pode ser alcançada através de uma combinação de etapas, incluindo a simplificação do projeto da peça para tempos de ciclo ideais, limitando o tempo de ferramenta caro e adicionando várias peças semelhantes ao mesmo molde. Por fim, uma das maneiras mais confiáveis e eficazes de manter os custos baixos é fazer parceria com um fabricante especializado como a Fast Radius.
A Fast Radius fornece soluções de fabricação sob demanda altamente flexíveis e eficientes, desde moldagem por injeção e fundição de uretano até serviços de fabricação aditiva de nível industrial. Nossa equipe é especializada em otimizar processos de ponta a ponta para tornar o desenvolvimento, a produção e o atendimento de produtos mais eficientes e econômicos. Entre em contato conosco hoje para saber mais.
Visite o centro de aprendizado Fast Radius para ler mais sobre moldagem por injeção, incluindo nossos guias sobre termoplásticos comuns e aditivos de materiais.
Pronto para fazer suas peças com Fast Radius?
Comece sua cotaçãoTecnologia industrial
- Tutorial de moldagem por injeção:Vídeos
- Por que o design do ângulo de inclinação é essencial para moldagem por injeção?
- Materiais para moldagem por injeção de reação (RIM)
- Dicas de design para moldagem por fundição
- Processo de moldagem por injeção
- Moldagem por injeção de plástico:tecnologia para as necessidades atuais
- Diferentes tipos de texturas de molde para moldagem por injeção
- Opções de materiais para moldagem por injeção
- Quando usar a impressão 3D para ferramentas de moldes de injeção
- Dicas de design para moldagem por injeção