Como um programa PM pode reduzir o tempo de inatividade
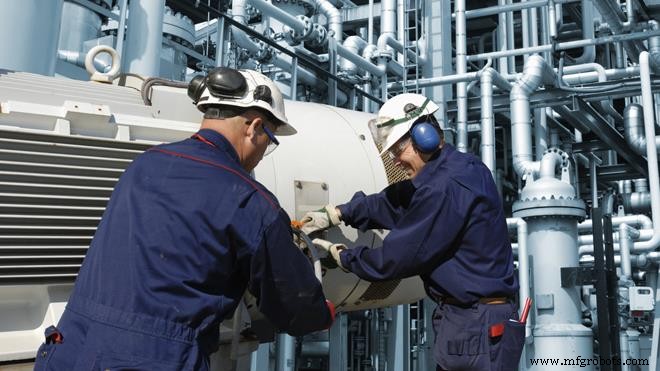
Vou ilustrar com um exemplo. Em uma grande fábrica de papel e celulose com várias linhas, uma válvula de guilhotina de 20 polegadas no coletor de efluente principal falhou, interrompendo toda a operação por três dias. Quando fabricado, o garfo da válvula de aço inoxidável foi preso ao corpo da válvula com pontos de solda. Essas soldas falharam, provavelmente por fadiga. A pressão forçou a pá para fora da válvula e o efluente de 180 graus que escapou submergiu as bombas elevatórias de efluente que alimentam o sistema de tratamento.
Essa falha poderia ter sido evitada se o sistema de manutenção preventiva tivesse sido melhor projetado? Não poderia, pelo menos não economicamente em uma planta de processo como uma fábrica de papel. O raciocínio era que, se o escopo do programa de inspeção de PM incluísse verificações regulares em itens como soldas de fábrica dos fabricantes em todos os equipamentos da fábrica, bem como outras verificações possíveis com esse nível de detalhe, então seria irrealisticamente caro. As inspeções de PM para essa planta devem ser limitadas aos modos de falha prováveis na maioria dos equipamentos. Este evento não foi resultado de um provável modo de falha.
Quando o tempo de inatividade na planta foi analisado ao longo de vários anos, as perdas totais dos modos de falha "provável" e "improvável" foram quase iguais. As falhas improváveis foram menos frequentes, mas cada uma resultou em uma grande perda de produção.
Obviamente, a profundidade até a qual é razoável (e econômico) buscar falhas potenciais depende da criticidade do equipamento, definida como a consequência da falha. Por exemplo, durante o projeto e a manutenção de aeronaves comerciais, todos os modos de falha possíveis para cada componente são examinados e ações são tomadas para prevenir a falha ou impedir que uma falha afete a segurança da aeronave (por exemplo, fornecendo back-up sistemas). Essa análise em uma grande operação de manufatura geralmente não é econômica ou necessária. No entanto, para sistemas muito críticos, como aqueles que contêm produtos químicos perigosos, um processo de design muito mais rigoroso e um nível correspondentemente mais alto de detalhes de inspeção são justificados.
Portanto, que ação deve ser tomada quando ocorre uma falha improvável? Uma possibilidade é estender o programa PM para incluir esse modo específico de falha em todos os equipamentos semelhantes. Isso só é prático se o período de desenvolvimento de falha para cada modo de falha for longo o suficiente para permitir inspeções regulares para detectar uma falha potencial com aviso suficiente para que os reparos sejam feitos antes que ocorra uma falha.
A melhor maneira de lidar com falhas improváveis é conduzir uma análise da causa raiz e tomar todas as medidas necessárias para evitar falhas semelhantes no futuro. Isso geralmente envolve alguma reformulação. No caso do exemplo da válvula, a fixação da culatra da válvula ao corpo da válvula foi reprojetada para evitar mais falhas.
Design do programa PM
Se o programa PM for bem projetado, a maioria dos modos de falha "prováveis" podem ser evitados com um tempo de desenvolvimento de falha razoável.
Bons registros de tempo de inatividade são de grande valor ao configurar um programa de PM. Depois que uma fábrica registrou todas as perdas de produção contra o equipamento que as causou, uma análise de Pareto revelou que 80 por cento de todo o tempo de inatividade não programado para manutenção pode ser atribuído a 87 itens, ou menos de 1 por cento de mais de 12.000 itens de equipamento. Um novo programa de PM com foco nesses 87 itens e equipamentos semelhantes reduziu o tempo de inatividade não programado para manutenção em mais de 50 por cento em 18 meses.
Em uma planta de processo, como uma fábrica de celulose e papel, as inspeções de PM não devem consumir mais do que 15-20 por cento da mão de obra de manutenção disponível. Também é uma boa "verificação do sistema" para comparar ocasionalmente o total de horas de trabalho geradas por seu programa de PM a cada ano com sua mão de obra total disponível.
Manutenção e reparo de equipamentos
- Como construir um programa de manutenção elétrica
- Como o programa baseado em confiabilidade melhora a segurança?
- Como sustentar a mudança em um programa de confiabilidade
- Como iniciar um programa de confiabilidade
- Como os gerentes de manutenção podem melhorar seu programa de saúde e segurança
- Como a automação pode reduzir o desperdício na cadeia de abastecimento alimentar
- Como reduzir o uso de energia na fabricação
- Como a medição de alto desempenho pode reduzir os custos de ferramentas
- A programação de manutenção preventiva eficaz pode reduzir o tempo de inatividade?
- Como a documentação atualizada pode reduzir as não conformidades?