Minimizando o impacto da manutenção programada nas operações comerciais
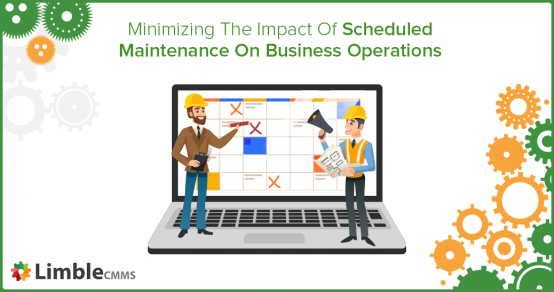
A maioria dos ativos físicos deve passar por manutenção de rotina para lidar com o desgaste devido às operações regulares. Em outras palavras, a manutenção programada deve fazer parte do fluxo de trabalho regular em qualquer instalação .
O lado negativo da manutenção programada é que às vezes pode interromper as operações normais de negócios. O principal exemplo é não poder usar uma determinada peça do equipamento enquanto ele está passando por uma manutenção programada.
Portanto, é importante saber como programar o trabalho de manutenção de uma forma que cause o mínimo de impacto na produtividade e na disponibilidade geral do sistema.
O que é manutenção programada?
A manutenção programada refere-se a qualquer trabalho de manutenção pré-planejado que deve ser concluído dentro de um certo tempo. Muitas vezes, essas são atividades de manutenção de rotina, como filtros de ar ou trocas de óleo, que se repetem em intervalos regulares.
Dito isso, a manutenção programada pode ser iniciada como uma resposta a um tíquete de manutenção. Nesses casos, o tempo de inatividade para manutenção deve ser planejado com antecedência. O planejamento incluirá o processo de manuseio de materiais, alocação de ferramentas e peças, designação de técnicos e cronograma de manutenção.
A manutenção programada pode ou não incluir o tempo de inatividade planejado. Algumas atividades de manutenção, como monitoramento de vibração pode ser feito em máquinas em operação ativa. Outros, como rebobinar um motor elétrico , exigirá o desligamento do equipamento.
O impacto da manutenção programada nos negócios
Como mencionamos na introdução, a manutenção programada pode interromper as operações regulares, a menos que um planejamento prudente seja feito.
Quando a máquina está em manutenção, ela pode criar um gargalo. O backup dos processos upstream é feito devido ao gargalo, enquanto os processos downstream estão ociosos. Todos podemos concordar que esta não é uma forma eficiente de utilizar os recursos da planta.
Devido à natureza de suas operações, algumas indústrias podem lidar com a manutenção programada sem qualquer impacto visível na disponibilidade do sistema.
O principal exemplo é a indústria de TI. No modelo moderno de nuvem de manutenção de infraestrutura, os provedores de IaaS conduzirão as tarefas de manutenção sem interferir nas operações ativas do sistema de TI.
As operações ao vivo serão transferidas para uma máquina redundante ou livre. Esse tempo pode ser utilizado para fazer o trabalho de manutenção na máquina original. A vantagem é que o trabalho de manutenção pode ser realizado sem afetar as operações regulares do produto de TI. A desvantagem é o custo de aquisição e manutenção de equipamentos redundantes.
Porcentagem crítica de manutenção programada (SMCP)
A porcentagem crítica de manutenção programada é uma ferramenta usada para determinar a prioridade de diferentes tarefas programadas. Todas as tarefas necessárias podem não ser concluídas dentro do tempo alocado para manutenção. Os técnicos devem escolher entre as diferentes tarefas de acordo com sua prioridade, que pode ser calculada usando a fórmula SMCP:

O SMCP é calculado para processos de manutenção que são repetidos em um intervalo constante. O número de dias no ciclo de manutenção representa este intervalo de manutenção regular. O número de dias de atraso é o número de dias desde que o processo de manutenção deveria acontecer.
Em outras palavras, o SMCP é um método empírico para quantificar o quão crítica é cada tarefa de manutenção. Ele pode ser usado para identificar e descartar o trabalho de baixa prioridade para concluir as tarefas de manutenção mais críticas.
Programação de manutenção com impacto mínimo nas operações de negócios
Os cronogramas de manutenção podem ser criados com base em:
- Diretrizes do OEM (programação de manutenção recomendada pelo fabricante)
- condições operacionais atuais das máquinas
- dados de manutenção anteriores e experiência
Se você olhar com atenção, verá que as programações de manutenção são tão precisas quanto as informações nas quais se baseiam. A previsão de falha da máquina não é uma ciência exata - portanto, programar o trabalho projetado para evitá-lo também não pode ser.
As estratégias e ferramentas de manutenção modernas são muito boas para detectar e prever falhas. No entanto, eles ainda têm uma barreira de entrada bastante alta por causa de seus requisitos técnicos e custos iniciais.
Vamos dar uma olhada em algumas maneiras diferentes em que as organizações podem programar a manutenção de uma forma que não interfira nas operações normais de negócios.
Usando o CMMS para planejar e organizar o trabalho de manutenção
Os sistemas computadorizados de gerenciamento de manutenção ajudam as empresas a planejar, automatizar e otimizar todas as tarefas relacionadas à manutenção, independentemente do setor.
Pode ser usado para:
- gerenciar solicitações de trabalho de manutenção recebidas
- rastrear e prever as necessidades de estoque de MRO
- ajude os planejadores de manutenção a ter uma visão geral dos recursos disponíveis e a criar cronogramas de manutenção eficientes
- acessar instantaneamente SOPs, listas de verificação e registros de manutenção, reduzindo o tempo que os técnicos precisam para solucionar problemas de equipamentos e realizar outras tarefas de manutenção programada
- visualizar e gerenciar o trabalho agendado por meio do calendário de manutenção
- e muito mais
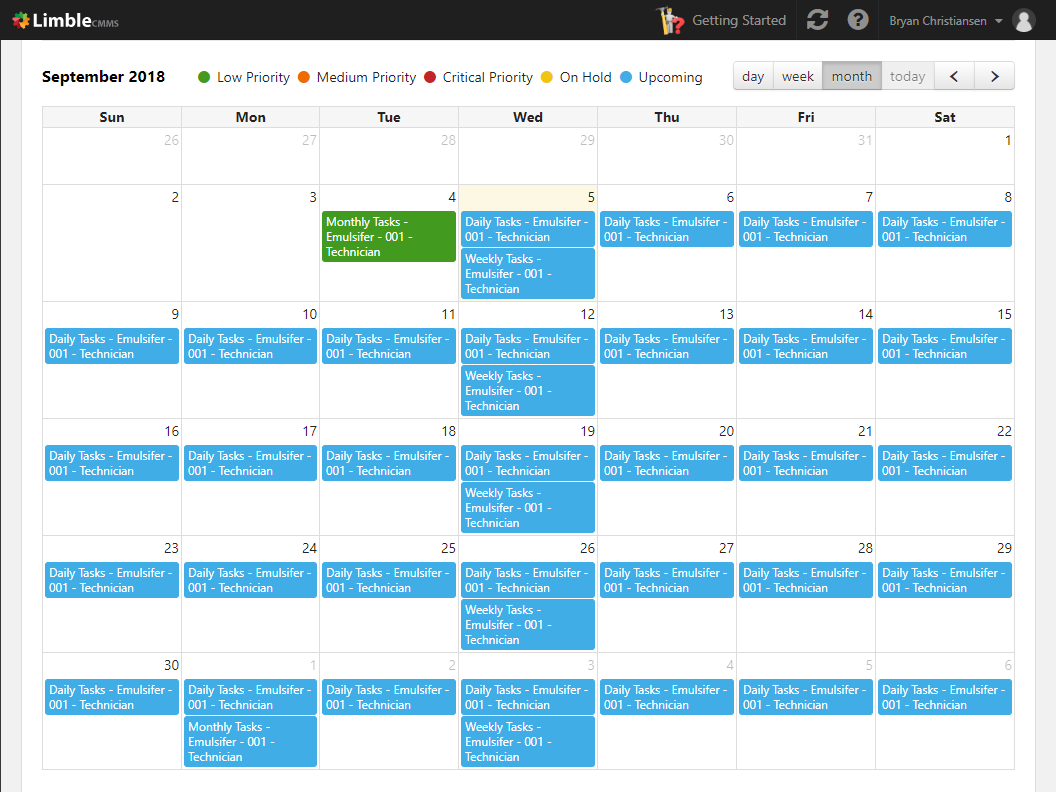
Instantâneo de um calendário de manutenção no Limble CMMS
Visão geral das tarefas de manutenção programada dentro do Limble CMMS
O CMMS atua como o repositório central para todas as atividades de manutenção. Os sistemas CMMS modernos são baseados em nuvem para que os dados possam ser acessados de qualquer lugar. Com ele, os dados de manutenção não estão apenas disponíveis, são muito mais precisos do que planilhas do Excel e logs de papel.
Todas as tarefas de manutenção programadas que surgem de novas ordens de serviço podem ser alocadas automaticamente a um técnico específico - levando em consideração os cronogramas de trabalho existentes e a disponibilidade de ferramentas / peças.
Isso é extremamente útil para grandes operações de manufatura, pois permite que os planejadores de manutenção coordenem o trabalho de manutenção planejada com os planejadores de produção e outros departamentos afetados.
Usando o SMCP para priorizar o trabalho de manutenção
O SMCP de um processo está diretamente relacionado a quão tarde a manutenção foi e quão crítica é a manutenção do maquinário. Isso pode ser calculado para todas as tarefas de manutenção que precisam ser concluídas dentro do prazo estipulado.
As tarefas de manutenção com SMCP mais alto têm prioridade e são concluídas primeiro. Se algo precisa acabar em uma lista de pendências de manutenção adiada, as tarefas serão menos importantes.
Redução do tempo de inatividade planejado por meio de treinamento e padronização
Os Procedimentos Operacionais Padrão (POPs) são criados para reduzir a variação no desempenho quando diferentes técnicos executam a mesma tarefa. Técnicos treinados com acesso a POPs e listas de verificação podem desempenhar suas funções prontamente, sem se atrapalharem entre os diferentes manuais. Isso reduz o tempo necessário para concluir as tarefas de manutenção programadas.
Processos padronizados também diminuem o número de erros humanos. Isso evita a necessidade de reprogramação devido à supervisão de um técnico. A vantagem disso é dupla. Isso evita outro tempo de inatividade e elimina problemas que surgem de um trabalho defeituoso.
Claro, isso importa pouco se a pessoa que executa o trabalho não for devidamente treinada ou não tiver acesso às ferramentas de manutenção certas.
Reduzindo a manutenção excessiva com monitoramento de condição e análise preditiva
Menos tarefas de manutenção programadas =menos potencial para interromper as operações de negócios.
Desde o início da manutenção preventiva, os planejadores de manutenção procuram maneiras de otimizar seus planos de manutenção preventiva. Qual é a menor quantidade de trabalho de manutenção que posso programar e, ao mesmo tempo, evito quebras de equipamento?
O monitoramento de condição, juntamente com a manutenção preditiva, permite que você elimine a manutenção excessiva, mantendo um pulso constante sobre a condição de seus ativos críticos. Você pode agendar apenas as tarefas necessárias - exatamente quando são necessárias - sem comprometer a integridade ou o desempenho dos ativos.
Usando sensores e análises preditivas, a equipe de manutenção já terá uma boa ideia do que deu errado e que tipo de trabalho precisa ser executado. Terá bastante tempo para alocar recursos (ferramentas, peças, mão de obra) e ajustar o trabalho necessário aos cronogramas de manutenção e produção existentes.
Resumo
A manutenção programada é uma atividade crítica para qualquer negócio que dependa da alta disponibilidade de seus ativos físicos. Ao mesmo tempo, a realização de um trabalho de manutenção excessivo pode afetar negativamente a produtividade, a entrega de serviços e os resultados financeiros.
É imperativo minimizar os impactos negativos dos processos de manutenção programada. Isso pode ser feito estabelecendo a prioridade das tarefas com a ajuda do SMCP, o uso eficaz de um sistema CMMS e contando com análises preditivas e automação de dados para melhorar o planejamento e programação da manutenção.
Manutenção e reparo de equipamentos
- A Evolução da Manutenção Industrial
- 4 maneiras pelas quais a lacuna de habilidades de fabricação pode impactar seus negócios
- A manutenção de quatro maneiras mudará o jogo para os negócios modernos
- Compreendendo os benefícios da manutenção preditiva
- A Evolução da Prática de Manutenção
- Operações + Manutenção =Produção
- O Gerente de Manutenção Profissional:Um Trabalho em Andamento
- A questão da manutenção do contrato - Parte I
- Nas mentes da manutenção
- O impacto da automação na confiabilidade do equipamento