O uso de inspeção visual em gerenciamento de ativos e controle de qualidade
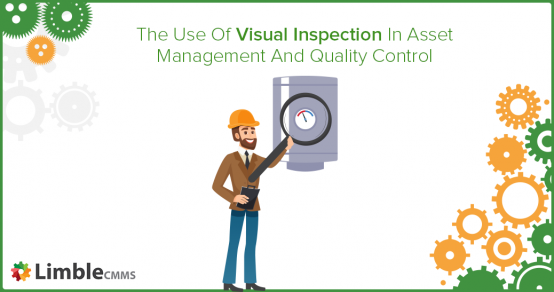
A inspeção visual é uma técnica muito comum utilizada pelos profissionais de manutenção na gestão de ativos físicos, bem como a última etapa na linha de produção de diversos bens.
Enquanto os engenheiros estão constantemente encontrando novas maneiras de automatizar ações repetitivas amplamente utilizadas, as inspeções visuais provaram ser bastante resistentes a esse respeito, especialmente no campo da manutenção de equipamentos.
Nesta postagem, tentamos entender a inspeção visual de vários pontos de vista. Discutimos os casos de uso básicos e modernos. Como a inspeção visual pode fornecer resultados variados devido à sua natureza subjetiva, encerraremos as coisas descrevendo as etapas que você pode seguir para padronizar o processo de inspeção.
A definição de uma inspeção visual
A inspeção visual é um método de inspeção muito básico usado no controle de qualidade de fabricação e manutenção de ativos. É o método de busca de falhas ou imperfeições a olho nu e com equipamentos de inspeção não especializados.
Muitas vezes, não existe uma fórmula empírica para encontrar produtos defeituosos ou inspecionar uma peça do equipamento. Portanto, a experiência da pessoa que está realizando a inspeção visual desempenha um papel significativo na determinação da eficácia do processo.
Procurar anomalias a olho nu é o método mais comum de inspeção visual. Mas não se limita necessariamente a isso. O uso de outros sentidos para inspeção também cai sob o amplo guarda-chuva da inspeção visual. O princípio básico é que uma pessoa experiente está usando suas capacidades sensoriais para identificar problemas com objetos que inspeciona.
Por exemplo, profissionais experientes podem avaliar a qualidade de materiais como madeira e metais, julgando o som produzido por eles. Eles podem simplesmente bater no objeto e fazer um julgamento com base no som produzido por ele.
Da mesma forma, um técnico de manutenção pode cheirar um vazamento de gás, ouça que algo está solto dentro do ativo, ou mesmo sentir que uma peça do equipamento vibra mais do que deveria ou irradia calor excessivo. Tudo isso durante a realização de uma inspeção visual .
Inspeções visuais na gestão de ativos físicos
A inspeção visual é parte integrante do gerenciamento de ativos físicos. Os profissionais de manutenção usam-no diariamente como parte de suas atividades de manutenção de rotina.
Ocasionalmente, uma organização treinará operadores de máquina para realizar inspeções visuais em vez de técnicos de manutenção. Essa prática é comumente conhecida como manutenção autônoma.
As inspeções regulares ajudam as equipes de manutenção a identificar sinais de desgaste que podem levar à falha do equipamento. Pequenos problemas são corrigidos no local se o técnico tiver acesso às ferramentas e peças certas. Caso contrário, eles deixarão uma nota sobre o problema detectado. O gerente ou supervisor de manutenção mais tarde adicionará uma nova tarefa ao plano de manutenção preventiva para que o problema não fique sem solução.
Embora possam ser muito úteis, as inspeções visuais apresentam algumas desvantagens. Freqüentemente, as máquinas precisam ser desligadas para que um técnico possa realizar uma inspeção visual. Como você pode imaginar, isso reduz o tempo de atividade do equipamento e pode prejudicar os resultados financeiros. O outro problema é que as inspeções visuais às vezes podem localizar o problema tarde demais. Se você detectar ruído, calor ou fumaça, a falha pode já estar em andamento.
Para combater esses problemas, mais e mais organizações estão usando sensores e equipamentos de monitoramento de condição para monitorar a integridade e o desempenho dos ativos em tempo real. Essa tecnologia permite que eles percebam os sinais de deterioração muito antes do que seria possível. Isso está perfeitamente representado no gráfico abaixo.
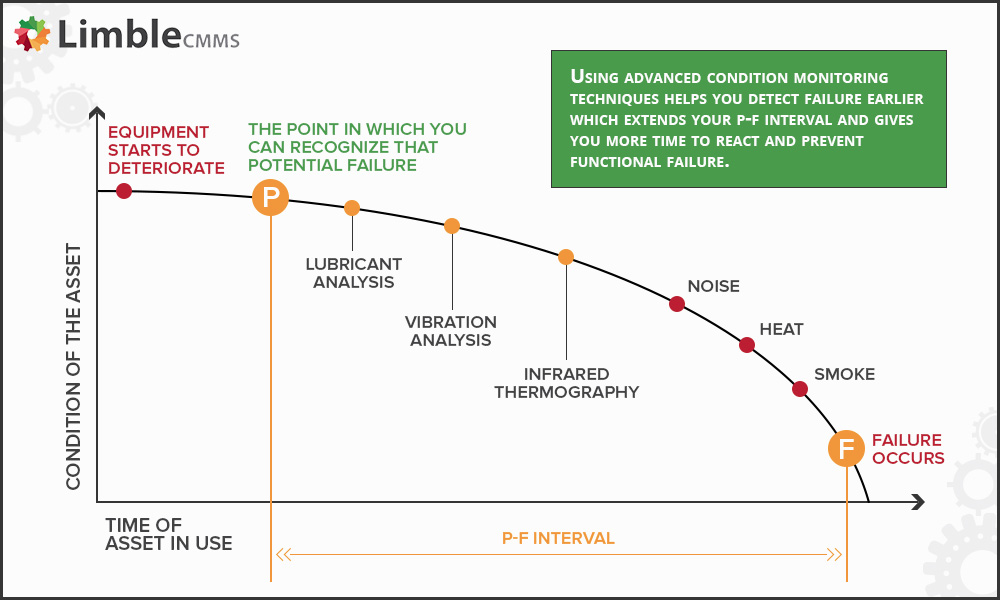
Esses sensores permitem que as organizações executem estratégias de manutenção avançadas, como manutenção baseada em condições e manutenção preditiva. Essas estratégias reduzem a necessidade de inspeções visuais, mas estão longe de torná-las obsoletas. Os sensores ainda são bastante caros e só podem detectar sinais de deterioração específicos. Isso significa que manual métodos de teste como inspeções visuais não são apenas necessários, mas uma opção mais econômica, especialmente para ativos baratos.
Inspeções visuais no controle de qualidade
A inspeção visual é o método de teste não destrutivo (NDT) mais antigo para controle de qualidade. Em sua forma original, a inspeção visual é usada para observar a superfície de um objeto e procurar rachaduras, arranhões, desalinhamentos, corrosão e outros defeitos físicos.
Grandes marcas, especialmente aquelas que produzem produtos caros, têm muito a perder se enviarem uma linha inteira de produtos defeituosos. A inspeção visual é uma ótima maneira de filtrar rapidamente itens com defeitos óbvios.
Por exemplo, fabricantes de automóveis como a Rolls-Royce dão extrema importância ao ajuste e acabamento de cada componente que entra em seus carros. Sua pesquisa interna mostra como cerca de 70% de todos os componentes com defeito são rejeitados devido a discrepâncias encontradas durante a inspeção visual .
Isso não quer dizer que as inspeções visuais sejam reservadas apenas para produtos de luxo. Um bom contra-exemplo vem da indústria de alimentos e bebidas. Aqui, as inspeções visuais são realizadas para garantir que não haja nenhum objeto estranho no produto, que as embalagens sejam uniformes e devidamente lacradas e que os produtos não estejam etiquetados incorretamente. Devido à natureza bastante direta dessas inspeções, muitos fabricantes de alimentos estão começando a adotar sistemas de visão de máquina para o controle de qualidade.
Um exemplo de sistema de inspeção visual automatizado ( Fonte da imagem )
Em termos gerais, o teste visual para controle de qualidade pode ser feito de três maneiras diferentes:
- Amostragem aleatória: As verificações de qualidade são realizadas em produtos selecionados aleatoriamente. Os produtos podem ser verificados na linha de produção quanto a defeitos visuais óbvios. Inspeções mais complexas (como testar o interior de um produto) geralmente são realizadas em áreas de teste especiais.
- Amostragem manual completa: Todos os produtos são inspecionados manualmente. Este pode ser um trabalho fisicamente exigente com muitas ações repetitivas. Para maximizar a saúde e a produtividade dos trabalhadores que realizam as inspeções, as organizações devem procurar fornecer as ferramentas e equipamentos ergonômicos necessários.
- Inspeção visual automatizada: Os produtos são inspecionados por meio de câmeras, métodos de processamento de imagem e algoritmos de aprendizado de máquina. Mais sobre isso posteriormente no artigo.
Os sistemas automatizados de inspeção visual parecem estar ganhando mais força à medida que o setor privado desenvolve soluções específicas para a indústria. Resta saber com que rapidez os fabricantes adotarão essa tecnologia.
Técnicas modernas de inspeção visual
As melhorias tecnológicas incrementais na qualidade da câmera e no aprendizado de máquina estão começando a mudar a forma como pensamos sobre as inspeções visuais. Os técnicos de manutenção agora têm a capacidade de realizar inspeções visuais em locais perigosos e de difícil acesso, estando a quilômetros de distância dos objetos que estão inspecionando. Os especialistas em controle de qualidade, por outro lado, têm cada vez mais acesso a soluções de inspeção visual automatizada.
Inspeções visuais remotas para manutenção de ativos
Hoje em dia, os técnicos podem usar robôs e drones para visualizar áreas de outra forma inacessíveis. Estamos falando de inspecionar objetos em grandes alturas, espaços muito confinados, locais perigosos como tanques de armazenamento e similares.
As imagens ou vídeos podem ser visualizados de um local remoto, até mesmo milhares de quilômetros de distância do local da inspeção - daí o nome inspeção visual remota. Os dados capturados podem ser acessados de duas maneiras diferentes:
- Transmissão ao vivo: Robôs ou drones podem retransmitir dados da localização para a estação base, onde o inspetor pode assistir a transmissão ao vivo. Nesse caso, o robô ou drone também pode ser controlado a partir do terminal remoto. Só pode ser usado nos casos em que haja comunicação sem fio constante entre o equipamento que está sendo operado e a estação base.
- Dados salvos :Em áreas extremamente remotas ou perigosas, onde não pode haver comunicação sem fio, os vídeos e as imagens são salvos e analisados posteriormente.
Uma vantagem adicional desses tipos de inspeções é que as imagens e vídeos podem ser facilmente compartilhados entre os técnicos e outros membros da equipe relevantes, sem a necessidade de estar fisicamente presente no local da inspeção. Esta colaboração pode ser extremamente útil na solução de problemas complexos ou quando houver necessidade de contatar especialistas especializados.
Inspeções visuais automatizadas (AVI) para produção em massa
A inspeção visual automatizada (AVI) usa visão computacional e inteligência artificial para realizar inspeções visuais em produtos, em vez de inspetores de qualidade. Essa tecnologia visa reduzir drasticamente a necessidade de intervenção humana para inspeção em fábricas automatizadas de grande escala.
Solução de inspeção visual cognitiva da IBM ( Fonte da imagem )
Foxconn, um dos maiores fabricantes de eletrônicos do planeta, está usando AVI em suas instalações de manufatura. Vamos usá-los como um exemplo para descrever brevemente como essa tecnologia deve funcionar.
Suponha que a Foxconn esteja fabricando placas-mãe para o iPhone mais recente. Uma amostra ideal da placa-mãe é feita e inspecionada por um inspetor visual humano. Depois de aprovado, esse modelo é carregado no banco de dados e o algoritmo pode usá-lo como referência. Alguns exemplos de modelos com defeito também são carregados no servidor e usados para ensinar algoritmos como reconhecer anomalias específicas.
O resto das placas-mãe sairão da linha de montagem automatizada e passarão pelos sistemas de câmeras do AVI. Várias imagens do produto são capturadas de vários ângulos. As imagens capturadas são comparadas às imagens de benchmark armazenadas usando algoritmos de aprendizado de máquina. Alguns dos fatores comparados podem ser:
- tamanho e forma de diferentes elementos
- locais de solda
- localizações de componentes
- componentes ausentes
- conectores
- anomalias de cor
O produto passa na inspeção se estiver suficientemente próximo da referência.
Pelo valor de face, essa tecnologia parece uma solução perfeita. Afinal, a ideia principal por trás da automação é deixar as tarefas rotineiras e mundanas para as máquinas, para que os funcionários possam se concentrar na solução criativa de problemas. É uma boa ideia, mas ainda existem muitas limitações que precisam ser abordadas antes que se torne um padrão no espaço industrial.
As limitações das soluções automatizadas
Existem dois impedimentos principais para a adoção da automação na inspeção visual.
O primeiro são as limitações tecnológicas . Embora os pesquisadores de IA tenham feito grandes avanços, os algoritmos de inspeção estão longe de ser perfeitos. Eles precisam de muitos exemplos de produtos bons e defeituosos para que possam aprender como detectar diferentes anomalias com bastante sucesso. Além disso, as máquinas têm dificuldade em trabalhar com superfícies reflexivas. Isso eliminaria o trabalho com a maioria dos metais encontrados em uma planta. Essas diferenças mínimas ainda não podem ser capturadas pelos algoritmos, mas os humanos podem fazer isso facilmente.
O segundo fator é o custo . Para implementar um sistema de inspeção automatizado, deve haver equipamentos complementares, como máquinas de imagem, ferramentas de rede, hardware de computador, etc. Esses custos de hardware, além do custo de software, ainda os tornam proibitivos para muitas organizações.
Com o tempo, a qualidade e o preço dos sistemas de inspeção visual automatizados devem cair e devemos ver uma adoção mais ampla.
Como padronizar o processo de inspeção visual
A padronização de qualquer processo torna-o repetível e verificável. Mas um problema com a padronização das inspeções visuais é que uma grande parte do trabalho é de natureza muito subjetiva e muito difícil de empacotar como uma lista de verificação.
Esforços de padronização na manutenção
As atividades de manutenção são frequentemente padronizadas por meio de procedimentos operacionais padrão escritos, diretrizes de segurança (como LOTO) e listas de verificação de manutenção. As inspeções visuais, até certo ponto, podem ser abordadas da mesma maneira.
Uma vez que os técnicos de manutenção já devem saber como realizar inspeções visuais básicas, diretrizes escritas podem ser criadas apenas para equipamentos complexos onde a inspeção adequada requer várias etapas para ser concluída.
O processo de padronização pode ser mais ou menos assim:
- Registre todos os ativos que são inspecionados visualmente regularmente.
- Mapeie as áreas pertinentes a serem verificadas.
- Anote as ações a serem tomadas dependendo do sinal de deterioração localizado.
- Crie um fluxograma com base nas informações acima.
- Crie uma lista de verificação de manutenção para as dicas que devem ser inspecionadas.
- Se possível, adicione a lista de verificação e o fluxograma ao seu sistema CMMS. Se você tem um CMMS móvel, os técnicos podem acessar rapidamente essas informações em seus smartphones e tablets, o que pode acelerar significativamente o fluxo de trabalho.
- Ocasionalmente, revise e atualize esses fluxogramas e listas de verificação.
Um ativo pode ter um milhão de problemas diferentes, mas o objetivo de uma inspeção visual direta é procurar sinais comuns de desgaste.
As listas de verificação de manutenção devem sempre ser criadas por técnicos experientes, familiarizados com o funcionamento interno dos equipamentos em suas instalações. Normalmente, serão as mesmas pessoas encarregadas de treinar novos técnicos. Isso é perfeito, pois os novos técnicos colherão o maior valor desses esforços de padronização.
Esforços de padronização para gerenciamento de qualidade
A chave para padronizar as inspeções visuais na gestão da qualidade está no processo de treinamento, que deve incluir:
- diretrizes muito claras sobre o que é considerado um defeito
- o que fazer com um produto com defeito
- quando e como usar quaisquer ferramentas especiais de inspeção visual
- quem contatar em casos limítrofes (pedindo uma segunda opinião)
- como e onde observar novas anomalias
- quaisquer outras diretrizes especiais que precisem ser seguidas no chão de fábrica
Mesmo depois disso, haverá casos em que a subjetividade do processo gerará polêmica. Um pequeno arranhão no produto pode prejudicar o negócio de um inspetor, enquanto o outro o marcaria como pronto para uso. Algum nível de inconsistência é inevitável, mas pode ser minimizado por meio da padronização.
Inspecione à distância
Vai demorar um pouco até que a tecnologia se torne um substituto adequado para os olhos e julgamento humanos. E isso vai demorar muito mais até que a mesma tecnologia se torne acessível para operações de pequeno e médio porte.
Até então, esta atividade simples continuará a ser uma parte crucial da gestão de ativos e controle de qualidade, realizada por pessoal treinado.
Como sempre, se você tiver alguma dúvida, sinta-se à vontade para iniciar uma discussão nos comentários abaixo. Se você estiver interessado em aprender mais sobre manutenção e confiabilidade de equipamentos, verifique os artigos mais recentes no blog Limble.
Manutenção e reparo de equipamentos
- Navegando na modernização da manutenção e gestão de instalações
- Os benefícios da gestão estratégica de ativos
- O controle de qualidade é a primeira etapa para a confiabilidade do motor
- Garantia de qualidade na gestão de materiais MRO
- Como a Internet Industrial está mudando o gerenciamento de ativos
- Por que agora é a hora de obter o software de manutenção e gerenciamento de ativos
- IoT e ativos conectados – revolucionando o gerenciamento de ativos
- Os desafios e oportunidades do “All Digital” para o Sistema de Gestão da Qualidade (SGQ)
- O impacto do gerenciamento visual no setor
- Noções básicas de controle de qualidade e inspeção em usinagem CNC