Processos de desgaseificação a vácuo para aço líquido
Processos de desgaseificação a vácuo para aço líquido
Durante o processo primário de fabricação do aço, gases como oxigênio (O2), hidrogênio (H2) e nitrogênio (N2) se dissolvem no aço líquido. Esses gases têm um efeito nocivo nas propriedades mecânicas e físicas do aço. O O2 dissolvido do aço líquido não pode ser removido como O2 molecular e sua remoção é denominada desoxidação. O termo desgaseificação é usado para a remoção de gases H2 e N2 do aço líquido. Como o processo de desgaseificação do aço líquido é realizado sob vácuo, também é conhecido como desgaseificação a vácuo do aço líquido. Os processos de desgaseificação a vácuo são realizados em panelas cheias de aço.
A remoção dos gases H2 e N2 do aço líquido é necessária, pois ambos os gases prejudicam as propriedades do aço. A solubilidade do H2 no aço é baixa à temperatura ambiente. O excesso de H2 é rejeitado durante a solidificação e resulta na formação de pinholes e resulta na porosidade do aço solidificado. Poucos ppm (partes por milhão) de gás H2 causam bolhas e perda de ductilidade de tração. No caso do gás N2, a solubilidade máxima do N2 no ferro líquido é de 450 ppm e inferior a 10 ppm à temperatura ambiente. Durante a solidificação, o excesso de N2 é rejeitado, o que pode causar a formação de orifícios de sopro ou nitretos. O excesso de N2 também causa fragilização da zona afetada pelo calor durante a soldagem de aços e também prejudica a conformabilidade a frio do aço.
Foi apenas no início da década de 1950 que o problema de produzir aço com teor mínimo de gás foi resolvido através do desenvolvimento de um método de tratamento a vácuo de aço líquido na panela antes de seu enchimento. O método foi proposto pelos cientistas AM Samarin e LM Novik da antiga URSS em 1940. Foi testado pela primeira vez industrialmente na então URSS em 1952 na usina metalúrgica Enakievskii. Em 1954, na então República Federal da Alemanha, no Bochumer Verein, foi tentado um método de desgaseificação de um fluxo de metal. A introdução industrial do método de panela de tratamento a vácuo foi feita pela primeira vez na então URSS em 1955. Isso iniciou uma nova tendência na fabricação de aço conhecida como tratamento a vácuo do aço.
O tratamento a vácuo do aço líquido na panela começou primeiro com os processos de desgaseificação a vácuo panela a panela e panela a lingote para a remoção de H2. Originalmente, a desgaseificação a vácuo do aço líquido é realizada sob condição redutora a uma pressão que varia de 0,5 a 10 mbar (1mbar =0,75 mm Hg ou 0,00102 kg/sq cm) com o objetivo de reduzir o teor de H2 para menos de 2 ppm.
No final da década de 1950, processos de desgaseificação a vácuo mais eficientes, como os processos Dortmund Hoerder (DH) e Ruhrstahl-Heraeus (RH), tornaram-se populares. Em meados da década de 1960, processos de desgaseificação como a desgaseificação a arco a vácuo (VAD), o processo ASEA-SKF e o processo de descarbonetação a vácuo (VOD) para o tratamento de aços com alto teor de cromo (Cr) foram implementados com sucesso.
Inicialmente, o conceito de desgaseificação a vácuo foi usado principalmente para a remoção do gás H2 do aço líquido, mas logo serviu para muitos outros propósitos também para a produção de aços limpos. Desde cerca de 1980, houve um aumento no uso de desgaseificação a vácuo para a produção de aços de carbono ultrabaixo (ULC) com teor de carbono (C) de 30 ppm ou menos. Além disso, com o desenvolvimento de aços livres de intersticiais (IF) com teores de C e N2 de 30 ppm ou menos, um tratamento sob vácuo tornou-se uma necessidade. Atualmente, um tratamento de desgaseificação a vácuo tornou-se uma instalação essencial para uma fundição de aço que produz aço de qualidade.
As características gerais da desgaseificação a vácuo são apresentadas abaixo.
- A dessorção de gases é uma reação interfacial gás/metal. O H2 ou N2 atômico do aço líquido tem que se difundir na interface gás/metal, onde é convertido em H2 ou N2 molecular que pode então ser dessorvido. A eficácia do tratamento a vácuo aumenta com o aumento da área de superfície do líquido exposto ao vácuo. A área de superfície aumentada do aço líquido exposto ao vácuo, e. na forma de um fluxo fino ou agitação induzida por gás acelera o processo de desgaseificação.
- A temperatura do aço líquido cai durante o processo de desgaseificação a vácuo. Maior é a área da superfície do fluxo exposta ao vácuo, maior é a queda de temperatura.
- O tempo de desgaseificação deve ser mantido no mínimo.
- O grau de desgaseificação aumenta com o grau de vácuo. O vácuo da ordem de 1 mm Hg ou mesmo inferior a 1 mm Hg (1 mm Hg =1torr) é empregado na prática. A capacidade de bombeamento a vácuo deve ser adequada.
Os processos de desgaseificação a vácuo que estão sendo usados atualmente podem ser classificados em três tipos:(i) prática de desgaseificação de fluxo, (ii) prática de desgaseificação de circulação e (iii) prática de desgaseificação em panela ou tanque.
Prática de desgaseificação de fluxo
Na desgaseificação por fluxo, o aço líquido é derramado em outro recipiente que está sob vácuo. A exposição repentina do fluxo de líquido no vácuo leva a uma desgaseificação muito rápida devido ao aumento da área de superfície criada pela quebra do fluxo em gotículas. Este processo ajuda o H2 dissolvido no aço a ser evacuado por uma bomba de vácuo. A maior quantidade de desgaseificação ocorre durante a queda da corrente líquida. A altura do fluxo de vazamento é um importante parâmetro de projeto. A tecnologia de desgaseificação de fluxo tem as seguintes variantes na prática.
- Concha para desgaseificação do lingote – O lingote pré-aquecido com hot top é colocado na câmara de vácuo. Acima da câmara é colocado um distribuidor. O aço líquido vazado na panela está em um superaquecimento equivalente a 30°C. A panela é colocada acima do distribuidor. É desejável o vazamento de aço líquido no fundo do distribuidor. O esquema da desgaseificação da panela para o molde é mostrado na Fig 1.
- Desgaseificação concha a concha – Na desgaseificação concha a concha, uma concha com a haste da rolha é colocada em uma câmara de vácuo. A panela contendo aço líquido do forno primário de fabricação de aço é colocada no topo da câmara de vácuo e a abertura é selada a vácuo. As adições de liga são feitas sob vácuo. O fluxo pode cair na panela onde o aço líquido é desgaseificado. As adições de liga são feitas sob vácuo.
Em algumas plantas, a desgaseificação é feita durante a extração. Neste arranjo, o aço líquido do forno primário de fabricação de aço é aproveitado em um distribuidor ou em uma pequena panela. A partir da pequena concha, o fluxo de líquido cai para uma concha que é evacuada. A panela é fechada por cima com uma tampa especial que contém a abertura de exaustão. Aço líquido com superaquecimento de 25°C a 30°C é colocado na panela.
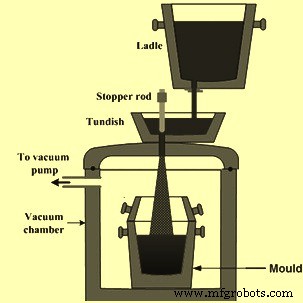
Fig 1 Esquema da panela para desgaseificação do molde
Prática de desgaseificação de circulação\
Na prática de desgaseificação por recirculação, o aço líquido pode circular continuamente na câmara de vácuo por arranjo especial. Neste processo, uma câmara de vácuo é posicionada acima da concha possuindo um snorkel ou snorkels que são mergulhados no banho de aço líquido. Existem dois tipos de processos de desgaseificação da circulação (Fig. 2) nomeadamente (i) processo de desgaseificação de Ruhrstahl – Heraeus (RH) e (ii) processo de desgaseificação de Dortmund – Hörder (DH). O processo de desgaseificação RH tem dois snorkels mergulhados na concha, enquanto o processo de desgaseificação DH tem um único snorkel e opera sugando repetidamente o aço líquido para a câmara de vácuo e depois liberando-o de volta na concha. O processo de desgaseificação RH é descrito em um artigo separado fornecido no link http://www.ispatguru.com/rh-vacuum-degassing-technology/.
Fig 2 Esquema dos processos de desgaseificação da circulação
No processo de desgaseificação RH, uma concha cilíndrica revestida de refratário com duas pernas (também chamada de snorkel) é projetada de modo que o aço líquido seja levantado em uma perna e caia de volta na panela após a desgaseificação através da segunda perna. O lado superior da carcaça cilíndrica é fornecido com exaustão, adições de liga, janela de observação e controle. A casca cilíndrica é revestida com tijolos de argila refratária na parte superior e tijolos de alumina (Al2O3) na parte inferior para sustentar a alta temperatura. As pernas são forradas com refratários Al2O3. O argônio (Ar), o gás de elevação, é injetado no tubo de entrada para aumentar a velocidade do aço líquido que entra no tubo de entrada.
A operação do desgaseificador RH inclui o seguinte.
- Aquecimento da câmara cilíndrica até a temperatura desejada (varia entre 900°C e 1500°C).
- Abaixamento da câmara em aço líquido até o nível desejado.
- Evacuação da câmara para que o líquido comece a subir na câmara.
- Introdução do gás de elevação que se expande e cria uma força de flutuação para aumentar a velocidade do aço líquido subindo para o snorkel de entrada.
- A desgaseificação do aço líquido na câmara ocorre e ele flui de volta através do outro snorkel para a concha. Este aço desgaseificado é ligeiramente mais frio que o aço na panela. A força de empuxo criada pela diferença de densidade (a densidade do aço líquido mais frio é maior que a do aço quente) agita o banho.
- A taxa de circulação do aço líquido na câmara cilíndrica controla a desgaseificação. A taxa de circulação depende da quantidade de gás de elevação e do grau de vácuo. 110 toneladas de aço líquido podem ser desgaseificadas em 20 minutos pela circulação de aço líquido a uma taxa de 12 toneladas/min. O consumo específico de Ar é de cerca de 0,075 cum/ton.
- Adições de ferro-ligas podem ser feitas no final da desgaseificação, dependendo do superaquecimento.
O processo RH tem várias vantagens que incluem (i) as perdas de calor são relativamente baixas, (ii) as adições de liga podem ser ajustadas mais de perto e (iii) a pequena capacidade de bombeamento de vácuo é adequada, pois o volume menor deve ser evacuado em comparação com panela a panela ou fluxo de desgaseificação.
No processo de desgaseificação DH, uma pequena quantidade em torno de 10% a 15% da massa total de aço líquido é desgaseificada de cada vez. O processo é repetido até que o nível necessário de desgaseificação seja alcançado. A disposição de um recipiente e da panela é um pouco semelhante, exceto que (i) no processo de desgaseificação DH o recipiente cilíndrico tem um snorkel e (ii) o recipiente cilíndrico tem instalação de aquecimento.
A câmara DH está equipada com instalação de aquecimento, arranjo de adição de liga e sistema de exaustão. O fundo do recipiente cilíndrico é fornecido com um snorkel que pode ser mergulhado no aço líquido. A parte superior da câmara DH é revestida com os tijolos refratários e a parte inferior com os tijolos de Al2O3. Snorkel é revestido com tijolos de Al2O3 de maior qualidade. O comprimento do snorkel é suficientemente grande para perceber o efeito da pressão atmosférica na elevação do aço no snorkel. A seguir estão os passos importantes para a operação do processo de desgaseificação DH.
- A câmara DH é pré-aquecida e abaixada na concha para que a ponta do snorkel mergulhe abaixo da superfície de aço líquido.
- A câmara evacuada é movida para cima e para baixo para que o aço entre na câmara.
- A câmara é movida de 50 a 60 vezes com um tempo de ciclo de 20 segundos.
- A desgaseificação adequada é possível em 20 a 30 ciclos.
- Uma camada de escória é mantida na panela para minimizar as perdas de calor.
- O processo de desgaseificação DH pode operar com superaquecimentos mais baixos em comparação com RH, pois a unidade DH possui instalação de aquecimento.
Prática de desgaseificação de panelas ou tanques
Aqui, a panela é colocada em um tanque a vácuo e agitada com um gás inerte enquanto o tanque é evacuado. Alternativamente, a panela pode ter um dispositivo de vedação na sua periferia para uma tampa a ser encaixada que forma a câmara de vácuo.
O aço líquido pode ser tratado em um tanque desgaseificador sem reaquecimento do arco. Isso pode ser feito com dois sistemas de agitação diferentes, a saber (i) uma agitação indutiva do banho de aço líquido e (ii) a agitação do banho borbulhando Ar através de um tampão poroso localizado no fundo da panela.
Uma prática de desgaseificação do tanque é usada (i) para reduzir as concentrações de gases dissolvidos no aço líquido, (ii) para homogeneizar a composição do aço líquido e a temperatura do banho, (iii) para remover materiais de inclusão de óxido do aço líquido e (iv) ) fornecer os meios e as condições técnicas favoráveis à dessulfuração. A remoção do enxofre (S) é conseguida através de reações de escória-metal, que são promovidas por forte fluxo de Ar (borbulhamento) dentro do envelope de vácuo. O processo de desgaseificação do tanque requer (i) evacuação rápida do tanque de vácuo, (ii) manutenção do vácuo enquanto ao mesmo tempo suga um fluxo pesado de gás inerte, (ii) disponibilidade imediata, (iv) resistência à poeira e (v) ) operação segura em condições adversas.
A panela é fornecida com um tampão poroso na parte inferior para purgar o gás Ar. A concha é colocada em uma câmara de vácuo. A câmara de vácuo está equipada com uma tremonha para fazer adições de elementos quando necessário. O gás de agitação é introduzido de cima através do teto por um tubo refratário submerso ou através do plugue poroso instalado na parte inferior da panela. Para desgaseificação eficaz de aço totalmente morto, é melhor purgar Ar pelo fundo da panela. A agitação do banho aumenta a taxa de remoção de gás. A remoção vigorosa de gases também causa respingos de aço líquido. Assim, a panela não é totalmente preenchida e cerca de 25% de sua altura é mantida como borda livre para acomodar as gotas salpicadas de aço líquido. A pressão é mantida entre 1 mm Hg a 10 mm Hg para uma desgaseificação eficaz. Durante a desgaseificação são feitas adições para desoxidação e liga. Em certos casos, a panela é aquecida para compensar a perda de calor durante a desgaseificação. Para a eficácia da desgaseificação, é necessário que o transporte de escória do forno primário de fabricação de aço seja o mais baixo possível. A escória transportada contém FeO e como o teor de O2 do aço está em equilíbrio com o teor de FeO da escória, o teor de O2 do aço aumenta.
Os requisitos fundamentais para o processo de desgaseificação da panela incluem (i) margem livre suficiente na panela para conter a escória induzida pelo vácuo e a ebulição do aço, (ii) um gás inerte percolando através do banho de aço para agitação, separação de inclusão e aprimoramento do desempenho de desgaseificação a vácuo , (iii) superaquecimento suficiente no aço para evitar a formação de caveiras, e (iv) meios para fornecer aditivos enquanto a panela está dentro do tanque de vácuo.
A conexão Ar com a panela é estabelecida quando a panela é colocada dentro do tanque de vácuo. O tanque de vácuo é evacuado para as pressões de operação necessárias por um sistema de bombeamento de vácuo. As emissões são evacuadas através do sistema de bombeamento a vácuo e são coletadas antes das bombas ou são descarregadas sob a água contida em um poço quente de concreto equipado com parede de açude. Os gases de processo, incluindo aqueles arrastados na água de descarga do condensador, são expelidos do poço quente por meio de um ventilador motorizado para uma chaminé de ventilação equipada com um queimador de flare. A água quente do poço é bombeada para uma torre de resfriamento do sistema de água de contato.
Esquemas de importantes processos de desgaseificação da panela são mostrados na Fig 3.
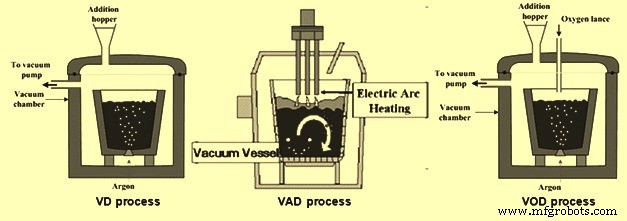
Fig 3 Esquema dos processos de desgaseificação da panela
Processo de desgaseificação a vácuo (VD)
Esta é uma unidade de desgaseificação de panela simples com provisões para adições de liga. Aqui, o vácuo é criado através de um sistema de bombeamento de vácuo. Uma pressão tão baixa quanto 0,5 mm Hg é criada. O processo é capaz de (i) homogeneização do banho de aço líquido em relação à temperatura e composição, (ii) ajuste fino da química e (iii) melhor desoxidação e redução nos teores de H2, N2 e O2. A dessulfuração é um grande problema para os calores processados diretamente através da unidade VD do forno primário de fabricação de aço. No entanto, o problema pode ser resolvido garantindo a redução da escória na panela antes de enviar o calor para a unidade VD e a dessulfuração aprimorada é causada pela mistura de escória-metal.
Processo de desgaseificação por arco a vácuo (VAD)
O processo de desgaseificação por arco a vácuo (VAD) é um processo de desgaseificação do tanque com eletrodos adicionados com a finalidade de reaquecer o aço líquido. Este é um processo de unidade única no qual a panela fica em um tanque a vácuo e é agitada por gás inerte através de um tampão poroso na parte inferior com provisão para aquecimento através de eletrodos e adições de liga. Após a adição de cal ao aço líquido na panela, o arco é realizado a uma pressão de 250 mm Hg a 300 mm Hg para aumentar a temperatura e fundir a cal seguida de desgaseificação de curta duração, adições para ajuste químico e desgaseificação profunda às pressões tão baixo quanto 1 mm Hg. A agitação do Ar é continuada em todas as etapas operacionais e o ajuste da vazão é feito para diferentes operações realizadas durante o processo de VAD. A taxa de aquecimento é de cerca de 3 graus C/min a 4 graus C/min e durante o aquecimento a taxa de fluxo de Ar é mantida no lado inferior. Neste sistema, sob vácuo, a reação C-O2 e a reação C-Al2O3 sob o arco de alta temperatura são de grande ajuda na obtenção de baixo teor de O2 sem qualquer produto sólido da reação. Níveis de H2 tão baixos quanto 1,5 ppm são alcançados devido à intensa transferência de massa por Ar e baixa pressão parcial de H2 devido à diluição do monóxido de carbono (CO) liberado. A principal vantagem deste processo é o alto grau de dessulfuração de até 80% para a produção de aços com níveis de enxofre tão baixos quanto 0,005%. O VAD é agora um processo amplamente utilizado para a produção de aço limpo.
ASEA – processo SKF
É um processo que possui um grupo integrado de unidades de tratamento geralmente consistindo em unidades separadas de desincrustação, aquecimento a arco e tratamento a vácuo. Aqui, a escória é removida por re-embalagem para evitar a refosforização após a qual a adição de ferro-liga é realizada. O aquecimento do arco é feito para aumentar a temperatura para compensar o efeito de resfriamento das adições de liga seguido de desgaseificação em uma atmosfera de vácuo para reduzir o teor de O2 e desidrogenação para atingir teores de H2 tão baixos quanto 1,5 ppm. O método envolve a aplicação de agitação eletromagnética que ajuda na flutuação das inclusões e resulta na produção de aços limpos. Atualmente, as unidades ASEA-SKF incorporaram agitação básica de gás inerte para permitir a dessulfuração.
Processo de descarbonetação de oxigênio a vácuo (VOD)
O processo VOD é uma unidade de desgaseificação do tanque que é adicionalmente equipada com uma lança de sopro de O2. Este fornecimento adicional de O2 pode ser utilizado para a produção de aço inoxidável grau C extra baixo (descarbonetação forçada) ou para aquecimento químico do aço líquido em conjunto com adições de Al/Si (silício) (processo VD-OB). A bomba de vácuo é projetada de acordo, tendo uma capacidade maior para lidar com o aumento do volume de gás.
O processo VOD é considerado um importante processo de vácuo para a produção de aço inoxidável. É principalmente adequado para aços inoxidáveis especiais que requerem o valor muito baixo dos níveis de C, N2 e H2. Neste processo, a panela é colocada na câmara de vácuo e há uma disposição para o lancetagem de O2 através de uma gaxeta estanque a vácuo e adições de liga. Basicamente, o processo envolve a oxidação preferencial do carbono sobre o Cr, levando a perdas mínimas de Cr.
Devido à redução do bordo livre disponível na panela, o teor inicial de C do aço líquido deve ser tão baixo quanto 1%. Aqui, a injeção de O2 é realizada em 100 mm Hg a 250 mm Hg. O Si é oxidado seguido de C. A descarbonetação ocorre através do início do borbulhamento determinado pela temperatura inicial e teor de Si do aço líquido. A taxa constante de descarbonetação ocorre dependendo da taxa de fluxo de O2. A relação CO/CO2 é monitorada e com um teor de C do banho de 0,08%, ela aumenta rapidamente. Além dessa porcentagem limitante de C, a taxa de descarbonetação cai independente da taxa de fluxo de O2 com oxidação simultânea de Cr. A punção de O2 é interrompida e a pressão do vaso é reduzida e a agitação de Ar é realizada ainda mais para a reação entre o O2 dissolvido e o C restante. Foi relatado que através de agitação vigorosa o C pode ser reduzido a níveis de 0,005% e C + total N2 inferior a 0,015% são alcançados.
A sequência de refino em geral é controlada pela combinação da variação da vazão de O2, distância ponta da lança – superfície do banho, controle da pressão de vácuo e vazão de Ar. A adição de quantidade suficiente de cal e Al ajuda na excelente dessulfuração do aço líquido.
Sistema de bomba de vácuo
O sistema de bomba de vácuo é a força motriz para os processos de desgaseificação a vácuo para aço líquido. Para criar vácuo, existem três tipos básicos de sistemas de bomba de vácuo que podem ser usados. Cada um tem suas próprias vantagens e desvantagens. São (i) ejetores de vapor com estágios de condensação necessários, (ii) ejetores de vapor em combinação com bombas de anel de água e (iii) sistemas de bombeamento mecânico a seco. Os jatos de vapor funcionam em uma base de fluxo de massa constante, enquanto as bombas de vácuo de anel de água funcionam em uma base de volume constante. Usados em conjunto, um ponto de equilíbrio econômico pode ser alcançado para aproveitar as melhores características de cada um. O sistema de bombeamento a vácuo com ejetores de vapor, bem como com ejetores de vapor junto com bombas de anel de água são mostrados na Fig 4.
Fig 4 Sistemas típicos de bombeamento a vácuo
Vários fatores desempenham um papel na seleção dos sistemas de bomba de vácuo. Estes são dados abaixo.
- A quantidade de gases dissolvidos a serem removidos. A pressão absoluta, a química do aço e a vazão de Ar afetam as taxas nas quais os gases são removidos pelo sistema de bombeamento a vácuo.
- A carga na pressão de projeto do sistema em "equivalente a ar seco".
- A carga que o sistema precisa atender em diferentes pressões (se exigido pelo sistema de desgaseificação).
- O volume do sistema envolvido.
- O requisito de tempo de processo necessário para ir da atmosfera ao vácuo profundo.
- A pressão absoluta final do sistema. Isso determina o número de estágios necessários.
- A quantidade de Ar necessária. Isso determina a energia de agitação e a taxa de remoção de gás dissolvido.
- A taxa de vazamento de ar no sistema.
- A pressão e a temperatura do vapor no caso de sistemas ejetores de vapor.
- A temperatura da água de resfriamento no caso de sistemas ejetores de vapor.
- O custo do vapor e da eletricidade
Cada sistema de desgaseificação deve ser projetado para atender aos requisitos específicos do processo de desgaseificação a vácuo.
Processo de manufatura
- Projetando Processos para Robôs vs. Pessoas
- Processo Finex para Produção de Ferro Líquido
- Processo de seleção do local para uma usina siderúrgica de campo verde
- Tecnologia de desgaseificação a vácuo RH
- Metalurgia Tundish
- Processos de fabricação de aço inoxidável
- Processo de Laminação para Aço
- Breakouts durante o lingotamento contínuo de aço líquido
- Classes de aço ferramenta para punções e matrizes
- Melhores materiais para peças torneadas