Forno de arco elétrico DC
Forno elétrico a arco DC
O forno elétrico a arco (EAF) DC (corrente contínua) é um forno para siderurgia primária que representa um conceito diferente nos projetos de fornos a arco. DC-EAF tem apenas um único eletrodo que atua como um cátodo e a corrente flui deste eletrodo de grafite para um ânodo que é montado na parte inferior do forno. O eletrodo de grafite único explora a transferência de calor altamente eficiente do arco gerado entre o eletrodo superior de grafite e o ânodo fornecido pela carga do forno. Uma visão típica de um DC-EAF é mostrada na Fig 1.
Fig 1 Vista típica do DC-EAF
O forno a arco DC-EAF compreende tipicamente um invólucro de aço cilíndrico revestido de refratário, com um eletrodo central de grafite posicionado verticalmente através de uma abertura no centro do teto. A conexão anódica na fornalha do forno está em contato direto com a camada de aço líquido que é coberta por uma camada de escória líquida. A energia é fornecida por meio de um arco de plasma aberto (Fig. 2) que é gerado entre a ponta inferior do cátodo e a superfície superior da escória fundida. Pelo menos uma porção central da superfície da escória está aberta. Como o forno é alimentado eletricamente, temperaturas muito altas (superiores a 1500°C) podem ser alcançadas.
DC-EAF é uma alternativa ao EAF baseado em CA (corrente alternada). A saída do transformador UHP (ultra high power) é convertida em DC usando um retificador de potência geralmente tiristores conectados em ponte. O DC-EAF equipado com sistemas retificadores de alta potência controláveis garante um arco estável em todas as condições, com a potência máxima possível. O arco em um DC-EAF é um jato sustentado de alta velocidade e alta temperatura, impulsionado pela aceleração eletromagnética (o efeito Maecker) na região constrita perto da raiz do arco na superfície do eletrodo. O arco é gerado pela interação entre o fluxo de fluido, o campo térmico e os campos eletromagnéticos. As forças eletromagnéticas autoconstritoras mantêm esse jato de plasma supersônico superaquecido (Fig. 2) razoavelmente coerente. Um reator DC é usado para estabilizar ainda mais o arco. Além disso, a superfície do banho líquido (ou pelo menos uma porção da superfície na zona de fixação do arco) é aberta, isto é, essencialmente descoberta pelo material de alimentação que não reagiu. O diagrama esquemático de um DC-EAF é mostrado na Fig 2.
Fig 2 Diagrama esquemático de um DC EAF
O DC-EAF possui vários requisitos exclusivos em relação aos fornos CA, além das diferenças óbvias no fornecimento de energia elétrica. As características importantes do DC-EAF são (i) design robusto e confiável, (ii) alta flexibilidade em relação aos materiais de carga (iii) alta densidade de corrente e uso de energia, (iv) alta estabilidade do arco, (v) boa qualidade de energia mesmo sob condições de rede fracas e (vi) controle independente de tensão e corrente. Outras características de um DC-EAF em comparação com AC-EAF são fornecidas abaixo.
- A operação é mais estável. A fusão é uniforme.
- Reduziu o consumo de eletrodos devido aos regulamentos do sistema. O consumo de eletrodos é reduzido para cerca de um terço. No entanto, há necessidade de melhorar a fragmentação e fissuração dos eletrodos. O menor consumo de eletrodos permite fazer aquecimentos de baixo carbono.
- Tem desgaste do forro inferior. O consumo de refratários é menor nas paredes laterais e mais no fundo. A economia geral no consumo de refratários está na faixa de 15% a 25%.
- Há agitação por convecção do banho.
- A distribuição de temperatura do banho é melhor. Melhor distribuição de temperatura resulta em melhor distribuição de calor. Os pontos quentes na parede do forno no caso de AC-EAF não estão lá.
- Os níveis de ruído são muito mais baixos (reduzem de 105 dB para 85 dB).
- Os custos de instalação são mais altos (cerca de 10% a 35% a mais).
- Os custos operacionais são mais baixos (cerca de 15% a 20% menos).
- Há menos distúrbios na rede. Há uma redução acentuada no efeito de cintilação. O nível de cintilação e a frequência de cintilação são reduzidos pela metade. A necessidade de equipamentos de compensação de Var é muito menor.
- Há menor consumo de energia. Há 5% a 10% de economia de energia.
- Os eletrodos inferiores tornam o fundo do forno complicado.
- Tem níveis mais baixos de emissões de poeira e gases.
O desenvolvimento da tecnologia de forno a arco DC
Acredita-se geralmente que o forno a arco DC é um desenvolvimento recente. Isso é apenas amplamente correto. Já em 1881 na Alemanha e em 1885 na Suécia, foram descritos fornos de fusão que utilizavam a tecnologia DC. Esses fornos tinham duas abordagens para a fusão a saber (i) o conceito de um arco de queima entre um eletrodo de grafite e uma carga metálica, como é usado hoje, e (ii) a proposta de um arco de queima entre dois eletrodos dispostos horizontalmente, neste caso de fusão a carga apenas por radiação. Uma vez que nem retificadores CC rápidos e controláveis de alta corrente nem uma solução para o problema de altas perdas térmicas estavam disponíveis durante esse período, o forno a arco CC não pôde ser desenvolvido em uma unidade viável para operação sob condições industriais predominantes.
No início da década de 1970, a tecnologia DC foi desenvolvida a tal nível que se tornou razoável usar essa tecnologia para fornos a arco. A aplicação dessa tecnologia criou uma nova geração de fornos a arco para uso na indústria siderúrgica, bem como nos setores de ferro-ligas e metais não ferrosos. O forno DC de eletrodo único de grafite explorou a transferência de calor altamente eficiente do arco gerado entre o eletrodo superior de grafite e o ânodo, fornecido pela carga no forno. Aplicações bem-sucedidas nas décadas de 1980 e 1990 estabeleceram vantagens de fusão e fundição do forno DC.
Recursos básicos de design
No DC-EAF a energia elétrica é convertida em energia térmica principalmente pelo arco, que é estabelecido entre a ponta do eletrodo superior e o banho de escória. A parte superior do eletrodo é conectada como cátodo e o sistema condutor inferior é conectado como ânodo.
Os fornos DC têm apenas um braço de mastro de eletrodo e um único eletrodo de grafite. Este eletrodo atua como o cátodo. Assim, o topo do forno é menos complicado e há menos componentes a serem mantidos no caso do DC-EAF e, em geral, tem menos componentes a serem mantidos em comparação com os projetos AC. O eletrodo é consumido durante a operação de aciaria e deve ser estendido por novas peças. O braço do eletrodo é usado para regulação do eletrodo. Como há eletrodo único, a perda de grafite por oxidação é menor quando comparada com o forno a arco CA.
Para o eletrodo superior, existem requisitos especiais de grafite e precisa de um grau especial de grafite. Os requisitos especiais quando comparados com o grafite para eletrodo para AC-EAF são (i) ter menor coeficiente de expansão térmica, (ii) ter menor resistividade específica do eletrodo, (iii) ter maior condutividade térmica transversal, (iv) ter menor coeficiente de expansão térmica, e (v) melhor homogeneidade e aspereza. O DC-EAF requer um arranjo de resfriamento eficaz na área do telhado e da parede lateral para neutralizar o efeito da escória de líquido quente em contato direto com o material refratário e o aumento da radiação térmica.
O DC-EAF, no entanto, precisa de um eletrodo de retorno, o ânodo, para completar o circuito elétrico. Este ânodo é normalmente referido como o eletrodo inferior, uma vez que está localizado na parte inferior do revestimento do forno. O forno opera com um salto quente para garantir um caminho elétrico para o ânodo de retorno. Vários projetos diferentes estão disponíveis para o eletrodo de retorno inferior, incluindo eletrodos de retorno de pino metálico com refratários não condutores, eletrodo de tarugo, eletrodos de aleta de metal e refratário inferior condutivo. Estes são mostrados na Figura 3.
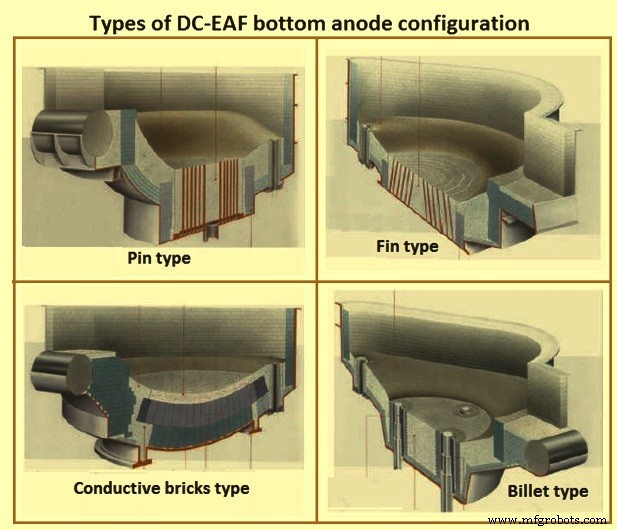
Fig 3 Diferentes tipos de configurações de anodo inferior
No caso de contato refratário condutor de corrente, o revestimento refratário no centro do fundo do forno atua como ânodo. O fundo tem um flange circular que fica dentro de um canal circular que é soldado ao invólucro do forno. No interior do canal, a flange é suportada por blocos cerâmicos reforçados com fibra. O espaço entre o canal, blocos de suporte e flange é preenchido com um composto de compactação refratário. Isso isola eletricamente o fundo do resto da carcaça do forno, como mostrado na Fig 4.
O fundo esférico do forno é feito de aço de alta temperatura. Uma placa de cobre circular é aparafusada diretamente ao fundo do forno. Quatro terminais de cobre se estendem através do fundo do forno a partir da placa de cobre e se conectam a cabos flexíveis que, por sua vez, são conectados aos tubos de barramento. Os tijolos refratários condutores são instalados sobre a placa de cobre. O fluxo de calor do fundo do forno (normalmente em torno de 15 kW/m²) é removido por resfriamento de ar forçado. Devido à grande área de superfície do eletrodo inferior, a densidade de corrente tende a ser bastante baixa, normalmente em torno de 5 kA/m². No entanto, em alguns fornos, o material de remendo não condutor é usado no centro do forno para forçar a distribuição da corrente mais uniformemente por todo o fundo. Caso a distribuição adequada da corrente não seja alcançada, isso resulta em pontos quentes no centro do forno.
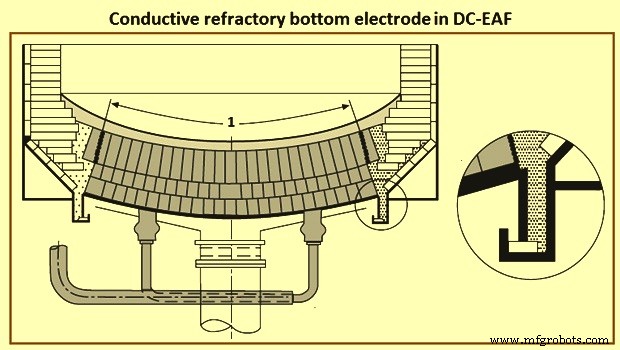
Fig 4 Eletrodo inferior refratário condutor
A configuração do eletrodo de retorno do tarugo usa de 1 a 4 tarugos de aço grandes em torno de 100 mm a 150 mm de diâmetro, mas pode ter até 250 mm de diâmetro, dependendo do tamanho do EAF. Normalmente, o projeto visa uma corrente de 40 kA a 45 kA por eletrodo inferior. Os tarugos estão em contato com o banho na superfície superior e, portanto, derretem de volta. O grau em que o tarugo derrete é controlado pelo resfriamento a água. O tarugo é inserido em uma carcaça de cobre através da qual circula a água de resfriamento. Ao fornecer resfriamento suficiente, pode-se garantir que o tarugo não derreta completamente. Os termopares monitoram a temperatura do tarugo inferior e a temperatura da água de resfriamento.
Uma bainha isolante isola a carcaça de cobre do tarugo. O tarugo é conectado a uma base de cobre. A base de cobre fornece a conexão a um cabo de alimentação. O arranjo típico de um ânodo de tarugo é dado na Fig 5.
Fig 5 Arranjo típico de um ânodo de tarugo
O eletrodo de retorno tipo pino usa vários pinos de metal de 25 mm a 50 mm de diâmetro para fornecer o caminho de retorno para o fluxo elétrico. Esses pinos são configurados verticalmente e realmente penetram no refratário. Os pinos se estendem até o fundo do forno, onde são fixados em posição por duas placas de metal. As extremidades inferiores dos pinos são ancoradas na placa condutora de energia inferior. A placa de contato inferior é resfriada a ar e está localizada no centro do fundo do forno. As partes superiores dos pinos estão alinhadas com o revestimento de trabalho no forno. Os pinos estão em contato direto com o banho e derretem à medida que o revestimento de trabalho se desgasta. Um cabo de alimentação de retorno é conectado à placa condutora inferior.
Um extenso sistema de monitoramento de temperatura é fornecido para rastrear o desgaste do revestimento e a vida útil do eletrodo inferior. Isso permite a troca programada do eletrodo inferior. O design do cartucho integral que evoluiu permite a troca rápida do eletrodo inferior durante uma interrupção programada de manutenção de 8 horas.
O eletrodo de retorno de aleta de aço utiliza aletas de aço dispostas em anel no fundo do forno para formar vários setores. Cada setor consiste em uma placa de aterramento horizontal e várias aletas de aço soldadas que se projetam para cima através do refratário. As aletas têm cerca de 1,6 mm de espessura e estão separadas por cerca de 90 mm. Os setores são aparafusados em um invólucro inferior refrigerado a ar que é eletricamente isolado do solo e conectado a condutores de cobre de 4 números.
A maioria dos DC-EAFs são operados com arcos longos, tipicamente 2 a 3 vezes aqueles encontrados nas operações convencionais de fornos UHP. Como resultado, o DC-EAF tem taxas de fluxo de água mais altas para painéis resfriados a água.
Revestimento refratário para DC-EAF
O conceito refratário de um forno CC deve ser projetado considerando as condições mais severas em que operam. Os fornos a arco DC possuem refratários especiais na parte inferior porque o ânodo é instalado na parte inferior do forno. Além dos refratários inferiores, outros pontos importantes que devem ser considerados para o projeto do revestimento refratário são o padrão de zoneamento do refratário, contorno da lareira, localização da linha de escória, tamanho do furo de derivação, ângulo e localização, orientação do telhado, tolerâncias de expansão, localização da porta do queimador , construção da porta de escória e elemento de agitação inferior.
O DC-EAF possui requisitos refratários especiais, pois o eletrodo de retorno geralmente é instalado na parte inferior do forno (alguns DC-EAFs usam um arranjo alternativo com dois eletrodos de grafite). No caso de um fundo condutor de corrente, o revestimento refratário no centro do fundo do forno atua como ânodo. Uma placa de cobre geralmente é conectada abaixo do refratário condutor e o barramento de cobre de retorno é conectado à placa. Neste caso, os requisitos especiais para o refratário são baixa resistência elétrica (preferencialmente inferior a 0,5 miliohms por metro), baixa condutividade térmica e alta resistência ao desgaste.
Uma configuração típica usa um revestimento de trabalho de 150 mm de espessura que consiste em misturas de magnésia ligadas a carbono contendo 5% a 10% de carbono. Esses materiais podem ser instalados a quente ou a frio. Abaixo do revestimento de trabalho é instalado um tijolo de carbono de magnésia de três camadas. O teor de carbono residual dos tijolos varia de 10% a 14%. Com manutenção regular, esta configuração de eletrodo inferior alcançou uma vida útil inferior de até 4.000 aquecimentos.
A configuração do eletrodo de retorno do tarugo usa de 1 a 4 tarugos de aço grandes (cerca de 250 mm de diâmetro), dependendo do tamanho do forno. Os tarugos são embutidos no refratário inferior. Os tarugos são cercados com um tijolo refratário básico. O restante da lareira é compactado com uma mistura especial de magnésia. A mistura de magnésia é usada para manter a área do tijolo ao redor do eletrodo. Esta configuração de eletrodo de retorno atingiu mais de 1.500 aquecimentos no fundo do forno.
O eletrodo de retorno tipo pino usa vários pinos de metal de 25 mm a 50 mm de diâmetro para fornecer o caminho de retorno para o fluxo elétrico. Esses pinos realmente penetram no refratário até o fundo do forno, onde são fixados a uma placa de metal. A mistura de compactação de magnésia seca é usada para todo o revestimento da lareira. Esta mistura é compactada entre os pinos metálicos. Alternativamente, o tijolo de carbono de magnésia pode ser usado na área ao redor do ânodo. Isso ajuda a melhorar a vida útil do fundo do forno, mas é mais caro. A vida útil típica do fundo varia de 2.000 a 4.000 aquecimentos, dependendo dos materiais refratários usados.
O eletrodo de retorno de aleta de aço utiliza aletas de aço dispostas em anel no fundo do forno para formar vários setores. Cada setor consiste em uma placa de aterramento horizontal e várias aletas de aço soldadas que se projetam para cima através do refratário. Mistura de compactação de magnésia seca é usada entre as aletas. A lareira também é forrada com este material.
Considerações elétricas para DC-EAF
Para alcançar o rendimento máximo do forno, o controle de potência do forno deve ser otimizado para garantir a máxima entrada de energia em todas as etapas do processo de fusão e durante as variações no material de carga. Ao mesmo tempo, a perturbação mínima da rede sempre deve ser garantida. Qualidade de energia é estar à vontade com a concessionária.
Fornecimento CC – A alta potência necessária é novamente fornecida por uma rede CA trifásica de alta tensão. Este é convertido em DC pela retificação da saída do transformador do forno. A retificação é obtida por tiristores conectados em ponte. Normalmente, os suprimentos de 12, 18 ou 24 pulsos são usados em fornos a arco, obtidos por múltiplos transformadores paralelos eletricamente deslocados um do outro, de modo que seus pulsos individuais se sobreponham uniformemente. Este deslocamento elétrico, de 15 graus, 10 graus ou 7,5 graus, correspondente aos sistemas de 12, 18 ou 24 pulsos, é feito por diversas conexões de bobinas dentro do transformador. Por esta razão, os transformadores usados para DC-EAFs são bastante diferentes daqueles para AC-EAF e geralmente são inadequados para operação de fornos AC.
A característica volt/amp de uma fonte CC consiste em uma queda fraca da tensão CC à medida que a corrente CC aumenta. A inclinação desta linha é da ordem de 1 volt por kA e é determinada pela reatância de comutação da combinação transformador/retificador, não pelo forno a arco. A fim, portanto, de limitar amplas excursões de corrente devido a tensões de arco amplamente diferentes, os tiristores são usados de preferência aos diodos. O instante de condução após o zero da corrente (atraso do ângulo de disparo) está sob o controle do terminal da porta. Cada tiristor pode, em princípio, ser desligado dentro de meio ciclo. Mesmo assim, dentro dos atrasos de vários milissegundos entre uma mudança de tensão do arco (por exemplo, um curto-circuito) e o controle dos tiristores, as correntes podem aumentar significativamente. Para reduzir a taxa de aumento da corrente é normal adicionar um reator dentro do circuito de corrente CC, sendo inadequada a reatância natural do circuito CC de alta corrente.
Esses reatores são dimensionados para ter uma indutância na faixa de 100 micro-Henry a 400 micro-Henry. Uma vez que eles tomam a corrente CC total, as perdas ôhmicas são significativas e só podem ser mantidas dentro de limites aceitáveis, empregando uma seção adequada de cobre ou alumínio que compõem as bobinas. Os tiristores são capazes de lidar com alguns kA e alguns kV de polaridade reversa. Um arranjo de tiristores conectados em série e em paralelo compõe cada perna. Fusíveis e resistores de balanceamento de tensão são usados como medidas de proteção. O resfriamento é afetado pela água deionizada.
Características elétricas do DC-EAF – O controle dos tiristores é normalmente escolhido para manter a corrente constante. Assim, a corrente AC antes do retificador também é constante, assim como a corrente primária. Considerando as potências no primário CA, vê-se que a corrente constante significa que o MVA é constante. A característica de MW em função de MVAR é, portanto, um quadrante de um círculo para o qual (quadrado de MW) + (quadrado de MVAR) =(quadrado de MVA) =constante. Normalmente, a inclinação da linha volt/amp é linear e cai tipicamente 100 V em 100 kA. Assim, a 100 kA, por exemplo, o controle dos tiristores pode manter uma corrente constante em uma faixa de tensão de arco de cerca de 900 V até um curto-circuito variando o ângulo de disparo.
Conexões inferiores – Para operar com um único arco CC é necessário fazer uma conexão elétrica (o ânodo positivo) à carga de aço. Várias soluções foram desenvolvidas para este problema. Alguns tipos de conexões inferiores para DC-EAF são mostrados na Fig 6.
Fig 6 Tipos de conexões inferiores
Em um tipo, a corrente do ânodo é compartilhada entre muitas hastes de aço embutidas em um bloco refratário compactado. As hastes, com cerca de 25 mm de diâmetro, podem chegar a um metro de comprimento e são ligadas por uma placa de cobre abaixo do casco do forno. Todo o bloco anódico pode medir de 1 m a 2 m de diâmetro. Uma variação do tipo de pino é usar chapas de aço finas, novamente embutidas no refratário. Outra variação é empregar um tarugo de aço de 250 mm de diâmetro passando por uma manga isolada, levando a uma conexão de cobre resfriada abaixo do casco do forno. Em todos esses três projetos (pino, chapa ou tarugo) a parte superior do condutor de aço derrete com o curso do calor. Ele se solidifica durante o desligamento e após o carregamento de sucata.
Uma alternativa aos projetos de corrente de aço para aço é aquela em que a corrente é levada através de refratários condutores para uma placa inferior de cobre de grande diâmetro. Em todos os tipos de conexão de fundo deve haver isolamento entre a conexão do ânodo e a carcaça do forno. Isso é para reduzir a probabilidade da corrente passar pelo invólucro diretamente para os barramentos anódicos
A qualidade de energia é a principal preocupação do sistema de alimentação de uma unidade EAF. É necessário respeitar os limites de flicker, fator de potência e harmônicos. Um algoritmo de controle de eletrodo eficaz reduz a comutação do transformador e o dimensionamento correto do reator CC e dos filtros harmônicos são necessários para atender aos requisitos da concessionária. Além disso, a redução de cintilação ativa opcional e a correção contínua do fator de potência através de um Static Var Compensator (SVC) são necessários para garantir a conformidade com as mais rigorosas demandas da concessionária e/ou permitir a operação em áreas remotas com condições de rede fracas.
A cintilação é causada principalmente por flutuações de potência reativa. Assim, é necessário um link fast-forward que envia informações do controle do retificador para o controle do SVC, permitindo o cálculo do consumo real de potência reativa do forno. Essas informações são usadas para melhorar o desempenho de mitigação de cintilação. O resultado do uso de um sistema SVC é (i) maior potência média de entrada em comparação com a compensação Var convencional, (ii) correção contínua do fator de potência próximo à unidade, (iii) controle da tensão do barramento do forno, (iv) ausência de carga desequilibrada na rede , e (v) baixos níveis de oscilação e harmônicos mesmo em grades fracas.
O estabilizador de arco é necessário para maior produtividade. Um processo estável é essencial para a operação produtiva. O uso de um projeto de reator CC otimizado (baixas perdas) para suavizar a corrente do eletrodo ajuda a manter um arco estável o tempo todo. O resultado é (i) menor estresse no sistema hidráulico do eletrodo, (ii) menos vibração, (iii) menor consumo de eletrodo, (iv) maior produtividade, (v) ainda maior redução de cintilação e (vi) menores perdas de radiação.
No caso do DC-EAF, os tiristores possuem duas terminações de cobre, uma das quais é conectada ao cabo de alimentação do EAF e outra é conectada ao eletrodo inferior do forno. O eletrodo inferior do forno é normalmente rígido, pois nenhum movimento é necessário durante a operação do forno. Em princípio, a terminação nos tiristores é análoga ao fechamento delta, embora fisicamente difere consideravelmente. No que diz respeito às questões de manutenção para o fechamento delta, no entanto, os mesmos conceitos podem ser aplicados à operação do CD.
Operações DC-EAF
O progresso na tecnologia de comutação de semicondutores de alta potência trouxe à existência fontes de alimentação DC de baixo custo e eficiência. Devido a esses avanços, a operação do forno CC de alta potência tornou-se viável. O DC-EAF é caracterizado pela retificação das tensões do transformador do forno trifásico por retificadores controlados por tiristores. Esses dispositivos são capazes de modular e controlar continuamente a magnitude da corrente de arco CC para obter uma operação estável. Os fornos DC usam apenas um eletrodo de grafite com o eletrodo de retorno integrado ao fundo do forno. Existem vários tipos de eletrodos de fundo fundo de lareira condutora, fundo de pino condutor, tarugo único ou múltiplo e aletas condutoras em uma lareira monolítica de magnesita.
Todos esses projetos de eletrodo de retorno inferior foram comprovados. Os que parecem ser usados com mais frequência são o fundo do pino condutor, onde vários pinos são presos a uma placa e formam o caminho de retorno e o design do tarugo inferior. O eletrodo inferior é resfriado a ar no caso do tipo pino e resfriado a água no caso do projeto de tarugo. A área entre os pinos é preenchida com massa de compactação e a ponta dos pinos fica no mesmo nível do revestimento interno do forno. À medida que o refratário se desgasta, os pinos também derretem.
Os DC-EAFs operam com um calcanhar quente para garantir um caminho elétrico para o eletrodo de retorno. Durante a partida em condições frias, uma mistura de sucata e escória é usada para fornecer um caminho elétrico inicial. Uma vez derretido, o forno pode ser carregado com sucata.
Alguns dos primeiros benefícios alcançados com a operação DC incluíram consumo reduzido de eletrodos (20% menor que CA de alta tensão, 50% menor que CA convencional), oscilação de tensão reduzida (50% a 60% da operação CA convencional) e consumo de energia reduzido (5 % a 10 % menor do que para AC). Os resultados acima foram alcançados principalmente em fornos menores que foram adaptados da operação AC para DC. No entanto, algumas instalações maiores de fornos DC não alcançaram imediatamente os benefícios alegados. Especialmente, surgiram duas áreas de preocupação, a saber, (i) consumo de eletrodos e (ii) consumo de refratários.
Várias operações de forno DC descobriram que a diminuição no consumo de eletrodos esperado na operação DC não ocorreu. Muitas análises dos produtores de eletrodos indicaram que as condições físicas dentro dos eletrodos são diferentes para operações de CA e CC. Como resultado, para grandes eletrodos CC transportando uma corrente muito grande, uma quantidade maior de rachaduras e fragmentação foi observada em comparação com as operações CA. Assim, tornou-se necessário desenvolver eletrodos com propriedades físicas mais adequadas à operação em CC.
O tamanho máximo econômico para fornos DC tende a ser uma função de limitações devido ao tamanho do eletrodo e capacidade de transporte de corrente. Atualmente, o tamanho máximo econômico para um único forno DC com eletrodo de grafite parece ser de cerca de 165 toneladas. Tamanhos maiores de fornos podem ser acomodados usando mais de um eletrodo de grafite.
Várias das primeiras operações DC tiveram problemas com desgaste refratário e vida útil do eletrodo inferior. Esses problemas estão diretamente relacionados ao alargamento do arco dentro do forno. O design do ânodo tem a maior influência no alargamento do arco. Em todos os fornos CC, o arco elétrico é desviado na direção oposta à fonte de alimentação devido a assimetrias nos campos magnéticos gerados pelo circuito CC. Assim, o arco tende a se concentrar em uma área dentro do forno criando um ponto quente e resultando em desgaste refratário excessivo. Várias soluções foram desenvolvidas para controlar ou eliminar o alargamento do arco. Todos os projetos de eletrodos inferiores estão atualmente configurados para forçar o arco para o centro do forno.
No caso do refratário condutor inferior e do fundo tipo pino, é necessário fornecer linhas de alimentação divididas para o ânodo inferior ou uma bobina inferior que ajude a modificar o campo magnético líquido gerado. No projeto do fundo do tarugo, a quantidade de corrente para cada tarugo é controlada juntamente com a direção do fornecimento do ânodo para controlar o arco. O projeto da aleta inferior utiliza o fato de que a alimentação elétrica ocorre em vários pontos para controlar a deflexão do arco. Quadrantes localizados mais distantes do retificador são alimentados com corrente mais alta do que aqueles localizados mais próximos do retificador.
Alguns acham que a possibilidade de maior automação das atividades de EAF é maior para o forno DC. Isso ocorre porque, com apenas um eletrodo, há um espaço maior tanto na parte superior quanto no interior do forno. Espera-se que o forno DC custe de 10% a 35% mais do que um forno AC comparável. No entanto, os cálculos de retorno indicam que esse custo adicional pode ser recuperado em um a dois anos devido aos menores custos operacionais.
Foi realizado um estudo que comparou as operações de fornos CA e CC e verificou-se que as perdas elétricas chegam a cerca de 4% em operações CA e 5,5% em operações CC, sendo a diferença em termos absolutos relativamente insignificante. A diferença no consumo total de energia entre os fornos CA e CC provavelmente será inferior a 9 kWh/ton a favor do forno CC. No entanto, muitas outras variáveis influenciam o consumo de energia e é difícil desenvolver números precisos.
Os fornos DC têm um consumo de eletrodos aproximadamente 25% menor do que os fornos AC, o que corresponde a tipicamente 0,4 kg/ton. Esta diferença parece ser maior para fornos AC menores. A cintilação é cerca de 60% menor para operações em CC, porém, os avanços nas configurações do sistema de energia CA (reatância adicional) reduziram essa diferença para 40%.
Alguns resultados típicos que foram apresentados para grandes operações DC EAF são o consumo de eletrodo de 1 kg/ton a 2 kg/ton de aço líquido, consumo de energia na faixa de 350 kWh/ton de aço líquido a 500 kWh/ton de aço líquido, tempo tap-to- tap variando de 45 minutos a 120 minutos, e vida útil inferior de 1.500 aquecimentos a 4.000 aquecimentos. É importante lembrar, no entanto, que o consumo de energia depende muito das práticas de operação, temperatura da torneira, uso de combustíveis auxiliares, tipo de sucata, etc.
Processo de manufatura
- Moedor de café elétrico feito na loja
- Guitarra elétrica
- Chaleira Elétrica de Chá
- Cobertor Elétrico
- Automóvel elétrico
- Automação de Controle e Modelagem de Forno Elétrico a Arco
- Forno de Otimização de Energia
- Utilização de Metal Quente para Siderurgia em Forno a Arco Elétrico
- Diferentes tipos de processo de soldagem a arco elétrico
- Entendendo a soldagem a arco elétrico