Um guia para manutenção preventiva na fabricação
Corrigindo problemas antes que eles se tornem problemas
Para fabricantes em todo o mundo, a manutenção preventiva tem sido uma ferramenta usada para prolongar a vida útil do equipamento e estender o retorno do investimento (ROI) do Capex. Sua importância se uniu em linhas formais e informais com programas internos baseados em observação e experiência, manuais fornecidos por OEMs e softwares sofisticados que ajudam as empresas a manter um cronograma de manutenção rigoroso.
Mas enquanto o conceito de manutenção preventiva existe há décadas, muitos do setor industrial consideram o quanto ele pode ser mais eficaz. Enquanto poucos gerentes permitem que máquinas e peças funcionem até a falha e reduzam os ciclos de vida do equipamento, outros se perguntam se a manutenção preventiva foi otimizada ao máximo. E em caso afirmativo, as tendências crescentes, como programas preditivos e prescritivos, possibilitadas pela IoT, são o próximo passo lógico?
O que é Manutenção Preventiva?
A manutenção preventiva, também conhecida como Manutenção Preventiva, ou simplesmente PM, é um programa formalizado usado na fabricação para otimizar e prolongar o ciclo de vida dos equipamentos de produção. Ao programar sistematicamente a manutenção dos equipamentos, os fabricantes procuram identificar e corrigir problemas antes que se tornem falhas.
A manutenção preventiva pode ser baseada em calendário, onde as peças são substituídas antes de quebrar ou desgastar. Ele também pode ser baseado em uso, projetado para levar em consideração o tempo de execução em ambientes como fábricas de operação contínua 24 horas por dia, 7 dias por semana. Ou pode ser baseado em condições, onde a condição visual ou medida de peças e equipamentos é usada para ambientes de fabricação que funcionam com diferentes graus de desgaste, dependendo do produto que está sendo executado.
IoT pode ajudar a desbloquear um programa de manutenção mais eficaz usando dados de máquina em tempo real para impulsionar a manutenção.
A importância da manutenção preventiva
A manutenção preventiva foi a primeira tentativa da indústria de sistematizar e melhorar o desempenho dos equipamentos. Historicamente, as empresas operavam em "manutenção reativa", onde as peças podiam falhar antes de serem reparadas. O objetivo era capturar as condições de funcionamento mais longas possíveis antes de perder tempo valioso para reparo.
No entanto, à medida que a medição e a amostragem estatística se tornaram mais disponíveis, os profissionais de manutenção descobriram que a manutenção preventiva era uma solução melhor em quase todas as circunstâncias. A importância da manutenção preventiva ficou evidente em sua abordagem planejada e programada.
As empresas poderiam projetar programas de manutenção preventiva que levassem em conta o tempo de execução, uso, condições e outros fatores. A partir dessa abordagem, eles poderiam desenvolver treinamento especializado, orçamentos mais precisos e melhores planos de Capex.
Benefícios e vantagens
Existem inúmeros benefícios para um programa de manutenção preventiva bem projetado, incluindo:
Economia de custos
Ao substituir as peças antes que elas falhem, há menos chance de as peças ao redor serem excessivamente desgastadas ou danificadas. Essa prática resulta em economia de custos em geral.
Melhorias de segurança
Muitas vezes, as peças podem se desgastar até que a falha possa se desintegrar e causar danos a outras peças em um efeito dominó. Ao substituir as peças antes desse ponto, o equipamento fica mais seguro para operadores e técnicos.
Qualidade melhorada
Os equipamentos de produção hoje dependem de um alto grau de precisão para produzir mercadorias de grande volume em pouco tempo ou peças com especificações rigorosas para aplicações feitas sob encomenda. Ao substituir uma peça antes que ela se desgaste, as tolerâncias da máquina são mantidas, resultando em produtos de primeira qualidade mais elevados.
Tempo de inatividade reduzido
As peças propensas a falhas geralmente resultam em tempo de inatividade mais prolongado, pois podem ser fundidas ou incorporadas em outras partes da máquina. Essa falha aumenta o tempo necessário para limpar detritos e soltar peças de eixos congelados e outros mecanismos. Substituir a peça em um programa de MP significa reparo mais rápido durante o tempo de inatividade planejado e reduz o tempo de inatividade não planejado.
Confiabilidade melhorada
Como a manutenção preventiva é planejada e programada, a confiabilidade dos cronogramas de produção é bastante aprimorada. Os gestores entendem que a manutenção é sistêmica e que não precisam mais “cruzar os dedos” e torcer pelo melhor.
Aumento da vida útil do equipamento
Ao decretar um plano formal de manutenção preventiva, a vida útil de uma máquina pode ser muito estendida por anos ou mesmo décadas. Essa vida útil mais longa reduz os valiosos investimentos necessários para os programas de Capex e permite que as empresas planejem o Capex estrategicamente ou por necessidade.
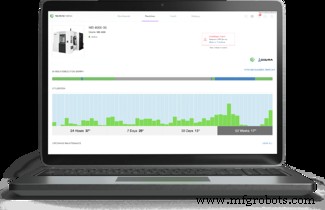
Ao analisar a integridade e o desempenho dos equipamentos, as equipes de manutenção podem adotar uma abordagem mais proativa e usar insights baseados em dados para tomar decisões mais eficazes.
Desvantagens da Manutenção Preventiva
Os programas de manutenção preventiva são baseados em suposições e probabilidades. Claro, estes podem ser afiados em muitos casos para corresponder à vida útil de uma peça. Mas como um sistema baseado em probabilidades, as estratégias básicas de manutenção preventiva carecem de dados precisos para se tornarem mais eficazes.
Devido a isso, existem muitas desvantagens para as formas mais populares de manutenção preventiva, incluindo:
Manutenção Excessiva
Como os programas de PM dependem de suposições e probabilidades, a manutenção excessiva é sempre um problema. Isso pode significar tempo e trabalho excessivos gastos para verificar e verificar novamente problemas que podem não estar lá. Ou pode resultar na substituição de peças com base em tabelas e gráficos de intervalos de manutenção fornecidos pelo OEM que não levam em conta aplicações particularmente pesadas ou leves que afetam o desgaste das peças. Em ambos os casos, o excesso de serviços pode aumentar o custo.
Falha inesperada
Mesmo os programas de manutenção preventiva mais bem projetados não podem explicar falhas não planejadas da máquina. Como os programas de PM são orientados por suposições e não por dados, falhas aleatórias e desgaste inesperado podem não ser detectáveis entre os intervalos de PM.
Treinamento extensivo contínuo
Embora um programa sólido de PM ofereça a oportunidade de treinamento especializado, isso pode se tornar caro com o tempo. À medida que novos equipamentos entram em operação, o treinamento deve ser atualizado para levar em conta novas funcionalidades. Os sistemas de PM devem ser atualizados juntamente com isso, e o processo se torna menos econômico.
Tipos de manutenção preventiva
Se você quiser se aprofundar nos diferentes tipos de manutenção que os fabricantes podem usar, leia o artigo completo. Aqui está um resumo das diferentes estratégias de manutenção preventiva:
- Manutenção baseada em tempo:estabelecer um calendário com intervalos para a atividade de manutenção.
- Manutenção baseada no uso:você substitui as peças quando a máquina é usada uma certa quantidade antes de quebrar.
- Manutenção baseada em condições:você substitui as peças quando elas parecem estar muito desgastadas para continuar funcionando adequadamente. Saiba mais sobre o monitoramento da condição da máquina.
- Manutenção preditiva:você utiliza dados históricos para fazer previsões sobre quando uma peça irá quebrar e substituir as peças com base nessas previsões, antes de elas quebrarem. Isso geralmente, mas nem sempre, utiliza inteligência artificial e aprendizado de máquina.
- Manutenção Prescritiva:Métodos avançados de análise de dados são usados para fazer mais do que prever pontos de falha, mas fornecem resultados hipotéticos para escolher a melhor ação que pode ser tomada antes da falha, riscos de segurança e problemas de qualidade surgirem, bem como o momento da implementação.
Usinagem BC:um exemplo de classe mundial de manutenção preventiva
Para Bob e seus funcionários da BC Machining, ferramentas quebradas e peças de sucata eram apenas um fato da vida. Eles estavam tão arraigados no negócio que Bob operou as máquinas com 200% da capacidade, simplesmente aceitando o tempo e os materiais perdidos devido à falha da ferramenta que se tornou a norma e não uma anomalia.
Nas palavras de Bob, “Quando você quebra ferramentas e faz uma peça de sucata, você está apenas jogando dinheiro fora”.
Para finalmente resolver esse problema, Bob contou com a ajuda da MachineMetrics e nosso novo produto inovador que oferece MachineMetrics Predictive, uma solução que permite diagnosticar, prever e prevenir automaticamente essas falhas de máquinas-ferramenta em suas máquinas Star CNC que levam a ferramentas quebradas, peças de sucata e tempo de inatividade dispendioso.
Após uma implantação rápida e bem-sucedida, em apenas algumas semanas os resultados falaram por si:"Desde que usamos a tecnologia de quebra de ferramenta preditiva da MachineMetrics, quase todo o nosso desperdício foi eliminado. Calculamos a economia em nossas máquinas de torneamento Swiss para ser cerca de US $ 72 mil por ano... tem sido monumental para dizer o mínimo.”
Nesta entrevista de estudo de caso, a equipe da BC Machining compartilha sua experiência usando o MachineMetrics Predictive e o impacto dramático que a tecnologia teve em seu chão de fábrica e seus resultados financeiros.
Leia o Estudo de Caso Completo.
Tecnologia industrial
- Guia para KPIs de Fabricação
- Gargalos na Manufatura - Um Guia Definitivo
- Guia para Fabricação Rápida
- Manutenção preventiva:uma visão geral
- A manutenção preventiva ou a manutenção preditiva são melhores?
- Um guia para criar um programa de manutenção de equipamentos
- Usando software de manutenção preventiva para fabricação
- O que é Manutenção Preventiva?
- Um guia simples para benchmark de manutenção
- Seu guia para gerenciamento de manutenção