Como conduzir um estudo de tempo no chão da fábrica
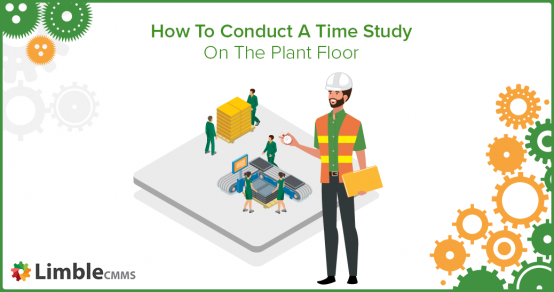
Há uma coisa em comum entre as forças armadas modernas, atletas, departamentos de RH e empresas de tecnologia do Vale do Silício - todos eles usam táticas e estratégias inspiradas por Frederick Winslow Taylor, frequentemente referido como o “pai da gestão científica”.
As ideias de Taylor, como melhorar a ética no trabalho, reduzir o desperdício e criar padrões de produção aprimorados, continuam a ter credibilidade. Uma dessas ideias, que é crítica para melhorar a eficiência no chão de fábrica, vem na forma de um estudo de tempo .
Conduzir estudos de tempo e movimento não é uma tarefa comum. Requer uma preparação cuidadosa com um plano bem elaborado. Nesta postagem, descreveremos o processo e mostraremos o que você precisa ter cuidado se quiser acertar na primeira tentativa.
O que é um estudo do tempo?
British Standards Institutions (BSI) é o principal órgão encarregado da criação de padrões de engenharia e industriais de produção no Reino Unido. É assim que o BSI define o estudo do tempo:
“Observação, registro e classificação do trabalho humano para estabelecer os tempos exigidos por um trabalhador qualificado para realizar o trabalho especificado sob condições estabelecidas em uma taxa de trabalho definida.”
O “trabalho” a que se refere envolve todas as atividades no chão de fábrica que contribuem para o processo de produção - o uso de trabalho manual ou de máquinas, operadores de máquina tomando decisões em tempo real e semelhantes.
Os estudos de tempo são mais adequados para atividades que envolvem um conjunto de ações previsíveis e repetitivas. Eles são ideais em configurações de fábrica, onde o processo de produção pode ser dividido em uma série de tarefas sequenciais e movimentos do operador.
Nesse contexto, você mede a quantidade de tempo gasto para uma determinada tarefa, realizada por vários trabalhadores, para encontrar o tempo padrão (mostraremos o cálculo posteriormente neste artigo). Em engenharia industrial e manufatura, o tempo padrão é o tempo médio gasto por um trabalhador devidamente treinado para concluir uma tarefa específica.
O estudo do tempo é uma atividade de medição do trabalho, geralmente realizada por um observador treinado, com o auxílio de equipamentos básicos como um cronômetro e uma prancheta para anotar os registros de tempo. Em fábricas modernas, os observadores podem usar mais ferramentas avançadas como câmeras de vídeo, computadores e até mesmo software especializado.
Por que realizar uma análise de estudo de tempo?
Quando conduzido adequadamente com o devido planejamento e análise cuidadosa, um estudo de tempo oferece uma visão granular de quão eficientemente o trabalho está sendo conduzido no chão de fábrica. O tempo padrão é uma métrica inestimável para gerentes que buscam maneiras de melhorar a eficiência da produção e a produtividade em geral.
Ele também pode ser usado para localizar falhas e pontos fracos ocultos em outros aspectos do chão de fábrica, como layouts abaixo do ideal e colocação de máquinas e estações de trabalho. Usando o tempo padrão, você pode localizar ineficiências na alocação de mão de obra, máquinas e outros insumos de produção.
Além das melhorias de custo e eficiência, os estudos de tempo podem ser vitais para o bem-estar do trabalhador. Pode ajudar na criação de espaços de trabalho melhores e mais seguros. Os gerentes podem identificar e remover movimentos e ações desnecessários e potencialmente perigosos no chão de fábrica, reduzindo assim o esforço necessário para concluir tarefas específicas.
Existem muitos outros benefícios em conduzir um estudo de tempo:
- necessário para um planejamento realista das programações de produção
- ajuda na alocação ideal de mão de obra no chão de fábrica
- pode ser usado para comparação com processos alternativos
- necessário para uma distribuição equilibrada do trabalho entre os funcionários
- ajuda a criar prazos e incentivos salariais
- ajuda a eliminar operações ineficientes ou desnecessárias e minimizar o esforço do trabalhador
- se feito para trabalhadores de manutenção, pode ajudar os planejadores e gerentes de manutenção a planejar e organizar melhor o trabalho de manutenção de rotina
O tempo padrão é uma métrica muito útil para engenheiros industriais e gerentes de produção. Isso permite que eles comparem a eficiência de suas instalações com os padrões da indústria. A métrica também é valiosa de uma perspectiva de planejamento futuro, ao estimar os seguintes aspectos principais:
- prazos de entrega de lotes de produtos futuros
- futuras necessidades de mão de obra e custos de mão de obra
- futuras necessidades de investimento em máquinas / equipamentos de produção
- necessidades futuras de aquisição de matéria-prima
- gerenciamento de estoque
- custo total de produção e preço de venda por unidade
Existem muitas razões para conduzir estudos de tempo. Vamos ver o que você deve instalar antes de iniciar o cronômetro.
Requisitos básicos para a realização de estudos de tempo bem-sucedidos
Independentemente da indústria ou dos processos de produção envolvidos, um estudo de tempo terá os mesmos requisitos básicos.
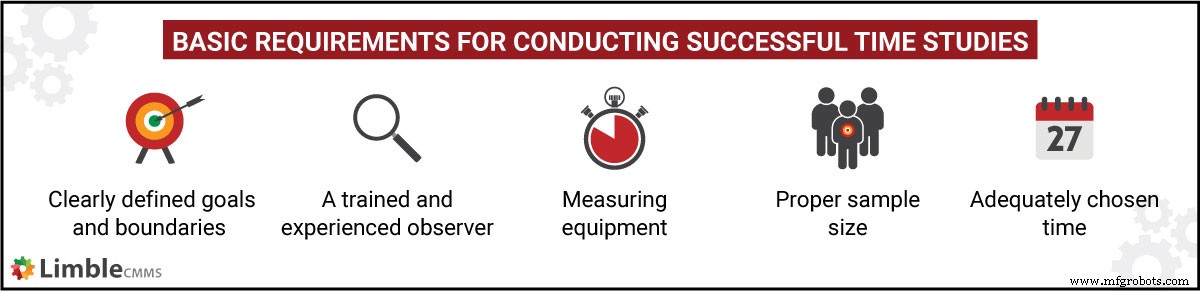
Podemos classificá-los nas 5 áreas a seguir que você precisa abordar ao preparar seu estudo de tempo:
1) Metas e limites claramente definidos
Antes de conduzir seu estudo de tempo e movimento, você precisa estabelecer limites claros.
Primeiro, determine e especifique os objetivos do estudo - acelerar o processo de produção, remover ações desnecessárias, etc.
Em seguida, escolha os processos que serão o foco central do estudo. Veja se o seu setor já estabeleceu horários padrão que você pode usar como ponto de referência para comparação.
2) Um observador treinado e experiente
Esta é a pessoa que conduzirá o estudo do tempo. Na maioria dos casos, engenheiros industriais com experiência e treinamento relevantes são os preferidos para este trabalho.
Idealmente, eles devem ter certificação em otimização de local de trabalho. O observador deve ter um ponto de vista seguro e confortável, de onde possa observar os trabalhadores enquanto realizam as tarefas regulares.
Existem empresas por aí, como a Industrial Time Study Institute, que oferece serviços de consultoria e treinamento. Eles podem ajudá-lo a executar seus estudos de tempo e responder a quaisquer perguntas técnicas.
3) Escolha do equipamento (básico vs avançado)
O papel desempenhado pelo equipamento de estudo do tempo mudou dramaticamente nos últimos anos. No passado, os estudos eram realizados com um cronômetro simples e pranchas de estudo de tempo, com o observador próximo aos trabalhadores.
Isso tinha algumas desvantagens importantes, a mais importante das quais era o “Efeito Hawthorne” - os trabalhadores podem se esforçar mais do que o normal quando sabem que estão sendo observados.
A tecnologia moderna permite que os observadores assistam e registrem os tempos à distância e em segredo, usando equipamentos de vídeo (CFTV) e plataformas de software especializadas que podem substituir o cronômetro e as tabelas básicas de registro do estudo do tempo.
4) Tamanho de amostra adequado
Deve-se tomar o devido cuidado ao escolher o tamanho da amostra de mão de obra. Se não for suficientemente grande e representativo de sua força de trabalho existente, sua medição de trabalho será praticamente inútil.
A qualidade e competência dos trabalhadores também são críticas. Um erro comum é escolher os indivíduos com melhor desempenho. Em vez disso, escolha um tamanho de amostra equilibrado que favoreça os trabalhadores bem treinados, mas cuja produção de trabalho não os coloque no extremo de baixa ou alta produtividade.
5) Horário adequadamente escolhido
Para reduzir a margem de erro, um estudo de tempo geralmente envolve fazer medições em vários ciclos de produção. Nas unidades fabris, haverá períodos de produção com prazos mais curtos e atividade mais intensa no chão de fábrica.
Deve-se ter cuidado ao escolher um período que seja representativo do fluxo de trabalho geral na instalação, dentro de limites previsíveis. A menos que você tenha um objetivo específico, evite os períodos de pico de demanda ao conduzir estudos de tempo.
Delineando o processo:como fazer um estudo do tempo?
Um estudo de tempo é conduzido linearmente, com várias etapas claramente definidas. O observador qualificado tomará o seguinte curso de ação assim que o estudo começar:
- Selecione as tarefas para estudar :isso vai depender dos objetivos do estudo e dos limites básicos estabelecidos pela empresa. O tipo de negócio de manufatura e o estado atual dos sistemas de produção terão um papel definidor aqui.
- Analise as tarefas individuais :a produção segue processos e padrões já estabelecidos na indústria? Se sim, o observador pode selecionar padrões de linha de base e calibrar o processo de medição para refleti-los. Se não houver padrões, o observador terá que usar sua experiência e julgamento para traçar a melhor linha de base.
- Selecione os trabalhadores qualificados :deve ser uma amostra representável de trabalhadores médios adequadamente treinados.
- Estime o número de ciclos a serem observados: mais amostras de dados resultarão em menos margem de erro, mas requerem mais tempo e esforço. É necessário um ato de equilíbrio aqui, com base nos limites de tempo e orçamento.
- Comunique os detalhes do estudo aos trabalhadores :os estudos de tempo podem ter uma influência disruptiva na força de trabalho. As pessoas ficarão preocupadas com as implicações potenciais que o estudo pode ter na segurança de seu emprego futuro. É muito importante comunicar o propósito de um estudo com antecedência.
- Observe e registre o desempenho do trabalhador e os tempos de cada elemento: muitas técnicas estão disponíveis para os observadores. Se estiver usando um relógio de ponto básico, os métodos de cronometragem incluem o método contínuo, o método snapback e o método acumulado. Ferramentas e softwares mais avançados permitem que essas medições sejam automatizadas.
- Use os dados observados para calcular o tempo padrão: a fórmula e os cálculos serão explicados em detalhes na seção seguinte.
Finalmente, com base nos cálculos e nos objetivos iniciais do estudo, a empresa deve ser capaz de chegar a algumas conclusões viáveis.
Como calcular a hora padrão
Depois que o observador registrou as leituras de tempo real de todos os trabalhadores no grupo de amostra, é hora de calcular o tempo padrão. O processo segue esta ordem:
- calcular Tempo médio
- calcular Tempo normal usando tempo médio e fatores de classificação
- calcular o Horário padrão usando o tempo normal e subsídios
1. Calcule o Tempo Médio
Como o nome indica, é o tempo que o trabalhador leva para concluir a tarefa, do início ao fim. Quando vários trabalhadores estão sendo observados como parte do estudo, um valor médio de tempo observado é gerado calculando a média de todas as leituras de tempo registradas, após a remoção de quaisquer valores anormais.
2. Determine os fatores de classificação
O desempenho real registrado de um trabalhador pode nem sempre estar de acordo com os padrões “normais” da tarefa. O observador deve aplicar um ajuste ao tempo observado para deduzir o tempo que um operador médio levaria para concluir a tarefa.
Usando seu julgamento e experiência, o observador pode determinar a classificação de desempenho de cada trabalhador. Os sistemas de classificação populares usados para esta finalidade incluem:
- Classificação de ritmo / velocidade
- Sistema Westinghouse
- Classificação objetiva
- Classificação sintética
Esses sistemas de classificação usam fatores como velocidade, habilidade, esforço e consistência do trabalhador para avaliar seu desempenho. O fator de classificação é calculado como uma porcentagem de 90% ou 120%. Isso mostra quaisquer desvios do desempenho esperado, que é representado como 100%.
3. Calcule o Tempo normal
Quando você multiplica o tempo médio pelo fator de classificação no formato decimal, obtém o valor de “tempo normal” para uma tarefa. Aqui está a fórmula:
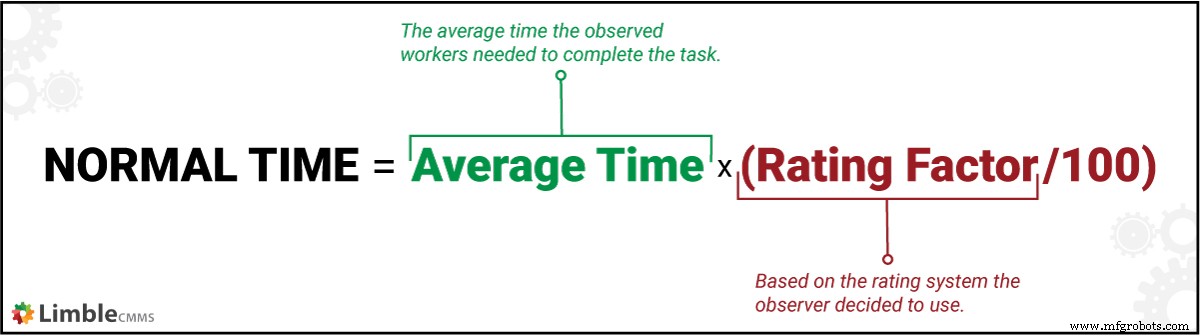
Para chegar no Horário Padrão, o Horário Normal é ajustado com valores adicionais chamados de “licenças”.
4. Fornecer abonos
As condições de trabalho do mundo real podem ter um impacto enorme na produtividade dos trabalhadores no chão de fábrica. Essas condições variam drasticamente de uma instalação de produção para outra. Os observadores devem fornecer subsídios para essas diferenças.
Eles têm uma ampla gama de fatores, que podem ser divididos em 5 categorias principais:
- Subsídio de relaxamento :inclui necessidades pessoais (tempo gasto para refeições, água e intervalos para ir ao banheiro, etc.) e cansaço (inclui coisas como duração da permanência, nível de iluminação, qualidade do ar, uso de força, esforço físico e mental, etc.).
- Tolerância de interferência: se o trabalhador tiver que operar várias máquinas ou ferramentas, essa permissão é usada para calcular o tempo de inatividade de uma máquina quando o trabalhador está ocupado em outras máquinas.
- Permissão de processo: é responsável por qualquer tempo de inatividade que venha como parte de um processo, ou devido a falha de energia, falhas nas máquinas, etc.
- Subsídio para imprevistos: isso será responsável por todas as interrupções ou atrasos irregulares e imprevisíveis (como manutenção de emergência) que podem surgir durante o processo de produção.
- Subsídio especial: algumas atividades de rotina - como partida, limpeza, desligamento e troca de equipamentos - são incentivadas pela administração, para melhorar a segurança e a longevidade do equipamento. A interrupção causada por essas interrupções é considerada no uso desse subsídio.
As concessões são dadas na forma de porcentagens, para que possam ser utilizadas no cálculo final do tempo padrão.
5. Calcule o Horário padrão
Finalmente, chegamos à métrica chave que nos dá o tempo gasto por um trabalhador normal para uma tarefa específica, quando ela é realizada em condições médias / padrão, depois de levar em consideração várias concessões para interrupções legítimas e inevitáveis.
Para chegar ao horário padrão, você deve multiplicar o horário normal por um fator de classificação de licenças. A fórmula é assim:
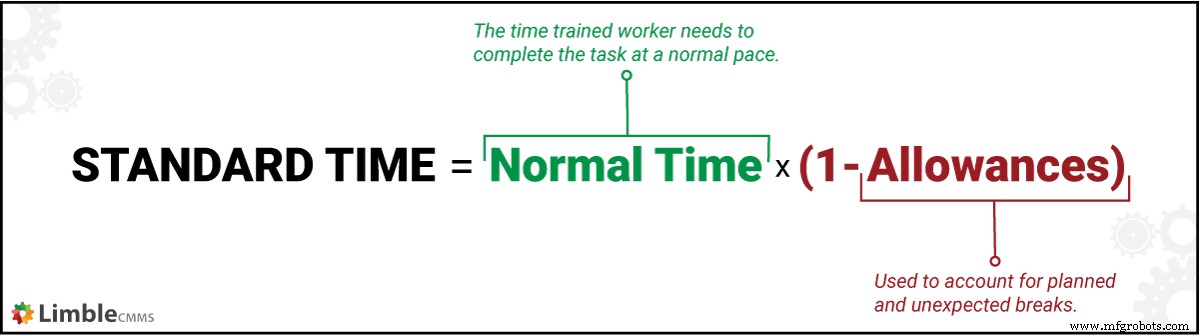
Agora, vamos mostrar como isso funciona em um exemplo real.
Exemplo de estudo de tempo de fabricação
Vamos considerar um ambiente de fabricação básico, onde os trabalhadores estão produzindo placas traseiras para pastilhas de freio de automóveis, em uma instalação totalmente nova. Imagine que esses trabalhadores levem em média 33 minutos para um lote de placas traseiras.
A empresa deseja realizar um estudo de tempo para descobrir como a eficiência do chão de fábrica se compara à média do setor e, se possível, identificar áreas que podem ser melhoradas.
Por causa deste exemplo, vamos supor que o valor de tempo esperado para a tarefa de produzir um lote de placas traseiras seja de 30 minutos.
As medições mostram que os trabalhadores são cerca de 10% mais lentos do que o normal. Assim, o observador pode atribuir com segurança um fator de classificação de desempenho de 90%, usando o método simples de classificação de velocidade.
Para acomodar as diferentes pausas observadas durante os ciclos de trabalho, o observador adiciona uma permissão de relaxamento de 7%, uma permissão de interferência de 5% e outra permissão especial de 8%, para um total de 20%.
Portanto, temos as seguintes variáveis conhecidas:
- Tempo médio =33 minutos
- Classificação de velocidade =90%
- Abonos =20%
Para calcular o tempo padrão, primeiro precisamos calcular o tempo normal usando o tempo médio observado e a classificação de velocidade:
Tempo normal =tempo médio X (classificação de velocidade / 100)
Tempo normal =33 x (90/100)
Tempo normal =29,7 minutos
Podemos arredondar para 30 minutos - esta é a velocidade básica em que se espera que os trabalhadores concluam a produção de um lote de placas traseiras ao trabalhar sem interrupções ou interrupções.
Em seguida, combinamos este tempo normal com as permissões para chegar ao Tempo Padrão para a produção de um lote de placas traseiras na fábrica:
Hora Padrão =Hora Normal ÷ (1 - Abonos)
Hora Padrão =30 ÷ (1 - 20/100)
Tempo Padrão =37,5 minutos
Como podemos ver nos cálculos acima, o tempo padrão gasto pelos trabalhadores na instalação para produzir um lote de placas traseiras, após levar em consideração vários fatores como classificação de velocidade e folga, é de cerca de 37 minutos e meio.
O estudo de tempo mostra várias áreas onde há espaço para melhorias. Por exemplo, os 33 minutos de tempo observado mostram que os trabalhadores não estão desempenhando - em média - em níveis ótimos. A administração pode precisar identificar as razões da ineficiência e aplicar medidas corretivas.
As concessões são outra área em que as instalações podem fazer melhorias. Cortar o subsídio de relaxamento pode ter efeitos negativos - redução do moral do funcionário, violações de conformidade (direitos do funcionário), etc. No entanto, o subsídio de interferência e o subsídio especial podem ser ajustados para melhorar ainda mais a produtividade.
A falha do equipamento é uma das causas mais comuns de interrupções no chão de fábrica. A melhor maneira de enfrentá-los é usar um sistema CMMS moderno para desenvolver uma cultura de gerenciamento de manutenção proativa.
A chave do sucesso está na melhoria contínua
Se você deseja eliminar o desperdício de seu chão de fábrica, deve adotar conceitos como manutenção enxuta e melhoria contínua.
A primeira etapa para melhorar a eficiência é adquirir pontos de dados específicos sobre as métricas de desempenho. Com máquinas, é fácil prever o desempenho. Mas os humanos que os operam são muito menos previsíveis.
Um estudo de tempo ajuda a preencher esse vazio crítico para os fabricantes. Com o advento da tecnologia moderna, agora é mais fácil do que nunca conduzir estudos precisos de tempo e movimento. Ainda assim, se você fizer isso à moda antiga, tudo que você precisa é de um cronômetro, uma prancheta e um pouco de paciência!
Manutenção e reparo de equipamentos
- Como o Coronavirus está impactando a manufatura?
- Fábrica da Bosch:como colocar as pessoas no centro da Indústria 4.0
- Explorando a planta virtual:Como o comissionamento virtual ajuda a integração do sistema
- Como a guerra comercial EUA-China pode beneficiar as PMEs
- Soluções de reparo da vida real do chão de fábrica - PLC precisa de reparos AGORA
- Como a tecnologia em nuvem facilita as melhorias do fluxo de trabalho na área de produção
- Como conduzir uma análise de gargalo
- Gemba Walk :como analisar a organização das indústrias
- Indústria:reduza o tempo de transição
- Como obter o seguro automóvel pela primeira vez?