Removendo obstáculos para otimizar processos de moagem recém-instalados
Geralmente novas linhas de alto volume que produzem peças complexas que incluem processos de retificação, como motor automotivo ou lâmina e palheta de motor aeronáutico, passam por vários estágios, desde a aquisição da máquina até a produção real, conforme descrito na Figura #1. Se essas linhas incluírem um processo considerado “alto risco ” será agendado com “tempo de desenvolvimento” como parte da avaliação e compra da capacidade do moedor (etapas 4 e 5) por teste e refinamento. Esta é uma estratégia eficaz e reduz substancialmente os problemas associados ao lançamento do programa, mas pode ser demorado e caro; muitas vezes, as amostras de peças podem nem estar disponíveis ou são protótipos sujeitos a alterações adicionais de design. Nesses casos ou para designs de componentes diferentes, mas não radicalmente diferente dos projetos existentes, o “tempo de otimização” raramente é programado antes da qualificação real da máquina.
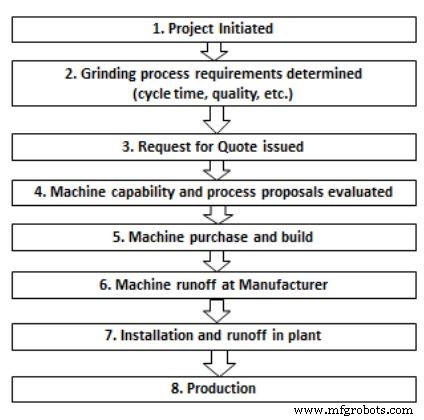
Quando as máquinas são qualificadas e instaladas com “não-radical ” processos, o foco está na qualidade da peça e no tempo de ciclo. As especificações da roda podem ser selecionadas para garantir a mais alta qualidade em meio às incertezas do novo projeto da peça e seu impacto na manutenção das tolerâncias das peças para especificações CpK muitas vezes mais rigorosas do que as exigidas para a produção. Além disso, devido ao custo ou disponibilidade, muitas vezes apenas 50 ou 100 peças são fornecidas para qualificação, tornando questionável o estabelecimento de um processo estável a longo prazo. Normalmente, não há muito tempo ou componentes para otimizar o custo de ferramental ou abrasivo por peça. Após a instalação, em muitos casos, uma atitude “se não está quebrado, não conserte” assume o controle e os processos ficam bloqueados. A otimização raramente é tentada.
Portanto, é muito importante que a “etapa extra” de otimização seja considerada como uma “auditoria” final do processo. Na maioria das vezes, essa etapa pode ser simplesmente uma "ajuste" do processo para que a requalificação de todo o processo não seja necessária, mas ocasionalmente oportunidades grandes o suficiente podem ser descobertas, o que justificaria grandes mudanças no ciclo e/ou na especificação da roda. A análise de custo/benefício seria realizada para determinar se uma mudança de processo mais substancial deveria ser feita.
Existem várias razões pelas quais a falta de “tempo de otimização” pode causar processos abaixo do ideal:
- Os ciclos podem funcionar de forma aceitável na máquina, mas não são "amigáveis para rodas". ou seja, a vida útil da roda pode ser inferior à ideal
- A tecnologia das rodas evolui. As estimativas feitas com a tecnologia existente podem não ser ideais para a nova tecnologia
- As variações sutis na configuração das peças, no projeto da máquina e nos requisitos de qualidade tornam a otimização do processo muito difícil fora da linha de produção. Isso porque a linha de produção fornece muitas peças e um ambiente com variações reais e metrologia. Essas duas qualidades fornecem um teste de "robustez" do processo "otimizado".
Exemplos:
O ciclo de moagem mostrado na Figura 2 foi enviado do OEM instalado em uma fábrica e está atualmente em produção. Este ciclo funciona bem e produz peças aceitáveis, mas não é “amigável às rodas”.
A "antipatia" da roda deste ciclo se deve ao grande pico (potência/força) no início do ciclo. O desgaste do rebolo é proporcional ao quadrado da força de retificação, forças altas farão com que o rebolo se desgaste rapidamente. Nesse caso, reduzir o avanço rápido e aumentar o avanço médio prolongaria a vida útil da roda, mantendo o tempo de ciclo e a qualidade da peça.
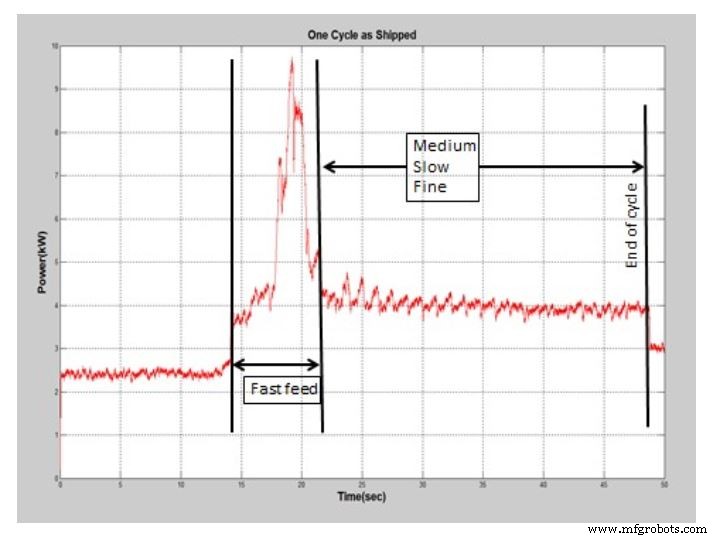
Um ciclo em processo de otimização
Em um caso incomum recente, o fabricante concordou em fazer a otimização "in situ" do processo de moagem. Inicialmente, o ciclo de retificação foi alterado para torná-lo mais "amigável ao rebolo", conforme discutido acima. Neste caso, o ciclo mais amigável também foi ~5 segundos mais curto que o ciclo inicial.
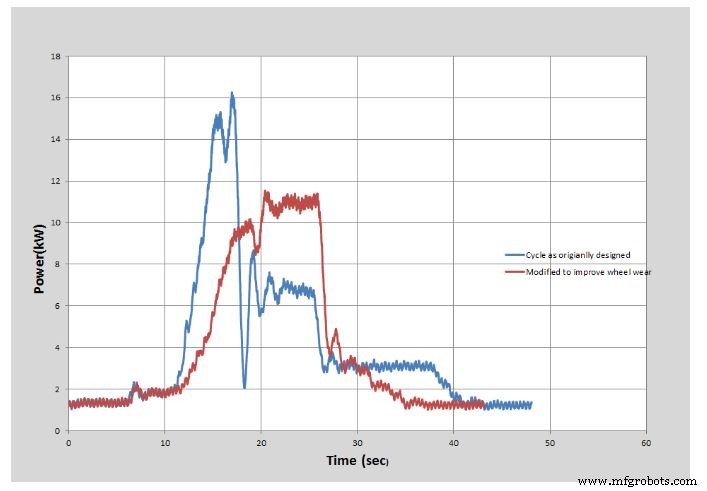
Depois que o ciclo modificado foi executado por várias semanas para validar a qualidade contínua da peça, as peças por revestimento foram aumentadas de 8 para 20 e a profundidade do revestimento foi reduzida de 0,03 mm para 0,02 mm. Este processo está em execução há cerca de 6 semanas sem alteração significativa na qualidade da peça. O resumo das economias de custo por ano é mostrado abaixo.
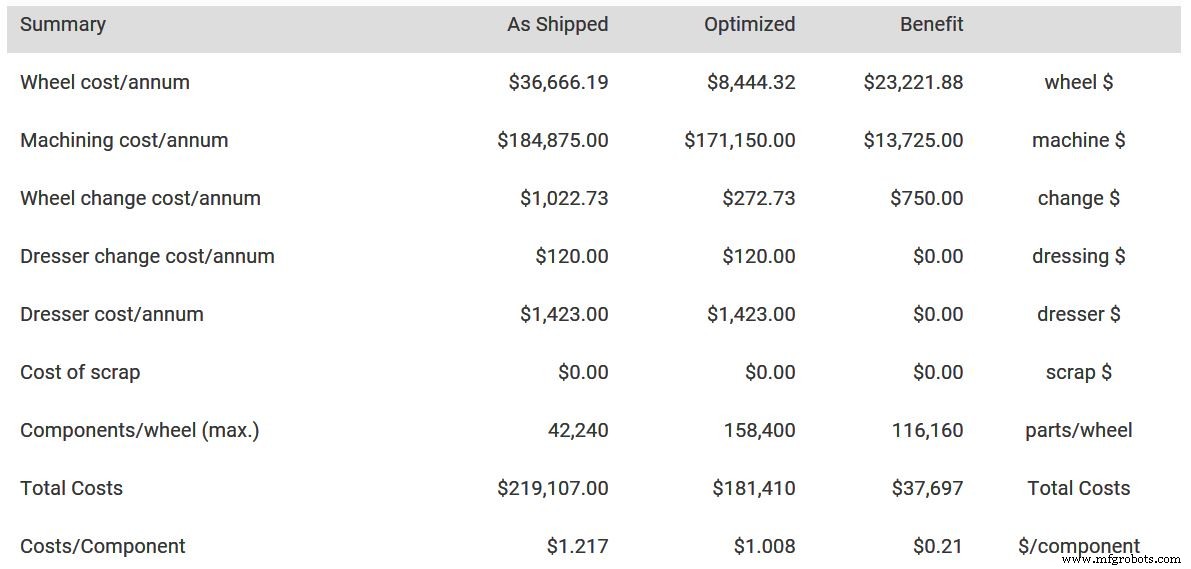
Estratégia para otimização
A solução, conforme ilustrado no segundo exemplo, é agendar tempo e peças nos estágios iniciais de produção (entre as etapas 7 e 8 na Figura #1) para trabalhar na otimização do processo com o fabricante da máquina e a equipe de engenharia de aplicação de ferramentas/abrasivos . No mínimo, o equipamento de monitoramento de energia deve ser usado durante esta fase para auxiliar na avaliação e desenvolvimento do ciclo. Com esta etapa adicional, o processo pode ser monitorado quanto à estabilidade em execuções de peças mais longas, o que pode trazer problemas à luz e/ou apresentar oportunidades de melhorias.
O retorno potencial desta etapa é grande, uma vez que as melhorias/economias de custos feitas nesta etapa estarão em vigor durante todo o ciclo de vida do projeto.
Apresentado anteriormente no Norton Abrasives
Compre nossa seleção de rodas de grade Norton em MSCdirect.com.
Tecnologia industrial
- Desenvolvendo Padrões Operacionais e Processos
- Airbus apresenta a fábrica do futuro
- Modos de falha dos processos de confiabilidade do equipamento
- Otimizando as operações de fabricação em sua fábrica
- Rodas retificadoras:Fabricação e classe | Indústrias | Metalurgia
- O valioso papel da automação de processos na busca por ESG
- O que é aprimorar? - Definição, processo e ferramentas
- Como implementar o gerenciamento de processos de negócios
- Serviços de retificação de superfície:processo e precisão
- Fundamentos da retificação OD