Papel da escória na fabricação de aço do conversor
Papel da escória na fabricação de aço do conversor
O processo de conversão de oxigênio é o principal processo siderúrgico para a produção de aços carbono e baixa liga. O processo é essencialmente um processo oxidante de refino do metal quente de alto carbono (HM) para aço líquido de baixo carbono. O processo de oxidação é realizado soprando oxigênio no conversor. Isso faz com que o ferro líquido e outras impurezas metálicas e não metálicas presentes no líquido se fundam no banho do conversor para formar óxidos mais leves que o aço líquido e flutuam na superfície do banho. O nome genérico desses óxidos é “escória”. Alguns óxidos são de natureza ácida que podem reagir com os refratários básicos do conversor e, portanto, uma escória básica usando cal e dolomita calcinada é geralmente feita para proteger os refratários do conversor. O oxigênio também pode reagir com o carbono para criar um gás que fornece bolhas para espumar a escória líquida e para fornecer a energia química necessária durante a fabricação do aço.
No processo siderúrgico, a escória é predominantemente uma mistura de óxidos com pequenas quantidades de sulfetos e fosfetos. Os óxidos são de natureza ácida ou básica. A escória é formada durante o refino de metal quente no qual Si oxida a SiO2, Mn a MnO, Fe a FeO e P a P2O5 etc., e adição de óxidos como CaO (cal), MgO (dolomita calcinada), óxido de ferro, e outros. A adição de óxidos é feita para obter as propriedades físico-químicas desejadas da escória como ponto de fusão, basicidade, viscosidade etc.
Existem quatro fontes primárias para a escória durante o processo de fabricação de aço no conversor. Estes são (i) oxidação de elementos metálicos no aço líquido (por exemplo, silício, manganês, alumínio, titânio, cromo e vanádio etc.), (ii) devido à presença de não-metálicos no banho líquido (por exemplo, enxofre e fósforo), (iii) adições de fluxo (por exemplo, cal, dolomita calcinada e espatoflúor) e refratários dissolvidos (por exemplo, MgO e CaO + MgO).
Uma escória ácida corrói o revestimento do conversor, uma vez que os tijolos do revestimento são básicos. A escória ácida contém grandes quantidades de SiO2, Al2O3 que podem tornar a escória mais fina. Uma escória básica contém óxidos como MgO e CaO, o que torna a escória mais espessa. O FeO é a parte mais importante da escória, pois faz com que a cal se dissolva em temperaturas mais baixas, o que é chamado de "fluxo". A temperatura de fusão do CaO sendo 2570 graus C e MgO sendo 2800 graus C, pode-se ver que é difícil sem FeO baixar o ponto de fusão para obter cal ou magnésia em solução onde as temperaturas de vazamento de aço são geralmente abaixo de 1650 graus C.
O papel desempenhado pela escória no processo de fabricação do aço conversor de oxigênio é muito importante. A cal é fundamental para a siderurgia. A ciência de como a cal interage com os vários componentes formados durante a fabricação do aço é a base para entender a velha frase “Faça a escória e o aço se fará”. A escória é um nome genérico e na siderurgia é principalmente uma solução de óxidos e sulfetos no estado líquido e as fases multicristalinas no estado sólido. A escória é uma fase separada do aço líquido, pois (i) é mais leve que o aço líquido e (ii) é imiscível no aço líquido. Os papéis importantes que a escória desempenha durante a fabricação de aço são apresentados abaixo.
- Age como sumidouro de impurezas durante o refino do aço.
- Controla o potencial oxidante e redutor do banho durante o refino através do teor de FeO. O teor mais alto de FeO da escória faz com que a escória oxide, enquanto o teor mais baixo de FeO torna a escória redutora.
- Ajuda na desfosforação e absorve um pouco de enxofre.
- Evita a passagem de nitrogênio e hidrogênio da atmosfera para o aço líquido no banho.
- Ele absorve inclusões de óxido/sulfeto.
- Isole o banho líquido e reduz as perdas térmicas. Ele fornece uma barreira térmica e, portanto, evita a transferência de calor do aço líquido para o ambiente.
- Ele fornece proteção ao aço líquido contra reoxidação.
- Ele emulsiona o metal quente e promove a oxidação do carbono.
As funções da escória como dadas acima requerem que a escória possua certas propriedades químicas (basicidade, potencial de oxidação), bem como propriedades físicas (densidade, ponto de fusão, viscosidade). Ambas as propriedades são controladas pela composição e estrutura da escória.
Do ponto de vista da formação de escória, existem duas práticas de sopro limitantes, a saber (i) sopro suave com alta posição da lança sem agitação de fundo de gás inerte e é caracterizada por baixa intensidade de mistura do banho de ferro, e (ii) sopro duro com baixa posição da lança e com agitação de fundo (em conversores soprados combinados), caracterizado por mistura mais intensiva do banho de ferro e interação mais profunda do jato de oxigênio com o banho líquido. No caso de sopro suave, a interação do jato de oxigênio com o banho de ferro é superficial, a transferência de massa do interior do banho é lenta devido à mistura fraca, e o ferro é oxidado primeiro e escória. No caso de sopro forte a interação entre o jato de oxigênio e o banho, assim como a transferência de massa do interior do banho para as camadas superficiais, é mais intensa e os elementos impuros do banho são oxidados primeiro. Os principais efeitos da prática de sopro suave são apresentados abaixo.
- Há um aumento na taxa de formação de escória
- Isso resulta em maior teor de FeO na escória
- Isso resulta em supersaturação de oxigênio do aço líquido
- Favorece a formação de espuma de escória
- Promove a desfosforização pelo menos em um alto nível de carbono
- Aumenta a taxa de oxidação de Mn e outras impurezas
- Aumenta o desgaste dos refratários
- Aumenta as probabilidades de escória slopping
Existem quatro princípios no controle da escória na siderurgia. Estes são (i) controle da basicidade da escória que é a razão entre os óxidos básicos e os óxidos ácidos, (ii) saturação da escória com MgO, (iii) controle de formação de espuma de escória também conhecido como controle de viscosidade da escória e (iv) equilíbrio de aço e escória no processo de fabricação do aço para atingir um 'estado de equilíbrio'.
O termo basicidade da escória é um meio pelo qual se determina quão ácida ou básica é uma escória em relação ao refratário básico utilizado no conversor. Se a escória for mais ácida, irá erodir os tijolos, se for mais básica, protegerá os tijolos. A basicidade da escória é normalmente fixada pela quantidade de cal e dolomita calcinada adicionada, os níveis de silício e alumínio do metal quente e sucata de aço carregada, bem como ferro-ligas. O valor mais baixo da razão indica que a escória é ácida e à medida que a razão aumenta a escória se torna cada vez mais básica.
Além da basicidade, o teor de MgO da escória também é importante. A escória contém compostos de cálcio dissolvidos e compostos ácidos que fazem com que o MgO se dissolva dos tijolos refratários do revestimento na escória. O MgO se dissolve na escória com base nas relações do teor de FeO, basicidade e temperatura. Quanto menor a basicidade da escória, maior a necessidade de MgO para a escória. Um aumento no FeO e na temperatura também aumenta a necessidade de MgO da escória. Os efeitos sobre o MgO podem ser vistos na Figura 1.
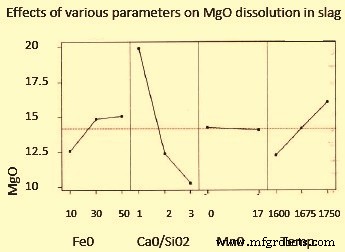
Fig 1 Efeitos de vários parâmetros na dissolução de MgO na escória
A altura da espuma no conversor é uma função do tempo de sopro. A altura máxima da espuma é alcançada quando a massa de escória se aproxima de 70% da quantidade de escória final. O pó do conversor reativo é uma fonte de óxidos de ferro e auxilia na rápida formação de escória espumante, mesmo quando o sopro começou com lança baixa, ou seja, prática de sopro forte. A escória espumante diminui a taxa de pós-combustão e aumenta a eficiência da transferência de calor para o banho.
Vários fatores afetam a tendência à formação de espuma da escória líquida. Estes são dados abaixo
- Teor de FeO na escória. A escória deve conter FeO e deve estar em quantidade suficiente para reagir com o carbono para fazer bolhas de CO.
- Corrija a viscosidade ou consistência para manter as bolhas o maior tempo possível.
- MgO suficiente para minimizar o desgaste refratário e promover a formação de espuma.
O carbono do ferro líquido no banho cria bolhas de CO para espumar a escória. A viscosidade da escória é determinada pela proporção dos componentes da escória e como esses componentes tornam a escória fina ou espessa. É o equilíbrio desses componentes para fazer com que a viscosidade da escória seja correta para manter as bolhas por mais tempo. SiO2, FeO e Al2O3 tornam a escória mais fina, enquanto CaO e MgO tornam a escória mais espessa.
Uma estimativa aproximada para a densidade da escória do conversor consistindo de CaO, SiO2, FeO e MnO etc. dentro das faixas típicas de composição e temperatura do processo de conversão de oxigênio é de 2,8 a 3 toneladas/cum. Se a razão de massa de escória para aço no final de um golpe do conversor varia entre 0,08 e 0,1, a razão de volume de escória para aço aumenta de quase zero no início do golpe para 0,20/0,25 no final do golpe.
Em geral, considera-se que a escória amortece as ejeções de metal (cuspir) e a formação de poeira do conversor durante o sopro. Se um conversor for operado com uma quantidade muito baixa de escória, podem ocorrer ejeções de metais pesados e formação de crânio. As propriedades da escória são, no entanto, de extrema importância. A escória fluida e fortemente oxidante é favorável para as reações de oxidação, mas pode resultar na saída da escória do conversor. O slopping geralmente ocorre se a formação de escória for atrasada, por algum motivo, e uma grande quantidade de oxigênio for "carregada" na escória por sopro suave, adição de minério/pó, etc. A formação intensiva de CO resulta na formação de emulsão de escória-metal, A formação de escória começa, as reações de oxidação secundária e terciária ocorrem vigorosamente e a formação de gás intensificada leva a um slopping pesado. O controle adequado da formação de escória e espuma é uma medida central na prevenção de slopping.
O FeO na escória é proporcional ao oxigênio dissolvido no aço. Em todas as reações escória/metal há uma razão entre quanto de uma coisa está no aço e quanto está na escória. Isso é chamado de “relação de partição”. O aço e a escória no conversor precisam ser balanceados para que fiquem no estado de equilíbrio. Existe também uma relação do teor de carbono no aço controlando o teor de oxigênio do aço. O carbono influencia o nível de oxigênio no aço. Em baixos níveis de carbono, o oxigênio reage com o ferro para formar FeO, o que torna a escória mais fina e afeta as perdas de rendimento.
O teor de SiO2 da escória determina a quantidade de cal necessária durante a fabricação do aço. Também diminui o rendimento. Todos os materiais que entram no banho do conversor em condições oxidantes influenciam os requisitos que a escória precisa e o custo dessas adições, bem como as perdas de rendimento. O metal quente e a sucata juntos influenciam o teor de SiO2 da escória. Cada quilograma de silício reagindo com oxigênio cria 2,17 quilogramas de SiO2. Este SiO2 precisa ser neutralizado com cal e dolomita calcinada para formar uma escória básica. Esta escória básica causa uma perda de 5 quilogramas de ferro na escória como FeO. A razão é que há um aumento no volume de escória aumentando a quantidade de material ácido que deve ser equilibrado por um material básico como a cal.
O desgaste químico do revestimento refratário depende, entre outros, de sua interação com escória/emulsão, metal líquido e fase gasosa, incluindo sopro de O2. O mecanismo mais importante é a dissolução do revestimento na escória. A rápida formação de escória para ligar e neutralizar a formação de SiO2 ácido no início do sopro é um ponto chave. A escória quente altamente oxidante dissolve facilmente o revestimento de magnésia ou dolomita. O uso de dolomita calcinada pode melhorar muito a vida útil do revestimento. Recentemente, o respingo de escória tornou-se uma prática estabelecida para prolongar a vida útil do conversor. A escória residual no conversor é condicionada pela composição química e temperatura após o vazamento e é respingada por um fluxo violento de nitrogênio ao redor da parede do conversor. O procedimento em si, bem como as consequências para o processo de conversão, são bastante complexos e a escória deve ser rigorosamente ajustada para o tratamento.
A escória deve realizar várias tarefas durante o processo de fabricação do aço no conversor de oxigênio. Principalmente, é formado espontaneamente pelos óxidos não voláteis, resultando na oxidação do ferro e dos constituintes menores do metal quente (SiO2, MnO, P2O5 e FeO). A fim de fundir os óxidos de impureza e formar um baixo ponto de fusão, escória fluida, cal e dolomita calcinada (uma mistura de CaO e MgO) e, se necessário, espatoflúor (CaF2) são carregados no conversor. Em segundo lugar, a escória líquida fornece um ambiente de reação para a remoção de enxofre e fósforo através dos processos de dessulfuração e desfosforação, embora com o desenvolvimento da metalurgia secundária a importância dessas reações no conversor de oxigênio não exista mais. A escória, ao formar uma emulsão com monóxido de carbono (CO) e gotas de aço líquido (espuma de escória), obviamente desempenha algum papel na pós-combustão de CO em dióxido de carbono (CO2), e afeta a transferência de calor por radiação do 'hot spot' formado na cavidade de choque de ferro líquido a jato de oxigênio, nivelando a distribuição de temperatura no conversor. A escória espumante também diminui claramente a taxa de geração de poeira ao absorver alguma fração da poeira.
A formação da escória começa com a dissolução do oxigênio no ferro líquido e a oxidação simultânea do ferro e outros constituintes do banho na zona de impacto do jato de oxigênio. Como a temperatura do banho líquido na zona de impacto do jato de oxigênio é muito alta (mais de 2000°C), uma grande quantidade de oxigênio (até 1%) pode ser dissolvida pelo ferro. Nesta zona de oxidação primária, o óxido de ferro é formado e o ferro líquido com alto teor de oxigênio penetra no banho e entra em contato com o ferro líquido do banho fresco com maior teor de carbono e outros constituintes oxidando-os. Parte dos produtos da reação primária é espalhada na escória e na atmosfera do forno.
Óxido de ferro e outros produtos de oxidação não voláteis, como SiO2, MnO e P2O5, etc. misturam-se com a escória existente e mais cal e dolomita calcinada são dissolvidos na escória líquida. A escória é, portanto, formada por uma complexa cadeia de reações. As reações de formação de escória são dadas abaixo.
[Si] + 2[O] =SiO2 |
[Mn] + [O] =MnO |
[Fe] + [O] =FeO |
[P] + 5[O] =P2O5 | + CaO + (CaO + MgO) => Escória
Essas reações são seguidas por reações secundárias de oxidação-redução, especialmente pela descarbonetação que ocorre na superfície das gotículas de ferro líquido que circulam na escória.
[FexOy] + y C =x Fe + y CO (g)
No período de partida de um golpe de conversor, quando a temperatura do banho é baixa, a escória é geralmente saturada por silicato dicálcico (2CaO.SiO2), mas com o progresso da oxidação do metal quente a composição da escória se afasta do dicálcico 'nariz' de silicato retornando na fase posterior do sopro de volta para ele e passando-o para a saturação de silicato tricálcico (3CaO.SiO2) ou mesmo faixa de saturação de cal. A avaliação do caminho da escória que passa pelas superfícies liquidus de alta temperatura, como o nariz de 2CaO.SiO2 ou superfícies liquidus do 3CaO.SiO2 ou cal e precipitação correspondente de fases sólidas do banho líquido, é um pouco obscurecida pelo fato de que as escórias são multicomponentes as fases e as temperaturas da escória foram relatadas como excedendo, mesmo em várias centenas de graus, a temperatura média do banho de ferro líquido.
Afinidades locais nos limites de fase (escória/banho, escória/gota, banho/gás escória/gás, etc.) controlam o progresso de reações semelhantes dos componentes na mesma fase de solução (ferro fundido ou escória). A magnitude da afinidade da reação depende da afinidade padrão e das atividades (potenciais químicos) dos componentes da reação nas fases da solução. As afinidades de reação locais que controlam a distribuição de oxigênio entre a reação de oxidação de elementos menores no banho de ferro e o ferro, ou seja, o progresso mútuo das reações de oxidação, mudam com o tempo e a evolução da temperatura do processo. Da mesma forma, as afinidades locais das reações de oxidação secundária pelo ferro (e outros óxidos na escória, como o óxido de manganês) controlam o progresso da descarbonetação versus oxidação de outros constituintes menores das gotículas de ferro no ambiente da escória. Este controle termodinâmico da reação de oxidação explica porque o ferro é oxidado e escória em golpe suave. A mistura fraca no banho de ferro resulta no transporte lento de constituintes menores do banho (Si, Mn, C, etc.) do interior do banho para as camadas superficiais onde ocorre a oxidação e das quais gotículas de ferro são respingadas ou estouradas na escória. Essas camadas são o esgotamento de elementos menores, suas atividades na fase metálica e, consequentemente, as afinidades de reação são diminuídas em relação ao ferro. A oxidação do ferro torna-se assim termodinamicamente favorável.
Pois a escória de desfosforação desempenha um papel importante na siderurgia conversora de oxigênio. O balanço da atividade de oxigênio no aço e escória pode ser relacionado na fase de oxidação, bem como nos materiais utilizados para desfosforização. A equação de remoção de fósforo do aço é, em termos simples, a seguinte.
2P + CaO + 5FeO => P2O5.CaO + 5 Fe Temp <1640 graus C
2P + CaO + 5FeO <=P2O5.CaO + 5 Fe Temp> 1640 graus C
Tudo isso mostra que para remover o fósforo da cal do aço (CaO) e o oxigênio (FeO) é necessário produzir o produto de P2O5.CaO para reter na escória. No entanto, se a temperatura ultrapassar 1640 graus C, a reação é revertida e ocorre a refosforização. Portanto, para a remoção de fósforo, a escória contendo P2O5.CaO deve ser removida pela desincrustação do conversor no meio do sopro ou é necessário adicionar mais cal, para diminuir mais o calor (atividade de oxigênio) ou mantê-lo resfriador.
Processo de manufatura
- Tela de cristal líquido (LCD)
- Escória de alto forno e seu papel na operação do forno
- Inclusões em siderurgia e siderurgia secundária
- Siderurgia Verde
- Forno de indução e siderurgia
- Processo de Sopro Combinado na Siderurgia Conversora
- Processo CAS-OB de Siderurgia Secundária
- O Papel da Tubulação de Precisão em Sistemas de Distribuição de Líquidos:Parte 3 de 3
- O Papel da Tubulação de Precisão em Sistemas de Distribuição de Líquidos:Parte 2 de 3
- O Papel da Tubulação de Precisão em Sistemas de Distribuição de Líquidos:Parte 1