Medidas corretivas e vida de campanha de um alto-forno
Medidas corretivas e vida útil da campanha de um alto-forno
O custo de reconstrução ou reembasamento de um alto-forno (BF) é muito alto. Portanto, as técnicas para prolongar a vida útil da campanha do BF são importantes e precisam ser seguidas de forma muito ativa.
Grandes BFs geralmente têm uma saída de campanha ligeiramente maior por unidade de volume. Essa diferença ocorre porque BFs maiores geralmente são de design mais moderno e bem automatizados. Uma vez que a viabilidade de uma siderúrgica integrada depende de um fornecimento contínuo de metal quente (HM), o que, em uma planta com um pequeno número de grandes BFs, dá grande importância à longa vida útil da campanha.
As técnicas para prolongamento da vida da campanha BF se enquadram nas três categorias a seguir.
- Práticas operacionais – O controle do processo de BF tem um grande efeito na vida da campanha. O BF deve ser operado não apenas para atender às necessidades de produção, mas também para maximizar sua vida útil. Portanto, é necessário modificar as práticas operacionais à medida que a campanha avança e em resposta às áreas problemáticas para maximizar a vida útil da campanha.
- Medidas corretivas – Quando o desgaste ou dano que afeta a vida útil do BF se torna evidente, técnicas de reparo de engenharia devem ser usadas ou desenvolvidas para maximizar a vida útil da campanha.
- Projetos aprimorados – À medida que materiais e equipamentos aprimorados são desenvolvidos, eles devem ser incorporados em futuras reconstruções para prolongar a vida útil das áreas críticas do BF, onde for econômico fazê-lo.
Medidas corretivas para melhorar a vida de campanha do BF são discutidas neste artigo. As medidas normalmente adotadas para melhorar a vida de campanha do BF estão descritas a seguir.
Reparos a frio e reparos de tiros
A obra de tijolos refratários empilhados geralmente está exposta ao desgaste mecânico na parte superior e também ao desgaste térmico e químico na parte inferior do BF. Para garantir uma operação estável do BF ao longo de sua vida de campanha, é necessário que o perfil de revestimento da pilha do BF seja mantido em condição equilibrada na direção circunferencial.
O reembasamento intermediário (rebricking) da área da pilha é feito após o BF ser derrubado. Isso é demorado, mas prolonga a vida útil da campanha BF, que normalmente é superior a 5 anos com práticas operacionais normais.
A chaminé e a área de bosh podem ser armadas com concretos à base de alumina adotando a prática de tiro a frio, o que significa o resfriamento completo do BF e a construção do andaime de onde os operadores de tiro podem realizar o trabalho de tiro. No entanto, este processo é demorado. Para diminuir o tempo de paralisação, foi desenvolvido o sistema de tiro por controle remoto.
Com a ajuda do sistema de tiro de controle remoto, reparos com concretos à base de alumina podem ser feitos nas áreas da pilha e da bosh usando circuito fechado de televisão para monitorar o trabalho. Este sistema elimina a necessidade de operários entrarem em um forno quente. O desligamento total necessário para a aplicação dos concretos nas áreas de bosh e empilhamento do BF usando esta técnica de tiro controlado remotamente é de apenas alguns dias. O número de dias depende do tamanho do forno, da extensão do tiro necessário e da quantidade de trabalho preparatório realizado.
O dispositivo de tiro de controle remoto é suspenso de uma viga cantilever por cabos e inserido através de uma porta na lateral da pilha perto do topo do BF. Em seguida, é posicionado no centro do BF por meio de um pórtico. O operador de tiro usa uma pistola refratária de alimentação contínua para aplicar uma mistura de material monolítico e água na parede do BF a uma distância uniforme e de um ângulo constante de 90 graus. O mecanismo de tiro pode ser girado 360 graus e pode ser levantado e abaixado para permitir que o operador alcance todas as partes da pilha. À medida que cada revolução é completada, o dispositivo de tiro é simplesmente elevado para o próximo nível. O operador pode parar a rotação para gunite mais nas áreas seriamente erodidas. A unidade é normalmente equipada com luzes para melhorar a visibilidade do operador.
A vantagem desta técnica é que a redefinição do perfil do BF pode ser concluída em poucos dias de interrupção contra um grande número de dias necessários para disparo a frio. Como o equipamento é operado por controle remoto a partir de uma plataforma situada fora do BF, não há necessidade de esperar o resfriamento do BF para iniciar os reparos de tiro.
Antes da operação de tiro, a limpeza da pilha e a remoção de grandes crostas é um pré-requisito importante. A remoção de materiais refratários soltos e/ou acreções pode ser feita por jato de água e a limpeza da pilha pode levar em torno de 10 a 15 horas. Durante o disparo, o rebote do material deve ser controlado. O material rebote deve ser derretido após o início do forno. Fundir um material de alto rebote pode trazer diversos problemas para o operador de BF.
Quando o procedimento de tiro é concluído, o BF é normalmente seco por sopro controlado de jato quente de baixa temperatura através do BF. A temperatura superior do gás é progressivamente aumentada para cerca de 400 graus C, aumentando a temperatura de explosão quente. O objetivo é aumentar a temperatura em 150 mm atrás do material aplicado para 120 ° C para expulsar a umidade proveniente da operação de tiro. Se isso não for feito, durante o aquecimento rápido após o início do BF, pode haver fragmentação maciça.
A duração de um desligamento para este tiro de robô depende do tamanho do BF e da extensão do tiro necessário e normalmente está na faixa de 4 a 8 dias. A vida útil dos refratários canhão varia e depende de vários fatores. Para um BF que opera em altos níveis de produtividade após reparos de canhão e sem interrupções frequentes, a vida útil esperada dos refratários de canhão pode estar na faixa de 9 a 15 meses.
A vida útil dos reparos por canhão pode ser estendida pela adição de acessórios à carcaça do forno. No método de tiro com armação hexagonal, uma armação de aço com grelhas hexagonais é fixada ao casco, onde o revestimento de tijolos está bastante desgastado, e um refratário moldável é armado no chassi com uma espessura de 150 a 200 mm para reconstruir o revestimento. A vantagem deste método é que o concreto armado pode ser totalmente canhão até a parte de trás das grelhas e que o concreto armado tem alta resistência. Espera-se que o método de canhão hexagonal prolongue a vida útil do revestimento da pilha superior sob baixas cargas térmicas. A instalação de tubos de resfriamento na pilha superior também pode dar suporte adicional ao refratário canhão.
Resfriamento aprimorado
O resfriamento aprimorado em áreas críticas das áreas da parede BF é uma maneira de promover o prolongamento da vida útil da campanha BF. Uma área crítica é o furo de torneira em um alto-forno. Em alguns BFs, uma unidade de refrigeração (um chiller) está sendo usada para resfriar a água que está sendo bombeada para as aduelas diretamente abaixo do orifício da torneira (a área com maior desgaste de carbono). A temperatura da água da aduela é reduzida para cerca de 5°C em comparação com os 30 a 35°C normais sem o uso de água gelada. Esta água gelada ajuda a construir um crânio mais rápido e mais espesso nesta área. Como resultado, a espessura da camada de solidificação na fornalha aumenta e a temperatura do tijolo de carbono diminui em conformidade.
Por vezes, é utilizado um sistema de refrigeração por baixo da lareira, caso haja tendência de aumento da temperatura no fundo da lareira. Sob a lareira, são instalados tubos de resfriamento com um espaçamento desejado de 500 mm no BF em paradas planejadas. A água de recirculação é passada por esses tubos para extrair calor. Isso ajuda na queda acentuada da temperatura local. Um sistema de resfriamento para resfriar a temperatura da água de recirculação também é usado às vezes para tornar a extração de calor mais eficaz.
Para melhorar ainda mais a durabilidade do revestimento da pilha superior, foi desenvolvido um método no qual são instaladas peças fundidas de ferro refrigeradas a água. As peças fundidas de ferro refrigeradas a água são instaladas de tal maneira que ficam expostas no BF, e um refratário moldável é rebocado no espaço entre o revestimento de tijolo desgastado e as peças fundidas de ferro resfriadas a água. Os fundidos de ferro refrigerados a água podem suportar mais adequadamente as variações de carga térmica do que os refratários. Fundições de ferro refrigeradas a água são instaladas em alguns BFs na área do eixo superior do BF para prolongamento da campanha.
Elementos de resfriamento cilíndricos (conhecidos como resfriadores de charutos) também são usados como âncora refratária refrigerada a água ou inserção de aduela durante os reparos dos BFs para prolongar a vida útil da campanha. Os resfriadores de charutos também oferecem alternativas econômicas para prolongar a vida útil de novos revestimentos refratários, sejam instalados durante reembasamento, reparos ou em novos fornos. Além da instalação desses resfriadores em um BF recém-revestido e como âncoras refratárias, suas configurações de placa de montagem incluem portas de injeção de argamassa integradas para economizar tempo e custos de instalação. Além disso, resfriadores cilíndricos duplos especiais podem ser montados em um flange ou placa comum contendo uma porta de reboco embutida. Esta unidade dupla pode então ser instalada em qualquer local na pilha do forno que exija rejunte, sem a necessidade de fazer furos na pilha e soldar os bicos de rejunte no lugar. Resfriadores cilíndricos também podem ser utilizados para restabelecer o resfriamento em aduelas com falha. Os refrigeradores são inseridos através da carcaça em aberturas que são fornecidas na aduela. Estas aberturas podem ser lancetadas ou empregadas com corte de água de alta pressão. O padrão de localização e o tamanho dos resfriadores dependem da configuração real da aduela e da localização dos tubos fundidos, parafusos de montagem e conexões de tubulação.
Grutagem e soldagem da casca BF
O reboco do casco BF é uma tecnologia bem conhecida para promover uma longa vida útil da campanha. A betumação da fornalha BF, ou seja, a injeção de material plástico refratário através do invólucro a partir do exterior, é realizada (i) para preenchimento após reparos, (ii) para neutralizar vazamentos de gás na área do furo da torneira, (iii) no 'frágil zonas' da parede da lareira, e (iv) em caso de aumento de temperatura na parede da lareira.
Ao realizar o rejuntamento na região da lareira, as ventaneiras e os topos dos cotovelos devem ser fechados. Como o material de rejunte flui bem, é suficiente ajustar a pressão de injeção para 5 kg/cm2. Isso evita que quaisquer resíduos de tijolos devido ao acúmulo de pressão de argamassa sejam empurrados para dentro do BF. A casca BF deve ser resfriada para evitar a vaporização excessivamente rápida dos plastificantes e a conseqüente formação de trincas. Normalmente são utilizadas massas isentas de água.
A saída de gás do orifício da torneira é causada pela queima insuficiente da massa devido à alta condutividade térmica dos tijolos de SiC usados naquela área e pela deterioração da argamassa usada entre o tijolo e a casca. Para evitar a saída do gás, estão sendo praticadas contramedidas de melhoria. Estas contramedidas são dadas abaixo.
- Injeção de alcatrão e resina através do invólucro BF ao redor do orifício da torneira para tapar a passagem do gás.
- Aperto do interior do orifício da torneira. A fim de interceptar a passagem de gás através das juntas de tijolo do furo da torneira, geralmente é feita a compactação de um material do tipo resina.
- Injeção de resina no furo da torneira para interceptar a passagem do gás através das juntas de tijolo do furo da torneira, às vezes é feita injeção de resina nos furos da torneira usando uma pistola de lama.
- Melhoria no método e no material para aplicação de canhão ao redor do furo da torneira para evitar a geração de vazios.
O invólucro BF deve suportar altas pressões operacionais e refratárias, tensões térmicas, cargas de carga e ter vários cortes para conexões internas de sistemas de refrigeração a água. Rachaduras no casco causam vazamento de gás. Os seguintes conceitos para minimizar rachaduras estão sendo praticados.
- A forma deve ser o mais simples possível.
- Um projeto que restringe o movimento da casca, como uma viga circular, deve ser evitado.
- A espessura da casca deve ser a mais fina possível.
Para atender a essas condições, o material da casca BF deve ter excelente elasticidade e soldabilidade. O uso de técnicas de elementos finitos permite uma placa de casca significativamente mais fina, em comparação com a prática de design sofisticado e design otimizado, para dar uma maior capacidade de resistir a rachaduras na última parte da campanha.
O corte de seções rachadas do casco e a substituição por um pedaço de casco pré-revestido estão sendo realizados em alguns dos BFs. Geralmente é visto que quase simultaneamente com o início do dano das placas de resfriamento, rachaduras ocorrem no casco, começando no canto da seção onde a placa de resfriamento é montada. Parte da casca, portanto, deve ser cortada durante a sopragem e uma casca pré-revestida com refratários moldáveis por cerca de 150 mm precisa ser instalada.
Substituição de pautas e refrigeradores
Placas de resfriamento danificadas são mais fáceis de serem substituídas, ao passo que é praticamente muito difícil trocar as aduelas de resfriamento e muitas vezes é necessário soprar o BF. A porção do invólucro do forno no local da aduela danificada é cortada e removida junto com a aduela de resfriamento danificada. Se necessário, o material deve ser raspado e as bordas cortadas da casca BF são preparadas para soldagem. Em seguida, o novo pedaço de placa de concha, juntamente com as aduelas de resfriamento instaladas, é empurrado no local e alinhado. A placa do casco é então soldada. Durante a troca da aduela de resfriamento, é necessário fazer a provisão para reboco. Após a soldagem, deve-se realizar o rejuntamento para preencher os vazios entre o resfriador substituído e o balanceado do revestimento do BF. A troca do cooler danificado aumenta a vida útil da campanha do BF.
Soprador de ar e jato frio principal
É importante evitar falhas principais do soprador e do jateamento frio, pois isso pode tirar repentinamente o BF do jateamento e também de maneira descontrolada. Nesses casos, a escória pode entrar em ventaneiras e até zarabatanas e, em casos excepcionais, nas tubulações e nas redes de jateamento a quente. Tais problemas exigem longos períodos não planejados fora da detonação, que têm um efeito prejudicial na vida útil da campanha do BF. Para reduzir a possibilidade de tais falhas, são necessários um soprador de reserva, boa manutenção e inspeção de rotina do sistema de jateamento a frio.
O isolamento do sistema de jato frio, muitas vezes realizado para economizar energia, geralmente aumenta a temperatura de trabalho do sistema de jato frio e dificulta as inspeções de rotina.
Fogões de explosão quente e principal de explosão quente
O fogão de sopro quente é um equipamento crítico em relação à vida útil da campanha da BF. A estufa deve funcionar sem problemas e sem parar durante toda a vida útil da campanha do BF. A salamandra de jacto quente com câmaras de combustão externa é a tecnologia mais avançada para temperaturas de jacto quente superiores a 1200 graus C. Estas salamandras são normalmente equipadas com queimadores cerâmicos. A temperatura de jateamento é regulada em uma câmara de mistura esférica. Um revestimento protetor especial é frequentemente usado para evitar a ocorrência de corrosão sob tensão intercristalina.
Além dos fogões de jateamento a quente, o sistema principal de jateamento a quente também precisa de atenção para que possa ser operado com segurança e economia. A expansão igual do tubo de agitação para o centro BF é muito importante. Para isso, é desejável o uso de cabides de três pontos no cano do bustle. A expansão igual do anel é normalmente alcançada por pequenos movimentos verticais. Com este projeto, obtém-se uma ótima segurança operacional nas ventaneiras, além de fácil acesso para troca das ventaneiras.
Os estoques de tuyere com compensadores multicamadas são caracterizados por baixas perdas de pressão e boas características de fluxo, garantindo assim baixa radiação de calor com revestimento ideal.
No que diz respeito ao ponto fixo do jacto principal à estufa, sabe-se que a expansão do invólucro principal do jacto quente é grande, uma vez que cobre uma grande distância entre o BF e o primeiro fogão quente. Com um arranjo de três elos, os problemas de expansão e revestimento refratário são geralmente superados.
Normalmente os bicos do jacto principal e o bico do jacto quente da estufa estão no mesmo eixo. Dependendo do comprimento da junta de expansão da válvula de jateamento quente, o movimento nesta área é normalmente limitado a +/-10 mm. Por esta razão, devem ser construídos pontos fixos à frente ou entre as estufas que sejam capazes de suportar o impulso das juntas de dilatação bem como a força de atrito do revestimento refractário. Dependendo do tamanho do sistema principal de jateamento quente, essas forças podem estar na faixa de 0f 60 a 120 toneladas. Se não existirem pontos fixos, ainda haverá uma espécie de medida restritiva devido à formação de um centro de massa no centro do arranjo principal de jateamento quente, onde a expansão se move tanto na direção do forno quanto na última fogão. Isso gera muitos problemas na tubulação e nas juntas de expansão da válvula de jateamento quente.
Em fogões modernos de alto-forno, existem três a seis válvulas de sopro quente (dependendo do sistema da planta e do número de fogões) instaladas como válvulas de fechamento do fogão, válvulas de isolamento do alto-forno e válvulas de ventilação para a azáfama principal. Essas válvulas de jateamento a quente geralmente operam em temperaturas de jateamento quente que podem chegar a 1500 graus C e em pressões de jateamento de até 5,5 kg/cm². As válvulas de jateamento a quente são atualmente fabricadas em aço e são resfriadas a água.
Um queimador com bom desempenho de combustão é um dos pré-requisitos para o funcionamento do fogão quente sem problemas. A substituição do queimador do fogão pode ser feita em condições frias em cerca de três meses, ou em condições quentes em cerca de duas semanas. A reparação dos queimadores do fogão danificados e a implementação de um modelo de computador para ajustar as configurações de combustão do fogão permite uma operação mais eficiente do fogão de jacto quente e permite que o sistema de jacto quente forneça uma temperatura de jacto mais alta. Em geral, a pulsação e a vibração da estufa devem ser controladas.
Válvula de controle de explosão quente
A válvula de controle de jato quente (HBCV) foi desenvolvida para controlar a taxa de fluxo do jato quente em cada ventaneira do BF. Com essas válvulas, é possível controlar o equilíbrio circunferencial do nível da linha de estoque no topo e isso leva a melhorias na condição do BF. O HBCV também ajuda em algumas operações inovadoras de BF, como sopro de pulso e novo controle de rosqueamento. A operação com HBCV permite que os operadores de BF ajustem a velocidade de descida da carga, remoção de andaimes na parede do forno e na extensão do tempo de rosqueamento. Como resultado da redução das frequências de derivação, a operação do BF é mais estável.
Corredores de elenco
A taxa de fluxo de HM e escória líquida no sistema runner aumentou com o aumento da produtividade dos BFs. Portanto, o design do corredor HM tornou-se um parâmetro extremamente importante. Se o canal for muito curto, a separação de escória HM-líquido é ruim, alto desgaste esperado na área do bloco escumador e a temperatura da escória líquida é alta, o que é prejudicial para o canal secundário. Por outro lado, se o corredor for muito longo, haverá alta expansão e corrosão do corredor. Portanto, o comprimento do corredor deve ser ótimo. Além disso, se o canal for muito estreito, o fluxo é turbulento e a temperatura do revestimento é alta, ambos levam ao aumento da corrosão do revestimento refratário. Por outro lado, se o canal for muito largo, as perdas térmicas serão indevidamente altas e será necessária maior quantidade de refratário para o revestimento inicial.
A durabilidade dos materiais refratários para o corredor HM é determinada pela carga mecânica, química e térmica. Os requisitos de propriedade do material refratário para o corredor são os seguintes. (Figura 1)
- É necessária resistência ao ataque químico de HM e escória líquida.
- Resistência à erosão e oxidação dos constituintes individuais do material do corredor.
- Necessidade de estabilidade de volume em altas temperaturas.
- Resistência a choques térmicos é necessária.
- Facilidade de trabalhar.
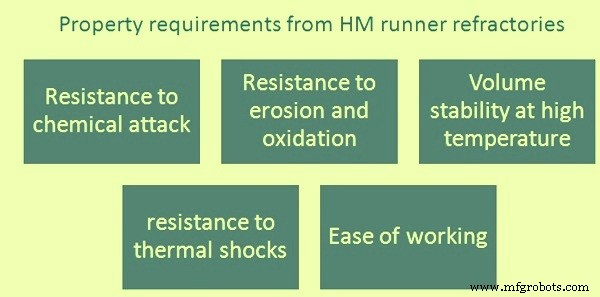
Fig 1 Requisitos de propriedade dos refratários do corredor HM
Os materiais refratários para o corredor devem ser feitos de matérias-primas de alta pureza. Devem ser quimicamente neutros, pois permanecem em contato com HM e escória líquida por muito tempo. As matérias-primas básicas utilizadas nos dias de hoje para os refratários do corredor são corindo fundido, bauxita, andaluzita e chamota. SiC e Si3N4 são adicionados como agentes antioxidantes. Além disso, às vezes são necessários materiais metálicos, como alumínio e pó de silício, para ligar os materiais. Principalmente água é adicionada como uma fase líquida.
Uma mistura de compactação não tóxica e um concreto não perigoso e de baixa umidade também foi desenvolvido para uso nos corredores do BF. As técnicas de revestimento das calhas principais foram desenvolvidas em paralelo com a melhoria da qualidade dos materiais das calhas, desde materiais normais monolíticos com compactação até à técnica de fundição muito moderna.
Máquinas de perfuração e armamento de furos
As máquinas de perfuração e canhão devem ser instaladas em locais onde sejam seguras em relação ao fogo, poeira e sujeira. Além disso, a disponibilidade deve ser alta e a manutenção fácil, para evitar atrasos na transmissão.
Controle de emissões da casa de fundição
O controle de emissões da casa de fundição em BF não é uma exigência legal em muitos países. No entanto, onde existe tal exigência, é necessária a total disponibilidade do sistema de despoeiramento para garantir a continuidade da operação do BF. Devido à legislação ambiental cada vez mais rigorosa em alguns países, uma redução na emissão de fumos da fundição tornou-se necessária para alguns operadores, durante a campanha de execução do BF. Os filtros de mangas podem causar problemas em termos de capacidade de temperatura, porque o ar residual com uma temperatura superior a 150 graus C deve ser limpo ao abrir o orifício da torneira.
Planta de limpeza de gás
O sistema de limpeza de gás de topo do tipo úmido de um BF moderno geralmente consiste em um coletor de poeira, o ciclone e o lavador úmido. As perdas de pressão ocorrem no coletor de pó e no ciclone, bem como no lavador venturi. Operar um BF com maior entrada de cloro pode causar problemas de corrosão no sistema de lavagem. Dependendo da taxa, a injeção de carvão introduz um extra de 0,2 kg/tHM a 0,3 kg/tHM de cloro no BF e isso causa problemas de corrosão no sistema de limpeza de gás wet top. Isso torna necessário o revestimento da lavadora, bem como uma ação adicional em relação ao valor de pH da água. É necessária atenção especial para o desgaste na planta de limpeza de gás. O revestimento de basalto fundido por fusão é normalmente usado. É preferível um revestimento de material resistente a ácidos no cone de entrada.
Sistema de carregamento e distribuição
BFs que estão sendo operados com fluxo de gás central, geralmente encontram altas temperaturas de topo de gás no meio. Essa temperatura pode chegar a 1000 graus C. Nesse caso, o resfriamento da calha do sistema de carregamento superior sem sino é uma solução possível.
A vida útil da placa de desgaste na calha superior sem campânula determina o tempo máximo entre as duas paradas do BF. A frequência de paradas pode ser estendida melhorando a qualidade dos materiais utilizados. A caixa de engrenagens do equipamento sem campânula também é fundamental para a operação do BF. Problemas como perda de óleo das caixas de engrenagens de ajuste de ângulo e danos no perfil do dente do anel de orientação podem ocorrer. O design da caixa de engrenagem de ajuste de ângulo é para permitir a substituição das vedações do eixo do segmento durante as condições de desligamento.
Eletrônica geral e sistema de controle
Normalmente o sistema eletrônico e de controle não está vinculado à vida da campanha do BF. Mas, à medida que a vida útil da campanha do BF aumenta, o problema de corrosão e deterioração do sistema eletrônico e de controle, que deve durar toda a campanha, torna-se motivo de grande preocupação. Além disso, ao longo de uma longa campanha, a disponibilidade de sobressalentes eletrônicos se torna difícil, pois a tecnologia no campo eletrônico está mudando em uma velocidade muito rápida.
Portanto, é aconselhável ter uma unidade stand by para o sistema de controle eletrônico crítico. Isso pode reduzir o tempo de inatividade do BF devido à falha do sistema de controle eletrônico. Isso, por sua vez, pode ter um efeito muito positivo na vida da campanha do BF.
Circuitos de resfriamento
No sistema de resfriamento BF, o acúmulo nas tubulações reduz a vazão e, consequentemente, a transferência de calor por condução é reduzida. O acúmulo nos circuitos de refrigeração ocorre devido à corrosão interna e deposição. Para evitá-lo, pode-se usar água tratada quimicamente. A limpeza ácida e o jato de água pressurizado também são usados às vezes para remover depósitos de tubos de resfriamento e trocadores de calor.
A vazão de água geralmente é aumentada para melhorar a eficiência do resfriamento, além de reduzir a temperatura da água na frente dos resfriadores.
Medição da vazão de explosão em cada ventaneira
Uma medida da vazão de explosão em cada ventaneira é importante quando o BF está sendo operado com injeção de hidrocarbonetos na ventaneira. Caso haja um bloqueio da abertura da ventaneira, pode ser devido a uma grande acreção, o injetor de hidrocarbonetos pode entrar em combustão no estoque da ventaneira ou na azáfama. Isso pode resultar em danos extensos e, portanto, exigir uma interrupção imediata e possivelmente prolongada do BF. A medição da queda de pressão através dos estoques de ventaneira é frequentemente utilizada para este fim, com um corte automático do injetor de ventaneira quando é indicado um fluxo de ventaneira restrito.
A medição do injetor de hidrocarboneto da ventaneira em cada ventaneira é necessária para permitir um bom controle das condições da pista, mesmo para operação circunferencial. Para otimizar o equilíbrio circunferencial, pode ser benéfico combinar o fluxo do injetor com o fluxo de explosão.
Placas de armadura da garganta
Para prolongar a vida útil do BF e reduzir os custos de manutenção, foi desenvolvido um arranjo para placas de armadura de garganta mutáveis. Este arranjo está em uso prático em muitos BFs. As placas são montadas retrospectivamente, em cima da armadura desgastada da garganta. Os preparativos para sua instalação, envolvendo perfuração e soldagem sob pressão, são realizados durante a produção, com poucas paradas preparatórias, seguidas de uma parada mais longa (tipicamente de 2 dias a 3 dias). Um desligamento muito mais longo seria necessário para reparar a placa de armadura da garganta de maneira tradicional.
Processo de manufatura
- Escória de alto forno e seu papel na operação do forno
- Aspectos importantes do projeto de alto-forno e equipamentos auxiliares associados
- Sistema de automação, medição e controle de processos de alto forno
- Forno de indução e siderurgia
- Geração e uso de gás de alto-forno
- Uso de Nut Coke em um Alto Forno
- Produtividade do Alto Forno e os Parâmetros Influenciadores
- Operação de alto-forno e escória de alta alumina
- Irregularidades do alto-forno durante a operação
- Fabricação de ferro por alto-forno e emissões de óxido de carbono