Entenda a falha do equipamento - para que você possa evitá-la
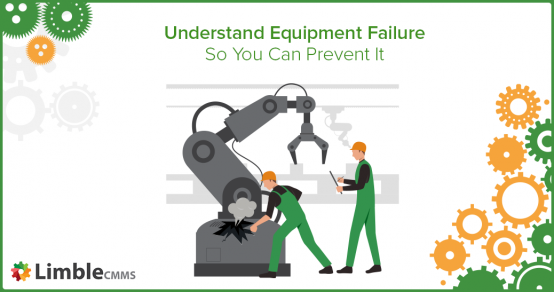
A falha do equipamento é um fenômeno comum no ambiente industrial. Isso pode resultar em custos de reparo mais altos, tempo de inatividade da produção, implicações para a saúde e segurança dos trabalhadores e afetar a produção e a entrega de serviços. A Sociedade Internacional de Automação indica que as fábricas perdem de 5% a 20% de sua produtividade devido ao tempo de inatividade - o equivalente a milhares e até milhões de dólares em alguns casos.
A implementação de uma defesa contra falhas e o tempo de inatividade subsequente requerem um entendimento completo das falhas da máquina e seus mecanismos. Isso inclui a análise das causas das falhas e suas consequências, para que possamos planejar estratégias de mitigação adequadas.
Uma definição rápida de falha de equipamento
Simplificando, a falha do equipamento é a condição na qual uma peça do equipamento não funciona como planejado. Com base na gravidade do problema e na funcionalidade do equipamento, podemos diferenciar entre duas grandes categorias:
- falha completa
- falha parcial
Qualquer evento que leva a uma perda total de valor do equipamento é uma falha completa e um evento que leva a uma perda parcial de valor representa uma falha parcial.
A falha completa é fácil de reconhecer, pois torna o ativo praticamente inutilizável. Exemplos comuns de falha completa do equipamento incluem rupturas de vaso, tubo ou válvula, quebras de motor, quebra de uma hélice em uma turbina, caldeira grave ou mau funcionamento de HVAC, falha de rolamento, etc.
Pode haver algumas condições quando o equipamento opera funcionalmente, mas só pode atender parcialmente ao desempenho pretendido. Isso é um sinal de falha parcial . Por exemplo, devido ao mau funcionamento do controle de velocidade do motor, a correia transportadora opera em uma velocidade mais lenta, levando à falha de sincronização da planta.
Outros exemplos de falha parcial incluem problemas como desgaste, corrosão, filtros de ar sujos, falta de lubrificação adequada e ocorrências semelhantes. Em muitos casos, basta realizar a manutenção corretiva para retornar a máquina à condição ideal de funcionamento.
As falhas vêm em vários graus e você não pode pegá-las todas. No entanto, com as ferramentas certas e uma abordagem proativa para manutenção, a maioria pode ser evitada e tratada antes que levem a problemas sérios e causem paralisações dispendiosas.
Causas comuns de falha de máquina e medidas preventivas
Não existe uma estratégia universal para evitar falhas de equipamento. A estratégia de prevenção de falhas deve ser projetada de forma diferente para diferentes equipamentos, operando dentro de seu contexto e definição de seu valor esperado.
Existem várias estratégias de manutenção disponíveis para evitar falhas na máquina, como manutenção preventiva, manutenção baseada na condição e manutenção preditiva. Escolher o caminho certo depende de muitos fatores e geralmente é uma compensação entre o investimento necessário e alcançar os objetivos de confiabilidade, disponibilidade, manutenção e segurança (RAMS).
Existem várias razões por trás das avarias de equipamento, que às vezes podem parecer imprevisíveis. Vários motivos podem fazer com que a máquina falhe ou tenha um desempenho inferior. A seguir estão algumas das causas mais frequentes de falha da máquina e dicas sobre como evitá-las.
1) Desgaste regular e rasgo
É a causa mais comum e ocorre em todos os tipos de equipamentos. O uso repetido de máquinas, mesmo seguindo as melhores práticas, acabará por levar ao desgaste (também conhecido como "fadiga do metal"). Vários motivos podem acelerar a falha do maquinário, como más condições de operação, falta de manutenção de rotina, uso impróprio e más condições de armazenamento. Quando deixado sem solução, o dano que ocorre devido ao uso e desgaste pode ser catastrófico.
Como evitá-lo
Uma das idéias comuns de prevenção do desgaste em máquinas rotativas é a lubrificação. A lubrificação regular das peças da máquina reduz o atrito nos elementos móveis e controla o desgaste e rasgos desnecessários nas máquinas. Para outros tipos de equipamentos, inspeções periódicas e manutenção preventiva / preditiva das peças da máquina, incluindo a substituição de correias, mangueiras, rolamentos, filtros, limpeza de poeira e sujeira e atenção aos contaminantes, também podem reduzir ainda mais a probabilidade de falha da máquina causado pelo desgaste.
2) Falta de manutenção de rotina e preventiva
Devido aos orçamentos limitados, muitas organizações ainda estão usando a manutenção de avarias. Embora essa abordagem funcione para alguns equipamentos, eles não são adequados para equipamentos complexos e críticos. A falta de manutenção de rotina e preventiva leva a enormes acúmulos de manutenção adiada - e todos os problemas operacionais e custos que vêm com isso.
A manutenção preventiva baseada no tempo também não é uma solução perfeita. Dependendo do mecanismo de falha, o equipamento tende a falhar com mais frequência à medida que se aproxima do fim da vida útil. Como a maior parte do equipamento é mantida em intervalos regulares fixos ao longo de sua vida útil, muitas vezes tende a ter manutenção insuficiente em estágios posteriores do ciclo de vida de seu ativo.
Como evitá-lo
Como você pode imaginar, implementar uma estratégia de manutenção proativa é uma solução para esse problema. A maneira mais fácil de fazer isso é usar um CMMS, pois ele o ajudará a gerenciar todos os recursos que precisam ser gerenciados com uma estratégia proativa - ativos, ordens de serviço, calendários, programações, fornecedores e estoque.
É muito mais fácil liderar uma equipe de manutenção organizada quando você tem todas as informações necessárias em um só lugar.
3) Uso impróprio e erros do operador
O erro do operador / humano é definido como a causa de consequências inesperadas devido à distração, más decisões, desvio do processo real (fazer tarefas extras ou não seguir a sequência de tarefas). Isso pode causar vários problemas que variam de tempo de inatividade operacional a graves incidentes de segurança.
Como evitá-lo
O treinamento do operador da máquina é uma das ferramentas mais eficazes para evitar o uso impróprio ou manuseio incorreto. A maioria das indústrias definirá um nível mínimo de treinamento necessário para diferentes ativos. Eles também podem procurar emitir certificados de treinamento para manter o nível desejado de competência para operar máquinas específicas.
Embora isso aconteça com menos frequência, uma peça do equipamento também pode ser danificada durante o processo de manutenção. Muitas organizações criam manuais de operação e manutenção, SOPs e listas de verificação para que qualquer pessoa que interaja com o equipamento saiba exatamente o que fazer.
4) Fraca cultura de confiabilidade
Em algumas organizações, o gerenciamento pode ter uma definição distorcida de confiabilidade da planta. Eles podem ver qualquer planta, onde uma peça do equipamento é imediatamente consertada em caso de falha, como confiável. Embora uma solução rápida possa melhorar a disponibilidade da planta e o MTTR - não é um bom reflexo da confiabilidade da planta.
Além disso, devido às limitações de orçamento, algumas empresas hesitam em investir na melhoria da cultura de confiabilidade, não vendo os benefícios imediatos que tem na gestão de ativos. Isso ocorre porque a melhoria da confiabilidade é um benefício de longo prazo, então pode demorar um pouco para ver um ROI significativo. Como muitas organizações de pequeno e médio porte também carecem de hábitos de planejamento de longo prazo, elas não conseguem entender o verdadeiro benefício de incorporar uma cultura orientada para a confiabilidade.
Como lidar com isso
Existem muitas soluções de melhoria de confiabilidade eficientes e econômicas disponíveis no mercado. Uma das soluções eficazes é um CMMS móvel moderno. Ele oferece uma melhoria substancial para empresas de manufatura e as ajuda a abraçar uma transformação em sua cultura de confiabilidade. As organizações que estão presas à mentalidade reativa terão que se esforçar mais no gerenciamento de mudanças para colocar sua organização no caminho certo.
Departamentos que estão seriamente interessados em melhorar seus esforços de confiabilidade devem olhar para técnicas como RCM, RCA e FMEA. Eles podem ajudá-los a avaliar os modos de falha comuns para ativos específicos e decidir qual estratégia de manutenção deve ser aplicada a cada ativo.
Gerencie e evite falhas de equipamento com um CMMS moderno
O CMMS pode ser facilmente implantado para simplificar, automatizar e organizar tarefas de manutenção preventiva e preditiva. Afinal, seu principal objetivo é ajudar as organizações a serem proativas.
Aqui está uma lista de maneiras pelas quais o CMMS pode ajudar a gerenciar e prevenir falhas na máquina:
- ajuda os gerentes e supervisores a desenvolver programações de manutenção de rotina
- possui um calendário de manutenção para facilitar o rastreamento e gerenciamento de tarefas recebidas
- mantém os técnicos responsáveis pelo trabalho de manutenção executado
- ajuda a monitorar e planejar o estoque de peças sobressalentes
- pode servir como um repositório centralizado para histórico de manutenção, SOPs, listas de verificação, procedimentos de segurança e outras diretrizes para gerenciamento de ativos
- pode ser integrado à tecnologia de monitoramento de condição para acionar ordens de serviço automaticamente com base em dados em tempo real
- no pior cenário, pode ajudá-lo a otimizar e coordenar a manutenção de emergência e outros tipos de trabalho reativo, com base em sua prioridade
Esta não é, de forma alguma, uma lista exaustiva do que o CMMS pode fazer, apenas das coisas que estão intimamente ligadas à manutenção preventiva de equipamentos.
Principal lição
Mesmo sem ler este artigo, a maioria dos profissionais de manutenção está ciente de que a falta de manutenção preventiva é a fonte da maioria de suas dores de cabeça. Embora não gostemos de falar mal, a solução é óbvia - implemente um CMMS e use-o como base para o desenvolvimento de um plano de manutenção preventiva.
Mesmo se o orçamento for apertado, o software de manutenção moderno não é particularmente caro e fornece um bom ROI que não afetará seus resultados financeiros de forma significativa. Para obter mais informações sobre os preços do Limble CMMS ou como iniciar um teste, clique aqui.
Manutenção e reparo de equipamentos
- Se a Bosch pode fazer, você também pode
- FRACAS:Como tornar a falha do equipamento seu amigo
- Como um programa PM pode reduzir o tempo de inatividade
- Com que frequência você deve inspecionar o equipamento?
- Fabricação flexível e confiabilidade podem coexistir
- Modos de falha dos processos de confiabilidade do equipamento
- 5 causas de falha do equipamento (e o que você pode fazer para evitá-lo)
- Por que você deve escolher equipamento industrial recondicionado
- O que você pode esperar de nossos amplos serviços de reparo de equipamentos
- 7 maneiras de prevenir acidentes com equipamentos