Geração e uso de gás de forno de coque
Geração e uso de gás de forno de coque
O coque é um insumo essencial para o processo de fabricação do ferro. Para fazer coque, o carvão é aquecido na ausência de ar para retirar a matéria volátil (VM). A conversão do carvão em coque é chamada de carbonização do carvão e o processo é realizado em fornos de coque. Uma bateria de forno de coque consiste em vários fornos de coque. Atualmente, existem dois métodos principais de produção de coque para alto-forno.
O primeiro método consiste em um processo de recuperação em que o carvão é aquecido em uma atmosfera completamente redutora e os produtos voláteis são recuperados em uma planta de subprodutos associada. Os fornos de coque usados para este método de carbonização de carvão são chamados de fornos de subproduto e a bateria do forno de coque é chamada de bateria do forno de coque de subproduto. Durante a carbonização do carvão de coque em uma bateria de forno de coque de subproduto, o VM que consiste em cerca de 25% a 30% do carvão carregado é eliminado como gás efluente que deixa as câmaras do forno de coque como o gás de coqueria quente. O gás de coqueria bruto é um gás inflamável e tem uma cor marrom amarelada e um odor orgânico.
No segundo método, a carbonização do carvão é realizada em uma bateria de forno de coque sem recuperação (também conhecida como recuperação de calor ou recuperação de energia). No processo de não recuperação, o ar é introduzido acima do topo do leito de coque no forno de coque e os produtos voláteis gerados durante a carbonização são queimados no próprio forno para fornecer o calor necessário para o processo de carbonização do carvão.
A planta de subprodutos é parte integrante do processo de fabricação de coque de subprodutos. A operação de cada forno é cíclica, mas a bateria contém um número suficientemente grande de fornos para produzir um fluxo essencialmente contínuo do gás bruto do forno de coque. Os fornos individuais são carregados e esvaziados em intervalos de tempo aproximadamente iguais durante o ciclo de coqueamento. A coqueificação prossegue por 15 horas a 18 horas para produzir o coque BF. Durante esse período, o VM do carvão destila como gás bruto de coqueria. O tempo de coqueificação é determinado pela mistura de carvão, teor de umidade, taxa de queima e as propriedades desejadas do coque. Quando a demanda por coque é baixa, os tempos de coque podem ser aumentados para 24 horas. As temperaturas de coqueamento geralmente variam de 900°C a 1100°C. O ar é impedido de vazar nos fornos de coque, mantendo uma contrapressão positiva no coletor principal. Os fornos de coque são mantidos sob pressão positiva mantendo alta pressão hidráulica principal de cerca de 10 mm de coluna de água nas baterias. Os gases e hidrocarbonetos que evoluem durante a destilação térmica são removidos através do sistema de off take e enviados para a planta de subprodutos para recuperação.
A grande quantidade de gás gerada devido à vaporização de VM no carvão durante a produção de coque na bateria do forno de coque de subprodutos é tratada em uma planta de subprodutos adjacente. Durante o ciclo de coqueificação, o gás é produzido durante a maior parte do período de coqueificação. A composição e a taxa de evolução do gás CO mudam durante o período e a evolução do gás CO normalmente está completa quando a carga de carvão na bateria atinge 700 graus C. Este gás é conhecido como gás bruto de forno de coque e é processado em a planta de subprodutos. As funções da planta de subprodutos são processar o gás bruto para recuperar produtos químicos valiosos do carvão e tratar o gás bruto do forno de coque suficientemente para que possa ser usado como um combustível limpo e ecológico. O gás de coqueria bruto após o tratamento na planta de subprodutos é chamado de gás de coqueria limpo ou simplesmente gás CO.
Na bateria do forno de coque de subproduto, o gás do forno de coque evoluído deixa as câmaras do forno de coque em altas temperaturas, aproximando-se de 1100 graus C. O gás CO bruto é resfriado por evaporação adiabática de parte do licor de pulverização (licor de lavagem) para cerca de 80 graus C e está saturado de água. A temperatura do gás torna-se suficientemente baixa para que possa ser manuseado na rede coletora de gás. Da tubulação coletora de gás, o gás bruto do forno de coque flui para a tubulação principal de sucção. A quantidade de licor de lavagem pulverizado no gás quente que sai das câmaras do forno é muito maior do que o necessário para o resfriamento, e o licor de lavagem restante que não é evaporado fornece um fluxo líquido no coletor principal de gás que serve para lavar o alcatrão condensado e outros compostos. A corrente de licor de lavagem flui por gravidade para a tubulação principal de sucção junto com o gás bruto do forno de coque. O gás de coqueria bruto e o licor de lavagem são separados usando um pote de drenagem (o canto inferior) na tubulação principal de sucção. O licor de lavagem e o gás bruto do forno de coque então fluem separadamente para a planta de subprodutos para tratamento. A composição típica dos principais componentes do gás bruto de coqueria está na Tab 1.
Tab 1 Composição do forno de coque bruto GA s | ||
Sl. No. | Nome químico | % Volume |
1 | Hidrogênio | 52-59 |
2 | Metano | 26-33 |
3 | Nitrogênio | 1,9-5,7 |
4 | Monóxido de carbono | 4,5-7,0 |
5 | Etileno | 2,0-2,8 |
6 | Dióxido de carbono | 1,4-2,1 |
7 | sulfeto de hidrogênio | 0,4-1,2 |
8 | Cianeto de hidrogênio | 0-1,2 |
9 | Etano | 0,7-1,1 |
10 | Amônia | 0-1,1 |
11 | Benzeno | 0-1,0 |
12 | Dissulfeto de carbono | 0-0,3 |
13 | Tolueno | 0,1-0,2 |
O gás bruto saturado proveniente da bateria do forno de coque contém cerca de 46% a 48% de vapor de água. Outro componente do gás bruto contém hidrogênio (H2), metano (CH4), nitrogênio (N2), monóxido de carbono (CO), dióxido de carbono (CO2), parafinas altas e hidrocarbonetos insaturados (etano, propano etc.) e oxigênio (O2) etc. O gás de coqueria bruto também contém vários contaminantes, que conferem ao gás de coqueria suas características únicas. Estes consistem em (i) componentes de alcatrão, (ii) gases de ácido de alcatrão (gases fenólicos), (iii) gases de base de alcatrão (bases de piridina), (iv) benzeno, tolueno e xileno (BTX), óleo leve e outros aromáticos, ( v) naftaleno, (vi) gás amoníaco, (vi) gás sulfureto de hidrogénio, (vii) gás cianeto de hidrogénio, (viii) cloreto de amónio e (ix) dissulfureto de carbono.
A fim de tornar o gás bruto do forno de coque adequado para uso como um gás combustível limpo e ecológico, a planta de subprodutos deve realizar certas funções que incluem (i) resfriar o gás bruto do forno para condensação de vapor de água e contaminantes, ( ii) remover alcatrão e naftaleno para evitar entupimento da linha de gás/equipamento, (iii) remover amônia (NH3) para evitar a corrosão da linha de gás, (iv) remover óleo de benzol para recuperação e venda de benzeno, tolueno e xileno (BTX), e ( v) remover o sulfeto de hidrogênio para atender aos regulamentos de emissões locais que regem a combustão de gás de coqueria. O diagrama de fluxo do tratamento do gás bruto do forno de coque é dado na Fig 1
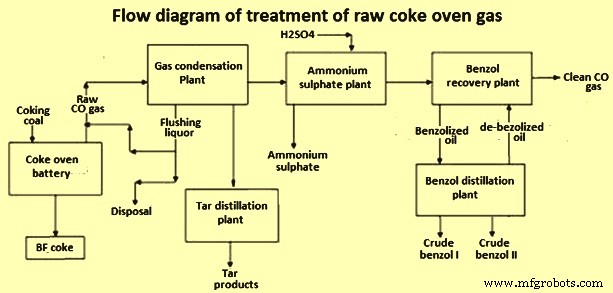
Fig 1 Diagrama de fluxo para tratamento de gás bruto de forno de coque
Os efeitos da recuperação de subprodutos do gás de coqueria são (i) redução no volume de gás de coqueria, (ii) redução no poder calorífico do gás, (iii) efeito na temperatura da chama e volume da chama, e (iv) alteração na densidade e composição do gás. O gás de coqueria limpo é um gás incolor com odor característico de sulfeto de hidrogênio e hidrocarbonetos.
O gás CO bruto pode conter hidrogênio, metano, nitrogênio, monóxido de carbono, dióxido de carbono, etano, oxigênio, etileno e benzeno. Também pode conter algumas quantidades de amônia, sulfeto de hidrogênio, vapor de água, ciclopentadieno, tolueno, naftaleno, cianeto de hidrogênio, cianogênio e óxido nítrico. Uma composição típica de gás de coqueria limpo é fornecida na Tab 2.
Tab 2 Composição do gás de coqueria limpo | ||
Sl. Não . | Nome químico | % Volume |
1 | Hidrogênio | 42-65 |
2 | Metano | 17-34 |
3 | Nitrogênio | 1,2-18 |
4 | Monóxido de carbono | 4,6-7,5 |
5 | Dióxido de carbono | 0,2-3,5 |
6 | Etano | 0,1–-2,9 |
7 | Oxigênio | 0-2,6 |
8 | Etileno | 0,1 -2,5 |
9 | Benzeno | 0-– 0,4 |
O rendimento final de gás de coqueria limpo após o tratamento na planta de subprodutos é de cerca de 300 N cum por tonelada de carvão seco. O rendimento do gás depende (i) da matéria volátil no carvão de carga e (ii) da condição de carbonização. A densidade do gás CO à temperatura e pressão padrão está na faixa de 0,45 kg/cum a 0,50 kg/cum. O gás CO tem um poder calorífico que varia entre 4000 kcal/N cum a 4600 kcal/N cum. Tem uma temperatura teórica de chama de 1982 graus C. Tem uma taxa de propagação de chama que permite que a temperatura real da chama seja próxima da temperatura teórica da chama. O gás CO transporta cerca de 18% da energia de entrada em um forno de coque e bateria de subprodutos (Fig. 2).
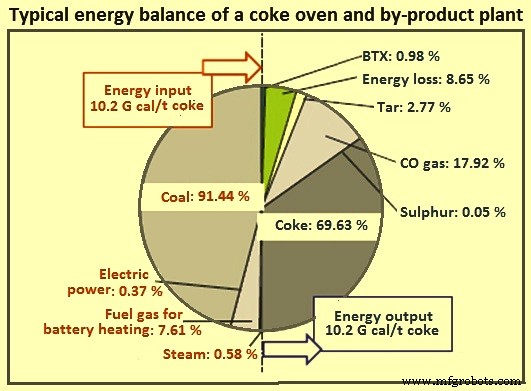
Fig 2 Balanço energético típico de um forno de coque e planta de subprodutos
Os dados analíticos indicam que os HAP (poluentes perigosos do ar) voláteis compreendem coletivamente muito menos de 1% em volume de gás CO após o tratamento convencional de gás CO bruto em uma planta de subprodutos. Portanto, a combustão do gás CO em unidades de combustão operadas com boa manutenção, como aquecedores de processo e caldeiras, etc., resulta em níveis muito baixos de emissões de HAP. As emissões de partículas filtráveis (PM) da combustão do gás CO são normalmente baixas. As emissões de metal HAP do gás CO não são significativas.
Usos do gás de coqueria
O gás de coqueria é um componente importante no balanço energético da siderurgia. É normalmente utilizado no aquecimento de baterias de fornos de coque, aquecimento em outros fornos da siderurgia e para geração de energia. O gás de coqueria pode ser usado como tal ou pode ser misturado com o gás de alto-forno antes de ser usado como combustível em um forno.
O COG também pode ser usado como redutor em alto-forno. A injeção de gás CO é um processo que envolve a injeção de grandes volumes de gás de coqueria na canaleta de um alto-forno. Isso fornece não apenas uma fonte suplementar de carbono, mas também acelera a produção de ferro líquido, além de reduzir a necessidade de coque metalúrgico para reações no alto-forno. A tecnologia de injeção de gás CO também reduz as emissões absolutas de CO2, bem como as emissões de SO2 do alto-forno.
A produção de DRI (ferro reduzido direto) na rota integrada do aço com base na utilização do gás CO disponível é um fenômeno muito recente. O uso do gás CO para a produção de DRI tem várias vantagens tanto do ponto de vista econômico quanto ambiental. O uso do gás CO excedente como gás redutor para produzir DRI recupera 97% da energia disponível em comparação com a recuperação de 30% a 40% pela queima do gás CO para produzir energia elétrica. A utilização de gás CO é mostrada na Fig 3.
Fig 3 Fluxo de gás típico em siderúrgica mostrando a utilização de gás CO
De acordo com um estudo de 2007 da Agência Internacional de Energia, cerca de 70% do gás CO está sendo usado em processos de fabricação de ferro e aço, 15% para aquecimento de fornos de coque e 15% para produção de eletricidade. Além disso, o estudo afirma que, ao usar mais gás CO para geração de energia (de preferência por técnica de geração de energia de ciclo combinado mais eficiente, que pode fornecer eficiências de cerca de 42%, em oposição ao uso em usinas de energia baseadas em caldeiras trabalhando em ciclos de vapor com eficiência média de cerca de 30 %, podem ser alcançadas melhorias na eficiência energética.
Processo de manufatura
- Sistema de Automação, Controle e Medição de Coqueria
- Geração e uso de gás de alto-forno
- Bateria de forno de coque sem recuperação
- Fábrica de Subprodutos de Forno de Coque
- 4 Uso engenhoso de IoT para monitoramento de gás no setor de petróleo e gás
- Como a IIoT melhora a eficiência e a geração de receita para OEMs de petróleo e gás
- A abordagem de segurança de gás e chama para a indústria de geração de energia
- Qual é a diferença entre um forno a gás e um forno elétrico?
- Diferentes tipos de processos de soldagem a gás e suas aplicações
- Geração de nitrogênio no corte a laser