Entendendo o Processo de Lingotamento Contínuo de Aço
Compreendendo o processo de lingotamento contínuo de aço
O lingotamento contínuo (CC) de aço é um processo pelo qual o aço líquido é solidificado em um produto de aço semi-acabado (tarugo, bloco, viga-em branco, redondo ou placa) para posterior laminação nos laminadores. A operação básica de uma máquina CC é converter aço líquido de uma determinada composição em um fio de forma e tamanho desejados através de um grupo de operações como operação de molde, zona de resfriamento por spray, operação de alisador, etc. para entender o comportamento do processo sob diferentes condições para essas operações. O processo de lingotamento contínuo compreende basicamente as seguintes seções.
- Um distribuidor, localizado acima do molde, para receber o aço líquido da panela cheia de aço e alimentá-lo ao molde a uma taxa regulada.
- Uma zona de resfriamento primária que consiste em um molde de cobre resfriado a água através do qual o aço líquido é alimentado a partir do distribuidor para gerar um invólucro de aço externo solidificado suficientemente forte para manter a forma do cordão à medida que passa para a zona de resfriamento secundária. >
- Uma zona de resfriamento secundária em associação com uma seção de contenção posicionada abaixo do molde, através da qual passa o fio de aço (ainda principalmente líquido) e é pulverizado com água ou uma mistura de água e ar (névoa de ar) para solidificação adicional do fio de aço.
- Uma seção para desdobramento e endireitamento de fios de aço. Esta seção não existe nas máquinas de fundição verticais retas.
- Uma seção de corte que consiste em maçaricos ou tesouras mecânicas para cortar os fios de aço solidificado em comprimentos desejados para remoção.
- Uma mesa de corrida para leitos de resfriamento ou diretamente para uma área de transferência de produtos.
No processo CC, o aço líquido flui da panela cheia de aço, através de um distribuidor para o molde. Geralmente é protegido da exposição ao ar por uma cobertura de escória sobre cada recipiente (concha, distribuidor e molde) e por tubos cerâmicos entre os recipientes.
Para iniciar o processo de lingotamento contínuo, uma barra fictícia (que é conectada a um sistema de extração mecânico externo) é inserida no molde e posicionada de forma que a parte superior da barra fictícia feche o fundo do molde. O aço líquido é entregue em uma panela cheia de aço para o piso de fundição, onde é despejado a uma taxa controlada no distribuidor. O aço líquido flui através de bocais no fundo do distribuidor e enche o molde. Quando o nível de aço líquido no molde atinge uma posição predeterminada, a retirada da barra fictícia é iniciada. Uma vez no molde, o aço líquido se solidifica contra as paredes do molde de cobre resfriado a água para formar uma casca sólida. Os rolos de acionamento mais baixos na máquina CC retiram continuamente a barra fictícia do molde. A velocidade de retirada da barra fictícia é predefinida com base na velocidade de fundição necessária ou na vazão de aço líquido do distribuidor. Quando a cabeça da barra fictícia, que agora está presa à forma solidificada que está sendo vazada, atinge uma determinada posição no sistema de extração, ela é desconectada mecanicamente e a barra fictícia é removida. A forma fundida solidificada continua através do sistema de retirada para o equipamento de corte a uma taxa (velocidade de fundição) que corresponde ao fluxo do aço líquido de entrada, de modo que o processo idealmente funciona em estado estacionário.
A solidificação do aço líquido, que começou no molde resfriado a água, continua progressivamente à medida que o fio de aço se move pela máquina CC. A solidificação começa no nível do menisco de aço líquido no molde formando uma casca de aço em contato com as paredes do molde. A distância do nível do menisco até o ponto de solidificação completa dentro da máquina CC é chamada de comprimento metalúrgico. O ponto de solidificação completa deve ocorrer naturalmente à frente do ponto de corte do fio e em muitas máquinas CC está à frente do alisador.
As condições de fundição são estabelecidas de modo que a resistência do invólucro de aço solidificado que sai do molde seja suficiente para suportar a pressão ferrostática do aço líquido no molde. Para evitar a aderência da casca solidificada à parede do molde, o molde é oscilado na direção vertical. O atrito entre a carcaça de aço e o molde é minimizado pela introdução de lubrificantes de molde, como óleos ou fundentes, que formam uma escória fluida.
Abaixo da saída do molde, o invólucro de aço solidificado atua como um recipiente para suportar o aço líquido restante. O calor adicional é removido do cordão nas zonas de resfriamento secundárias que consistem em uma série de jatos de água e névoa de ar. As taxas de fluxo são controladas de perto para obter taxas de resfriamento ideais e para manter a temperatura da superfície até que o núcleo líquido esteja sólido. As unidades de rolos de suporte são fornecidas para conter o cordão para evitar o movimento transversal e para evitar o abaulamento do invólucro de solidificação quente devido à pressão ferrostática interna. O sistema de resfriamento e contenção do cordão é projetado, assim como o molde, para evitar defeitos externos e internos na seção fundida e garantir a qualidade do produto siderúrgico exigida.
A área secundária de resfriamento e contenção é seguida, em certos tipos de máquina, por uma unidade de dobra e um endireitador que está presente em todas as máquinas.
Após o endireitamento, a seção fundida é cortada no comprimento desejado por tochas ou tesouras. Os comprimentos de corte a quente são então transportados por uma mesa de rolos para leitos de resfriamento ou agrupados e transferidos diretamente para operações de laminação subsequentes.
Requisitos do aço líquido
O controle de temperatura é crítico para o processo CC. Geralmente o aço líquido para o lingotamento contínuo deve ser rosqueado a uma temperatura de rosqueamento mais alta. A temperatura de rosqueamento é mais alta, pois deve compensar as perdas de calor associadas ao aumento do tempo de transferência para a máquina CC. A temperatura para o lingotamento contínuo também deve ser mantida dentro de limites mais próximos. Se a temperatura estiver muito alta, geralmente há uma fuga; e se a temperatura for muito baixa, geralmente ocorre a solidificação prematura do aço líquido nos bicos do distribuidor. A temperatura de fundição também pode afetar a estrutura de cristalização do aço fundido. Estruturas ótimas são normalmente obtidas com baixos superaquecimentos que precisam ser uniformes ao longo de todo o processo de fundição. A prática comum geralmente usada para atingir a temperatura uniforme é agitar o aço líquido na panela cheia pela injeção de uma pequena quantidade de argônio no aço líquido.
O aço líquido para o lingotamento contínuo também deve ser totalmente desoxidado (morto) para evitar a formação de bolhas ou pinholes na superfície do aço fundido ou próximo a ela. Esses orifícios ou orifícios geralmente resultam em costuras no processo de laminação subsequente. Normalmente, duas práticas são usadas para desoxidação do aço líquido, dependendo do grau do aço que está sendo produzido e das aplicações do produto de aço. Estas são (i) desoxidação de silício com uma pequena adição de alumínio para aços de grão grosso e (ii) desoxidação de alumínio para aços de grão fino. Os aços mortos com silício são mais fáceis de fundir do que os aços mortos com alumínio. Isso ocorre porque os depósitos de alumina no bico do distribuidor, que causam o bloqueio do bico, são evitados.
Aplicativo de Tundish
No processo CC, o aço líquido é transferido inicialmente de uma panela para o distribuidor. Em seguida, o aço líquido é distribuído em diferentes cordões de moldes, através de um bocal para cada cordão. O distribuidor é essencialmente uma caixa retangular com bicos localizados ao longo do fundo. O seguinte é possível por causa do tundish.
- Alcançar a estabilidade das correntes de aço líquido que entram no molde de fundição e, por sua vez, atingir uma velocidade de fundição constante.
- Para lançar uma sequência de baterias.
- Para trocar a panela cheia de aço vazia por uma panela cheia de aço sem interromper o fluxo de aço líquido nos moldes.
- Para fazer uma classe mista com aço de duas classes diferentes de dois calores diferentes, se necessário.
- Para fornecer a possibilidade de evitar que inclusões e escórias entrem no distribuidor e, assim, escorreguem para o molde
Os distribuidores são normalmente pré-aquecidos antes da fundição para minimizar as perdas de calor do aço líquido durante os estágios iniciais da fundição e, assim, evitar a solidificação do metal, particularmente nas áreas críticas do bocal. As tampas tundish também são usadas para reduzir as perdas de calor radiante durante a operação de fundição.
Encobrimento de aço líquido
Durante o lingotamento a céu aberto, o aço líquido flui diretamente, através do ar, da panela cheia de aço para o distribuidor ou do distribuidor para o molde. Sob essas condições, o fluxo de aço líquido desprotegido pega oxigênio (e algum nitrogênio) do ar e inclusões prejudiciais são formadas no aço líquido. Essas inclusões são transferidas para o molde de fundição, onde são retidas na seção de fundição ou flutuam na superfície do aço líquido. Aqueles presentes na superfície do aço líquido são posteriormente presos na casca solidificante e resultam em defeitos na superfície ou quebram a casca abaixo do molde. Além da formação direta de inclusões na corrente de aço exposta, o ar arrastado na corrente também pode reagir com o aço líquido tanto no molde quanto no distribuidor.
Para evitar esses problemas, normalmente a operação CC é realizada empregando fluxo encoberto de aço líquido. A ênfase é geralmente colocada na proteção do fluxo de aço líquido entre o distribuidor e o molde devido à gravidade do problema. No entanto, a blindagem da panela para o tundish é agora amplamente utilizada, especialmente no caso da fundição de aços mortos com alumínio, onde a prevenção de inclusões de alumina é de extrema importância. Existem dois tipos básicos de cobertura com um grande número de variações e combinações. Estes são, a saber, (i) invólucro de gás e (ii) invólucro de tubo cerâmico.
No caso de cobertura de gás, nitrogênio ou argônio é usado como gás de proteção. Coberturas de tubos cerâmicos são normalmente usadas para fundição de aço morto com alumínio. Eles são usados tanto entre a panela fervilhante de aço e o tundish, quanto entre o tundish e o molde. Uma extremidade do tubo é presa à panela (ou distribuidor) com a outra extremidade imersa no aço quando o distribuidor ou molde está sendo preenchido com o aço líquido. Os tubos cerâmicos são geralmente feitos de sílica fundida ou grafite de alumina.
O projeto mecânico do tubo cerâmico é importante, principalmente na extremidade de saída que fica imersa no aço líquido. Um tipo é um design direto. Outro tipo, geralmente usado no molde, tem um design multiportas (abertura), como um tubo bifurcado com o fundo do tubo fechado e duas aberturas laterais localizadas perto do fundo do tubo. Este tipo de cobertura evita a penetração profunda do fluxo de vazamento no molde e modifica o padrão de fluxo no molde. Assim, as inclusões na corrente de vazamento não são aprisionadas na seção de solidificação, mas sobem para a superfície do aço líquido e são removidas com a escória formada pelo pó de fundição.
Controle de fluxo de aço líquido
Alguns dos fenômenos importantes que governam o processo de lingotamento contínuo e determinam a qualidade do aço fundido são descritos aqui. O aço líquido flui para o molde através das portas no bocal de entrada submerso (SEN), que geralmente é bifurcado. As altas velocidades produzem números de Reynolds superiores a 100.000 e um comportamento totalmente turbulento. O gás argônio também é geralmente injetado no bico para evitar entupimento. As bolhas resultantes fornecem flutuabilidade que afeta significativamente o padrão de fluxo no bico, bem como no molde. Essas bolhas também acumulam inclusões e podem ficar presas na casca de aço solidificado, levando a sérios defeitos de superfície no produto de aço fundido. O jato de aço líquido que sai do bocal flui através do molde e colide contra a carcaça de aço solidificando na face estreita. O jato carrega superaquecimento, que pode corroer a carcaça de aço onde colide com regiões localmente finas. Em casos extremos, essa erosão pode causar uma ruptura, onde o aço líquido rompe a casca de aço.
Geralmente o jato de aço líquido que incide na face estreita se divide para fluir para cima em direção à superfície livre superior e para baixo em direção ao interior do cordão. As zonas de recirculação de fluxo são formadas acima e abaixo de cada jato. Esse padrão de fluxo muda radicalmente com o aumento da taxa de injeção de argônio ou com a aplicação de forças eletromagnéticas, que podem frear ou agitar o líquido. O padrão de fluxo pode flutuar com o tempo, levando a defeitos, portanto, o comportamento transitório é importante.
O fluxo de líquido ao longo da superfície livre superior do molde é muito importante para a qualidade do aço fundido. A velocidade horizontal ao longo da interface induz o fluxo e controla a transferência de calor nas camadas de fluxo líquido e sólido, que flutuam na superfície livre superior. A cobertura inadequada do fluxo de líquido leva a uma solidificação inicial não uniforme e a uma variedade de defeitos de superfície.
Se a velocidade da superfície horizontal for muito grande, o fluxo de cisalhamento e os possíveis vórtices que o acompanham podem arrastar o fluxo líquido para o aço. Este fenômeno depende muito da tensão superficial dependente da composição da interface e da possível presença de bolhas de gás, que se acumulam na interface e podem até criar espuma. Os glóbulos de fluxo então circulam com o fluxo de aço e podem mais tarde ser aprisionados no invólucro de aço solidificado mais baixo na máquina CC para formar inclusões sólidas internas.
O aço líquido contém inclusões sólidas, como a alumina. Essas partículas têm várias formas e tamanhos e se movem pelo campo de fluxo enquanto colidem para formar aglomerados maiores e podem se prender a bolhas. Eles circulam no fluxo do molde na superfície superior ou são aprisionados na casca de solidificação para formar defeitos internos fragilizantes no aço fundido final.
O pó de fundição é adicionado à superfície superior para fornecer isolamento térmico e químico para o aço líquido. Este pó à base de óxido sinteriza e derrete na camada líquida superior que flutua na interface livre superior do aço. A taxa de fusão do pó e a capacidade do fluxo fundido fluir e absorver inclusões de alumina prejudiciais do aço dependem de sua composição. É governado pela termodinâmica dependente do tempo. Algum fluxo líquido se solidifica contra a parede fria do molde, criando uma borda de fluxo sólido que inibe a transferência de calor no menisco. Outro fluxo é consumido no espaço entre a carcaça de aço e o molde pelo movimento descendente da carcaça de aço, onde estimula a transferência uniforme de calor e ajuda a evitar a aderência.
A oscilação periódica do molde é necessária para evitar a aderência da casca solidificante às paredes do molde e para estimular a infiltração uniforme do fluxo do molde na abertura. Esta oscilação afeta as flutuações de nível e defeitos associados. Também cria depressões periódicas na superfície da casca (chamadas de marcas de oscilação), que afetam a transferência de calor e atuam como locais de iniciação de rachaduras.
Mofo e transferência de calor
A função primária do sistema de molde é conter e iniciar a solidificação do aço líquido para atingir os seguintes objetivos.
- Forma do produto fundido (configuração geral e espessura da casca)
- Distribuição de temperatura
- Qualidade interna e superficial. Isso inclui estrutura fundida, uniformidade química juntamente com ausência de trincas, porosidade e inclusões não metálicas.
Uma das características mais importantes do molde é a sua capacidade de transferência de calor. Um molde é basicamente uma estrutura de caixa que contém um revestimento interno fabricado a partir de uma liga de cobre que serve de interface com o aço líquido a ser fundido. Existem pequenas passagens de água entre o revestimento interno e a estrutura de suporte para a água de resfriamento do molde que absorve o calor do aço líquido solidificado em contato com o revestimento. A lubrificação do molde permite uma melhor transferência de calor na parte superior do molde. Mais um fator que influencia a transferência de calor nesta superfície do molde é a conicidade do molde. Isso tende a aumentar a transferência de calor porque se opõe à formação do entreferro entre o invólucro de aço e a superfície do molde.
Além da capacidade de transferência de calor, a resistência a altas temperaturas e a resistência ao desgaste do molde e à deformação do molde também são muito importantes. Embora o material de construção do revestimento interno seja geralmente um cobre laminado a frio de alta pureza, o cobre com pequenas quantidades de prata é comumente usado para obter maior resistência à temperatura elevada. A superfície de trabalho do liner é frequentemente revestida com cromo ou níquel para fornecer uma superfície de trabalho mais dura e também para evitar o acúmulo de cobre na superfície do cordão fundido.
Resfriamento secundário, contenção e retirada de fios
Nas máquinas CC recentes, o resfriamento secundário, a contenção e a retirada do cordão formam um sistema integrado e interligado que também inclui a dobra e o endireitamento do cordão. Nos projetos anteriores de máquinas CC, havia uma maior separação funcional e física dos componentes desta parte da operação de fundição.
O resfriamento secundário e o sistema de contenção e retirada se estendem desde o fundo do molde até a completa solidificação do cordão até as operações de corte. O sistema é capaz de produzir uma seção fundida que tenha a forma adequada, juntamente com a qualidade interna e superficial. Para conseguir isso, a seção de solidificação que sai do molde é resfriada em uma série de zonas de pulverização e contida e retirada por uma série de conjuntos de rolos até que a seção de moldagem solidificada atinja a máquina de corte e a mesa de saída horizontal.
O sistema de resfriamento secundário geralmente é dividido em várias zonas para controlar a taxa de resfriamento à medida que o cordão fundido avança pela máquina CC. Este sistema normalmente consiste em sprays de água ou sprays de névoa de ar que são direcionados para a superfície do fio através de aberturas entre os rolos de contenção.
As principais funções de transferência de calor do sistema de resfriamento secundário são fornecer o seguinte.
- A quantidade necessária de água para atingir a solidificação completa sob as restrições da operação CC, como grau de aço e velocidade de fundição, etc.
- O sistema tem a capacidade de regular as condições térmicas do cordão desde abaixo do molde até a operação de corte, como temperatura da superfície do cordão e gradientes térmicos no cordão.
- Funções auxiliares, como resfriamento dos rolos de contenção.
É essencial que tanto os níveis de temperatura quanto os gradientes térmicos sejam controlados no cordão de aço para evitar a ocorrência de defeitos superficiais e internos como forma inadequada e trincas. Em altas temperaturas, as propriedades de resistência do invólucro de aço têm um papel crítico a desempenhar em sua capacidade de suportar as forças externas e internas impostas pela operação do CC. As forças primárias são aquelas exercidas pela pressão ferrostática do núcleo líquido e pela tração da operação de retirada. Em particular, a ductilidade do aço próximo à temperatura solidus é baixa e a casca do aço é propensa à formação de trincas. É importante controlar os gradientes de temperatura porque podem ser causadas deformações térmicas que excedem a resistência do aço, resultando em trincas. Deformações térmicas excessivas resultam de mudanças na taxa de extração de calor por resfriamento excessivo ou insuficiente. As condições de subresfriamento podem ocorrer por reaquecimento, que é produzido quando o resfriamento por spray é encerrado de forma inadequada e o fio reaquece por transferência de calor do interior com um aumento de temperatura antes de decair por transferência de calor por radiação para o ambiente. Sob essas condições, podem ocorrer tensões e rachaduras excessivas. O efeito pode ser reduzido estendendo e variando a operação de resfriamento por pulverização de água para proporcionar uma transição suave com a área de resfriamento por radiação.
Assim, durante o projeto do sistema de resfriamento secundário, as condições térmicas ao longo do cordão devem ser estabelecidas que satisfaçam a integridade e a qualidade do aço fundido. Por exemplo, as temperaturas da superfície ao longo do cordão são especificadas. Eles estão normalmente na faixa de 1200 graus C a 700 graus C. Com base nesta informação, as taxas de resfriamento ao longo do cordão são determinadas a partir de equações de transferência de calor. Parâmetros importantes nesses cálculos incluem o coeficiente de transferência de calor por convecção dos jatos de água e a quantidade de água por unidade de área de contato da superfície (fluxo de água). O tipo e o número de bicos de pulverização, a posição do bico em relação à superfície do fio de aço e a pressão da água são selecionados para fornecer o fluxo de água necessário e a distribuição pelas zonas de resfriamento secundárias. Múltiplos bicos são normalmente usados em cada nível ao longo do cordão de aço que tem um padrão de sobreposição.
Normalmente, uma série de zonas de resfriamento é estabelecida ao longo do cordão, cada uma com as mesmas configurações de bocal e características de transferência de calor. O fluxo de água em zonas sucessivas diminui, uma vez que as taxas de resfriamento necessárias diminuem ao longo do comprimento do cordão.
Durante a operação CC, mudanças no fluxo de água são feitas para compensar as mudanças nas condições de fundição, como velocidade de fundição, temperatura da superfície do cordão, temperatura da água de resfriamento e grau do aço.
O sistema de água de pulverização é normalmente um sistema de recirculação.
O cordão de aço é contido por uma série de rolos de retenção que se estendem através de suas duas faces opostas das seções fundidas na direção horizontal. Os rolos de borda também podem ser posicionados no outro par de faces em uma direção perpendicular à direção de fundição para aumentar ainda mais a contenção. O equipamento mecânico de contenção e retirada do cordão faz parte integrante do sistema de resfriamento secundário. As funções básicas deste equipamento são (i) apoiar e guiar o cordão desde a saída do molde até as operações de corte do cordão, e (ii) conduzir o cordão a uma velocidade controlada através da máquina CC. O objetivo final em ambas as funções é minimizar o estresse mecânico e as deformações incorridas durante o processo de CC.
O suporte do cordão envolve a contenção da forma do aço solidificado que consiste em um invólucro de aço sólido com um núcleo líquido. A pressão ferrostática, criada pela altura do aço líquido presente, tende a inchar o aço especialmente nos níveis superiores logo abaixo do molde onde a espessura da casca solidificada é pequena. O abaulamento neste local pode causar defeitos no aço fundido, como rachaduras internas, ruptura da pele e rompimento. O abaulamento é controlado por um espaçamento de rolo apropriado que normalmente é muito próximo logo abaixo do molde. O espaçamento entre rolos aumenta progressivamente nos níveis inferiores da máquina CC à medida que a espessura da pele aumenta. Todas as quatro faces do cordão fundido são geralmente apoiadas abaixo do molde e normalmente duas faces são apoiadas nos níveis inferiores. Além da pressão ferrostática e da espessura da pele, o espaçamento dos rolos também é baseado na temperatura da superfície do cordão e no grau do aço fundido.
Além de conter o cordão, a série de rolos que guiam o cordão através de um arco prescrito do plano vertical para o horizontal deve ser forte o suficiente para suportar as forças de reação de flexão. Durante a flexão, o raio externo da casca de aço sólido está em tração enquanto o raio interno está em compressão. A deformação resultante, que é uma função do raio do arco e da resistência do tipo de aço específico que está sendo fundido, pode ser crítica. Deformação excessiva no raio externo resulta na falha do aço e rachaduras na superfície. Para minimizar a ocorrência de defeitos superficiais, mas, ao mesmo tempo, manter um raio de arco efetivo mínimo, adota-se atualmente a flexão de ponto triplo (três arcos, com raios progressivamente menores).
Um alisador de rolos múltiplos geralmente é instalado após a conclusão da dobra. Este alisador endireita o cordão fundido e completa a transição do plano vertical para o horizontal. Durante o endireitamento, o cordão é não dobrado, o que inverte as forças de tração e compressão nas faces horizontais do cordão.
O cordão é puxado através das diferentes partes da máquina CC por roletes que normalmente estão localizados nas seções de roletes verticais, curvas e horizontais. Este sistema de roletes múltiplos é projetado para produzir forças de compressão na superfície do cordão para melhorar a qualidade da superfície. O objetivo é empurrar o cordão através da máquina CC, em oposição à tração do cordão com as tensões de tração associadas que tendem a causar defeitos na superfície. Além disso, o uso de vários conjuntos de roletes de acionamento distribui a força de tração necessária ao longo do comprimento do cordão fundido e, como resultado, reduz os efeitos nocivos das forças de tração. A colocação adequada dos roletes de acionamento também pode reduzir as tensões adversas de flexão e endireitamento exercendo uma força de compressão de compensação (colocando os roletes de acionamento antes de um conjunto de roletes de dobra). Em todos os casos, a pressão exercida pelos roletes para prender o cordão não deve ser excessiva. A pressão excessiva pode deformar a forma da seção que está sendo moldada.
Após o endireitamento, o fio fundido é transportado em mesas de rolos para a máquina de corte onde a seção é cortada no comprimento desejado. Existem dois tipos de máquinas de corte:(i) maçaricos de oxicorte e (ii) tesouras mecânicas. As tochas de oxi-combustível são geralmente usadas para grandes seções, como lajes e flores. Seções menores, como tarugos, são cortadas por tochas ou por tesouras. O produto de aço fundido é então agrupado ou transportado diretamente para os laminadores ou para os leitos de resfriamento que são principalmente do tipo viga móvel para manter a retilinidade do aço fundido.
Os esquemas do processo CC e os fenômenos na região do molde são mostrados na Fig 1.
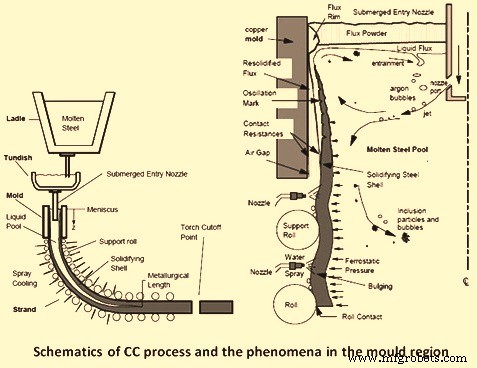
Fig 1 Esquema do processo CC e os fenômenos na região do molde
Processo de manufatura
- Compreendendo o Processo de Fabricação do Eixo
- Uma Visão Geral Rápida do Processo de Fundição
- Etapas envolvidas no processo de fundição:as 4 principais etapas | Ciência da Manufatura
- Automação, Instrumentação e Modelagem de Lingotamento Contínuo de Aço
- Processo de fundição de aço inoxidável
- Dados para alimentar o processo de melhoria contínua
- Compreendendo o processo de fabricação de carcaças de fundição de investimento
- Introdução ao processo de fundição de aço inoxidável
- Entendendo como o processo de cisalhamento é realizado
- Entendendo o processo de fundição em areia