Sete dicas para paradas de fábrica eficazes
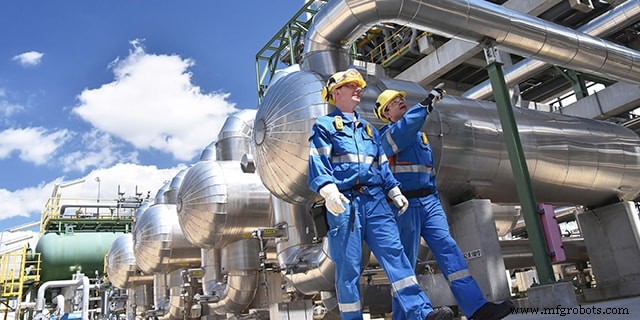
Sete dicas para paradas de fábrica mais eficazes e eficientes
Mike Aughenbaugh, Gerente de Desenvolvimento de Negócios, Swagelok Chicago, e Steven Robertson, Gerente de Vendas Downstream, Swagelok Sudeste do Texas
O turnaround da planta é um empreendimento importante para plantas químicas e refinarias em todo o mundo. Esses eventos complexos geralmente envolvem centenas de técnicos de vários fornecedores, trabalhando simultaneamente para concluir uma variedade de atividades importantes de manutenção, reforma e renovação em um sistema específico ou em uma planta inteira de uma só vez.
Uma vez que uma paralisação envolve deixar os processos offline, interrompendo assim a produção, é do interesse do proprietário/operador concluir esses projetos da maneira mais eficiente possível. Além disso, projetos de parada prolongada envolvem manter os contratados no local por mais tempo, aumentando assim o custo e o risco. Para instalações maiores, as paradas podem envolver anos de planejamento e representam um investimento maciço em nome do operador - não é incomum que as paradas representem uma parte importante do orçamento anual de manutenção da organização. Por esses motivos, uma reviravolta mal gerenciada pode causar um grande impacto financeiro para uma organização.
Com tudo isso em mente, aqui estão sete práticas recomendadas que os proprietários/operadores podem seguir para um gerenciamento de paradas mais eficaz:
#1. Envolva-se cedo com fornecedores confiáveis. O planejamento de paradas é um processo extenso, muitas vezes começando anos antes do próprio trabalho começar - e por boas razões. Estar o mais preparado possível pode ajudar a eliminar armadilhas imprevistas do projeto.
Uma qualidade de um projeto de recuperação bem preparado é o envolvimento precoce do proprietário com peças críticas e fornecedores de serviços. Os principais sistemas de fluidos são entidades complexas, alguns exigindo peças e componentes especializados feitos de ligas altamente específicas, dependendo do processo. Os prazos de entrega para obter essas peças projetadas sob encomenda geralmente são mais longos do que os componentes de aço inoxidável em estoque, mas o contato antecipado com seu fornecedor pode ajudar a mapear essas necessidades com antecedência.
Essa não é a única razão pela qual o envolvimento precoce com os fornecedores pode ser benéfico para as paradas. Você também pode …
#2. Identificar áreas de novas oportunidades. Embora o objetivo das paradas seja restaurar todas as partes do sistema para condições ideais de trabalho, as paradas também são ótimas oportunidades para fazer melhorias adicionais no sistema que podem resultar em maior confiabilidade e desempenho.
Fazer essas melhorias requer planejamento avançado. As alterações do sistema normalmente devem ser aprovadas bem antes do próprio evento de parada devido aos requisitos de gerenciamento de alterações (MOC) e antes do congelamento de engenharia do projeto. Os operadores que já se envolveram com os fornecedores antecipadamente estão à frente da curva, aqui - e podem trabalhar ainda mais com esses especialistas para obter recomendações de especialistas sobre aprimoramento do sistema.
Um exemplo de aprimoramento do sistema inclui painéis de amostragem aleatória pré-projetados e montados, que podem substituir os elementos tradicionais de amostragem aleatória em um sistema. Esta é uma melhoria prática que não altera o design fundamental do sistema e ajuda os operadores a extrair amostras adequadas com mais facilidade.
#3. Esteja preparado para o inesperado. Levar em consideração variáveis e contingências durante a parada é outra maneira pela qual os operadores podem garantir a eficiência geral do projeto.
Por exemplo, devido à natureza grande e complexa dos sistemas de fluidos nas plantas químicas e refinarias, é praticamente impossível saber exatamente quais e quantos componentes específicos serão necessários durante a parada. Por esse motivo, é benéfico estocar uma variedade de mangueiras, válvulas e adaptadores antes do início do projeto. Ter alguns desses componentes básicos à mão pode ser uma economia significativa de tempo em relação à necessidade de solicitar peças adicionais quando a instalação já estiver em andamento.
É claro que nenhum operador quer ficar preso ao estoque não utilizado. Por esse motivo, pode ser benéfico buscar termos com fornecedores, permitindo que você armazene estoque temporário ou em consignação para projetos de recuperação, para que as peças certas estejam sempre disponíveis. Nessas condições, você só precisará pagar pelas peças utilizadas durante o projeto.
#4. Garantir a disponibilidade de suporte local. Às vezes, porém, o inesperado acontece – e você pode não ter as peças certas à mão no momento em que precisa delas. Ao coordenar com seus fornecedores, certifique-se de que eles possam oferecer suporte localizado próximo ao seu projeto para qualquer fornecimento de peças imprevisto que possa ocorrer para garantir a entrega pontual.
#5. Fique de olho na instalação de peças críticas. O número de técnicos trabalhando em um determinado projeto de recuperação pode ser impressionante, envolvendo centenas de trabalhadores de diferentes empresas e disciplinas, muitas vezes de todo o mundo. Como tal, o nível de conhecimento de instalação desses vários fornecedores geralmente é inconsistente.
A inconsistência é a última coisa que um proprietário quer em um projeto de recuperação. Por exemplo, tubos mal encaminhados em sistemas de fluido existentes podem estar em risco de fadiga por vibração - e um técnico inexperiente pode simplesmente substituir componentes do sistema usando exatamente os mesmos pontos de roteamento e fixação. Um técnico mais experiente pode otimizar o roteamento para eliminar o risco de vibração. Além disso, um técnico mais inexperiente pode não dar a devida atenção às ferramentas e equipamentos usados para realizar o trabalho de instalação, o que pode danificar os componentes e levar a um desempenho ruim posteriormente.
Como você garante uma instalação consistente, usando as ferramentas certas, em dezenas de empreiteiros diferentes? Uma estratégia é incluir treinamento e certificação dentro de sua especificação. Isso garante que qualquer pessoa que esteja trabalhando em seu sistema esteja equipada com certos conhecimentos básicos e esteja familiarizada com as práticas recomendadas de instalação de som.
#6. Procure montagens pré-fabricadas. Devido à complexidade de engenharia de muitos sistemas de fluidos em plantas químicas e refinarias, quanto mais eles puderem ser pré-fabricados, pré-montados e pré-testados antes da parada, mais eficientemente os empreiteiros poderão instalar esses sistemas críticos.
Os conjuntos pré-fabricados podem, mais uma vez, ajudar a aliviar as preocupações de consistência de conhecimento e experiência em vários fornecedores e empreiteiros, e podem liberar horas de trabalho. Os painéis de amostragem de garra são uma boa área de oportunidade, permitindo a captura de amostras segura e eficiente, ao mesmo tempo em que atende às suas necessidades específicas de aplicação da planta. Em outros lugares, os sistemas de suporte do selo mecânico podem ajudar a aumentar a longevidade do selo mecânico. Os subsistemas analíticos, incluindo loops rápidos, estações de campo, módulos de calibração e comutação, sondas de amostra e cabeçalhos de distribuição de fluidos, podem trazer eficiência e consistência às suas operações, com dimensões de projeto simplificadas.
#7. Manter rígido controle de qualidade. É do interesse do operador manter um controle rigoroso da qualidade e consistência das peças que estão sendo instaladas durante uma parada. Especificações que permitem muita flexibilidade podem levar alguns empreiteiros a adquirir componentes mais baratos e de qualidade inferior. A qualidade inconsistente das peças em diferentes sistemas pode levar a desempenho inconsistente, necessidades de manutenção prematura ou tempo de inatividade posterior. Manter uma especificação rigorosa e atualizada que permita apenas o uso de componentes de alta qualidade em seus sistemas de fluidos críticos é mais uma maneira de tornar seu retorno eficaz. Além disso, quanto mais consistente for um operador em não misturar peças de diferentes fornecedores e não trocar peças diferentes, mais fácil será manter os sistemas consistentemente no futuro.
Mantendo essas dicas em mente, qualquer fábrica de produtos químicos ou operador de refinaria pode ver seu caminho através de paradas mais rápidas e eficientes, melhorando potencialmente a confiabilidade e o desempenho de longo prazo dos sistemas de fluidos. Interessado em aprender mais sobre paradas de fábrica eficazes? A Swagelok pode ajudar; nossa equipe de engenharia de campo ajuda regularmente os clientes de processamento químico ou de refino em todo o mundo com paradas de fábrica eficazes. Descubra como podemos ajudar a tornar a sua próxima reviravolta bem-sucedida.
Mike Aughenbaugh é Gerente de Desenvolvimento de Negócios da Swagelok Chicago. Ele está na empresa há mais de dez anos. Sua experiência em aplicações químicas e de refino inclui lavagem de vedação para equipamentos rotativos, analisadores, skid químico, sistemas de lubrificação, estações de coleta de amostras e bombas de amostra, purgadores de vapor, equipamentos de laboratório, rastreamento a vapor/elétrico e sondas de amostra.
Steven Robertson é Gerente de Vendas Downstream na Swagelok Southeast Texas. Ele passou quase 20 anos na Swagelok em uma variedade de funções técnicas e voltadas para vendas. Ele tem experiência em ajudar clientes químicos e de refino em todo o Texas a resolver desafios críticos de sistemas de fluidos.
Tecnologia industrial
- 5 dicas de acabamento para sinterização direta a laser de metal
- 6 Dicas de soldagem para manutenção da planta
- 4 dicas para uma planta mais lucrativa
- 9 Dicas eficazes de redução de custos para empresas de manufatura
- 4 dicas para otimizar seu jato de água
- Minimizando tempos de retorno para peças grandes
- Seis dicas para um desbaste otimizado eficaz
- 9 dicas de segurança eficazes para o local de trabalho industrial
- Sete dicas para oficinas mecânicas que consideram apagar as luzes
- Dicas de segurança para gerenciar uma parada de fábrica