Fundição e laminação de placas finas
Fundição e laminação de lajes finas
Para a produção de produtos planos, o aço líquido é geralmente moldado na forma de placas geralmente na faixa de espessura de 150 mm a 350 mm nas máquinas de lingotamento contínuo de placas. Essas placas são inspecionadas, escarificadas e depois reaquecidas em forno de reaquecimento de placas até as temperaturas de laminação antes de serem laminadas para bobinas laminadas a quente em laminadores de tiras a quente semicontínuos ou contínuos. O desenvolvimento da tecnologia de fundição e laminação de placas finas (TSCR) é um passo à frente para reduzir o número de etapas do processo na produção de bobinas laminadas a quente (HRC). Originalmente a tecnologia TSCR foi desenvolvida com o objetivo principal de reduzir os custos de investimento e produção, mas hoje tornou-se uma das rotas de produção mais promissoras para manter o aço como material líder em aplicação tecnológica e está sendo considerado como a tecnologia que atingiu um alto grau de maturidade. A velocidade de lançamento de 6,0 metros por minuto (m/min) para espessura de laje de 50/55 mm é bastante comum nos dias de hoje.
Inicialmente, apenas aços-carbono lisos de qualidade comercial estavam sendo fundidos através da rota de lingotamento de placas finas. Mas atualmente a maioria das classes de aço, incluindo aços de baixo, médio e alto carbono, classes de aço HSLA (alta resistência e baixa liga), classes de aço para tubos de linha e classes de aço para aplicação automotiva, incluindo classes IF (sem intersticial) podem ser fundidas através de placas finas rota de fundição. Na verdade, esta tecnologia trouxe uma mudança de paradigma na tecnologia do aço de fundição e laminação. A tecnologia de lingotamento e laminação de placas finas foi possível devido às diversas melhorias nos processos de lingotamento e laminação que incluem (i) projeto do molde, (ii) oscilações hidráulicas do molde, (iii) uso de freios eletromagnéticos (EMBR), (iv ) uso de descalcificador de alta pressão e guia lateral do rolo (bordador) no moinho, (v) redução dinâmica do núcleo líquido (LCR), (vi) qualidade do pó do molde e SEN redesenhado e (vii) resfriamento por pulverização de água.
As principais vantagens da tecnologia TSCR sobre a fundição de placas grossas e laminação a quente incluem (i) redução no custo de capital, (ii) redução na mão de obra, (iii) redução no espaço necessário, (iv) melhoria no rendimento do produto acabado a partir de líquido aço, (v) redução do consumo específico de combustível e (vi) redução do consumo específico de energia.
Histórico
A implementação do conceito TSCR não obteve nenhum sucesso até meados dos anos 80 devido aos inúmeros desafios tecnológicos associados à tecnologia. O primeiro avanço nesse sentido foi alcançado em outubro de 1985 pela SMS Schloemag-Siemag, quando a primeira placa fina de 50 mm de espessura foi moldada em uma planta piloto em Kreuztal-Buschhutten. Este sucesso foi alcançado com um molde em forma de funil patenteado e um bico de entrada submerso otimizado. A SMS Schloemag-Siemag deu a esta tecnologia o nome de ‘Compact Strip Production (CSP)’. A primeira planta CSP foi encomendada no final de 1987 e comissionada na Nucor Steel, Crawfordsville, Indiana, em julho de 1989. Poucos dias após o comissionamento, houve uma grande avaria na máquina de fundição devido a operadores inexperientes. Isto tem um efeito sobre a rápida aceitação desta tecnologia. Quase ao mesmo tempo, o processo de produção de tiras em linha (ISP) estava sob intenso desenvolvimento pela Mannesmann Demag e pelo grupo Arvedi. O desenvolvimento do ISP começou em 1988 com base em uma patente de Arvedi-Mannesmann. Em 1992, o protótipo da planta ISP foi construído pela Arvedi em sua fábrica de Cremona, onde a maior parte do desenvolvimento desse processo foi realizada. Em 1994-95, a planta protótipo completou a primeira fase de seu desenvolvimento. Mais tarde, com base na tecnologia ISP, a Acciaieria Arvedi desenvolveu um novo processo de fundição de lajes finas/laminação sem fim sob a marca Arvedi ESP. Com este processo está sendo produzida uma tira de 0,8 mm de espessura. Voest Alpine (VAI) da Áustria (agora tecnologias Primetals) e Danieli da Itália também desenvolveram tecnologias de laminação e fundição de placas finas. A tecnologia da VAI é conhecida como Tecnologia de Laminação e Laminação Contínua de Lajes Finas (CONROLL) e produz lajes de até 125 mm de espessura. É mais de lajes de espessura média. A tecnologia desenvolvida pela Danieli ficou conhecida como Laminação Contínua Flexível de Lajes Finas (fTSR) e produz lajes na faixa de espessura de 70 mm a 90 mm. Implementação As tecnologias TSCR tiveram um grande impulso depois que a China e a Índia começaram a expandir sua produção de aço de forma massiva. Hoje, uma planta TSCR de três fios baseada na tecnologia CSP foi instalada em ESSAR, Gujarat, Índia (agora Arcelormittal Nippon Steel India Limited).
O processo TSCR passou por um desenvolvimento extremamente dinâmico principalmente no que diz respeito à produção por planta, disponibilidade, custos de conversão, variedade de tipos de aço produzidos, dimensões próximas ao formato líquido, geometria da tira, parâmetros de qualidade e características da superfície. Hoje, a tecnologia TSCR é usada para produzir não apenas aços na faixa de baixo e médio carbono, mas também aços inoxidáveis ferríticos e austeníticos e aços de silício com grão orientado. Os estágios a montante e as instalações de processamento de tiras a quente a jusante também passaram por um maior desenvolvimento, com a engenharia e a tecnologia da planta se adaptando aos produtos da planta CSP, por exemplo, espessuras de tiras a quente até cerca de 1 mm.
Características metalúrgicas e outras importantes do processo TSCR
Ao processar o aço no processo TSCR, do distribuidor ao bobinador, existem várias características metalúrgicas e outras importantes do processo, conforme descrito abaixo.
- A solidificação rápida da placa fina refina a estrutura dendrítica. A correção na estrutura dendrítica contribui para uma estrutura mais homogênea.
- As inclusões não metálicas são pequenas e globulares, mantêm sua forma durante a laminação a quente e contribuem para propriedades isotrópicas (como tenacidade, dobrabilidade etc.).
- Todos os elementos de microliga adicionados permanecem em solução. Devido à alta temperatura da laje fundida antes da laminação a quente, a precipitação prematura é evitada.
- Para minimizar as dificuldades de fundição na região peritética, o teor de carbono de muitos aços microligados é restrito entre 0,05% e 0,06%. Essa restrição beneficia a tenacidade e a soldabilidade.
- A alta temperatura da laje durante a flexão e não flexão minimiza a tendência de formação de trincas transversais.
- A temperatura no forno de equilíbrio depende do elemento de microliga e é projetada para manter a microliga em solução.
- O carregamento direto é o principal fator que reduz o consumo de energia durante a laminação a quente.
- Na laminação de lajes finas, a deformação nos passes iniciais muitas vezes excede 50%. A deformação pesada em altas temperaturas é essencial para refinar grãos austeníticos grosseiros (mais de 1000 micrômetros) por recristalização.
- O refinamento e a uniformidade dos grãos austeníticos é um pré-requisito para uma estrutura ferrítica fina de até 4 micrômetros a 5 micrômetros.
- O resfriamento acelerado na mesa de saída e o resfriamento inferior da austenita refina ainda mais a ferrita.
O processo de produção e o nível típico de evolução de temperatura no processo TSCR são mostrados na Fig 1.
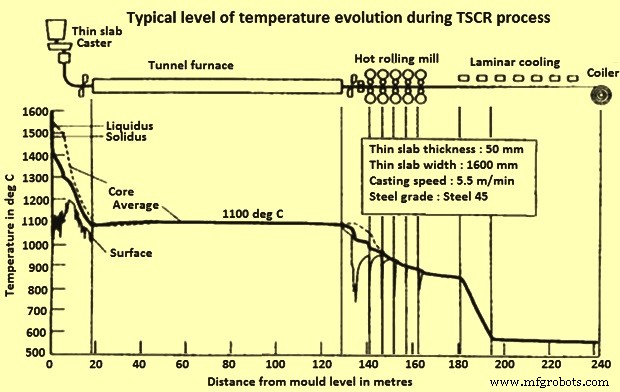
Fig 1 Nível típico de evolução da temperatura durante o processo TSCR
A solidificação mais rápida no TSCR fornece estruturas mais finas e uniformes. Espaçamento entre braços dendríticos secundários finos (SDAS), alcançado devido à rápida solidificação no lingotamento, e promove uma estrutura mais homogênea com menor estrutura de microseparação do que o lingotamento convencional. A microssegregação é a segregação entre os braços dendríticos onde a concentração mínima de soluto está no centro dos braços dendritos e a concentração máxima de soluto está entre os braços. De fato, o SDAS é uma medida da não homogeneidade no lingotamento contínuo de lajes. Na fundição de placas finas, é usado o sistema de “redução de núcleo líquido” (LCR). A redução do núcleo líquido permite que a espessura do cordão abaixo do molde seja reduzida enquanto o núcleo ainda está na fase líquida. Geralmente, o primeiro segmento no sistema de guia de cordão pode ser ajustado para obter a redução desejada na espessura do cordão. Os diferentes processos TSCR são descritos abaixo.
Produção de tiras compactas
O conceito básico na tecnologia CSP é a obtenção da máxima eficiência de custo através da ligação das três etapas do processo, a saber (i) fundição, (ii) equalização de temperatura e (iii) laminação a quente. O aço líquido após a fabricação do aço é colocado no distribuidor da máquina de lingotamento contínuo (CCM). Nesta tecnologia, o aço líquido é moldado em placas com a espessura desejada que varia de 50 mm a 90 mm. A placa é então cortada no comprimento adequado e transportada para o túnel ou forno de equilíbrio normalmente ajustado a uma temperatura de 1150°C. Neste ponto, a placa mostra um tamanho de grão de austenita de 500 micrômetros a 1000 micrômetros. Após o tempo de residência de 20 minutos no forno, a placa deixa o forno e é cortada. A placa fina a quente entra no laminador de acabamento a cerca de 1000 graus C. A placa é laminada em tiras a quente (espessura variando de 0,8 mm a cerca de 16 mm e largura variando de 800 mm a 1880 mm) à medida que passa pelo laminador de acabamento de 5, 6 ou até 7 suportes. A tira a quente após a laminação entra na mesa de saída (ROT) onde sofre resfriamento laminar até a temperatura de bobinagem. Em seguida, é enrolado à temperatura ambiente. O esquema do processo CSP é mostrado na Figura 2.
Fig. 2 Esquema do processo de produção de aço compacto
Os principais elementos do processo CSP são torre de panela, molde, sistema de guia de fio, unidade de rolo de aperto, cisalhamento pendular, forno de aquecimento com carro de transferência para conectar dois suportes de fundição, laminador com 5 a 7 suportes, resfriamento de tiras e bobinadeiras. O processo possui ajuste flexível da espessura da laje durante o lingotamento através da redução do núcleo líquido, permitindo adaptação à espessura final da tira e da espessura e velocidade de lingotamento. Tiras a quente de 1 mm de espessura podem ser confortavelmente laminadas a quente por esta tecnologia. CSP utiliza sistemas de controle de perfil e planicidade adotando a conhecida tecnologia CVC para ajuste. As capacidades de uma planta de um fio são de até 1,5 milhão de toneladas por ano (Mpta), a de dois fios é de até 3 Mpta e a de 3 fios de até 4 Mpta. O layout esquemático da planta CSP de três vertentes é mostrado na Fig 3 e diferentes conceitos das plantas CSP são mostrados na Fig 4.
Fig 3 Layout esquemático da planta CSP de três vertentes
Fig 4 Diferentes conceitos das plantas CSP
O coração do processo CSP é o molde patenteado em forma de funil com 1100 mm de comprimento de cromo-zircônio-cobre (Fig 5). A alimentação do aço líquido é feita através de um bocal de entrada submerso (SEN) nos confins de uma cavidade estreita do molde por alargamento da entrada do molde na forma de um funil. Este funil termina aproximadamente no meio do comprimento do molde, além do qual as paredes laterais largas dos moldes são paralelas e separadas por uma espessura que é igual à espessura da placa fina. Os lados da parede do molde são afunilados para compensar o encolhimento do aço solidificado. Devido à rápida solidificação da placa fina, é necessário fornecer orientação do fio em um comprimento de cerca de 4,5 m a 5 m, mesmo com uma alta velocidade de fundição de 6 m/min.
Em comparação com o seu projeto original, a máquina de fundição CSP teve desenvolvimentos notáveis no que diz respeito à configuração do molde em forma de funil, ao comprimento da guia do fio, aos loops de controle tecnológico, bem como à sua flexibilidade em termos de rendimento e espessura de fundição . Nas fábricas de fundição que estão em operação hoje, o comprimento da guia do cordão foi aumentado de cerca de 6,0 m para 9,7 m (Fig. 5). Este desenvolvimento foi implementado mantendo o conceito vertical com todas as suas vantagens relacionadas com os equipamentos e metalúrgicas. Um passo decisivo foi o desenvolvimento do molde desde o design de estrutura em U até o molde de estrutura dupla ou estrutura em O. Este molde inovador é fixado no seu centro, ao mesmo tempo que aumenta significativamente a estabilidade de toda a estrutura. A estrutura possui janelas laterais para acomodar o garfo se e quando um freio eletromagnético (EMBR) for usado.
Fig 5 Diagrama esquemático de uma máquina de fundição de placas finas CSP e seu desenvolvimento progressivo
Os circuitos de controle tecnológico do rodízio CSP foram sistematicamente ampliados com o objetivo de alcançar a máxima confiabilidade operacional e a melhor qualidade do produto. Isso se refere principalmente ao controle do nível do molde, oscilador hidráulico do molde, redução do núcleo líquido (LCR) e medição da densidade do fluxo de calor no molde e detecção precoce de rompimento, bem como o controle dinâmico da solidificação final com o objetivo de garantir uma alta temperatura de entrada da laje no forno túnel. A ligação direta de lingotamento e laminação cria um potencial adicional em relação à capacidade de produção e dimensões finais. O LCR permite que a espessura ideal da placa seja definida para atingir as dimensões limite, a capacidade máxima de produção ou o grau de conformação necessário enquanto a fundição está em andamento.
O desenvolvimento do laminador CSP progrediu para atender às demandas do mercado. A melhor solução para atender a vários requisitos e incluir uma ampla gama de produtos acabados é o layout compacto do laminador com seis ou sete carrinhos, dependendo do mix de produtos. Para obter espessuras mínimas de tiras acabadas de até 0,8 mm, diferentes espessuras de entrada de placas são usadas e os diâmetros do cilindro de trabalho e os materiais do cilindro são otimizados de forma que dois ou três diâmetros de cilindro diferentes sejam usados. A tecnologia CVC (coroa continuamente variável), que já provou ser bem-sucedida em laminadores a quente convencionais, foi aprimorada ainda mais com o desenvolvimento dos laminadores de acabamento CSP. O resultado é o chamado processo 'CVC Plus', que apresenta uma faixa de ajuste marcadamente mais ampla para controle de perfil de até 190% da faixa de configuração do CVC.
O uso de sistemas de refrigeração entre bancadas mais eficientes permite a laminação ferrítica de aços de ultra baixo carbono, bem como a laminação termomecânica de aços HSLA. Uma tesoura voadora instalada à frente de uma bobinadeira de rotor e/ou de duas bobinadeiras descendente oferece a possibilidade de laminação sem fim de tiras finas. Os sistemas de resfriamento rápido a jusante do último suporte ou na parte traseira da linha de resfriamento, oferecem maior flexibilidade na implementação de curvas de temperatura-tempo para obter propriedades específicas da tira e processar aços multifásicos.
A capacidade de rolar até espessuras finais inferiores a 1,5 mm é uma característica particular do processo CSP, e os pacotes de tecnologia foram desenvolvidos especificamente para isso, no entanto, dependendo das espessuras de entrada, evolução da temperatura, distribuição da redução e velocidade de laminação, espessuras finais de até 0,8 mm podem ser alcançadas em temperaturas de laminação de acabamento austenítico.
Em comparação com a produção convencional de tiras a quente, as espessuras alcançáveis são até 50% mais finas, dependendo do tipo de aço envolvido. Isso, por sua vez, aumenta as exigências no laminador CSP, especialmente em termos de força e demanda de energia, desgaste dos rolos predominantemente nas bancadas tardias e planicidade das tiras. A lubrificação da folga do rolo é adotada para minimizar o desgaste, redução da força e torque de separação do rolo, bem como para melhorar a superfície da tira. Para medição e controle de planicidade, laçadeiras segmentadas são instaladas em vários moinhos que detectam não apenas a tensão entre suportes, mas também a distribuição de tensão da tira ao longo da largura, e que ativam a função de dobra do rolo de trabalho para fins de controle de planicidade.
Apesar destas medidas, no entanto, para tiras muito finas, é difícil obter uma planicidade elevada da tira uma vez que a tira tenha arrefecido. A tira, embora ainda plana na mesa do rolo de saída porque está sob tensão, pode apresentar ondulação da borda durante o desenrolamento posterior. O mascaramento de bordas foi desenvolvido para proteger a planicidade da tira resfriada. Placas de guia ajustáveis sob os grupos de resfriamento de fluxo laminar mantêm a água longe das bordas da tira e permitem que a planicidade seja melhorada de 250 unidades I para 25 unidades I (as unidades I é uma medição de planicidade quantitativa exata. É um número adimensional que incorpora tanto a altura quanto o comprimento pico a pico de uma onda repetida).
As malhas de controle instaladas em um laminador CSP são constantemente atualizadas para o status tecnológico real. Servem não apenas para determinar a estratégia de laminação, calcular o cronograma de passes e predefinir o laminador, mas principalmente para atingir os parâmetros necessários do produto acabado, como perfil, contorno e planicidade, monitorar o fluxo de massa, controlar o laminador para atingir a espessura final exigida e garantir tolerâncias mínimas desses parâmetros. As propriedades mecânicas da tira acabada são significativamente afetadas pelas temperaturas de laminação e bobinagem de acabamento, bem como pela estratégia de resfriamento. Modelos de processos físicos adequados foram desenvolvidos e adaptados aos requisitos cada vez maiores do produto.
Tiras laminadas a quente produzidas por meio da tecnologia CSP, especialmente tiras na faixa de espessura inferior até 0,8 mm, começaram a influenciar o design das etapas do processo tecnológico a jusante, como decapagem e galvanização. Um exemplo típico de uma configuração de planta combinada é a linha de decapagem e galvanização de tiras a quente colocada em operação em Wuppermann na Holanda em 2000, que decapa e galvaniza tiras a quente na faixa de espessura de 0,8 mm a 3,0 mm. Também é possível integrar uma ou duas bancadas de laminação a frio em linhas de processamento deste tipo.
Processo de produção de tiras em linha
O processo de produção de tiras em linha (ISP) produz bobinas laminadas a quente até bitolas acabadas de 1 mm. Uma das características mais marcantes do processo ISP é a compactação geral da planta. Com um comprimento de linha de apenas 180 m de aço líquido para bobina laminada a quente, é geralmente reconhecida como a linha de tiras mais curta do mundo. Esta característica é o resultado de três características significativas do processo ISP, a saber (i) lingotamento contínuo com redução do núcleo líquido durante a solidificação da laje, (ii) ligação direta entre o lingotamento do aço e a laminação inicial da laje e (iii) o uso de um aquecedor de indução compacto combinado com dois fornos de caixa de bobina, em vez de fornos de túnel longo no lado de entrada do laminador a quente.
O aço líquido é fundido em molde multicurvador com oscilação servo-hidráulica e espessura de saída de 70 mm. A laje sofre uma suave redução à medida que desce o rodízio de 5,2 m de raio, para emergir a uma velocidade de 5,5 m/min e com uma espessura máxima de 55 mm. O bocal do distribuidor é projetado para garantir o crescimento homogêneo da casca e a fundição de longas sequências.
Imediatamente após a saída do lingotamento, a placa entra em um desbaste de 3 suportes para redução para uma barra de transferência de 10 mm a 18 mm de espessura, que é então cortada no comprimento por uma tesoura pendular transversal. A redução do núcleo líquido permite a produção de uma placa de aço homogênea de alta pureza, praticamente livre de segregação e com bom refinamento de grão para conferir melhores características mecânicas ao aço acabado. Além disso, a combinação da redução do núcleo líquido com a entrada direta da placa no desbaste traz vantagens de economia de energia em relação às sequências de laminação interrompidas convencionais.
Depois de passar por um forno de aquecimento por indução para elevar a temperatura do aço em 150 graus C a 250 graus C, a barra de transferência chega ao ‘forno Cremona’. Esta unidade é composta por duas bobinadeiras alojadas em câmaras isoladas, ou caixas, e enquanto uma bobinadeira está recebendo e bobinando uma barra de transferência vinda do forno de indução, a outra está desbobinando a barra de transferência anterior para alimentar o laminador a quente.
Embora o forno Cremona a gás desvincule a etapa de lingotamento e desbaste do laminador de acabamento, ele é um amortecedor dinâmico, pois mantém o aço em linha e homogeneiza o perfil de temperatura pronto para laminação a quente e, portanto, alcança alta produtividade e eficiência. As bordas de tiras a quente resultantes estendem as campanhas de rolos de trabalho no laminador de acabamento em até 150 km.
O aço é descalcificado a alta pressão antes de entrar em um laminador a quente de 5 estantes equipado com deslocamento e dobra de rolos de trabalho, além de controle automático de medidor em todas as estantes de 4 alturas. Uma bitola de entrada do laminador de 20 mm ou menos permite à Arvedi produzir tiras laminadas a quente de até 1 mm em uma única passagem com alto perfil e precisão de bitola, um nível de coroamento de 1% a 3%, baixa rugosidade superficial e boa deformabilidade a frio.
Nesta bitola inferior, os desvios de comprimento ao longo da faixa são inferiores ou iguais a uma unidade 'I'. Finalmente, a tira laminada passa ao longo de uma mesa de resfriamento de fluxo de água laminar antes do enrolamento descendente. Um alto nível de controle e automação do processo é uma característica integral de toda a planta. As emissões de gases de escape são de 1,0 mg / N cum, e a recirculação total da água no local evita descargas de líquidos.
As tolerâncias dimensionais da tira laminada a quente são comparáveis às do produto laminado a frio, com bobina de 1 mm a 1,2 mm apresentando um valor transversal plano quando medido a 25 mm da borda da tira. Este processo é mostrado esquematicamente na Fig 6.
Fig 6 Esquema do processo de produção de tiras em linha
Tecnologia de laminação e fundição de lajes finas da Danieli
O processo de primeira geração ou processo de lingotamento e laminação de placas finas da Danieli consistia na unidade de lingotamento de placas finas flexíveis (fTSC) conectada à unidade de laminação de placas finas (fTSR) através de um forno túnel. A unidade fTSC foi capaz de fundir lajes de espessura de 60 mm. O rodízio era de design curvo vertical, possuindo molde em funil com redução suave e resfriamento por névoa de ar. O laminador consistia em um laminador de acabamento com 6 a 7 carrinhos de laminação em configuração de cluster. Este processo é mostrado esquematicamente na Fig 7.
Fig 7 Esquema do processo fTSC e fTSR
Por meio do desenvolvimento contínuo do processo, a Danieli desenvolveu dois conceitos de layout diferentes e, sob esses conceitos, o processo de laminação e fundição de placas finas foi nomeado como 'Quality Strip Production (QSP) e 'Quality Strip Production Endless (QSP-E) (Fig 8).
No QSP, a planta com um ou dois cordões de lingotamento é conectada ao laminador por meio de forno(s) longo(s) túnel(s), que tem a função de reaquecer e equalizar a temperatura da placa, além de garantir tempo de buffer suficiente em caso de paradas programadas do moinho (por exemplo, troca do rolo de trabalho) ou interrupções não programadas do fluxo de material. Nos últimos anos, graças a um aumento progressivo do fluxo de massa devido ao aumento das velocidades de lingotamento herdado da última geração de lingotamentos de placas finas operando em velocidades ultra-altas, e em combinação com a introdução confiável da tecnologia de aquecimento por indução no lugar dos fornos de túnel , foi possível desenvolver a configuração do QSP-E. Essa configuração resultou em plantas extremamente compactas que são especificamente dedicadas à produção de medidores ultrafinos. Isso é possível graças à aplicação do processo de laminação sem fim (ou seja, a conexão direta e ininterrupta entre lingotamento e laminação), para superar os conhecidos problemas de rosqueamento de tiras na produção de bitolas finas no modo bobina a bobina.
Fig 8 Processos QSP e QSP-E
As plantas QSP podem ser operadas com 2 cordões de fundição, o que tornou possível ampliar drasticamente o mix de tipos de chapas finas de aço e aumentar a produtividade da planta bem acima de 3 Mpta. Essas plantas foram concebidas inicialmente para a aplicação da laminação bobina a bobina e depois para o processo semi-infinito de laminação de bitolas mais finas abaixo de 1 mm. O conceito QSP-E possibilitou otimizar a produção de bitolas ultrafinas no modo sem-fim, mas apresentando pouca flexibilidade na produção de classes mais sofisticadas devido à rígida ligação entre lingotamento e laminação.
No caso de laminação sem fim, o fundidor é de fato forçado a trabalhar sempre em velocidades de fundição muito altas e isso não é possível para todos os tipos de aço por razões metalúrgicas. Além disso, o processo sem-fim provou ser economicamente competitivo apenas para a produção de bobinas com espessura de tira inferior a 1,5 mm, mas assim que a espessura da tira é aumentada, a potência necessária para que os aquecedores de indução continuem operando torna-se excessivamente alta, tornando-se economicamente necessário para retornar ao modo bobina a bobina.
Em um esforço contínuo para melhorar os processos e tecnologias existentes e superar suas limitações atuais, a Danieli desenvolveu um novo conceito em plantas TSCR. Este conceito é chamado Danieli Universal Endless (DUE). O conceito DUE é capaz de unificar em uma única linha de produção todos os recursos vencedores que até agora foram desenvolvidos usando diferentes abordagens, eliminando os fatores limitantes de cada um deles.
O layout DUE apresenta (i) alta produtividade devido a uma combinação inédita de espessura e velocidade da placa, (ii) alta flexibilidade de produção, capaz de operar no modo bobina a bobina, semi-sem e sem fim, (iii) alta flexibilidade, devido à presença do forno túnel e tempo de buffer relevante, (iv) abrange todo o espectro de aços produzidos para produtos planos, incluindo os mais sofisticados laminados por laminação termomecânica (graus API pipeline) ou com temperatura controlada laminação (produtos multifásicos), bem como os graus que exigem velocidades de fundição moderadas como peritético, aços elétricos e graus de alto carbono, sendo sensíveis a trincas, e (v) cobre todo o espectro de dimensões geométricas de tiras, variando de 0,8 mm ultra - bitolas finas, produzidas em modo sem-fim, com tiras de até 25 mm de espessura. Isso, claro, em combinação com um custo de transformação imbatível, inferior a qualquer outro processo atualmente disponível.
tecnologia CONROLL
O processo CONROLL produz chapas de 70 mm a 80 mm de espessura através de um molde reto com lados paralelos, mas não realiza reduções na espessura do cordão. Altas velocidades de fundição na faixa de 2 m/min a 4 m/min e largura de 800 mm a 1600 mm são possíveis. O rodízio é conectado ao laminador através de um forno de reaquecimento de rolos que equaliza a temperatura da placa a 1120 graus C. O laminador pode incluir quatro, cinco ou seis bancadas de acabamento, dependendo da mistura de produtos e do calibre de acabamento necessário. O laminador consiste em um mecanismo de cisalhamento hidráulico, desincrustante de água de alta pressão, sistema de resfriamento de tiras laminares e um downcoiler. A espessura final da tira está na faixa de 1,8 mm a 20 mm.
A tecnologia CONROLL foi instalada em abril de 1995 em Mansfield da Armco. A Armco adotou essa tecnologia porque foi projetada especificamente para aço inoxidável. As classes de aço produzidas incluem aço carbono, classes de aço inoxidável das séries 400 409 e 430, uma pequena porcentagem de classes de alta resistência e baixa liga (HSLA), classes de aço de alta liga e aços de silício.
tecnologia TSP
A Tippins Incorporated dos EUA uniu-se à fabricante de rodízios Samsung Heavy Industries da Coréia do Sul para desenvolver a tecnologia TSP. Esta tecnologia é adequada para aços de baixo a alto carbono, aços inoxidáveis, aços HSLA, aço silício, aços API e aços de qualidade de trefilação. Um dos pontos fortes do moinho é a sua versatilidade. Pode produzir bobinas ou chapas discretas permitindo a produção de uma ampla gama de larguras e bitolas. A fundição de placas de espessura intermediária apresenta algumas vantagens. A placa é fina o suficiente para eliminar a necessidade de um desbaste separado e grossa o suficiente para manter a boa qualidade. A espessura intermediária permite maior largura da laje, menor tempo de reaquecimento e, portanto, menor formação de incrustações em comparação com lajes finas de 50 mm.
Após a fundição, as placas são enviadas diretamente para o forno de reaquecimento para equalizar a placa à temperatura de laminação correta. O tempo de espera típico para aquecer uma placa a 1250 graus C é de 12 min a 13 min. Uma vez que a tira tenha sido reduzida para 20 mm a 25 mm de espessura, ela é enrolada no forno de bobinagem para reter a temperatura da tira. A tira é então revertida para frente e para trás através do laminador. Um total de três passadas de desbaste planas e seis passadas de acabamento de bobinagem são geralmente necessárias para o acabamento de bitolas de 1,5 mm de espessura.
Processo de manufatura
- Tecnologia de fundição de liga de titânio
- Prós e Contras da Fundição de Espuma Perdida
- Fundição em areia com tecnologia FDM
- Tundish e seu papel na fundição contínua de aço
- Tecnologia de Fundição de Feixe em Branco
- Tecnologia de Resfriamento Secundário no Processo de Fundição Contínua
- Defeitos de Fundição:Tipos, Causas e Soluções
- ABB Robotics:inovação tecnológica e pesquisa e desenvolvimento de robótica
- Centro de Torneamento e Tecnologia de Máquinas
- Processo de Laminação a Quente e Frio