Ei, Job Shops:hora de automatizar!
Acha que a automação é muito difícil em um ambiente de alto mix e baixo volume? Pense novamente
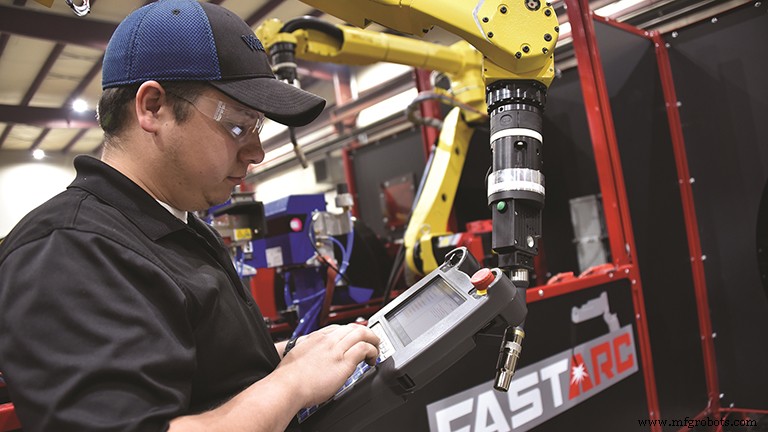
Robôs e oficinas de trabalho normalmente não são discutidos juntos. Afinal, todo mundo sabe que a automação é adequada apenas para produção de alto volume, e a típica operação familiar é tudo menos – sua agenda cheia de pedidos para trabalhos de alta mistura, baixo volume e muitas vezes altamente complexos. Quem precisa de um robô nesse ambiente, onde os setups são realizados várias vezes por semana, ou mesmo todos os dias?
Antes de pular para o próximo artigo, porém, você pode querer considerar algumas coisas. Para começar, muitos especialistas sugerem que, independentemente do que os proprietários possam dizer a si mesmos, as oficinas sofrem a menor utilização de máquinas do setor. Valores de eficácia geral do equipamento (OEE) de 50% ou menos não são incomuns. A automação é uma solução clara para melhorar esse número.
E como a troca de máquinas é mais frequente nas oficinas, são necessários maquinistas e programadores mais habilidosos para realizar atividades relacionadas à configuração – pessoas que estão comandando salários mais altos e são difíceis de encontrar. Isso aumenta os custos operacionais, reduz as oportunidades de trabalho adicional e torna a produção contínua extremamente desafiadora. Dada a escassez de trabalhadores qualificados, a automação deve, portanto, ser o Santo Graal para qualquer job shop, mesmo que a implementação possa não ser um caminho fácil.
Possibilidades de Plug and Play
A questão é, por onde você começa? Zach Spencer tem algumas ideias. Um engenheiro de proposta personalizada da Methods Machine Tools Inc., Sudbury, Massachusetts, ele observou que a automação pode estar próxima de um caso plug-and-play, especialmente quando incluída como parte de uma nova compra de máquina-ferramenta.
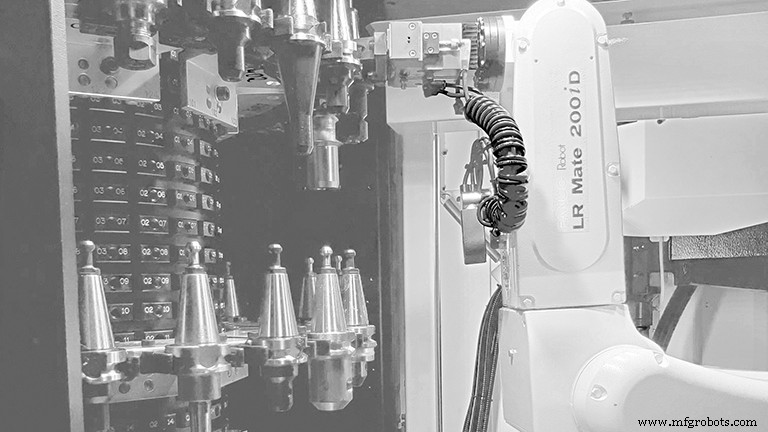
“Desenvolvemos nosso JobShop Cell há quase 15 anos e desde então se tornou uma das nossas soluções de automação mais populares para o FANUC RoboDrill”, disse ele. “Ele foi projetado para lojas que têm pelo menos algumas trocas todos os dias, são restritas no espaço físico e precisam de flexibilidade para alternar facilmente de uma parte para outra.”
O JobShop Cell está disponível em duas configurações, explicou. Um usa um arranjo de transportador acima/abaixo para trazer a matéria-prima para o robô e retirar as peças acabadas, enquanto o outro usa um gabinete contendo uma série de gavetas para armazenamento de peças e materiais. Ambos empregam um robô FANUC para carregar e descarregar a máquina (ou par de máquinas, no caso do Twin RoboDrill JobShop Cell da Methods), e ambos fornecem uma maneira de deixar um CNC sem supervisão por horas ou até mesmo um turno completo, dependendo da peça de trabalho.
Para volumes maiores, a Methods oferece o Plus-E, um sistema de automação multi-paletes estilo elevador para trabalhos de médio a alto volume, bem como o Plus-K para lojas que desejam automatizar a configuração e a operação da máquina, com a capacidade de trocar porta-ferramentas, morsas pré-carregadas e acessórios. “Você pode dizer ao sistema que esses cinco tornos são a Parte A, os próximos dois tornos são a Parte B, o seguinte é a Parte C e os próximos dez serão a Parte D”, disse Spencer. “Depois disso, basta carregar o material e ir para casa. Ambas as máquinas da Série Plus são unidades independentes que ficam ao lado de uma RoboDrill e são perfeitas para oficinas que procuram uma maneira fácil de entrar na automação.”
Pegue o carrinho
A Methods não é o único provedor que adota essa abordagem. Eric Nekich, responsável por operações, tecnologia e vendas internas da Lang Technovation Co., Hartland, Wisconsin, disse que os sistemas de automação RoboTrex da empresa usam um robô FANUC e até quatro carrinhos móveis, cada um contendo uma série de morsas pré-carregadas. O RoboTrex 52, por exemplo, pode armazenar até 42 tornos por carrinho (com base no tamanho da peça e na configuração do carrinho), oferecendo potencialmente usinagem autônoma de 168 peças.
Assim como o JobShop Cell, o RoboTrex é independente e totalmente protegido, mas também pode ser integrado a uma variedade de marcas e modelos de centros de usinagem. O único obstáculo é a necessidade de investir em algumas das morsas de cinco eixos Makro-Grip da Lang, necessárias para uso com o sistema (e feitas, coincidentemente, em 50 centros de usinagem equipados com RoboTrex na fábrica de Lang na Alemanha) . “É um investimento com um ROI muito rápido, no entanto, porque o tempo de atividade do seu fuso aumentará drasticamente com o sistema RoboTrex USA”, disse Nekich.
Michael Gamache é o gerente de desenvolvimento de negócios da Gamache Systems, com sede em New Berlin, Wisconsin, uma divisão da Metalcraft de Mayville e o integrador exclusivo dos sistemas RoboTrex nos Estados Unidos. Ele reconhece que alguns clientes podem se recusar a investir em um novo sistema de fixação de peças, mas ofereceu algumas excelentes razões para fazer exatamente isso.
“Como proprietário de uma empresa, entendo o fato de que os tornos não são baratos, mas do ponto de vista da automação, a fixação de alta qualidade é metade da batalha”, disse ele. “Você precisa levar a matéria-prima para o robô de maneira repetitiva e precisa, e o sistema Makro-Grip é uma das melhores maneiras de fazer isso. Além disso, o sistema é muito fácil de configurar e operar porque o robô está manipulando as morsas e não uma grande variedade de tamanhos de matéria-prima; por isso, um programa funciona para cada parte.”
Tenha um controle
Tyler Mardaus, engenheiro de design da Kurt Manufacturing – Divisão de Produtos Industriais, com sede em Minneapolis, concordou com a necessidade de fixação de alta qualidade, embora a abordagem de sua empresa seja significativamente diferente da proposta por Lang. “Nossa equipe de Custom Engineered Workholding (CEW) projeta muitos sistemas hidráulicos de dupla ação controlados por solenóide”, disse ele. “A hidráulica fornece psi mais alto e, portanto, maior força de fixação do que a fixação manual, enquanto o solenóide suporta a ativação eletrônica da morsa através do controle do robô ou da máquina, criando um sistema verdadeiramente automatizado.”
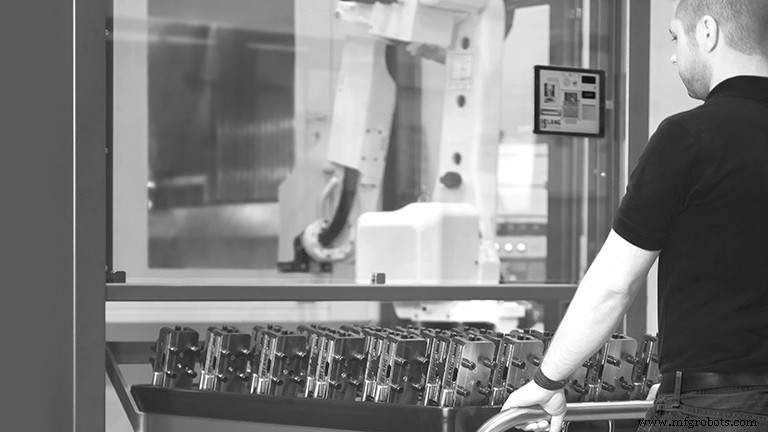
Ele acrescentou que as lojas devem iniciar sua jornada de automação visando os trabalhos de maior volume. E se houver peças que possam usar uma morsa (ou várias morsas) com mordentes usináveis, elas podem ser trocadas durante a troca, reduzindo o tempo de configuração. Quanto ao investimento, não há como evitar a necessidade de uma bomba hidráulica e encanamento, mas pode ser possível modernizar as morsas manuais existentes de uma oficina com conjuntos de porcas e parafusos hidráulicos.
“Você deve se esforçar para criar um sistema de controle de circuito fechado”, disse Mardaus. “Isso começa com a instalação de algum tipo de dispositivo de confirmação de assento parcial, mas você também precisa verificar se a morsa foi fixada com a força correta antes de permitir que o ciclo inicie e se a morsa está solta antes que o robô tente remover o peça de trabalho. Todas essas etapas são cruciais para qualquer solução de usinagem automatizada.”
Acelerando o intercâmbio de workholding
O comentário de Mardaus sobre a redução do tempo de setup está correto. Afinal, por que se preocupar em reduzir os custos de mão de obra por meio da automação se você vai incorrer em horas de inatividade cara toda vez que muda de emprego? As mandíbulas de troca rápida que ele mencionou são um excelente ponto de partida, mas se o orçamento permitir, um sistema de posicionamento de ponto zero, como o Makro-Grip de Lang (e outros), transforma a troca de workholding em um exercício de um minuto. Também deve haver recursos CAM robustos, com software de simulação que avalia os caminhos de ferramenta pós-processados, porta-ferramentas, ferramentas de corte, peças de trabalho, suporte de trabalho e a própria máquina-ferramenta.
E, como explicou Dietmar Moll, diretor de desenvolvimento de negócios da Zoller Inc., Ann Arbor, Michigan, as lojas devem dar alta prioridade ao gerenciamento de ferramentas, começando com um sistema de predefinição offline e software associado. “Um dos maiores benefícios de qualquer estratégia de automação é que a manutenção de máquinas e outros trabalhos sem valor agregado são assumidos por um robô ou cobot, liberando pessoal qualificado para realizar tarefas mais importantes”, disse Moll.
A predefinição de ferramentas offline é uma dessas tarefas, mas também há um planejamento de trabalho completo, manutenção e organização de porta-ferramentas, inspeção de ferramentas de corte e análise de dados de chão de fábrica. Para isso, a Zoller oferece uma variedade de soluções que vão muito além do conjunto de ferramentas. Suas soluções de gerenciamento de ferramentas (TMS) de nível Bronze, Silver e Gold permitem que uma oficina aumente seus recursos conforme necessário, proporcionando visibilidade significativamente maior aos processos de produção e ativos relacionados a ferramentas. E como eles podem se comunicar com o robô colaborativo »cora« de Zoller, acrescentou Moll, eles servem para “fechar o ciclo” automatizando tarefas da sala de ferramentas, como limpeza e armazenamento de ferramentas.
Da mesma forma, as soluções integradas de armazenamento de ferramentas da empresa ajudam a organizar esses ativos, reduzindo ainda mais o tempo de inatividade e a ineficiência. E quando o trabalho estiver concluído, esses mesmos sistemas podem ser usados para verificar as ferramentas de volta ao berço, revisar seu desempenho e registrar qualquer vida útil restante da ferramenta. “Isso ajuda as oficinas a entender melhor quais ferramentas de corte estão funcionando bem e quais não estão, dando-lhes a capacidade de melhorar ainda mais os processos e reduzir os custos de ferramentas”, disse ele.
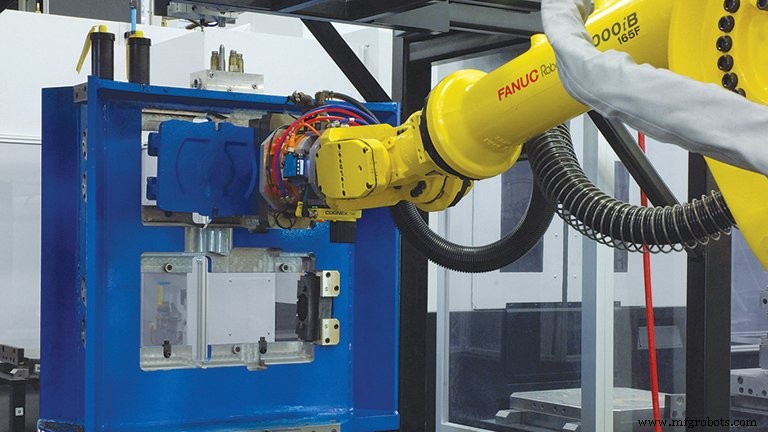
Sugestões de agendamento
O gerenciamento robusto de ferramentas também é uma parte essencial do agendamento de tarefas, algo crítico para a utilização de máquinas-ferramenta e robôs. Para Moll, isso significa saber quais são os próximos trabalhos e quais ferramentas são necessárias para executá-los. Para Daniel Carranco, significa mais do que isso, principalmente no contexto da automação. O diretor de melhoria contínua da Global Shop Solutions Inc., The Woodlands, Texas, observou que todas as lojas - automatizadas ou não - devem ter um bom sistema de ERP e agendamento, que também possa monitorar o chão de fábrica e coletar informações sobre o processo de usinagem.
Alcançar a parte de monitoramento e coleta de dados dessa equação requer software ERP, máquinas-ferramentas e robótica fáceis de integrar. “Tivemos situações em que o cliente queria integrar seu equipamento ao nosso sistema, mas descobrimos que era quase impossível trabalhar com a plataforma de software usada por esse equipamento”, disse ele. “Portanto, o primeiro conselho para quem busca um ambiente de produção integrado é garantir que tudo possa se comunicar de forma eficaz e que todos tenham clareza sobre os tipos e volumes de dados que serão trocados.”
Comunicação, ao que parece, significa mais do que antes. Onde os sistemas ERP há muito se destacam na coleta de dados dos humanos no chão de fábrica, agora eles também devem coletá-los de robôs e controladores de máquinas. Além disso, esses dados não apenas contêm o número de trabalho onipresente, o tempo de produção e a quantidade concluída (ou descartada) que os usuários esperam, mas também podem exibir o consumo de material em tempo real, informações de inspeção e qualidade da peça, status da máquina e do robô, e assim por diante.
“Certamente, há muito mais informações disponíveis hoje do que antes e, com o software, equipamento e integração de ERP corretos, tudo isso pode ser coletado de forma transparente e automática”, disse ele. “Fazer isso oferece oportunidades completamente novas para melhoria contínua, mas, mais importante, libera os funcionários para se concentrarem em coisas mais importantes. Não há mais perda de tempo na coleta manual de dados, que geralmente é irregular, e as pessoas podem trabalhar no planejamento e análise de processos.”
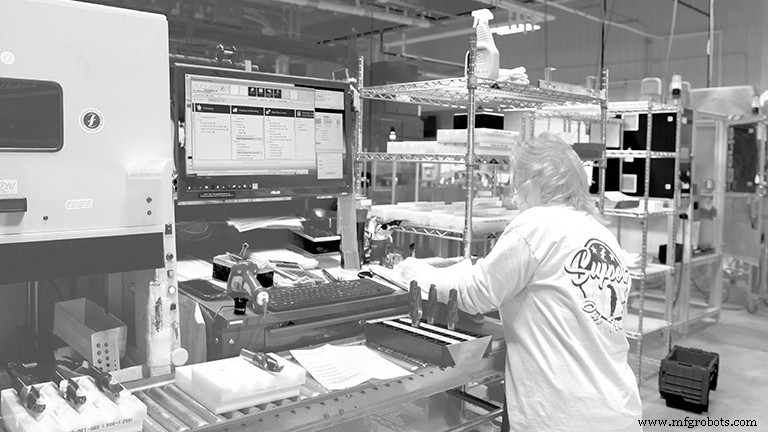
Aprimorando as práticas recomendadas
Como sugeriu Carranco, essas tecnologias devem ser buscadas independentemente dos planos de automação de uma oficina, pois todas servem para tornar as operações mais eficientes e seus níveis de OEE muito mais altos. E quando o próximo passo for dado – implementar um robô ou sistema de manuseio de materiais – o investimento será recompensado muito mais rápido. Supondo que você não se importe ou não possa usar nenhum dos sistemas pré-configurados já discutidos, a pergunta então se torna:“que robô devemos comprar e como devemos implementá-lo?”
Dean Elkins pode recomendar um. Líder do segmento de manuseio de materiais na Motoman Robotics Division da Yaskawa America Inc., Miamisburg, Ohio, Elkins disse que as oficinas geralmente apresentam uma variedade de aplicações robóticas adequadas, seja manutenção de máquinas, rebarbação de peças, montagem automatizada ou soldagem robótica. Encontrar o equipamento certo para essas aplicações, no entanto, requer uma boa avaliação e conversar com pessoas experientes.
“Justifying an investment in automation depends on several factors,” said Elkins. “Obviously, the larger the production quantity, the more it makes sense to automate it. But even lower volume, repeat work can be profitable, provided the shop takes the necessary steps to reduce setup time as much as possible. Parts with longer run times are also good candidates, as are parts with simple handling requirements.”
Elkins noted that most job shops find a small to medium-sized floor-mounted robot—meaning a payload of 5-25 kg—is all that’s needed to deburr a batch of parts, weld a crateful of brackets, or tend a CNC lathe after everyone’s gone home for the night. With that, however, some level of safety guarding will be required, as will grippers, an interface to the machine tool, and possibly programming and simulation software.
Tomorrow, Today
And don’t forget the training, he warned. Automation is much simpler than it once was, yet the savvier job shop owner is still going to make an additional investment in training, and have a dedicated person on staff to manage the shop’s robotics. That said, collaborative and force-limiting robots are becoming quite popular, especially where floor space is a concern. Robots can be equipped with self-changing or quick-change grippers, increasing flexibility. Vision systems can often eliminate or at least simplify part conveying systems, and the ability to teach a robot its tasks helps reduce the need for offline programming systems. “There’s a lot to consider,” said Elkins. “That’s why I encourage anyone interested in automation to do their homework, ask questions, and partner with a reputable integrator.”
Acieta LLC, Waukesha, Wis., is one such company. Steve Alexander, vice president of operations, warns that not all integrators are created equal. “Make sure you work with someone who has experience with your type of work and the skill level to implement your robotic automation project,” he said. “Get references, go see their previous installations, and understand the quality of their work. Industrial robots are designed to last well over 10 years, so you want to make sure everything else in the cell is designed for an automated environment and is just as reliable as the robot itself.”
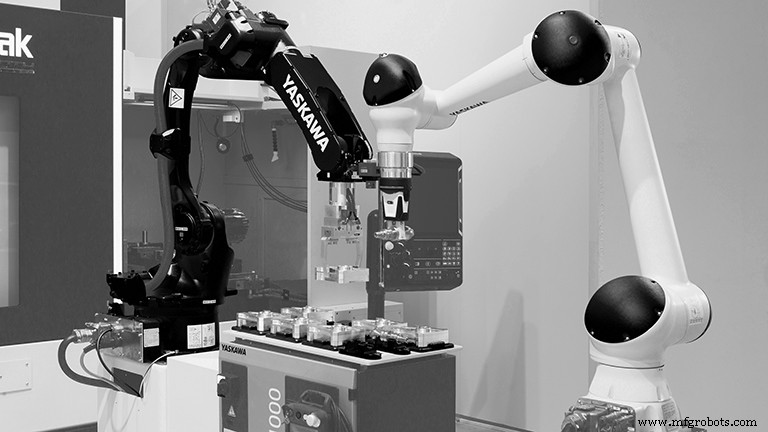
Doing so can lead to a return on investment (ROI) of just a few months, although a year or two is probably a more realistic expectation. Much of that depends on the application, of course, but the type of robot also plays a role. As Elkins noted, collaborative robots—or cobots—have become all the rage over the past few years, mainly due to their ease of use and seemingly safer operation in proximity to humans. Yet appearances can be deceiving. Cobots can be slower and less accurate than so-called “industrial robots,” possibly slowing ROI, and even the friendliest cobot can harm a human if established safety procedures aren’t followed.
This is why Elkins and others strongly recommend a risk assessment with any robot installation. He also suggested that the best approach for automation newbies is to start small and easy. “Find a single pain point and conquer that one first before looking at adding additional processes or complexity,” he said. “You want to have success right out of the gate so that everyone—the shop owner, the machine operators, and the people doing the integration—are comfortable moving on to larger or more complex projects. Sometimes, the biggest challenge is getting employee buy-in. There’s always the fear that robots will replace humans, so it’s important to make them part of the implementation. Educate them, get them involved in the roll-out, and when they find that the robot actually makes their job easier and more interesting, they’ll end up being your biggest cheerleaders.”
Sistema de controle de automação
- Automatizar ... ou então
- Hahn apresenta "amplo espectro" de soluções de automação na Automate
- Como a automação pode ajudar a acelerar uma vacina
- Atingindo o potencial total de automação - modelo operacional de automação (parte 3)
- Construindo a equipe - Modelo operacional de automação (Parte 2)
- A automação poderia ser a chave para a criação de empregos na manufatura?
- Sou muito pequeno para não automatizar
- Determinando quando investir em automação
- Dica interna do integrador de sistemas:quando automatizar
- Automação precisa – Automatize 2019 Press Release