O valor da solução de problemas da máquina
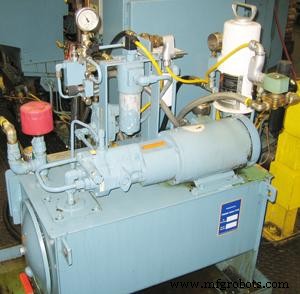
O verdadeiro problema é que a solução de problemas é essencial para qualquer fabricante se manter competitivo nos difíceis mercados de hoje. A solução de problemas rápida e eficaz da máquina é vital para evitar que as margens de lucro reduzidas como papel caiam no vermelho. Isso coloca uma enorme responsabilidade sobre os instrutores técnicos para preparar os trabalhadores para começarem a trabalhar. Já se foram os dias em que uma máquina ficava parada por longos períodos de tempo enquanto os solucionadores de problemas substituíam um componente após o outro com base em suas experiências pessoais ou conjecturas.
Uma vez que não é viável permitir que jovens solucionadores de problemas promissores levem anos para adquirir habilidades de solução de problemas no trabalho, ensinar essas habilidades em um ambiente de sala de aula é fundamental. Os futuros técnicos e operadores devem obter experiência na solução de problemas do mundo real antes de chegarem ao chão de fábrica. Portanto, instituições como faculdades comunitárias e centros de treinamento de empresas devem ser capazes de criar problemas de equipamento em muitas combinações para construir experiência em resolução de problemas. O uso de equipamento de treinamento com a capacidade de inserir uma ampla gama de falhas realistas em um sistema é fundamental para que os trabalhadores possam obter experiência prática no diagnóstico e correção de uma ampla gama de problemas vistos no mundo real. Para garantir que os procedimentos adequados sejam ensinados, um programa de treinamento de solução de problemas deve usar um currículo aprovado pelo setor que garanta que os resultados para cada trabalhador sejam consistentes.
As faculdades comunitárias e os centros de treinamento industrial estão se preparando para enfrentar esse desafio com programas voltados especificamente para o ensino de habilidades de solução de problemas. Embora esses programas possam variar em métodos de ensino, a solução de problemas eficaz, independentemente da tecnologia específica, segue cinco etapas básicas:identificar os sintomas, isolar o problema em um componente específico, testar o componente suspeito, reparar ou substituir o componente e testar o sistema.
Identificar os sintomas de uma máquina com defeito é fundamental porque pode encurtar o processo de solução de problemas, colocando o foco apenas nos componentes capazes de causar esses problemas específicos. É essencial ensinar os futuros solucionadores de problemas a pedir ao operador que identifique quaisquer sintomas observados em uma máquina com defeito. Não importa o quão bem um solucionador de problemas seja treinado, o operador que opera e monitora diariamente aquela máquina em particular está muito mais familiarizado com sua operação do que qualquer outra pessoa, e sua contribuição é muito valiosa neste estágio. Muitas vezes, os solucionadores de problemas inexperientes presumem que sabem a resposta quando, na verdade, não entendem a pergunta. Ao treinar solucionadores de problemas, é importante ensiná-los a não negligenciar esse recurso crucial. Uma vez que o operador identificou os sintomas específicos da máquina, é muito mais simples tirar conclusões úteis sobre a falha que está causando o problema.
Categorizar a falha provável com base nos sintomas concentra os esforços do solucionador de problemas em uma área significativamente menor, o que economiza tempo e dinheiro valiosos. Um solucionador de problemas bem treinado deve ser capaz de categorizar rapidamente o problema em sequência da máquina, desempenho da máquina ou problemas relacionados ao sistema. A sequência da máquina está relacionada à ordem em que os eventos ocorrem, incluindo movimentos do atuador, mudanças de pressão ou mudanças de velocidade. O desempenho da máquina se refere às características de movimento ou saída de um atuador, como velocidade ou saída de força. Os problemas relacionados ao sistema envolvem as características gerais do sistema, incluindo vibração, temperatura do fluido, pressão geral do sistema, vazamentos de fluido, etc.
Por exemplo, vamos considerar um sistema de energia de fluido para ver como categorizar a falha é útil. As falhas de sequência da máquina indicam problemas com componentes que controlam o movimento, como sensores, válvulas de controle direcional ou um controlador PLC. Por outro lado, as falhas de desempenho da máquina são comumente causadas por componentes de saída ou componentes que afetam a saída, como válvulas redutoras de pressão, válvulas de alívio ou bombas. Os sintomas que se enquadram nessas duas categorias podem limitar rapidamente os esforços de solução de problemas para áreas e peças específicas da máquina. Quando falhas relacionadas ao sistema, como vazamentos, são relatadas, elas apontam para problemas que podem causar falha da máquina. Em alguns casos, as falhas relacionadas ao sistema acompanham uma falha de sequência ou desempenho e são indicadores úteis do que pode estar causando o problema. Essa abordagem sistemática concentra rapidamente o solucionador de problemas no problema.
Uma vez que o problema é categorizado, uma metodologia de teste deve ser usada para identificar corretamente o componente com falha.
Shotgun
Cada componente ou conexão na área afetada é testado até que o problema seja localizado.
Meio-divisão
Este método testa continuamente um ponto a meio caminho entre um ponto de teste bom conhecido e um ponto de teste ruim conhecido até que o problema seja identificado.
Resultado de retorno
A abordagem output-back começa a testar as saídas do sistema e sistematicamente trabalha de volta para as entradas até que o problema seja detectado.
Sintoma e causa
Essa técnica isola o problema de acordo com a possibilidade de o componente causar os sintomas observados.
Muitos solucionadores de problemas altamente qualificados recomendam o método do sintoma e da causa como os mais eficazes. Ensinar os solucionadores de problemas a se concentrar apenas nos componentes que são capazes de causar os sintomas observados economiza tempo, razão pela qual a identificação adequada dos sintomas de uma máquina é crítica. Para que esse método seja eficaz, os solucionadores de problemas não devem apenas compreender a função de um componente, mas também como ele opera internamente para cumprir essa função.
Depois que o componente com defeito é identificado por meio de testes no circuito, ele deve ser testado fora do circuito para verificar sua falha. O teste fora do circuito isola o componente do resto do sistema e pode evitar a perda de tempo na substituição do componente errado. Um fabricante de peças afirmou que quase 70 por cento de suas peças devolvidas não estavam com defeito.
Depois que o problema for "corrigido", testar a operação do sistema é a última etapa antes de assinar o tíquete de trabalho e sair do reparo da máquina. O exemplo a seguir ilustra a importância desta etapa.
Depois que a válvula de alívio principal do sistema hidráulico foi substituída, o sistema começou a apresentar vazamentos. No entanto, depois que o pessoal de manutenção saiu, o operador da máquina tentou ajustar a válvula para a pressão adequada do sistema apenas para descobrir que isso não poderia ser feito porque a válvula de substituição errada tinha sido instalada. Isso resultou em mais tempo de inatividade e quase o dobro do custo de mão de obra para consertá-lo.
A indústria precisa de mais solucionadores de problemas. À medida que os fabricantes se esforçam para criar produtos de qualidade em menos tempo, eles enfrentam uma falta desesperada desses trabalhadores qualificados. Embora as faculdades comunitárias e os centros de treinamento estejam ensinando essas habilidades hoje, elas são necessárias em uma capacidade muito maior do que a disponível atualmente.
Manutenção e reparo de equipamentos
- O valor em tempo real da manutenção preditiva
- A História das Furadeiras
- O valor real da planta que você está comprando
- O valor da confiabilidade como um serviço
- Maximizando o valor dos dados IoT
- O valor da medição analógica
- As melhores marcas CNC
- A história do torno mecânico
- Noções básicas de fresadora
- STAEDTLER:o valor da automação na fabricação