Projetos aprimorados e vida útil de campanha de um alto-forno
Designs aprimorados e vida útil de campanha de um alto-forno
O custo de reconstrução ou reembasamento de um alto-forno (BF) é muito alto. Portanto, as técnicas para prolongar a vida útil da campanha do BF são importantes e precisam ser seguidas de forma muito ativa.
Grandes BFs geralmente têm uma saída de campanha ligeiramente maior por unidade de volume. Essa diferença ocorre porque BFs maiores geralmente são de design mais moderno e bem automatizados. Uma vez que a viabilidade de uma siderúrgica integrada depende de um fornecimento contínuo de metal quente (HM), o que, em uma planta com um pequeno número de grandes BFs, dá grande importância à longa vida útil da campanha.
As técnicas para prolongamento da vida da campanha BF se enquadram nas três categorias a seguir.
- Práticas operacionais – O controle do processo de BF tem um grande efeito na vida da campanha. O BF deve ser operado não apenas para atender às necessidades de produção, mas também para maximizar sua vida útil. Portanto, é necessário modificar as práticas operacionais à medida que a campanha avança e em resposta às áreas problemáticas para maximizar a vida útil da campanha.
- Medidas corretivas – Quando o desgaste ou dano que afeta a vida útil do BF se torna evidente, técnicas de reparo de engenharia devem ser usadas ou desenvolvidas para maximizar a vida útil da campanha.
- Projetos aprimorados – À medida que materiais e equipamentos aprimorados são desenvolvidos, eles devem ser incorporados em futuras reconstruções para prolongar a vida útil das áreas críticas do BF, onde for econômico fazê-lo.
Projetos aprimorados do BF para melhorar a vida útil da campanha são discutidos neste artigo. O projeto correto do forno adequado é fundamental para uma operação confiável, desempenho metalúrgico, alta produtividade sustentada, longa vida útil e uma disponibilidade de mais de 98%.
O design BF teve muitas melhorias nas últimas décadas e campanhas de mais de 20 anos agora são obtidas. A blindagem bosh, pilha e garganta eram áreas críticas de projeto no passado, mas hoje a aplicação de aduelas de cobre, resfriadores de placas de cobre, grafite e SiC no bosh, barriga, pilha inferior e intermediária, em combinação com refrigeradores de aduelas de ferro fundido no pilha superior mais armadura de garganta permite longas campanhas e operações de alta produtividade. Mas agora há ênfase na importância de um design robusto de fundo e lareira.
Um projeto BF avançado requer sistemas de refrigeração de alta eficiência e alta capacidade e instrumentação e controle avançados. Tal sistema inclui instrumentação e sistemas de controle para monitorar o processo, as operações e o desempenho do revestimento.
Designs e dimensões do BF
O projeto do BF é lidar com as reações e a metalurgia. Normalmente bosh e fuste do BF estão sujeitos a erosão por coque enquanto fundo e lareira estão sujeitos a erosão por HM. É necessária a instalação de uma casca fina e independente totalmente otimizada e uma estrutura estruturalmente sólida para resistir a tensões e trincas por fadiga térmica, mesmo no final de uma campanha de BF.
O mais recente design de concha BF independente é com torre de acesso. O projeto mecânico de última geração geralmente é baseado em análises abrangentes de distribuição de tensões. O uso de aço resistente a trincas garante os menores requisitos de manutenção possíveis.
A filosofia de design da BF está orientada para o desempenho maximizado, garantindo que durante toda a campanha, o perfil interno permaneça o mais próximo possível do perfil que estava no momento da explosão. O design é otimizado com base na análise dos vários mecanismo de ataque térmico, químico e mecânico por área. Esses mecanismos de ataque são previstos dependendo do mix escolhido de matérias-primas, prática de carga e outros parâmetros do processo. Em geral, o projeto do revestimento deve se concentrar na formação de uma camada solidificada de escória e material de carga que reduz consideravelmente o efeito desses mecanismos de ataque.
As áreas críticas para atingir a meta de maximização do valor do BF devem ser identificadas e atenção especial deve ser dada ao fortalecimento dessas áreas.
O perfil do forno é decidido com base na experiência adquirida do ponto de vista do perfil e dos resultados operacionais, desgaste refratário do corpo do forno, operação estável e outras características dos BFs existentes em grande escala.
A altura do eixo é normalmente um compromisso entre requisitos opostos. Para eficiência de combustível, é desejável ter contato gás/sólido prolongado, de modo que o uso do calor sensível e poder redutor do gás possam estar mais próximos dos limites teóricos. Também é muito importante ter a altura do poço do BF acima de um determinado valor para garantir que os minérios de ferro entrem na zona coesiva com um grau máximo de metalização, para que a fornalha não resfrie e crie problemas na fundição.
Além disso, para BFs de maior volume, como regra, o volume interno do BF é expandido aumentando o diâmetro do BF com a altura do forno mantida quase inalterada. A julgar pela experiência adquirida com os resultados operacionais obtidos no passado, normalmente considera-se que dado um certo volume interno, um BF que é pequeno em altura e grande em diâmetro é melhor do que um grande em altura e pequeno em diâmetro em termos de permeabilidade e eficiência de toque
Garganta BF
A falha da armadura da garganta tem um efeito prejudicial significativo na distribuição de carga na linha de estoque e diretamente abaixo. Isso resulta na descida irregular da carga e na estabilidade do processo comprometida. Portanto, o projeto da armadura da garganta precisa ser otimizado em relação à resistência a fragmentação, flutuações de temperatura, rachaduras por tensão, fadiga e abrasão/erosão.
Para o eixo superior (área da garganta), resfriadores de aduela são normalmente empregados para manter o perfil do forno e evitar desordem na distribuição da carga juntamente com o desgaste do tijolo sob as placas de armadura da garganta (desgaste). A instalação de uma placa de suporte refrigerada a água ou caixa de resfriamento para um sistema de armadura de garganta fixa também tem sido usada para proteger partes da armadura.
Pilha, barriga e bosh
As áreas da pilha e da barriga são expostas a cargas de calor e abrasão severa. A área bosh é severamente carregada pela carga descendente que carrega e pelos gases da pista em sua vizinhança. Caso essas áreas não sejam projetadas corretamente, o corpo de resfriamento e o revestimento se desgastam a níveis críticos muito cedo após a sopragem, induzindo o risco de rupturas. Na área bosh, isso também significa que a carga é transportada pelos narizes das ventaneiras e pelos refrigeradores jumbo, causando paradas despreparadas altamente frequentes. Assim, o design bosh e pilha atualmente consiste em resfriadores de aduelas de cobre ou resfriadores de placas de cobre e grafite de alta condutividade junto com grafite de silício protetor nas áreas superiores. Este design ajuda a transferir cerca de 95% da carga de calor para a água de resfriamento, garantindo assim uma temperatura inferior a 50 graus C do invólucro BF. O sistema de resfriamento de água, o número e o posicionamento das aduelas, a vazão de água, a instrumentação e os sistemas de monitoramento de calor são totalmente otimizados para garantir uma longa vida útil do revestimento do forno e requisitos mínimos de manutenção.
O desenvolvimento de refrigeradores de aduelas levou à chamada quarta geração de aduelas de hoje. As características são tubos de resfriamento adicionais nos cantos da aduela, um tubo em forma de meandro (serpentina) adicional no lado do casco e nervuras de retenção estendidas para o revestimento refratário. Isso torna a alvenaria de proteção supérflua. As aduelas de terceira geração mostraram que rachaduras e desgaste excessivo estavam ocorrendo nos cantos e nas extremidades superior e inferior das aduelas. Na quarta geração, os tubos de canto foram incorporados para eliminar esses problemas. A adição do tubo de refrigeração sinuoso serve como um sistema de refrigeração de backup, em caso de falha de qualquer um dos outros tubos de refrigeração.
Um desenvolvimento adicional das aduelas de quarta geração é aquele em que o revestimento do forno é fixado à aduela, preso por nervuras cônicas, na própria fundição. Levando em consideração o fato de que a velocidade de desgaste do metal de aduela resfriado é um décimo ou menor que a do tijolo na frente do metal de aduela, a espessura do tijolo é reduzida para 200 mm e a espessura da aduela foi aumentada em 400 mm, de modo que a vida do tijolo da frente e da aduela permanece quase inalterada. As aduelas de quarta geração são de uma construção de unidade de parede fina composta por um tijolo fundido na aduela. A construção desta unidade eliminou a necessidade de alvenaria e minimizou a alteração do perfil da face quente, contribuindo na estabilização da operação do BF. As melhorias nos refrigeradores de aduelas, especialmente a aduela de quarta geração, aumentaram muito a durabilidade das aduelas. As vantagens gerais das aduelas de quarta geração são (i) extensão da vida útil do revestimento refratário, (ii) redução nas rachaduras e desgaste excessivo no canto da aduela e (iii) combate à perda de capacidade de resfriamento devido a falhas do tubo pelo adição de um tubo de resfriamento em forma de meandro.
Com o objetivo de estabilizar ainda mais a operação do BF através da manutenção do perfil estável da face quente, redução da espessura da parede da aduela e alongamento da vida útil da aduela, são introduzidas aduelas de cobre.
As aduelas têm a grande vantagem de resfriar toda a área do invólucro BF, enquanto as placas de resfriamento resfriam apenas áreas localizadas. No entanto, placas de resfriamento danificadas podem ser facilmente substituídas, enquanto é praticamente impossível trocar as aduelas sem soprar o forno.
No entanto, a vantagem de resfriar toda a área do invólucro BF é mais importante, e a desvantagem de não poder trocar facilmente o elemento de resfriamento deve ser superada projetando-o para uma vida útil extremamente longa e segura. Isso levou ao desenvolvimento de uma aduela com um tempo de vida alvo idêntico ao tempo de vida do BF versus 12 a 15 anos com aduelas de ferro fundido de última geração. A experiência com aduelas de ferro fundido mostrou desgaste e perda de material, primeiro nos cantos e depois nas bordas. Isso porque os tubos fundidos devem estar localizados a aproximadamente 80 mm das bordas e 110 mm dos cantos das aduelas, para atender aos requisitos de fundição e fornecer uma geometria de dobra admissível. Essas condições, juntamente com a condutividade relativamente baixa do ferro fundido, impedem que as arestas e cantos sejam resfriados adequadamente. As condições de resfriamento são ainda mais exacerbadas pelas folgas não refrigeradas relativamente largas entre duas aduelas de ferro fundido adjacentes. Além disso, os problemas de resfriamento resultam do revestimento isolante do tubo usado para evitar a captação de carbono durante a fundição, o que resulta em uma temperatura mais alta do lado quente, causando rachaduras e maior desgaste. Para evitar rachaduras nos cantos e bordas das aduelas de ferro fundido, tubos de canto foram instalados nas aduelas de quarta geração, o que significava tubos adicionais, furos na carcaça do alto-forno e requisitos adicionais de água e energia.
Esses problemas não existem com aduelas de cobre laminadas. A chapa de cobre é laminada com tolerâncias estreitas e pode ser usinada perto das laterais. Os canais de resfriamento podem ser perfurados com precisão e localizados o mais próximo possível das bordas e cantos, conforme ditado pela espessura mínima da parede necessária para evitar vazamentos sob a pressão da água. Finalmente, a folga entre as aduelas pode ser estreita, de modo que essa área crítica e não resfriada seja praticamente eliminada. Em relação às propriedades físicas, a condutividade térmica do cobre é dez vezes maior que a do ferro fundido e o fato de, devido à resistência mecânica do cobre, a temperatura precisar ser mantida abaixo de 120°C, significa que mais calor é removido do BF ao usar aduelas de cobre em comparação com outros sistemas de refrigeração de aduelas. Para evitar esse efeito, foi encontrada uma solução de projeto em que tijolos refratários de baixa condutividade e alta alumina são instalados no lado quente da aduela de cobre. De acordo com a experiência de operação, uma camada de acreção extremamente estável protege adicionalmente a aduela e evita altas perdas térmicas do BF.
Os resultados de campo com aduelas de cobre mostraram resultados muito bons. Após 9 anos de operação, as aduelas de ferro fundido geralmente apresentam fortes sinais de desgaste, rachaduras e tubos de refrigeração expostos, enquanto as aduelas de cobre têm uma aparência praticamente inutilizada, com arestas e cantos vivos. O material de cobre restante manteve suas propriedades físicas originais após esse período. Os principais aspectos técnicos do uso de aduelas de cobre estão resumidos abaixo.
- Para um sistema de aduelas de cobre com três fileiras de aduelas de cobre na área da barriga/eixo inferior e aduelas de ferro fundido na área restante, as taxas de remoção de calor e circulação de água de resfriamento são comparáveis com um sistema de aduelas de ferro fundido puro. Em alguns casos, a remoção de calor das aduelas de cobre é ainda menor do que a das aduelas de ferro fundido, devido à camada de acreção estável.
- Aduelas de cobre, em contraste com aduelas de ferro fundido e placas de resfriamento de cobre, não precisam de ressaltos ou pontas. As aduelas de cobre apresentam uma superfície lisa para o interior do BF e não interferem nas camadas de carga, o que geralmente afeta negativamente a permeabilidade ao gás na área da parede.
- Como as camadas de acreção estáveis se formam na frente das aduelas de cobre, não é necessário instalar materiais refratários caros que são substituídos por crostas após um certo tempo. Em um sistema de aduela de cobre, a possível vida adicional obtida por material refratário caro é insignificante quando comparada com a vida útil geral esperada. As aduelas podem, portanto, ser instaladas com refratários baratos.
No total, o BF refrigerado por aduela de cobre é, em suas partes relacionadas ao elemento de resfriamento, cerca de 10% mais alto em custos de investimento do que um BF com um sistema de aduela clássico e 5,4% mais caro que um BF com placas de resfriamento de cobre densamente compactadas. Isso é compensado pelo material refratário mais barato na frente das aduelas de cobre e pelo maior tempo de vida das aduelas de cobre.
Lareira BF
A operação contínua e suave do alto-forno, bem como a boa qualidade do coque, são pré-requisitos para uma longa vida útil do forno. O alto PCI (injeção de carvão pulverizado) desafia a vida útil da lareira devido à redução da permeabilidade e aumento da turbulência. O grande volume da lareira e a profundidade do reservatório reduzem as velocidades dos líquidos. Velocidades de líquidos mais baixas resultam em menor carga de calor. Menor carga de calor resulta em temperaturas mais baixas do revestimento e temperaturas mais baixas do revestimento resultam em maior vida útil.
A lareira BF enfrenta processos exigentes e condições de operação, portanto, o desempenho do revestimento da lareira é crítico. O desempenho da lareira BF é atualmente o fator limitante em muitas plantas existentes e a condição da lareira BF determina a vida útil da campanha. O fluxo de líquidos introduz um desgaste considerável por meio de mecanismos como erosão e dissolução de carbono. Além disso, a integridade estrutural da lareira provavelmente será afetada, pois a expansão durante o aquecimento pode causar deslocamento.
Como medidas para prolongar a vida útil do recuperador, é necessário aumentar a capacidade de refrigeração do recuperador e melhorar as qualidades dos blocos de carbono utilizados no recuperador. Para a seção da parede lateral da lareira que está sujeita a maior erosão (a parte abaixo de cada furo de torneira), uma aduela de ferro fundido ou aduela de cobre que oferece alta condutividade térmica também está sendo usada. Além disso, a temperatura da água de resfriamento deve ser reduzida. Para a lareira, um sistema de resfriamento de duas etapas ou sistema de resfriamento em forma de rosquinha, etc., cuja taxa de resfriamento é ajustável, é normalmente empregado para evitar que o homem morto fique inativo devido ao super-resfriamento. Para o refratário inferior, está sendo utilizada uma combinação de blocos de carbono e revestimento interno de cerâmica. A vida útil dos blocos de carbono foi prolongada principalmente por meio de melhorias na condutividade térmica e resistência ao ferro fundido dos materiais refratários. Os designs avançados da lareira BF incluem resfriamento por água no fundo e resfriamento da jaqueta da lareira, pois isso fornece mais espaço dentro da concha.
Design aprimorado da lareira e do furo de torneira
O furo do macho é exposto a um ambiente extremamente dinâmico. Não apenas as temperaturas e as pressões são altas, o ataque químico é substancial e a perfuração frequente e o entupimento do furo da torneira tornam as circunstâncias ainda mais complicadas. Projetar o furo de macho final capaz de facilitar a operação do BF para sua vida útil de campanha superior a 20 anos é um dos desafios mais exigentes impostos aos projetistas de BF. Hoje, os melhores resultados podem ser alcançados com resfriamento superior da carcaça ao redor do furo da torneira, um design de revestimento redundante e capacidade de monitoramento suficiente.
A profundidade do poço (distância do furo da torneira até a superfície inferior) da fornalha parece ser o fator decisivo no desgaste da parede da fornalha pelo fluxo de HM durante a roscagem. Recomenda-se que o morto descanse completamente no fundo da lareira ou flutue completamente no poço do HM. Para evitar o desgaste dos “pés de elefante”, a flutuação parcial do morto deve ser evitada. Devido ao desgaste do fundo com o tempo, um objeto inicialmente apoiado completamente no fundo pode tornar-se parcialmente flutuante. A profundidade do reservatório deve, portanto, ser escolhida desde o início a um nível tal que o morto possa flutuar. A profundidade crítica necessária do reservatório depende do tamanho e do método de operação do BF.
Deve-se levar em consideração que mudanças na composição da carga podem levar a uma mudança na situação e nos fluxos de HM na fornalha no rosqueamento, se a espessura média da camada de carga e, portanto, a tensão de compressão da carga no homem morto Mudou. Um exemplo é a diferença entre toda operação de coque, e operação com altas taxas de injeção de óleo ou carvão. Uma outra possibilidade para evitar o desgaste progressivo da parede da fornalha sob o orifício da torneira é afunilar a camisa da fornalha e aumentar a espessura da parede do revestimento refractário desta área.
A técnica de rosqueamento e o desenho do furo do macho têm uma grande influência na vida da campanha BF. O cálculo do modelo e os ensaios de sangria foram realizados em um modelo de água 1:10 (1,4 m de diâmetro) de um alto-forno de 14 m de diâmetro de lareira, com leito empacotado simulando o homem morto. A partir desses ensaios, foi recomendado que o BF não deve ser esvaziado até o ponto em que o gás possa escapar. A observação desta taxa pode prevenir a formação de turbilhões promotores de desgaste na área da junta fundo-parede. As interrupções do processo de rosqueamento devem ser mantidas o mais curtas possível. Isso evita que o metal fundido quente e insaturado, da zona de fusão, entre em contato com o revestimento refratário, onde pode dissolver o tijolo de carbono. O diâmetro do furo do macho deve ser mantido pequeno, pois isso ajuda a reduzir o nível geral da vazão.
A influência do comprimento do furo de derivação na tensão de escoamento da parede da lareira foi investigada por cálculos e por modelagem. Com furos de macho mais longos, o ponto de ataque do fluxo se afasta para a esquerda e para a direita do furo de macho. A intensidade do ponto de ataque diminui com o aumento da distância do furo da torneira. O objetivo do controle de processo para os BFs é, portanto, manter o orifício de derivação o maior tempo possível para deslocar o fluxo de derivação da parede da fornalha para o interior da fornalha.
Um projeto de furo de torneira foi instalado em um dos BF, onde um encapsulamento de cobre não apenas tornou a região do furo de torneira estanque ao gás, mas também a protegeu da entrada de água.
Em geral, os tijolos perfurados devem ser superiores em resistência a álcalis, fragmentação, oxidação, fusão em HM, escória e abertura por oxigênio. Para estabilizar o furo da torneira, tijolos AI2O3-C-SiC, com boa durabilidade, foram desenvolvidos e aplicados em um BF. O material desenvolvido apresentou excelente desempenho, com exceção da resistência à oxidação. Além disso, os blocos de carbono apresentam menor resistência à fusão em HM e menor resistência à oxidação do que o material AI2O3-C-SiC.
Refratários aprimorados
A escolha dos refratários e sistemas de resfriamento corretos em cada zona do BF é fundamental para a longa vida útil da campanha do BF. Os projetos refratários estão sendo desenvolvidos continuamente e hoje são comprovados em suas longas campanhas de produtividade. Os designs e materiais mais recentes são aplicados de forma integrada, levando em consideração a vida útil da campanha, as operações do processo, os requisitos de refrigeração, o layout da planta e os procedimentos de construção.
Na pilha superior, onde o desgaste é principalmente mecânico, o refratário para o revestimento BF evoluiu ao longo dos anos de um tijolo de barro refratário normal, com 39 % de Al2O3, para um grau de argila de fogo denso prensado a seco, com cerca de 45 % de Al2O3 . Sua vantagem para essa área é a boa resistência à abrasão e alta resistência à oxidação. Como a baixa resistência ao choque térmico é um problema, em áreas críticas da pilha superior, diferentes tipos de revestimentos compostos estão sendo usados, o que envolve tijolos com 60% de Al2O3 e carboneto de silício para melhorar a resistência ao choque térmico. A sua durabilidade adequada, que só pode ser melhorada a custos significativamente mais elevados com a utilização de tijolos de maior qualidade, não suscita quaisquer expectativas de novos desenvolvimentos para esta zona.
As zonas abaixo da pilha superior, ou seja, bosh, barriga, pilha inferior até o nível da ventaneira, são expostas adicionalmente ao desgaste térmico e químico. Isso significa desgaste por altas temperaturas, fluxos de calor altos e flutuantes e ataque químico por álcalis, zinco, escória, etc. juntamente com abrasão.
As soluções de desgaste para essas zonas também podem ser divididas em solução térmica e solução refratária.
A solução térmica são tijolos de grafite, semi-grafite e SiC, tendo os tijolos de SiC encontrado aceitação para esta zona devido à dureza da matéria-prima. Em um dos altos-fornos, o revestimento bosh foi atualizado em comparação com o reembasamento de 1980, de um sistema combinado de grafite/semi-grafite para um projeto de grafite completo, porque um projeto refratário de grafite completo pode lidar melhor com altas temperaturas e flutuações de temperatura.
Do paralelo bosh até a pilha do meio, o sistema refratário é uma combinação de grafite e carboneto de silício. O principal objetivo do grafite é resfriar o carboneto de silício a temperaturas relativamente baixas, enquanto o objetivo principal do carboneto de silício é proteger o grafite da abrasão. Como solução refratária para bosh, barriga e pilha inferior, foi desenvolvido o uso de tijolo sialon de corindo especial. A condutividade deste tijolo é boa, embora não varie muito com a temperatura e seja menor do que para os tijolos de carbeto de silício. Os tipos de tijolos de corindo sialon têm um grão de corindo e um sistema de ligação não óxido semelhante aos tijolos de SiC. Resultados operacionais satisfatórios já foram alcançados com esses tijolos.
Os refratários da fornalha BF normalmente determinam a vida útil de um forno. A seleção, especificação, inspeção e instalação corretas do material são decisivas para uma fornalha segura e sem problemas.
Em princípio, o revestimento refratário das lareiras BF construídas na última década pode ser subdividida em projetos de revestimento refratário “preto” e “preto/branco”. Para lareiras pretas, são usados blocos de carbono de formato pequeno ou grande de qualidades variáveis. Os designs preto/branco têm camadas cerâmicas na parte inferior, abaixo ou acima das camadas inferiores de carbono, com paredes de revestimento reembasadas feitas de blocos de carbono ou aditivos com diferentes alturas de revestimento cerâmico. Outra definição para a construção de forro de lareira é a 'solução térmica', usando refratários de alta condutividade combinados com resfriamento potente, e a 'solução refratária', envolvendo materiais refratários de baixa condutividade.
A variante de revestimento "solução térmica" teve que ser melhorada em relação às propriedades termomecânicas e termoquímicas. As propriedades dos tijolos, que são afetadas pela escolha das matérias-primas e pelo processo de fabricação do tijolo, atuam em grande parte em direções opostas e devem ser avaliadas quanto ao seu efeito na aplicação operacional.
Graus modernos aprimorados de tijolos de revestimento de lareira à base de carbono visam melhorar uma propriedade que é considerada importante, se possível sem piorar as outras. Isto é conseguido através da escolha da matéria-prima, processo de fabricação e aditivos metálicos e/ou cerâmicos na mistura bruta. Assim, os vários produtores de tijolos trabalham de maneiras diferentes, muitas vezes em estreita cooperação com fábricas BF e institutos de pesquisa. O seguinte levou a novos desenvolvimentos.
- Introdução de Al2O3 muito finamente distribuído na matriz de ligação
- Impregnação com soluções coloidal de SiO2
- Adição de Si ou modificações contendo Si à matriz de ligação, que formam ligações SiC e/ou Si-O-N sob condições de queima adequadas
- Impregnação de alcatrão com pós-queima
Os aditivos geralmente não são usados em tijolos de grafite. Os aditivos de óxido metálico são reduzidos em altas temperaturas de combustão. Os tijolos semi-grafite tornam-se microporosos com esses aditivos. Existem alguns tijolos semi-grafite com apenas aditivos de Si e SiC e alguns em que o pó de Al2O3 é misturado durante a composição.
O tijolo de carbono amorfo microporoso também é produzido a partir do tijolo de carbono amorfo tradicional à base de antracito, pela adição de silício ou modificações de silício à composição do tijolo. Al2O3 também é adicionado durante a composição por outros produtores para melhorar a resistência à dissolução por HM subsaturado. A desvantagem, que Al2O3 pode reagir com álcalis infiltrados resultando em um aumento de volume e descamação do tijolo, deve ser tolerada.
A resistência à dissolução em HM e à infiltração de HM é considerada mais importante pelos fabricantes e usuários. Com a tendência de poros ainda mais finos e tipos de tijolos super microporosos, a matéria-prima foi otimizada quanto à preparação e pureza na composição. Se necessário, a composição também incorpora uma proporção maior de grafite.
As potenciais vantagens apontadas são (i) a maior condutividade térmica, (ii) o comprimento reduzido dos blocos na direção através da parede, (iii) que o uso de cimento libera tensão térmica, (iv) a melhor condutividade térmica do a lareira porque os tijolos estão em contato próximo com as aduelas, (v) que a baixa porosidade, desenvolvida durante a fabricação por aquecimento e pressão simultâneos, minimiza a penetração de água e ferro, e (vi) a alta resistência alcalina.
Como solução refractária para a lareira, os tijolos incorporados nesta são caracterizados por uma elevada resistência aos mecanismos de desgaste a altas temperaturas. Tenta-se minimizar a taxa de desgaste até a aplicação do sistema de refrigeração do lado de fora. Esses tijolos de carbono são baseados na matéria-prima antracite.
Para um tijolo de antracite a alta resistência e baixa solubilidade em HM são mencionadas como vantagens. A baixa condutividade térmica, o alto módulo ? e o maior coeficiente de expansão térmica em comparação com a grafite e a menor resistência aos álcalis são referidos como desvantagens.
Também foi sugerida uma ‘copo de cerâmica’, instalada em vários BFs, como solução refratária para a lareira. Pode-se observar pelo cálculo das isotérmicas, que a isotérmica de 800°C, responsável pela formação da camada frágil nos refratários de carbono, encontra-se dentro do material cerâmico. Em combinação com uma profundidade de poço suficiente da lareira, o copo de cerâmica é mais uma medida de apoio para evitar o desgaste dos blocos de carbono, especialmente o “pé de elefante”.
Instrumentação abrangente e confiável
Sendo o recuperador BF considerado o fator chave para a duração de uma campanha, o acompanhamento da evolução do desgaste no recuperador é de grande importância. As medições de temperatura por termopares são usadas para monitorar o avanço do desgaste na fornalha e os termopares são instalados em uma grade de níveis variados na parede da fornalha. Os termopares NiCr-Ni são normalmente envenenados na faixa de temperatura acima de 600 graus C e podem indicar um nível de temperatura muito baixo. Assim, os termopares só devem ser colocados onde não são esperadas temperaturas acima de 400°C. Esses problemas são evitados usando termopares mutáveis com um tubo de proteção adequado.
Deve-se notar que os termopares indicam apenas o desgaste local e o monitoramento abrangente só é possível com uma densidade extremamente alta de termopares. De um modo geral, é, portanto, possível detectar apenas o curso médio de desgaste. Um método alternativo de monitorar o progresso do desgaste é o uso de uma câmera termovisual ou sondas de fluxo de calor.
Como programa de pesquisa, uma série de 12 sondas de fluxo de calor foi instalada na alvenaria de um alto-forno, para medir diretamente a densidade do fluxo de calor. As seguintes vantagens das sondas de fluxo de calor em comparação com os termopares são apontadas.
- As sondas de fluxo de calor podem ser instaladas perto da camisa do alto-forno em áreas mais frias do revestimento refratário. Portanto, a durabilidade é maior em comparação com os termopares.
- O revestimento refratário de tijolos de carbono não deve ser danificado.
- Em vez de vários termopares, é necessário apenas um sensor em um local de medição para determinar a densidade do fluxo de calor.
- As sondas de fluxo de calor reagem de forma mais sensata a danos na alvenaria refratária.
Os cálculos relativos a uma distribuição local ótima das sondas de fluxo de calor mostraram que uma distância entre duas sondas de 3 m parece ser suficiente para um controle de desgaste confiável e completo. Para obter a mesma certeza com os termopares, estes teriam que ser colocados no meio da alvenaria de carbono com distâncias entre si de cerca de 1 m. O perfil de desgaste geralmente é calculado com base nos dados fornecidos sobre a densidade do fluxo de calor.
Diferentes tipos de revestimentos de lareira e posição das sondas de fluxo de calor são mostrados na Fig 1.
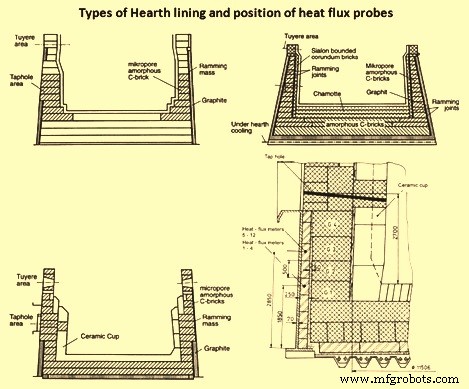
Fig 1 Diferentes tipos de revestimentos de lareira e posição das sondas de fluxo de calor
Processo de manufatura
- Escória de alto forno e seu papel na operação do forno
- Aspectos importantes do projeto de alto-forno e equipamentos auxiliares associados
- Sistema de automação, medição e controle de processos de alto forno
- Forno de indução e siderurgia
- Geração e uso de gás de alto-forno
- Uso de Nut Coke em um Alto Forno
- Produtividade do Alto Forno e os Parâmetros Influenciadores
- Operação de alto-forno e escória de alta alumina
- Irregularidades do alto-forno durante a operação
- Fabricação de ferro por alto-forno e emissões de óxido de carbono