Estudo de caso de confiabilidade da planta farmacêutica
Profissionais de manutenção e confiabilidade podem fazer a diferença. Na maioria das fábricas, isso significa um trabalho focado que permite às operações obter mais produtos acabados (sejam refrigerantes, motocicletas, lâmpadas, carros, cupcakes, aquecedores de água, etc.) para fora da porta.
Na fábrica de insulina humana biossintética (BHI) da Eli Lilly em Indianápolis, fazer a diferença ganha um significado adicional.
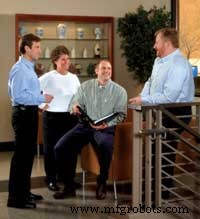
Quase 21 milhões de pessoas na América - e 200 milhões de pessoas em todo o mundo - têm diabetes. Só nos EUA, quase 1 milhão de novos casos são diagnosticados a cada ano. Muitas pessoas com diabetes precisam de insulina para controlar o açúcar no sangue (glicose), e a planta BHI ajuda a suprir essa necessidade. Inaugurado para produção em 1992, o site produz uma porcentagem significativa da insulina medicinal do mundo. O trabalho de manutenção e confiabilidade que aumenta a produtividade permite que a empresa obtenha medicamentos de alta qualidade e sustentáveis nas mãos de quem precisa.
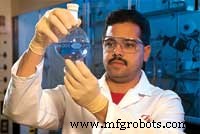
Quer você trabalhe para uma empresa que fabrica chips de computador ou batata frita, quando você agrega valor às partes interessadas ou à economia, isso não pode ser menosprezado de forma alguma ”, diz Ken Swank, líder da equipe de manutenção e confiabilidade da fábrica. “Não importa o que você faça. É importante. Porém, há uma diferença distinta. Eu trabalhava para uma empresa de tintas industriais. Nossos revestimentos cobriram tudo, desde bolas de golfe até o ônibus espacial e instrumentos cirúrgicos. Quando vi o produto final, soube que fazia parte disso. Mas quando você trabalha para uma empresa farmacêutica. . . isso significa muito a nível pessoal.
Conheci um casal no fim de semana que tem um filho pequeno. Começamos a conversar e descobri que o menino tem diabetes. Eu perguntei se ele tinha tipo 1 ou tipo 2. O pai perguntou, como você sabe tanto sobre diabetes? O menino me disse que era do Tipo 1. Eu olhei para ele e disse:'Adivinha o que eu faço para viver? Eu faço insulina. Eu trabalho na Eli Lilly e faço Humulin. "Ele disse:" Obrigado. Eu realmente gosto do meu remédio. Isso me faz sentir muito melhor. '
“Meu departamento é responsável por garantir que este prédio produza os medicamentos que deve produzir todas as vezes. Existem milhões de pessoas que dependem dele e o buscam todos os dias. ”
A planta BHI é grande e tecnicamente complexa. Abriga mais de 17.000 peças de equipamento, 13.000 pontos de entrada / saída e 600 unidades operacionais. O método de processamento para gerar a molécula de BHI envolve várias etapas de centrifugação, um punhado de reações, muitas etapas de purificação e várias etapas de troca de solvente. Como resultado, aproximadamente um terço das unidades operacionais são classificadas como de alto risco ou de operação crítica para a segurança. Os esforços de aprimoramento da BHI começaram com a adição de um engenheiro de confiabilidade em 1999 e a introdução de projetos de Manutenção Centrada em Confiabilidade (RCM) e análise de falha de causa raiz (RCFA). Esses esforços aumentaram quando agências regulatórias como a Food and Drug Administration e a Environmental Protection Agency começaram a examinar de perto a manutenção na indústria farmacêutica. A mensagem das agências era simples:manutenção é igual a confiabilidade da planta; a confiabilidade da planta é igual à confiabilidade do produto; e a confiabilidade geral é igual a conformidade. Empresas “não confiáveis” podem enfrentar penalidades, incluindo o encerramento de suas operações. "Foi quando, eu acho, a confiabilidade começou a ter o foco que tem hoje", diz Swank. "Em nossa jornada para nos tornarmos uma planta verdadeiramente confiável, a visão é que quando a produção usar um pedaço de equipamento, está em um estado qualificado, está disponível quando necessário e vai funcionar no nível de desempenho predeterminado. Obviamente, desempenhamos um grande papel nisso. As estratégias de manutenção que elaboramos tratam de manter esse equipamento em um estado qualificado. Além disso, a profundidade das estratégias de manutenção aborda a utilização ou o tempo de atividade necessário. Existem operações na instalação que funcionam mais do que outras, têm menos redundância do que outras ou são mais essenciais do que outras. Essas operações requerem mais atenção e investigação mais detalhada . ”
O campus da empresa em Indianápolis contém
fábricas e escritórios corporativos.
Crescentes demandas
Alguns anos atrás, os líderes de manutenção e confiabilidade decidiram que era necessário implementar mudanças substanciais para maximizar o tempo do departamento, as habilidades, os recursos e o impacto potencial na fábrica. A BHI estava operando com mais do que o dobro de sua capacidade original de design e a demanda de negócios continuou a aumentar. Os técnicos estavam comprometidos demais, os esforços de remediação eram freqüentemente repriorizados para atender às necessidades do momento e os sistemas cruciais não estavam recebendo uma porcentagem justa de atenção.
Eli Lilly produz 25 por cento do suprimento mundial de insulina.
Nunca nos preocupamos com o funcionamento de nossos equipamentos em um estado qualificado ”, afirma Swank. “Mas, como o resto da indústria farmacêutica na época, não demos ênfase extra aos nossos equipamentos, a não ser que sempre quisemos o máximo de tempo de atividade que pudéssemos obter para produzir o máximo de remédios. Mas quando você olha para tirar o máximo possível de quilos pela porta, chegamos ao ponto em que você questiona:‘Continuamos adicionando instalações ou fazemos isso de forma inteligente do ponto de vista de negócios e nos concentramos na confiabilidade?’ ”
Era algo que várias instalações da Eli Lilly estavam ponderando no final dos anos 1990. Por exemplo, o gerente de engenharia da BHI, Ron Reimer, liderou os esforços para aumentar o trabalho proativo e o tempo de atividade e diminuir os custos de manutenção enquanto estava no local dos Laboratórios Clinton (Ind.) Da empresa. Como parte desse projeto, que foi sistematizado e denominado Proactive Asset Management, ele contratou o primeiro engenheiro de confiabilidade da empresa.
Envolvimento direto de todos os principais interessados na confiabilidade da planta
(produção, HSE, controle de qualidade, finanças, engenharia e gerenciamento) ajuda a garantir o sucesso da iniciativa de priorização de confiabilidade.
Importância da comunicação
De acordo com o líder da equipe de manutenção e confiabilidade Ken Swank, a comunicação desempenha um papel importante no sucesso da iniciativa de priorização de confiabilidade da planta de BHI.
“A comunicação é uma das partes mais importantes do meu trabalho”, diz ele. “Eu me encontro com os líderes de produção com frequência e explico a eles o que está acontecendo. Eu obtenho o compromisso deles e os ajudo a entender o valor que ele está agregando. Eles também precisam desembolsar alguns recursos. Uma análise adequada não é apenas nosso departamento, obviamente. Envolve engenharia, manutenção, confiabilidade, operações, serviços técnicos, automação às vezes. Gastamos muito tempo para garantir que eles entendam o valor.
Tenho que dançar e cantar bastante para ajudá-los a entender. Mas, de todas as contas, a adesão foi boa. ”
Uma iniciativa de priorização que começou no início de 2004 foi fundamental nesta estratégia para entregar tempo de atividade e confiabilidade às unidades operacionais que merecem mais atenção.
Como a Eli Lilly define funções de confiabilidade
De acordo com os líderes de manutenção e confiabilidade da Eli Lilly BHI, as funções e responsabilidades de seus engenheiros de confiabilidade incluem:
As funções de trabalho e responsabilidades dos técnicos de confiabilidade incluem:
Faça disso uma prioridade
Swank reconta as ordens de marcha que acabariam por levar a um remédio para a confiabilidade.
“Meu chefe disse na época:‘ Descubra como vamos tornar as instalações da BHI mais confiáveis. Precisamos controlar isso '”, diz Swank. “O que ele realmente quis dizer foi:'Você e sua equipe precisam entender as necessidades de negócios da instalação, determinar um método para definir um caminho a seguir para remediar as lacunas de confiabilidade priorizadas corretamente, vendê-lo para a empresa, executá-lo e fazer é sustentável. ”
Parece fácil, ou assim ele pensou.
“Começamos em fevereiro (2004) e presumimos que terminaríamos em março ou abril”, diz ele. “Rapidamente percebemos que isso era mais complicado e complexo do que antecipávamos. Além disso, queríamos fazer certo. ”
O plano de jogo seria desenvolver uma análise que use os dados existentes para priorizar a correção do sistema como um esforço de melhoria contínua fora dos esforços de suporte diários do departamento. Os requisitos de análise foram:
Esse desafio foi colocado sobre os ombros da parte de engenharia de confiabilidade do departamento. O grupo incluía os engenheiros de confiabilidade sênior Mark Lafever, Vadim Redchanskiy e Rod Matasovsky (agora aposentado) e os técnicos de engenharia de confiabilidade David Doyle, Mary Ann Dust e Matt O’Dell. Eles começaram a traçar estratégias para o conteúdo da análise.
“Eles são os mais espertos. Fui o tradutor da gestão para os funcionários ”, diz Swank. “Eles entenderam os sistemas de dados e o que fazia sentido e o que não fazia.”
O grupo reconheceu que, para obter apoio para esta iniciativa, a análise teria que se basear em fatos e envolver diretamente e ser significativa para todos os principais interessados na confiabilidade da planta - produção; saúde, segurança e meio ambiente (SMS); controle de qualidade (QC); finança; Engenharia; e gestão. Este seria um ato de equilíbrio incrível.
“Qualquer um pode sair e extrair um monte de dados”, diz Lafever. “Tínhamos que decidir de onde extrair os dados, como iríamos extraí-los e descobrir se os dados nos diriam as informações de que precisávamos para tomar as decisões certas.”
Tabela 1. Resumo das ponderações para os cinco cenários.
Tabela 2. Exemplo da análise de sensibilidade do primeiro cenário.
Depois de várias iterações - e “muita esfregação de cabeça”, diz Lafever - a equipe finalizou uma análise que levou as partes interessadas em consideração, usando dados existentes dos últimos 12 meses. Esses dados incluem:
1) Horas de Trabalho Emergencial, equiparadas ao tempo de inatividade do equipamento, para atender à produção. Isso foi coletado do sistema de gerenciamento de manutenção computadorizado da planta, que rastreia todas as horas cobradas em cada unidade operacional. O trabalho de emergência foi definido como “trabalho que não pode esperar”. Embora não seja uma medida tradicional de tempo de inatividade do sistema, isso se correlaciona diretamente com a quantidade de interrupção da produção sentida quando o sistema não estava funcionando corretamente.
2) Classificação de risco, de acordo com o Gerenciamento de Segurança de Processo Globalmente Integrado (GIPSM) da Lilly, para satisfazer HSE. O sistema de classificação tem quatro possibilidades:operação crítica para a segurança, o principal fator de risco; alto risco, que envolve considerável risco ambiental, de saúde e de incêndio; integridade mecânica, que é definida pela Administração de Segurança e Saúde Ocupacional; e nenhum risco ou "nenhuma das opções acima".
3) Número de desvios ao processo causados por falhas de equipamento para satisfazer o CQ. Esses desvios direcionados eram o resultado de problemas de confiabilidade do equipamento, e não de erro do operador ou outros problemas não relacionados ao equipamento. O número de desvios foi levado em consideração junto com um nível (1, 2 ou 3) que localizou o impacto do desvio na qualidade do produto.
4) Custo do trabalho reativo para satisfazer as finanças. Isso foi novamente retirado do CMMS, que rastreia todos os encargos orçamentários contra as unidades operacionais. Esse custo inclui todas as peças e mão de obra associada ao trabalho reativo realizado no sistema.
5) Entrada do engenheiro de processo para satisfazer a engenharia. O engenheiro de processo responsável por cada sistema foi pesquisado sobre tópicos como idade do sistema, horas de tempo de inatividade potencial gerado por falha do sistema e impacto regulatório.
6) Plano de manutenção do estado do sistema, também para satisfazer a engenharia. Isso foi elaborado para incluir quatro níveis:Nível 1, nenhuma manutenção de rotina conduzida, que foi considerada a mais severa; Nível 2, existe manutenção preventiva no sistema; Nível 3, Avaliações Periódicas de Qualificação (PQEs), destinadas a garantir que o sistema está em um estado constante de qualificação e apto para o uso, são executadas; e, Nível 4, uma análise baseada em RCM foi usada no sistema para gerar um plano de manutenção.
Esses dados criaram uma avaliação de “equipamento crucial” que olhou para as 420 unidades operacionais e identificou aquelas com potencial para interromper a produção ou causar um incidente reportável OSHA ou EPA.
“A maneira como nossa estrutura é configurada em nosso CMMS e a maneira como controlamos nosso banco de dados de incidentes, a unidade operacional foi a melhor opção”, disse Lafever. “Às vezes, uma unidade operacional é um equipamento. Na maioria das vezes, é uma peça importante do equipamento, além de muito mais. ”
Por exemplo, Redchanskiy diz que a unidade operacional EV1411 (processo de evaporação) inclui “50 a 60 peças de equipamento e instrumentação, como válvulas, trocadores de calor e bombas”.
A avaliação cortou a lista inicial em 70 por cento, de 420 unidades operacionais para 135.
Os fatos não mentem
Quando se trata de determinar a importância de uma unidade operacional específica, é difícil contestar os fatos.
“Antes de fazermos esta análise, tudo o que a produção falava era da centrífuga ligada o front-end ”, diz Ken Swank, líder da equipe de manutenção e confiabilidade da Eli Lilly. “Após a análise e mostrar a eles o que descobrimos - eu apontei que a centrífuga estava classificada em 63º lugar (na lista de 135 unidades operacionais) - eles não perguntam muito sobre isso.
“Isso também nos faz olhar para fora da definição de equipamento de produção. Antes da análise, as pessoas se esqueceram de incluir tanques de resíduos, manipuladores de ar, etc. Eles não pensaram no Tanque 1099 na Sala de Controle 2, para onde vão todos os ralos do chão. A descarga passa pelos ralos e vai para o tanque. Se esse tanque não estiver operacional, temos que encerrar nossas etapas de purificação. ”
Pesos e medidas
Para garantir a priorização adequada das 135 unidades restantes, o grupo decidiu aplicar uma ponderação a cada fonte de dados e realizou várias análises de sensibilidade.
“Não achamos que os seis critérios tivessem o mesmo peso”, diz Swank. “Sentimos que a segurança e a qualidade tiveram um impacto maior do que, digamos, a quantidade de dinheiro que estávamos gastando em trabalhos de emergência”.
Um sistema de pontuação (zero a 3, com zero sendo o menor impacto e severidade e 3 sendo o maior impacto e severidade) foi desenvolvido para cada conjunto de dados e aplicado a cada unidade operacional. A repartição foi a seguinte:
Horário de Trabalho de Emergência (HEW) :menos de 15 horas (pontuação zero), 15 a menos de 25 horas (uma), 25 a menos de 40 horas (duas) e 40 ou mais horas (três).
Classificação de risco (RC) :sem risco de SMS (zero), sistema de integridade mecânica (um), processo de alto risco (dois) e operação crítica de segurança (três).
Desvios (D) :Quatro agrupamentos foram feitos levando em consideração os níveis e números de desvios. Foi determinado que um desvio de Nível 2 era igual a três vezes um desvio de Nível 1 e um desvio de Nível 3 era igual a duas vezes um desvio de Nível 2. Isso fez com que um desvio de Nível 1 valesse um ponto, um desvio de Nível 2 valesse três pontos e um desvio de Nível 3 valesse seis pontos. Isso foi aplicado a todos os desvios. Como resultado, os valores foram:dois ou menos (zero), maior que dois a cinco (um), maior que cinco a oito (dois) e maior que oito (três).
Custo do trabalho reativo (CRW) :menos de $ 5.000 (zero), $ 5.000 a menos de $ 7.499 (um), $ 7.500 a $ 14.999 (dois) e $ 15.000 ou mais (três).
Entrada do Engenheiro de Processo (PEI) :sistema de impacto mínimo (zero) e escalonamento até sistema de impacto máximo (três).
Estado do Plano de Manutenção do Sistema (SSMP) :Análise de RCM realizada no sistema (zero), PQE executado de forma rotineira (um), PMs realizados (dois) e nenhuma manutenção de rotina realizada (três).
As pontuações foram aplicadas às 135 unidades operacionais. As informações foram carregadas em uma planilha e vários pesos foram aplicados para enfatizar a importância de vários conjuntos de dados. O projeto de análise de sensibilidade incluiu cinco cenários de ponderação diferentes para garantir que um único ponto de dados não conduzisse à priorização de um sistema.
Os cenários variaram de uma distribuição de peso bastante uniforme (HEW, HSE, D e SSMP, 20 por cento cada; CRW e PEI, 10 por cento cada) à eliminação de duas categorias (HEW, HSE, D e CRW, 20 por cento cada; PEI e SSMP, zero por cento). No último cenário, os conjuntos de dados restantes eram “dados verdadeiros” que mudavam de acordo com o nível de confiabilidade demonstrado pelo sistema. Os cenários são mostrados na Tabela 1.
Cada cenário na análise de sensibilidade pegou o fator de risco e o multiplicou pela ponderação desse cenário específico. O produto de cada categoria foi somado para cada unidade operacional. A Tabela 2 mostra um exemplo do primeiro cenário.
Quando todos os cinco cenários foram concluídos, as pontuações finais das unidades operacionais foram representadas graficamente e examinadas pela equipe de confiabilidade. Antes de determinar as classificações finais e planos de remediação, fatores adicionais foram considerados. A unidade em questão foi substituída recentemente ou está no plano de reposição? Os planos de remediação desta unidade podem ser aplicados a outras unidades? Quais grupos funcionais são necessários para essa correção e eles estão disponíveis? Quais atividades de remediação foram realizadas no passado?
“Por exemplo, uma das centrífugas saiu perto do topo da lista, mas sabíamos que outro site estava fazendo um RCM em um sistema muito semelhante”, diz Swank. “Não precisamos duplicar os esforços.”
A lista final das atividades de remediação propostas variava, dependendo da unidade operacional, de uma análise detalhada de RCM até a não correção do sistema.
Nesse ponto, a equipe sabia que tinha um plano abrangente.
“Foi difícil”, diz Lafever. “Criamos um plano três vezes - parecia 30 - e continuávamos dizendo:'Isso não é bom o suficiente.' 'Como seria o controle de qualidade sobre isso?' 'Como a engenharia de processo se sentiria sobre isso?' ficaram muito perplexos. Tínhamos que ter certeza de que abordamos todas as facetas e todas as possíveis questões. ”
Swank acrescenta:“A primeira tentativa foi como,‘ Uau, não chega nem perto ’. Tornou-se óbvio por que não havia sido feito antes. É um monte de trabalho. Também há coisas do dia-a-dia que continuam tirando você de algo assim. Mas dissemos a nós mesmos que iríamos continuar e fazer isso ”.
Por escrito
Em 21 de setembro de 2004, Swank apresentou formalmente o modelo de priorização para a equipe principal da fábrica, que inclui o chefe do local e todos os gerentes funcionais. Os exaustivos sete meses de trabalho valeram a pena.
“Não houve troca ou discussão de um lado para outro”, diz ele. “They were like, ‘This is great. Proceed.’”
Of course, a head nod and a hand wave only go so far. So, Swank had Lafever create a report that summed up the evaluation process and detailed how the crucial equipment analysis would be performed year over year. The report would serve as a template for future evaluations.
“I told the lead team members to sign it,” says Swank. “They did. I have it in writing. There was no hesitation. That goes to show you that the analysis we did was real strong.”
On Feb. 28, 2005, the crucial equipment analysis was formalized and approved by the lead team, and the remediation activities for the plant’s most vital operating units were included in the plant’s 2005 and 2006 business plans.
The template has made subsequent evaluations almost seamless.
“Last year, it was a breeze to do the analysis,” says Lafever.
The 2006 plan was completed in May.
Remedy's Results
Maintenance and reliability department leaders at this Eli Lilly plant say they are currently unable to quantify the bottom-line, dollars-and-cents impact of the reliability prioritization initiative.
“The unfortunate part is we don’t always see the results of our work year after year,” says Lafever. “There might be a year delay because it takes time to work through the system.”
But that doesn’t mean there haven’t been benefits and results.
Redchanskiy and Doyle say there are inevitable cost savings just by re- evaluating how maintenance is performed on a given asset.
“In the analysis, we found we were spending a considerable amount of money on a couple of systems that didn’t have any reactive work,” says Redchanskiy. “We spent a ton on preventive maintenance. We overdid it on PMs. We changed the way we did maintenance on those systems.”
“The biggest shift from this is that for some systems, people can now say that it’s actually OK to run to failure,” says Doyle. “If that is our diagnosis and plan for that particular system, it’s OK. That’s a whole different philosophy for us.”
Swank says positives can be drawn from the plant’s productivity levels.
“The fact that we’ve met our inventory levels, and the fact that our business model is moving toward heightened productivity, shows we have already reached our first major milestone,” he says.
Lafever believes involvement with remediation projects has led to increased technical knowledge and increased uptime.
“When most maintenance and operations people come out of an RCM analysis, they could be classified as experts on that system,” he says. “Everybody has a better understanding of the groups’ individual functions and how they work together to perform their part of fixing a piece of equipment or identifying when there’s a problem with a piece of equipment. That interaction itself, I think, reduces the amount of emergency work that develops.”
The best indicator of success?
“It makes our upper management happy,” says Doyle.
“And that makes me happy,” says Swank.
All of these improvements could explain why BHI received the 2005 Making Medicine Award, which goes to the Eli Lilly plant that “best meets the needs of the business and embodies what manufacturing is supposed to be like at the company.”
Other Lilly plants are taking note of the prioritization initiative and are examining the feasibility of adoption. This has led to increased visibility corporate-wide for maintenance and reliability.
“Part of the good has been corporate understanding and awareness of the value that maintenance adds,” says Reimer. “It’s something that we definitely want to take advantage of.”
This team demonstrates daily that maintenance and reliability professionals can and do make a difference.
Manutenção e reparo de equipamentos
- Estudo de caso:acionamentos e retrofits em cortadora-rebobinadeira de fábrica de papel
- A planta de pistão adota uma abordagem proativa para confiabilidade e OEE
- Drew Troyer:Como os processos de negócios afetam a confiabilidade
- Como a confiabilidade da planta afeta uma implementação enxuta
- Usina hidrelétrica no Havaí aumenta sua eficiência, confiabilidade
- Saudi Electricity Company para aumentar a confiabilidade da usina de energia
- Sistema sem fio para aumentar a confiabilidade na usina de Nevada
- Melhorar a disponibilidade é muito mais do que manutenção
- NV Energy instala solução sem fio para aumentar a confiabilidade da planta
- Estudo de caso:Solução de crise de máquina desativada