Vs programado. Manutenção não programada em instalações de manufatura
A manutenção programada e a manutenção não programada fazem parte das operações normais de uma instalação industrial. No entanto, ao considerar a manutenção programada versus não programada, há uma diferença clara na forma como cada tipo de procedimento afeta a produtividade, eficiência, vida útil da máquina e qualidade de saída.
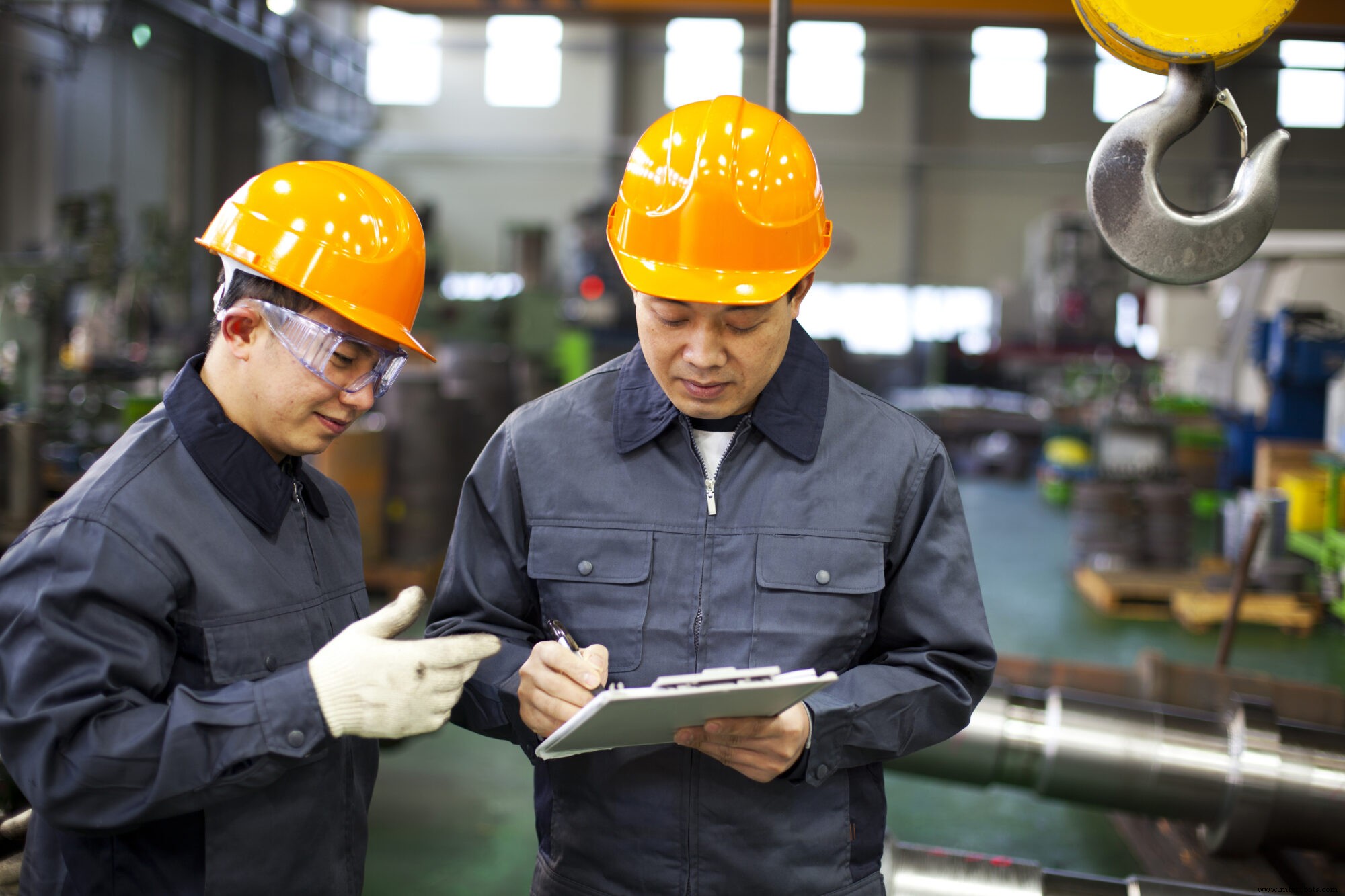
Como uma visão geral, a manutenção programada é planejada para um momento e cenário específicos. A manutenção não programada, por outro lado, é uma abordagem mais reativa que é utilizada quando um componente ou máquina para de funcionar.
Veremos cada tipo com mais detalhes abaixo e explicaremos por que a manutenção programada é uma opção mais prática para quem procura melhorar as operações gerais de suas instalações.
Benefícios da manutenção programada
A manutenção programada - também conhecida como “manutenção preventiva” pelos fabricantes de equipamentos ou profissionais de manutenção - oferece inúmeros benefícios aos equipamentos de produção. No geral, a manutenção programada representa um forte retorno sobre o investimento na forma de tempo, dinheiro e recursos economizados em comparação com a manutenção reativa ou não programada.
A manutenção programada inclui tarefas (dentro e fora das configurações de fábrica) como:
- Mudanças de óleo
- Alterações de filtro
- Lubrificação de equipamentos
- Limpeza
- Calibração
- Inspeção visual de componentes como correias, com substituição conforme necessário
- Otimização de controle
A manutenção programada pode ocorrer em uma programação baseada em tempo ou em uma programação baseada em uso. Na maioria das instalações, é quase certo que ambos serão necessários. As práticas de manutenção programada também podem incluir uma série de iniciativas de manutenção preditiva, como monitoramento de temperatura e vibração. Ao utilizar tecnologias preditivas durante o tempo de inatividade programado para manutenção, as equipes de manutenção identificam outros problemas potenciais bem antes que eles causem problemas de produção. Embora a janela de planejamento seja menor nesses cenários, esse tipo de manutenção oferece muito mais flexibilidade em termos de quando a manutenção ocorrerá, permitindo tempo para planejar uma parada de linha e coletar materiais para o tempo de inatividade mais eficiente possível.
Seguindo essas práticas, as instalações podem ver os seguintes benefícios:
- Menos tempo de inatividade não planejado: O tempo de inatividade não planejado inevitavelmente acontecerá em uma instalação industrial, mas um tempo de inatividade programado para abordagem de manutenção pode garantir que esse tempo de inatividade seja mínimo, planejado e destinado a evitar mais tempo de inatividade. É muito preferível planejar o tempo de inatividade para permitir uma programação de produção mais precisa, métodos alternativos de produção (se necessário) e preparação aprimorada para o pessoal de manutenção.
- Manutenção mais rápida: Desligamentos não planejados são freqüentemente uma confusão. A liderança da fábrica deve agir rapidamente para garantir que as pessoas, equipamentos, tecnologias e procedimentos certos estejam disponíveis para solucionar o problema. Cada segundo desperdiçado na busca por esses componentes é tempo de produção perdido. Com o tempo de inatividade planejado, o pessoal está pronto para começar a trabalhar assim que o equipamento for interrompido e a produção volta aos trilhos assim que a manutenção de rotina for concluída.
- Custos de manutenção mais baixos: A manutenção planejada permite mais controle sobre o gerenciamento de estoque de peças sobressalentes e reduzirá amplamente a necessidade de atendimento emergencial de peças sobressalentes, o que pode elevar exponencialmente o custo de um reparo ou substituição. Além disso, a manutenção planejada pode reduzir ou eliminar a necessidade de horas extras não planejadas para concluir um reparo não planejado. Ele também protegerá seu investimento em equipamento de forma mais eficaz do que a manutenção reativa, permitindo um planejamento de produção mais eficiente - o que também economizará dinheiro ao longo do tempo.
- Melhor desempenho do equipamento: Em um plano de manutenção reativo e não programado, máquinas e componentes funcionam até a falha. Antes dessa falha, muitos desgastes estão acontecendo com todos os componentes da máquina, fazendo com que ela quebre com mais frequência ao longo do tempo. Isso criará um efeito dominó, pois máquina após máquina continua a se desgastar, causando mais tempo de inatividade não planejado e a necessidade de procedimentos de manutenção mais reativos. A manutenção programada garante que o equipamento esteja funcionando com desempenho máximo pelo maior tempo possível e permite que o pessoal de manutenção dê à máquina os intervalos de que ela precisa para inspeção e reparo.
Na maioria dos casos, pelos motivos acima, a manutenção programada é a abordagem de escolha. Existem alguns cenários, no entanto, em que a manutenção não programada não só é aceitável, mas é preferível. Mais sobre isso abaixo.
A manutenção não programada está sempre OK?
Resumindo, sim. Existem cenários em que a manutenção programada pode ser ineficiente ou desnecessária. Algumas perguntas podem determinar se uma abordagem reativa e não programada é adequada para uma operação ou componente específico:
- O reparo é rápido e fácil de executar? Nesse caso, a manutenção preventiva pode ser desnecessária, uma vez que o tempo de inatividade para esses tipos de reparos será mínimo. Um exemplo desse tipo de manutenção pode ser a substituição do filtro.
- O componente ou operação desempenha um papel crítico na qualidade da peça? Se a falha de uma peça do equipamento levar a peças danificadas ou rejeitadas, isso é considerado crítico para suas operações principais. Esses componentes devem estar no topo da sua lista de manutenção preventiva. Se uma peça pode falhar sem afetar a peça acabada, no entanto, pode ser adequada para manutenção reativa.
Manutenção preventiva com ATS
Como especialistas na área de manutenção industrial há mais de três décadas, os profissionais de manutenção da ATS entendem que a manutenção preventiva é muitas vezes vista como um “bom ter” que pode ser adiado até que haja tempo para planejá-la e implementá-la. É por isso que ajudamos centenas de fabricantes em todo o mundo a transformar suas abordagens de manutenção reativa em operações de manutenção preventiva e eficientes.
Deixe-nos ajudá-lo a criar um programa de manutenção programada que permitirá que você obtenha os benefícios listados acima. Para obter mais informações sobre todos os nossos serviços de manutenção de fábrica, visite nosso site ou entre em contato conosco hoje mesmo. Nossos representantes estão prontos para discutir suas necessidades e objetivos de manutenção.
Manutenção e reparo de equipamentos
- Navegando na modernização da manutenção e gestão de instalações
- Manufatura enxuta:O que é e o que a manutenção tem a ver com isso?
- EPA homenageia instalações de manutenção de veículos USPS em NY
- Krieger para chefiar a fabricação e manutenção em Winnebago
- Compreendendo as métricas de manutenção:Porcentagem crítica de manutenção programada
- A Importância da Manutenção de Equipamentos na Fabricação
- Usando software de manutenção preventiva para fabricação
- Como manter seu equipamento de fabricação industrial
- Os diferentes tipos de manutenção na fabricação
- Impacto das manutenções preditivas na fabricação