5 causas de falha do equipamento (e o que você pode fazer para evitá-lo)
Esta postagem foi originalmente escrita como um blog convidado por Nicole Pontius da Camcode. Editado e atualizado pela equipe Fiix em junho de 2019.
- 5 causas comuns de falha de equipamento
- Causa nº 1:operação inadequada
- Causa nº 2:Falha ao realizar manutenção preventiva
- Causa # 3:Muita manutenção preventiva
- Causa # 4:Falha em monitorar continuamente o equipamento
- Causa 5:cultura de confiabilidade ruim (ou nenhuma!)
- O resultado final
Falha do equipamento acontece. O impacto disso pode variar desde facilmente corrigido com perdas mínimas até catastrófico, dependendo de fatores como custos de reparo, tempo total de inatividade, implicações de saúde e segurança e impacto na produção e entrega de serviços.
Há vários motivos comuns pelos quais o equipamento pode quebrar, e entender por que seu equipamento pode estar falhando é a sua primeira linha de defesa contra as sérias consequências de um tempo de inatividade não planejado.
Use estes sete segredos para reduzir o tempo de inatividade e vencer as falhas
Bata a falha do equipamento
5 causas comuns de falha de equipamento
Causa nº 1:operação inadequada
Há muitas pessoas que podem estar dentro e ao redor do equipamento diariamente e que podem ter um impacto significativo em suas condições gerais de operação.
Os operadores de equipamentos são um desses grupos. Eles normalmente recebem treinamento aprofundado sobre procedimentos operacionais adequados, solução de problemas básicos e melhores práticas para o uso seguro de equipamentos relevantes para as máquinas com as quais trabalharão. No entanto, pode chegar o dia em que um operador acabe trabalhando em uma máquina para a qual não foi treinado adequadamente. Às vezes, essa situação surge como resultado de falta de pessoal ou ausências inesperadas. Outras vezes, surgem emergências que exigem remediação rápida com a equipe disponível que pode não ter necessariamente o nível de especialização que os seus operadores mais experientes têm.
Uma solução para esses problemas é garantir que você tenha operadores treinados o suficiente para permitir alguma flexibilidade e um plano de contingência para emergências de falta de pessoal. Se possível, todos os seus operadores devem ter algum treinamento em cada peça do equipamento - mesmo os ativos com os quais eles normalmente não trabalham.
Mais importante ainda, nunca permita que um operador use equipamento para o qual não está qualificado. Isso não apenas ajudará a reduzir os erros operacionais, mas, em alguns setores, é fundamental para a conformidade regulamentar. A Administração de Segurança e Saúde Ocupacional (OSHA) estabelece regulamentos para requisitos de treinamento de operadores para certos tipos de equipamentos e para segurança ocupacional em geral. Depende de você, no entanto, saber os regulamentos aplicáveis ao seu setor e garantir que você tenha os procedimentos de conformidade adequados em vigor.
Causa nº 2:Falha ao realizar manutenção preventiva
A maioria dos equipamentos requer manutenção regular para um desempenho ideal, mas muitas vezes, a manutenção preventiva é a primeira tarefa a ser executada quando você está com pouca equipe e sobrecarregado. É fácil descartar a manutenção regular quando as coisas parecem estar funcionando bem, e muitas empresas partem do pressuposto de que trabalhadores experientes identificarão problemas iminentes antes que o equipamento falhe totalmente.
Dito isso, muitos dos sinais sutis de desempenho lento ou os estágios iniciais de falha não são facilmente detectáveis e muitas vezes passam despercebidos. Em outros casos, as empresas simplesmente carecem de métodos de planejamento eficientes para garantir que a manutenção contínua seja realizada. O rastreamento de equipamentos e máquinas com etiquetas de ativos pode ajudar a manter os cronogramas de manutenção em dia e os equipamentos operando com eficiência operacional máxima.
A manutenção preventiva é uma função contínua que nunca deve ser deixada de lado. Cuidar do seu equipamento com ajustes regulares irá estender a vida útil do seu equipamento, dando a você mais por cada dólar. Além disso, a manutenção preventiva pode identificar pequenos problemas com soluções baratas antes que se tornem grandes e dispendiosas avarias. Quando você usa estratégias eficazes de controle de estoque para garantir que você tenha as peças de reposição certas em estoque para as tarefas de manutenção e avarias mais comuns, o tempo de inatividade para manutenção de rotina e reparos é mínimo. Na verdade, o Departamento de Energia dos EUA estima que a manutenção preventiva resulta em:
- Redução de até 30% nos custos de energia e manutenção
- 35% a 45% menos avarias
- Reduções no tempo de inatividade em até 75%
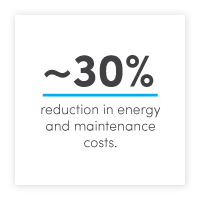
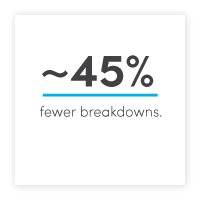
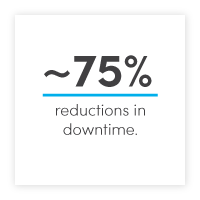
Pare de combater incêndios o dia todo com este modelo de programação de manutenção preventiva gratuita
Causa # 3:Muita manutenção preventiva
“Certamente isso é um erro”, você está pensando. “Você acabou de me dizer que NÃO fazer manutenção preventiva fará com que as coisas quebrem.” É verdade - há um pouco de uma situação Goldilocks acontecendo quando se trata de manutenção preventiva. Não o suficiente pode ser problemático pelos motivos que descrevemos acima, mas o excesso também é um grande motivo de preocupação.
Já escrevemos sobre isso antes, então confira este blog se quiser se aprofundar no conceito de avarias pós-manutenção. Mas aqui estão as Notas de Coles:Cada vez que você entra em uma máquina para mantê-la, você abre aquele equipamento para um conjunto completo de riscos e, com o tempo, esses riscos podem se agravar e levar à falha.
PMs insuficientes
Sinais de falha precoce são perdidos
Os cronogramas de manutenção sofrem
Eficiência reduzida do equipamento
A vida útil do ativo diminui
Avarias e aumento do tempo de inatividade
Os custos disparam
PMs suficientes
Os custos são controlados
A entrega just-in-time é alcançada
O tempo de inatividade foi cortado
A eficiência do técnico é impulsionada
Melhora a segurança
A produtividade de ativos críticos é otimizada
Muitos PMs
Gastos excessivos aumentam
O desgaste dos ativos aumenta
O tempo do técnico é desperdiçado
Inventário desnecessário é usado
Informações imprecisas são coletadas
Certifique-se de não fazer muitos PMs com este modelo de registro de manutenção
Pense nisso em termos de cirurgia - um bypass triplo é uma operação que salva vidas. Mas você não quer se submeter a cirurgia cardíaca aberta regularmente simplesmente porque alguns anos se passaram ou porque seu coração bateu alguns milhões de vezes. Mas, com frequência, é exatamente assim que abordamos a manutenção preventiva. É feito em um cronograma predefinido (geralmente com base no tempo ou uso), sem levar em consideração a condição operacional real do ativo.
O que nos leva a ...
Causa # 4:Falha em monitorar continuamente o equipamento
Então, como você encontra o equilíbrio certo de manutenção preventiva? A cura aqui é simples no conceito, mas um pouco mais complexa na execução:manutenção baseada em condições. Esta é a manutenção que é feita com base na condição de operação de uma peça do equipamento, em vez de apenas uma programação "configure e esqueça". Ele leva muitas coisas em consideração, desde o histórico de informações do fabricante do equipamento até dados em tempo real, como análise de vibração.
O monitoramento contínuo depende dos dados do sensor para estabelecer uma linha de base de como são as boas condições do equipamento, a fim de detectar mudanças sutis, que podem ser usadas para prever quebras e falhas. Isso permite mais tempo para o planejamento de contingência e programação do tempo de inatividade para minimizar as interrupções da produção. Este tipo de monitoramento e os dados que são coletados no processo podem ajudar as empresas a identificar as causas do aumento do estresse nas máquinas e ajustar as cargas de trabalho e cronogramas para diminuir a carga no equipamento, mostrando indicadores iniciais de falha iminente.
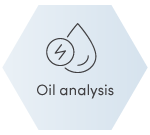
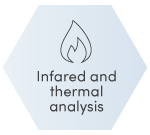
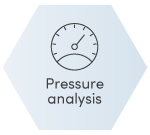
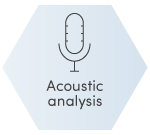
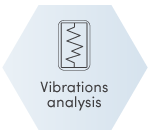
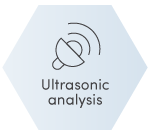
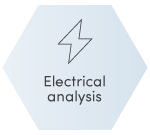
Prepare-se para cada falha em seus ativos críticos com este modelo FMEA
O problema aqui é que isso é realmente muito difícil de fazer se você estiver gerenciando a manutenção com caneta e papel ou Excel. Se é aqui que você deseja que suas operações de manutenção cheguem, pode ser hora de considerar a mudança para uma solução de manutenção digital.
Quando usar o monitoramento baseado em condição
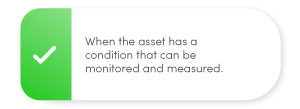
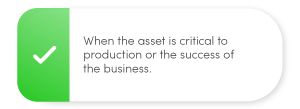
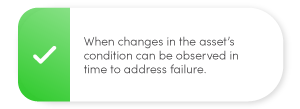
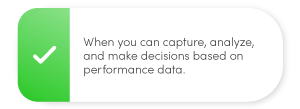
Causa # 5:cultura de confiabilidade ruim (ou nenhuma!)
Todo mundo já esteve lá - a grande pressão do topo significa que não há um segundo a perder se você tem alguma esperança de atingir seus objetivos de produção. Nessas circunstâncias, pode ser tão tentador (e tão fácil) para um operador ou trabalhador de manutenção perceber que algo não está funcionando a 100%, colocar um band-aid e dizer:"Vou descobrir isso quando as coisas se acalmarem baixa". O problema é que, realisticamente, as coisas nunca se acalmam a ponto de você ter tempo para revisitar esse trabalho. O que significa que a solução band-aid torna-se uma solução semipermanente até parar de funcionar e se tornar uma falha completa.
Um bom exemplo disso é a Boeing. Você provavelmente está familiarizado com os dois acidentes mortais envolvendo a aeronave 737 Max da empresa, o que levantou questões sobre se a pressa da Boeing para colocar o avião em produção levou a empresa a assumir riscos de segurança que acabaram resultando nos acidentes.
Mas a história mais tranquila diz respeito a um modelo de avião diferente - o 787 Dreamliner. Vários denunciantes se apresentaram para dar o alarme sobre os Dreamliners, que foram fabricados em 2009 em uma fábrica então nova perto de Charleston, na Carolina do Sul. Desde o início, a produção desleixada foi um problema que foi consistentemente varrido para debaixo do tapete em favor de cronogramas de produção agressivos.
Se você quiser a história completa, verifique o artigo completo do New York Times aqui (ou o podcast relacionado do Daily se você gosta de áudio). Mas, para encurtar a história, os problemas da Boeing são um exemplo realmente bom de pressão competitiva nos níveis mais altos de uma empresa, tendo um efeito cascata em toda a cadeia de comando, até o chão de fábrica. A má cultura no topo cria uma mentalidade de "faça tudo rápido" que pode resultar em omissões devastadoras, soluções de band-aid e erros.
E daí se a má cultura estiver na raiz da falha do seu equipamento? O que você pode fazer? Cobrimos o tópico de como começar a estabelecer uma cultura que está focada na confiabilidade, então vá em frente e verifique uma (ou todas!) Dessas peças para obter uma base sólida em confiabilidade.
O resultado final:operadores treinados, uma sólida programação de PM e um foco na cultura de confiabilidade são seus ingressos para um futuro sem falhas (ou pelo menos menos falhas)
Os equipamentos podem ser imprevisíveis e podem ocorrer falhas. As pessoas cometem erros, as peças envelhecem e, às vezes, a manutenção preventiva é apenas o que falta em um dia já agitado. Mas, garantindo o treinamento adequado do operador, executando a manutenção preventiva ou baseada na condição no momento certo e trabalhando em prol de uma cultura geral melhor, você terá uma chance muito melhor de manter seu equipamento funcionando em ótima forma.
Manutenção e reparo de equipamentos
- Manutenção autônoma:o que é e por que é importante
- O que é confiabilidade e gerenciamento de ativos?
- O que constitui manutenção e confiabilidade de classe mundial?
- A morte do departamento de manutenção e o que podemos fazer a respeito
- O que você pode fazer para aprimorar a manutenção e a confiabilidade?
- Principais causas de falha de máquina e como evitá-las
- O que é uma queda de pressão e como evitá-la?
- 4 dicas de manutenção para prolongar a vida útil do equipamento e o ROI
- O que é executar até a falha e o RTF é sempre ruim?
- Instalação e manutenção industrial