Projeto da peça moldada por injeção, parte 3:Chefes
As peças moldadas por injeção são uma solução fantástica para produtos de médio a alto volume. Dependendo do produto, o volume de vendas alvo por ano, o custo das mercadorias e a estratégia de reparo planejado, moldados em saliências de plástico oferecem uma forma de baixo custo para alinhar as peças e fornecem opções de fixadores para componentes de montagem e proteção de gabinetes. No entanto, é necessária uma consideração adequada no projeto e na colocação dos ressaltos de montagem em uma peça de plástico para evitar falhas estéticas desnecessárias e resistência adequada para evitar falhas de projeto.
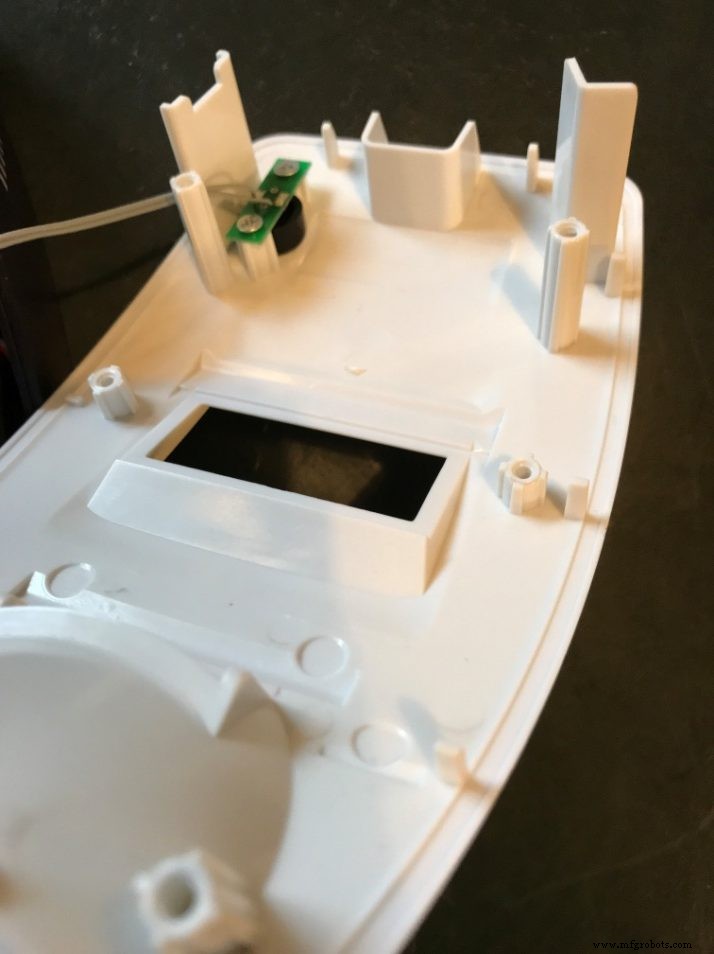
Pode-se encontrar muitas sugestões de design de peças de molde de injeção para a criação de ressaltos, mas muitas vezes essas diretrizes divergem entre si. As recomendações podem variar dependendo se são feitas por um fabricante de parafusos formadores de rosca, um fabricante contratado de moldagem por injeção, a equipe de montagem final ou mesmo, às vezes, um designer industrial. A verdade é que todas essas entradas precisam ser consideradas, e o recurso de saliência precisa ser executado e não causar falhas estéticas que são visíveis na peça. Mas para conseguir isso, um pequeno compromisso precisa ser alcançado pelo engenheiro mecânico que projeta a peça moldada por injeção. É claro que a entrada de todos os membros da equipe precisa ser considerada e, em particular, o moldador por injeção precisa ser trabalhado, pois eles irão refinar o processo de moldagem e possuir a qualidade das peças sendo produzidas.
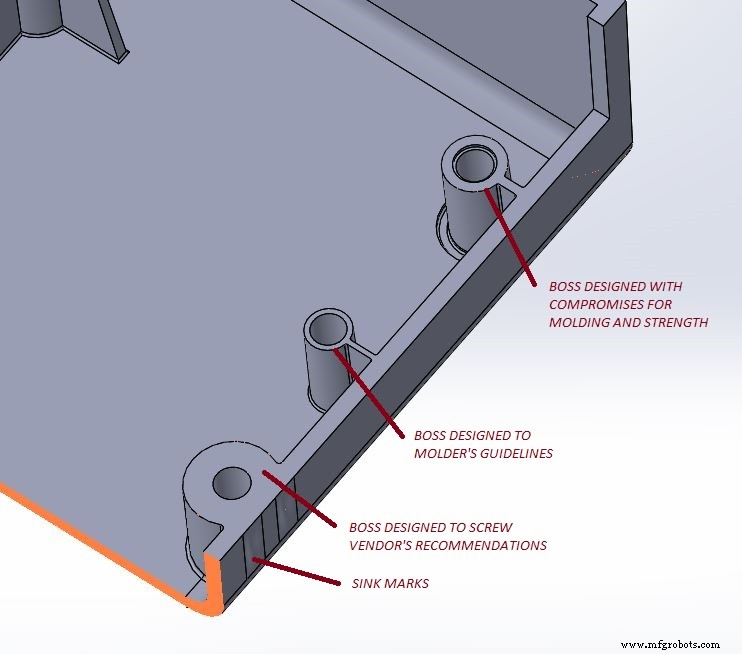
Então, onde começa o problema e quais são os problemas? Uma saliência superdimensionada ou uma saliência colocada incorretamente pode causar marcas de afundamento nas paredes opostas da peça moldada por injeção, que podem ser as principais superfícies cosméticas. O afundamento em peças moldadas por injeção é onde existem seções grossas de plástico devido às interseções de recursos internos com uma parede externa. Se a seção espessa tiver muito mais volume do que a espessura da parede nominal adjacente da peça moldada por injeção, então o interior do material plástico irá resfriar muito mais lentamente e se contrair no plástico já frio e rígido ao seu redor, criando covinhas nas superfícies de plástico. o exterior e o estresse na parte.
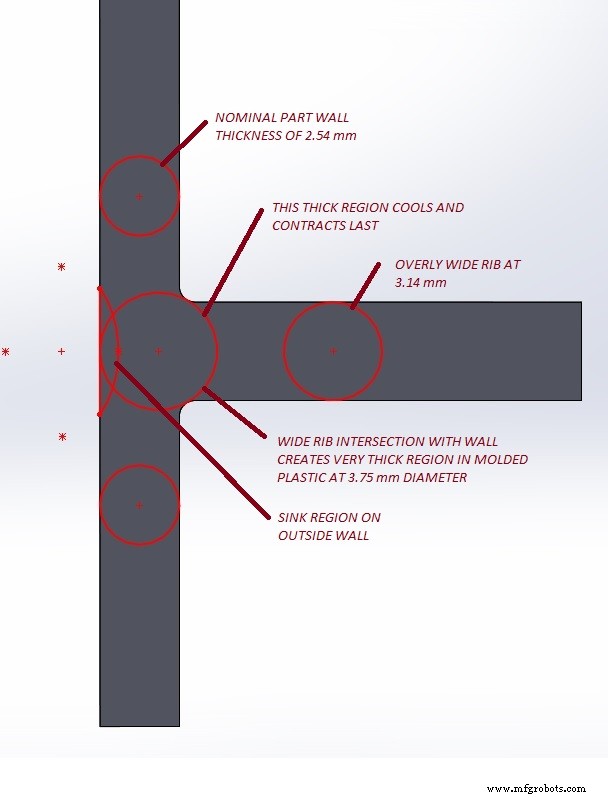
Isso também pode causar empenamento em uma peça moldada por injeção e, ainda pior, os recursos de saliência na peça podem causar outros problemas de fluxo de molde que afetam a capacidade da peça moldada por injeção de preencher sem outras falhas.
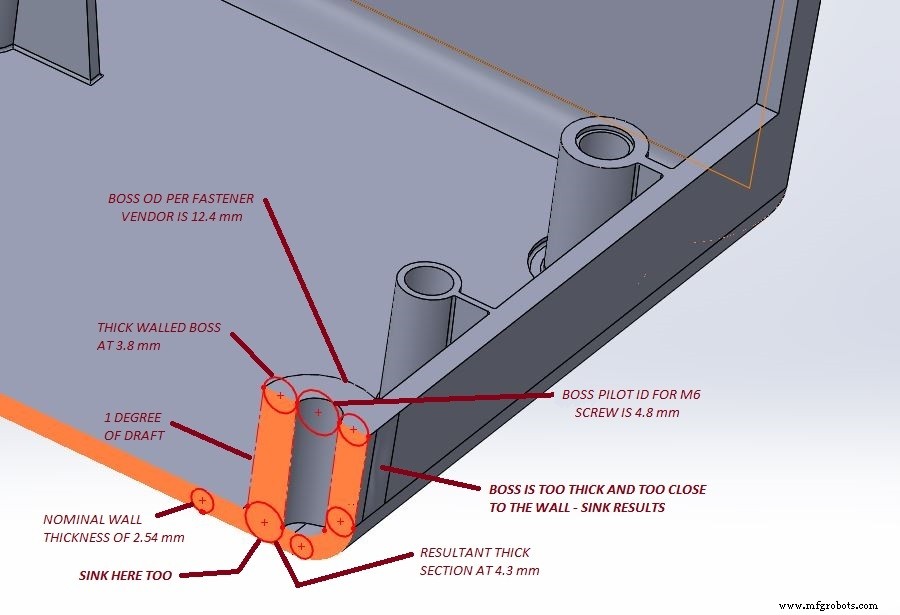
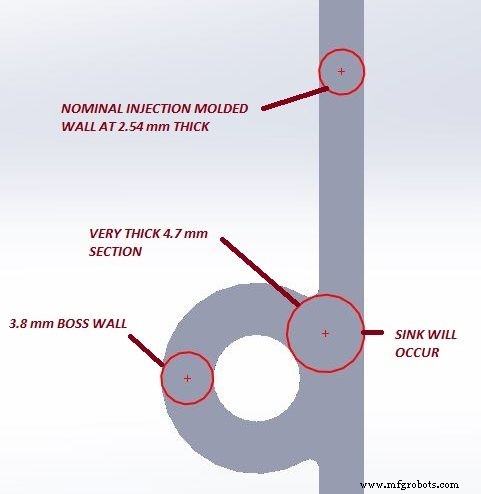
Por outro lado, uma saliência subdimensionada pode ser fácil de moldar, mas pode não reter o fixador instalado, fazendo com que as peças e componentes se soltem e comprometam o produto, ou pior, a saliência pode estourar levando a rejeições de peças na fabricação e até mesmo totalmente falha do produto em campo.
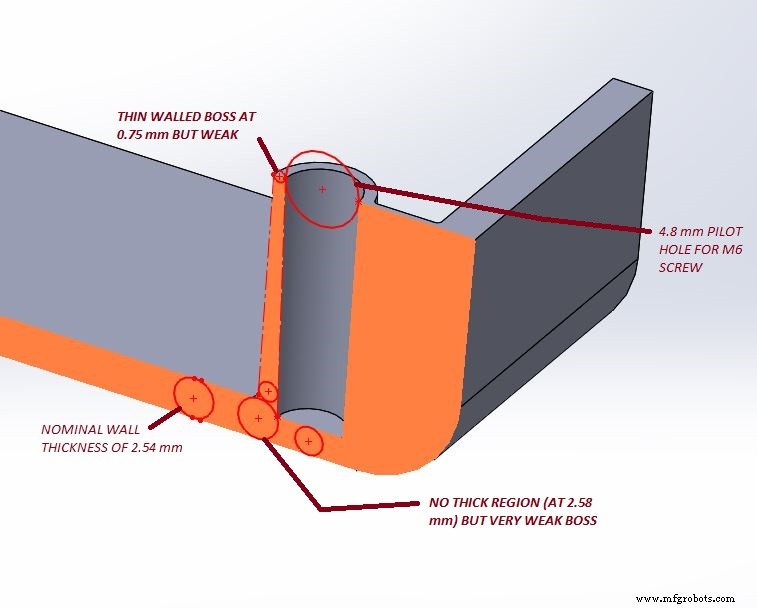
Para acertar, é uma espécie de ato de equilíbrio dar à saliência espessura de parede suficiente para que, à medida que um fixador corta ou forma seu caminho até o orifício piloto da saliência, haja material plástico suficiente para lidar com essas forças de instalação e o suficiente para garantir que as roscas do fixador podem contar com a saliência para resistência de retenção. Muito pouco material e o plástico, se não quebrar na instalação, podem escoar a frio e permitir que o fixador, e por sua vez a montagem, se solte, pois o material restante não é adequado para dissipar as tensões da junta. Essas cargas podem variar dependendo do que se espera do produto, das pressões que ele vê e até mesmo da faixa de temperatura em que é usado.
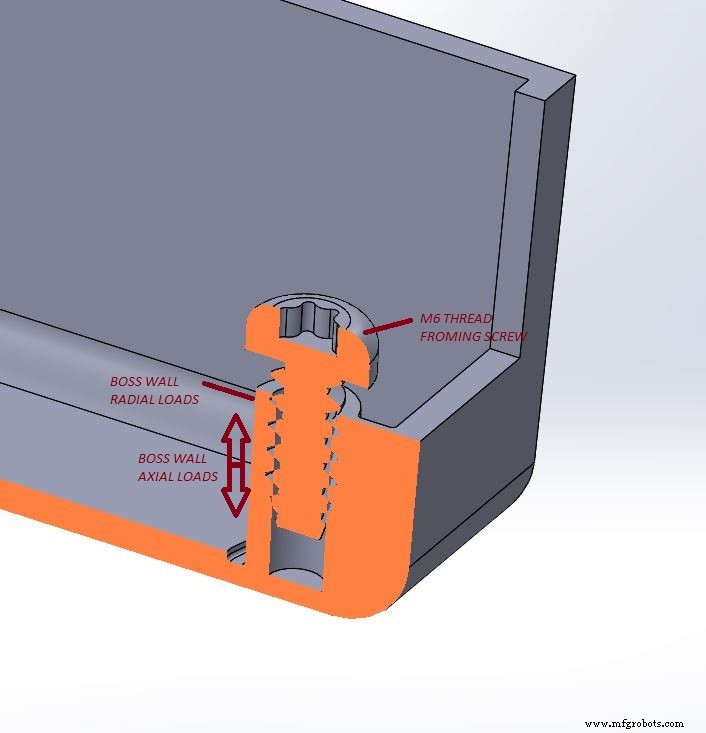
Para tornar o desafio da moldagem ainda maior para a peça moldada por injeção, a saliência precisará ter calado para permitir que a peça seja ejetada da ferramenta de molde de aço, pelo menos em suas paredes de diâmetro externo. Isso significa que a seção transversal das bosswalls ficará maior na base. É geralmente uma boa prática ter um ligeiro filé também nesta junção. No entanto, assim como as nervuras, já falamos sobre elas, uma saliência pode ser considerada uma nervura circular, e sua seção de parede deve estar perto de 50 a 60 por cento da parede nominal na qual ela está assentando, para evitar que haja uma depressão. Torna-se difícil manter essa restrição e ter uma seção de parede espessa o suficiente na parte superior da saliência de modo que o fixador que engata ali não sopre apenas para fora do lado da parede da saliência, pelo menos para qualquer coisa que não seja saliências muito curtas. Lembre-se de saliências de plástico muito curtas não permitem o engate da rosca pelo fixador. Para parafusos em plástico, geralmente de 2 a 2,5 vezes, o tamanho nominal do parafuso é recomendado para o engate da rosca. O número de roscas envolvidas em uma porca de plástico ajuda com a resistência mais do que o convencional para um fixador de metal em uma porca de aço.
Para inserir o boss mais forte possível, mas não ter problemas de moldagem por injeção e falhas estéticas como coletor, um bom design mantém a intenção das recomendações em mente, mas engana um pouco em ambos os tamanhos e aplica alguns truques.
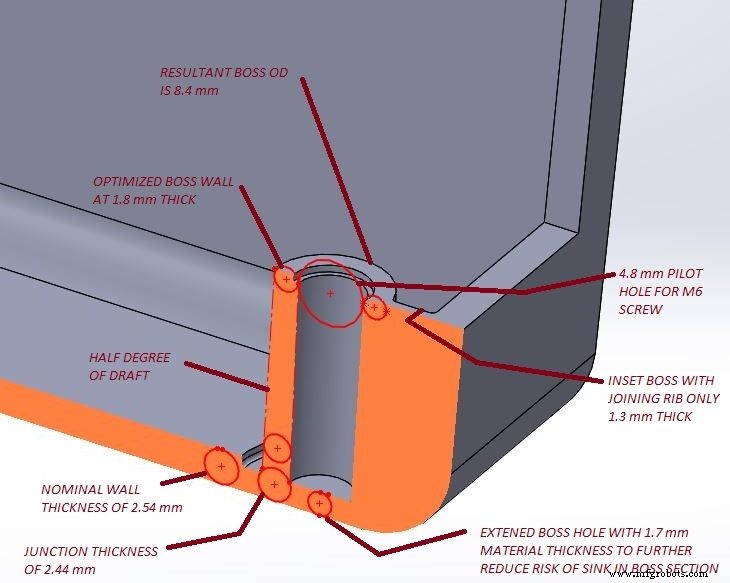
Reduzindo o diâmetro externo da saliência da recomendação de paredes excessivamente grossas do fabricante do parafuso para uma espessura razoavelmente moldável que ainda fornece resistência semelhante às paredes de plástico circundantes, usando um esboço mínimo em superfícies de saliência interiores lisas e mantendo a saliência longe das paredes externas permite uma boa combinação de resistência e baixo risco de problemas de moldagem por injeção. As paredes externas são mantidas em uma espessura quase constante e as nervuras de união são mantidas em 50 a 67 por cento da espessura nominal da parede. O orifício piloto para o parafuso é dimensionado próximo, mas não no menor diâmetro recomendado, a profundidade de engate da rosca aumentada garante uma junta forte na saliência moldada por injeção de plástico, distribuindo as cargas para menor tensão.
Com o furo da saliência 30 por cento mais profundo na base nominal da saliência e uma calha circundante externa na base da parede da saliência, as seções de material de interseção são minimizadas, o que permite paredes da saliência mais espessas do que seria possível sem esses truques.
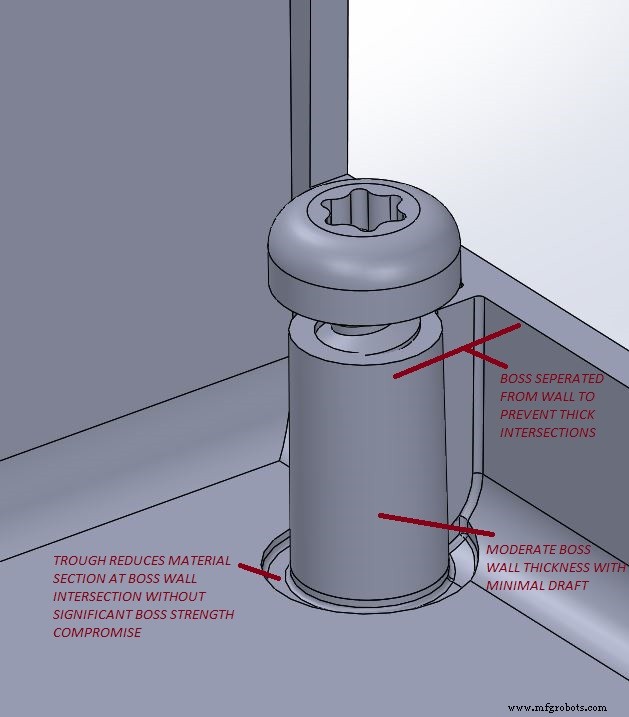
Lembre-se de que nas primeiras peças de injeção produzidas fora da ferramenta de moldagem por injeção de metal, os ressaltos e fixadores especificados podem ser avaliados e confirmados quanto ao desempenho. Existem muitos tipos de parafusos disponíveis para aplicações em plástico com designs de rosca variados.
Além disso, uma saliência de parafuso moderadamente projetada em uma peça moldada por injeção que foi projetada com considerações para a montagem do produto e os requisitos de moldagem da peça terá uma pequena passagem em qualquer direção para maior discagem. Uma abordagem em que um pouco mais de plástico é adicionado ao o projeto da peça moldada por injeção para engrossar ainda mais uma saliência exigirá apenas a remoção de um pouco mais de metal da ferramenta. Isso é chamado de ser metal ou aço seguro, e é muito mais fácil e barato modificar uma ferramenta de molde de injeção de metal removendo o material do que adicionando-o de volta.
Alterar o tamanho do furo da saliência de uma forma ou de outra também pode ser bastante fácil, pois isso pode exigir apenas a substituição de um pino de aço na ferramenta de moldagem por injeção. E isso pode ajustar o engate do fixador, valores de torque de montagem e tensões na peça de plástico. Isso geralmente não é um problema, mas são opções se necessário, por exemplo, se a liga de plástico for alterada durante as fotos iniciais da peça.
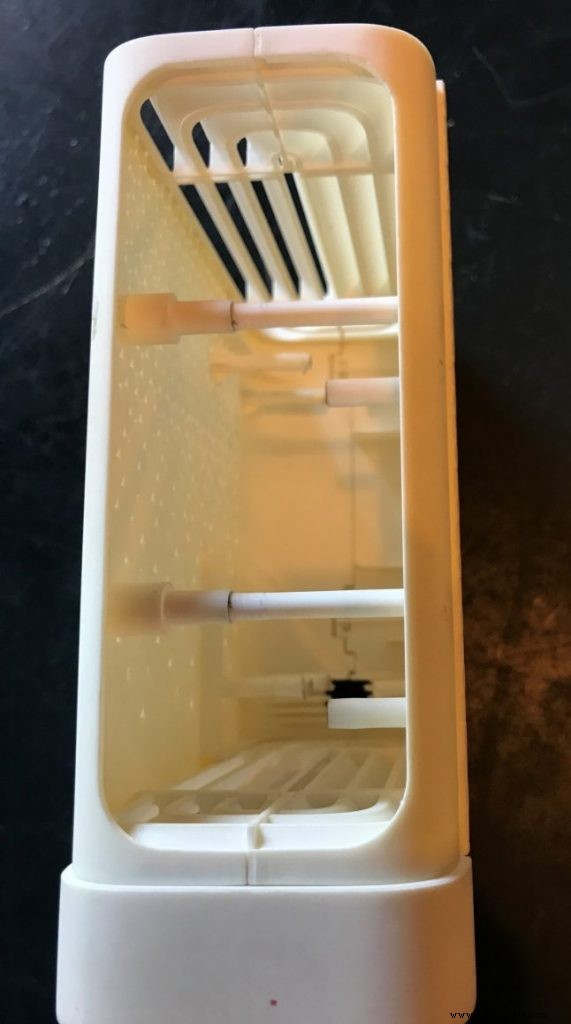
É claro que cada projeto individual terá seus próprios requisitos e prioridades. Algumas peças que são apenas funcionais e não são vistas na parte externa do produto podem aceitar falhas de moldagem se não causarem tensões que comprometem a resistência geral. É aqui que a equipe de design e o moldador precisam trabalhar juntos para criar as melhores peças possíveis.
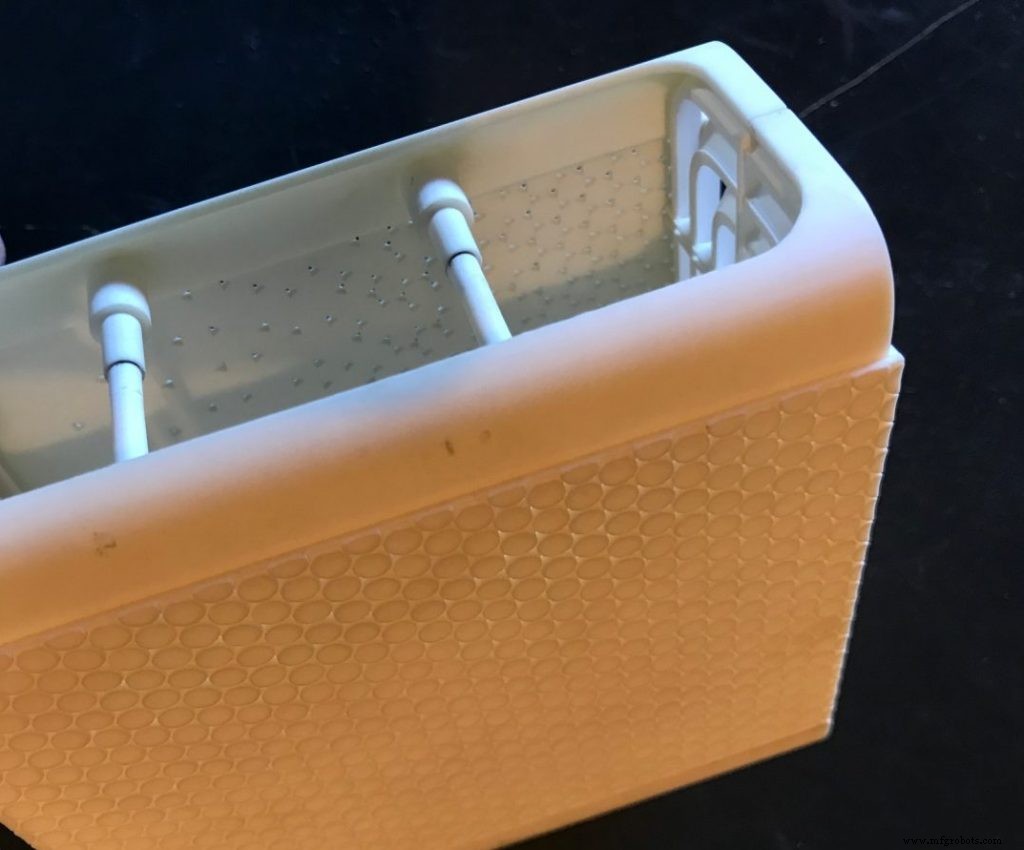
Além disso, se o design da peça moldada por injeção e seus chefes andaram na linha entre os extremos, há muito que o parceiro de moldagem pode ajustar via processo, tempo de ciclo e resfriamento para reduzir os menores sumidouros de modo que os problemas cosméticos possam ser eliminados para o "como projetado ”peça moldada por injeção.
Portanto, trabalhe em direção a um projeto equilibrado, trabalhando com a equipe de desenvolvimento de orifícios para garantir que os projetos de saliências moldadas por injeção sejam fáceis de moldar e fortes o suficiente para segurar.
Verifique aqui:Parte 1, Parte 2, Parte 4
Processo de manufatura
- Projeto da peça moldada por injeção - Parte 6:Gerenciamento de equipes e fabricantes contratados
- Projeto de peça moldada por injeção, parte 5:Rascunho
- Projeto da peça moldada por injeção - Parte 4:Warp
- Projeto de peça moldada por injeção - Parte 2:Marcas de dissipação
- 6 Considerações importantes de projeto para impressão 3D em metal
- Como projetar uma peça composta termofixa [Infográfico]
- Diretrizes de design para manufatura – Parte 2
- Diretrizes de design para manufatura – Parte 1
- Qual é o melhor acabamento de superfície SPI para sua peça moldada por injeção?
- Dicas de design para moldagem por injeção