4 Elementos-chave para o sucesso do programa de manutenção
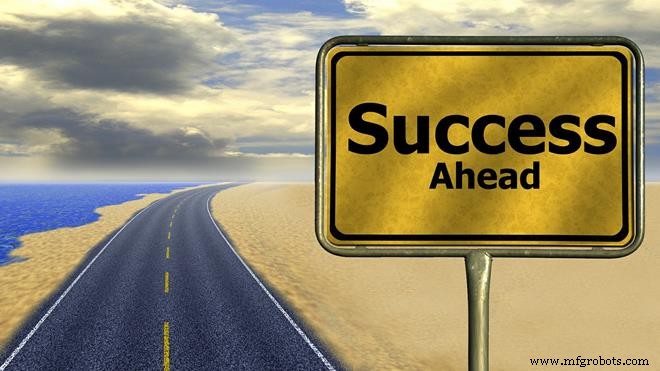
O mesmo relatório do Aberdeen Group conclui que os melhores fabricantes (identificados a partir das pontuações de desempenho de 20 por cento principais) têm 90 por cento de eficácia geral do equipamento (OEE) e uma redução de custo de manutenção de 11 por cento ano após ano, o que dá às empresas uma meta de desempenho de manutenção . Como as empresas alcançam o sucesso?
Este artigo cobre quatro elementos básicos do sucesso do programa de gerenciamento de manutenção:simplificar o processo de gerenciamento de ordens de serviço, capacitar com tecnologia, converter dados históricos e em tempo real em inteligência de ativos e manutenção e mudar de um modelo de manutenção reativo para proativo. Ao abraçar o cenário de manutenção em constante mudança e focar nesses quatro elementos principais, as empresas podem reduzir o tempo de inatividade, melhorar a produtividade e diminuir os custos de manutenção.
Priorizando
Os departamentos de manutenção enfrentam diversos desafios em busca da excelência. A primeira etapa na construção de um programa de manutenção bem-sucedido é identificar e priorizar as principais áreas a serem tratadas. Muitos dos problemas de manutenção mostrados na Figura 1 são comuns em todos os setores e empresas.
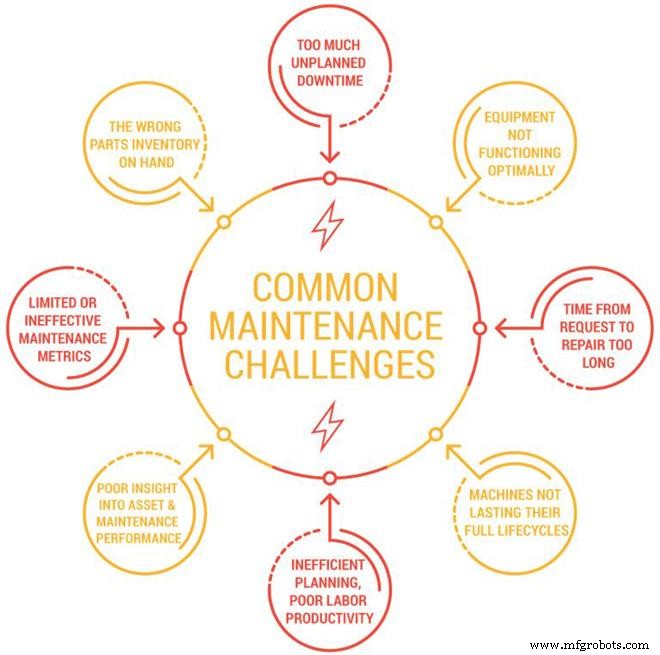
Figura 1. Desafios de manutenção comuns
Esses desafios afetam significativamente o desempenho da manutenção, bem como os resultados gerais dos negócios. Somente na indústria de manufatura, mais de US $ 50 bilhões são perdidos anualmente devido ao tempo de inatividade não planejado.
As prioridades de uma empresa definem seus objetivos de programa de manutenção e abordagem subsequente. A Figura 2 reflete os objetivos típicos do programa de manutenção.
Figura 2. Metas de manutenção comuns
Existem muitos componentes para o sucesso do programa de manutenção. No entanto, quatro elementos-chave que constroem uma base sólida para o programa de manutenção são mostrados na Figura 3.
Figura 3. Quatro blocos de construção do sucesso do programa de manutenção
As empresas têm diferentes graus de complexidade de manutenção a superar e estão em vários pontos da curva de desenvolvimento do programa de manutenção. Algumas organizações estão operando com uma mentalidade principalmente reativa e não têm programas eficazes de manutenção preventiva (PM) em vigor.
Outros já iniciaram programas de PM e estão percebendo os impactos positivos da transição da manutenção reativa para a pró-ativa. A lacuna entre essas empresas em relação à manutenção proativa pode ser grande, mas ambas ainda têm oportunidades de melhorar seu desempenho de manutenção. Mesmo pequenos ganhos incrementais relacionados a esses elementos-chave podem ter um grande impacto nos negócios.
Gerenciamento de Ordem de Serviço
No centro da maioria dos programas de manutenção está um sistema de ordem de serviço. O gerenciamento de ordens de serviço é como uma empresa lida com as atividades de manutenção, desde a solicitação até a execução, conclusão e manutenção de registros.
Muitos fatores influenciam a metodologia que uma empresa usa para gerenciar ordens de serviço, como tamanho da operação, número de técnicos, etc. Existem três abordagens principais:sistemas baseados em papel, planilhas e um software de gerenciamento de manutenção automatizado (CMMS) ou gerenciamento de ativos corporativos (EAM) sistema.
Usar uma abordagem baseada em papel pode ser adequado para pequenas operações, mas torna difícil pesquisar o histórico de equipamentos e manutenção. Por exemplo, pesquisar o histórico de uma bomba pode significar um técnico sentado na oficina folheando um grande fichário. O gerenciamento de ordens de serviço com base em papel aumenta a ineficiência da mão de obra e não se alinha aos valores de sustentabilidade ou iniciativas verdes de muitas empresas.
As planilhas são outra metodologia comum. Isso pode ser difícil de manter para operações de médio a grande porte com muitos ativos. Eles também tendem a tornar a acessibilidade em tempo real um desafio. Por exemplo, um técnico em campo não pode pesquisar e recuperar a ordem de serviço ou o histórico do equipamento com facilidade. O controle de revisão de planilhas de manutenção também pode ser um desafio, dependendo de como o arquivo pertence, é compartilhado e atualizado.
Um sistema CMMS ou EAM é outra maneira pela qual muitas empresas gerenciam ordens de serviço. Um CMMS é a solução de gerenciamento de ordem de trabalho mais robusta e fornece acesso sob demanda ao histórico de ativos e manutenção. Uma lista de peças e várias documentações também podem ser vinculadas ou associadas a ativos e / ou ordens de serviço, o que pode ser útil. A desvantagem de um CMMS é que, para os trabalhadores que não são experientes em tecnologia, a curva de aprendizado pode ser íngreme e eles geralmente resistem à mudança para um sistema automatizado.
O processo de gerenciamento de ordens de serviço é crítico porque todas as atividades de manutenção requerem uma ordem de serviço. Qualquer que seja a metodologia empregada, é importante refletir sobre o processo geral da ordem de serviço e como os principais elementos desse processo serão tratados. Boas estratégias de gerenciamento de ordens de trabalho otimizam o processo de manutenção, ao mesmo tempo que fornecem o máximo valor organizacional.
Os elementos básicos do gerenciamento de ordens de serviço são mostrados na Figura 4. A etapa inicial é uma solicitação de manutenção, após a qual as ordens de serviço são atribuídas e o trabalho é agendado. O trabalho de manutenção é então concluído, documentado e encerrado.

Figura 4. Processo básico de gerenciamento de ordens de serviço
Este processo básico de ordem de serviço não deve parecer intimidante. É simples e direto, mas um tanto enganoso. Na realidade, existem muitas considerações e complexidades para cada uma das etapas do processo de ordem de serviço. Por exemplo, quando uma solicitação de manutenção é feita, deve-se determinar se precisa de atenção urgente.
Se estiver fora do expediente, será uma solicitação que justifique a chamada de técnicos para fazer horas extras? As informações na solicitação de ordem de serviço estão completas? Muitas ordens de serviço não têm informações adequadas na solicitação inicial e exigem conversas de acompanhamento com o solicitante. Talvez uma ordem de serviço seja iniciada como parte de um programa de manutenção preventiva? Como um PM é tratado de forma diferente?
Examinando a etapa de atribuição da ordem de serviço, os supervisores geralmente consideram quem está disponível e quais habilidades são necessárias. Eles também consideram quanto tempo acham que as tarefas de manutenção levarão e onde isso se encaixa em outras prioridades antes de agendar o trabalho. Da mesma forma, pode haver considerações operacionais em potencial que afetam a programação.
Por exemplo, a atividade de manutenção pode exigir uma interrupção ou o equipamento de backup pode precisar ser colocado em serviço antes do trabalho. Algumas tarefas de manutenção requerem ferramentas ou equipamentos especiais, complicando a programação do trabalho. Por exemplo, se uma plataforma elevatória for necessária, pode ser necessário agendá-la ou alugá-la, dependendo das práticas de negócios da empresa.
Como um precursor para iniciar a manutenção, os técnicos geralmente desejam revisar o equipamento e o histórico de ordens de serviço. Esses históricos podem ajudar a indicar o problema de manutenção antecipadamente, para que um técnico saiba por onde começar e se deve substituir ou reparar. Depois que um técnico começa a atividade de reparo e manutenção, a capacidade de verificar rapidamente a disponibilidade de peças pode ser valiosa. Quando o trabalho de manutenção é concluído, o tempo de conclusão é registrado.
A etapa final de gerenciamento da ordem de serviço é documentar todas as atualizações (por exemplo, desenhos marcados em vermelho, fotos de equipamentos ou reparos, etc.) e, em seguida, fechar a ordem de serviço.
Numerosas considerações entram no processo de gerenciamento de ordens de serviço de manutenção, o que pode torná-lo muito mais complexo do que a representação básica na Figura 4. Por que é importante focar no processo de gerenciamento de ordens de serviço? Os benefícios de um processo de gerenciamento de ordem de serviço forte e abrangente são mostrados na Figura 5.
Figura 5. Benefícios do bom gerenciamento de ordens de serviço
Capacitando com tecnologia
Existem muitos termos de tecnologia relacionados à manutenção, como CMMS / EAM, internet das coisas (IoT), mobilidade e analítica. Essas tecnologias incríveis podem ajudar as empresas a cumprir e superar suas metas de desempenho de manutenção. A aplicação de tecnologias digitais para funções como manutenção já está melhorando o desempenho da planta, minimizando o tempo de inatividade e reduzindo os custos operacionais.
Com tantas opções de tecnologia, pode ser difícil saber o que aplicar ou quando aplicar a solução para apoiar o sucesso do programa de manutenção. Não existe uma resposta certa sobre quais tecnologias são as melhores. Para uma planta, pode não fazer sentido aplicar a inteligência artificial, mas para outra pode ser a tecnologia que as impulsiona.
Algumas dessas tecnologias representam mudanças de equipamento e filosofia. Por exemplo, a robótica que substitui as funções humanas foi adotada em muitas fábricas discretas. Tecnologias como robótica, inteligência artificial e transformação digital podem ser aplicadas diretamente às operações da planta, mas ainda têm impactos perceptíveis na manutenção.
Quando as forças de trabalho são capacitadas com essas tecnologias, isso pode aumentar a eficiência do trabalho, reduzir o tempo de inatividade e melhorar a inteligência de ativos. A tecnologia CMMS existe há anos e tem uma presença estabelecida. Pode haver uma hesitação em adotar ferramentas mais novas até que elas sejam amplamente comprovadas com um tempo de execução significativo. Apesar desse cuidado, as tecnologias ganharam uma tração considerável.
Onde está o valor em adotar tecnologias modernas? Isso depende da tecnologia específica, mas abaixo estão alguns exemplos de como algumas dessas tecnologias agregam valor.
Os sistemas CMMS ou EAM são freqüentemente considerados a base de fortes programas de gerenciamento de ordens de serviço. Eles tendem a fornecer um alto retorno sobre o investimento quando implementados de maneira adequada. Um dos benefícios essenciais é que, ao longo do tempo, eles criam um histórico de gerenciamento de ativos e manutenção.
O histórico em um CMMS pode ser usado para detectar tendências, estabelecer métricas, programar atividades de manutenção preventiva e acelerar o tempo de reparo. Um CMMS também pode oferecer muitos outros benefícios, como estender a vida útil do equipamento, reduzir o tempo de inatividade e melhorar o planejamento e a produtividade do trabalho.
A adoção da mobilidade pode fazer uma grande diferença na eficiência do trabalho, no tempo de reparo e em outras métricas importantes de manutenção. Considere um técnico que pode acessar informações importantes em um dispositivo móvel sem ter que caminhar de volta para a loja. Quantas etapas e quanto tempo pode ser economizado?
Além do valor de fornecer dados a um técnico onde ele estiver, os recursos móveis podem permitir que o técnico registre informações com mais precisão. Por exemplo, se um técnico pode registrar a conclusão da ordem de serviço de um dispositivo móvel, isso resultará em um tempo de conclusão mais preciso que pode ser usado para um planejamento mais preciso.
A robótica é amplamente difundida em muitas operações de manufatura discretas e aplicada em algumas operações contínuas. Eles podem ajudar a apoiar a consistência operacional e ser usados para melhorar a segurança ao lidar com atividades de alto risco. Um desafio para os departamentos de manutenção é que a robótica pode mudar os conjuntos de habilidades de que os técnicos de manutenção precisam. No passado, os técnicos eram especializados, com experiência em disciplinas dedicadas como mecânica ou instrumentos e elétrica.
A manutenção robótica é uma mistura de habilidades, exigindo que os técnicos tenham conhecimento de manutenção multidisciplinar e tenham uma abordagem mais abrangente para reparos. A robótica tende a economizar custos operacionais, proporcionando consistência, melhorando a velocidade e eficiência, etc. No entanto, os requisitos de manutenção na robótica podem ser altos, potencialmente aumentando os custos de manutenção anual.
Atualmente, um dos termos de tecnologia mais populares é internet das coisas (IoT). Este é um termo amplo caracterizado por dispositivos e sistemas conectados com o objetivo de fornecer inteligência em tempo real. Um exemplo de IoT é um sistema de monitoramento de vibração conectado a um sistema de alarme que pode iniciar uma ordem de serviço de manutenção preditiva.
Se os dados históricos indicam que o equipamento irá falhar quando a vibração atingir um certo nível, então, ao alarmar e iniciar uma ordem de serviço antes desse evento, o tempo de inatividade não planejado pode ser evitado, economizando dinheiro significativo. Este é um exemplo único de alto nível, mas há muitos outros dos amplos recursos da IoT e como ela pode agregar valor aos programas de manutenção.
A adoção de tecnologias modernas capacita os funcionários com melhor inteligência em tempo real e histórico de ativos e manutenção. Os benefícios disso são melhor eficiência de trabalho, melhor tomada de decisão e desempenho geral de manutenção aprimorado.
Obtendo Inteligência de Ativos e Manutenção
Bons dados são vitais para as empresas otimizarem o desempenho e tomarem decisões de negócios sólidas. Um dos primeiros desafios que as organizações devem superar para construir um programa de manutenção melhor é começar a coletar informações de manutenção relevantes.
A primeira pergunta para as organizações é quais informações de ativos e manutenção são importantes. O histórico de ativos e equipamentos pode fornecer informações valiosas durante o processo de manutenção e reparo. Por exemplo, saber quando o equipamento foi comprado e há quanto tempo está em serviço pode ser um bom indicador se será um reparo ou um cenário de substituição.
Informações detalhadas sobre ordens de serviço anteriores relacionadas ao equipamento podem ser extremamente úteis para sugerir o problema antes mesmo de o trabalho de manutenção ser iniciado. Uma lista de peças, desenhos de referência e documentação são outros exemplos de dados que podem ser valiosos para o processo de manutenção.
Depois que uma empresa determina quais informações são necessárias, a próxima etapa do processo é construir um histórico ou biblioteca de informações de manutenção. As organizações podem optar por fazer isso de várias maneiras, mas uma das mais comuns é usar um sistema CMMS ou EAM. A vantagem de construir esse histórico em um CMMS é que ele está disponível no mesmo sistema que trata do gerenciamento de ordens de serviço, facilitando a acessibilidade.
Conforme os dados de manutenção e ativos são coletados, é imperativo que estejam disponíveis para as pessoas que precisam deles. Pode ser um grupo grande e diversificado de muitos usuários diferentes, de um gerente externo a um técnico de campo. Não se trata apenas de disponibilidade, mas também de formato. A granularidade de que um técnico precisa é provavelmente muito maior do que a de que um vice-presidente precisa.
Embora a coleta de dados seja a primeira etapa, o valor da informação aumenta quando transformada em inteligência. Isso é feito avaliando os dados quanto às tendências e, em seguida, atuando de acordo com essas tendências. Por exemplo, se a análise de dados mostra que as últimas três falhas de uma bomba ocorreram logo após ela ter estado em serviço por 2.000 horas, então o agendamento de uma atividade de manutenção preventiva (PM) em 2.000 horas pode evitar a falha da bomba.
Agendar o PM é uma ação, e essa é uma parte essencial da conversão de dados em inteligência. Dados acionáveis são fundamentais para conduzir um programa de manutenção eficaz.
A inteligência de manutenção e as análises correspondentes melhoram a tomada de decisões, permitem que as métricas sejam estabelecidas, facilitam a manutenção e a medição do desempenho dos ativos e dão suporte à implementação de manutenção preditiva.
Transição de manutenção reativa para pró-ativa
O bloco de construção final para um programa de manutenção eficaz envolve a transição da manutenção reativa para a pró-ativa. A manutenção reativa pode ser melhor definida como uma abordagem de manutenção do tipo “conserte quando quebrar”.
As empresas que reagem quando ocorre um problema, em vez de agir antes do problema, veem um alto volume de tempo de inatividade não planejado, vida útil mais curta do equipamento e custos de manutenção mais altos.
Embora muitas organizações queiram criar um programa de manutenção mais proativo, isso pode ser desafiador. Existem várias chaves para a transição reativa para proativa. No nível básico, isso não pode ser feito até que uma empresa esteja coletando inteligência de manutenção e ativos. Esta é a razão pela qual os sistemas CMMS são tão básicos para o desempenho de manutenção. Eles são uma das maneiras mais fáceis e econômicas de reunir informações de manutenção.
Como mencionado anteriormente, não basta ter os dados. As empresas devem investir na análise das informações e na identificação de tendências que lhes permitam planejar e programar um trabalho de PM eficaz. Um objetivo de longo prazo é mudar para um modelo de manutenção mais preditivo em conjunto com as atividades de PM.
Os eventos de tempo de inatividade não planejado podem não ser eliminados completamente, mas mudar para uma abordagem proativa, onde as empresas antecipam e agem sobre os problemas antes que eles ocorram, pode reduzir o tempo de inatividade não planejado, aumentar a eficiência da programação de trabalho, melhorar a confiabilidade do equipamento e reduzir os custos de manutenção.
Construindo uma base para o sucesso
Os desafios de manutenção são semelhantes em todos os setores e organizações. Cada empresa deve estabelecer suas prioridades e metas de manutenção e, em seguida, construir um programa de manutenção de acordo. Não existe uma resposta “tamanho único”, pois o sucesso da manutenção tem muitos fatores.
No entanto, existem elementos fundamentais para construir uma boa base para o sucesso da manutenção. Quatro elementos principais são gerenciamento de ordem de trabalho, capacitação com tecnologia, obtenção de inteligência de ativos e manutenção e transição de uma abordagem de manutenção reativa para pró-ativa. Esses blocos de construção podem oferecer benefícios importantes, como redução do tempo de inatividade não planejado, aumento da eficiência do trabalho, extensão da vida útil do equipamento e redução dos custos gerais de manutenção.
Este artigo foi publicado anteriormente na Reliable Plant 2019 Conference Proceedings.
Manutenção e reparo de equipamentos
- A chave nº 1 para o sucesso da confiabilidade
- Medindo o sucesso do programa de manutenção preditiva
- Hamilton Sundstrand fornecerá manutenção para a companhia aérea
- SMRP é valioso para profissionais de M&R
- Comportamento de sucesso das unidades de programação de manutenção
- Perguntas de manutenção preditiva respondidas
- Penske reconhecida pelo programa de treinamento de manutenção
- Como construir um programa de manutenção elétrica
- Acompanhamento é a chave para maior eficiência
- Gerenciamento de códigos QR para gerenciamento de instalações